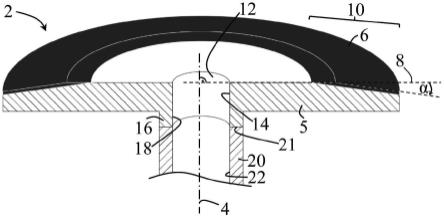
具有集成式液态金属轴承外壳的旋转x射线阳极
技术领域
1.本发明涉及一种根据权利要求1的前序部分的具有集成式液态金属轴承外壳的旋转x射线阳极,涉及一种具有旋转x射线阳极的旋转x射线阳极系统,所述旋转x射线阳极具有集成式液态金属轴承外壳和插入其中的液态金属轴承内壳,并且还涉及一种用于这样的旋转x射线阳极的制造方法。
背景技术:2.旋转x射线阳极用于x射线管中以产生x射线。在使用中,电子从x射线管的阴极发射,并以聚焦电子束的形式加速到旋转的旋转x射线阳极上。由于旋转x射线阳极的旋转运动,电子束扫描环形轨迹,即焦点轨迹。来自电子束的大部分能量在旋转x射线阳极中被转换为热量,而小部分作为x辐射被发射。局部释放的热量导致旋转x射线阳极的显著加热。旋转x射线阳极的旋转抵消了阳极材料的过热。
3.尤其是在高性能领域,需要高辐射功率(或剂量功率),其可以通过使用相应的高能量和高聚焦的电子束来产生。为了避免由于高温和温度梯度引起的材料疲劳,旋转x射线阳极必须被设计用于高频旋转和用于有效且均匀的热耗散。关于这些要求,使用液态金属轴承来安装旋转x射线阳极是有利的。
4.us2016/0086760a1和us2017/0125199a1各自公开了一种旋转x射线阳极系统,其中将承载液态金属的外壳作为插入物插入到旋转x射线阳极的中心通道孔中。us2016/0086760a1还公开了一种使用引入到焊接区中的中间部件的摩擦焊接方法。从公开us5,204,890a和us6198805b1中已知另外的旋转x射线阳极系统。
技术实现要素:5.本发明的目的是在高旋转频率下的良好安装和均匀且有效的散热方面改进旋转x射线阳极。此外,能够以稳定的过程廉价地制造旋转x射线阳极。
6.该目的通过如权利要求1所述的旋转x射线阳极、如权利要求10所述的旋转x射线阳极系统以及如权利要求15所述的制造旋转x射线阳极的方法来实现。本发明的有利改进在从属权利要求中说明。
7.根据本发明,提供了一种具有集成式液态金属轴承外壳的旋转x射线阳极。该旋转x射线阳极具有由mo(mo:钼)或mo基合金制成的阳极盘,并且具有在旋转轴线的区域中的中心形成的并且在轴向方向上至少延伸穿过阳极盘的一部分的孔,以及由mo或mo基合金制成的衬套。衬套的内壁至少在其轴向部段上周向地(即,在基于旋转轴线的周向方向上)形成为液态金属轴承运行表面,并且形成液态金属轴承外壳的第一子部段。更特别地,衬套的整个(通常为圆筒形)内壁可采用液态金属轴承运行表面的形式。可替代地,也可以仅仅将衬套的内壁的轴向部段构造成液态金属轴承运行表面,该轴向部段于是同样典型地构造成圆筒形的,而另一轴向部段例如也可以具有机械的边界元件和/或涂层,液态金属在使用时通过该边界元件和/或涂层保持在液态金属轴承中。液态金属轴承外壳由第一和相邻的第二
子部段形成,并具有连续的液态金属轴承运行表面。在此,衬套通过材料结合以如下方式连接到阳极盘,即衬套的内壁延续阳极盘中的孔。此外,阳极盘中的孔的内壁的至少一个轴向部段周向地(即,在基于旋转轴线的周向方向上)形成为液态金属轴承运行表面,并且形成液态金属轴承外壳的第二子部段的至少一部分。这里,孔的整个(通常为圆筒形)内壁也可以周向地形成为液态金属轴承运行表面。在盲孔的情况下,可选地,孔的底部也可以形成液态金属轴承运行表面。可替代地,也可以仅将孔的内壁的轴向部段周向地形成为液态金属轴承运行表面,该轴向部段于是同样典型地为圆筒形。
8.在液态金属轴承中,在彼此匹配的液态金属轴承外壳和液态金属轴承内壳之间形成限定的轴承间隙,并且液态金属轴承外壳和液态金属轴承内壳中的一个形成在固定部件上,而液态金属轴承内壳中的另一个形成在旋转部件上。在当前情况下,液态金属轴承外壳与旋转x射线阳极一体地形成,并且因此作为旋转部件。液态金属轴承内壳可以例如一体地形成在插入液态金属轴承外壳中的套管(固定部件)上。在使用中,轴承间隙填充有液态金属(例如镓、镓合金,例如共晶镓-铟-锡合金等)。间隙宽度通常从几微米到500μm(至少≤1mm);尤其是5-500μm,优选地7-40μm,其中间隙宽度也可以在轴承间隙的长度上变化。特别地,还可以在液态金属轴承外壳和/或内壳中设置至少一个周向切口和/或台阶或脊,在其区域中,间隙宽度也可以形成为不同于轴承间隙的其余部分(例如,参见de102015215306a1)。更特别地,至少一个周向脊可设置在一个部件上,而(至少)相应地形成的凹槽设置在另一部件上,用于在轴向方向上相对于彼此固定该两个部件。液态金属轴承运行表面指的是液态金属轴承外壳和液态金属轴承内壳的部段,其在使用中在液态金属轴承外壳和液态金属轴承内壳上都被液态金属润湿,因此能够实现低摩擦旋转。液态金属防止液态金属轴承外壳和液态金属轴承内壳之间的直接接触,同时用作润滑剂,这实现了优异的运行特性。为了驱动旋转x射线阳极,液态金属轴承外壳设置有转子或(机械地)联接到转子,该转子被设置成以已知的方式与定子相互作用而旋转。
