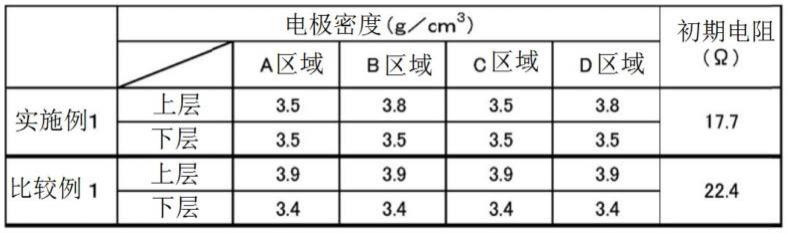
1.本发明涉及二次电池用电极和该电极的制造方法。
背景技术:2.锂离子二次电池等的二次电池由于与现有电池相比轻量且能量密度高,因此优选用作车辆搭载用的高输出电源或个人计算机和移动终端的电源。锂离子二次电池特别优选用作电动汽车(bev)、混合动力汽车(hev)、插电式混合动力汽车(phev)等车辆的驱动用高输出电源。
3.作为这种二次电池所具备的正极和负极(以下,不特别区分正负极时简称为“电极”)的典型结构,可举出在箔状的电极集电体的单面或两面形成以电极活性物质为主成分的电极活性物质层。上述电极活性物质层通过以下方式而形成:将电极活性物质、粘合材料(粘结剂)、导电材料等固体成分分散于规定的溶剂中,将由此制备的浆(糊)状的电极材料涂布于集电体的表面而形成涂膜,使该涂膜干燥后,施加加压压力而制成规定的密度、厚度。
4.二次电池不断要求高容量化、高能量密度化等电池性能的进一步提高。为了使二次电池高容量化、高能量密度化,例如,可举出将电极活性物质层涂布得比以往更厚并以规定的加压压力进行加压的方法。但是,通常,li离子难以均匀地扩散到集电体附近的电极活性物质中,特别是在电极活性物质层比以往更厚且提高了密度的情况下,集电体附近的电极活性物质由于li离子枯竭,电池性能(例如,电池容量)难以提高。
5.专利文献1中公开了如下方案:为了提供一种在高电流倍率放电中发挥优异电池性能的非水电解质电池,使用从电极活性物质层表面朝着集电体以固体成分浓度变大的方式具有浓度梯度的电极。另外,专利文献2中公开了一种电极的制造方法,以高输出和高能量密度化等为目的,通过将负极活性物质复合材料糊涂布于集电体的至少一方,使其干燥后,再次供给溶剂并抵接具有凹凸图案的模具而具有凹凸图案。
6.现有技术文献
7.专利文献
8.专利文献1:日本特开2005-50755号公报
9.专利文献2:日本特开2015-138619号公报
技术实现要素:10.然而,专利文献2所公开的方法中,由于再次向通过干燥后加压而使电极密度提高了的电极供给溶剂,因此溶剂无法均匀地渗透到电极活性物质层,通过将具有凹凸图案的模具抵接于该状态的电极活性物质层,会使电极的表面部的密度局部变高(即,致密化)。因此,电极的表面部被致密化至所需以上,因此li离子的嵌入/脱嵌路径狭窄,离子扩散性降低。另外,专利文献1和2的方法需要在通常的电极的制造方法的基础上增加涂布工序、干燥工序的次数,因此与通常的电极的制造方法相比生产成本增加。
11.本发明是鉴于上述情况而进行的,其主要目的在于提供一种通过在电极的表面部具有相对为高密度的区域和低密度的区域而使离子扩散性提高的电极。另一目的在于提供一种利用抑制了生产成本的方法来制造上述电极的方法。
12.为了实现上述目的,提供一种二次电池用电极。在此公开的二次电池用电极为二次电池的正负极中的任一电极,且具备电极集电体和形成于该电极集电体上的电极活性物质层,在上述电极活性物质层的表面以规定的图案和一定的间距重复电极密度相对为低密度的低密区域和相对为高密度的高密区域。将上述电极活性物质层在从该活性物质层的表面直到上述集电体的厚度方向均等地区分为上层、中间层和下层这3个层,将上述低密区域的该上层、该中间层、该下层的上述电极密度(g/cm3)分别设为d
l1
、d
l2
、d
l3
且将上述高密区域的该上层、该中间层、该下层的上述电极密度(g/cm3)分别设为d
h1
、d
h2
、d
h3
时,具备(d
h3
/d
l3
)<(d
h1
/d
l1
)的关系。
13.电极活性物质层的低密区域的固体成分彼此具有适当的间隙(空隙),是形成了li离子的嵌入/脱嵌路径的状态。另外,电极活性物质层的高密区域中固体成分彼此的接触性相对变高,是恰当地形成导电路径的状态。通过不是电极的表面部全部被致密化的状态,而是以规定的图案形成低密区域和高密区域,从而能够使整个电极活性物质层高效地参与电化学反应。由此,能够实现提高了电极活性物质层内的离子扩散性的电极。
14.在此公开的电极的优选的一个方式中,在上述电极活性物质层中,上述低密区域上层d
l1
和下层d
l3
具备(d
l1
/d
l3
)<1.1的关系。
15.低密区域是如上所述地作为li离子的嵌入/脱嵌路径而发挥功能的区域,通过从上层到下层以密度差小的状态形成上述低密区域,能够将li离子恰当地导入到存在于集电体附近的电极活性物质。由此,能够提供离子扩散性进一步提高的电极。
16.在此公开的电极的优选的一个方式中,上述低密区域与上述高密区域的间距以250μm~5mm重复。
17.根据上述构成,能够有效地提高离子扩散性。
18.在此公开的电极的优选的一个方式中,上述电极活性物质层的表面具有规定图案的凹凸形状,在上述凹凸形状的凹部形成上述低密区域,在上述凹凸形状的凸部形成上述高密区域。
19.根据上述构成,li离子更容易扩散到集电体附近的电极活性物质,li离子的扩散性提高。
20.为了实现上述的另一目的,提供一种电极的制造方法。在此公开的电极的制造方法是具有正负极中的任一者的电极集电体和电极活性物质层的电极的制造方法,包含如下工序:准备由至少含有电极活性物质、粘结剂树脂和溶剂的凝聚粒子形成的湿润粉体的工序,在此,上述湿润粉体的以个数计至少50%以上的上述凝聚粒子的固相、液相和气相形成钟摆状态或索带状态;使用上述湿润粉体在电极集电体上以该涂膜残留气相的状态形成由该湿润粉体构成的涂膜的工序;在以残留上述气相的状态成膜的涂膜的表面部以规定的图案和一定的间距形成凹凸的工序;使形成上述凹凸的上述涂膜干燥而形成电极活性物质层的工序;以及,将上述电极活性物质层进行加压的工序。
21.根据上述构成,能够制造具备上述特性的理想的电极。另外,上述电极通过在干燥工序前实施凹凸形成工序而实现。因此,能够与进行多次涂布工序、干燥工序的以往的制造
方法相比抑制生产成本。
22.在此公开的电极制造方法的优选的一个方式中,上述凹凸形成工序中的上述涂膜在上述涂膜的截面sem图像中气相在上述涂膜的单位截面积中所占的面积的比例的平均值为55%以下。
23.根据上述构成,能够通过具有气相而使涂膜的延展性提高,更恰当地实施凹凸形成工序。
24.在此公开的电极制造方法的优选的一个方式中,对于准备上述湿润粉体的工序中所准备的湿润粉体,将以不施加力而刮平的方式将湿润粉体(g)装入规定容积(ml)的容器中进行测量而得的堆积密度设为松散堆积密度x(g/ml)且将假设不存在气相而由湿润粉体的组成算出的密度设为真密度y(g/ml)时,真密度y与松散堆积密度x之比y/x为1.2以上。
