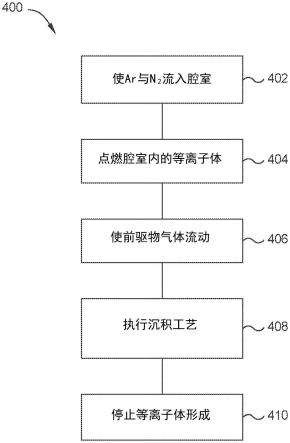
掺杂氮的碳硬模膜
背景领域
1.本公开的实施例总体涉及集成电路的制造以及用于在基板上沉积材料的工艺以及由所述材料形成的结构。
背景技术:2.减小集成电路(ic)的尺寸以得到性能改善、增加产能(capacity)和/或降低生产成本。每次尺寸减小都需要更复杂的技术来形成ic。光刻通常用于图案化基板上的ic。在基板上产生图案化材料需要用于去除暴露材料的受控方法。碳基膜可用作半导体处理(包括存储器和逻辑器件制造)中的硬模和蚀刻停止层。随着平版印刷术中深宽比的增加,硬模需要更高的蚀刻选择性。
3.当前形成碳硬模的方法使用等离子体增强化学气相沉积(pecvd)工艺,并且导致硬模具有差的沉积均匀性和低蚀刻选择性。因此,在本领域中对于形成碳硬模以改善沉积均匀性和蚀刻选择性的方法有需求。
技术实现要素:4.本公开的实施例总体涉及一种用于形成掺杂氮的碳硬模的方法。在一个实施例中,所述方法包括以下步骤:使含氩气体流入处理腔室;使含氮气体流入处理腔室;在处理腔室中点燃等离子体;在点燃等离子体之后,使前驱物气体流入处理腔室;在约560摄氏度至约700摄氏度的温度下执行沉积工艺;以及形成掺杂氮的碳硬模。
5.在另一个实施例中,所述方法包括以下步骤:使含氩气体流入处理腔室;使含氮气体流入处理腔室;将射频功率施加于所述含氩气体和所述含氮气体,以点燃等离子体;在点燃等离子体之后,使前驱物气体流入处理腔室;在约560摄氏度至约700摄氏度的温度下执行沉积工艺;以及形成掺杂氮的碳硬模。
6.在另一个实施例中,所述方法包括以下步骤:使含氩气体流入处理腔室;使含氮气体流入处理腔室;含氮气体与含氩气体的比例为约1:3至约1:10;将射频功率施加于所述含氩气体和所述含氮气体,以点燃等离子体;在点燃等离子体之后,使有机前驱物气体流入处理腔室;在约560摄氏度至约700摄氏度的温度下执行沉积工艺;以及在处理腔室内的基板上形成掺杂氮的碳硬模。
附图说明
7.为了能够详细理解本公开的上述特征,可以通过参考实施例对以上简要概述的本公开进行更具体的描述,所述实施例中的一些在附图中示出。然而,值得注意的是,附图仅示出示例性实施例,因此不应被视为对其范围的限制,并且本公开可允许其他等效的实施例。
8.图1是经配备以执行等离子体增强化学气相沉积(pecvd)工艺的处理腔室的示意
性截面图。
9.图2a至图2c是在不同的处理操作期间的器件的截面图。
10.图3是在pecvd工艺期间的基板支撑件、基板和等离子体的截面图。
11.图4是沉积掺杂氮的碳硬模的方法。
12.图5是示出在基板的边缘处的掩模厚度的曲线图。
13.图6是示出第一工艺之后和第二工艺之后的膜厚度差的图表。
14.为便于理解,在可能的情况下,使用相同的附图标记代表附图中相同的要素。可以预期的是,一个实施例中的要素与特征可有利地用于其他实施例中而无需赘述。
具体实施方式
15.图1是经配备以执行等离子体增强化学气相沉积(pecvd)工艺的处理腔室100的示意性截面图。处理腔室100具有腔室主体102、基板支撑件104与盖组件106,基板支撑件104设置在腔室主体102内部,盖组件106耦接到腔室主体102并将基板支撑件104封围在处理空间120中。通过开口126将基板提供到处理空间120,可使用阀门将开口126密封以用于处理。
