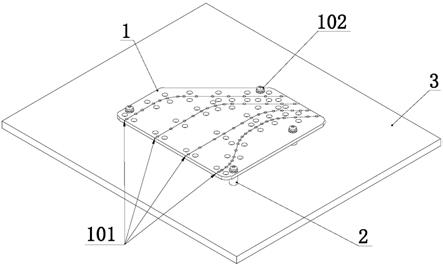
1.本实用新型涉及线缆固定设备,尤其涉及一种用于雷达天线阵的线架板。
背景技术:2.在现有技术中,雷达天线阵的干涉仪设备、射频接收机设备由于线缆较多,需要使用线架板来进行布线,目前的线架板底部设有与线架板本体一体成型的支撑柱,支撑柱通过螺钉等紧固件安装于被布线设备的壳体或者专用的底板上,线架板本体上设置有用来固定线缆的凹槽,在加工过程中,目前的线架板工艺复杂,浪费材料,加工成本高且耗费时间长,导致成品率低,且实际安装中,由于凹槽大小固定,若将少量线缆固定于凹槽中,则线缆容易脱出,若将大量线缆固定于凹槽中,则线缆可能因挤压受损。
3.因此,亟需一种新的线架板来解决现有线架板所存在的问题。
技术实现要素:4.本实用新型要解决的技术问题就在于:针对现有技术存在的技术问题,本实用新型提供一种用于雷达天线阵的线架板,节省材料,降低成本和加工时间,且便于布线过程中的线缆固定。
5.为解决上述技术问题,本实用新型提出的技术方案为:
6.一种用于雷达天线阵的线架板,包括线架板本体和支撑柱,所述支撑柱可拆卸安装于线架板本体的底部,且所述支撑柱与线架板本体可拆卸连接,所述线架板本体的表面设置有至少一条布线轨迹,所述布线轨迹上可拆卸安装有固定件,使得被布线的线缆延布线轨迹被固定。
7.优选的,所述布线轨迹的转弯半径大于被布置的线缆的最小转弯半径。
8.优选的,还包括螺钉,所述线架板本体上开设有供螺钉穿过的第一通孔,所述支撑柱为管状结构且支撑柱的内孔设有螺纹,所述螺钉、第一通孔和支撑柱一一对应,所述螺钉穿过对应的第一通孔和对应的支撑柱内孔螺纹连接。
9.优选的,所述线架板本体上开设有与支撑柱一一对应的第二通孔,所述支撑柱的顶端设有膨胀卡扣,所述膨胀卡扣插设于对应的第二通孔中。
10.优选的,所述布线轨迹一侧设置有沿布线轨迹间隙布置的第一安装孔,所述布线轨迹另一侧设置有沿布线轨迹间隙布置的第二安装孔,所述固定件、第一安装孔和第二安装孔一一对应,所述固定件的两端分别设置于对应的第一安装孔和第二安装孔中。
11.优选的,所述固定件为扎带,所述扎带的一端穿过对应的第一安装孔,所述扎带的另一端穿过对应的第二安装孔,且所述扎带两端相连。
12.优选的,所述固定件为第一压板,所述第一压板底部的两端均设有膨胀卡扣,所述第一压板一端的膨胀卡扣插设于对应的第一安装孔中,所述第一压板另一端的膨胀卡扣插设于对应的第二安装孔中。
13.优选的,所述固定件包括第二压板和两个螺栓,所述第二压板的两端均设有供螺
栓穿过的第三通孔,所述第一安装孔和第二安装孔均为螺纹孔,一个螺栓穿过第二压板一端的第三通孔且和第一安装孔螺纹连接,另一个螺栓穿过第二压板另一端的第三通孔且和第二安装孔螺纹连接。
14.优选的,所述布线轨迹包括间隙布置的标识孔,相邻的标识孔之间连接有标识线。
15.优选的,所述线架板本体的厚度为2mm~2.5mm。
16.与现有技术相比,本实用新型的优点在于:
17.本实用新型的线架板本体和支撑柱可拆卸安装,且线架板上设置固定件来固定线缆,从而降低了线架板的加工难度,节省了加工时间,避免了线架板本体和支撑柱一体化加工造成的材料浪费,从而降低了成本,且采用固定件的方式相比用凹槽固定线缆显著降低了线架板的加工难度,进一步节省了加工时间,降低成本并且避免浪费材料。
附图说明
18.图1为本实用新型实施例一中线架板安装示意图。
19.图2为本实用新型实施例一中线架板安装侧视图。
20.图3为本实用新型实施例一中线架板本体正视图。
21.图例说明:1-线架板本体、2-支撑柱、3-底板、101-布线轨迹、102-螺钉。
具体实施方式
22.以下结合说明书附图和具体优选的实施例对本实用新型作进一步描述,但并不因此而限制本实用新型的保护范围。
23.实施例一
24.如图1所示,本实施例中出一种用于雷达天线阵的线架板,包括线架板本体1和支撑柱2,支撑柱2可拆卸安装于线架板本体1的底部,且支撑柱2与线架板本体1可拆卸连接,线架板本体1的表面设置有至少一条布线轨迹101,布线轨迹101上设置有固定件,使得被布线的线缆延布线轨迹101被固定。
25.本实施例中,线架板本体1和支撑柱2分别通过单独加工得到,其中线架板本体1的加工工艺为钣金加工,支撑柱2的加工工艺为数控机加工,相比一体化加工能够有效的节约材料消耗,并且降低成本,从而减少了线架板的制作时间。
