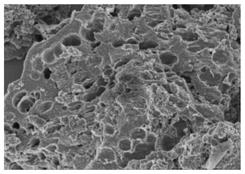
1.本发明属于电极材料技术领域,特别涉及一种硼硫共掺杂多孔碳材料及其制备方法和应用。
背景技术:2.超级电容器具有充放电快速、能量密度大和循环性能优异的优点。多孔碳材料是超级电容器常见的电极材料。生物质多孔碳材料具有丰富的孔结构,有利于电子的运输,进而提升其电化学性能,以生物质为前驱体转化的生物质多孔炭材料,得到了超级电容器研究人员的广泛关注。电极表面化学性质是影响碳基超级电容器性能的因素之一,电解质离子的传输优良与否取决于电极碳材料的润湿性的高低。b、s等掺杂原子可以提高碳材料表面与所用电解质溶液的润湿能力,能够增强表面润湿性并提供更多的电化学活性反应点;掺杂原子还可以为碳材料提供额外的赝电容贡献。
3.目前,大部分碳材料的掺杂工作大多是在单原子上进行,制备的材料掺杂原子含量低,得到的掺杂多孔碳材料能量密度和循环寿命等电化学性能欠佳。
技术实现要素:4.有鉴于此,本发明的目的在于提供一种硼硫共掺杂多孔碳材料及其制备方法,本发明提供的硼硫共掺杂多孔碳材料掺杂原子含量高,有利于获得能量密度高且循环寿命长的性能,满足超级电容器电极的使用需求。
5.为了实现上述发明的目的,本发明提供以下技术方案:
6.本发明提供了一种硼硫共掺杂多孔碳材料,包括多孔碳和掺杂在所述多孔碳表面和孔隙中的b和s;所述b的掺杂含量为5.56~7.85wt.%,s的掺杂含量为0.90~1.55wt.%。
7.优选的,所述硼硫共掺杂多孔碳材料的孔径为2~5nm,比表面积为 360~400m2/g。
8.本发明还提供了上述技术方案所述硼硫共掺杂多孔碳材料的制备方法,包括以下步骤:
9.将生物碳源、硼酸、氯化锌、硫脲和水混合,去除水后得到混合原料粉;
10.保护气条件下,将所述混合原料粉进行焙烧,得到焙烧粉;
11.将所述焙烧粉进行酸洗,得到所述硼硫共掺杂多孔碳材料。
12.优选的,所述生物碳源包括八宝茎秆、核桃青皮、小麦秸秆和玉米秸秆中的一种或多种。
13.优选的,所述生物碳源的目数为50~200目。
14.优选的,所述生物碳源和硼酸的质量比为1:(0.5~1.5);
15.所述生物碳源和氯化锌的质量比为(0.8~1):(1~1.2);
16.所述生物碳源和硫脲的质量比为(0.8~1):(1~1.2)。
17.优选的,所述焙烧的温度为400~1000℃;时间为1~6h。
18.优选的,所述焙烧的温度由室温升温得到;所述升温的速率为2~10℃ /min。
19.本发明还提供了上述技术方案所述硼硫共掺杂多孔碳材料或上述技术方案所述制备方法得到的硼硫共掺杂多孔碳材料作为电极材料的应用。
20.优选的,所述应用为在超级电容器中的应用。
21.本发明提供了一种硼硫共掺杂多孔碳材料,包括多孔碳和掺杂在所述多孔碳表面和孔隙中的b和s;所述b的掺杂含量为5.56~7.85wt.%,s的掺杂含量为0.90~1.55wt.%。本发明提供的硼硫共掺杂多孔碳材料b和s掺杂含量高,更高含量的b、s掺杂原子可以提高碳材料表面与所用电解质溶液的润湿能力,能够增强表面润湿性并提供更多的电化学活性反应点;同时,较高含量的掺杂原子b、s可以为碳材料提供更高的额外的赝电容,从而提高掺杂多孔碳材料能量密度和循环寿命等电化学性能。