16.第一电极108邻近腔室主体102设置,并将腔室主体102与盖组件106的其他部件分开。第一电极108可以是盖组件106的部分,或者可以是单独的侧壁电极。第一电极108可以是环形或环状构件,并且可以是环电极。第一电极108可以是绕处理腔室100的周边的连续环,或者如果需要的话,第一电极108可以在所选位置处是不连续的,处理腔室100围绕处理空间120。第一电极108也可以是穿孔电极,诸如穿孔环或网状电极。第一电极108也可以是板电极,例如次级气体分配器。
17.隔离器110是介电材料(诸如陶瓷或金属氧化物(例如氧化铝和/或氮化铝)),隔离器110与第一电极108接触并将第一电极108与气体分配器112电分离且热分离,并将第一电极108与腔室主体102电分离且热分离。气体分配器112具有开口118,开口118用于准许处理气体进入处理空间120中。气体分配器112耦接到电功率源142,诸如rf生成器。也可使用dc电源、脉冲dc电源和脉冲rf电源。
18.气体分配器112可以是导电气体分配器或非导电气体分配器。气体分配器112也可由导电和非导电部件制成。例如,气体分配器112的主体可以是导电的,而气体分配器112的面板是不导电的。如图1所示,在等离子体处理腔室中,可以为气体分配器112供电,或者可将气体分配器112耦接到接地。
19.电极108耦接到控制处理腔室100的接地路径的调谐电路128。调谐电路128包括电子传感器130和电子控制器134,电子控制器134可以是可变电容器。调谐电路128可以是包括一个或多个电感器332的llc电路。调谐电路128可以是在处理期间在存在于处理空间120中的等离子体条件下具有可变或可控阻抗的任何电路。在可与其他实施例结合的图1的实施例中,调谐电路128具有与电子控制器134串联的第一电感器132a以及与电子控制器134并联的第二电感器132b。电子传感器130可以是电压或电流传感器,且可与电子控制器134耦接,以提供对处理空间120内的等离子体条件的一定程度的闭环控制。
20.第二电极122耦接到基板支撑件104或设置在基板支撑件104中。第二电极122可以是板、穿孔板、网孔、线网或以任何其他分布来布置。第二电极122可以是调谐电极,且可通过设置在基板支撑件104的轴144中的导管146来耦接到第二调谐电路136。第二调谐电路
136包括第二电子传感器138和第二电子控制器140,第二电子控制器140可以是第二可变电容器。第二电子传感器138可以是电压或电流传感器,且可与第二电子控制器140耦接以提供对处理空间120中的等离子体条件的进一步控制。
21.第三电极124与基板支撑件104耦接,第三电极124可以是偏压电极和/或静电吸盘电极。第三电极通过滤波器148与第二电功率源150耦接,滤波器148可以是阻抗匹配电路180。第二电功率源150可以是dc电源、脉冲dc电源、rf电源、脉冲rf电源或其组合。
22.图1的盖组件106和基板支撑件104可与任何用于等离子体处理或热处理的处理腔室一起使用。可有利地与盖组件106和基板支撑件104一起使用的等离子体处理腔室的一个示例是可从位于加利福尼亚州圣克拉拉市的应用材料公司(applied materials,inc.)取得的平台和腔室。来自其他制造商的腔室也可与上述部件一起使用。
23.在操作中,处理腔室100可提供对处理空间120中等离子体条件的实时控制。将基板设置在基板支撑件104上,且根据任何预定的流动计划使处理气体流过盖组件106。例如,处理气体通过入口114流入气室116。接着,处理气体通过开口118从气室流到处理空间。气体通过出口152离开腔室100。电力与气体分配器112耦接以在处理空间120中建立等离子体。如果需要,可使用第三电极124使基板经受电偏压。