26.另一方面,由于不需要开设凹槽来容纳线缆,本实施例中的线架板本体1厚度为2mm~2.5mm,在保证强度的前提下,大大降低了线架板的厚度,也节省了制作时的材料消耗。
27.本实施例中,布线轨迹101的转弯半径大于被布置的线缆的最小转弯半径,从而保证射频信号传输畅通,有效节省了成本,且布线结构简洁美观,售后维护方便。
28.如图1所示,本实施例中通过螺钉102将线架板本体1和支撑柱2固定,线架板本体1上开设有供螺钉102穿过的第一通孔,支撑柱2为管状结构且支撑柱2的内孔设有螺纹,螺钉102、第一通孔和支撑柱2一一对应,螺钉102穿过对应的第一通孔和对应的支撑柱2内孔螺纹连接,本实施例中的螺钉102采用十字盘头螺钉,保证线架板固定状态稳定,且结构简洁美观。
29.为了将本实施例中的线架板固定于外部的底板3上,支撑柱2的底端可以设置螺
柱,且底板3上开设螺纹孔,从而可以将螺柱插设于螺纹孔中且二者螺纹配合。此外,支撑柱2也可以为光滑内孔,螺钉102采用长螺钉,从而可以穿过支撑柱2后插设于螺纹孔中且与螺纹孔螺纹配合。
30.本实施例中,布线轨迹101通过计算并利用3d软件绘制得到,包括间隙布置的标识孔,标识孔通过激光多点位打孔得到,相邻的标识孔之间连接有标识线,标识线由黑色记号笔绘制得到,即通过黑色记号笔将布线轨迹101中所有标识孔逐个相连,就能得到明晰的轨迹。通过计算和利用3d软件进行3d布线明确了雷达天线阵的射频缆线路轨迹、精确的长度和线路转弯半径,有效地指导生产布线。
31.如图1和图3所示,本实施例中,布线轨迹101一侧设置有沿布线轨迹101间隙布置的第一安装孔,布线轨迹101另一侧设置有沿布线轨迹101间隙布置的第二安装孔,固定件、第一安装孔和第二安装孔一一对应,固定件的两端分别设置于对应的第一安装孔和第二安装孔中。本实施例中,固定件为扎带或者扎绳,以扎带为例,扎带的一端穿过对应的第一安装孔,扎带的另一端穿过对应的第二安装孔,且扎带两端相连,从而能够将扎带围绕而成的圆环中间的线缆进行固定,能够有效规范操作人员的操作工艺,使操作人员能方便快捷的完成布线操作,省去了将线缆安装到凹槽内的步骤,且布线更加简洁美观。
32.实施例二
33.本实施例与实施例一基本相同,区别在于线架板本体1与支撑柱2的安装方式线架板本体1上开设有与支撑柱2一一对应的第二通孔,支撑柱2的顶端设有膨胀卡扣,膨胀卡扣插设于对应的第二通孔中。本实施例中的支撑柱2可为实心圆柱体结构,支撑柱2的底端可以设置螺柱,且底板3上开设螺纹孔,从而可以将螺柱插设于螺纹孔中且二者螺纹配合。
34.通过上述结构,本实施例中支撑柱2的加工方式更加简便,进一步节约材料消耗,并且降低成本,从而减少了线架板的制作时间。
35.实施例三
36.本实施例与实施例一基本相同,区别在于固定件固定线缆的方式与实施例一不同,本实施例中的固定件为第一压板,第一压板底部的两端均设有膨胀卡扣,第一压板一端的膨胀卡扣插设于对应的第一安装孔中,第一压板另一端的膨胀卡扣插设于对应的第二安装孔中。
37.通过上述结构,本实施例采用可拆卸的压板替换扎带或者扎绳,便于后续进行线缆的布线调整,需要调整布线时,仅需要分别取下每个布线轨迹101上的第一压板,重新布线后再将第一压板按照原位安装,而实施例一中需要剪开扎带或者扎绳,重新布线后再用新的扎带或者扎绳固定每个布线轨迹101上线缆。
38.显然,本实施例相比实施例一节约材料消耗,并且降低成本。
39.实施例四
40.本实施例与实施例三基本相同,区别在于本实施例中的固定件包括第二压板和两个螺栓,第二压板的两端均设有供螺栓穿过的第三通孔,第一安装孔和第二安装孔均为螺纹孔,一个螺栓穿过第二压板一端的第三通孔且和第一安装孔螺纹连接,另一个螺栓穿过第二压板另一端的第三通孔且和第二安装孔螺纹连接。
41.通过上述结构,本实施例中可以调整第二压板与线架板本体1之间的间隙,从而适应不同数量的线缆,布线轨迹101上线缆较少时,可以旋紧螺栓,从而减小第二压板与线架
板本体1之间的间隙,布线轨迹101上线缆较多时,可以旋送螺栓,从而增加第二压板与线架板本体1之间的间隙。
42.相比实施例三,本实施例通过上述结构保证线缆固定稳固,同时避免线缆因挤压受损。
43.上述只是本实用新型的较佳实施例,并非对本实用新型作任何形式上的限制。虽然本实用新型已以较佳实施例揭露如上,然而并非用以限定本实用新型。因此,凡是未脱离本实用新型技术方案的内容,依据本实用新型技术实质对以上实施例所做的任何简单修改、等同变化及修饰,均应落在本实用新型技术方案保护的范围内。