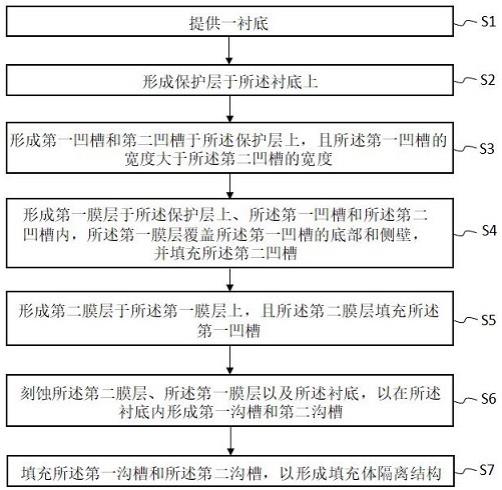
1.本发明涉及半导体技术领域,特别涉及一种半导体隔离结构的制造方法。
背景技术:2.图像传感器一般包括逻辑区域和像素区域,在现有的沟槽隔离工艺中,逻辑区域以及像素区域采用不同的沟槽隔离成形方法。其中,像素区的沟槽和逻辑区的沟槽需要经过二次刻蚀以达到较深的深度。但是,通过两次干法刻蚀工艺形成沟槽之后,逻辑区域与像素区域的沟槽的顶部表面存在高度差,容易产生多晶硅残留的问题,并对衬底表面造成二次损伤。
3.因此,如何改善沟槽的成形工艺,消除沟槽表面的高度差,避免衬底的二次损伤已经成为亟需解决的问题。
技术实现要素:4.鉴于上述现有技术的不足,本技术提出一种半导体隔离结构的制造方法,旨在,以消除逻辑区域和像素区域表面沟槽的高度差,避免衬底的二次损伤。
5.为实现上述目的及其他目的,本技术提出一种半导体隔离结构的制造方法,包括:提供一衬底;形成保护层于所述衬底上;形成第一凹槽和第二凹槽于所述保护层上,且所述第一凹槽的宽度大于所述第二凹槽的宽度;形成第一膜层于所述保护层上、所述第一凹槽和所述第二凹槽内,所述第一膜层覆盖所述第一凹槽的底部和侧壁,并填充所述第二凹槽;形成第二膜层于所述第一膜层上,且所述第二膜层填充所述第一凹槽;刻蚀所述第二膜层、所述第一膜层以及所述衬底,以在所述衬底内形成第一沟槽和第二沟槽;以及填充所述第一沟槽和所述第二沟槽,以形成填充体隔离结构;其中,所述第二膜层的蚀刻率大于所述第一膜层的蚀刻率。
6.可选地,形成所述第一凹槽和所述第二凹槽于所述保护层上的方法包括将所述第一凹槽和所述第二凹槽刻蚀至所述衬底的上表面。
7.可选地,形成填充体隔离结构的方法包括:移除所述衬底表面的填充体和所述衬底表面的所述保护层。
8.可选地,所述填充体的上表面与所述衬底的上表面在同一平面上。
9.可选地,所述第一沟槽与所述第一凹槽的中心轴线重合,且所述第二沟槽与所述第二凹槽的中心轴线重合。
10.可选地,所述第一膜层位于所述保护层上的厚度范围为10-15nm。
11.可选地,所述第二膜层位于非凹槽区内的所述第一膜层上的厚度范围为25-35nm。
12.可选地,所述第一沟槽于所述衬底中的深度大于所述第二沟槽于所述衬底中的深度。
13.可选地,所述第一沟槽的底面积小于所述第一沟槽的开口面积。
14.可选地,所述第二沟槽的底面积与所述第二沟槽的开口面积相等。
15.综上所述,本技术一种半导体隔离结构的制造方法。在衬底和保护层上设置不同蚀刻率的膜层,改进了沟槽的成形工艺,将两次光罩形成沟槽改进为一次光罩形成沟槽。消除了沟槽表面的高度差,避免了对衬底的二次损伤。通过调整不同膜层的蚀刻率,可以获取不同形状的沟槽。
16.附图说明:图1为本技术在一实施例中的半导体隔离结构制造方法流程示意图;图2为本技术在一实施例中的保护层示意图;图3为本技术在一实施例中的光刻胶层示意图;图4为本技术在一实施例中的掩膜版结构示意图;图5为本技术在一实施例中的沟槽结构示意图;图6为本技术在一实施例中的第一膜层示意图;图7为本技术在一实施例中的第二膜层示意图;图8为本技术在一实施例中的保护层表面示意图;图9为本技术在一实施例中的第一阶段沟槽刻蚀示意图;图10为本技术在一实施例中的第二阶段沟槽刻蚀示意图;图11为本技术在一实施例中的第三阶段沟槽刻蚀示意图;图12为本技术在一实施例中的沟槽结构示意图;图13为本技术在一实施例中的填充体示意图;图14为本技术在一实施例中的填充体平坦化示意图。
17.附图标记说明:10
ꢀꢀꢀꢀꢀꢀꢀꢀ
衬底;101
