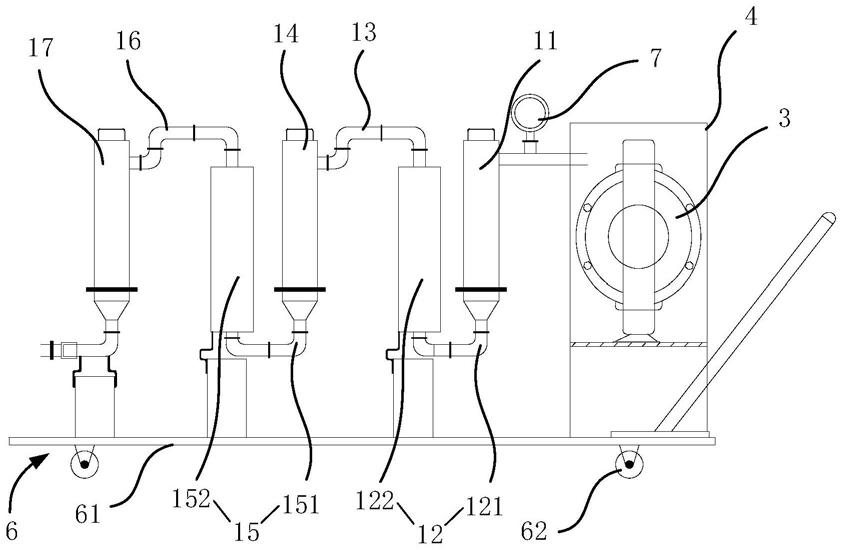
1.本实用新型涉及电池生产领域,特别是一种杂质清除机构及杂质清除系统。
背景技术:2.在锂离子电池生产过程中,会使用到电池浆料,由于电池浆料制造和输送过程中容易产生磁性金属杂质,如果不去除这些磁性金属杂质的话,生产出来的电池在充电时,磁性金属杂质会在隔膜上沉积并不断生长,最后刺穿隔膜,导致正负极的微短路,造成电池自放电,给电池带来安全隐患。
3.为了提高电池的良品率,市面上出现了一款杂质清除机构,杂质清除机构内置一根磁棒,电池浆料流经磁棒周围的磁场时,磁性金属杂质会被磁棒吸附,但由于电池浆料流经磁场的时间较短,导致距离磁棒较远的电池浆料中的磁性金属杂质未能有足够时间迁移到磁铁表面,因此磁性金属杂质的清除率较低,电池的良品率没有显著提升。
技术实现要素:4.本实用新型实施例要解决的技术问题在于,提供一种杂质清除机构及杂质清除系统,以解决现有技术中的杂质清除机构在使用时,电池浆料流经磁场的时间较短,导致距离磁棒较远的电池浆料中的磁性金属杂质未能有足够时间迁移到磁铁表面,因此磁性金属杂质的清除率较低,电池的良品率没有显著提升的问题。
5.第一方面,本实用新型实施例提供了一种杂质清除机构,用于清除电池浆料中的磁性金属杂质,包括第一吸附组件,所述第一吸附组件包括:壳体,其开设有入料口与出料口,所述壳体的内腔形成有流道,所述流道与所述入料口及所述出料口连通,所述电池浆料经由所述入料口流入所述流道,并沿第一方向于所述流道中流动,随后经由所述出料口流出所述流道;磁性件,其沿所述第一方向设置于所述流道中。
6.进一步地,还包括粗滤网组件,所述粗滤网组件包括:第一连接管,其一端与所述出料口连通;粗滤网,其与所述第一连接管另一端连通,以使所述出料口流出的所述电池浆料流动至所述粗滤网。
7.进一步地,还包括:第二连接管,其一端与所述粗滤网连通;第二吸附组件,其与所述第一吸附组件结构一致,所述第二吸附组件的入料口与所述第二连接管另一端连通,以使经由所述粗滤网过滤后的所述电池浆料流动至所述第二吸附组件。
8.进一步地,还包括精滤网组件,所述精滤网组件包括:第三连接管,其一端与所述第二吸附组件的出料口连通;精滤网,其与所述第三连接管另一端连通,以使经由所述第二吸附组件吸附后的所述电池浆料流动至所述精滤网。
9.进一步地,还包括:第四连接管,其一端与所述精滤网连通;第三吸附组件;其与所述第二吸附组件结构一致,所述第三吸附组件的入料口与所述第四连接管另一端连通,以使经由所述精滤网过滤后的所述电池浆料流动至所述第三吸附组件。
10.进一步地,所述磁性件与所述内腔的腔壁之间的距离小于25mm。
11.进一步地,所述粗滤网的目数大于等于80且小于等于170,所述精滤网的目数比所述粗滤网大30至70。
12.进一步地,所述磁性件为磁棒,所述壳体呈圆桶状;其中,所述磁棒的直径为35mm至115mm,所述壳体的直径比所述磁棒的直径大10mm至30cm。
13.第二方面,本实用新型实施例还提供了一种杂质清除系统,包括两个杂质清除机构,其为上述第一方面所述的杂质清除机构;分流管,其具有两个输出口以及一个输入口,两个所述输出口分别连接两个第一吸附组件的入料口;供料泵,其与所述输入口连通,所述供料泵用于抽取电池浆料,并将所述电池浆料输入至所述输入口。
14.进一步地,还包括:承载板,所述杂质清除机构与所述供料泵均装设于所述承载板上;车轮,其装设于所述承载板底部。
15.本实用新型实施例的有益效果在于:通过在壳体上开设有入料口以及出料口,使得电池浆料能经由入料口流入壳体内腔形成的流道处,随后经由出料口流出流道,由于流道处设置有磁性件,所以能吸附电池浆料中的磁性金属杂质,其中,电池浆料在流道中是沿第一方向流动的,磁性件沿第一方向设置于流道中,所以电池浆料的流向是与磁性件的长度方向平行的,这种结构能最大程度地延长电池浆料流经磁场的时间,使电池浆料中的磁性金属杂质有足够时间迁移到磁性件表面,因此电池浆料中的磁性金属杂质的清除率较高,进而使电池的良品率得到显著的提升。
