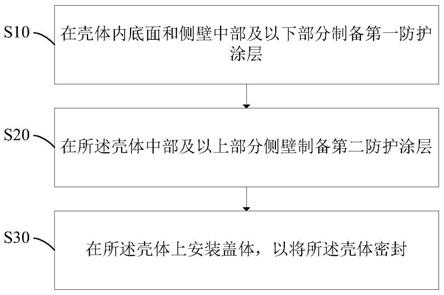
1.本发明涉及液态金属电池技术领域,特别涉及一种液态金属电池正极集流体的加工工艺及液态金属电池。
背景技术:2.2006年,“液态金属电池”的概念由美国麻省理工学院(mit)的sadoway 教授团队提出,液态金属电池,具体的说是通过熔融状态即液态金属的氧化还原反应,将化学能转化为电能;此电池工作模式下,电极均为液态金属,电解质为熔融态无机盐,电极与电解质由于密度不同且互不混溶而自然分层。
3.液态金属发展至今,诸多新型电化学体系先后被报道,包括mg-sb,ca-bi, ca-sb,li-bi,li-sb-pb,li-sb-sn等,液态金属电池具有无污染运行、高能量效率、灵活的功率和能量搭配输出等特征以及长寿命、低维护成本等优点,是应用前景非常好的储能技术。但是,电池300℃~700℃的工作温度电池正负极金属对绝缘部件和集流器会发生腐蚀行为,对电池的电化学性能产生影响,高温条件下,对电池关键部件的设计提出了较高的要求。在一些电极体系中,如正极材料为锡锑合金等的电池在运行过程中,液体的正极金属可以与电池不锈钢壳体发生合金化反应,电池运行一定时间后,底部的液态的正极金属会沿着电池的壳壁往上附着,我们称之为“爬壁”现象。这一现象会不仅造成壳体的缓慢腐蚀,会产生电池放电电压波动和容量衰减等影响,而且壳壁上正极金属的富集也容易使电池发生短路
技术实现要素:4.本发明的主要目的是提供一种液态金属电池壳体及其加工工艺,旨在解决现有技术中液态金属电池壳体缓慢腐蚀和负极尖端放电的技术问题。
5.为实现上述目的,本发明提出一种液态金属电池壳体的加工工艺,所述加工工艺包括:
6.在壳体内底面和侧壁下部分制备第一防护涂层;
7.在所述壳体上部分侧壁制备第二防护涂层;
8.在所述壳体上安装盖体,以将所述壳体密封。
9.可选地,在所述壳体内表面制备所述第一防护涂层和所述第二防护涂层可采用热喷涂、化学气相镀、磁控溅射等工艺中的一种或多种工艺,所述第一防护涂层和所述第二防护涂层采用的工艺可以相同或不同。
10.可选地,所述壳体内表面制备的所述第一防护涂层可以采用c、wc、w、 mo中的一种或多种。
11.可选地,所述壳体内表面制备的所述第二防护涂层可为一层或多层涂层,至少有一层为绝缘陶瓷涂层。
12.可选地,所述壳体内表面制备的所述第二防护涂层绝缘陶瓷层可采用碳化钨、氧化铝、氧化锆、氮化铝、氧化锆、碳化铬、氧化钛及氮化硼中的一种或多种材料制成。
13.可选地,所述壳体采用镍及镍合金、铜及铜合金、因瓦合金和不锈钢等当中的一种或多种材料制成。
14.可选地,所述第一防护涂层的厚度为10微米~100微米,且所述第一防护涂层和第二防护涂层的宽度小于或等于所述壳体的一半高度。
15.可选地,所述液态金属电池应用有如上述液态金属电池正极集流体的加工工艺制成的正极集流体。
16.本发明技术方案通过在所述壳体的壳体内底面和侧壁中部及以下部分附着所述第一防护涂层将所述壳体与液态金属电池正极隔开,从而改善液态金属电极与所述壳体之间的润湿行为和界面反应,同时也可改善正极金属及熔融电解质盐对所述壳体的腐蚀问题,避免正极金属出现“爬壁”现象造成电池容量衰减,甚至短路。通过在所述壳体的中部及以上部分侧壁附着第二防护涂层将所述液态金属电池负极与所述壳体隔开,避免正负极金属间导通,导致电池短路,同时改善负极尖端放电现象。
附图说明
