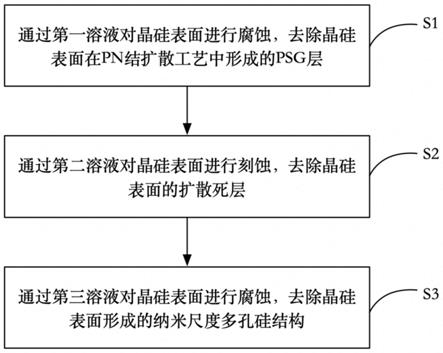
1.本发明属于太阳能电池技术领域,具体涉及一种晶硅扩散死层处理方法及晶硅太阳能电池。
背景技术:2.随着环境的恶化和传统能源的日渐短缺,寻找一种清洁环保、储量丰富的替代能源是非常有必要的。光伏发电凭借着无污染、不受使用地域限制等优势,在近二十年里得到了迅猛的发展。在各类太阳能电池中,晶硅太阳能电池因其原料储量丰富、工艺成熟而在光伏领域占据着主导地位,同时进一步实现提效降本也成为了晶硅太阳能电池领域研究的重点。pn结作为太阳能电池的核心部分,其制备工艺直接影响着发电效率。以p型晶硅太阳能电池为例,在通过热扩散制备pn结的这个过程中,磷原子的浓度从表面随着扩散深度的增大而呈梯度式下降,最外层磷原子浓度最大,往往会超出其在硅中的固溶度,多出来的非电活性磷原子将处于晶格间隙位置中形成填隙原子,使得这个区域出现晶格的损伤、失配。因此该区域的光生载流子在抵达pn结前会因位错、缺陷的存在而被迅速复合,无法对电流的产生做出贡献,称之为扩散死层,对于表面具有倒金字塔、纳米线等特殊绒面结构的晶硅片而言,经扩散处理后其表面磷源分布尤为不均。
3.现有技术中已经公开了一些扩散死层的处理方法,如:
4.1、公开号为cn110112260a的中国专利提出了一种单晶硅基类倒金字塔绒面结构的扩散方法,将具有类倒金字塔结构的硅片放入扩散炉中进行分步式扩散,利用三步有序沉积的设计和两步缓冲式降温方式来减少因表面磷原子堆积而产生的死层,该技术需要进行往复式升降温,工艺步骤与时间过于冗长繁琐,不利于大规模的生产应用;
5.2、公开号为cn102623568b的中国专利提出了一种晶体硅太阳电池扩散死层的去除方法,将扩散后的硅片表面丝网印刷一层腐蚀性浆料,采用腐蚀性浆料的方法在扩散后的硅片表面进行腐蚀,刻蚀掉一层硅表面,去除扩散死层,该技术与现行量产工艺不兼容,需要增加耗材、设备等投入,硅片表面腐蚀性浆料的去除也进一步使工艺复杂化,这制约了其产业推广;
6.3、公开号为cn02983218b的中国专利提出了一种去除死层的常规工艺电池片制备方法,使用湿法刻蚀的机台在扩散后的硅片pn结表面以喷淋的方式进行反刻,反刻工艺采用按照一定比例混合的氢氟酸、硝酸、水的混合酸液,经过一定的反应时间,将表层p含量浓度最高的硅腐蚀掉,该技术的反应速率过快,刻蚀程度不易控制,且对发射极处的微纳米绒面结构具有较大的影响。因此寻找一种能够有效减少甚至去除死层,对正表面反射率等光学特性影响小,又适合自动化商业化大规模生产的工艺是至关重要的。
7.在实际生产中,有的技术方案通过将pn结的深度做浅来降低硅片表面磷浓度,减少死层的产生,但这会影响丝网印刷电极时栅线与晶硅片之间的欧姆接触,增大电池的串联电阻,导致填充因子下降;有的技术方案利用混合酸对扩散后的晶硅片进行刻蚀来去除死层,但是其工艺窗口小,刻蚀的反应速率难以控制,在去除死层的同时也对晶硅片表面的
微纳绒面结构造成了破坏,降低了电池的陷光性能,不适用于工业化应用;有的技术方案则在扩散时通过前氧处理在硅片表面形成一层均匀的氧化层作为扩散面,利用厚度均匀的氧化层减小气流和温度对磷原子沉积的影响,并在扩散结束后增加后氧处理深度氧化硅片绒面,通过后续hf的漂洗提升扩散结的均匀性,该工艺对死层的去除程度还有待进一步的提升。
8.因此,针对上述技术问题,有必要提供一种晶硅扩散死层处理方法及晶硅太阳能电池。
技术实现要素:9.有鉴于此,本发明的目的在于提供一种晶硅扩散死层处理方法及晶硅太阳能电池,以去除晶硅表面的扩散死层。
10.为了实现上述目的,本发明一实施例提供的技术方案如下:
11.一种晶硅扩散死层处理方法,所述方法包括:
12.s1、通过第一溶液对晶硅表面进行腐蚀,去除晶硅表面在pn结扩散工艺中形成的psg层;
13.s2、通过第二溶液对晶硅表面进行刻蚀,去除晶硅表面的扩散死层;
14.s3、通过第三溶液对晶硅表面进行腐蚀,去除晶硅表面形成的纳米尺度多孔硅结构。
15.一实施例中,所述第一溶液为hf溶液,hf的质量浓度为0.1%~10%。
