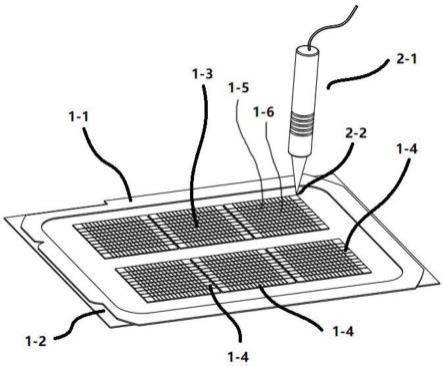
1.本发明涉及芯片封装检测技术领域,尤其涉及一种用于半导体封装芯片分离切割飞边的工艺。
背景技术:2.现有的半导体封装工序中,注塑机将芯片、引线和金属引线边框用树脂材料包裹,形成整条的基板,将基板贴合在承载膜上,承载膜一般为uv膜、蓝膜或绿膜,切割机将基板在承载膜上切割成独立的封装半导体单元。
3.由于金属引线边框和塑封面积大于芯片面积,在每条基板的芯片区域四周边缘会产生“飞边”,即金属引线边框和塑封的边缘区域的废料。整条的基板经切割后,飞边形成细碎的“切割飞边”,“切割飞边”混入芯片,会在后道检验工序中频繁引发检测设备的报警和停机,大大降低生产效率,因此切割飞边必须剔除,防止与芯片混料。
4.切割飞边的剔除一般需要人工操作,手工将切割飞边从承载膜上铲下。因为承载膜有较强的弹性,变形量大,且薄而易破,一旦承载膜被铲破,就无法继续铲边工作。因此铲飞边工序至今无法实现自动化。
5.上述现有的工序中,大部分企业使用人工将切割飞边铲下,这种方式容易存在以下缺陷:一是铲飞边的过程容易产生静电损伤芯片;二是人工操作容易产生刮蹭,损伤芯片;三是容易将芯片误铲混入切割飞边。还有的企业使用人工贴胶带封住切割飞边,再使芯片从承载膜上脱落,而切割飞边被胶带固定在承载膜上,但是该方法存在以下缺陷:一是效率低下,贴胶带非常耗费人工;二是切割飞边往往不能很好的被粘附在胶带上,仍有一部分飞边混入芯片,再次从芯片中挑选飞边则更耗费人工,难以将飞边清理干净。
6.在现有的工艺中,在芯片外观检验工序中,需要用针尖或镊子在放大镜或显微镜下将不良品芯片从承载膜上剔除出来,该工序同样耗费大量人力。
技术实现要素:7.针对现有技术不足,本发明的目的在于提供一种用于半导体封装芯片分离切割飞边的工艺。
8.为了实现上述目的,本发明一实施例提供的技术方案如下:
9.一种用于半导体封装芯片分离切割飞边的工艺,包括以下步骤:
10.(1)将切割飞边固着在承载膜上,使切割飞边与承载膜的固着力大于良品芯片与承载膜的固着力;
11.(2)在承载膜背面施加作用力,使得良品芯片从承载膜上脱落,良品芯片与承载膜分离,切割飞边保持在承载膜上。
12.作为本发明的进一步改进,所述步骤(1)中,通过加热使得切割飞边固定在承载膜上。
13.作为本发明的进一步改进,通过激光照射切割飞边或切割飞边下方的承载膜,使
得切割飞边固定在承载膜上。
14.作为本发明的进一步改进,在所述步骤(2)之前,还包括将不良品芯片固着在承载膜上,使不良品芯片与承载膜的固着力大于良品芯片与承载膜的固着力。
15.作为本发明的进一步改进,通过加热使得不良品芯片固定在承载膜上。
16.作为本发明的进一步改进,通过激光照射不良品芯片或不良品芯片下方的承载膜,使得不良品芯片固定在承载膜上。
17.作为本发明的进一步改进,所述步骤(1)中,通过点胶使得切割飞边固定在承载膜上。
18.作为本发明的进一步改进,在所述步骤(1)之前,还包括通过机器视觉系统识别切割飞边/切割飞边和不良品芯片。
19.作为本发明的进一步改进,所述步骤(2)中,通过超声或手工作用于承载膜背面,使得良品芯片从承载膜上脱落。
20.作为本发明的进一步改进,所述承载膜为uv膜、蓝膜或绿膜。
21.本发明的有益效果是:
