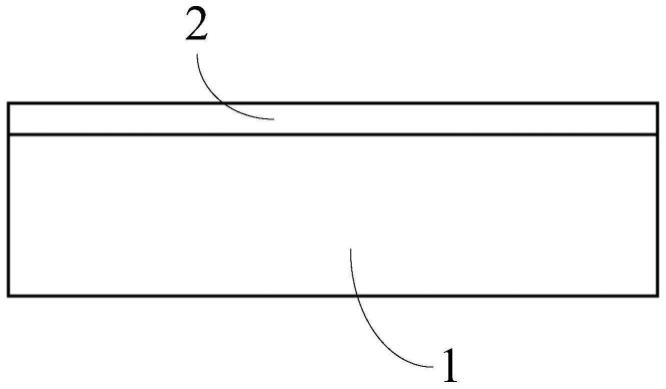
1.本发明涉及一种制备方法,尤其是一种低界面态密度碳化硅功率半导体器件的制备方法。
背景技术:2.sic材料可以通过热氧化形成sio2,使其可以沿用si晶片的功率半导体器件制作工艺,从而相对于其他宽禁带半导体材料可以实现更高的可靠性。然而由于c元素的存在,通过热氧化形成的sio2/sic界面存在高密度的界面态(1012
–
1013cm-2ev-1),比sio2/si界面态高2个量级以上。
3.对于sic晶片,高密度的界面态主要由si悬挂键,c悬挂键,或c-c键组成。近界面氧化层同样存在缺陷,导致由电荷俘获引起的沟道迁移率降低,限制了sic功率半导体器件的关键性能,即导通电阻ron无法降低至sic器件的理论性能。
4.实际应用中,sic器件的沟道迁移率约为《20cm2/vs,低于体迁移率2个量级,是目前阻碍sic功率半导体器件性能发展的最主要难题之一。除降低迁移率外,sio2/sic界面的高密度缺陷同样引起sic功率半导体器件的阈值电压不稳定,同样对sic功率半导体器件生产以及应用形成较大的困难。
技术实现要素:5.本发明的目的是克服现有技术中存在的不足,提供一种低界面态密度碳化硅功率半导体器件的制备方法,其能实现低密度界面态的碳化硅半导体器件制备,与现有工艺兼容,安全可靠。
6.按照本发明提供的技术方案,一种低界面态密度碳化硅功率半导体器件的制备方法,提供碳化硅晶片、制备于所述碳化硅晶片正面上的氧化膜以及制备于所述氧化膜上的正面元胞结构;在碳化硅晶片上氧化膜,包括如下步骤:
7.步骤1、采用热氧化工艺在碳化硅晶片上制备得到氧化底膜,并对所述碳化硅晶片以及氧化底膜进行所需的氧化后退火工艺;
8.步骤2、在上述氧化底膜上制备所需的硅膜层,所述硅膜层覆盖在氧化底膜上;
9.步骤3、对硅膜层进行热氧化,并热氧化退火后,制备得到覆盖于碳化硅晶片上的氧化膜。
10.步骤1中,氧化底膜的厚度为10nm~20nm。
11.步骤1中,步骤1中,所述氧化后退火工艺的温度范围700℃-1700℃,所使用的气体包括o2、ar、h2、n2、no、n2o或pocl3。
12.步骤2中,硅膜层采用沉积或贴合方式制备于氧化底膜上。
13.所述硅膜层的厚度为10nm~30nm,硅膜层采用沉积制备于氧化底膜上时,所述沉积方法包括cvd、pecvd、溅射或电子束蒸镀。
14.硅膜层采用贴合方式制备于氧化底膜上时,所述贴合方式包括smartcut贴合。
15.所述氧化膜的厚度为30nm~70nm。
16.还包括制备于碳化硅晶片背面的背面电极结构,利用背面电极结构以及位于碳化硅晶片正面上的正面元胞结构形成所需的功率半导体器件,其中,功率半导体器件为mosfet器件或igbt器件。
17.步骤3中,所述氧化后退火工艺的温度范围700℃-1700℃,所使用的气体包括o2、ar、h2、n2、no、n2o或pocl3。
18.本发明的优点:通过热氧化在碳化硅晶片正面形成氧化底膜,氧化底膜的厚度不大于20nm,从而可实现低密度界面态的sic/sio2界面;在氧化底模上设置硅膜层,通过对硅膜层热氧化以及热氧化后的退火,能形成所需的氧化膜,在氧化膜上制备正面元胞结构后,即能实现低密度界面态的碳化硅半导体器件制备,与现有工艺兼容,安全可靠。
附图说明
19.图1~图4为具体制备得到氧化膜的工艺步骤剖视图,其中
20.图1为本发明碳化硅晶片的剖视图。
21.图2为本发明制备氧化层底模后的示意图。
22.图3为本发明制备得到硅膜层后的示意图。
23.图4为本发明制备得到氧化膜后的示意图。
24.附图标记说明:1-碳化硅晶片、2-氧化底膜、3-硅膜层以及4-氧化膜。
具体实施方式
25.下面结合具体附图和实施例对本发明作进一步说明。