22.实施例测试结果表明,本发明提供的硼硫共掺杂多孔碳材料的b、s 掺杂含量高,孔隙丰富;在三电极体系、0.5a
·
g-1
时显示出最大比电容为 168~290.7f
·
g-1
,组装成对称超级电容器后,在中性电解液体系下具有 11.3~16.65wh
·
kg-1
的超高能量密度,且在10000次寿命测试后具有 97.09~100.67%的电容保持率。
23.本发明还提供了上述技术方案所述硼硫共掺杂多孔碳材料的制备方法,包括以下步骤:将生物碳源、硼酸、氯化锌、硫脲和水混合,去除水后得到混合原料粉;保护气条件下,将所述混合原料粉进行焙烧,得到焙烧粉;将所述焙烧粉进行酸洗,得到所述硼硫共掺杂多孔碳材料。在本发明中,氯化锌作为活化剂,在高温下蒸发,氯化锌分子进入碳内部作为骨架,碳聚合物被碳化并沉积在骨架上,经酸洗后,zncl2被去除,形成发育良好的孔隙结构。这种分层多孔结构提供了一个具有互连和短离子扩散路径的导电网,用于快速电荷传输和离子迁移。硼酸和硫脲为多孔碳提供了丰富的硼和硫原子,硼原子可用作电催化剂,加速含o和含n等官能团的氧化还原反应,提供额外的赝电容;碳晶格中的b原子能够促进o2的化学吸附,从而形成具有反应性的碳表面;硫脲引入c-s,这种n型掺杂剂s能够提供更多可逆的假位点和极化表面,而且,硫脲中含有的含硫官能团可作为高温下较大孔隙的支撑骨架,减少碳化过程中微孔的收缩,从而提供快速的离子传输。
附图说明
24.图1为对比例1的八宝茎秆碳粉的sem图;
25.图2为实施例1所得硼硫共掺杂多孔碳材料的sem图;
26.图3为实施例1所得硼硫共掺杂多孔碳材料的tem图;
27.图4为实施例1所得硼硫共掺杂多孔碳材料的xrd图;
28.图5为实施例1所得硼硫共掺杂多孔碳材料的raman谱图;
29.图6为实施例1所得硼硫共掺杂多孔碳材料的氮气吸脱附谱图;
30.图7为实施例1所得硼硫共掺杂多孔碳材料的xps谱图;
31.图8为实施例1所得硼硫共掺杂多孔碳材料在三电极体系下的电化学测试结果;
32.图9为实施例2所得硼硫共掺杂多孔碳材料在三电极体系下的电化学测试结果;
33.图10为实施例3所得硼硫共掺杂多孔碳材料在三电极体系下的电化学测试结果;
34.图11为实施例4所得硼硫共掺杂多孔碳材料在三电极体系下的电化学测试结果;
35.图12为实施例5所得硼硫共掺杂多孔碳材料在三电极体系下的电化学测试结果;
36.图13为实施例6所得硼硫共掺杂多孔碳材料在三电极体系下的电化学测试结果;
37.图14为实施例7所得硼硫共掺杂多孔碳材料在三电极体系下的电化学测试结果;
38.图15为实施例8所得硼硫共掺杂多孔碳材料在三电极体系下的电化学测试结果;
39.图16为实施例1所得硼硫共掺杂多孔碳材料在以koh为电解液的对称超级电容器体系中的电化学测试结果;
40.图17为实施例1所得硼硫共掺杂多孔碳材料在以na2so4为电解液的对称超级电容器体系中的电化学测试结果;
41.图18为实施例6所得硼硫共掺杂多孔碳材料在以na2so4为电解液的对称超级电容器体系的能量密度图;
42.图19为实施例7所得硼硫共掺杂多孔碳材料在以na2so4为电解液的对称超级电容器体系的能量密度图;
43.图20为实施例8所得硼硫共掺杂多孔碳材料在以na2so4为电解液的对称超级电容器体系的能量密度图;
