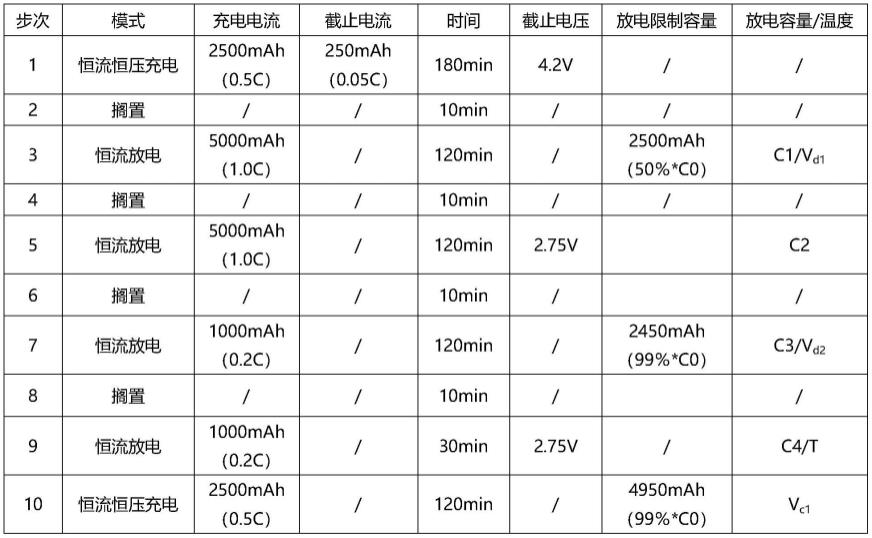
1.本发明专利涉及锂电池的技术领域,具体而言,涉及改善锂电池配组压差的 方法。
背景技术:2.锂电池经常多个配组使用,形成锂电池组,锂电池组在使用过程中,经常出 现由于锂电池组的压差过大产生的软件报警,限制了锂电池组的正常使用或限制 锂电池组功能的有效发挥。
3.目前,导致锂电池组压差报警主要原因有两个,首先,锂电池组中的各个锂 电池的电容量差异较大,因电容量差异较大,导致锂电池组压差报警;其次,锂 电池组中的各个锂电池的电容量差异较小,但是,各个锂电池的充放电曲线不重 合,这样,也会导致多个锂电池之间实际状态存在差异,进而表现为锂电池组压 差报警。
4.现有技术中,主要聚焦是如何提升锂电池组中各个锂电池的电容量测试准确 性,并尽可能减小各个锂电池之间的电容量差值,但是,没有关于锂电池的充放 电曲线差异所引起的锂电池组压差报警相关的研究。
技术实现要素:5.本发明的目的在于提供改善锂电池配组压差的方法,旨在解决现有技术中, 没有通过减小锂电池组中各个锂电池的充放电曲线的差异,解决锂电池组压差报 警的问题。
6.本发明是这样实现的,改善锂电池配组压差的方法,包括以下步骤:
7.1)、将锂电池充电至满电状态,将充电后的锂电池搁置设定时间;
8.2)、设置阶梯式放电容量:将搁置后的锂电池在环境温度为t的条件下进 行大小电流组合的阶梯放电,并测量各个放电阶段的放电容量和各个放电阶段放 电结束后的电压;第1放电阶段的放电容量为c(1),第1放电阶段放电结束 时的放电电压为v
d1
,第2放电阶段的放电容量为c(2),第2放电阶段放电结 束时的放电电压为v
d2
,第n放电阶段的放电容量为c(n),第n放电阶段放 电结束时的放电电压为v
dn
,最后放电阶段,在环境温度为t的条件下以标准放 电电流a的放电容量为c(n+1);
9.3)、设置阶梯式充电容量:对锂电池进行充电,并采集达到充电容量时锂 电池的电压;第1充电阶段达到充电容量时的充电电压为v
c1
,第2充电阶段达 到充电容量时的充电电压为v
c2
,第n充电阶段达到充电容量时的充电电压为 v
cn
;
10.4)、建立锂电池以标准放电电流a的总放电容量c(0)的数学模型为:c (0)=c(1)+c(2)+
……
c(n)+c(n+1)+c(n+1)*(a*t+b),a为环境 温度为t时,对最后放电阶段放电容量c(n+1)的受温度影响系数,b为修正 系数;
11.5)、保证锂电池的设计、材料、结构以及容量测试方法一致,按照所述步 骤2)的放电方式,测试不同环境温度下各放电阶段的总放电容量,通过(c(1) +c(2)+
……
+c(n)+c(n+1)-c(0))/c(n+1)作线性拟合,确定系数a 和系数b的确定值,通过所述数学模型计算批量
生产过程中按标准放电电流a放 电的放电容量;
12.6)、对总放电容量为c0、达到限制放电容量时的放电电压v
dn
以及达到限 制充电容量时的充电电压v
cn
的锂电池进行配组。
13.进一步的,所述步骤2)中的标准放电电流a为0.2c。
14.进一步的,所述步骤2)的第n放电阶段中,放电至所述锂电池的放电电压v
dn
达到2.5v或2.75v时,停止放电。
15.进一步的,所述步骤2)的最后放电阶段中,所述锂电池的放电电压保持为 2.5v或2.75v。
16.进一步的,所述步骤2)的最后放电阶段,放电时间为30分钟。