25.根据上述构成,能够更恰当地制造高品质的电极。
26.在此公开的电极制造方法的优选的一个方式中,上述凹凸转印工序通过将表面形成有规定图案的旋转辊抵接于具有上述涂膜的集电体的该涂膜的表面而进行。
27.根据上述构成,能够在不负担对所期望的凹凸形状为过量的负荷的情况下在涂膜的表面形成凹凸。
附图说明
28.图1a是示意地示出一个实施方式的电极的低密区域和高密区域的图案的一个例子的图。
29.图1b是示意地示出一个实施方式的电极的低密区域和高密区域的图案的另一例子的图。
30.图1c是示意地示出一个实施方式的电极的低密区域和高密区域的图案的另一例子的图。
31.图1d是示意地示出一个实施方式的电极的低密区域和高密区域的图案的另一例子的图。
32.图2是对一个实施方式的电极进行示意说明的图。
33.图3是示出一个实施方式的电极制造方法的大致工序的流程图。
34.图4是示意地示出一个实施方式的具备辊式成膜部的电极制造装置的构成的框图。
35.图5是示意地示出构成湿润粉体的凝聚粒子中的固相(活性物质粒子等固体成分)、液相(溶剂)、气相(空隙)的存在形态的说明图,(a)表示钟摆状态,(b)表示索带状态,(c)表示毛细管状态,(d)表示浆料状态。
36.图6是示意地示出一个实施方式的搅拌造粒机的一个例子的说明图。
37.图7是示意地示出一个实施方式的成膜装置的构成的说明图。
38.图8是示意地示出一个实施方式的电极复合材料层的加压工序的图,(a)示出干燥工序后的状态,(b)示出加压工序的状态,(c)示出加压工序后的状态。
39.图9是示意地示出另一实施方式的电极复合材料层的加压工序的图,(a)示出干燥工序后的状态,(b)示出加压工序的状态,(c)示出加压工序后的状态。
40.图10是示意地示出一个实施方式的锂离子二次电池的说明图。
41.图11是示出使用气相控制湿润粉体而形成的正极活性物质层(加压后)的结构的截面sem图像。
42.符号说明
43.1 凝聚粒子
44.2 活性物质粒子(固相)
45.3 溶剂(液相)
46.4 空隙(气相)
47.10 电极
48.12 电极集电体
49.14 电极活性物质层
50.22 低密区域
51.24 高密区域
52.26 间距
53.30 电极材料
54.32 涂膜
55.40 成膜装置
56.64 正极活性物质层
57.74 负极活性物质层
58.80 卷绕电极体
59.90 隔离件
60.100 电极制造装置
61.110 搅拌造粒机
62.112 混合容器
63.114 混合叶片
64.118 马达
65.120 成膜部
66.130 涂膜加工部
67.132 凹凸转印辊
68.150 加压部
69.200 锂离子二次电池
具体实施方式
70.以下,以作为二次电池典型例的锂离子二次电池所优选采用的电极为例,对在此公开的湿润粉体和使用该湿润粉体的成膜工艺(mps)进行详细说明。
71.本说明书中除了特别提及的事项以外的事情且为实施所必需的事情可以基于该领域中现有技术作为本领域技术人员的设计事项而把握。在此公开的技术内容可以基于本说明书中公开的内容和该领域中的技术常识来实施。
72.另外,尺寸关系(长度、宽度、高度等)并不反映实际的尺寸关系。
73.应予说明,本说明书中表示范围的“a~b(其中,a、b为任意的值)”的记载意味着a
以上b以下。
74.本说明书中“锂离子二次电池”是指电解质中的锂离子担负电荷移动的二次电池。另外,“电极体”是指成为由正极和负极构成的电池的主体的结构体。本说明书中,无需将正极和负极进行特别区别时,简写为电极。电极活性物质(即正极活性物质或负极活性物质)是指能够可逆地吸留和放出作为电荷载体的化学物质(锂离子二次电池中为锂离子)的化合物。
75.如图1a~图1d和图2所示,本实施方式的电极10具备电极集电体12和该集电体12上形成的电极活性物质层14。在此公开的电极10的特征在于,在电极活性物质层14的表面以规定的图案和一定的间距重复电极密度相对较低的低密区域22和相对较高的高密区域24。
76.电极集电体12可以没有特别限制地使用作为这种二次电池的电极集电体所使用的金属制的电极集电体。电极集电体12为正极集电体时,电极集电体12例如由具有良好的导电性的铝、镍、钛、不锈钢等金属材料构成。特别优选铝(例如铝箔)。电极集电体12为负极集电体时,电极集电体12例如由具有良好的导电性的铜、以铜为主体的合金、镍、钛、不锈钢等金属材料构成。特别优选铜(例如铜箔)。电极集电体12的厚度例如大致为5μm~20μm,优选为8μm~15μm。
77.形成电极活性物质层14的电极材料至少含有多个电极活性物质粒子、粘结剂树脂和溶剂。
78.作为属于固体成分的主成分的电极活性物质,可以使用作为以往的二次电池(这里为锂离子二次电池)的负极活性物质或正极活性物质所采用的组成的化合物。例如,作为负极活性物质,可举出石墨、硬碳、软碳等碳材料。另外,作为正极活性物质,可举出lini
1/3
co
1/3
mn
1/3
o2、linio2、licoo2、lifeo2、limn2o4、lini
0.5
mn
1.5
o4等锂过渡金属复合氧化物、lifepo4等锂过渡金属磷酸化合物。电极活性物质的平均粒径没有特别限定,0.1μm~50μm左右比较适当,优选为1~20μm左右。应予说明,本说明书中,“平均粒径”是指在基于通常的激光衍射/光散射法的体积基准的粒度分布中从粒径小的微粒侧起累积频率相当于50体积%的粒径(d
50
,也称为中值粒径)。
79.作为溶剂,例如,可以优选使用n-甲基-2-吡咯烷酮(nmp)、水系溶剂(水或以水为主体的混合溶剂)等。
80.作为粘结剂树脂,可举出聚偏氟乙烯(pvdf)、羧甲基纤维素(cmc)、苯乙烯-丁二烯橡胶(sbr)、聚丙烯酸(paa)等。根据所使用的溶剂而采用适当的粘结剂树脂。
81.电极材料可以含有电极活性物质和粘结剂树脂以外的物质、例如导电材料、增稠剂等作为固体成分。作为导电材料,例如,可举出乙炔黑(ab)等炭黑、碳纳米管这样的碳材料作为优选例。另外,作为增稠剂,例如,可以优选使用羧甲基纤维素(cmc)、甲基纤维素(mc)等。只要不损害本发明的效果,电极材料也可以含有上述以外的材料(例如各种添加剂等)。
82.应予说明,本说明书中,“固体成分”是指上述各材料中不包括溶剂在内的材料(固体材料),“固体成分率”是指在将各材料全部混合的电极材料中固体成分所占的比例。