17.为了更清楚地说明本发明实施例或现有技术中的技术方案,下面将对实施例或现有技术描述中所需要使用的附图作简单地介绍,显而易见地,下面描述中的附图仅仅是本发明的一些实施例,对于本领域普通技术人员来讲,在不付出创造性劳动的前提下,还可以根据这些附图示出的结构获得其他的附图。
18.图1为本发明加工工艺第一实施例的流程示意图;
19.图2为本发明液态金属电池正极集流体的结构示意图;
20.图3为本发明液态金属电池正极集流体的剖面结构示意图。
21.附图标号说明:
22.标号名称标号名称1盖体2壳体3第一防护涂层4第二防护涂层5负极集流体6负极金属7电解质8正极金属
23.本发明目的的实现、功能特点及优点将结合实施例,参照附图做进一步说明。
具体实施方式
24.下面将结合本发明实施例中的附图,对本发明实施例中的技术方案进行清楚、完整地描述,显然,所描述的实施例仅仅是本发明的一部分实施例,而不是全部的实施例。基于本发明中的实施例,本领域普通技术人员在没有作出创造性劳动前提下所获得的所有其他实施例,都属于本发明保护的范围。
25.需要说明,本发明实施例中所有方向性指示(诸如上、下、左、右、前、后
……
)仅用于解释在某一特定姿态(如附图所示)下各部件之间的相对位置关系、运动情况等,如果该特定姿态发生改变时,则该方向性指示也相应地随之改变。
26.另外,在本发明中如涉及“第一”、“第二”等的描述仅用于描述目的,而不能理解为指示或暗示其相对重要性或者隐含指明所指示的技术特征的数量。由此,限定有“第一”、“第二”的特征可以明示或者隐含地包括至少一个该特征。在本发明的描述中,“多个”的含义是至少两个,例如两个,三个等,除非另有明确具体的限定。
27.在本发明中,除非另有明确的规定和限定,术语“连接”、“固定”等应做广义理解,例如,“固定”可以是固定连接,也可以是可拆卸连接,或成一体;可以是机械连接,也可以是电连接;可以是直接相连,也可以通过中间媒介间接相连,可以是两个元件内部的连通或两个元件的相互作用关系,除非另有明确的限定。对于本领域的普通技术人员而言,可以根据具体情况理解上述术语在本发明中的具体含义。
28.另外,本发明各个实施例之间的技术方案可以相互结合,但是必须是以本领域普通技术人员能够实现为基础,当技术方案的结合出现相互矛盾或无法实现时应当认为这种技术方案的结合不存在,也不在本发明要求的保护范围之内。
29.本发明所指的“上下”是以图1所示的方位为基准,即本发明所指的“上下”对应图1的上下方位。
30.本发明提出了一种液态金属电池正极集流体的加工工艺,请参照图1,图 1为本发明所述加工工艺第一实施例的流程示意图,所述加工工艺具体包括以下步骤:
31.步骤s10:在壳体内底面和侧壁中部及以下部分制备第一防护涂层;
32.步骤s20:在所述壳体中部及以上部分侧壁制备第二防护涂层;
33.步骤s30:在所述壳体上安装盖体,以将所述壳体密封。
34.在本实施例中,请同时参照图2及图3,所述壳体2呈圆筒状设置,其中一端为闭口,另一端为开口,所述盖体1安装在所述壳体2开口的一端,从而与所述壳体2配合形成密闭的容置腔,从而所述容置腔内设置相应的液态金属等物质。所述盖体1和所述壳体2之间可采用焊接的方式安装,从而保证所述盖体1和所述壳体2连接的位置处具有良好的密封性能,防止电池泄漏。