24.一旦在处理空间120中激发等离子体,在等离子体与第一电极108之间建立电势差。在等离子体和第二电极122之间也建立了电势差。然后,使用电子控制器134与电子控制器140来调整由两个调谐电路128和136表示的接地路径的流动性质。可将设定点传送到第一调谐电路128和第二调谐电路136,以提供从中心到边缘的沉积速率和等离子体密度均匀性的独立控制。在电子控制器都是可变电容器的实施例中,电子传感器可独立地调整可变电容器以最大化沉积速率以及最小化厚度不均匀性。
25.控制器(诸如控制器160)也是处理腔室100的部分。控制器160控制处理腔室100内的工艺和操作。控制器160还可控制向本文所述的电极中的任何电极(诸如第一电极108、第二电极122和第三电极124)的供电。
26.尽管图示描述了可以与本公开的各方面一起使用的处理腔室100,但是可以预期,其他处理腔室也可受益于本文所述的各方面或用于执行本文所述的各方面。
27.图2a至图2c是在不同的处理操作期间的器件200a的截面图。参考图2a,器件200a包括基板202、硬模层204和光刻胶层206。光刻胶层206设置在硬模层204的顶部上。硬模层设置在基板202的顶部上。
28.基板202可以是任何合适的基板。在一个实施例中,基板202可以是硅基板,诸如硅晶片。在另一个实施例中,基板202可以是掺杂硅的基板。替代地,基板202可以是多个半导体器件层的组合。基板202是如图所示的连续层,但是可以预期其他形貌,包括形成在基板202中的器件特征。
29.硬模层204是掺杂的碳硬模膜。掺杂的碳硬模膜可以是掺杂氮的碳硬模膜。可通过pecvd工艺将硬模层204沉积在基板202上。器件200a中的硬模层204是连续层。硬模层204形成在整个基板202之上。光刻胶层204的厚度为第一厚度d1。硬模层204的第一厚度d1为约1um至约5um,诸如约1.5um至约4um,诸如约1.7um至约3.5um。在一些实施例中,硬模层204的厚度大于1.5um,诸如大于1.7um。
30.在器件200a中,光刻胶层206具有顶部抗蚀剂表面208和底部抗蚀剂表面210。底部
抗蚀剂表面210接触顶部掩模表面212。顶部掩模表面212是硬模层204的顶表面。硬模层204的底表面是底部掩模表面214。底部掩模表面214与顶部基板表面216接触。顶部基板表面216是基板202的顶表面。
31.光刻胶层206是任何合适的光刻胶材料,且可以已经通过任何合适的沉积工艺沉积在基板上。光刻胶层206可以是负光刻胶或正光刻胶。在一个示例中,光刻胶是重氮萘醌-酚醛树脂。器件200a的光刻胶层206是光刻胶的连续层。光刻胶层206的层是平坦的并且具有恒定且预定的厚度。光刻胶层206的厚度为第二厚度d2。光刻胶层206的第二厚度d2为约0.5um至约2.5um,诸如约1um至约2um。也可将其他硬模层(未图示)设置在光刻胶层206下方,以将图案转移到掺杂的碳硬模上。其他硬模层(未图示)的厚度可以是约0.5um至约1.5um,诸如约1um。
32.图2b是在第二时间点的器件200b的截面侧视图。器件200b类似于图2a中描述的器件200a。在器件200b中,光刻胶层206暴露于光子源,然后开口220随后被蚀刻穿过光刻胶层206。
33.开口220包括侧壁218。侧壁218是垂直的侧壁,但是可替代地以一角度形成。光刻胶层206中的开口220垂直延伸穿过光刻胶层206。开口220延伸穿过底部抗蚀剂表面210,使得开口220暴露出顶部掩模表面212的部分。在此实施例中,开口220延伸穿过光刻胶层206的整个第二厚度d2。