44.图21为实施例1所得硼硫共掺杂多孔碳材料在以na2so4为电解液的对称超级电容器体系的循环寿命测试图;
45.图22为实施例6所得硼硫共掺杂多孔碳材料在以na2so4为电解液的对称超级电容器体系的循环寿命测试图;
46.图23为实施例7所得硼硫共掺杂多孔碳材料在以na2so4为电解液的对称超级电容器体系的循环寿命测试图;
47.图24为实施例8所得硼硫共掺杂多孔碳材料在以na2so4为电解液的对称超级电容器体系的循环寿命测试图。
具体实施方式
48.本发明提供了硼硫共掺杂多孔碳材料,包括多孔碳和掺杂在所述多孔碳表面和孔隙中的b和s;所述b的掺杂含量为5.56~7.85wt.%,s的掺杂含量为0.90~1.55wt.%。
49.在本发明中,所述硼硫共掺杂多孔碳材料,包括多孔碳和掺杂在所述多孔碳表面和孔隙中的b和s。在本发明中,所述硼硫共掺杂多孔碳材料中b 的掺杂含量为5.56~7.85wt.%。在本发明中,硼硫共掺杂多孔碳材料中s的掺杂含量为0.90~1.55wt.%。
50.在本发明中,所述硼硫共掺杂多孔碳材料的孔径优选为2~5nm。在本发明中,所述硼硫共掺杂多孔碳材料的比表面积优选为360~400m2/g。在本发明中,所述硼硫共掺杂多孔碳材料的孔体积优选为0.25~0.3cm3/g。
51.本发明还提供了上述技术方案所述硼硫共掺杂多孔碳材料的制备方法,包括以下步骤:
52.将生物碳源、硼酸、氯化锌、硫脲和水混合,去除水后得到混合原料粉;
53.保护气条件下,将所述混合原料粉进行焙烧,得到焙烧粉;
54.将所述焙烧粉进行酸洗,得到所述硼硫共掺杂多孔碳材料。
55.在本发明中,若无特殊说明,所述制备方法中的各组分均为本领域技术人员熟知的市售商品。
56.本发明将生物碳源、硼酸、氯化锌、硫脲和水混合,去除水后得到混合原料粉。
57.在本发明中,所述生物碳源优选包括八宝茎秆、核桃青皮、小麦秸秆和玉米秸秆中的一种或多种。在本发明中,所述生物碳源的目数优选为50~200 目,更优选为60~190目,再优选为80~150目。
58.本发明优选将所述生物碳源依次进行水洗和干燥,再将干燥的生物碳源与硼酸、氯化锌、硫脲和水混合。本发明对所述水洗没有特殊限定,以能够去除生物碳源上附着的杂质为准。在本发明中,所述干燥的温度优选为 75~85℃,更优选为78~83℃;时间优选为6~16h,更优选为7~15h。
59.在本发明中,所述生物碳源和硼酸(h3bo3)的质量比优选为1: (0.5~1.5),更优选为1:(0.6~1.4)。
60.在本发明中,所述生物碳源和氯化锌(zncl2)的质量比优选为(0.8~1): (1~1.2),更优选为(0.9~1):(1~1.1),最优选为1:1。
61.在本发明中,所述生物碳源和硫脲(ch4n2s)的质量比优选为(0.8~1): (1~1.2),更优选为(0.9~1):(1~1.1),最优选为1:1。
62.在本发明中,所述生物碳源和水的质量比优选为1:(15~25),更优选为1:(18~23)。
63.在本发明中,所述生物碳源、硼酸、氯化锌、硫脲和水的混合优选为搅拌;本发明对所述搅拌的速率没有特殊限定,采用本领域技术人员熟知的搅拌速率即可;本发明对所述搅拌的时间没有特殊限定,以能够将物料充分混合为准。
64.本发明对所述生物碳源、硼酸、氯化锌、硫脲和水的混合顺序没有特殊限定,能够将物料混合均匀即可。