83.电极活性物质层14的平均膜厚没有特别限定,例如,可以为10μm~300μm(例如,20μm~250μm)。从电池的高容量化的观点考虑,优选平均膜厚比以往更厚,例如可以为150μm
~300μm(例如,200μm~250μm)左右。
84.如图1a~图1d所示,在此公开的电极10的表面以规定的图案和一定的间距形成电极密度相对较低的低密区域22和电极密度相对较高的高密区域24。应予说明,本说明书中,“电极密度(g/cm3)”是指在电极活性物质层(即,干燥后的涂膜)中除去空隙(气相)以外的固体成分密度。例如,电极密度(g/cm3)可以通过将电极活性物质层的质量w除以电极活性物质层的表观体积v而求出。电极活性物质层的表观体积v可以由电极活性物质层的俯视下的面积s和电极活性物质层的厚度t而求出。
85.电极密度(g/cm3)根据所使用的电极材料等而不同,因此不能一概而言,例如,在电极为正极的情况下,电极密度优选为1.0g/cm3~4.5g/cm3,更优选为2.0g/cm3~4.2g/cm3,进一步优选为2.2g/cm3~3.8g/cm3。在电极为负极的情况下,例如,电极密度优选为0.8g/cm3~2.0g/cm3,更优选为0.9g/cm3~1.8g/cm3,进一步优选为1.0g/cm3~1.6g/cm3。典型而言,在上述电极密度的范围内形成低密区域22和高密区域24。
86.另外,本说明书中,“图案”是指特定的形状(样式)。“间距”是指重复低密区域22和高密区域24的最小单位,图2中“间距”用图中的符号26表示。图1a~图1d示意地图示了电极10中形成的典型的规定的图案。如图1a~图1d所示,规定的图案可以为横纹状、竖纹状、菱形状、点状。如图1a、图1b所示,间距26可以仅在x方向或y方向中的一个方向形成为恒定的。
87.图2为示意地示出在此公开的电极的一个例子的图。图2中的符号x表示电极的长边方向,符号z表示电极的厚度方向。如图2所示,将电极活性物质层14均等地区分所得的3个层在本说明书中称为上层、中间层和下层。从电极活性物质层14与电极集电体12的界面沿着厚度方向(z方向)依次位于下层、中间层、上层。例如,下层是指从电极活性物质层14与电极集电体12的界面沿着厚度方向(z方向)直到电极活性物质层14的厚度的大体33%以内的位置。同样,中间层是指沿着电极活性物质层14的厚度方向(z方向)位于电极活性物质层14的厚度的大体33%~66%的位置,上层是指位于电极活性物质层14的厚度的大体66%~100%的位置。另外,将低密区域22中的上层、中间层和下层的电极密度分别设为d
l1
、d
l2
、d
l3
,将高密区域24中的上层、中间层和下层电极密度分别设为d
h1
、d
h2
、d
h3
。
88.应予说明,上层、中间层和下层的电极密度例如可以通过将电极的真密度乘以该范围(即上层、中间层和下层中的任一者)的填充率而求出。电极的真密度例如为基于构成成分的密度和含有比例而算出的值。该范围的填充率例如可以通过在基于扫描式电子显微镜(sem)的电极活性物质层的截面观察中进行二值化处理而算出。具体而言,取得多个该截面图像,使用开放资源且作为公有领域的图像处理软件而著名的图像解析软件“imagej”,进行将该范围存在的固相部分设为白色并将气相(空隙)部分设为黑色的二值化处理。由此,可以将固相存在的部分(白色部分)的面积设为s1,将空隙部分(黑色部分)的面积设为s2,由“s1/(s1+s2)
×
100”而算出。
89.在此公开的电极10的特征在于,低密区域22和高密区域24的上层和下层的电极密度(g/cm3)具备(d
h3
/d
l3
)<(d
h1
/d
l1
)的关系。即,特征在于:电极10(电极活性物质层14)的上层中的电极密度的差别大于下层中的电极密度的差别,在电极10的表面部形成了电极密度相对为低密度的低密区域22和高密度的高密区域24。根据上述构成,在可以成为与电解液的界面的电极活性物质层14的上层存在成为li离子的嵌入/脱嵌路径的低密区域22和导电路径增加的高密区域24,因此li离子扩散阻力降低。由此,能够实现使用电极10的二次电池
的输出特性提高。
90.另外,电极活性物质层14的低密区域22的上层和下层的电极密度具备(d
l1
/d
l3
)<1.1的关系。更优选低密区域22的上层和下层的电极密度具备0.8<(d
l1
/d
l3
)<1.1的关系,进一步优选具备0.9<(d
l1
/d
l3
)<1.08的关系。低密区域22的上层和下层不存在电极密度之差的情况下,(d
l1
/d
l3
)的值为1。即,在此公开的电极10中,特性在于:低密区域22的上层和下层中电极密度的差别小(即(d
l1
/d
l3
)接近1)。根据上述构成,通过以从上层到下层的密度差小的状态形成上述低密区域,能够将li离子适当地导入到集电体附近存在的电极活性物质中。
91.低密区域22和高密区域24以规定的图案和一定的间距而形成。上述间距例如优选为250μm~5mm,更优选为750μm~4mm,进一步优选为1mm~3mm。如果为上述范围内的间距,则能够更理想地发挥上述效果。
92.电极活性物质层14例如可以在表面以规定的图案形成凹凸形状。电极活性物质层14具有凹凸形状时,在作为相对较低的位置的凹部形成低密区域22,在作为相对较高的位置的凸部形成高密区域24。凹凸形状的凹部深度(即,凹凸形状的高低差)没有特别限定,为5μm~100μm(例如,10μm~50μm)左右。根据上述构成,在与高密区域24相比相对较低的区域形成可成为li离子的嵌入/脱嵌路径的低密区域22,因此能够将li离子适当地扩散到电极10(电极活性物质层14)的更下层。
93.应予说明,电极活性物质层14在表面具有凹凸形状的情况下,在凹部和凸部分别将电极活性物质层14在厚度方向均等地区分为上层、中间层和下层这3个层。
94.能够通过在电极活性物质层14的表面以规定的图案和一定的间距形成低密区域22和高密区域24而提高电极10的离子扩散性的理由没有特别限定,但推测如下。电极活性物质层14(即干燥后的涂膜)的电极密度相对较低的低密区域22中,固体成分(例如,电极活性物质、导电材料等)之间存在比较多的空隙(气相),因此为形成了li离子的嵌入/脱嵌路径的状态。由此,在电解质与电极10之间促进li离子的迁移。另一方面,电极密度相对较高的高密区域24的空隙(气相)相对较少,固体成分以更紧密接触的状态存在。通过提高作为固体成分的电极活性物质彼此以及电极活性物质与导电材料的接触性,在高密区域24内适当地形成导电路径。另外,在此基础上,通过将低密区域22和高密区域24以规定图案和一定的间距而形成,能够使整个电极活性物质层14参与电化学反应,能够提高电极10的电池性能。