17.进一步的,所述步骤1)中,所述锂电池的充电电流为0.5c,所述锂电池充 电至充电电压为4.2v时,所述锂电池为满电状态。
18.进一步的,所述锂电池满电状态时,所述锂电池的截止电流为0.05c。
19.进一步的,所述步骤1)中,满电状态的锂电池搁置时间大于10分钟。
20.进一步的,所述参与配组的锂电池单体间的总放电容量c0极差≤50mah。
21.进一步的,所述步骤2)中,第1放电阶段放电结束时的配组锂电池的放电 电压v
d1
极差≤20mv,所述步骤3)中,第1充电阶段达到充电容量时的配组锂 电池的充电电压v
c1
极差≤20mv。
22.与现有技术相比,本发明提供的改善锂电池配组压差的方法,具有以下益处:
23.1)、贴近锂电池配组使用场景,解决了因锂电池充放电过程中,因为充放 电曲线差异或者锂电池电容量差异导致的锂电池组压差报警,大大提高锂电池组 性能及体验;
24.2)、广泛应用于锂电池批量加工生产过程中的检测工序,且不会对生产效 率及生产操作的便捷性产生影响。
具体实施方式
25.为了使本发明的目的、技术方案及优点更加清楚明白,以下结合实施例,对 本发明进行进一步详细说明。应当理解,此处所描述的具体实施例仅仅用以解释 本发明,并不用于限定本发明。
26.以下结合具体实施例对本发明的实现进行详细的描述。
[0027][0028]
改善锂电池配组压差的方法,其特征在于,包括以下步骤:
[0029]
1)、将锂电池充电至满电状态,将充电后的锂电池搁置设定时间;
[0030]
2)、设置阶梯式放电容量:将搁置后的锂电池在环境温度为t的条件下进 行大小电流组合的阶梯放电,并测量各个放电阶段的放电容量和各个放电阶段放 电结束后的电压;
[0031]
第1放电阶段的放电容量为c(1),第1放电阶段放电结束时的放电电压 为v
d1
,第2放电阶段的放电容量为c(2),第2放电阶段放电结束时的放电电 压为v
d2
,第n放电阶段的放电容量为c(n),第n放电阶段放电结束时的放 电电压为v
dn
,最后放电阶段,在环境温度为t的条件下以标准放电电流a的放 电容量为c(n+1);
[0032]
3)、设置阶梯式充电容量:对锂电池进行充电,并采集达到充电容量时锂 电池的
电压;第1充电阶段达到充电容量时的充电电压为v
c1
,第2充电阶段达 到充电容量时的充电电压为v
c2
,第n充电阶段达到充电容量时的充电电压为 v
cn
;
[0033]
4)、建立锂电池以标准放电电流a的总放电容量c(0)的数学模型为:c (0)=c(1)+c(2)+
……
c(n)+c(n+1)+c(n+1)*(a*t+b),a为环境 温度为t时,对最后放电阶段放电容量c(n+1)的受温度影响系数,b为修正 系数;
[0034]
5)、保证锂电池的设计、材料、结构以及容量测试方法一致,按照步骤2) 的放电方式,测试不同环境温度下各放电阶段的总放电容量,通过(c(1)+c (2)+
……
+c(n)+c(n+1)-c(0))/c(n+1)作线性拟合,确定系数a和 系数b的确定值,通过数学模型计算批量生产过程中按标准放电电流a放电的放 电容量;
[0035]
6)、对总放电容量为c0、达到限制放电容量时的放电电压v
dn
以及达到限 制充电容量时的充电电压v
cn
的锂电池进行配组。
[0036]
上述提供的改善锂电池配组压差的方法,具有以下益处:
[0037]