34.开口220通过曝光工艺形成,然后被烘烤和/或显影。可通过任何合适的方法(诸如暴露于蚀刻剂)来对图案化的光刻胶层进行图案化。图案化的光刻胶层对硬模层204进行图案化。利用其中对硬模层204的蚀刻选择性相对较高的蚀刻工艺。高蚀刻选择性提高了图案保真度(fidelity)和线宽控制。
35.图2c是在第三时间点的器件200的截面侧视图。器件200c类似于图2a-2b中描述的器件200a和200b。在器件200c中,发生了对硬模层204的选择性蚀刻,并且去除了光刻胶层206。穿过硬模层204以预定图案形成硬模开口222。
36.硬模开口222在硬模开口222中的每一者内具有侧壁224和底表面226。侧壁224是延伸到硬模层204中的垂直壁。硬模开口222的底表面226是底部抗蚀剂表面214,使得开口222的深度d3等于光刻胶层204的第一厚度d1。硬模开口222具有等于硬模层204的第一厚度d1的深度d3。当硬模开口222的深度d3等于硬模层204的第一厚度d1时,硬模开口222的底表面226是顶部基板表面214。
37.图3是在pecvd工艺期间基板支撑件104的截面侧视图。基板支撑件104包括支撑表面310、设置在支撑表面310的顶部上的多个柱308、以及围绕支撑表面310的边缘环302。边缘环302和支撑表面310形成袋部312,基板202设置在袋部312中。基板202设置在袋部312内的多个柱308的顶部上。柱308的上表面314限定基板202接收表面。
38.多个柱308的上表面基本上共面。多个柱308可以是任何合适的形状,诸如矩形柱、圆形柱、椭圆形柱、六边形柱或其他形状。柱308经设计以减少对基板202的背面损坏并减小整个基板202的温度变化。边缘环302在柱308的上表面324上方延伸并且围绕支撑表面310。当将基板202放置在多个柱308上时,边缘环302围绕基板202的外周延伸。在基板202是非圆形的实施例中,边缘环302围绕基板202的外周延伸。
39.等离子体306形成在基板202上方。等离子体306由处理气体的组合形成,诸如含氮
气体、氩和碳氢化合物前驱物。用于形成等离子体306的气体通过入口114和气体分配器112(如图1所示)中的开口118进入腔室。通过向第一电极108、第二电极122和/或第三电极124的组合供电来形成和控制等离子体306。等离子体可用于沉积碳硬模,诸如掺杂氮的碳硬模。
40.图4是沉积掺杂氮的碳硬模的方法400。使用含氮气体、氩气和碳氢化合物前驱物气体形成掺杂氮的硬模。
41.方法400在约560摄氏(c)度至约700摄氏度的温度下执行。在一些实施例中,方法400可在约600度至约650摄氏度的温度下执行,诸如约620摄氏度至约640摄氏度,诸如约630摄氏度。方法400在约6托至约12托的压力下执行。在一些实施例中,方法400在约8托至约10托、诸如8托至约9托或9托至约10托的压力下进行。
42.方法400包括使含氩气体和含氮气体流入处理腔室中的第一操作402。处理腔室可以是图1的处理腔室100。含氩气体是元素氩(ar)。含氮气体可以是双原子氮(n2)、二氧化氮(no2)、氨气(nh3)或其他合适的含氮气体。
43.含氩气体以约2000sccm至约4000sccm的流速流入处理腔室。在可与其他实施例结合的一些实施例中,含氩气体的流速为约2100sccm至约2750sccm。在可与其他实施例结合的一些实施例中,含氩气体的流速为约2100sccm至约2200sccm。在可与其他实施例结合的其他实施例中,含氩气体的流速为约3000至约4000sccm,诸如约3250sccm至约3750sccm,诸如约3400sccm至约3650sccm,诸如约2500sccm至3550sccm。