9.使用液态金属轴承来安装旋转x射线阳极是有利的,因为液态金属轴承被设计用于高负载和高旋转频率,并且同时具有高操作可靠性和长寿命。一个优点(例如,相对于球轴承)是,在轴承间隙中存在的液态金属的升高的压力形成在该区域的更大部段上(尤其是在轴向范围内),因此增加了机械稳定性。更特别地,在液态金属轴承的情况下,高达300hz(赫兹)的旋转频率是可能的,而球轴承例如通常被设计用于远低于200hz(例如140hz)的旋转频率。此外,与球轴承相比,液态金属轴承具有低噪音水平,并且由于增加的接触面积(通过液态金属填充的轴承间隙),能够在大面积上有效地散热。这样,热量可以有效地消散到固定部件(例如,消散到在内侧上插入到液态金属轴承外壳中的套管)。然后,热量又可以经由内侧上的冷却(借助于在至少一个冷却管道内传导的冷却剂)从固定部件有效地移除,使得热管理是非常有效的,并且因此适合于高性能领域。相反,由于使用热敏涂层,球轴承不是设计用于通过轴承有效散热,因为这会导致相应涂层的损坏。
10.mo或mo基合金作为用于阳极盘和用于衬套的材料是特别有利的,因为它们具有高强度(甚至在高使用温度下)并且能够实现良好的散热。此外,mo或mo基合金对通常使用的液态金属具有良好的润湿性。因此,衬套的内壁和阳极盘中的孔的内壁形成为液态金属轴承运行表面也是有利的,因为即使基材也因此产生良好的润湿性。可选地,可以在衬套的内壁上和/或在孔的内壁上提供涂层(厚度通常小于10μm),在所有情况下完全地或仅按部段
提供。然而,没有提供在内部具有液态金属轴承外壳的单独的插入件,该外壳将必须插入到阳极盘中的孔中并结合到其上,这将在制造方面更加复杂并且可能构成对散热的屏障。此外,在阳极盘和液态金属轴承外壳之间实现了高的机械稳定性,这对于运行特性是有利的。由于衬套的内壁延续阳极盘中孔的内壁,并且因此提供具有相应长的轴向范围的液态金属轴承运行表面,这确保了在阳极盘旋转时的机械稳定和精确的引导。
11.在本文中,mo基合金是指含有>50重量%mo的合金。特别是,它含有≥80重量%的mo,更优选≥98重量%,这对于mo的上述特性是特别有利的。这里的阳极盘和衬套不必完全由mo或mo基合金形成;而是,这里特别提到的是基材。特别地,它们可以设置有涂层(例如,用于增加所发出的热输出的黑化层)、配合部件,例如作为热存储装置固定在阳极盘上的c基体(例如,石墨体)、安装在衬套上的凸缘等,或者涂层,例如施加在焦点轨迹区域中的圆周焦点轨迹涂层。如开头所阐述的,“焦点轨迹”在这里是指阳极盘的圆周部段,其形成围绕旋转轴线的环,该环在使用中由电子束扫描。通常,在焦点轨迹的区域中(具有一定的径向范围),焦点轨迹涂层被施加到阳极盘。焦点轨迹涂层尤其由w或具有1-15重量%,尤其是5-10重量%的re含量的w-re合金(w:钨;re:铼)形成。此外,阳极盘在焦点轨迹的区域中通常具有成角度的焦点轨迹表面,其优选地形成圆周截头圆锥形的壳表面。更特别地,焦点轨迹表面相对于与旋转轴线成直角延伸的参考平面成角度,这使得所生成的x辐射能够通过相应x射线设备中的横向出射窗离开。例如,其相对于该参考平面形成在2
°‑
16.25
°
的范围内,尤其是在7
°‑
13
°
的范围内的焦点轨迹角。
12.所指的“旋转轴线”由旋转x射线阳极和液态金属轴承外壳的旋转对称基本形状限定。旋转轴线同时限定“轴向方向”(其平行于该轴线延伸)和“径向方向”(其与该轴线成直角延伸)。旋转x射线阳极的“参考平面”(其通常同时形成其主延伸平面)尤其垂直于旋转轴线延伸。应当注意,旋转x射线阳极不需要在每个细节中都精确地旋转对称,使得例如在周向方向上形成的狭缝、突起、凹陷、配合部件等的周期性布置可以破坏精确的旋转对称。衬套是指具有(通道)孔的部件,在本上下文中,其内壁至少部分地形成为液态金属轴承运行表面,其中衬套可具有不同的轮廓(尤其是外形)和配合部件。在优选的变型中,衬套(以及相应地,旋转x射线阳极的机械安装)被设置在阳极盘的与焦点轨迹相对的一侧上。可替代地,衬套(以及相应地旋转x射线阳极的机械安装)也可以被设置在阳极盘的其上提供有焦点轨迹的一侧上。
13.根据本发明,液态金属轴承外壳的第一子部段与衬套一体形成,并且液态金属轴承外壳的第二子部段的至少一部分与阳极盘一体形成。这里“整体”的意思是,所讨论的部件通过冶金制造(优选地通过粉末冶金或可替代地通过熔融冶金)以单件制造,具有随后的机械加工的可能性,例如用于引入孔和/或表面结构化,和/或随后施加至少一个层。从(由mo或mo基合金组成的基材的)均匀且恒定的显微组织,一体形成对于本领域技术人员是明显的。优选通过粉末冶金制造阳极盘和/或衬套,其中这包括压制和烧结相应的起始粉末的步骤,并且优选随后形成(例如轧制、锻造、挤出等)所得成形体。通过粉末冶金的制造导致对于本领域技术人员来说是明显的典型微结构,其例如与熔体微结构(在通过熔体冶金的制造中获得)明显不同。因此,衬套的内壁至少在液态金属轴承运行表面的区域中由衬套的基材(mo或mo基合金)形成,并且阳极盘中的孔的内壁至少在液态金属轴承运行表面的区域中由阳极盘的基材(mo或mo基合金)形成。在衬套的内壁和/或在阳极盘中的孔的内壁处,还