65.在本发明中,去除水的方法优选为烘干。在本发明中,所述烘干的温度优选为75~85℃,更优选为78~83℃。在本发明中,所述烘干的设备优选为鼓风干燥箱。
66.本发明通过氯化锌溶解与生物碳源混合均匀,可使得在后续焙烧活化过程中,氯化锌可以均匀分布在碳骨架上,有利于得到高孔隙多孔碳,同时有利于硼酸和硫脲在碳分子上引入可以增加润湿性和赝电容的硼原子和硫原子,得到双掺杂多孔碳。本发明物料混合的方法使得各组分分散均匀,克服活化剂(氯化锌)和掺杂剂(硼酸和硫脲)在活化过程中掺杂、活化不均匀的缺点,有利于提高多孔碳的孔隙结构含量和原子掺杂量。
67.得到混合原料粉后,本发明在保护气条件下,将所述混合原料粉进行焙烧,得到焙烧粉。
68.在本发明中,所述保护气优选包括氩气、氮气或氦气。
69.在本发明中,所述焙烧的温度优选为400~1000℃,更优选为450~950℃;时间优选为1~6h,更优选为2~5h。
70.在本发明中,所述焙烧的温度优选由室温升温得到;所述升温的速率优选为2~10℃/min,更优选为3~9℃/min。在本发明中,所述焙烧的设备优选为管式炉。
71.在本发明中,所述焙烧中发生活化掺杂反应,氯化锌在高温下汽化进入到碳内部起骨架作用,生物碳源作为碳的高聚物,炭化后沉积到骨架表面,同时硼酸和硫脲提供硼源和硫源掺杂入多孔碳材料中。
72.得到焙烧粉后,本发明将所述焙烧粉进行酸洗,得到所述硼硫共掺杂多孔碳材料。
73.在本发明中,所述酸洗用酸洗液优选为盐酸。在本发明中,所述盐酸的浓度优选为
1~4mol/l,更优选为1.5~3.5mol/l。在本发明中,所述酸洗的时间优选为6~16h,更优选为7~15h。本发明利用盐酸去除均匀分布在碳骨架上的氯化锌,生成高度发达的孔隙结构,这种多孔结构有利于快速进行电荷传输和离子迁移。
74.所述酸洗后,本发明优选将酸洗固体进行水洗和干燥。本发明对所述水洗没有特殊限定,以洗去酸洗液和杂质为准。在本发明的实施例中,所述水洗的方法优选为:在抽滤的条件下进行水洗,至抽滤所得滤液的ph值为中性。在本发明中,所述干燥的温度优选为75~85℃,更优选为77~83℃;时间优选为6~16h,更优选为8~14h。
75.本发明还提供了上述技术方案所述硼硫共掺杂多孔碳材料或上述技术方案所述制备方法得到的硼硫共掺杂多孔碳材料作为电极材料的应用。
76.在本发明中,所述应用优选为在超级电容器中的应用。
77.本发明对所述硼硫共掺杂多孔碳材料在超级电容器中的应用没有特殊限定,采用本领域技术人员熟知的应用即可。
78.为了进一步说明本发明,下面结合实施例对本发明提供的一种硼硫共掺杂多孔碳材料及其制备方法和应用进行详细地描述,但不能将它们理解为对本发明保护范围的限定。显然,所描述的实施例仅是本发明一部分实施例,而不是全部的实施例。基于本发明中的实施例,本领域普通技术人员在没有做出创造性劳动前提下所获得的所有其他实施例,都属于本发明保护的范围。
79.实施例1
80.将八宝茎秆进行水洗,80℃干燥后,粉碎,得到100目的八宝茎秆粉末;
81.将2g八宝茎秆粉末、2g硼酸、2g氯化锌、2g硫脲和40ml水搅拌混合,然后在80℃烘干12h去除水,得到混合原料粉;
82.保护气氮气条件下,将所述混合原料粉装在瓷舟中,在管式炉中以5℃ /min升温至700℃保温进行焙烧2h,得到焙烧粉;