35.需要说明的是,在本实施例中,所述壳体2的形状包括但不限于上述方案,所述壳体2的形状还可以是例如长方体、球体或者其他不规则形状皆可。具体可根据应用场景进行调整。在所述壳体2上安装所述盖体1之前,首先在所述壳体2的内表面下部分喷涂或者涂抹一层所述第一防护涂层3,其中所述壳体2的内表面是指所述壳体2在安装所述盖体1之后,形成密闭容置腔一侧的表面,外表面则是指背离该容置腔一侧的表面,所述盖体1同理。也即除所述壳体2开口一侧之外,任意一侧内壁均为所述壳体2的内表面,所述盖体1朝向该容置腔一侧的表面为内表面。
36.在喷涂或者涂抹所述第一防护涂层3后,通过所述第一防护涂层3,可以有效改善液态正极金属及熔融电解质盐对所述壳体2的腐蚀问题,以及出现“爬壁”现象引起电池短路。
37.在所述壳体2的内表面上部分喷涂或者涂抹上所述第二防护涂层4,通过所述第二防护涂层4对所述壳体2以及所述盖体1的外表面进行保护,防止所述壳体2或者所述盖体1的外表面氧化、生锈或者在使用过程中被划伤造成破裂等等问题,进一步提高液态金属电池在使用过程中的安全性以及可靠性,提高用户的使用体验。本实施例中,所述壳体2和/或所述盖体1可以采用例如镍及镍合金、铜及铜合金、因瓦合金和不锈钢等当中的一种或多种材料制成,利用上述合金刚度高、物理及化学性能稳定的特点,提高它所述壳体2的抗氧化性、耐蚀性、高温强度和改善某些物理性能。
38.此外,本实施例中,由于所述第一防护涂层3以及所述第二防护涂层4 均通过喷涂或者涂抹的方式覆盖在所述壳体2以及所述盖体1的表面上,相较于在所述壳体2内加装陶瓷套管等结构,本发明还能够尽可能减小所述壳体2的体积及重量,间接提高了液态金属电池的能量密度,具体的,所述第一防护涂层3的厚度为10微米~100微米,通过涂层的方式,能够尽可能减小所述壳体2内容置腔的容置空间,从而在同等的体积大小下,相较于现有技术中通过设置陶瓷套管的方式,本发明间接高了液态金属电池的能量密度,进一步提高了产品的竞争力以及用户的使用体验。所述壳体内表面制备的所述第一防护涂层3可以采用c、wc、w、mo中的一种或多种。所述壳体内表面制备的所述第二防护涂层4可为一层或多层涂层,至少有一层为绝缘陶瓷涂层,从而对所述壳体2进行保护,避免所述壳体2生锈,氧化,形成划痕以及不利用单体串并联成组使用等问题。
39.并且,所述第一防护涂层3的高度(a方向上的长度)大于或等于所述壳体2侧壁的厚度、小于或等于所述壳体2的高度(a方向上的长度),使所述壳体2与所述第一防护涂层3结构更加合理,且结构简单,易于操作,适用于大规模生产。
40.本发明技术方案通过在所述壳体2的壳体内底面和侧壁中部及以下部分附着所述第一防护涂层3将所述壳体与液态金属电池正极隔开,从而改善液态金属电极与所述壳体之间的润湿行为和界面反应,同时也可改善正极金属及熔融电解质盐对所述壳体的腐蚀问题,避免正极金属出现“爬壁”现象造成电池容量衰减,甚至短路。通过在所述壳体的中部及以上部分侧壁附着第二防护涂层将所述液态金属电池负极与所述壳体隔开,避免正负极金属间导通,导致电池短路,同时改善负极尖端放电现象。
41.在所述壳体2内表面制备所述第一防护涂层3和所述第二防护涂层4可采用热喷涂、化学气相镀、磁控溅射等工艺中的一种或多种工艺,所述第一防护涂层3和所述第二防护涂层4采用的工艺可以相同或不同。采所述第一防护涂层3的喷涂方式包括但不限于上述方案,同时所述第二防护涂层4的喷涂方式也可以采用上述相同的工艺。以等离子喷涂方式为例,将所述第一防护涂层3的原料,通过喷枪均匀喷涂在所述壳体2的内表面上,所述第一防护涂层3采用陶瓷特层和/或金属涂层,从而使所述壳体2的内表面具有耐磨、耐蚀、耐高温氧化、电绝缘、隔热、防辐射、减磨和密封等性能。