可以提供涂层(厚度通常小于10μm)和/或表面结构。
14.材料结合连接应理解为是指产生连续的材料结合,但不是指仅存在机械连接(例如,经由螺钉或夹具连接、经由机械固定元件等)。更特别地,衬套和阳极盘的材料结合连接通过焊接、通过钎焊或通过扩散连接(扩散结合)来建立。如果通过显微镜在截面上检查结合区,则焊接结合对于本领域技术人员而言是明显的,其通过相应的焊接区(熔融的或至少塑化的基材)、通过相应的钎焊区的焊料结合(焊料的熔融结构)和通过相应的扩散区的扩散结合(相互结合的基材的扩散区)。
15.从成形、尤其是从相对于旋转轴线以旋转对称方式形成在内侧上的液态金属轴承运行表面,以及从使得能够引入具有相应液态金属轴承内壳的套管(或其它类型的部件)的内轮廓,形成为液态金属轴承外壳对于本领域技术人员是明显的。此外,在内轮廓上没有设置用于球轴承的运行凹槽(即使液态金属轴承运行表面原则上可以是逐渐变化的和/或设置有脊或切口)。可选地,在液态金属轴承外壳和/或液态金属轴承内壳的端部部段的区域中设置有表面结构、涂层和/或机械边界元件,用于将液态金属保持在液态金属轴承的区域中。
16.在一种改进中,材料结合连接是经由扩散结合、摩擦焊接结合或束焊接结合(通过激光或电子束)建立的结合。所提及的结合技术的优点在于,即使在高的使用温度下,也可以利用其以实现具有高强度的材料结合连接。更特别地,在结合区的区域中,可以省去任何添加的材料(例如焊料、填充材料等),其可以在液态金属轴承的区域中形成麻烦的杂质(例如在液态金属中),对于真空稳定性(在高真空下使用)可能是关键的,和/或可以具有较低的熔点(与结合的部件的基材相比)。与焊料通常具有比(结合部件的)基材低的熔点并且至少在高温下具有比(结合部件的)基体材料低的强度的焊料结合相比,这是特别有利的。
17.在扩散结合的情况下,待接合的部件的(通常适当制备的)表面被组装,并且通过施加压力和温度引起原子在结合区的区域中的扩散,以产生材料结合连接(扩散结合)。根据对在此形成基础的扩散结合的(较窄的)理解,在结合区的区域中不发生待结合的部件的基材的熔化。如上所述,通过显微切片中的结合区的显微镜分析,扩散结合对于本领域技术人员来说是显而易见的,其中来自相应的扩散区(相互结合的基材的扩散区域)的相应的扩散区中没有熔融微结构出现。如果由相同材料制成的部件通过扩散结合彼此结合,则扩散结合在显微镜切片中可能不明显,因为在结合区的区域中可以实现相对于特定基材恒定的均匀微结构。在这些情况下,扩散结合的存在则可仅从所结合的部件(在本情况下为阳极盘和衬套)的向外几何形状得到,例如因为它们不能以相应的整体形状以单件形式(例如通过粉末冶金)制造。通过显微切片中的结合区的显微镜分析、其中出现(基材的以及可能还另外使用的填充材料的)相应的熔融微结构的焊接区的显微镜分析、以及熔融区的根部和位置,束焊接结合对于本领域技术人员是显而易见的。由于热影响区小,所以束焊接结合(尤其是通过电子束焊接)是有利的。此外,与纯钼相比,该束焊接方法更适用于mo基合金。
18.在摩擦焊接的情况下,部件相对于待结合的另一部件移动并与其接触(例如旋转),以在邻接表面处产生热量。通过在相对运动(例如旋转运动)停止期间或之后施加力来完成焊接,存在多种形式的能量供应和相对运动。在当前情况下,结合位于很大程度上旋转对称的部件之间,并且因此一个部件(例如衬套或短柱)被设置为旋转,然后与另一部件(例如阳极盘)接触,以产生摩擦热。摩擦焊接也能够实现较高壁厚(尤其是20-130mm)的部件的
结合,其仅在接合横截面中导致相对低的接合温度,因此在许多情况下适用于否则必须困难地焊接的材料和材料组合(在这方面也参见dineniso15620)。这对于纯mo以及mo基合金尤其如此。通过显微切片中的结合区的显微镜分析,借助于典型的微观结构,摩擦焊接结合对于本领域技术人员是明显的。更特别地,由于在摩擦焊接过程中基材仅仅被置于塑化状态,因此没有明显的熔融微结构。通常,焊接区相对较窄并且具有细粒显微组织。具体地,在衬套和阳极盘的摩擦焊接结合的情况下,在焊接区的区域中明显存在具有略微不同微观结构的多个焊接区(在衬套的基材和阳极盘之间),其中衬套和阳极盘中的每一个由mo和/或mo基合金形成。更具体地说,本发明涉及晶粒尺寸分布和晶粒排列。通常,晶粒在材料流的方向上延伸,这尤其在形成焊道时发生。尤其是在衬套具有高的晶粒延伸度并且阳极盘具有较低的晶粒延伸度时,出现不同晶粒延伸度的区域(在衬套附近具有高的晶粒延伸度并且在阳极盘附近具有较低的晶粒延伸度),这在这些部件中通过其相应的制造方法得到证明。此外,摩擦焊接结合的宏观指示是何时在阳极盘上使用突出连接端口以便能够在摩擦焊接期间形成焊道(由于压缩阶段期间的材料流动)。这尤其从连接端口和与阳极盘间隔开的衬套之间的焊接区是明显的。