83.利用2mol/l的盐酸对所述焙烧粉酸洗12h,然后在抽滤的条件下进行水洗,至滤液的ph至为7,将所得的固体在80℃干燥12h,得到所述硼硫共掺杂多孔碳材料。
84.实施例2
85.焙烧温度为600℃,其他技术手段与实施例1一致,得到所述硼硫共掺杂多孔碳材料。
86.实施例3
87.焙烧温度为800℃,其他技术手段与实施例1一致,得到所述硼硫共掺杂多孔碳材料。
88.实施例4
89.硼酸的质量为1g,其余技术手段与实施例2一致,得到所述硼硫共掺杂多孔材料。
90.实施例5
91.硼酸的质量为3g,其余技术手段与实施例2一致,得到所述硼硫共掺杂多孔材料。
92.实施例6
93.以核桃青皮代替实施例1的八宝茎秆,其余技术手段与实施例1一致,得到所述硼硫共掺杂多孔材料。
94.实施例7
95.以小麦秸秆代替实施例1的八宝茎秆,其余技术手段与实施例1一致,得到所述硼硫共掺杂多孔材料。
96.实施例8
97.以玉米秸秆代替实施例1的八宝茎秆,其余技术手段与实施例1一致,得到所述硼硫共掺杂多孔材料。
98.对比例1
99.将八宝茎秆进行水洗,80℃干燥后,粉碎,得到100目的八宝茎秆粉末;
100.将2g八宝茎秆粉末保护气氮气条件下,装在瓷舟中,在管式炉中以5℃ /min升温至700℃保温进行焙烧2h,得到八宝秸秆碳粉。
101.测试:
102.(1)对对比例1的八宝茎秆碳粉进行扫描电镜测试,所得sem图见图 1。由图1可见,直接碳化的八宝秸秆碳粉样品呈现出块状结构,表面光滑,不存在孔径。对实施例1的硼硫共掺杂多孔碳材料进行扫描电镜测试,所得sem图见图2。由图2可见,实施例1的硼硫共掺杂多孔碳材料在表面区域形成了大量随机分布的孔,这有助于离子从电解质溶液中更快的吸附和扩散,这证明经过氯化锌活化和后续的焙烧后,碳材料的物理形态发生了良性改变。
103.(2)对实施例1所得硼硫共掺杂多孔碳材料进行透射电镜测试,所得 tem图见图3,图3的左图和右图为不同放大尺寸的tem图。由图3进一步证实了实施例1所得硼硫共掺杂多孔碳材料具有高度互连的网络结构。
104.此外,由图3的右图可见,其中存在大量白点,表明所提供的硼硫共掺杂多孔碳材料存在丰富的微孔,并且从中可以观察到的晶格条纹(排列的石墨层),证实实施例1所得硼硫共掺杂多孔碳材料存在层状的石墨结构,这些条纹为石墨相关(002)平面。因此,图3的测试结果表明,硼硫共掺杂多孔碳材料中富含孔隙的碳由丰富的无定形碳和少量石墨结构组成。
105.(3)对实施例1所得硼硫共掺杂多孔碳材料进行x-射线衍射测试,所得xrd图见图4。由图4可见,在约26
°
和43.3
°
处显示2个代表性峰,分别与(002)和(001)的衍射有关,它显示了样品的无定形碳特性,并具有大量不规则石墨微晶;(101)峰相对较弱,表明样品石墨化不均匀,这是由于该系统使用的活化温度较低,而石墨化程度与活化温度有关。
106.(4)对实施例1所得硼硫共掺杂多孔碳材料进行拉曼测试,所得raman 谱图见图5。由图5可见,硼硫共掺杂多孔碳材料的d峰(无序或缺陷带) 和g峰(结晶石墨带)分别出现在1366cm-1
和1593cm-1
的拉曼位移处,样品均显示d峰含量高于g峰,表明存在大量sp3键合碳原子;强度比(id/ig) 经计算为1.02,这也说明b和s元素的掺杂在被认为有利于离子扩散过程的碳材料的骨架中形成了更多的缺陷。
