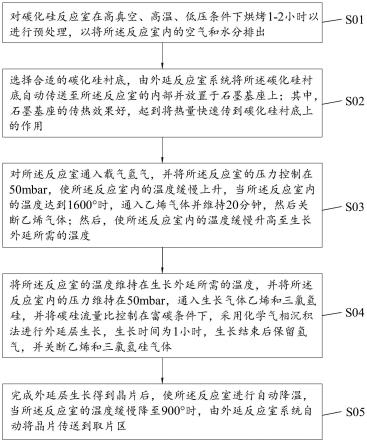
1.本发明涉及半导体技术领域,尤其涉及一种有效降低碳化硅外延背景掺杂浓度的方法。
背景技术:2.碳化硅(sic)作为宽禁带半导体材料,具有高的临界击穿电场、高热导率以及电子饱和迁移速率高等特点,这些独特的优势使其能够应用在大功率、高温、高压、抗辐射等应用领域。
3.碳化硅(sic)电力电子器件研制需要特定掺杂浓度及厚度的单层或者多层碳化硅外延材料,目前sic外延材料主要采用化学气相沉积法制备。其中,碳化硅外延背景掺杂是碳化硅外延工艺中的关键参数,因为它的高低决定了外延层的掺杂浓度范围、电阻率、热导率等,并且对器件的击穿电压具有影响。背景掺杂杂质的来源主要是反应炉内壁及炉内石墨配件表面吸附的氧气、水分子和氮气。在外延工艺过程中,反应炉内壁所吸附的气体会缓慢释放进入到反应腔中,影响背景掺杂浓度的气体主要是氮气。
4.对于高压双极型器件,低掺杂厚外延材料是制造高压sic器件必不可少的材料,同时要求其载流子浓度足够低。例如,为了制造20kv的sic双极型器件,要求外延膜厚度应当大于200um,载流子浓度要接近1
×
10
14
/cm3;这就同时需要碳化硅外延背景掺杂浓度要足够低,低背景掺杂浓度外延材料能大大降低高压器件的反向偏置电场,如果背景掺杂浓度偏高,外延材料就不能获得低的载流子浓度。
5.然而,目前碳化硅外延背景掺杂浓度普遍在5
×
10
13
/cm3~1
×
10
14
/cm3之间,但超高压器件材料需要更低的背景掺杂浓度,现有方式无法获得更低的背景掺杂浓度,不能满足超高压器件的制备要求。
6.因此,有必要提供一种能够有效降低碳化硅外延背景掺杂浓度的方法,以解决上述问题。
技术实现要素:7.本发明的目的在于提供一种能够有效降低碳化硅外延背景掺杂浓度的方法。
8.为实现上述目的,本发明的技术方案为:提供一种降低碳化硅外延背景掺杂浓度的方法,其包括如下步骤:
9.(1)对碳化硅反应室在高真空、高温、低压条件下烘烤1-2小时以进行预处理,以将所述反应室内的空气和水分排出;
10.(2)选择合适的碳化硅衬底,由外延反应室系统的机械手装置将所述碳化硅衬底自动传送至所述反应室的内部并放置于石墨基座上;其中,石墨基座的传热效果好,起到将热量快速传到碳化硅衬底上的作用;
11.(3)对所述反应室通入载气氢气,并将所述反应室的压力控制在50mbar,使所述反应室内的温度缓慢上升,当所述反应室内的温度达到1600
°
时,通入乙烯气体并维持20分
钟,然后关断乙烯气体;然后,使所述反应室内的温度缓慢升高至生长外延所需的温度;具体地,在该升温步骤通入乙烯气体,主要是用于在生长外延前来调节反应室的氛围,乙烯气体在高温下分解成碳原子,使反应室处在偏碳的氛围下,不利于杂质气体掺杂到外延层上;
12.(4)将所述反应室的温度维持在生长外延所需的温度,并将所述反应室内的压力维持在50mbar,通入生长气体乙烯和三氯氢硅,并将碳硅流量比控制在富碳条件下,采用化学气相沉积法进行外延层生长,生长时间为1小时,生长结束后保留氢气,并关断乙烯和三氯氢硅气体;其中,将碳硅流量比控制在富碳条件下,能起到降低掺杂效率作用;
13.(5)完成外延层生长得到晶片后,使所述反应室进行自动降温,当所述反应室的温度缓慢降至900
°
时,由外延反应室系统的机械手装置自动将晶片传送到取片区。
14.较佳地,在本发明之降低碳化硅外延背景掺杂浓度的方法的一种实施方式中,所述步骤(1)具体包括:
15.(11)将所述反应室的温度升到1200
°
~1600
°
之间,同时通入100升的氢气,并将所述反应室的压力控制在100mbar~200mbar之间,维持所述温度及压力状态30分钟;具体地,氢气起到传热的作用,该步骤通过升温并通入氢气(h2),将反应室内的空气和水分排走;
16.(12)将所述反应室的温度降到1100
°