19.在一种改进中,(阳极盘和/或衬套的)mo基合金是mhc和/或tzm。更特别地,衬套的基材(即除了涂层、装配部件等之外)由mhc和/或tzm(优选仅由mhc或仅由tzm)制成。更特别地,阳极盘的基材(即除了涂层、装配部件等之外)由mhc和/或tzm(优选仅由mhc或仅由tzm)制成。两种合金(mhc,tzm)都具有高强度和硬度。它们的机械性能在高温下基本上保持不变,这使得在制造中能够有更高的工艺温度,并且也使得旋转x射线阳极的使用温度更高。对于温度高达1250℃的mhc和对于温度高达1100℃的tzm,这是特别正确的。因此mhc对于高性能领域和高使用温度具有特别好的适用性。
20.mhc是由申请人普兰西股份有限公司提供的mo基合金,具有以下组成:
[0021]-hf含量为1.00-1.30重量%,
[0022]-c含量为500-1200μg/g(μg:微克),
[0023]-余量:mo(通常≥97.0重量%,优选≥98.0重量%,其中具有相应低杂质比例的mo含量甚至可以≥98.5重量%)。
[0024]
tzm是在标准astmb387(364)中规定的并且由申请人普兰西股份有限公司提供的mo基合金,其具有用于本技术的以下组成:
[0025]-ti含量为0.40-0.55重量%,
[0026]-zr含量为0.06~0.12重量%,
[0027]-c含量为50-500μg/g,其中该范围(其特别地对于旋转x射线阳极的应用领域具有非常好的适合性)比标准astmb387
[0028]
(364)中规定的100-400μg/g范围稍宽,
[0029]-余量:mo(通常≥98.0重量%,优选≥99.0重量%,其中具有相应低杂质比例的mo含量甚至可以≥99.3重量%)。
[0030]
可能存在的任何杂质的可能/容许含量通常不是针对所有元素而规定的,而是特别针对通常存在的和/或对于其而言过高含量对于合金的有利性质而言将是关键的那些元素而规定的。在该背景下,以下容许范围的杂质是特别有利的:特别是,mhc和tzm中的金属杂质的含量总计≤5000μg/g。特别是在mhc和tzm的情况下,根据普兰西股份有限公司的特
别有利的规范,al(铝)和ni(镍)中的每一种的含量≤10μg/g,cr(铬)、cu(铜)、fe(铁)、k(钾)和si(硅)中的每一种的含量≤20μg/g,w(钨)的含量≤300μg/g,cd(镉)和pb(铅)中的每一种的含量≤5μg/g,并且hg(汞)的含量≤1μg/g。mhc和tzm中可能存在的任何h(氢)、n(氮)和o(氧)杂质的含量总计≤1000μg/g。尤其是在根据普兰西股份有限公司规范的mhc中,h和n中的每一种的含量≤10μg/g,并且o的含量≤600μg/g。tzm中可能存在的任何h、n、o和c(碳)杂质的含量总计≤1500μg/g。特别是在根据普兰西股份有限公司规范的tzm的情况下,h和n中的每一种的含量≤10μg/g,并且o的含量≤500μg/g。根据制造工艺的不同,cr(vi)杂质和有机杂质是可能的且可接受的,最大值≤1000μg/g;它们通常在普兰西股份有限公司提供的合金中检测不到。mhc和tzm的所有杂质的总和s最好尽可能在0≤s≤6000μg/g的范围内,w(钨)作为典型的杂质,优选比例≤300μg/g。
[0031]
原则上,阳极盘和衬套可以由不同的材料制成。在一种改进中,阳极盘和衬套都由钼或相同的钼基合金形成。由于两个部件(例如都由mhc制成,或者都由tzm制成)的相同材料特性,这对于材料结合连接(尤其是在摩擦焊接结合或束焊接结合的情况下)是特别有利的。如本领域技术人员所清楚的,钼基合金被认为是相同的,即使在组成上存在微小的差别。特别是当两种成分在所讨论的mo基合金的规范范围内时(例如对于上面规定的tzm或mhc),仅存在“轻微差异”。如果没有对所讨论的合金的规范,即使当mo含量的差异≤2重量%时,通常也仅仅存在“轻微差异”,非金属合金成分(例如c、n)的差异总计≤0.2重量%,任何存在的金属合金成分的差异总计≤1重量%,w的差异≤0.05重量%(对于杂质,上面针对tzm和mhc规定的范围是特别适用的)。
[0032]
在一种改进中,材料结合连接是摩擦焊接结合。这对于实现粘合的高强度和热稳定性是有利的。此外,在摩擦焊接技术中,存在高再现性和高水平的自动化。在摩擦焊接的情况下,优选地省去任何添加的材料(例如填充材料、引入待结合的部件之间的插入件等),这意味着除了结合部件的基材之外基本上没有外来材料,并且在材料结合连接的区域中基本上没有可检测的不同组成。在摩擦焊接的情况下,mo基合金优于纯mo。甚至更优选地,两个部件(阳极盘、衬套)由相同的mo基合金形成(例如,两者都由mhc形成,两者都由tzm形成,等等),因为这样可以实现特别高的摩擦焊接结合的稳定性和质量。关于摩擦焊接(例如与束焊方法相比)的特别有利之处在于,在结合区中不形成熔融物;相反,待结合的部件的基材仅仅是塑化的。这在结合区的区域中建立了有利的微结构,并且保持了存在的元素/化合物的均匀分布(例如在mo基合金中)。