107.(5)对实施例1所得硼硫共掺杂多孔碳材料进行氮气吸脱附测试,所得氮气吸脱附谱图见图6,图6中(a)为iv型等温线,(b)为孔径分布曲线。由图6可见,n2在低压范围内的陡峭吸附(p/p0《0.1),表明微孔的存在。此外,在较大的相对压力下(p/p0》0.4),曲线缓慢增加,这表明样品中还具有中孔/大孔的特性。值得注意的是,这有利于实际应用中电解液的缓冲。结合图6的(b),进一步证实了硼硫共掺杂多孔碳材料中存在大量小比例的窄介孔(2~5nm)。根据bet结果,样品的比表面积为400m2/g,孔体积为0.28cm3/g。
108.(6)对实施例1所得硼硫共掺杂多孔碳材料进行xps测试,所得xps 谱图见图7,图7
中,(a)为xps总谱,(b)为c1s的xps谱图,(c) 为b1s的xps谱图,(d)为s2p的xps谱图。由图7的(a)可见,b和 s的峰出现在样品的中,这意味着由于硼酸和硫脲的使用,硼和硫元素已顺利引入碳中;同时,xps谱也显示了n1s和o1s信号,明确表明生物材料的碳化作用可能在最终的碳产物中实现了自身o2和n2的遗传。为了突出碳基体中的硼硫共掺杂结构,进一步分析了样品的c1s、b1s和s2p的高分辨 xps图像以确定它们的化学状态。由图7的(b)~(d)可见,c1s光谱均由四个峰拟合,中心位于284.6
±
0.1ev、285.2
±
0.1ev、286.4
±
0.1ev和288.3
ꢀ±
0.1ev,分别表示为c-c、c-n-b、c-o/c-n和c=o,除了碳-碳键之外,还显示了与其他元素的结合,其中氧官能团能够提高表面亲水性并带来额外的伪电容。b1s光谱由2个峰拟合,分别位于190.8
±
0.1ev和192
±
0.1ev,可分别指定为b-c
2-o和b-c-o2。研究表明,b的相关官能团可以作为电化学催化剂促进n和o的氧化还原反应,使样品中一定含量的n和o也可以提供额外的赝电容。硼硫共掺杂多孔碳材料中的s2p光谱以164
±
0.1ev、 165.2
±
0.1ev和168.9
±
0.1ev为中心由3个峰拟合,可分别记作c-s、c-s-c 和c-so
x-c,这些氧化的s官能团有望提高电解质的润湿性。
109.(7)对实施例1所得硼硫共掺杂多孔碳材料在三电极体系下的电化学性能进行测试:为了探索所制备硼硫共掺杂多孔碳电极材料在超级电容器领域的潜在效用,利用三电极系统来测量6mol/l的koh中的电容特性,测试结果见图8,图8中,(a)为在不同扫描速率下的cv曲线,(b)为在各种电流密度下的gcd图,(c)为比电容和安培密度关系曲线,(d)为电化学阻抗谱(eis),(d)的内插图为高频区域内奈奎斯特图的放大。由图8的(a)可见,硼硫共掺杂多孔碳材料作为电极在-1至0v的电位范围内显示出明显的宽峰,这意味着丰富的表面杂原子的存在有助于形成显着的赝电容。这些现象可归因于以下两个可能的原因:(
ⅰ
)更多的活性杂原子(尤其是b、s)不仅提供更大的伪电容,而且在亲水表面暴露更多的离子并增加cv环的面积;(
ⅱ
