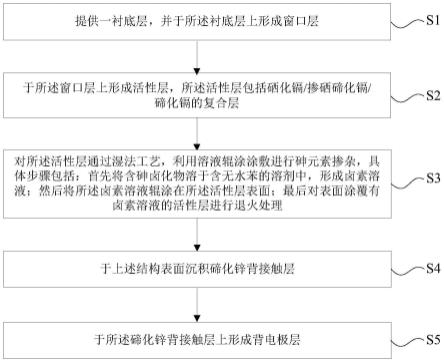
1.本发明涉及太阳能电池技术领域,特别是涉及一种碲化镉薄膜太阳能电池及其制备方法。
背景技术:2.碲化镉太阳能电池,较单晶硅太阳能电池有制作方便,成本低廉和重量较轻等优点。碲化镉薄膜太阳能电池简称cdte电池,它是一种以p型cdte和n型cds或cdse的异质结为基础的薄膜太阳能电池。一般标准的碲化镉薄膜太阳能电池由五层结构组成:背电极、背接触层、活性层、窗口层、tco层。碲化镉薄膜太阳能电池的生产成本大大低于晶体硅和其他材料的太阳能电池技术,其次它和太阳光谱很一致,可吸收95%以上的阳光。cdte薄膜太阳能电池技术是太阳能行业中成本最低的发电方法之一,受益于快速cdte活性层沉积、cdcl2处理和cu掺杂,但铜掺杂光电压低,存在不稳定性问题。因此,目前一般采用将v族元素掺杂到cdte活性层中以解决这些挑战。尽管高温原位v族掺杂cdsete太阳能电池器件的效率已经超过20%,但它们依然面临着沉积后掺杂激活过程、较短的载流子寿命以及较低的激活比等障碍。
技术实现要素:3.鉴于以上所述现有技术的缺点,本发明的目的在于提供一种碲化镉薄膜太阳能电池及其制备方法,用于解决现有技术中原位v族掺杂cdsete的太阳能电池面临着活性层沉积后掺杂激活过程中较短的载流子寿命以及较低的激活比等的问题。
4.为实现上述目的及其他相关目的,本发明提供一种碲化镉薄膜太阳能电池的制备方法,所述制备方法包括:
5.提供一衬底层,并于所述衬底层上形成窗口层;
6.于所述窗口层上形成活性层,所述活性层包括硒化镉/掺硒碲化镉/碲化镉的复合层;
7.对所述活性层通过湿法工艺,利用溶液辊涂涂敷进行砷元素掺杂,具体步骤包括:首先将含砷卤化物溶于含无水苯的溶剂中,形成卤素溶液;然后将所述卤素溶液辊涂在所述活性层表面;最后对表面涂覆有卤素溶液的活性层进行退火处理;
8.于上述结构表面沉积碲化锌背接触层;
9.于所述碲化锌背接触层上形成背电极层。
10.可选地,所述含砷卤化物为ascl3;所述卤素溶液的浓度介于1mg/l~100mg/l之间;将所述卤素溶液辊涂在所述活性层表面的参数包括传输辊转速介于30mm/s~100mm/s之间,涂敷辊转速介于30mm/s~100mm/s之间,涂敷辊与活性层表面之间的间距介于1mm~10mm之间;对表面涂覆有卤素溶液的活性层进行退火处理的退火温度介于25℃~120℃之间。
11.进一步地,所述卤素溶液中的溶剂为无水苯。
12.可选地,形成所述活性层的方法包括:首先于所述窗口层上依次形成硒化镉层及碲化镉层的活性材料层;然后通过活化退火工序控制完成对所述窗口层及所述活性材料层的活化退火处理,以使所述活性材料层形成为包括硒化镉/掺硒碲化镉/碲化镉的复合层的所述活性层。
13.进一步地,采用近空间升华法或气相传输沉积法形成所述活性材料层。
14.进一步地,对所述窗口层及所述活性材料层活化退火处理的活化退火温度介于350℃-600℃之间,活化退火时间介于5min-40min之间。
15.可选地,所述衬底层为fto材料层;所述窗口层为氧化锌掺镁层、氧化铝掺镁层及氧化钛层中的一层或至少两层的叠层。
16.可选地,所述窗口层的厚度介于0nm~70nm之间,所述活性层的厚度介于2.0μm~4.0μm之间,所述背电极层的厚度介于220nm~250nm之间。
17.可选地,采用磁控溅射法形成所述窗口层;采用磁控溅射法形成所述背电极层,所述背电极层为钼层、铝层及铬层中一层或至少两层的叠层。
18.可选地,形成所述碲化锌背接触层之前还包括:对所得结构进行0.05%~5%的盐酸刻蚀清洗的步骤。