ꢀꢀꢀꢀꢀꢀꢀ
第一沟槽;102
ꢀꢀꢀꢀꢀꢀꢀ
第二沟槽;20
ꢀꢀꢀꢀꢀꢀꢀꢀ
保护层;201
ꢀꢀꢀꢀꢀꢀꢀ
氧化保护层;202
ꢀꢀꢀꢀꢀꢀꢀ
氮化保护层;30
ꢀꢀꢀꢀꢀꢀꢀꢀ
凹槽;301
ꢀꢀꢀꢀꢀꢀꢀ
第一凹槽;302
ꢀꢀꢀꢀꢀꢀꢀ
第二凹槽;40
ꢀꢀꢀꢀꢀꢀꢀꢀ
光刻胶层;50
ꢀꢀꢀꢀꢀꢀꢀꢀ
掩膜版;60
ꢀꢀꢀꢀꢀꢀꢀꢀ
第一膜层;70
ꢀꢀꢀꢀꢀꢀꢀꢀ
第二膜层;80
ꢀꢀꢀꢀꢀꢀꢀꢀ
填充体;801
ꢀꢀꢀꢀꢀꢀꢀ
第一填充体;
802
ꢀꢀꢀꢀꢀꢀꢀ
第二填充体。
具体实施方式
18.以下通过特定的具体实例说明本发明的实施方式,本领域技术人员可由本说明书所揭露的内容轻易地了解本发明的其他优点与功效。本发明还可以通过另外不同的具体实施方式加以实施或应用,本说明书中的各项细节也可以基于不同观点与应用,在没有背离本发明的精神下进行各种修饰或改变。
19.需要说明的是,本实施例中所提供的图示仅以示意方式说明本发明的基本构想,遂图式中仅显示与本发明中有关的组件而非按照实际实施时的组件数目、形状及尺寸绘制,其实际实施时各组件的型态、数量及比例可为一种随意的改变,且其组件布局型态也可能更为复杂。
20.图像传感器中的逻辑区域和像素区域有着不同的集成度要求,使用二次蚀刻法分别形成逻辑区域和像素区域的沟槽时,容易在沟槽的顶部表面产生高度差。所以二次蚀刻法形成沟槽容易导致多晶硅残留,并对衬底表面造成二次损伤。
21.请参阅图1,图1为本技术在一实施例中的半导体隔离结构制造方法流程示意图。本技术提出一种半导体隔离结构的制造方法,在本实施例中,半导体隔离结构的制造方法可以包括以下步骤:s1、提供一衬底;s2、形成保护层于所述衬底上;s3、形成第一凹槽和第二凹槽于所述保护层上,且所述第一凹槽的宽度大于所述第二凹槽的宽度;s4、形成第一膜层于所述保护层上、所述第一凹槽和所述第二凹槽内,所述第一膜层覆盖所述第一凹槽的底部和侧壁,并填充所述第二凹槽;s5、形成第二膜层于所述第一膜层上,且所述第二膜层填充所述第一凹槽;s6、刻蚀所述第二膜层、所述第一膜层以及所述衬底,以在所述衬底内形成第一沟槽和第二沟槽;s7、填充所述第一沟槽和所述第二沟槽,以形成填充体隔离结构。
22.请参阅图2,图2为本技术在一实施例中的保护层示意图。在步骤s1中,提供一衬底10,在本技术的一些实施例中,衬底10的材料可以为例如硅、锗、锗化硅、碳化硅、砷化镓、镓化铟或者其它iii/v族化合物半导体。衬底10还可以包括半导体构成的多层结构,例如为绝缘体上硅、绝缘体上层叠硅、绝缘体上层叠锗化硅、绝缘体上锗化硅或者绝缘体上锗等。在本技术的一个实施例中,衬底10的材料可以为例如硅衬底。在本技术的一实施例中,衬底10可以用于形成例如cis(cmos image sensor,cmos图像传感器),衬底10可以包括例如像素区域和逻辑区域,像素区域用来检测光电二极管,而逻辑区域用来将检测到的光信号处理为电信号以获取光学数据。
23.请参阅图2,在本技术的一实施例中,在步骤s2中,形成保护层20于衬底10的上表面。保护层20可以包括氧化保护层201和氮化保护层202。氧化保护层201可以设置在衬底10的上表面,氮化保护层202可以设置在氧化保护层201的上表面。首先清洗衬底10的表面,去除衬底10表面的杂质颗粒或其它污染物。然后在衬底10上形成氧化保护层201,形成氧化保