左右,然后关闭氢气,利用外延反应室系统的机械真空泵将所述反应室内的压力抽至1mbar~5mbar之间;
17.(13)启用外延反应室系统的分子泵进一步将所述反应室内的压力抽至2
×
10-5
mbar~5
×
10-5
mbar之间,并维持该压力状态1~2小时;
18.(14)将所述反应室的温度缓慢降到900
°
,同时通入30升的氢气,使残留在所述反应室的石墨配件内的空气、氮气、水分被释放出,然后将所述反应室内的气体抽走;使反应室达到更高的洁净度。
19.在本发明之降低碳化硅外延背景掺杂浓度的方法的一种实施方式中,所述步骤(2)中选择6英寸偏向《11-20》方向4
°
的n型碳化硅衬底。
20.在本发明之降低碳化硅外延背景掺杂浓度的方法的一种实施方式中,所述步骤(3)中通入氢气的流量为150l/min,通入乙烯气体的流量为7-15ccm/min,并且生长外延所需的温度为1680
°
。
21.在本发明之降低碳化硅外延背景掺杂浓度的方法的一种实施方式中,所述步骤(4)中以180-250ccm/min的流量通入乙烯气体,以450-560ccm/min的流量通入三氯氢硅气体,并且碳硅流量比控制在1.4-1.6之间,这样的流量比例使得反应室内处于富碳条件,富碳条件起到两个方面的作用:一是降低掺杂效率,二是加快生长速率,在本发明中,外延层的生长速率可以达到100微米每小时,相较于现有的生长速率普遍在60微米每小时以下的情况,本发明较高的生长速率也起到降低掺杂效率的作用。
22.与现有技术相比,由于本发明的降低碳化硅外延背景掺杂浓度的方法,首先对碳化硅反应室进行预处理,在高真空、高温、低压条件下对反应室烘烤1-2小时,以将反应室的空气、水分等都排走,有效提高反应室的洁净度;其次,在生长外延层之前通入乙烯(c2h4)一种气体来调节反应室的氛围,使反应室内部处在偏碳的环境下,因此不利于杂质气体掺杂到外延层上;最后,采用化学气相沉积法在高温、低压环境下生长外延层,其中,采用乙烯(c2h4)气体作为碳源,三氯氢硅(sihcl3)气体作为硅源,通过控制较高的碳硅流量比而使反应室内部处在富碳条件下,以此在生长过程中加快生长速率,从而降低背景掺杂浓度,同
时富碳条件也能起到降低掺杂效率的作用。
附图说明
23.图1是本发明之降低碳化硅外延背景掺杂浓度的方法的流程图。
24.图2是图1中步骤s01的子流程图。
25.图3是通过本发明之降低碳化硅外延背景掺杂浓度的方法进行外延生长后测得的背景掺杂浓度图。
26.图4是现有方法进行外延生长后测得的背景掺杂浓度图。
具体实施方式
27.现在参考附图描述本发明的实施例,附图中类似的元件标号代表类似的元件。需说明的是,本发明所涉及到的方位描述,例如上、下、左、右、前、后等指示的方位或位置关系均为基于附图所示的方位或位置关系,仅是为了便于描述本技术的技术方案或/和简化描述,而不是指示或暗示所指的装置或元件必须具有特定的方位、以特定的方位构造和操作,因此不能理解为对本技术的限制。所描述到的第一、第二等只是用于区分技术特征,不能理解为指示或暗示相对重要性或者隐含指明所指示的技术特征的数量或者隐含指明所指示的技术特征的先后关系。
28.本发明所提供的降低碳化硅外延背景掺杂浓度的方法,适用于外延反应室系统以生长外延层。其中,外延反应室系统主要由进气装置、抽气装置、反应室、冷却腔体、机械手装置等几个部分组成,其中,反应室内设有石墨基座,机械手装置负责将衬底传送到反应室内的石墨基座上以及将外延生长得到的晶片传送到取片区。本发明所涉及到的外延反应室系统的以上各个部分的结构、工作原理等均为本领域的常规方式,因此不再详细说明。
29.下面先参看图1所示,本发明所提供的降低碳化硅外延背景掺杂浓度的方法,具体包括如下步骤:
30.s01、对碳化硅反应室在高真空、高温、低压条件下烘烤1-2小时以进行预处理,以将所述反应室内的空气和水分排出;