95.<电极的制造方法>
96.如图3所示,在此公开的电极的制造方法大致包含以下的5个工序:(1)准备湿润粉体(电极材料)的工序(s1);(2)形成由湿润粉体构成的涂膜的工序(s2);(3)在涂膜上形成凹凸的工序(s3);(4)将凹凸形成后的涂膜干燥的工序(s4);(5)对干燥后的涂膜(电极活性物质层)进行加压的工序(s5),其特征在于:以残留气相的状态形成涂膜并在干燥工序前形成凹凸。因此,其它工序没有特别限定,为与以往这种制造方法同样的构成即可。以下,对各工序进行说明。
97.图4是示意地示出本实施方式的具备辊式成膜部的电极制造装置的简要构成的说明图。图4中示出的电极制造装置100典型地具备:一边将从未图示的供给室传送来的片状电极集电体12沿着长边方向传送一边在电极集电体12的表面上形成由电极材料30构成的
涂膜32的成膜部120,在该涂膜32的表面形成凹凸形状的涂膜加工部130,使表面具有凹凸形状的涂膜32适当干燥而形成电极活性物质层14的干燥部140,以及对干燥后的电极活性物质层14以适当的加压压力进行加压的加压部150。它们沿着预先确定的传送路径依次配置。
98.<准备工序>
99.电极材料30可以通过使用以往公知的混合装置将上述电极活性物质、溶剂、粘结剂树脂、以及其它添加物等材料混合来准备。作为上述混合装置,例如,可举出行星式混合机、球磨机、辊磨机、捏合机、均质机等。
100.电极材料30可以取得糊料、浆料和造粒体的形态,但造粒体、特别是包含少量溶剂的湿润状态的造粒体(湿润粉体)适合于在这里公开的电极制造装置100中将电极活性物质层14成膜于电极集电体12上的目的。应予说明,本说明书中,关于湿润粉体的形态的分类,采用capes c.e.著的“particle size enlargement”(elsevier scientific publishing company刊,1980年)中记载且现在成为公知的4种分类,在此公开的湿润粉体已经明确规定。具体而言,如下所述。
101.关于构成湿润粉体的凝聚粒子中的固体成分(固相)、溶剂(液相)和空隙(气相)的存在形态(填充状态),可以分类为“钟摆状态”、“索带状态”、“毛细管状态”和“浆料状态”这4种。
102.这里,如图5的(a)所示,“钟摆状态”为以将凝聚粒子1中的活性物质粒子(固相)2间桥联的方式不连续地存在溶剂(液相)3的状态,活性物质粒子(固相)2可以以相互连接的(连续的)状态存在。如图示那样,溶剂3的含有率相对较低,其结果,凝聚粒子1中存在的空隙(气相)4大多连续存在,形成与外部连通的连通孔。而且,可举出如下特征:在钟摆状态下,在电子显微镜观察(sem观察)中看不到遍及凝聚粒子1的整个外表面而连续的溶剂的层。
103.另外,如图5的(b)所示,“索带状态”是凝聚粒子1中的溶剂含有率与钟摆相比相对更高的状态,是在凝聚粒子1中的活性物质粒子(固相)2的周围连续存在溶剂(液相)3的状态。但是,由于溶剂量依然很少,因此与钟摆状态同样以活性物质粒子(固相)2相互连接的(连续的)状态存在。另一方面,虽然凝聚粒子1中存在的空隙(气相)4中的与外部连通的连通孔的比例略微减少,有不连续的独立空隙的存在比例增加的趋势,但确认了存在连通孔。
104.索带状态为钟摆状态与毛细管状态之间的状态,在区分为靠近钟摆状态的索带i状态(即,溶剂量较少的状态)和靠近毛细管状态的索带ii状态(即,溶剂量较多的状态)时的索带i状态下,依然包含在电子显微镜观察(sem观察)中在凝聚粒子1的外表面看不到溶剂的层的状态。
[0105]“毛细管状态”如图5的(c)所示,凝聚粒子1中的溶剂含有率增大,凝聚粒子1中的溶剂量接近饱和状态,在活性物质粒子2的周围连续存在足够量的溶剂3,结果,活性物质粒子2以不连续的状态存在。凝聚粒子1中存在的空隙(气相)也因溶剂量的增大而使几乎所有空隙(例如总空隙体积的80vol%)以独立空隙的形式存在,空隙在凝聚粒子中所占的存在比例也变小。
[0106]“浆料状态”如图5的(d)所示,活性物质粒子2已经为悬浮于溶剂3中的状态,成为不能称为凝聚粒子的状态。几乎不存在气相。
[0107]
一直以来已知有使用湿润粉体而成膜的湿润粉体成膜,但以往的湿润粉体成膜中,湿润粉体是在粉体整体中连续形成液相的即图5(c)中示出的“毛细管状态”。
[0108]
与此相对,在此公开的湿润粉体是以个数计至少50%以上的凝聚粒子1形成(1)上述钟摆状态或索带状态(特别是索带i状态)的湿润粉体。优选具有通过控制气相而(2)在电子显微镜观察中看不到遍及该凝聚粒子的整个外表面的由上述溶剂构成的层作为一个形态特征。
[0109]
以下,将具备在此公开的上述(1)和(2)的要件的湿润粉体称为“气相控制湿润粉体”。
[0110]
应予说明,在此公开的气相控制湿润粉体优选以个数计至少50%以上的凝聚粒子具备上述(1)和(2)的要件。
[0111]
气相控制湿润粉体可以按照以往的毛细管状态的湿润粉体的制造工艺来制造。即,可以通过以气相的比例多于以往的方式,具体而言以形成很多从凝聚粒子的内部到外部的连续的空隙(连通孔)的方式调整溶剂量与固体成分(活性物质粒子、粘结剂树脂等)的配合来制造包含于上述钟摆状态或索带状态(特别是索带i状态)的作为电极材料(电极复合材料)的湿润粉体。
[0112]
另外,为了用最少的溶剂来实现活性物质间的液桥,优选所使用的粉体材料的表面与所使用的溶剂具有适当的亲和性。
[0113]
作为在此公开的优选的气相控制湿润粉体,可优选举出如下湿润粉体:通过电子显微镜观察而看到的三相的状态为钟摆状态或索带状态(特别是索带i状态),进而由松散堆积密度x(g/ml)和原料基体的真密度y(g/ml)算出的“真密度y与松散堆积密度x之比:y/x”为1.2以上、优选1.4以上(进而1.6以上)且优选为2以下,所述松散堆积密度是将所得到的湿润粉体以不施加力而刮平的方式装入规定容积的容器进行测量所得到的实测的堆积密度,所述原料基体的真密度y是假定不存在气相而由湿润粉体的组成算出的密度。
[0114]