42.进一步地,所述壳体内表面制备的所述第二防护涂层绝缘陶瓷层可采用碳化钨、氧化铝、氧化锆、氮化铝、氧化锆、碳化铬、氧化钛及氮化硼中的一种或多种材料制成。首先准备好所述喷涂粉末,对所述喷涂粉末进行干燥过筛,从而保证所述喷涂粉末均匀,以保证后续加工质量。随后将干燥过筛后的所述喷涂粉末加热,使其加热到熔融或半熔融状态,再进行热气流雾化,从而便于通过喷枪进行喷涂,同时也能够进一步加速形成粒子流,将雾化后的所述喷涂粉末喷涂在所述壳体2的内表面,粒子与所述壳体2内表面发生碰撞、变形、凝固和堆积后,形成所述第二防护涂层4。
43.此外,在对所述壳体2的内表面进行喷涂之前,还需要对所述壳体2的内表面进行预处理,首先对所述壳体2的内表面进行乙醇超声清洗,防止所述壳体2的内表面上附着有其他杂物,提高喷涂质量,防止对所述壳体2后续使用过程中造成影响。随后对所述壳体2的表面进行喷砂粗化,提高所述第一防护涂层3的附着力,从而保证喷涂所述第一防护涂层3时,粒子流能够牢固附着在所述壳体2的内表面上,保证本发明所述加工工艺的稳定性及可靠性。
44.此外,为解决上述问题,本发明还提出了一种液态金属电池,所述液态金属电池应用有如上述液态金属电池正极集流体的加工工艺制成的正极集流体。
45.本发明提出了一种液态金属电池正极集流体的加工工艺,请参照图1,图 1为本发明所述加工工艺第一实施例的流程示意图,所述加工工艺具体包括以下步骤:
46.步骤s10:在壳体内底面和侧壁中部及以下部分制备第一防护涂层;
47.步骤s20:在所述壳体中部及以上部分侧壁制备第二防护涂层;
48.步骤s30:在所述壳体上安装盖体,以将所述壳体密封。
49.在本实施例中,所述壳体2呈圆筒状设置,其中一端为闭口,另一端为开口,所述盖体1安装在所述壳体2开口的一端,从而与所述壳体2配合形成密闭的容置腔,从而所述容置腔内设置相应的液态金属等物质。所述盖体1 和所述壳体2之间可采用焊接的方式安装,从而保证所述盖体1和所述壳体2 连接的位置处具有良好的密封性能,防止电池泄漏。
50.需要说明的是,在本实施例中,所述壳体2的形状包括但不限于上述方案,所述壳体2的形状还可以是例如长方体、球体或者其他不规则形状皆可。具体可根据应用场景进行调整。在所述壳体2上安装所述盖体1之前,首先在所述壳体2的内表面下部分喷涂或者涂抹一层所述第一防护涂层3,其中所述壳体2的内表面是指所述壳体2在安装所述盖体1之后,形成密闭容置腔一侧的表面,外表面则是指背离该容置腔一侧的表面,所述盖体1同理。也即除所述壳体2开口一侧之外,任意一侧内壁均为所述壳体2的内表面,所述盖体1朝向该容置腔一侧的表面为内表面。
51.在喷涂或者涂抹所述第一防护涂层3后,通过所述第一防护涂层3,可以有效改善液态正极金属及熔融电解质盐对所述壳体2的腐蚀问题,以及出现“爬壁”现象引起电池短路。
52.在所述壳体2的内表面上部分喷涂或者涂抹上所述第二防护涂层4,通过所述第二防护涂层4对所述壳体2以及所述盖体1的外表面进行保护,防止所述壳体2或者所述盖体1的外表面氧化、生锈或者在使用过程中被划伤造成破裂等等问题,进一步提高液态金属电池在使用过程中的安全性以及可靠性,提高用户的使用体验。本实施例中,所述壳体2和/或所述盖体1可以采用例如镍及镍合金、铜及铜合金、因瓦合金和不锈钢等当中的一种或多种材料制成,利用上述合金刚度高、物理及化学性能稳定的特点,提高它所述壳体2的抗氧化性、耐蚀性、高温强度和改善某些物理性能。