31.在本发明的方法中,特意增加对反应室进行预处理的步骤,目的是将反应室内的空气和水分充分排走,进而有效提高反应室的洁净度。
32.s02、选择合适的碳化硅衬底,由外延反应室系统的机械手装置将所述碳化硅衬底自动传送至所述反应室的内部并放置于石墨基座上;其中,石墨基座的传热效果好,起到将热量快速传到碳化硅衬底上的作用;
33.在本发明中的一种优选实施方式中,选择6英寸偏向《11-20》方向4
°
的n型碳化硅衬底。在sic外延生长中,为了保证外延材料能够有效的继承衬底的堆垛序列,保证晶体质量,目前大多采用沿c轴方向偏《11-20》方向切割的衬底,衬底偏角切割的意义在于在衬底表面引入原子级别的台阶,在外延过程中,吸附的原子倾向于在台阶处成核生长,确保外延过程按台阶流(step-flow)的模式进行。目前常用的sic衬底的偏角主要有4
°
和8
°
两种,4
°
偏角和8
°
偏角sic衬底表面的台阶密度不同,氢气对衬底的刻蚀速率及台面上方的硅蒸气平衡分压有所不同,因此需要采用的在线刻蚀工艺有所不同。可理解地,本发明并不限于上述碳化硅衬底,当然可根据生产需要选择其他类型的碳化硅衬底。
34.s03、对所述反应室通入载气氢气,并将所述反应室的压力控制在50mbar,使所述反应室内的温度缓慢上升,当所述反应室内的温度达到1600
°
时,通入乙烯气体并维持20分钟,然后关断乙烯气体;然后,使所述反应室内的温度缓慢升高至生长外延所需的温度;
35.具体地,该步骤为反应室的升温阶段,其中通入氢气(h2)的流量优选为150l/min,通入乙烯(c2h4)气体的流量优选为7-15ccm/min,当然,并不限于前述流量,可根据需要灵活调整氢气(h2)、乙烯(c2h4)气体的流量。当通入乙烯(c2h4)气体后,乙烯(c2h4)气体在高温下分解成碳原子,使反应室处在偏碳的氛围下,主要目的是用于在生长外延前来调节反应室的氛围,偏碳的氛围不利于杂质气体掺杂到外延层上;
36.在本发明中的一种优选实施方式中,本步骤中所述的生长外延所需的温度为1680
°
,可理解地,并不限于该温度,当然可根据需要设置适合的生长温度。
37.s04、将所述反应室的温度维持在生长外延所需的温度,并将所述反应室内的压力维持在50mbar,通入生长气体乙烯和三氯氢硅,并将碳硅流量比控制在富碳条件下,采用化学气相沉积法进行外延层生长,生长时间为1小时,生长结束后保留氢气,并关断乙烯和三氯氢硅气体;
38.在本发明中的一种优选实施方式中,将反应室的温度维持在1680
°
,压力维持在50mbar,然后以180-250ccm/min的流量通入生长气体乙烯(c2h4)以及以450-560ccm/min的流量通入三氯氢硅(sihcl3),当然,乙烯(c2h4)气体以及三氯氢硅(sihcl3)气体的流量可根据需要进行调节。另外,本发明中将碳硅流量比优选控制在1.4-1.6之间,使反应室内处于富碳条件,相较于现有的碳硅流量比在1.0-1.2之间的方式,本发明较高的碳硅流量比所创造的富碳条件起到两个方面的作用:一是降低掺杂效率,二是加快生长速率,在本发明中,外延层的生长速率可以达到100微米每小时,相较于现有的生长速率普遍在60微米每小时以下的情况,本发明较高的生长速率同时也起到降低掺杂效率的作用。
39.s05、完成外延层生长得到晶片后,使所述反应室进行自动降温,当所述反应室的温度缓慢降至900
°
时,由外延反应室系统的机械手装置自动将晶片传送到取片区。
40.下面结合图1-2所示,在本发明之降低碳化硅外延背景掺杂浓度的方法的一种实施方式中,所述步骤s01具体包括如下步骤:
41.s11、将所述反应室的温度升到1200
°
~1600
°
之间,同时通入100升的氢气,并将所述反应室的压力控制在100mbar~200mbar之间,维持所述温度及压力状态30分钟;