上述湿润粉体可以通过使用如图6所示的搅拌造粒机(行星式搅拌机等搅拌机)110将各材料混合来制造湿润粉体(即,凝聚粒子的集合物)。如图示那样,这种搅拌造粒机110典型而言具备为圆筒形的混合容器112、收容于该混合容器112的内部的混合叶片114、以及介由旋转轴116与混合叶片(也称为桨叶)114连接的马达118。向如图6所示的搅拌造粒机110的混合容器112内投入作为固体成分的电极活性物质和各种添加物(粘结剂树脂、增稠材料、导电材料等),驱动马达118使混合叶片114例如以2000rpm~5000rpm的旋转速度旋转1~30秒左右,由此制造固体成分的混合体。然后,将以固体成分为55%以上、更优选60%以上(例如65~90%)的方式计量的少量溶剂添加到混合容器112内,使混合叶片114例如以100rpm~1000rpm的旋转速度进一步旋转1~30秒左右。由此,能够将混合容器112内的各材料与溶剂混合来制造湿润状态的造粒体(湿润粉体)。应予说明,能够通过进一步以1000rpm~3000rpm左右的旋转速度间歇进行1~5秒左右的短期搅拌来防止湿润粉体的凝聚。所得到的造粒体的粒径例如可以为50μm以上(例如100μm~300μm)。
[0115]
另外,对于上述气相控制湿润粉体,溶剂含有率低至在凝聚粒子的外表面看不到溶剂的层的程度(例如溶剂分率可以为2~15%左右,可以为3~8%),相反,气相部分相对较大。上述气相控制湿润粉体可以按照上述湿润粉体的制造工艺来制造。即,可以通过以与上述湿润粉体相比气相的比例变多的方式,具体而言以形成许多从凝聚粒子的内部到外部
的连续的空隙(连通孔)的方式调整溶剂量与固体成分(活性物质粒子、粘结剂树脂等)的配合来制造包含于上述钟摆状态或索带状态(特别是索带i状态)的作为电极材料的湿润粉体。另外,为了用最少的溶剂来实现活性物质间的液桥,优选所使用的粉体材料的表面与所使用的溶剂具有适当的亲和性。
[0116]
<成膜工序>
[0117]
在此公开的制造方法中,特征在于,以残留电极材料30的气相(空隙)的状态形成涂膜32。由电极材料30构成的涂膜32的成膜例如可以使用如图7中示意地示出的成膜装置40而进行。成膜装置40具备由第1旋转辊41(以下称为“供给辊41”)和第2旋转辊42(以下称为“转印辊42”)构成的一对旋转辊41、42。供给辊41的外周面与转印辊42的外周面彼此对置,这一对旋转辊41、42可以如图7的箭头所示向相反方向旋转。另外,供给辊41与转印辊42仅分开为与在电极集电体12上成膜的涂膜32的所期望的厚度对应的距离。即,供给辊41与转印辊42之间具有规定宽度(厚度)的间隙,可以根据上述间隙的尺寸来控制由附着于转印辊42的表面的电极材料30构成的涂膜32的厚度。另外,通过调整上述间隙的尺寸,还能够调整将在供给辊41与转印辊42之间通过的电极材料30压缩的力。因此,通过取得比较大的间隙尺寸,能够以保持电极材料30(具体而言,各凝聚粒子)的气相的状态进行成膜。
[0118]
供给辊41和转印辊42的宽度方向的两端部设置有隔壁45。隔壁45将电极材料30保持在供给辊41和转印辊42上,同时起到利用2个隔壁45间的距离来规定成膜于电极集电体12上的涂膜32的宽度的作用。利用进料口(未图示)等向该2个隔壁45之间供给电极材料30。
[0119]
本实施方式的成膜装置40中,与转印辊42相邻地配置支撑辊43作为第3旋转辊。支撑辊43起到将电极集电体12传送到转印辊42的作用。转印辊42与支撑辊43如图7的箭头所示向相反方向旋转。
[0120]
供给辊41、转印辊42、支撑辊43分别连接于未图示的彼此独立的驱动装置(马达),通过依次将供给辊41、转印辊42和支撑辊43各自的旋转速度缓慢提高,能够将电极材料30沿着转印辊42传送,从转印辊42的外周面将该电极材料30转移至由支撑辊43传送来的电极集电体12的表面上作为涂膜32。
[0121]
应予说明,图7中,供给辊41、转印辊42、支撑辊43虽然配置成各旋转轴水平排列,但并不局限于此。
[0122]
供给辊41、转印辊42和支撑辊43的尺寸没有特别限制,与以往的成膜装置同样即可,例如直径可以分别为50mm~500mm。这3种旋转辊41、42、43的直径可以为相同的直径,也可以为不同的直径。另外,形成涂膜32的宽度也与以往的成膜装置同样即可,可以根据形成涂膜32的对象电极集电体12的宽度而适当地决定。
[0123]
供给辊41、转印辊42和支撑辊43的外周面的材质与以往公知的成膜装置中的旋转辊的材质相同即可,例如,可举出sus钢、suj钢等。为了防止金属异物的产生,与电极材料30直接接触的供给辊41和转印辊42的外周面的材质更优选为例如氧化锆、氧化铝、氮化铬、氮化铝、二氧化钛、氧化铬等陶瓷。
[0124]
如图4所示,成膜部120与上述成膜装置40同样地具备分别连接于未图示的彼此独立的驱动装置(马达)的供给辊121、转印辊122、123、124和支撑辊125。
[0125]
本实施方式的成膜部120中,如图示那样,连续具备多个转印辊。该例中,具备与供给辊121对置的第1转印辊122、与该第1转印辊122对置的第2转印辊123、和与该第2转印辊
123对置且也与支撑辊125对置的第3转印辊124。
[0126]
供给辊121、第1转印辊122、第2转印辊123、第3转印辊124和支撑辊125由于连接于各自独立的未图示的驱动装置(马达),因此可以分别以不同的旋转速度进行旋转。具体而言,与供给辊121的旋转速度相比第1转印辊122的旋转速度更快,与第1转印辊122的旋转速度相比第2转印辊123的旋转速度更快,与第2转印辊123的旋转速度相比第3转印辊124的旋转速度更快,与第3转印辊124的旋转速度相比支撑辊125的旋转速度更快。
[0127]
通过这样在各旋转辊间沿着集电体传送方向(行进方向)一点一点提高旋转速度,能够进行与图7的成膜装置40不同的多阶段辊式成膜。
[0128]
如图4所示,将供给辊121与第1转印辊122之间设为第1间隙g1、将第1转印辊122与第2转印辊123之间设为第2间隙g2、将第2转印辊123与第3转印辊124之间设为第3间隙g3、而且将第3转印辊124与支撑辊125之间设为第4间隙g4时,间隙的尺寸以第1间隙g1相对最大且第2间隙g2、第3间隙g3、第4间隙g4依次一点一点变小的方式设定(g1>g2>g3>g4)。由于将间隙g1~g4以沿着电极集电体12的传送方向(行进方向)间隙缓慢变小的方式设定,因此能够一边调整涂膜32的气相(空隙)的状态一边进行成膜。各间隙g1~g4的尺寸(宽度)没有特别限定,只要设定成涂膜32的平均膜厚成为10μm~300μm(例如,20μm~150μm)的间隙尺寸即可。
[0129]
另外,电极材料30为气相控制湿润粉体的情况下,通过进行多阶段辊式成膜,能够保持气相控制湿润粉体的连通孔而形成适当的涂膜。即,能够防止构成气相控制湿润粉体的凝聚粒子的过度压碎,保持连通孔并防止在凝聚粒子内产生独立空隙。
[0130]