16.一实施例中,所述步骤s1中腐蚀温度为常温,腐蚀时间为20s~100s。
17.一实施例中,所述第二溶液为氧化剂、hf、去离子水的混合溶液,氧化剂的质量浓度为0.1%~30%,hf的质量浓度为1%~10%,所述氧化剂为亚硝酸盐、h2o2、hno3中的一种或多种,所述亚硝酸盐包括亚硝酸钠、亚硝酸钾、亚硝酸铵中的一种或多种。
18.一实施例中,所述步骤s2中刻蚀温度为常温,刻蚀时间为20s~200s。
19.一实施例中,所述第三溶液为碱、h2o2、去离子水的混合溶液,碱的质量浓度为1%~10%,h2o2的质量浓度为0.1%~10%。
20.一实施例中,所述步骤s3中腐蚀温度为50℃~90℃,腐蚀时间为20s~200s。
21.一实施例中,所述步骤s3得到的晶硅较步骤s1前的晶硅,扩散方块电阻升高35ω/
□
~45ω/
□
;和/或,
22.所述步骤s1前的晶硅表面磷浓度为3
×
10
20
cm-3
~3
×
10
21
cm-3
,步骤s3得到的晶硅表面磷浓度为0.5
×
10
20
cm-3
~3
×
10
20
cm-3
。
23.一实施例中,所述晶硅为p型硅片或n型硅片;和/或,所述晶硅为单晶硅片、多晶硅片或准单晶硅片。
24.本发明另一实施例提供的技术方案如下:
25.一种晶硅太阳能电池,所述晶硅太阳能电池包括晶硅,晶硅通过上述的处理方法获得。
26.本发明具有以下有益效果:
27.本发明可有效去除晶硅表面的扩散死层,降低表层的磷掺杂浓度及光生载流子的复合速率,提高电池片的开路电压,同时对原有的绒面结构无影响,保持着良好的陷光效
果,保证了电池片的光电转换效率;
28.本发明可与现行量产工艺兼容,主要工序在常温下即可进行,可以较好地控制反应速度和刻蚀程度,操作简单,能耗低。
附图说明
29.为了更清楚地说明本技术实施例或现有技术中的技术方案,下面将对实施例或现有技术描述中所需要使用的附图作简单地介绍,显而易见地,下面描述中的附图仅仅是本技术中记载的一些实施例,对于本领域普通技术人员来讲,在不付出创造性劳动的前提下,还可以根据这些附图获得其他的附图。
30.图1为本发明晶硅扩散死层处理方法的流程示意图;
31.图2为本发明一具体实施例中去除psg层后晶硅表面的sem扫描图;
32.图3为本发明一具体实施例中去除纳米尺度多孔硅结构后晶硅表面的sem扫描图;
33.图4为本发明一具体实施例中去除扩散死层前后晶硅表面的ecv曲线图;
34.图5为本发明一具体实施例中去除扩散死层前后晶硅表面的反射率曲线图。
具体实施方式
35.为了使本技术领域的人员更好地理解本发明中的技术方案,下面将结合本发明实施例中的附图,对本发明实施例中的技术方案进行清楚、完整地描述,显然,所描述的实施例仅仅是本发明一部分实施例,而不是全部的实施例。基于本发明中的实施例,本领域普通技术人员在没有做出创造性劳动前提下所获得的所有其他实施例,都应当属于本发明保护的范围。
36.参图1所示,本发明公开了一种晶硅扩散死层处理方法,包括:
37.s1、通过第一溶液对晶硅表面进行腐蚀,去除晶硅表面在pn结扩散工艺中形成的psg层。
38.其中,第一溶液为hf溶液,hf的质量浓度为5%~10%;腐蚀温度为常温,腐蚀时间为20s~100s,优选为60s,表面psg层去除效果最佳。
39.s2、通过第二溶液对晶硅表面进行刻蚀,去除晶硅表面的扩散死层。
40.其中,第二溶液为氧化剂、hf、去离子水的混合溶液,氧化剂的质量浓度为0.1%~30%,优选为0.1%~10%,hf的质量浓度为1%~10%,优选为1%~10%,氧化剂为亚硝酸盐、h2o2、hno3中的一种或多种,亚硝酸盐包括亚硝酸钠、亚硝酸钾、亚硝酸铵中的一种或多种,氧化剂优选为亚硝酸钠。
41.刻蚀温度为常温,刻蚀时间为20s~200s,优选为60s。
42.s3、通过第三溶液对晶硅表面进行腐蚀,去除晶硅表面形成的纳米尺度多孔硅结构。
43.其中,第三溶液为碱、h2o2、去离子水的混合溶液,碱的质量浓度为1%~10%,h2o2的质量浓度为0.1%~10%;腐蚀温度为50℃~90℃,优选为50~60℃,腐蚀时间为20s~200s,优选为60s;碱可以为koh,也可以为naoh等其他常规碱。