护层201的方法可以为例如高温炉管氧化法、快速热氧化法、原位水蒸气产生氧化法或其他方法。氧化保护层201的厚度范围可以为例如150-200埃,例如为170埃。氧化保护层201的材料可以为例如二氧化硅材质。在本技术的一实施例中,对衬底10进行热氧化以形成保护氧化层201。在保护氧化层201的表面进行氮化物淀积,以形成氮化保护层202。氮化保护层202在进行化学机械抛光时可以充当抛光的阻挡材料。氮化保护层202的材料可以为例如氮化硅,氮氧化物、金属氮化物或者其他材料。氮化保护层202可以通过例如低压化学气相沉积,次大气压化学气相沉积,常压化学气相沉积,离子体增强化学气相沉积或高密度等离子体化学气相淀积等方法形成。在利用低压化学气相淀积工艺制备氮化保护层202时,可以通过氨气和二氯硅烷发生反应生成氮化硅,反应温度可以为例如750摄氏度。氮化保护层202的应力较大,在衬底10上形成氮化保护层202时,容易在衬底10表面造成位错。氧化保护层201用于在形成氮化保护层202时提供缓冲,避免在衬底10上产生位错的问题。氧化保护层201同时可以作为化学机械研磨平坦化沟槽中填充的介质材料的停止层。
24.请参阅图3-5,图3为本技术在一实施例中的光刻胶层示意图。图4为本技术在一实施例中的掩膜版结构示意图。图5为本技术在一实施例中的沟槽结构示意图。在步骤s3中,形成第一凹槽301和第二凹槽302于保护层20上,且第一凹槽301的宽度大于第二凹槽302的宽度。去除部分保护层20,以形成凹槽30。首先在氮化保护层202上旋涂一层光刻胶层40,通过掩膜版50进行紫外线曝光。将所要蚀刻的衬底10的第一沟槽101和第二沟槽102范围内的光刻胶薄膜通过显影、曝光的方式清洗,以便在保护层内形成凹槽30。在对光刻胶薄膜进行清洗时可以使用清洗剂,以去除光刻胶层104。清洗剂可以为例如包括醇胺、硼酸及其衍生物的混合液。在本技术的一实施例中,凹槽30可以包括第一凹槽301和第二凹槽302。第一凹槽301和第二凹槽302刻蚀至衬底10的上表面。经过光刻之后,用离子和强腐蚀性的化学物质把没有被光刻胶保护的区域的氮化硅、氧化硅和硅刻蚀掉。当使用等离子体干法刻蚀时,刻蚀气体可以为例如四氟化碳和三氟甲烷。刻蚀气体的压强取值范围可以为例如10mt~20mt。气体流量的取值范围可以为例如50sccm~130sccm。刻蚀时间的取值范围可以为例如10s~40s。显影后通过干法刻蚀去除曝露的氮化保护层202和氧化保护层201。图像传感器中包括逻辑区域和像素区域,在本技术的一些实施例中,第一凹槽301可以设置在逻辑区域内,第二凹槽302可以设置在像素区域内。第一凹槽301和第二凹槽302的数量可以为多个。在本技术的一实施例中,第一凹槽301的宽度宽度可以大于第二凹槽302的宽度宽度。第一凹槽301和第二凹槽302刻蚀至衬底10的上表面,为后续对衬底10的刻蚀定位,也为第一膜层60和第二膜层70提供了空间。
25.请参阅图6,图6为本技术在一实施例中的第一膜层示意图。在步骤s4中,形成第一膜层60于保护层20上以及第一凹槽301和第二凹槽302内,第一膜层60覆盖第一凹槽301的底部和侧壁。形成第一膜层60于凹槽30的底部,且第一膜层60覆盖保护层20。第一膜层60可以覆盖第一凹槽301的底部和侧壁,并填充第二凹槽302。在本技术的一实施例中,第一膜层60可以覆盖在氮化保护层202的上表面。第一膜层60可以通过例如低压化学气相沉积,次大气压化学气相沉积,常压化学气相沉积,离子体增强化学气相沉积或高密度等离子体化学气相淀积等方法形成。在本技术的一实施例中,第一膜层60可以使用ald(atomic layer deposition,原子层沉积法)进行制备。将气相前驱体交替地通入反应器,并在沉积基体形成沉积膜。ald在沉积过程中,反应前驱体交替沉积,每次反应只沉积一层原子。ald沉积材