[0033]
在一种改进中,阳极盘朝向衬套的一侧具有连接端口,该连接端口的内壁延伸阳极盘中的孔,并且该连接端口相对于阳极盘外侧上的周缘面突出。连接端口的内壁的至少一个轴向部段在此周向地形成为液态金属轴承运行表面,并且形成(以及阳极盘中的孔的内壁和任何另外的部段)液态金属轴承外壳的第二子部段的一部分。此外,在阳极盘的突出连接端口与衬套之间形成材料结合连接。通过突出连接端口,其尤其可以具有管状或空心圆筒形的基本形式,可以更容易地建立阳极盘和衬套之间的材料结合。这在摩擦焊接结合的情况下(但也在束焊接结合的情况下)尤其如此,因为这基本上提供了待彼此结合的两个相同部段(尤其是具有周向壁和环形端面)。因此,材料结合连接也与阳极盘外侧上的周缘面间隔开例如2-50mm,优选地5-30mm(适用于完成的材料结合的范围)。这为形成焊道创造了足够的空间,尤其是在摩擦焊接结合的情况下,焊道在压缩阶段期间通过材料的流动形
成(焊道随后通过进一步处理被去除)。由于在摩擦焊接期间实现压缩,所以应选择连接端口的初始轴向长度(在建立材料结合之前),尤其是当采用摩擦焊接工艺时,以便比材料结合的稍后期望位置长,例如长3-8mm。连接端口优选地与阳极盘整体地形成,这在稳定性和运行特性方面是有利的。优选地,连接端口在锻造工艺中由阳极盘的材料整体地形成。可替代地,其也可以材料结合到阳极盘。
[0034]
在一种改进中,阳极盘中的孔具有通孔的形式,并且阳极盘在与衬套相对的一侧上具有延伸端口,该延伸端口的内壁延伸阳极盘的通孔,并且该延伸端口相对于阳极盘外侧上的周缘面突出。延伸端口的内壁的至少一个轴向部段在此周向地形成为液态金属轴承运行表面,并且形成(除了阳极盘中的孔的内壁之外,可选地形成连接端口和任何另外的部段)液态金属轴承外壳的第二子部段的一部分。提供这种延伸端口对于液态金属轴承外壳的稳定性和运行特性是有利的(尤其是因为液态金属轴承运行表面的延伸部分然后设置在阳极盘的任一侧上)。以与连接端口的情况相对应的方式,延伸端口优选地与阳极盘整体地形成(例如通过锻造形成)或者可替代地材料结合到阳极盘也是可能的。优选地,延伸端口和存在的任何其它部件然后形成液态金属轴承外壳的结论。可替代地,取决于液态金属轴承的构造,也可以使另一个轴承材料结合到延伸端口,并且因此使液态金属轴承外壳更进一步延伸,并且在此针对连接端口到衬套的结合所描述的变型同样是可能的。
[0035]
在一种改进中,阳极盘的厚度(在轴向方向上测量)在朝向旋转轴线的径向方向上增加。这种厚度的增加可以是连续的(具有恒定的斜率或者具有变化的厚度分布)或处于一个或多个级。因此,在焦点轨迹的区域中产生的热量可以在逐渐增大的材料横截面上朝着旋转轴线被分开,并且然后在液态金属轴承外壳的大的区域上被有效地移除(通过设置在轴承间隙中的液态金属,并且然后通过液态金属轴承内壳和邻接的部件,例如通过具有冷却剂冷却的套管)。材料横截面在径向向内方向上的这种增加避免了在液态金属轴承的区域中局部出现的温度尖峰和过高的温度,所述温度尖峰和过高的温度可能导致对液态金属轴承的损坏和阳极盘中的应力。在一种改进中,从在倾斜的焦点轨迹区域的中间径向测量的参考厚度开始直至在孔的区域中的厚度增加为30-300%,尤其是50-260%,甚至更优选70-230%(100%的厚度增加对应于厚度的加倍)。这对于热量消散以及液态金属轴承外壳的稳定性和运行特性是特别有利的。“孔区域中的厚度”指的是直接在孔内壁区域中的阳极盘的厚度,并且该厚度测量还包括与阳极盘整体地形成的任何部段,例如整体连接端口和/或整体延伸端口,而不是仅材料结合到阳极盘的部件(例如衬套)。然而,优选地,阳极盘在径向向内方向上厚度增加,而不包括任何整体连接端口和/或延伸端口。特别地,在提供这种整体式连接端口和/或延伸端口的情况下,使用直接(径向)在连接端口和/或延伸端口外部的参考区域而不是“孔的区域”,后者的厚度增加为20-150%,优选地30-100%。
[0036]
在一种改进中,阳极盘具有多个狭缝,这些狭缝均匀地布置在圆周上并且穿过阳极盘的厚度,这些缝隙中的每一个在阳极盘的外圆周与阳极盘中的孔之间的区域中的径向部段上延伸。在出现的高温下使用时,这种狭缝能够使阳极盘的材料膨胀而其没有塑性变形,这避免了材料内的应力,并因此避免了材料疲劳或材料失效。这种狭缝在此可以精确地径向延伸。可替代地,它们也可以相对于径向方向稍微倾斜地延伸(例如,以》0
°
直到5
°
的角度)。关于径向方向的走向、关于轴向方向的走向(这里也是如此,它们可以相对于轴向方向略微倾斜地延伸,例如倾斜1
°‑
10
°
范围内的角度),和/或狭缝的宽度可以根据限定的轮廓