附图说明
16.下面将结合附图及实施例对本实用新型的具体实施方式作进一步详细的说明,附图中:
17.图1是本实用新型实施例提供的杂质清除系统的结构示意图;
18.图2是本实用新型是实力提供的第一吸附组件、第二吸附组件以及第三吸附组件的结构简图;
19.图3是图1所示杂质清除系统另一角度的整体结构示意图;
20.图中各附图标记为:
21.1、杂质清除机构;11、第一吸附组件;111、壳体;1111、入料口;1112、出料口;1113、流道;1114、内腔的腔壁;112、磁性件;12、粗滤网组件;121、第一连接管;122、粗滤网;13、第二连接管;14、第二吸附组件;141、第二吸附组件的入料口;142、第二吸附组件的出料口;15、精滤网组件;151、第三连接管;152、精滤网;16、第四连接管;17、第三吸附组件;171、第三吸附组件的入料口;2、分流管;3、供料泵;4、防护罩;5、第五连接管;6、承载车;61、承载板;62、车轮;7、压力表。
具体实施方式
22.需要说明的是,在不冲突的情况下,本技术中的实施例及实施例中的特征可以相互组合。现结合附图,对本实用新型的较佳实施例作详细说明。
23.本实用新型提实施例供了一种杂质清除机构1,用于清除电池浆料(图中未示出)中的磁性金属杂质(图中未示出),如图1-3所示,杂质清除机构1包括第一吸附组件11,第一吸附组件11包括壳体111以及磁性件112。壳体111开设有入料口1111与出料口1112,壳体
111的内腔形成有流道1113,流道1113与入料口1111及出料口1112连通。电池浆料经由入料口1111流入流道1113,并沿第一方向(x方向)于流道1113中流动,随后经由出料口1112流出流道1113。磁性件112沿第一方向设置于流道1113中。
24.通过实施本实施例,电池浆料从入料口1111处进入壳体111并流入流道1113中,随后经由出料口1112从流道1113中流出,由于流道1113处设置有磁性件112,所以能吸附电池浆料中的磁性金属杂质,从而提高电池的良品率。又因为本实施例的电池浆料在流道1113中是沿第一方向流动的,磁性件112又是沿第一方向设置于流道1113中,所以电池浆料的流向是与磁性件112的长度方向平行的,这样设置能最大程度地延长电池浆料流经磁场的时间,使电池浆料中的磁性金属杂质有足够时间迁移到磁性件112表面,因此电池浆料中的磁性金属杂质的清除率较高,进而使电池的良品率得到显著的提升。
25.在具体实施例中,如图1-3所示,杂质清除机构1还包括粗滤网组件12,粗滤网组件12包括第一连接管121以及粗滤网122。第一连接管121一端与出料口1112连通,另一端与粗滤网122连通,以使出料口1112流出的电池浆料能流动至粗滤网122。
26.具体地,经过第一吸附组件11对电池浆料中的磁性金属杂质进行吸附后,电池浆料会流经粗滤网组件12。粗滤网组件12可以降低电池浆料的流速,从而延长电池浆料流经磁场的时间,使电池浆料中的磁性金属杂质有足够时间迁移到磁性件112表面。进一步地提高了电池浆料中的磁性金属杂质的清除率,使电池的良品率得到进一步地提升。
27.由于电池浆料中混合有粉体,若粉体于电池浆料中不能有效分散,则会存在大颗粒团聚,如果不能将这些大颗粒去除或分散开,就会造成电池的极片外观不良,严重影响良品率。本实施例的粗滤网122可以起到过滤以及分散大颗粒的作用,而且由于粗滤网122的孔径较大,所以不易产生架桥现象,在提高良品率的同时,提高了生产时的稳定性。这里的架桥现象指的是由于粉体与滤网摩擦系数太大、粉体之间的内摩擦系数太大、滤网的锥角太大等因素导致粉体在滤网处形成一个拱形的料塞,导致电池浆料穿过滤网时不均甚至中断。
28.在具体实施例中,如图1-3所示,杂质清除机构1还包括第二连接管13以及第二吸附组件14。第二吸附组件14与第一吸附组件11结构一致,第二连接管13一端与粗滤网122连通,另一端与第二吸附组件的入料口141连通,以使经由粗滤网122过滤后的电池浆料流动至第二吸附组件14。