料可以包括例如al2o3、cao、tan
x
、sio2或其他材料。ald沉积过程可有效控制薄膜的厚度和均匀性,实现高深宽比孔道的均匀覆盖。ald的反应温度范围可以为例如50-500℃,工作压力范围可以为例如0.1-10mbar,所沉积薄膜在保护层20上的的厚度范围可以为例如10-15nm。ald工艺可以在真空中相对低温下进行,并能够有效应用于敏感表面。
26.请参阅图7,图7为本技术在一实施例中的第二膜层示意图。在步骤s5中,形成第二膜层70于第一膜层60上,且第二膜层70填充第一凹槽301。形成第二膜层70于第一膜层60上。在本技术的一实施例中,第一膜层60覆盖第一凹槽301的底部和侧壁。第二膜层70可以填充在第一凹槽301内部,并覆盖于第一膜层60上。在本技术的一实施例中,第一凹槽301内可以包括第一膜层60和第二膜层70。第二凹槽302内可以被第一膜层60填充。在本技术的一实施例中,第二膜层70的蚀刻率可以大于第一膜层60的蚀刻率。第二膜层70可以通过例如低压化学气相沉积,次大气压化学气相沉积,常压化学气相沉积,离子体增强化学气相沉积或高密度等离子体化学气相淀积等方法形成。在本技术的一实施例中,第二膜层70可以使用lpcvd(low-pressure cvd,低压化学气相沉积法)工艺进行制备。使用lpcvd法沉积的薄膜材料可以为例如氮化硅、磷硅玻璃、掺杂多晶硅或其他材料。工作温度范围可以为例如400-450℃,所沉积的薄膜在非凹槽区内的第一膜层60上的厚度范围可以为例如25-35nm。lpcvd法具备较高的沉积速率,可以大大降低颗粒污染源。
27.请参阅图8-12,图8为本技术在一实施例中的保护层表面示意图。在本技术的一实施例中,在步骤s6中,刻蚀第二膜层70、第一膜层60以及衬底10,以在衬底10内形成第一沟槽101和第二沟槽102。刻蚀衬底10,以形成第一沟槽101和第二沟槽102。在本技术的一些实施例中,在完成步骤s5之后,可以使用cmp (chemical mechanical polishing,化学机械抛光)工艺或者干法刻蚀将氮化保护层202、第一凹槽301以及第二凹槽302之外的第一膜层60和第二膜层70去除,并对凹槽30及其下方的衬底10进行刻蚀。刻蚀气体可以为氯气、溴化氢或者溴化氢与其它气体的混合气体。在本技术的一实施例中,可以使用例如化学机械抛光工艺将氮化保护层202、第一凹槽301以及第二凹槽302之外的第一膜层60和第二膜层70去除。使用抛光液,将上述工件在一定的下压力中相对于抛光垫作旋转运动,借助磨粒的机械磨削及化学氧化剂的腐蚀作用来完成对工件表层材料的去除。抛光液可以为例如超细颗粒、化学氧化剂与液体介质的混合液。
28.请参阅图9和图6-7,图9为本技术在一实施例中的第一阶段沟槽刻蚀示意图。在本技术的一些实施例中,对沟槽进行刻蚀可以是一个连续的过程,也可以按照时间段间歇进行刻蚀。在本技术的其他实施例中,沟槽刻蚀还可以包括第四阶段、第五阶段或其他所需阶段。在本技术的一实施例中,第二膜层70的蚀刻率可以大于第一膜层60的蚀刻率。在第一凹槽301内,第一膜层60覆盖在第一凹槽301的底面和侧壁,而第二膜层70对第一凹槽301进行填充。在刻蚀的初始阶段,由于第二膜层70的蚀刻率可以大于第一膜层60的蚀刻率,相同时间内,第一凹槽301内的刻蚀深度大于第二凹槽302内的刻蚀深度。