而变化。此外,在狭缝的至少一端(优选在径向内端),也可以提供优选延伸穿过阳极盘厚度的终止孔,并且每个终止孔的直径大于开口狭缝和/或周向槽的宽度。优选地,狭缝一直延伸到外圆周,即,通向外圆周,同时它们在阳极盘中的孔的径向外侧终止。优选地,所有的狭缝相对于旋转轴线相对于彼此对称地形成。提供这种狭缝是有利的,尤其是当阳极盘的厚度朝向旋转轴线增加时。
[0037]
本发明还涉及一种旋转x射线阳极系统,其包括具有集成式液态金属轴承外壳的本发明的旋转x射线阳极,其也可以可选地根据一个或多个上述改进形成,以及液态金属轴承内壳,其已经被插入到液态金属轴承外壳中并且具有液态金属轴承运行表面,其中,液态金属轴承外壳和液态金属轴承内壳彼此匹配,使得在它们之间形成限定的轴承间隙(间隙宽度,尤其如上所述)。
[0038]
在一种改进中,在液态金属轴承外壳上的液态金属轴承运行表面和/或液态金属轴承内壳上的液态金属轴承运行表面的至少一个轴向端部部段(轴向:基于旋转轴线)的区域中设有至少一个周向的机械的边界元件,该边界元件在使用时限制存在于轴承间隙中的液态金属在轴向方向上的流动。机械边界元件因此用于将液态金属保持在液态金属轴承的(轴向)内部区域中,在该区域中需要实现润滑效果。机械边界元件可以特别地由以下变型中的一个或多个形成:
[0039]-由多级形成的轴承间隙的延续,用于形成迷宫式密封(例如,参见jp2012/084400a);
[0040]-在液态金属轴承的一个(例如固定的、内部的)部件上的一个或多个周向(恒定的或者沿周向方向被短的部段中断的)脊和在液态金属轴承的另一个(例如旋转的、外部的)部件上的相应的凹槽,由此还同时提供液态金属轴承的轴向固定;在多个脊的情况下,这些脊也可以交替地设置在一个和盖另一个部件上;
[0041]-由与存在于轴承间隙中的液态金属相互作用的材料(例如含铁、镍和钴的合金)制成的垫环(例如,参见de102015204488a1)。
[0042]
在一种改进中,在液态金属轴承外壳上的液态金属轴承运行表面和/或在液态金属轴承内壳上的液态金属轴承运行表面的至少一个轴向端部部段的区域中设有周向涂层,该涂层在使用期间抑制在轴承间隙中液态金属的润湿。这将液态金属保持在液态金属轴承的(轴向)内部区域中,在该区域中需要实现润滑效果。合适的涂层包括氧化钛、氧化铝、氮化钛及其混合物,尤其是crn(氮化铬)、cr2n(氮化铬)、cr2o3(氧化铬(iii))、tialn(氮化钛铝)(例如参见us2017/0169984a1)。涂层可以设置在液态金属轴承内壳上和液态金属轴承外壳上。然而,如果合适,它也可以单独设置在一个壳体上(例如单独设置在液态金属轴承内壳上)。此外,它也可以设置在至少一个机械边界元件的区域中。
[0043]
在一种改进中,液态金属轴承内壳形成在被引导通过衬套至少进入阳极盘中的孔中的套管上。优选地,套管具有至少一个用于引导冷却剂的冷却剂管道。如果孔被形成为通道孔,则套管优选地同样完全延伸穿过该通道孔。在此,套管优选地由一个部件(以单件形式)形成,因为这在其稳定性和冷却剂管道的防漏方面是有利的。可替代地,其也可由以形状配合和/或材料结合方式彼此结合的多个部件形成,这在液态金属轴承的复杂构造的情况下可能是特别有利的。通过优选地在套管的长度的至少80%上延伸的至少一个冷却剂管道,可以在使用中有效地去除热量。
[0044]
在一种改进中,液态金属轴承外壳上的液态金属轴承运行表面和/或液态金属轴承内壳上的液态金属轴承运行表面具有在轴向上彼此间隔的、周向的、表面结构化的至少两个运行表面。优选地,在至少两个表面结构化的运行部段之间设置至少一个没有表面结构化的部段。在表面结构化的运行部段的区域中,液态金属在使用中在旋转部件旋转时聚集并且形成升高的压力。这实现了特别好的润滑效果。同时,实现了旋转和静止部件在径向方向上相对于彼此的固定。提供至少两个这样的运行部段还防止了旋转x射线阳极在使用中的倾斜和振动。在此特别有利的是,表面结构化的运行部段在完全设置在阳极盘内部的区域中形成或者至少与该区域重叠地形成。这里的表面结构化可以采取例如凹槽图案的形式(例如具有一个或多个子区域,每个子区域具有彼此平行延伸的凹槽)。表面结构化的运行部段原则上可以设置在液态金属轴承内壳上和外壳上。原则上,表面结构化的运行部段也可以彼此相对地形成(基于轴承间隙)。然而,优选的是,在一个部件的表面结构化的运行部段的区域中(例如在液态金属轴承内壳上),在相对的区域中的另一个部件不具有表面结构化的运行部段。
[0045]
本发明还涉及一种制造本发明的旋转x射线阳极的方法,所述旋转x射线阳极可选地也可以根据一个或多个上述改进和变型形成,其中,所述方法具有以下步骤:
[0046]
·
提供由mo或mo基合金制成的阳极盘,
[0047]
·
提供由mo或mo基合金制成的短柱,
[0048]
·
将短柱与阳极盘材料结合,使得短柱基于阳极盘的旋转轴线处于中心布置,以及
[0049]
·
机械地加工阳极盘和短柱以形成具有集成式液态金属轴承外壳的旋转x射线阳极,其中,短柱形成具有液态金属轴承运行表面的衬套,并且阳极盘具有孔,在孔中,内壁的至少一个轴向部段周向地形成为液态金属轴承运行表面。