29.本实施例采用两个吸附组件(第一吸附组件11、第二吸附组件14)对磁性金属杂质进行吸附,以提高电池浆料中的磁性金属杂质的清除率,进一步地提高电池的良品率。
30.在具体实施例中,如图1-3所示,杂质清除机构1还包括精滤网组件15,精滤网组件15包括:第三连接管151以及精滤网152。第三连接管151一端与粗滤网122连通,另一端与精滤网152连通,以使经由第二吸附组件14过吸附的电池浆料流动至精滤网152。
31.具体地,精滤网152可以进一步降低电池浆料的流速,从而延长电池浆料流经磁场的时间,使电池浆料中的磁性金属杂质有足够时间迁移到磁性件112表面,进一步地提高了电池浆料中的磁性金属杂质的清除率,使电池的良品率得到进一步地提升。
32.由于本实施例的电池浆料在通过精滤网152之前,已经被粗滤网122滤过,所以已经有部分团聚的颗粒被过滤或打散,因此不易在精滤网152处产生架桥现象,且精滤网152可以进一步地分散团聚的颗粒,进一步地提高良品率。
33.上述实施例的粗滤网122与精滤网152具体都是使用桶型的滤网,当然,可以理解的是,也可以使用片状的滤网或其它类型的滤网,本实用新型在此不做限定,本领域技术人员可以对此进行适应性调整。
34.在一实施例中,如图1-3所示,粗滤网122的目数大于等于80且小于等于170,精滤网152的目数比粗滤网122大30至70。目数的选择主要取决于电池浆料的粒度,以下列举几个实施例以供参考。
35.实施例一:粗滤网122的目数为100,精滤网152的目数为150。这一实施例适用于粒度≤100μm的电池浆料。
36.实施例二:粗滤网122的目数为150,精滤网152的目数为200。这一实施例适用于粒度≤75μm的电池浆料。
37.实施例三:粗滤网122的目数为80,精滤网152的目数为110。这一实施例适用于粒度≤130μm的电池浆料。
38.实施例四:粗滤网122的目数为150,精滤网152的目数为240。这一实施例适用于粒度≤55μm的电池浆料。
39.当然,可以理解的是,本领域技术人员可以根据电池浆料的粒度进行适应性调整,只要粗滤网122与精滤网152目数符合上述约束即可。
40.在具体实施例中,如图1-3所示,杂质清除机构1还包括第四连接管16以及第三吸附组件17。第三吸附组件17与第二吸附组件14结构一致,第四连接管16一端与精滤网152连通,另一端与第三吸附组件的入料口171连通,以使经由精滤网152过滤后的电池浆料流动至第三吸附组件17。
41.本实施例采用三个吸附组件(第一吸附组件11、第二吸附组件14、第三吸附组件17)对磁性金属杂质进行吸附,以提高电池浆料中的磁性金属杂质的清除率,更进一步地提高电池的良品率。本实施例中,电池浆料进入杂质清除机构1时,会先经由第一吸附组件11清除掉部分磁性金属杂质,随后经由粗滤网122将电池浆料中团聚的粉体过滤出来或分散开,随后经由第二吸附组件14对电池浆料进行第二次吸附,进一步清除掉部分磁性金属杂质,随后经由精滤网152进一步地将电池浆料中团聚的粉体过滤出来或分散开,最后经由第三吸附组件17对电池浆料进行第三次吸附。
42.在一实施例中,磁性件112与内腔的腔壁1114之间的距离小于25mm。
43.具体地,磁性件112与内腔的腔壁1114之间的距离与电池浆料于流道1113中的流通速度呈正比,与电池浆料中的磁性金属杂质的清除率呈反比。由于流通速度与生产效率呈正比,磁性金属杂质的清除率与良品率呈正比,由此可见磁性件112与内腔的腔壁1114之间的距离对生产效率与良品率能起到决定性作用。为了兼顾生产效率与良品率,研发人员绞尽脑汁进行了多次计算与分析后,得出磁性件112与内腔的腔壁1114之间的距离在小于25mm时,能较好地权衡流通速度与磁性金属杂质的清除率。
44.在一实施例中,磁性件112为磁棒,壳体111呈圆桶状。其中,磁棒的直径为35mm至115mm,壳体111的直径比磁棒的直径大10mm至30cm。