22.(1)本发明采用将切割飞边和不良品芯片牢固的固定在承载膜上的方式,然后通过手工或超声的方式作用于承载膜的背面,依据良品芯片在承载膜上附着力低,而切割飞边和不良品芯片在承载膜上附着力高,利用两者之间对承载膜的附着力的差异,从而将良品芯片从承载膜上剥离下来,而切割飞边和不良品芯片则保持在承载膜上,实现良品芯片与切割飞边和不良品芯片的分离。
23.(2)本发明工艺大大减少了铲飞边的人工和剔除不良品的人工,容易实现自动化,工艺简单,可极大地提高生产效率,同时提高半导体封装芯片的良品率。
附图说明
24.为了更清楚地说明本发明实施例或现有技术中的技术方案,下面将对实施例或现有技术描述中所需要使用的附图作简单地介绍,显而易见地,下面描述中的附图仅仅是本发明中记载的一些实施例,对于本领域普通技术人员来讲,在不付出创造性劳动的前提下,还可以根据这些附图获得其他的附图。
25.图1是本发明的优选实施例一的激光加热固定切割飞边的状态示意图;
26.图2是本发明的优选实施例一的激光加热固定不良品芯片的状态示意图;
27.图3是本发明的优选实施例一的超声分离良品芯片与切割飞边和不良品芯片的状态示意图;
28.图4是本发明的优选实施例二的点胶固定切割飞边和激光加热固定不良品芯片的状态示意图;
29.图5是本发明的优选实施例二的超声分离良品芯片与切割飞边和不良品芯片的状态示意图;
30.图6是本发明的优选实施例三的点胶固定切割飞边的状态示意图;
31.图7是本发明的优选实施例三的超声分离切割飞边与半导体芯片单元的状态示意图。
具体实施方式
32.为了使本技术领域的人员更好地理解本发明中的技术方案,下面将结合本发明实施例中的附图,对本发明实施例中的技术方案进行清楚、完整地描述,显然,所描述的实施例仅仅是本发明一部分实施例,而不是全部的实施例。基于本发明中的实施例,本领域普通技术人员在没有做出创造性劳动前提下所获得的所有其他实施例,都应当属于本发明保护的范围。
33.一种用于半导体封装芯片分离切割飞边的工艺,包括以下步骤:
34.(1)将切割飞边固着在承载膜上,使切割飞边与承载膜的固着力大于良品芯片与承载膜的固着力;
35.(2)在承载膜背面施加作用力,使得良品芯片从承载膜上脱落,半导体芯片的良品芯片与承载膜分离,切割飞边保持在承载膜上。
36.其中,在步骤(1)中,通过加热使得切割飞边固定在承载膜上。
37.具体地,通过激光照射切割飞边,使得切割飞边固定在承载膜上。
38.在其他实施例中,通过激光照射切割飞边下方的承载膜,激光照射承载膜的背面,使得切割飞边固定在承载膜上。更具体地,通过激光照射切割飞边正下方的承载膜,使得切割飞边更稳固在承载膜上。
39.可选地,对于有些产品,如集成芯片,在步骤(2)之前,还包括将不良品芯片固着在承载膜上,使不良品芯片与承载膜的固着力大于良品芯片与承载膜的固着力。也即在步骤(1)与步骤(2)之间,添加该步骤。当然,可以理解的是,对于有些产品,如led芯片,在此工序中不需要外观检验,因此,将不良品芯片固着在承载膜上的这一工序可以省略。
40.具体地,通过加热使得不良品芯片固定在承载膜上。
41.更具体地,通过激光照射不良品芯片,使得不良品芯片固定在承载膜上。
42.在其他实施例中,通过激光照射不良品芯片下方的承载膜,激光照射承载膜的背面,使得不良品芯片固定在承载膜上。更具体地,通过激光照射不良品芯片正下方的承载膜,使得不良品芯片更稳固在承载膜上。
43.在另一实施例中,在步骤(1)中,通过点胶使得切割飞边固定在承载膜上。