1)、贴近锂电池配组使用场景,解决了因锂电池充放电过程中,因为充放 电曲线差异或者锂电池电容量差异导致的锂电池组压差报警,大大提高锂电池组 性能及体验;
[0038]
2)、广泛应用于锂电池批量加工生产过程中的检测工序,且不会对生产效 率及生产操作的便捷性产生影响。
[0039]
步骤2)中,大小放电电流组合的阶梯放电工艺,以先大电流放电后,按0.2c 小电流放电的两步阶梯放电工艺为最优方法,既能通过大电流放电实现快速放 电,提高生产效率,又能通过小电流放电实现准确测量总锂电池容量,提高测量 的准确性。
[0040]
本实施例中,步骤2)中的标准放电电流a为0.2c。
[0041]
步骤2)的第n放电阶段中,放电至锂电池的放电电压v
dn
达到2.5v或2.75v 时,停止放电。
[0042]
步骤2)的最后放电阶段中,锂电池的放电电压保持为2.5v或2.75v。
[0043]
步骤2)的最后放电阶段,放电时间为30分钟。
[0044]
步骤1)中,锂电池的充电电流为0.5c,锂电池充电至充电电压为4.2v时, 锂电池为满电状态。
[0045]
锂电池满电状态时,锂电池的截止电流为0.05c。
[0046]
步骤1)中,满电状态的锂电池搁置时间大于10分钟。
[0047]
配组锂电池单体间的总放电容量c0极差≤50mah。
[0048]
步骤2)中,第1放电阶段放电结束时的配组锂电池的放电电压v
d1
极差≤ 20mv,步骤3)中,第1充电阶段达到充电容量时的配组锂电池的充电电压为 v
c1
极差≤20mv。
[0049]
步骤2)中,设置阶梯式放电容量时,优选锂电池总容量的40%-60%和90%
ꢀ‑
99%。
[0050]
步骤3)中,设置阶梯式充电容量,优选锂电池总容量的90%-99%。
[0051]
以下提供两个具体实施例
[0052]
实施例一
[0053]
一种26650锂电池,锂电池设计容量5000mah,该锂电池包括正极镍钴锰酸 锂三元材料,负极石墨,六氟磷锂电解液,隔膜、钢壳等关键材料,基本原理是 充电时正极脱锂嵌入负极石墨,放电时,负极石墨脱嵌锂离子回到正极材料,改 善该改善锂电池配组压差的
方法,包括如下步骤:
[0054]
1)、取8pcs锂电池分别在25℃恒温环境中搁置30min,然后按照产品规格 书要求0.5c恒流恒压充电至4.2v,截止电流0.05c;
[0055]
2)、搁置10min后按产品规格书所规定的标准放电电流0.2c放电至2.75v, 放电容量标记为c(0);
[0056]
3)、按照步骤1)将锂电池再次充电至4.2v,搁置10min后先以1.0c放电 至2.75v,放电容量标记为c(1),再以标准放电电流放电至2.75v,容量标记 为c(2);
[0057]
4)、重复步骤1)至3),分别在27℃、29℃、31℃和33℃测试各放电电 流下放电容量c(0)、c(1)和c(2)及达到放电容量时的放电电压;
[0058]
5)、用(c(1)+c(2)-c(0))/c(2)~t作拟合分析,该型号锂电池 容量测试数学转化模型为:c(0)=c(1)+c(2)-c(2)*(0.1440*t-3.464), 23℃≤t≤33℃;
[0059]
6)、锂电池批量生产按下表1所述的充放电工步完成测试,采集1.0c放电 电流放电至设计容量的50%(2500mah,标记为c(1))时放电电压(标记为 v
d1