<凹凸形成工序>
[0131]
对涂膜32形成凹凸例如可以使用如图4所示的凹凸转印辊132和支撑辊134而进行。在此公开的电极的制造方法中,其特征在于,对以残留空隙(气相)的状态成膜的涂膜32实施凹凸形成工序s3。上述涂膜32的平均空隙率(气相率)优选至少为1%以上,例如可以为1%~55%、典型而言为5%~55%。通过以残留气相的状态形成凹凸而使延展性提高,因此能够用小于以往的负荷对涂膜32赋予所期望的凹凸形状。另外,即便为了形成凹凸而施加负荷,也能够在涂膜32的表面部以不使局部密度上升(致密化)的方式形成凹凸形状。
[0132]
应予说明,本说明书中,“涂膜的平均空隙率(气相率)”例如可以通过基于扫描式电子显微镜(sem)的涂膜的截面观察而算出。对该截面图像使用为开放资源且作为公有领域的图像处理软件而著名的图像解析软件“imagej”进行将固相或液相部分设为白色且将气相(空隙)部分设为黑色的二值化处理。由此,可以将存在固相或液相的部分(白色部分)的面积设为s1,将空隙部分(黑色部分)的面积设为s2而算出“s2/(s1+s2)
×
100”。将其作为干燥前的涂膜的空隙率。取得多个截面sem图像(例如5张以上),将上述空隙率的平均值作为这里的干燥前的“涂膜的平均空隙率(气相率)”。应予说明,“涂膜的平均空隙率(气相率)”不包含凹凸形成过程中形成的凹部(即宏观的空隙)。
[0133]
凹凸转印辊132具有用于在涂膜32的表面以一定的间距形成规定图案的凹部和凸部。支撑辊134是用于一边支撑被传送来的电极集电体12一边在传送方向送出的辊。凹凸转印辊132和支撑辊134配置于对置的位置。通过在凹凸转印辊132与支撑辊134的间隙通过电极集电体12上的涂膜32而将凹凸转印辊132的凹凸部转印到涂膜32的表面,由此能够在涂膜32的表面形成所期望的形状。凹凸转印辊132的线压可以根据所期望的形状的凹部深度
等而不同,因此没有特别限定,可以大体设定为15n/cm~75n/cm、例如25n/cm~65n/cm左右。
[0134]
应予说明,对涂膜32加工凹凸的方法也可以通过使用了凹凸转印辊的凹凸转印以外的方法而进行。例如,可以使用具有所期望的凹凸形状的平板压延机,进行挤压而在涂膜32的表面部形成凹凸形状。该情况下的加压压力例如可以设定为1mpa~100mpa、例如5mpa~80mpa左右。
[0135]
本发明人等反复进行深入研究,结果,凹凸转印辊132的凹部与凸部的间距可以设定为250μm~5mm(例如,1mm~3mm)。根据上述构成,可以在干燥后的涂膜32(电极活性物质层14)适当形成电极密度相对较低的低密区域22和相对较高的高密区域24。由此,可以提高干燥后的涂膜32(电极活性物质层14)的li离子扩散性。
[0136]
涂膜32通过为残留气相的状态,从而即便在干燥工序s4前形成凹凸形状,也能够形成所期望的图案并保持该图案。另外,更理想的是,涂膜32优选由气相控制湿润粉体构成。气相控制湿润粉体如上所述以保持连通孔的状态成膜,因此能够更适当地实施所期望的图案的形成和该图案的保持。
[0137]
图4所示出的一个例子中,凹凸转印辊132和支撑辊134仅设置一对,但是并不局限于此,也可以沿着传送方向配置多个凹凸转印辊,并以各自的加压压力不同的方式设定。
[0138]
另外,也可以进一步包含在涂膜加工部130中使用加压辊136和支撑辊138来调整涂膜32的电极密度、膜厚的工序。加压辊136是用于将涂膜32在膜厚方向挤压而压缩的辊,支撑辊138是用于将传送来的电极集电体12边支承边在传送方向送出的辊。加压辊136和支撑辊138配置于对置的位置。可以将被传送来的电极集电体12上形成(成膜)的由钟摆状态或索带状态(优选索带i状态)的电极材料30构成的涂膜32加压并压缩到例如不产生独立空隙的程度。由此,可以以更适合实施凹凸形成的方式调整涂膜32的气相的状态。
[0139]
上述工序中的基于加压辊136的适当的加压压力可以根据目标涂膜(电极活性物质层)的膜厚、密度而不同,因此没有特别限定,例如,可以设定为0.01mpa~100mpa、例如0.1mpa~70mpa左右。
[0140]
<干燥工序>
[0141]
如图4所示,本实施方式的电极制造装置100的相对于涂膜加工部130在传送方向的下游侧配置具备未图示的加热器(heater)的干燥室142作为干燥部140,对从涂膜加工部130传送来的涂膜32进行干燥,在电极集电体12的表面上形成电极活性物质层14。干燥的方法没有特别限定,例如,可举出热风干燥、红外线干燥等方法。应予说明,干燥工序s4与以往的这种电极制造装置中的干燥工序相同即可,由于并不特别表征本发明,因此省略进一步的详细说明。
[0142]
<加压工序>
[0143]
干燥工序s4之后,加压部150中以调整电极活性物质层14的单位面积重量、电极密度为目的而实施加压工序s5。上述加压工序可以使用辊式压延机、平板压延机按照以往公知的方法而进行。
[0144]
图8和图9是示意地示出干燥工序s4后实施的加压工序的过程的图。图8和图9的(a)示出干燥工序后的状态,(b)示出加压工序的状态,(c)示出加压工序后的状态。以下,参照图8和图9对加压工序s5进行说明。
[0145]
这里实施的加压是对利用干燥工序s4从涂膜32中蒸发(挥发)溶剂(液相)后的电极活性物质层14实施的加压,因此优选设定为与对干燥前的湿润状态的涂膜32的加压压力相比较高的加压压力。例如,基于辊式压延机的辊式加压中,优选设定为线压1ton/cm~5ton/cm左右。利用平板压延机进行加压时,例如,优选设定为100~500mpa左右。
[0146]
本实施方式的电极10(电极活性物质层14)如图8的(a)所示以干燥后保持规定的凹凸形状的状态向加压工序s5传送。如图8(b)所示地使用加压装置152来实施加压。此时,首先,对电极活性物质层14的凸部进行加压。电极活性物质层14的凸部被加压到与电极活性物质层14的凹部大致同等高度时,接着也对电极活性物质层14的凹部进行加压。这里,形成如图8(c)所示的电极活性物质层14的表面平坦的电极10的情况下,以加压到电极活性物质层14的凹部的高度的方式设定加压压力即可。另外,如图9(c)所示略微残留凹凸形状而形成电极10的情况下,适当设定进行加压直到所期望的高度的加压压力即可。应予说明,图8a~图8c和图9a~图9c中的符号x表示电极的长边方向,符号z表示电极的厚度方向。
[0147]