19.可选地,对所述活性层进行的湿法工艺过程在密封负压腔体中进行。
20.本发明还提供一种碲化镉薄膜太阳能电池,所述碲化镉薄膜太阳能电池采用如上所述任意一项的碲化镉薄膜太阳能电池的制备方法制备得到
21.如上所述,本发明的碲化镉薄膜太阳能电池及其制备方法,通过湿法工艺,利用溶液辊涂涂敷实现
ⅴ
族砷元素对包括硒化镉/掺硒碲化镉/碲化镉的复合层的活性层的非原位掺杂,砷元素不易在活性层中扩散,稳定性能好,且采用该湿法涂敷更易于控制掺杂比率,掺杂效率高,因此掺杂后可有效延长载流子寿命以及提高激活比,从而提高碲化镉薄膜太阳能电池的初始性能和长期稳定性,大幅提高转换效率;另外该工艺操作简单,容易控制。
附图说明
22.图1显示为本发明的碲化镉薄膜太阳能电池的制备方法的流程步骤示意图。
23.图2至图8显示为本发明的碲化镉薄膜太阳能电池的制备方法中各步骤对应的截面结构示意图。
24.元件标号说明
[0025]1ꢀꢀꢀꢀꢀꢀꢀꢀꢀꢀꢀꢀꢀꢀꢀꢀꢀꢀꢀꢀꢀꢀꢀ
衬底层
[0026]2ꢀꢀꢀꢀꢀꢀꢀꢀꢀꢀꢀꢀꢀꢀꢀꢀꢀꢀꢀꢀꢀꢀꢀ
窗口层
[0027]3ꢀꢀꢀꢀꢀꢀꢀꢀꢀꢀꢀꢀꢀꢀꢀꢀꢀꢀꢀꢀꢀꢀꢀ
活性层
[0028]
30
ꢀꢀꢀꢀꢀꢀꢀꢀꢀꢀꢀꢀꢀꢀꢀꢀꢀꢀꢀꢀꢀꢀ
活性材料层
[0029]
31
ꢀꢀꢀꢀꢀꢀꢀꢀꢀꢀꢀꢀꢀꢀꢀꢀꢀꢀꢀꢀꢀꢀ
硒化镉层
[0030]
32
ꢀꢀꢀꢀꢀꢀꢀꢀꢀꢀꢀꢀꢀꢀꢀꢀꢀꢀꢀꢀꢀꢀ
碲化镉层
[0031]4ꢀꢀꢀꢀꢀꢀꢀꢀꢀꢀꢀꢀꢀꢀꢀꢀꢀꢀꢀꢀꢀꢀꢀ
砷掺杂的活性层
[0032]5ꢀꢀꢀꢀꢀꢀꢀꢀꢀꢀꢀꢀꢀꢀꢀꢀꢀꢀꢀꢀꢀꢀꢀ
碲化锌背接触层
[0033]6ꢀꢀꢀꢀꢀꢀꢀꢀꢀꢀꢀꢀꢀꢀꢀꢀꢀꢀꢀꢀꢀꢀꢀ
背电极层
[0034]
s1~s6
ꢀꢀꢀꢀꢀꢀꢀꢀꢀꢀꢀꢀꢀꢀꢀꢀꢀꢀ
步骤
具体实施方式
[0035]
以下通过特定的具体实例说明本发明的实施方式,本领域技术人员可由本说明书所揭露的内容轻易地了解本发明的其他优点与功效。本发明还可以通过另外不同的具体实施方式加以实施或应用,本说明书中的各项细节也可以基于不同观点与应用,在没有背离本发明的精神下进行各种修饰或改变。
[0036]
请参阅图1至图8。需要说明的是,本实施例中所提供的图示仅以示意方式说明本发明的基本构想,遂图示中仅显示与本发明中有关的组件而非按照实际实施时的组件数目、形状及尺寸绘制,其实际实施时各组件的型态、数量及比例可根据实际需要进行改变,且其组件布局型态也可能更为复杂。
[0037]
如图1所示,本发明提供一种碲化镉薄膜太阳能电池的制备方法,所述制备方法包括如下步骤:
[0038]
s1,提供一衬底层,并于所述衬底层上形成窗口层;
[0039]
s2,于所述窗口层上形成活性层,所述活性层包括硒化镉/掺硒碲化镉/碲化镉的复合层;
[0040]
s3,对所述活性层通过湿法工艺,利用溶液辊涂涂敷进行砷元素掺杂,具体步骤包括:首先将含砷卤化物溶于含无水苯的溶剂中,形成卤素溶液;然后将所述卤素溶液辊涂在所述活性层表面;最后对表面涂覆有卤素溶液的活性层进行退火处理;
[0041]
s4,于上述结构表面沉积碲化锌背接触层;
[0042]
s5,于所述碲化锌背接触层上形成背电极层。
[0043]
本发明的制备方法通过湿法工艺,利用溶液辊涂涂敷实现
ⅴ
族砷元素对包括硒化镉/掺硒碲化镉/碲化镉的复合层的活性层的非原位掺杂,砷元素不易在活性层中扩散,稳定性能好,且采用该湿法涂敷更易于控制掺杂比率,掺杂效率高,因此掺杂后可有效延长载流子寿命以及提高激活比,从而提高碲化镉薄膜太阳能电池的初始性能和长期稳定性,大幅提高转换效率;另外该工艺操作简单,容易控制。