44.本发明中,步骤s3得到的晶硅较步骤s1前的晶硅,扩散方块电阻升高35ω/
□
~45ω/
□
;步骤s1前的晶硅表面磷浓度为3
×
10
20
cm-3
~3
×
10
21
cm-3
,步骤s3得到的晶硅表面磷
浓度为0.5
×
10
20
cm-3
~3
×
10
20
cm-3
。
45.本发明还公开了一种晶硅太阳能电池,其包括晶硅,晶硅通过上述的处理方法获得。本发明适用于p型或n型单晶、多晶、准单晶硅基太阳电池作为发射极(背场)使用的p型或n型晶硅。
46.以下结合具体实施例对本发明作进一步说明。
47.本发明一具体实施例中晶硅扩散死层处理方法,包括以下步骤:
48.1、通过第一溶液对晶硅表面进行腐蚀,去除晶硅表面在pn结扩散工艺中形成的psg(磷硅玻璃)层。
49.第一溶液为hf溶液,hf的质量浓度为10%;腐蚀温度为常温,腐蚀时间为60s。
50.2、将步骤1得到的晶硅进行去离子水清洗、甩干后,通过第二溶液对晶硅表面进行刻蚀(回刻),去除晶硅表面的扩散死层。
51.第二溶液为亚硝酸钠、hf、去离子水的混合溶液,亚硝酸钠的质量浓度为0.5%,hf的质量浓度为2%,;刻蚀温度为常温,刻蚀时间为60s。
52.3、将步骤2得到的晶硅进行去离子水清洗、甩干后,通过第三溶液对晶硅表面进行腐蚀,去除步骤2中晶硅表面形成的纳米尺度多孔硅结构,进一步去除扩散死层。
53.第三溶液为koh、h2o2、去离子水的混合溶液,koh的质量浓度为0.5%,h2o2的质量浓度为1%;腐蚀温度为62℃,腐蚀时间为60s。
54.4、最后将步骤3得到的晶硅进行去离子水清洗、甩干,得到的晶硅即可在常规电池片产线上继续进行后续的生产工序。
55.图2所示为本实施例中去除psg层后晶硅表面的sem扫描图,图3所示为本实施例中去除纳米尺度多孔硅结构后晶硅表面的sem扫描图。对比图2、图3可以发现,晶硅表面形貌结构几乎没有变化,本发明的方法对硅片原绒面有良好的保形性。
56.将去除扩散死层后的晶硅和去除psg层前的晶硅通过四探针测试其方块电阻,去除扩散死层后的晶硅扩散方块电阻升高35ω/
□
~45ω/
□
。
57.采用ecv曲线表征去除扩散死层前后晶硅表面磷掺杂浓度的变化情况,并截取了完整ecv曲线上镶嵌式磷含量段与部分替位式磷含量段的数据,结果如图4所示。由图4可见,在去除扩散死层后,晶硅上pn结表面的磷浓度由4
×
10
20
cm-3
降低到1.6
×
10
20
cm-3
,意味着容易引起晶格位错与失配的镶嵌式磷含量得到了明显的降低,扩散死层基本被去除。
58.参图5所示为去除扩散死层前后晶硅表面的反射率曲线图,可见,尽管去除扩散死层后晶硅表面最上层的杂质基本已被刻蚀掉,但该工艺对其表面形貌几乎无影响,反射率整体无变化,依旧保持着原有陷光效果。
59.由以上技术方案可以看出,本发明具有以下优点:
60.本发明可有效去除晶硅表面的扩散死层,降低表层的磷掺杂浓度及光生载流子的复合速率,提高电池片的开路电压,同时对原有的绒面结构无影响,保持着良好的陷光效果,保证了电池片的光电转换效率;
61.本发明可与现行量产工艺兼容,主要工序在常温下即可进行,可以较好地控制反应速度和刻蚀程度,操作简单,能耗低。
62.对于本领域技术人员而言,显然本发明不限于上述示范性实施例的细节,而且在不背离本发明的精神或基本特征的情况下,能够以其他的具体形式实现本发明。因此,无论
从哪一点来看,均应将实施例看作是示范性的,而且是非限制性的,本发明的范围由所附权利要求而不是上述说明限定,因此旨在将落在权利要求的等同要件的含义和范围内的所有变化囊括在本发明内。不应将权利要求中的任何附图标记视为限制所涉及的权利要求。
63.此外,应当理解,虽然本说明书按照实施方式加以描述,但并非每个实施方式仅包含一个独立的技术方案,说明书的这种叙述方式仅仅是为清楚起见,本领域技术人员应当将说明书作为一个整体,各实施例中的技术方案也可以经适当组合,形成本领域技术人员可以理解的其他实施方式。