44.含氮气体以约250sccm至约1000sccm的流速流入处理腔室。在可与其他实施例结合的一些实施例中,含氮气体的流速为约350sccm至约900sccm。在可与其他实施例结合的一些实施例中,含氮气体的流速为约350sccm至约600sccm,诸如约400sccm至约550sccm,诸如约450sccm至约550sccm。在可与又其他实施例结合的其他实施例中,含氮气体的流速为约500sccm至约1100sccm,诸如约550sccm至约1000sccm,诸如约650sccm至约950sccm,诸如约700sccm至约900sccm。
45.在可与其他实施例结合的一些实施例中,在整个方法400中,含氩气体和含氮气体的流可以以不同的速率流动。在其他实施例中,在整个方法400中,含氩气体和含氮气体的流速是恒定的。
46.含氮气体流速与含氩气体流速的比例为约1:3至约1:10。在可与其他实施例结合的一些实施例中,含氮气体流速与含氩气体流速的比例为约1:3至约1:6,诸如约1:3至约1:5,诸如约1:3.5至约1:5,诸如约1:4至约1:5。
47.在可与其他实施例结合的一些实施例中,含氩气体和含氮气体可开始分别流入处理腔室,使得含氩气体或含氮气体中的任一者首先被单独引入。在可与其他实施例结合的一些实施例中,在将含氮气体引入处理腔室之前,首先使含氩气体流入处理腔室。在可与其他实施例结合的其他实施例中,在将含氩气体引入处理腔室之前,首先使含氮气体流入处理腔室。在可与其他实施例结合的一些实施例中,同时使含氩气体和含氮气体两者流入处理腔室中。
48.在第一操作402之后,执行第二操作404,并且在处理腔室内点燃等离子体。在第一操作402中,从引入到处理腔室的含氮和氩的气体点燃等离子体。
49.在第二操作404期间点燃处理腔室内的等离子体包括以下步骤:施加约2000瓦至
约5500瓦、诸如约2000瓦至约5000瓦、诸如约2000瓦至约4000瓦的rf功率。在可与其他实施例结合的一些实施例中,施加约2000瓦至约2250瓦的rf功率以点燃处理腔室内的等离子体。在可与其他实施例结合的其他实施例中,施加约3000瓦至约5500瓦、诸如约3250瓦至约5000瓦、诸如约3250瓦至约4500瓦、诸如约3400瓦至约4000瓦的rf功率以点燃处理腔室内的等离子体。
50.通过电功率源142将rf功率施加到气体分配器112(如图1所示),并通过将rf功率施加到含氩气体和含氮气体来点燃气体分配器和基板支撑件104之间的等离子体。电极108和第二电极122可分别用于控制处理空间120内的等离子体形状和流动。
51.在等离子体的初始点燃之后以及在随后的操作(诸如本文描述的方法400的第三操作406和第四操作408)期间,维持rf功率。
52.在第二操作402和点燃等离子体之后执行方法400的第三操作406。在第三操作406处,前驱物气体流入处理腔室。前驱物气体是适合于沉积碳硬模的碳氢化合物或有机化合物气体。例如,前驱物气体包括以下各项中的任一项:乙炔(c2h2)、甲烷(ch4)、乙烷(c2h6)、丙烷(c3h8)、丙烯(c3h6)、环丙烷(c3h6)、丁烷(c4h
10
)、戊烷(c5h
12
)、己烷(c6h
14
)、庚烷(c7h
16
)、辛烷(c8h
18
)、壬烷(c9h
20
)、癸烷(c
10h22
)、十一烷(c
11h24
)、十二烷(c
12h26
)等。也可使用其他有机化合物。