图8和图9的(a)中通过利用加压将作为电极活性物质层14的凸部的区域向厚度方向(z方向)压缩而成为电极密度相对较高的高密区域24。上述高密区域可以为能量密度高的区域。另外,图8和图9的(a)中作为电极活性物质层14的凹部的区域,利用加压装置152所施加的加压压力小,成为电极密度相对较低的低密区域22。根据上述制造方法,能够以所期望的图案形成高密区域24和低密区域22。
[0148]
由此制造的片状电极作为通常的这种片状正极或负极而用于构建锂离子二次电池。
[0149]
例如,将可使用本实施方式的片状电极而构建的锂离子二次电池200的一个例子示于图10。
[0150]
图10中示出的锂离子二次电池200通过将扁平形状的卷绕电极体80和非水电解质(未图示)收容于可密闭的箱型电池壳体50而构建。电池壳体50中设置有外部连接用的正极端子52和负极端子54、以及以电池壳体50的内压上升到规定水平以上时释放该内压的方式设定的薄壁的安全阀56。另外,电池壳体50中设置有用于注入非水电解质的注入口(未图示)。正极端子52与正极集电板52a进行电连接。负极端子54与负极集电板54a进行电连接。电池壳体50的材质优选高强度、轻量且热传导性良好的金属制材料,作为这样的金属材料,例如,可举出铝、钢等。
[0151]
卷绕电极体80典型地具有将长条片状的正极(以下,称为正极片60)和长条片状的负极(以下,称为负极片70)隔着长条片状的隔离件90重叠并在长边方向卷绕而成的形态。正极片60具有在正极集电体62的单面或两面沿着长边方向形成正极活性物质层64的构成。负极片70具有在负极集电体72的单面或两面沿着长边方向形成负极活性物质层74的构成。正极集电体62的宽度方向的一侧的边缘部设置有沿着该边缘部不形成正极活性物质层64而露出正极集电体62的部分(即,正极集电体露出部66)。负极集电体72的宽度方向的另一侧的边缘部设置有沿着该边缘部不形成负极活性物质层74而露出负极集电体72的部分(即,负极集电体露出部76)。正极集电体露出部66和负极集电体露出部76分别接合正极集电板52a和负极集电板54a。
[0152]
正极(正极片60)和负极(负极片70)使用由上述制造方法而得到的正极和负极。应予说明,本构成例中,正极和负极在集电体12(正极集电体62和负极集电体72)的两面形成
电极活性物质层14(正极活性物质层64和负极活性物质层74)。
[0153]
作为隔离件90,例如,可举出由聚乙烯(pe)、聚丙烯(pp)、聚酯、纤维素、聚酰胺等树脂构成的多孔性片材(膜)。上述多孔质片材可以为单层结构,也可以为二层以上的层叠结构(例如,在pe层的两面层叠有pp层的三层结构)。隔离件90可以设置有耐热层(hrl)。
[0154]
非水电解质可以使用与以往的锂离子二次电池同样的非水电解质,典型而言,可以使用在有机溶剂(非水溶剂)中含有辅助盐(支持塩)的溶液。作为非水溶剂,可以没有特别限制地是使用碳酸酯类、酯类、醚类、腈类、砜类、内酯类等有机溶剂。具体而言,例如,可以优选使用碳酸亚乙酯(ec)、碳酸二乙酯(dec)、碳酸二甲酯(dmc)、碳酸甲乙酯(emc)、单氟碳酸亚乙酯(mfec)、二氟碳酸亚乙酯(dfec)、单氟甲基二氟甲基碳酸酯(f-dmc)、三氟碳酸二甲酯(tfdmc)等非水溶剂。这样的非水溶剂可以单独使用1种,或者适当组合2种以上使用。作为辅助盐,例如,可以优选使用lipf6、libf4、liclo4等锂盐。辅助盐的浓度没有特别限定,优选为0.7mol/l~1.3mol/l左右。
[0155]
应予说明,上述非水电解质只要不明显损害本发明的效果,也可以包含上述非水溶剂、辅助盐以外的成分,例如气体产生剂、被膜形成剂、分散剂、增稠剂等各种添加剂。
[0156]
由此构成的锂离子二次电池200可以用于各种用途。作为优选的用途,可举出搭载于电动汽车(bev)、混合动力汽车(hev)、插电式混合动力汽车(phev)等车辆的驱动用电源。锂离子二次电池200也可以以将多个串联和/或并联连接而成的电池组的形态使用。
[0157]
以下,对将在此公开的钟摆状态或索带状态的气相控制湿润粉体作为电极复合材料使用时的一些实施例进行说明但并不有意将在此公开的技术限定为该实施例所示的技术方案。
[0158]
<第1试验>
[0159]
制作可优选用作正极材料的气相控制湿润粉体,接着,使用该制作的湿润粉体(正极材料)在铝箔上形成正极活性物质层。
[0160]
本实施例中,使用基于激光衍射和散射方式的平均粒径(d
50
)为20μm的锂过渡金属氧化物(lini
1/3
co
1/3
mn
1/3
o2)作为正极活性物质,使用聚偏氟乙烯(pvdf)作为粘结剂树脂,使用乙炔黑作为导电材料,使用nmp作为非水溶剂。
[0161]
首先,将由90质量份的上述正极活性物质、2质量份的pvdf和8质量份的乙炔黑构成的固体成分投入到如图6所示的具有混合叶片的搅拌造粒机(行星式搅拌机或高速搅拌机),进行混合搅拌处理。
[0162]
具体而言,在具有混合叶片的搅拌造粒机内将混合叶片的旋转速度设定为4500rpm,进行15秒的搅拌分散处理,得到由上述固体成分构成的粉末材料的混合物。在所得到的混合物中以固体成分率为90重量%的方式添加作为溶剂的nmp,以300rpm的旋转速度进行30秒的搅拌造粒复合化,接着以4500rpm的旋转速度搅拌2秒而进行微细化。由此制作本实施例的湿润粉体(正极材料)。
[0163]
接下来,将上述得到的气相控制湿润粉体(正极材料)向上述电极制造装置的成膜部供给,将涂膜转印到另外准备的由铝箔构成的正极集电体的表面(实施例1)。
[0164]
对上述得到的实施例1的干燥前的涂膜的气相率(空隙率)(%)进行测定。具体而言,通过利用扫描式电子显微镜(sem),观察截面图像而算出。取得该截面图像,使用图像解析软件“imagej”,进行将固相或液相部分设为白色并将气相(空隙)部分设为黑色的二值化
处理。由此,将存在固相或液相的部分(白色部分)的面积设为s1,将空隙部分(黑色部分)的面积设为s2,算出“s2/(s1+s2)
×
100”。将其作为干燥前的涂膜的空隙率。取得5张截面sem图像,将上述空隙率的平均值作为这里的干燥前的“涂膜的平均空隙率(气相率)”。
[0165]
其结果,实施例1的涂膜的平均空隙率为55%。
[0166]
将实施例1的涂膜传送到涂膜加工部,使用凹凸转印辊(线压约40n/cm),赋予凹凸形状(间距1mm)。将具有上述凹凸形状的涂膜在干燥部进行加热干燥,其后,以线压约4ton/cm进行辊式加压。由此,得到在电极集电体上形成有由气相控制湿润粉体构成的电极活性物质层的电极(正极)。