42.具体地,由于氢气(h2)起到传热的作用,本步骤通过升温并通入氢气(h2),并在高温、高压力之下维持一定时长,从而初步的将反应室内的空气和水分排走。
43.s12、将所述反应室的温度降到1100
°
左右,然后关闭氢气,利用外延反应室系统的机械真空泵将所述反应室内的压力抽至1mbar~5mbar之间;
44.本步骤的目的是将反应室内的空气、水分等抽出,同时降低反应室内的压力,在本步骤中所涉及到的外延反应室系统的机械真空泵为外延反应室系统的抽气装置的一部分,其结构及原理均为本领域的常规方式,在此不再详细说明。
45.s13、启用外延反应室系统的分子泵进一步将所述反应室内的压力抽至2
×
10-5
mbar~5
×
10-5
mbar之间,并维持该压力状态1~2小时;
46.本步骤的目的是使反应室内达到更低的压力,并且,本步骤中所涉及到的外延反应室系统的分子泵也是外延反应室系统的抽气装置的一部分,其结构及原理均为本领域的
常规方式,在此不再详细说明。
47.s14、将所述反应室的温度缓慢降到900
°
,同时通入30升的氢气,使残留在所述反应室的石墨配件内的空气、氮气、水分被释放出,然后将所述反应室内的气体抽走。
48.更具体地,由于气体在高温、低压下会膨胀,因此通过上述步骤s12-s13将反应室内的压力降低后,在本步骤中通入氢气(h2),氢气(h2)膨胀使残留在反应室内的石墨配件里面的空气、氮气和水分释放出来,再通过抽气方式将反应室内的气体抽走,从而进一步的将反应室内的杂质气体、水分等排走,使反应室内部达到更高的洁净度。
49.下面结合图1-4所示,利用本发明之降低碳化硅外延背景掺杂浓度的方法生长外延层,背景掺杂浓度可以达到2
×
10
13
/cm3以下。具体参看图3所示,对利用本发明的方法在生长外延层后的背景掺杂浓度进行检测,得到的背景掺杂浓度为1.4155
×
10
13
/cm3。相应地,对采用现有方式生长外延层的背景掺杂浓度进行检测,得到的背景掺杂浓度为6.851
×
10
13
/cm3,具体参看图4所示。由以上对比可得知,本发明的方法确实可有效降低背景掺杂浓度。
50.综上所述,由于本发明的降低碳化硅外延背景掺杂浓度的方法,首先对碳化硅反应室进行预处理,在高真空、高温、低压条件下对反应室烘烤1-2小时,以将反应室的空气、水分等都排走,有效提高反应室的洁净度;其次,在生长外延层之前通入乙烯(c2h4)一种气体来调节反应室的氛围,使反应室内部处在偏碳的环境下,因此不利于杂质气体掺杂到外延层上;最后,采用化学气相沉积法在高温、低压环境下生长外延层,其中,采用乙烯(c2h4)气体作为碳源,三氯氢硅(sihcl3)气体作为硅源,通过控制较高的碳硅流量比而使反应室内部处在富碳条件下,从而在生长过程中加快生长速率,以此降低背景掺杂浓度,同时富碳条件也能起到降低掺杂效率的作用。因此,本发明通过生长外延前对反应室的预处理以及生长中提高碳硅流量比,从而达到加快生长速率以及降低背景掺杂浓度的目的。
51.至此,以说明和描述的目的提供上述实施例的描述,不意指穷举或者限制本公开。特定的实施例的单独元件或者特征通常不受到特定的实施例的限制,但是在适用时,即使没有具体地示出或者描述,其可以互换和用于选定的实施例。在许多方面,相同的元件或者特征也可以改变,这种变化不被认为是偏离本技术,并且所有的这种修改意指为包括在本技术的范围内。
52.提供示例实施例,从而使本技术变得透彻,并且将会完全地将该范围传达至本领域内技术人员。为了透彻理解本技术的实施例,阐明了众多细节,诸如特定零件、装置和方法的示例,显然,对于本领域内技术人员,不需要使用特定的细节,示例实施例可以以许多不同的形式实施,而且两者都不应当解释为限制本技术的范围,在某些示例实施例中,不对公知的工序、公知的装置结构和公知的技术进行详细地描述。
53.以上所揭露的仅为本发明的优选实施例而已,当然不能以此来限定本发明之权利范围,因此依本发明申请专利范围所作的等同变化,仍属本发明所涵盖的范围。