29.请参阅图10和图6-7,图10为本技术在一实施例中的第二阶段沟槽刻蚀示意图。在本技术的一实施例中,继续对第一凹槽301和第二凹槽302中的第一膜层60和第二膜层70进行刻蚀。第一凹槽301内刻蚀深度大于氮化保护层202的厚度,同时第二凹槽302内的第一膜层60同步进行刻蚀。在上述刻蚀过程中,第一凹槽301内的刻蚀深度始终大于第二凹槽302内的刻蚀深度。
30.请参阅图11和图6-7,图11为本技术在一实施例中的第三阶段沟槽刻蚀示意图。在本技术的一实施例中,第一凹槽301内的第一膜层60和第二膜层70被刻蚀穿透,进而继续对所暴露出的衬底10的上表面进行刻蚀。此时,第二凹槽302中的第一膜层60仍未刻蚀完毕。第二膜层70的蚀刻率大于第一膜层60的蚀刻率,且两者的蚀刻率差别较大,在第一凹槽301内可以刻蚀出例如上宽下窄的倒梯形轮廓。在对第一凹槽301下方的衬底10进行蚀刻时,将上述倒梯形轮廓映射倒衬底10内部。而第二凹槽302中存在第一膜层60,其在衬底10上刻蚀出的形状可以例如为矩形。
31.请参阅图12和图6-7,图12为本技术在一实施例中的沟槽结构示意图。在本技术的一实施例中,第一凹槽301内的第一膜层60和第二膜层70被刻蚀穿透,进而继续对所暴露出的衬底10的上表面进行刻蚀。第二凹槽302中的第一膜层60被刻蚀穿透,同时也对所暴露出的衬底10的上表面进行刻蚀。在完成对第一凹槽301下方的衬底10的蚀刻后,在衬底10内形成第一沟槽101。在完成对第二凹槽302下方的衬底10的蚀刻后,在衬底10内形成第二沟槽102。
32.请参阅图12,在本技术的一实施例中,第一沟槽101位于第一凹槽301的正下方。第二膜层70的蚀刻率大于第一膜层60的蚀刻率时,第一凹槽301内的第二膜层70的蚀刻速度大于第一凹槽301内的第一膜层60的蚀刻速度。在第一凹槽301内形成例如倒梯形结构,将第一凹槽301内的倒梯形结构复刻在衬底10上,形成第一沟槽101。蚀刻完成后,第二沟槽102位于第二凹槽302的正下方。第二凹槽302内部被第一膜层60覆盖,由于不存在不同蚀刻率膜层之间的蚀刻速度的差异,所以在第二凹槽302内形成矩形结构。蚀刻完成后,将第二凹槽302内的矩形结构复刻在衬底10上,形成第二沟槽102。在本实施例中,第二膜层70的蚀刻率大于第一膜层60的蚀刻率,在衬底10上获取的第一沟槽101的深度大于第二沟槽102的深度。
33.请参阅图13,图13为本技术在一实施例中的填充体示意图。在本技术的一实施例中,在步骤s7中,填充第一沟槽101和第二沟槽102,以形成填充体隔离结构。对第一沟槽101和第二沟槽102进行填充体80的填充。填充体80可以包括第一填充体801和第二填充体802,第一填充体801可以位于第一沟槽101内,第二填充体802可以位于第二沟槽102内。第一填充体801在填充第一沟槽101之后继续填充第一凹槽301,第二填充体802在填充第二沟槽102之后继续填充第二凹槽302。在本技术的其他实施例中,还可以先对第一沟槽101和第二沟槽102的侧壁及顶角进行热氧化。在第一沟槽101和第二沟槽102中形成热氧化侧壁及热氧化圆化顶角,以提高隔离性能。通过等离子体增强化学气相沉积工艺在第一沟槽101和第二沟槽102上形成填充体80。填充体80的材料可以为例如二氧化硅、氮化硅、氮氧化硅、氟硅玻璃、未掺杂的硅盐酸玻璃、正硅酸四乙酯或其他材料。在本技术的一实施例中,在第一沟槽101和第二沟槽102中添加填充体80的工艺可以使用例如高深宽比沉积工艺、旋转涂布法、流动化学气相沉积法或者其他方法实现。