[0044]
下面结合具体附图对本发明的碲化镉薄膜太阳能电池的制备方法进行详细说明。
[0045]
如图1及图2所示,首先进行步骤s1,提供一衬底层1,并于所述衬底层1上形成窗口层2。
[0046]
所述衬底层1可以作为太阳能电池的前电极,起到导电子阻空穴的作用。一般地,所述衬底层1的材料选择掺氟氧化锡(简称fto)、导电玻璃、氧化钛或掺铝氧化锌等。本实施例中选择所述衬底层1的材料为fto。
[0047]
作为示例,所述窗口层2可以为氧化锌掺镁层、氧化铝掺镁层及氧化钛层中的一层或至少两层的叠层。即,所述窗口层2可以是氧化锌掺镁层或氧化铝掺镁层或氧化钛层,也可以为氧化锌掺镁层、氧化铝掺镁层及氧化钛层中任意两层的叠层,也可以为氧化锌掺镁层、氧化铝掺镁层及氧化钛层三层的叠层。所述窗口层2的厚度一般选择介于0nm~70nm之间较佳。制备方法一般选择磁控溅射法形成所述窗口层2。
[0048]
如图1及图3至图5所示,然后进行步骤s2,于所述窗口层2上形成活性层3,所述活性层3包括硒化镉/掺硒碲化镉/碲化镉的复合层。采用复合结构的活性层可有效降低碲化
镉的能带,使电池对700nm~900nm波长的光的吸收大幅增加,使太阳能电池对长波长的短波长光的吸收达到最大,以此增加电池短路电流密度,提高电池效率。
[0049]
作为示例,形成所述活性层3的方法包括:首先于所述窗口层2上依次形成硒化镉层31及碲化镉层32的活性材料层30;然后通过活化退火工序控制完成对所述窗口层2及所述活性材料层30的活化退火处理,以使所述活性材料层30形成为包括硒化镉/掺硒碲化镉/碲化镉的复合层的所述活性层3。一般采用近空间升华法(close space sublimation,css)或气相传输沉积法(vtd)形成所述活性材料层30。活化退火工序可使硒化镉层31及碲化镉层32表面之间互相渗透融合形成新的掺硒碲化镉层,从而使活性层3形成为具有一定掺硒梯度的硒化镉/掺硒碲化镉/碲化镉的复合层,该方法可以实现掺硒碲化镉层的均质化,可控化,从而进一步增加光电流,提高太阳能电池的短路电流密度。较佳地,该活化退火工序的活化退火温度介于350℃-600℃之间,活化退火时间介于5min-40min之间。
[0050]
形成所述硒化镉层31及碲化镉层32的活性材料层30的方法可以是单次循环的方式,也可以是多次循环的方式。如图3所示,为单次循环的方式形成所述活性材料层30,即所述活性材料层30由一层硒化镉层31及一层碲化镉层32叠层形成。如图4所示,为多次循环的方式形成所述活性材料层30,即所述活性材料层30以一层硒化镉层31及一层碲化镉层32形成的叠层为循环单元实现至少两个循环单元的层叠形成。
[0051]
作为示例,所述活性层3的厚度选择为介于2.0μm~4.0μm之间。
[0052]
如图1及图6所示,接着进行步骤s3,对所述活性层3通过湿法工艺,利用溶液辊涂涂敷进行砷元素掺杂,形成砷掺杂的活性层4,具体步骤包括:首先将含砷卤化物溶于含无水苯的溶剂中,形成卤素溶液;然后将所述卤素溶液辊涂在所述活性层3表面;最后对表面涂覆有卤素溶液的活性层3进行退火处理。通过该步骤可实现对活性层3的砷元素非原位掺杂,砷元素不易在活性层中扩散,稳定性能好,且采用该湿法涂敷更易于控制掺杂比率,掺杂效率高,因此掺杂后可有效延长载流子寿命以及提高激活比,从而提高碲化镉薄膜太阳能电池的初始性能和长期稳定性,大幅提高转换效率;另外该工艺操作简单,容易控制。
[0053]