45.具体地,磁棒的直径越大,磁性金属杂质的清除率就越高,但成本也越高。为了权衡磁性金属杂质的清除率以及磁棒的成本,本实施例将磁棒的直径限制在35mm至115mm,壳体111的直径比磁棒的直径大10mm至30cm。当电池浆料的流量较小时,可以采用直径小的磁
棒,当电池浆料的流量较大时,可以采用直径大的磁棒。以下列举几个实施例以供参考。
46.实施例一:磁棒的直径为50mm,壳体111的直径为70mm。这一实施例适用于电池浆料的流量≥50l/min的情况。
47.实施例二:磁棒的直径为100mm,壳体111的直径为120mm。这一实施例适用于电池浆料的流量≥100l/min的情况。
48.实施例三:磁棒的直径为35mm,壳体111的直径为45mm。这一实施例适用于电池浆料的流量≥25l/min的情况。
49.实施例四:磁棒的直径为115mm,壳体111的直径为145mm。这一实施例适用于电池浆料的流量≥130l/min的情况。
50.当然,可以理解的是,本领域技术人员可以根据电池浆料的流量进行适应性调整,只要磁棒的直径符合上述约束即可。
51.本实用新型实施例展示了一种杂质清除机构1,如图1-3所示,通过在壳体111上开设有入料口1111以及出料口1112,使得电池浆料能经由入料口1111流入壳体111内腔形成的流道1113处,随后经由出料口1112流出流道1113,由于流道1113处设置有磁性件112,所以能吸附电池浆料中的磁性金属杂质,其中,电池浆料在流道1113中是沿第一方向流动的,磁性件112沿第一方向设置于流道1113中,所以电池浆料的流向是与磁性件112的长度方向平行的,这种结构能最大程度地延长电池浆料流经磁场的时间,使电池浆料中的磁性金属杂质有足够时间迁移到磁性件112表面,因此电池浆料中的磁性金属杂质的清除率较高,进而使电池的良品率得到显著的提升。
52.本实用新型还提供了一种杂质清除系统,如图1-3所示。杂质清除系统包括两个杂质清除机构1、分流管2以及供料泵3。杂质清除机构1为上述实施例的杂质清除机构1。分流管2具有两个输出口(图中未示出)以及一个输入口(图中未示出),两个输出口分别连接两个第一吸附组件11的入料口1111,供料泵3与输入口连通,供料泵3用于抽取电池浆料,并将电池浆料输入至输入口。
53.具体地,供料泵3可以用隔膜泵、螺杆泵或其它供料泵3,本实用新型在此不做限定,本领域技术人员可以对此进行适应性调整。
54.通过实施本实施例,可以最大程度地延长电池浆料流经磁场的时间,使电池浆料中的磁性金属杂质有足够时间迁移到磁性件112表面,因此电池浆料中的磁性金属杂质的清除率较高,进而使电池的良品率得到显著的提升,并且本实施例只需使用一个供料泵3,即可为两个杂质清除机构1提供电池浆料,提高了供料泵3的工作效率,降低了生产成本。
55.在一实施例中,如图1-3所示,杂质清除系统还包括防护罩4与第五连接管5。防护罩4罩设于供料泵3,防护罩4上开设有通孔(图中未示出)。第五连接管5穿设于通孔,且第五连接管5一端与分流管2的输入口连通,另一端与供料泵3连通。
56.本实施例中,供料泵3抽取的电池浆料经由第五连接管5输入至分流管2。防护罩4罩设于供料泵3,当电池浆料意外泄漏时,防护罩4可以起到防护作用。
57.在一实施例中,如图1-3所示,杂质清除系统还包括承载车6,承载车6包括承载板61与车轮62。杂质清除机构1与供料泵3均装设于承载板61上,车轮62装设于承载板61底部。
58.具体地,将杂质清除机构1与供料泵3装在承载车6上。需要对杂质清除系统进行清洗时,可以将杂质清除系统整体运离出生产现场,而不影响生产环境管控。
59.在一实施例中,如图1-3所示,第五连接管5上还安装有压力表7,压力表7可以测量第五连接管5内部的压力,从而在压力表7上反馈杂质清除机构1的运行状态。
60.应当理解的是,以上实施例仅用以说明本实用新型的技术方案,而非对其限制,对本领域技术人员来说,可以对上述实施例所记载的技术方案进行修改,或者对其中部分技术特征进行等同替换;而所有这些修改和替换,都应属于本实用新型所附权利要的保护范围。