44.在步骤(1)之前,还包括通过机器视觉系统识别切割飞边和不良品芯片。当然,可以理解的是,当不需要进行外观检验时,通过机器视觉仅识别切割飞边。
45.具体地,步骤(2)中,通过超声作用于承载膜背面,使得良品芯片从承载膜上脱落。但并不局限于此种方式,也可以通过手工作用于承载膜背面,使得良品芯片从承载膜上脱落。
46.在一实施例方式中,承载膜为uv膜,但并不局限于uv膜,也可以为蓝膜或绿膜。
47.上述工艺大大减少了铲飞边和剔除不良品的人工;配合机器视觉系统检测芯片外观不良,可以实现检测、剔除不良品和铲飞边的自动化,大幅度提高生产效率。
48.以下结合具体实施例对本发明作进一步的阐述。
49.实施例一
50.如图1所示,料环1-1贴合承载膜1-2,承载膜1-2是uv膜,但并不局限于uv膜,也可以为蓝膜或绿膜。切割机把基板切割成半导体芯片单元1-3,其中,基板是通过注塑机将芯片、引线和金属引线边框用树脂材料包裹而形成的,半导体芯片单元1-3的四周有切割飞边
1-4,半导体芯片单元1-3包括不良品芯片1-5和良品芯片1-6。激光器2-1的光斑2-2聚焦在切割飞边1-4上,光斑2-2的热量传导给切割飞边1-4,由于切割飞边1-4是金属材料,可快速将热量传导给承载膜1-2,高温破坏承载膜1-2表面粘性胶层,切割飞边1-4与承载膜1-2由于热量的作用开始熔融,这一过程通过控制好激光器2-1的功率和照射时间,既能实现承载膜1-2与切割飞边1-4的熔融,又不会完全破坏承载膜1-2。根据切割飞边1-4的材料、尺寸和承载膜1-2的特性,激光器2-1的功率为5w~50w,照射时间为0.1秒~2秒。待切割飞边1-4和承载膜1-2冷却后,切割飞边1-4固着在承载膜1-2的正面上。
51.如图2所示,激光器2-1的光斑2-2聚集在不良品芯片1-5上,光斑2-2的热量传导给不良品芯片1-5,不良品芯片1-5被烧蚀且热量传导给承载膜1-2,承载膜1-2与不良品芯片1-5由于热量的作用开始熔融,这一过程通过控制好激光器2-1的功率和照射时间,既能实现承载膜1-2与不良品芯片1-5的熔融,又不会完全破坏承载膜1-2。根据不良品芯片1-5的材料、尺寸和承载膜1-2的特性,激光器2-1的功率为5w~50w,照射时间为0.1秒~2秒。待不良品芯片1-5和承载膜1-2冷却后,不良品芯片1-5固着在承载膜1-2的正面上。
52.如图3所示,完成将切割飞边1-4和不良品芯片1-5固着在承载膜1-2上后,由于良品芯片1-6与承载膜1-2之间粘附力相对较弱,切割飞边1-4和不良品芯片1-5与承载膜1-2之间粘附力相对较强。采用适当规格的超声头4,超声头4功率为10w~100w,超声头4扫描承载膜1-2的背面,即承载膜1-2无胶的一面,使粘附力相对较强的切割飞边1-4和不良品芯片1-5仍然附着在承载膜1-2上,粘附力相对较弱的半导体芯片单元1-3的良品芯片1-6被超声头4震落。由此,实现良品芯片1-6与切割飞边1-4和不良品芯片1-5的分离。
53.实施例二
54.如图4所示,料环1-1贴合承载膜1-2,承载膜1-2是uv膜,但并不局限于uv膜,也可以为蓝膜或绿膜。切割机把基板切割成半导体芯片单元1-3,其中,基板是通过注塑机将芯片、引线和金属引线边框用树脂材料包裹而形成的,半导体芯片单元1-3的四周有切割飞边1-4,半导体芯片单元1-3包括不良品芯片1-5和良品芯片1-6。盛有可固化胶水3-3的针筒3将可固化胶水3-3挤出,按特定运动轨迹点胶,将胶水3-3涂布在切割飞边1-4上,胶水3-3延伸到承载膜1-2上,可固化胶水3-3固化后形成胶条3-2,胶条3-2将切割飞边1-4固着在承载膜1-2上。