[0050]
该方法建立了用于制造本发明的旋转x射线阳极的廉价且可靠的制造路线。此外,通过提供相应的方法步骤,在本发明的方法中,上述改进和变型也是可能的,并且实现了上述优点。
[0051]
优选地,通过粉末冶金制造来提供阳极盘和/或短柱。这尤其包括相应的起始粉末的压制和烧结,优选还包括成型(例如轧制、锻造、圆轧、圆锻等)。在材料结合之前,阳极盘中的孔和/或衬套中的通道孔可能已经被预先形成,这使得进一步的机械处理不太复杂。可替代地,它们也可在机械加工操作中精心制作(即,阳极盘和/或短柱在材料结合之前仍然不具有孔或通道孔)。材料结合优选地通过摩擦焊接实现。在材料结合之前,可以已经在阳极盘上施加了焦点轨迹涂层(例如通过在复合材料中的粉末冶金制造),但是也可以随后例如通过热喷涂(例如真空等离子体喷涂)、通过化学气相沉积(cvd:化学气相沉积)或通过物理气相沉积(pvd:物理气相沉积)来施加。在制造过程中,同样可以添加开头已经说明的其它配合部件、涂层、覆盖物等。
附图说明
[0052]
本发明的其它优点和便利从以下工作示例的描述中变得明显,参考附图。
[0053]
附图示出了:
[0054]
图1:根据第一实施例的本发明的旋转x射线阳极的横截面立体图;
[0055]
图2a、2b:图1中的旋转x射线阳极的两个横截面图,用于说明制造;
[0056]
图3:根据第二实施例的本发明的旋转x射线阳极的横截面图;
[0057]
图4:根据第三实施例的本发明的旋转x射线阳极的横截面图;
[0058]
图5:根据第四实施例的本发明的旋转x射线阳极的横截面图;
[0059]
图6:根据第五实施例的本发明的旋转x射线阳极的横截面图;
[0060]
图7:根据第六实施例的本发明的旋转x射线阳极的横截面图;
[0061]
图8:根据第七实施例的本发明的旋转x射线阳极的横截面图;以及
[0062]
图9:本发明的具有插入的套管的旋转x射线阳极系统的横截面图,示出了在横截面图上方的套管的两个变体a和b,每个变体在俯视图中示出一次并且在横截面图中示出一次。
具体实施方式
[0063]
图1-9是尺寸比没有精确再现的示意图,并且没有示出液态金属轴承外壳和液态金属轴承的轴向终端的细节。对于液态金属轴承的轴向终端,如专业领域中已知的,不同的构造是可能的,其实例包括de102015204488a1、us2016/0086760a1、us5,204,890a、jp2012/084400a和us2017/0169984a1中所示的那些。换句话说,在图1-9的图中,衬套、阳极盘和套管还可以进一步在轴向上延续,可能具有不同的级数或不同的构造,和/或还可以连接到另外的部件。
[0064]
下面参考图1和2a、2b说明本发明的旋转x射线阳极2的第一实施例。在其基本形式中,其具有由mhc制成的阳极盘5,该阳极盘以相对于旋转轴线4(轴向)旋转对称的方式形成。在阳极盘5的一侧上是具有w-re合金(w:95重量%;re:5重量%)的焦点轨迹涂层的圆周焦点轨迹6。在焦点轨迹6的区域中,阳极盘5具有周向倾斜焦点轨迹表面10,其相对于与旋转轴线4成直角延伸的参考平面8成角度(成角度α)。孔12延伸穿过阳极盘5,其内壁14形成为液态金属轴承运行表面。在焦点轨迹6的相对侧上,阳极盘具有整体形式的管状连接端口16,其通过锻造被附接并且由阳极盘5的材料制成,并且其相对于阳极盘5的外侧上的周缘面突出。其内壁18延伸阳极盘5中的孔12并且同样采取液态金属轴承运行表面的形式。同样由mhc形成的管状衬套20通过其轴向(环形)端面经由材料结合部21结合到连接端口16的相应形成的轴向(环形)端面。衬套20的内壁22周向地形成为液态金属轴承运行表面。阳极盘5、连接端口16和衬套20的液态金属轴承运行表面一起形成连续的液态金属轴承运行表面,在本情况下,该连续的液态金属轴承运行表面以外圆柱面的形式以线性方式延伸,该外圆柱面形成液态金属轴承外壳的一部分。图2a示出了仍然作为单独部件的衬套20和阳极盘5,并且图2b示出了它们在经由摩擦焊接(以及进一步的机械处理)建立材料结合21之后的最终状态。如所阐明的,沿轴向方向的摩擦焊接导致连接端口16和衬套20在连接区域的区域中的截断。
[0065]
在随后的进一步实施例的描述中,其中相同或大致相同的部件受到影响,使用相同的附图标记,并且主要解决相对于第一实施例的差异。
[0066]
在图3所示的第二实施例中,阳极盘5'的厚度(在轴向上测量)在径向向内的方向上连续增加。特别地,厚度从参考厚度dr(在倾斜焦点轨迹表面10的区域的中间径向测量)开始增加30-300%直到孔12的区域中的最大厚度d
ii
(包括整体结合到阳极盘5'的所有部
件,即在连接端口16的当前情况下)。此外,即使不包括一体地形成的连接端口16,厚度也从参考厚度dr开始在径向向内的方向上增加20-150%,在这种情况下,对于该目的至关重要的内部区域中的厚度di在连接端口16的外部直接(径向)测量。