53.前驱物气体的流速为约300sccm至约900sccm,诸如约350sccm至约800sccm,诸如约350sccm至约750sccm。在一些实施例中,前驱物气体的流速可以是约300sccm至约500sccm,诸如约350sccm至约450sccm。在其他实施例中,前驱物气体的流速可以是约500sccm至约900sccm,诸如约550sccm至约800sccm,诸如约600sccm至约750sccm,诸如约650sccm至约700sccm。
54.前驱物气体的流速与含氩气体和含氮气体的组合气体的流速的比例可以是约1:15至约1:3,诸如约1:10至约1:5,诸如约1:9至约1:6,诸如约1:8至约1:6,诸如约1:7至约1:6。由于在操作404中形成的等离子体而使前驱物气体离子化,因此前驱物气体的引入使得能够沉积碳硬模。如果使用前驱物气体与含氩气体和含氮气体的更大比例,则硬模的成分发生变化,使得硬模内的氮与碳的比例降低。如果使用前驱物气体与含氩气体和含氮气体的更小比例,则硬模的成分发生变化,使得硬模内的氮与碳的比例增加。
55.在将前驱物气体引入处理腔室之后,进行执行沉积工艺的第四操作408。在执行沉积工艺期间,将掺杂氮的硬模沉积到基板(诸如图2和图3的基板202)上。掺杂氮的硬模可以是图2a-2c的硬模层206。在第四操作408期间的沉积速率可以是约2500埃/分钟至约8000埃/分钟,诸如约3000埃/分钟至约7500埃/分钟,诸如约3000埃/分钟至约5000埃/分钟,诸如约3200埃/分钟至约3500埃/分钟。在一些实施例中,掺杂氮的硬模的沉积速率可以是约3500埃/分钟至约6000埃/分钟,诸如约3750埃/分钟至约5000埃/分钟。在操作404中,沉积速率受所施加的用于形成等离子体的rf功率影响。随着施加的rf功率增加,沉积速率也增加。
56.可沉积掺杂氮的硬模,直到硬模达到预定厚度,诸如约0.5um至约6um的厚度,诸如约1um至约5um,诸如约1.5um至约4um,诸如约1.7um至约3.5um。在一些实施例中,掺杂氮的硬模的厚度可以是约5um或更大。掺杂氮的碳硬模的弓形部(bow)可以是约30um至约40um,诸如约32um至约38um,诸如约33um至约37um。掺杂氮的碳硬模内的内部应力可以是约30mpa
至约37mpa,诸如约32mpa至约36mpa,诸如约32.5mpa至约35mpa。掺杂氮的硬模中的氮成分小于掺杂氮的硬模的原子浓度的约16%,诸如小于掺杂氮的硬模的原子浓度的约15%或约10%。在一些实施例中,掺杂氮的硬模内的氮原子百分比为约1%至约16%,诸如约2%至约16%,诸如约3%至约16%,诸如约4%至约16%,诸如约5%至约16%,诸如约6%至约16%,诸如约7%至约16%,诸如约8%至约16%,诸如约1%至约15%,诸如约1%至约10%,诸如约2%至约10%,诸如约3%至约10%,诸如约4%至约10%,诸如约5%至约10%。在一些实施例中,掺杂氮的硬模内的氮原子百分比为约5%至约9%,诸如约5%至约8%。增加的rf功率会增加掺杂氮的碳硬模中氮的掺入量。
57.在掺杂氮的碳硬模达到期望的厚度之后,在操作410中停止等离子体的形成。可通过停止向气体分配器112施加rf功率和停止前驱物气体流入处理腔室来停止等离子体形成。在停止等离子体形成和前驱物气体流入处理腔室之后,可停止含氩气体和含氮气体的流动。接着,在通过开口(诸如图1中的处理腔室100的开口126)从处理腔室中移出基板之前,将处理腔室排空。