34.请参阅图14,图14为本技术在一实施例中的填充体平坦化示意图。第一填充体801和第二填充体802填充完成之后,需要移除部分填充体80,以形成具有隔离作用的第一沟槽101和第二沟槽102。移除衬底10表面的填充体80和衬底10表面的保护层20。可以使用例如化学机械研磨工艺去除衬底10上表面的氧化保护层201、氮化保护层202以及填充体80。可以通过例如化学机械研磨工艺对沟槽70进行平坦化处理。例如将衬底10放置在研磨垫上,
使得衬底10与研磨垫接触,然后对衬底10上的填充体80进行研磨。在本技术的一实施例中,例如通过稀释的氢氟酸将位于衬底10顶部的填充体80移除掉,通过稀释的氢氟酸将氮化保护层202移除。对填充物700进行平坦化处理,去除残余的氮化硅和二氧化硅。在本技术的另一实施例中,可以在衬底10的表面生长一层新的热氧化层作为牺牲氧化层,以减少界面缺陷。在进行化学机械研磨时,工件在一定的下压力中相对于抛光垫作旋转运动,使用抛光液,借助磨粒的机械磨削及化学氧化剂的腐蚀作用来完成对工件表层材料的去除。抛光液可以为例如超细颗粒、化学氧化剂与液体介质的混合液。在本技术的其他实施例中,还可以使用湿法刻蚀工艺去除衬底10上表面的氧化保护层201、氮化保护层202以及填充体80,例如采用磷酸溶液进行湿法刻蚀。
35.综上所述,本技术提出一种半导体隔离结构的制造方法。在衬底和保护层上设置不同蚀刻率的膜层,改进了沟槽的成形工艺,将两次光罩形成沟槽改进为一次光罩形成沟槽。消除了沟槽表面的高度差,避免了对衬底的二次损伤。通过调整不同膜层的蚀刻率,可以获取不同形状的沟槽。
36.本发明所示实施例的上述描述(包括在说明书摘要中所述的内容)并非意在详尽列举或将本发明限制到本文所公开的精确形式。尽管在本文仅为说明的目的而描述了本发明的具体实施例和本发明的实例,但是正如本领域技术人员将认识和理解的,各种等效修改是可以在本发明的精神和范围内的。如所指出的,可以按照本发明所述实施例的上述描述来对本发明进行这些修改,并且这些修改将在本发明的精神和范围内。
37.本文已经在总体上将系统和方法描述为有助于理解本发明的细节。此外,已经给出了各种具体细节以提供本发明实施例的总体理解。然而,相关领域的技术人员将会认识到,本发明的实施例可以在没有一个或多个具体细节的情况下进行实践,或者利用其它装置、系统、配件、方法、组件、材料、部分等进行实践。在其它情况下,并未特别示出或详细描述公知结构、材料和/或操作以避免对本发明实施例的各方面造成混淆。
38.因而,尽管本发明在本文已参照其具体实施例进行描述,但是修改自由、各种改变和替换意在上述公开内,并且应当理解,在某些情况下,在未背离所提出发明的范围和精神的前提下,在没有对应使用其他特征的情况下将采用本发明的一些特征。因此,可以进行许多修改,以使特定环境或材料适应本发明的实质范围和精神。本发明并非意在限制到在下面权利要求书中使用的特定术语和/或作为设想用以执行本发明的最佳方式公开的具体实施例,但是本发明将包括落入所附权利要求书范围内的任何和所有实施例及等同物。因而,本发明的范围将只由所附的权利要求书进行确定。
39.以上描述仅为本技术的较佳实施例以及对所运用技术原理的说明,本领域技术人员应当理解,本技术中所涉及的发明范围,并不限于上述技术特征的特定组合而成的技术方案,同时也应涵盖在不脱离所述发明构思的情况下,由上述技术特征或其等同特征进行任意组合而形成的其它技术方案,例如上述特征与本技术中公开的(但不限于)具有类似功能的技术特征进行互相替换而形成的技术方案。除说明书所述的技术特征外,其余技术特征为本领域技术人员的已知技术,为突出本发明的创新特点,其余技术特征在此不再赘述。