[0067]
在图4所示的第三实施例中,与第一实施例相比,阳极盘5在与衬套20相对的一侧上具有延伸端口24,其利用其内壁26延伸阳极盘5的(通道)孔12,并且相对于阳极盘5外侧上的周缘面突出。延伸端口24的内壁26同样周向地形成为液态金属轴承运行表面,并且因此形成液态金属轴承外壳的一部分。此外,图4示出了从参考厚度dr开始直到最大厚度d
ii
(包括整体结合到阳极盘5的所有部件,即在当前情况下为连接端口16和延伸端口24)的厚度增加。在图5所示的第四实施例中,与第一实施例相比,阳极盘5”不具有连接端口。相反,衬套20经由扩散结合直接结合到阳极盘5”的平面上。
[0068]
在图6-9所示的实施例中,衬套20设置在与焦点轨迹6相同的一侧。与第一实施例相比,在图6所示的第五实施例中,连接端口16'设置在阳极盘5”',同样在焦点轨迹6的一侧。在图7所示的第六实施例中,阳极盘5”——类似于第四实施例(见图5)——不具有连接端口。相反,衬套20经由扩散结合直接结合到阳极盘5”的平面上。图8中所示的第七实施例与第六实施例的不同之处在于,阳极盘5
””
的厚度在径向向内的方向上连续增加。
[0069]
图9示出了旋转x射线阳极系统27,其中根据第五实施例(参见图6)形成旋转x射线阳极2以及阳极盘5”'、连接端口16'和衬套20。还示出了插入到内侧上的套管28,液态金属轴承内壳形成在该套管上。轴承间隙30形成在套管28的液态金属轴承内壳和液态金属轴承外壳之间,该液态金属轴承外壳在使用中填充有液态金属(未示出)。在旋转x射线阳极上方示出了用于形成套管28的两个示例性变型。在第一变型a中(在图9的顶部示出,一次是在顶视图的左侧,一次是在旋转x射线阳极2内的右侧横截面),套管28具有管状基本形状,并且在外侧具有光滑表面。在第二变型b中(在图9中从左起第三个图的顶部处示出,一次在俯视图中,且向右一次在横截面中),套管28'具有两个表面结构化的运行部段32、34,其在轴向方向上间隔开。套管28'还具有在内侧延伸的冷却剂管道36,该冷却剂管道具有插入盲孔38中的冷却剂管40,其中选择冷却剂管40的直径以便相应地小于盲孔38的直径,使得冷却剂例如可以经由冷却剂管40流入并且通过形成在冷却剂管40和盲孔38之间的环形管道在外侧流回。
[0070]
制造实例:
[0071]
实例1:下面描述本发明的旋转x射线阳极的制造过程,其中,阳极盘和衬套由mhc形成,并通过摩擦焊接彼此结合。首先,通过粉末冶金制造阳极盘和具有圆筒形基本形状的短柱,该粉末冶金包括提供相应的起始粉末(用于mhc)、压制和烧结的步骤,并且在本情况下包括随后的成型(阳极盘的锻造;短柱的径向锻造)。该短柱被机械加工,使得其具有管状基本形状,以形成随后的衬套。此外,在形成(锻造)的过程中,突出的管状连接端口(具有40mm的轴向长度)在一侧上被锻造到阳极盘的中心,这意味着连接端口由阳极盘的材料整体地形成。管状短柱的端面和连接端口的端面都具有2000mm2的待焊接面积和44mm的内径(由此确定外径)。在当前情况下,使用具有主轴的直接驱动的摩擦焊机。管状短柱夹持在摩擦焊机的(非旋转)支架中,而阳极盘夹持在(旋转)主轴支架中。随后,阳极盘被设置成旋转(2000转每分钟)并且以30巴的摩擦压力压靠短柱。随后,停止阳极盘的驱动,并且压缩压力增加到65巴。总摩擦时间,即,在阳极盘和短柱之间发生相对旋转运动的时间,是3秒。然后,
接着进行机械加工操作以建立最终几何形状,然后管状短柱形成衬套。如开头所阐明的,还可以添加其它配合部件、涂层、覆盖物等。根据部件的几何形状和加工步骤,可以在制造过程期间包括一次或多次低应力退火(例如在1100℃-1300℃范围内的温度下)。
[0072]
实例2:下面描述本发明的旋转x射线阳极的制造过程,其中,阳极盘和衬套由tzm形成,并通过摩擦焊接彼此结合。使用与实施例1相同的步骤和参数,除了以下区别:提供了用于从tzm(而不是从mhc)制造阳极盘和短柱的起始粉末。所使用的摩擦压力仅为25巴,并且在阳极盘的驱动已经结束之后压缩压力增加到仅60巴。
[0073]
实例3:下面描述本发明的旋转x射线阳极的制造过程,其中,阳极盘和衬套由tzm形成,并经由扩散结合彼此结合。首先,以与第二工作实例相同的方式,由tzm制造阳极盘和管状短柱。管状短柱的端面(待结合)和连接端口的端面(待结合)都被机械地处理,然后被研磨和/或抛光,以便提供平滑的平坦表面。随后,在1700℃的温度和10mpa的压力下,将具有相互邻接端面的两个部件进行扩散结合,持续至少5分钟(优选在6-15分钟的范围内)。
[0074]
本发明并不限于附图中所示的工作实例。更特别地,液态金属轴承外壳的液态金属轴承运行表面不必具有外圆柱面形式的线性渐进部;如开头所述,它也可以具有阶梯状的走向、周向的隆起部等,其中液态金属轴承内壳则典型地具有相应适配的走向。