58.值得注意的是,本文提供的气体流速适用于300mm圆形基板,且气体流速可针对其他形状和尺寸的基板按比例增减。
59.图5是示出针对掺杂氮的碳硬模与未掺杂的碳硬模在基板的边缘处的掩模厚度的曲线图500。掩模的边缘定义为掩模半径的外部20mm。掩模的厚度绘制成以掩模厚度作为y轴和自变量,而以mm为单位的距基板中心的距离为x轴和因变量。
60.针对碳硬模的两种不同组成来绘制掩模厚度。在一个实施例中,绘制掺杂氮的碳硬模的厚度分布图。使用本文所述的方法400形成掺杂氮的碳硬模。掺杂氮的碳硬模的边缘落差(edge drop)由图5中的d4定义。掺杂氮的碳硬模可具有约55nm至约25nm、诸如约51nm至约30nm的边缘落差d4。
61.在另一个实施例中,绘制未掺杂的(例如未掺杂氮的)碳硬模的厚度分布图。使用传统的硬模形成工艺来形成未掺杂氮的碳硬模。未掺杂氮的碳硬模的边缘落差由图5中的d5定义。未掺杂氮的碳硬模可具有约65nm至约75nm、诸如约67.5nm至约72.5nm的边缘落差d5。
62.在曲线图5中描述的碳硬模的沉积速率相同的实施例中,掺杂氮的碳硬模的边缘落差d4可小于未掺杂氮的碳硬模的边缘落差d5的50%。通过在硬模沉积期间对碳硬模掺杂氮,显著减少了边缘落差。减少的边缘落差导致更精确的图案化,从而能够以更小规模实现集成电路。
63.图6是示出本公开的n掺杂的碳硬模以及传统硬模的柱位置厚度损失的图表600。图表600示出横跨基板在柱(诸如图3的多个柱308)与基板(诸如图3中的基板202)下侧接触以促进支撑基板202的位置处的平均相对厚度损失。由于由柱的热传导引起的基板内的热梯度,导致在基板与柱接触的部分处的硬模的厚度的损失。在柱上方的硬模的部分处的厚度损失导致在硬模的表面上的轻微凹陷(dimpling)效应。通常,有利的是减少由柱引起的凹陷效应,使得有更平坦的硬模和更均匀的图案化。更均匀的图案化能够实现更高的深宽比。
64.实验结果已经表示,未掺杂氮的碳硬模具有第一平均柱位置相对厚度损失602,而掺杂氮的碳硬模具有第二平均柱位置相对厚度损失604。图表600中的厚度损失是厚度损失
的百分比。如曲线图600所示,当使用掺杂氮的碳硬模和本文所述的方法400时的厚度损失百分比小于使用传统的未掺杂氮的碳硬模和相关的硬模形成方法时的厚度损失百分比的一半。当利用具有类似沉积速率(诸如本文所述的沉积速率)的方法时,可以看到厚度损失百分比的降低。
65.在可与其他实施例结合的一些实施例中,第一平均柱位置相对厚度损失在约0.45%至约0.6%之间,诸如约0.5%至约0.55%。在可与其他实施例结合的一些实施例中,第二平均柱位置相对厚度损失在约0.075%至约0.25%之间,诸如约0.1%至约0.2%之间,诸如约0.14%。
66.在可与其他实施例结合的一些实施例中,硬模层的厚度分布均匀性小于约3%,诸如在约2.9%至约2.4%之间,诸如约2.8%至约2.5%。在一些实施例中,使用本文描述的方法形成的掺杂氮的碳硬模的厚度分布均匀性为约2.7%。通过从硬模层的最大分布厚度减去硬模层的最小分布厚度来计算硬模层的厚度分布均匀性以提供厚度范围。接着将厚度范围除以二以产生半厚度范围。然后将半厚度范围除以整个硬模层的平均厚度,并以百分比表示。在计算厚度分布均匀性时,距离晶片边缘3.2mm以内的硬模层厚度被打折(discounted)。用于形成未掺杂氮的碳硬模的现有方法产生的厚度分布均匀性大于约3%,诸如大于3.35%。
67.虽然前面内容针对本公开的实施例,但在不背离本公开的基本范围的情况下,可设计本公开的其他与进一步的实施例,且本公开的范围由所附权利要求书确定。