53.此外,本实施例中,由于所述第一防护涂层3以及所述第二防护涂层4 均通过喷涂或者涂抹的方式覆盖在所述壳体2以及所述盖体1的表面上,相较于在所述壳体2内加装陶瓷套管等结构,本发明还能够尽可能减小所述壳体2的体积及重量,间接提高了液态金属电池的能量密度,具体的,所述第一防护涂层3的厚度为10微米~100微米,通过涂层的方式,能够尽可能减小所述壳体2内容置腔的容置空间,从而在同等的体积大小下,相较于现有技术中通过设置陶瓷套管的方式,本发明间接高了液态金属电池的能量密度,进一步提高了产品的竞争力以及用户的使用体验。所述壳体内表面制备的所述第一防护涂层3可以采用c、wc、w、mo中的一种或多种。所述壳体内表面制备的所述第二防护涂层4可为一层或多层涂层,至少有一层为绝缘陶瓷涂层,从而对所述壳体2进行保护,避免所述壳体2生锈,氧化,形成划痕以及不利用单体串并联成组使用等问题。
54.并且,所述第一防护涂层3的高度(a方向上的长度)大于或等于所述壳体2侧壁的
厚度、小于或等于所述壳体2的高度(a方向上的长度),使所述壳体2与所述第一防护涂层3结构更加合理,且结构简单,易于操作,适用于大规模生产。
55.本发明技术方案通过在所述壳体2的壳体内底面和侧壁中部及以下部分附着所述第一防护涂层3将所述壳体与液态金属电池正极隔开,从而改善液态金属电极与所述壳体之间的润湿行为和界面反应,同时也可改善正极金属及熔融电解质盐对所述壳体的腐蚀问题,避免正极金属出现“爬壁”现象造成电池容量衰减,甚至短路。通过在所述壳体的中部及以上部分侧壁附着第二防护涂层将所述液态金属电池负极与所述壳体隔开,避免正负极金属间导通,导致电池短路,同时改善负极尖端放电现象。
56.在所述壳体2内表面制备所述第一防护涂层3和所述第二防护涂层4可采用热喷涂、化学气相镀、磁控溅射等工艺中的一种或多种工艺,所述第一防护涂层3和所述第二防护涂层4采用的工艺可以相同或不同。采所述第一防护涂层3的喷涂方式包括但不限于上述方案,同时所述第二防护涂层4的喷涂方式也可以采用上述相同的工艺。以等离子喷涂方式为例,将所述第一防护涂层3的原料,通过喷枪均匀喷涂在所述壳体2的内表面上,所述第一防护涂层3采用陶瓷特层和/或金属涂层,从而使所述壳体2的内表面具有耐磨、耐蚀、耐高温氧化、电绝缘、隔热、防辐射、减磨和密封等性能。
57.进一步地,所述壳体内表面制备的所述第二防护涂层绝缘陶瓷层可采用碳化钨、氧化铝、氧化锆、氮化铝、氧化锆、碳化铬、氧化钛及氮化硼中的一种或多种材料制成。首先准备好所述喷涂粉末,对所述喷涂粉末进行干燥过筛,从而保证所述喷涂粉末均匀,以保证后续加工质量。随后将干燥过筛后的所述喷涂粉末加热,使其加热到熔融或半熔融状态,再进行热气流雾化,从而便于通过喷枪进行喷涂,同时也能够进一步加速形成粒子流,将雾化后的所述喷涂粉末喷涂在所述壳体2的内表面,粒子与所述壳体2内表面发生碰撞、变形、凝固和堆积后,形成所述第二防护涂层4。
58.此外,在对所述壳体2的内表面进行喷涂之前,还需要对所述壳体2的内表面进行预处理,首先对所述壳体2的内表面进行乙醇超声清洗,防止所述壳体2的内表面上附着有其他杂物,提高喷涂质量,防止对所述壳体2后续使用过程中造成影响。随后对所述壳体2的表面进行喷砂粗化,提高所述第一防护涂层3的附着力,从而保证喷涂所述第一防护涂层3时,粒子流能够牢固附着在所述壳体2的内表面上,保证本发明所述加工工艺的稳定性及可靠性。
59.以上所述仅为本发明的优选实施例,并非因此限制本发明的专利范围,凡是在本发明的发明构思下,利用本发明说明书及附图内容所作的等效结构变换,或直接/间接运用在其他相关的技术领域均包括在本发明的专利保护范围内。