[0167]
对上述得到的实施例1的电极活性物质层(即干燥后的涂膜)的状态利用sem进行观察。将结果示于图11。
[0168]
作为比较对象,使用相同的材料,准备浆料状态的电极(正极)材料。将上述正极材料涂布到正极集电体上进行干燥、加压,形成正极活性物质层。再次向上述正极活性物质层供给溶剂,对整个电极以线压约4ton/cm进行加压用以形成凹凸形状(间距1mm),再次进行干燥而得到形成了具有凹凸形状的正极活性物质层的电极(正极)(比较例1)。
[0169]
测定实施例1和比较例1的电极密度(g/cm3)。对于电极密度,根据从基准点起形成的间距设定a~d区域,在各位置测定上层和下层的电极密度。应予说明,上层和下层的电极密度通过将电极的真密度乘以该范围的填充率而求出。电极的真密度基于构成成分的密度和含有比例而算出。另外,该范围的填充率通过在基于扫描式电子显微镜(sem)的电极活性物质层的截面观察中使用图像解析软件“imagej”进行二值化处理而算出。将结果示于表1。
[0170]
<评价用锂离子二次电池的制作>
[0171]
使用上述制作的实施例1和各比较例1的电极,制作评价用锂离子二次电池。
[0172]
作为负极,准备由浆料状态的电极材料构成的电极。
[0173]
另外,作为隔离片,准备2张具有pp/pe/pp的三层结构的多孔性聚烯烃片材。
[0174]
将所制作的实施例1和比较例1的电极(正极)、负极和所准备的2张隔离片重叠,卷绕而制作卷绕电极体。对所制作的卷绕电极体的正极片和负极片分别通过焊接而安装电极端子,并将其收容于具有注入口的电池壳体。
[0175]
从上述注入口注入非水电解液,利用封口盖对该注入口进行气密性密封。应予说明,作为非水电解液,使用使作为辅助盐的lipf6以1.0mol/l的浓度溶解于以1:1:1的体积比包含碳酸亚乙酯(ec)、碳酸二甲酯(dmc)和碳酸甲乙酯(emc)的混合溶剂而成的溶液。由此得到评价用锂离子二次电池。
[0176]
<活化处理>
[0177]
在25℃的环境下,进行各评价用锂离子二次电池的活化处理(首次充电)。活化处理为恒定电流-恒定电压方式,通过以1/3c的电流值进行恒定电流充电直到4.2v后,进行恒定电压充电直到电流值达到1/50c而达到满充电状态。其后,以1/3c的电流值进行恒定电流放电直到电压达到3.0v。
[0178]
<初期电阻测定>
[0179]
将活化处理后的各评价用锂离子二次电池调整为soc(充电状态,state of charge)60%后,在25℃的温度环境下放置。以1c的电流值放电10秒,求出电压下降量(δv)。将上述电压下降量δv除以放电电流值(1c),算出电池电阻,将其作为初期电阻。应予说
明,随着上述初期电阻变小,可以评价为输出特性良好。将结果示于表1。
[0180]
[表1]
[0181][0182]
根据表1可知:比较例1中,a~d的所有区域的上层中电极密度上升。与此相对,实施例1中,b区域和d区域的上层中电极密度上升,电极的表面部形成高密区域和低密区域。另外,实施例1与比较例1相比,初期电阻变低。即,可知在电极活性物质层的表面以规定的图案和一定的间距重复电极密度相对为低密度的低密区域和相对为高密度的高密区域、具备(d
h3
/d
l3
)<(d
h1
/d
l1
)的关系的二次电池用电极的离子扩散性提高,将该电极用于二次电池时,初期电阻降低。
[0183]
另外,可知实施例1中低密区域的上层的电极密度d
l1
和下层的电极密度d
l3
满足(d
l1
/d
l3
)<1.1。
[0184]
<第2试验>
[0185]
变更电极材料和形成的凹凸形状的间距的条件而实施第2试验。具体而言,制作可优选作为负极材料使用的气相控制湿润粉体,使用该制作的湿润粉体(负极材料)在铜箔上形成负极活性物质层。
[0186]
本实施例中,使用基于激光衍射和散射方式的平均粒径(d
50
)为10μm的石墨粉作为负极活性物质,使用苯乙烯-丁二烯橡胶(sbr)作为粘结剂树脂,使用羧甲基纤维素(cmc)作为增稠剂,使用水作为溶剂。
[0187]
首先,将由98质量份的上述石墨粉、1质量份的cmc和1质量份的sbr构成的固体成分投入到如图6所示的具有旋转叶片的搅拌造粒机(行星式搅拌机或高速搅拌机),进行混合搅拌处理。
[0188]
具体而言,在具有旋转叶片的搅拌造粒机内将旋转叶片的旋转速度设定为4500rpm,进行15秒的搅拌分散处理,得到由上述固体成分构成的粉末材料的混合物。在所得到的混合物中添加作为溶剂的水以使固体成分率为90质量%,以300rpm的旋转速度进行30秒的搅拌造粒复合化处理,接着以1000rpm的旋转速度搅拌2秒继续进行微细化处理。由此制作本实施例的湿润粉体(负极材料)。进行混合搅拌处理和微细化,制作本实施例的湿润粉体(负极材料)。
[0189]
接下来,将上述得到的气相控制湿润粉体(负极材料)向上述电极制造装置的成膜部供给,将涂膜转印到另外准备的由铜箔构成的负极集电体的表面(实施例2)。
[0190]
利用与上述方法同样的方法测定上述得到的实施例2的干燥前的涂膜的气相率(空隙率)(%)。其结果,实施例2的涂膜的平均空隙率为50%。
[0191]
将实施例2的涂膜传送到涂膜加工部,使用凹凸转印辊(线压约40n/cm),赋予凹凸形状(间距250μm)。将具有上述凹凸形状的涂膜在干燥部进行加热干燥,其后,以线压约
4ton/cm进行辊式加压。由此,得到在电极集电体上形成有由气相控制湿润粉体构成的电极活性物质层的电极(负极)。
[0192]
按照与上述方法同样的方法测定实施例2的电极密度。对于电极密度,根据从基准点起形成的间距而设定a~d区域,在各位置测定上层和下层的电极密度。将结果示于表2。
[0193]
另外,使用上述制作的实施例2的电极来制作评价用锂离子二次电池。准备由浆料状态的电极材料构成的电极作为正极。除此以外的条件与上述同样地制作评价用锂离子二次电池,测定初期电阻值。将结果示于表2。
[0194]
[表2]
[0195][0196]
根据表2可知:即便改变电极材料、间距而制成电极时,也能够在电极的表面部形成相对的高密度区域和低密度区域。另外,还可知初期电阻为与实施例1同等程度的值。另外,第2试验中还可知低密区域的上层的电极密度d
l1
和下层的电极密度d
l3
满足(d
l1
/d
l3
)<1.1。
[0197]
以上,对本发明的具体例进行了详细说明,但这些仅为例示,并非限定要求保护的范围。要求保护的范围所记载的技术中包含对以上例示的具体例进行各种变形、变更的技术方案。