26.为了能实现低密度界面态的碳化硅半导体器件制备,本发明低界面态密度碳化硅功率半导体器件的制备方法,具体地,提供碳化硅晶片1、制备于所述碳化硅晶片1正面上的氧化膜4以及制备于所述氧化膜4上的正面元胞结构;在碳化硅晶片1上氧化膜4,包括如下步骤:
27.步骤1、采用热氧化工艺在碳化硅晶片1上制备得到氧化底膜2,并对所述碳化硅晶片1以及氧化底膜2进行所需的氧化后退火工艺;
28.具体地,碳化硅晶片1可以采用现有常用的形式,如图1所示,碳化硅晶片1的厚度等可以根据实际需要选择,为本技术领域人员所熟知,此处不再赘述。低密度界面态的碳化硅功率半导体器件,具体是指,氧化膜4与碳化硅晶片1接触面呈现为低密度界面态。
29.为了能制备得到与碳化硅晶片1正面低密度界面态接触的氧化膜4,在碳化硅晶片1的正面先采用热氧化工艺制备得到氧化底膜2,氧化底膜2位于碳化硅晶片1的正面,如图2所示,其中,所采用热氧化工艺的方式以及条件等均可以根据需要选择,以能满足制备得到所需厚度的氧化底膜2为准,为本技术领域人员所熟知,此处不再赘述。
30.本发明实施例中,氧化底膜2的厚度为10nm~20nm;在热氧化时,仅生成厚度不大于20nm的氧化底膜2,当热氧化制备得到的氧化底膜2在20nm以下时,在这个厚度下由于c元素的生成物co的排出比直接氧化至50nm顺畅,同时,sic中的c元素主要反应为co气体扩散至氧化层外(部分c元素向晶片方向扩散),co气体排出一般通过高温氧化促进,实现更低的sio2/sic界面缺陷密度,即可实现低密度界面态的sic/sio2界面。
31.具体实施时,在制备得到所需厚度的氧化底膜2后,还需要进行氧化后退火工艺,其中,所述氧化后退火工艺的温度范围700℃-1700℃,所使用的气体包括o2、ar、h2、n2、no、n2o或pocl3。所述氧化后退火工艺的过程以及工艺条件均可以根据实际需要选择,此处不再赘述。
32.步骤2、在上述氧化底膜2上制备所需的硅膜层3,所述硅膜层3覆盖在氧化底膜2上;
33.具体实施时,硅膜层3采用沉积或贴合方式制备于氧化底膜2上,如图3所示。所述硅膜层3的厚度为10nm~30nm,硅膜层3采用沉积制备于氧化底膜2上时,所述沉积方法包括cvd(化学气相沉积)、pecvd(plasma enhanced chemical vapor deposition)、溅射或电子束蒸镀。硅膜层3采用贴合方式制备于氧化底膜2上时,所述贴合方式包括smartcut贴合。
34.步骤3、对硅膜层3进行热氧化,并热氧化退火后,制备得到覆盖于碳化硅晶片1上的氧化膜4。
35.具体地,对对硅膜层3进行热氧化,即能将硅膜层3的硅氧化成二氧化硅;当然,将硅膜层3热氧化成二氧化硅后,还需要进行热氧化后的退火工艺,从而在退火后,能得到覆盖于碳化硅晶片1上的氧化膜4,如图4所示。具体实施时,所述氧化后退火工艺的温度范围700℃-1700℃,所使用的气体包括o2、ar、h2、n2、no、n2o或pocl3。
36.为了满足功率半导体器件的耐压需要,所述氧化膜4的厚度为30nm~70nm,氧化膜4的具体厚度可以根据实际需要选择,在确定氧化膜4的厚度后,可以通过上述氧化底膜2以及硅膜层3的厚度控制,并最终得到所需厚度的氧化膜4。
37.在制备得到氧化膜4后,采用本技术领域常用的技术手段制备得到正面元胞结构,正面元胞结构的具体形式可以根据实际需要选择,为本技术领域人员所熟知,此处不再赘述。
38.还包括制备于碳化硅晶片1背面的背面电极结构,利用背面电极结构以及位于碳化硅晶片1正面上的正面元胞结构形成所需的功率半导体器件,其中,功率半导体器件为mosfet器件或igbt器件。
39.本发明实施例中,背面电极结构以及制备背面电极结构的工艺均可以根据实际需要选择,为本技术领域人员所熟知,此处不再赘述。