55.激光器2-1的光斑2-2聚集在不良品芯片1-5上,光斑2-2的热量传导给不良品芯片1-5,不良品芯片1-5被烧蚀且热量传导给承载膜1-2,承载膜1-2与不良品芯片1-5由于热量的作用开始熔融,这一过程通过控制好激光器2-1的功率和照射时间,既能实现承载膜1-2与不良品芯片1-5的熔融,又不会完全破坏承载膜1-2。根据不良品芯片1-5的材料、尺寸和承载膜1-2的特性,激光器2-1的功率为5w~50w,照射时间为0.1秒~2秒。待不良品芯片1-5和承载膜1-2冷却后,不良品芯片1-5固着在承载膜1-2的正面上。
56.如图5所示,完成将切割飞边1-4和不良品芯片1-5固着在承载膜1-2上后,由于良品芯片1-6与承载膜1-2之间粘附力相对较弱,切割飞边1-4和不良品芯片1-5与承载膜1-2之间粘附力相对较强。采用适当规格的超声头4,超声头4功率为10w~100w,超声头4扫描承载膜1-2的背面,即承载膜1-2无胶的一面,使粘附力相对较强的切割飞边1-4和不良品芯片1-5仍然附着在承载膜1-2上,粘附力相对较弱的半导体芯片单元1-3的良品芯片1-6被超声头4震落。由此,实现良品芯片1-6与切割飞边1-4和不良品芯片1-5的分离。
57.实施例三
58.如图6所示,料环1-1贴合承载膜1-2,承载膜1-2是uv膜,但并不局限于uv膜,也可以为蓝膜或绿膜。切割机把基板切割成半导体芯片单元1-3,其中,基板是通过注塑机将芯片、引线和金属引线边框用树脂材料包裹而形成的,此半导体芯片可以为led芯片,半导体芯片单元1-3的四周有切割飞边1-4,半导体芯片单元1-3包括不良品芯片1-5和良品芯片1-6。盛有可固化胶水3-3的针筒3将可固化胶水3-3挤出,按特定运动轨迹点胶,将胶水3-3涂布在切割飞边1-4上,胶水3-3延伸到承载膜1-2上,可固化胶水3-3固化后形成胶条3-2,胶条3-2将切割飞边1-4固着在承载膜1-2上。
59.如图7所示,完成将切割飞边1-4固着在承载膜1-2上后,由于半导体芯片单元1-3与承载膜1-2之间粘附力相对较弱,切割飞边1-4与承载膜1-2之间粘附力相对较强。采用适当规格的超声头4,超声头4功率为10w~100w,超声头4扫描承载膜1-2的背面,使粘附力相对较强的切割飞边1-4仍然附着在承载膜1-2上,粘附力相对较弱的半导体芯片单元1-3被超声头4震落。由此,实现半导体芯片单元1-3与切割飞边1-4的分离,从承载膜1-2上脱落的不良品芯片1-5和良品芯片1-6再经过后续的全检和分类。
60.对于本领域技术人员而言,显然本发明不限于上述示范性实施例的细节,而且在不背离本发明的精神或基本特征的情况下,能够以其他的具体形式实现本发明。因此,无论从哪一点来看,均应将实施例看作是示范性的,而且是非限制性的,本发明的范围由所附权利要求而不是上述说明限定,因此旨在将落在权利要求的等同要件的含义和范围内的所有变化囊括在本发明内。不应将权利要求中的任何附图标记视为限制所涉及的权利要求。
61.此外,应当理解,虽然本说明书按照实施方式加以描述,但并非每个实施方式仅包含一个独立的技术方案,说明书的这种叙述方式仅仅是为清楚起见,本领域技术人员应当将说明书作为一个整体,各实施例中的技术方案也可以经适当组合,形成本领域技术人员可以理解的其他实施方式。