作为一较佳实施例,所述含砷卤化物为ascl3;所述卤素溶液的浓度介于1mg/l~100mg/l之间;将所述卤素溶液辊涂在所述活性层3表面的参数包括传输辊转速介于30mm/s~100mm/s之间,涂敷辊转速介于30mm/s~100mm/s之间,涂敷辊与活性层3表面之间的间距介于1mm~10mm之间;对表面涂覆有卤素溶液的活性层3进行退火处理的退火温度介于25℃~120℃之间,更佳地,所述卤素溶液中的溶剂仅为无水苯,对于采用以上参数的ascl3掺杂的cdsete太阳能电池,掺杂剂活性比达到5.88%,空穴密度达到》2
×
10
15
cm-3
,载流子寿命达到20ns以上,因此,非原位as掺杂cdsete太阳能电池的开路电压达到863mv,而cu掺杂cdsete太阳能电池的开路电压最高为852mv。
[0054]
作为示例,所述卤素溶液的溶剂除了含有无水苯之外,还可以包括异丙酮、丙酮、甲醇和乙醇等溶剂,但单纯只使用无水苯的效果为最佳。
[0055]
作为示例,由于所述卤素溶液有毒性,所以对所述活性层3进行的湿法工艺过程在密封负压腔体中进行,以降低危害性。
[0056]
如图1及图7所示,接着进行步骤s4,于上述结构表面沉积碲化锌背接触层5。
[0057]
作为示例,采用磁控溅射法形成所述碲化锌背接触层5。
[0058]
作为一较佳示例,形成所述碲化锌背接触层5之前还包括对所得结构进行0.05%
~5%的盐酸刻蚀清洗的步骤。由于在形成活性层3及对活性层3进行掺杂处理时均有退火处理过程,该些过程会使活性层表面产生氧化,采用盐酸清洗可以去除该氧化部分;另外,盐酸还可以去掉活性层表面的一部分镉原子,使表面产生碲的悬挂键,从而在形成碲化锌背接触层时,使活性层与碲化锌背接触层之间形成良好的接触。
[0059]
如图1及图8所示,最后进行步骤s5,于所述碲化锌背接触层5上形成背电极层6。
[0060]
作为示例,可以采用但不限于磁控溅射法形成所述背电极层6。所述背电极层6为钼层、铝层及铬层中的一层或至少两层的叠层,即,所述背电极层6为钼层、铝层及铬层中一层的单层结构,或钼层、铝层及铬层中两层的叠层结构,或钼层、铝层及铬层三层的叠层结构。
[0061]
作为示例,所述背电极层6的厚度介于220nm~250nm之间。
[0062]
作为示例,在形成所述碲化锌背接触层5后先对整个芯片进行激光1刻划,进行组件的电池分割,分割为小的单元;然后进行光刻胶涂覆显影,填充刻划的单元;接着再经过激光2刻划;激光2刻划后再进行背电极层6的沉积,接着进行退火,进行常规组件封装。
[0063]
作为示例,芯片封装后,在最终效率测试之前,通过电注入或光照的方式对碲化镉进行激活。电注入方式是通过在电池的接线端加载适应的偏压进行激活。
[0064]
本发明还提供一种碲化镉薄膜太阳能电池,该碲化镉薄膜太阳能电池采用如上所述的碲化镉薄膜太阳能电池的制备方法制备得到。
[0065]
综上所述,本发明提供一种碲化镉薄膜太阳能电池及其制备方法,通过湿法工艺,利用溶液辊涂涂敷实现
ⅴ
族砷元素对包括硒化镉/掺硒碲化镉/碲化镉的复合层的活性层的非原位掺杂,砷元素不易在活性层中扩散,稳定性能好,且采用该湿法涂敷更易于控制掺杂比率,掺杂效率高,因此掺杂后可有效延长载流子寿命以及提高激活比,从而提高碲化镉薄膜太阳能电池的初始性能和长期稳定性,大幅提高转换效率;另外该工艺操作简单,容易控制。所以,本发明有效克服了现有技术中的种种缺点而具高度产业利用价值。
[0066]
上述实施例仅例示性说明本发明的原理及其功效,而非用于限制本发明。任何熟悉此技术的人士皆可在不违背本发明的精神及范畴下,对上述实施例进行修饰或改变。因此,举凡所属技术领域中具有通常知识者在未脱离本发明所揭示的精神与技术思想下所完成的一切等效修饰或改变,仍应由本发明的权利要求所涵盖。