),继续1.0c放电电流放电至2.75v时测量该步放电容量(标记为c(2)), 然后按0.2c放电至设计容量的99%(4950mah,标记为c(3))时放电电压(标 记为v
d2
),继续按0.2c放电至2.75v,测量该步放电容量和温度(标记为c(4) 和t),搁置10min后按2500mah充电电流恒流恒压充电至设计容量的99% (4950mah)时测量充电电压(标记为v
c1
)。该型号锂电池满电4.2v按0.2c 放电至2.75v容量c(0)=c(1)+c(2)+c(3)+c(4)-(c(3)+c(4))* (0.1440*t-3.464),23℃≤t≤33℃。
[0060]
7)、对锂电池进行配组放电容量c(0)极差≤50mah,放电平台电压差 v
d1
≤10mv,放电末端电压差v
d2
≤10mv,充电末端电压差v
c1
≤10mv,配组后 锂电池组在充电末端、放电平台及放电末端的压差显著改善。
[0061]
表1 26650批量测试充放电工步
[0062][0063]
实施例二
[0064]
一种18650锂电池,设计容量3350mah,该锂电池包括正极镍钴铝材料,负 极石墨,六氟磷锂电解液,隔膜、钢壳等关键材料,基本原理是充电时正极脱锂 嵌入负极石墨,放电时负极石墨脱嵌锂离子回到正极材料。
[0065]
改善该改善锂电池配组压差的方法,包括如下步骤:
[0066]
1)、取8pcs锂电池分别在25℃恒温环境中搁置30min,然后按照产品规格 书要求0.5c恒流恒压充电至4.2v,截止电流0.05c;
[0067]
2)、搁置10min后按产品规格书所规定的标准放电电流0.2c放电至2.5v, 放电容量标记为c(0);
[0068]
3)、按步骤1)所述方法将锂电池再次充电至4.2v,搁置10min后先以1.0c 放电至2.5v,放电容量标记为c(1),再以标准放电电流放电至2.5v,容量标 记为c(2);
[0069]
4)、重复步骤1)至3)分别在27℃、29℃、31℃和33℃测试各放电电流 下放电容量c(0)、c(1)和c(2);
[0070]
5)、用(c(1)+c(2)-c(0))/c(2)~t作拟合分析,该型号锂电池 容量测试数学转化模型为:c(0)=c(1)+c(2)-c(2)*(0.06475*t-1.659), 23℃≤t≤33℃;
[0071]
6)、锂电池批量生产容量测试按下表2所述的工步充放电,采集1.0c放电 电流放电至设计容量的50%(1675mah,标记为c(1))时放电电压(标记为 v
d1
),继续1.0c放电电流放电至2.5v时测量该步放电容量(标记为c(2)), 然后按0.2c放电至设计容量的99%(3316mah,标记为c(3))时放电电压(标 记为v
d2
),继续按0.2c放电至2.5v,测量该步放电容量和温度(标记为c(4) 和t),搁置10min后按1675mah充电电流恒流恒压充电至设计容量的99% (3316mah)时测量充电电压(标记为v
c1
),该型号锂电池满电4.2v按0.2c 放电至2.5v容量c(0)=c(1)+c(2)+c(3)+c(4)-(c(3)+c(4))* (0.06475*t-1.659),23℃≤t≤33℃。
[0072]
表1 26650批量测试充放电工步
[0073][0074]
以上所述仅为本发明的较佳实施例而已,并不用以限制本发明,凡在本发明 的精神和原则之内所作的任何修改、等同替换和改进等,均应包含在本发明的保 护范围之内。