)三维多孔结构有利于电子的传导并改善电荷转移。由图8 的(b)可见,在每个电流密度下,恒流充放电曲线对应于cv曲线,变形轻微,呈准对称三角形,表明可逆性可靠,同时存在edlc和赝电容。由图 8的(c)可见,硼硫共掺杂多孔碳材料的电极比电容随着安培密度的升高而减小,这是由于在较大安培密度下增强的扩散限制和更短的离子传输时间。硼硫共掺杂多孔碳材料的电极在0.5a
·
g-1
时显示出最大比电容290.7f
·
g-1
。此外,即使在10a
·
g-1
下,硼硫共掺杂多孔碳材料的电极也表现出70%的电容器保持率,显示出卓越的倍率性能。推断原因是,富含掺杂原子的电极一方面可以提供额外的赝电容,另一方面有利于电极和电解质之间的接触概率,确保电荷存储的有效表面大,从而使电极具有出色的速率性能。由图8的(d) 可见,硼硫共掺杂多孔碳材料的电极内的离子扩散显着促进。此外,b/s多孔碳电极表现出非常低的溶液电阻,约为0.72ω,可以推断掺杂原子掺杂带来的润湿性大大降低了样品的电阻并提高了电导率。
110.(8)对实施例2~8所得的硼硫共掺杂多孔碳材料在三电极体系下进行电化学测试,测试方法与实施例1一致,测试结果见图9~15。由图9可见,硼硫共掺杂多孔碳材料的电极在0.5a
·
g-1
时显示出最大比电容为237.9f
·
g-1
。由图10可见,硼硫共掺杂多孔碳材料的电极在0.5a
·
g-1
时显示出最大比电容为168f
·
g-1
。由图11可见,硼硫共掺杂多孔碳材料的电极在0.5a
·
g-1
时显示出最大比电容为212.3f
·
g-1
。由图12可见,硼硫共掺杂多孔碳材料的电极在 0.5a
·
g-1
时显示出最大比电容为245.8f
·
g-1
。由图13可见,硼硫共掺杂多孔碳材料的电极在0.5a
·
g-1
时显示出最大比电容为240f
·
g-1
。由图14可见,硼硫共掺杂多孔碳
材料的电极在0.5a
·
g-1
时显示出最大比电容为223f
·
g-1
。由图15可见,硼硫共掺杂多孔碳材料的电极在0.5a
·
g-1
时显示出最大比电容为 200.2f
·
g-1
。
111.(9)将实施例1所得硼硫共掺杂多孔碳材料作为电极组装成对称超级电容器后,以6mol/l的koh为电解液,进行电化学测试,测试结果见图 16,图16中,(a)为在不同扫描速率下的cv曲线,(b)为在各种电流密度下的gcd图,(c)为比电容和安培密度关系曲线,(d)为ragone图。由图16的(a)可见,以硼硫共掺杂多孔碳材料作为电极,得到的对称超级电容器的cv曲线显示准矩形形状,即使在200mv
·
s-1
的大扫描速度下也没有明显变形,表明双电层占主导地位,具有快速充电/放电过程和良好的倍率电化学性能。由图16的(b)可见,gcd曲线呈现一个典型的三角形,表明理想的电容特性和电化学可逆性。由图16的(c)可见,硼硫共掺杂多孔碳材料为电极,制备的对称超级电容器在0.5a
·
g-1
时呈现出200f
·
g-1
的高比电容,当安培密度增加到10a
·
g-1
时,它仍然具有116.4f
·
g-1
的比电容,显示出优异的倍率性能。由图16的(d),计算出超级电容器的能量密度为 6.94wh
·
kg-1
,功率密度为248.4w
·
kg-1
。
112.(10)将实施例1所得硼硫共掺杂多孔碳材料作为电极组装成对称超级电容器后,以1mol/l的na2so4为电解液,进行电化学测试,测试结果见图 17,图17中,(a)为在不同扫描速率下的cv曲线,(b)为在各种电流密度下的gcd图,(c)为比电容和安培密度关系曲线,(d)为ragone图。由图17的(a)可见,当电压增幅增加到1.8v时,cv曲线保持大致矩形和对称,没有明显的氧化还原峰,表明理想的电容行为。由图17的(b)可见, gcd曲线显示出完美的对称性和出色的可逆性。由图17的(c),根据放电时间,在1a
·
g-1
的安培密度下,比电容估计为142f
·
g-1
。电容随着电流密度的增加而减小。由图17的(d)可见,在450w
·
kg-1
的功率密度下,对称超级电容器的最大能量密度为16.65wh
·
kg-1
。按照对实施例1的测试方法测试实施例6~8所得硼硫共掺杂多孔碳材料作为电极组装成对称超级电容器,以1mol/l的na2so4为电解液时的能量密度,能量密度图见图18~20,其中,图18为实施例6所得硼硫共掺杂多孔碳材料在以na2so4为电解液的对称超级电容器体系的能量密度图;图19为实施例7所得硼硫共掺杂多孔碳材料在以na2so4为电解液的对称超级电容器体系的能量密度图;图20为实施例 8所得硼硫共掺杂多孔碳材料在以na2so4为电解液的对称超级电容器体系的能量密度图。由图18可见,实施例6所得硼硫共掺杂多孔碳材料作为电极组装成对称超级电容器的最大能量密度为12wh
·
kg-1
。由图19可见,实施例7所得硼硫共掺杂多孔碳材料作为电极组装成对称超级电容器的最大能量密度为12.5wh
·
kg-1
。由图20可见,实施例8所得硼硫共掺杂多孔碳材料作为电极组装成对称超级电容器的最大能量密度为11.3wh
·
kg-1
。
113.(11)将实施例1所得硼硫共掺杂多孔碳材料作为电极组装成对称超级电容器,以1mol/l的na2so4为电解液,进行循环寿命测试,测试结果见图 21。由图21可见,在10a
·
g-1
的电流密度下,在10000次循环后,对称超级电容器保持率约为97.09%。按照对实施例1的测试方法测试实施例6~8所得硼硫共掺杂多孔碳材料作为电极组装成对称超级电容器,以1mol/l的 na2so4为电解液时的循环寿命,循环寿命测试结果见图22~24,其中,图22 为实施例6所得硼硫共掺杂多孔碳材料在以na2so4为电解液的对称超级电容器体系的循环寿命测试图;图23为实施例7所得硼硫共掺杂多孔碳材料在以na2so4为电解液的对称超级电容器体系的循环寿命测试图;图24为实施例8所得硼硫共掺杂多孔碳材料在以na2so4为电解液的对称超级电容器体系的循环寿命测试图。由图22可见,实施例6所得硼硫共掺杂多孔碳材料
在10a
·
g-1
的电流密度下,在10000次循环后,对称超级电容器保持率约为98.2%。由图23可见,实施例7所得硼硫共掺杂多孔碳材料在10a
·
g-1
的电流密度下,在10000次循环后,对称超级电容器保持率约为97.6%。由图 24可见,实施例8所得硼硫共掺杂多孔碳材料在10a
·
g-1
的电流密度下,在 10000次循环后,对称超级电容器保持率约为100.67%。这样的结果表明,所制备的硼硫共掺杂多孔碳材料显示出优异的长期循环性能,循环寿命长。
114.以上所述仅是本发明的优选实施方式,应当指出,对于本技术领域的普通技术人员来说,在不脱离本发明原理的前提下,还可以做出若干改进和润饰,这些改进和润饰也应视为本发明的保护范围。