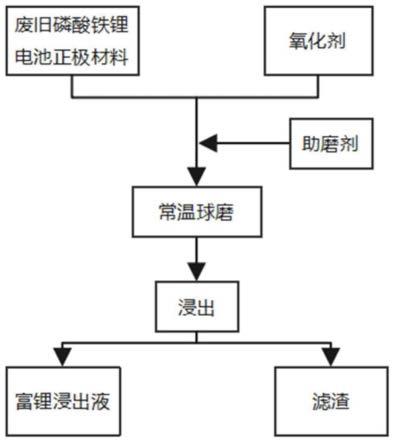
1.本发明涉及锂回收方法领域,具体是一种机械法无酸高选择性从磷酸铁锂正极材料中回收锂的方法。
背景技术:2.磷酸铁锂 (lifepo4,lfp) 于20世纪80年代上首次报道,被认为是用于电动汽车,混合动力电动汽车和大型储能设施的优良正极材料。磷酸铁锂具有低毒性以及原料广泛丰富的优点。当磷酸铁锂应用于电池时,这些设备显示出卓越的热安全性和较长的循环寿命。
3.现如今新能源汽车战略新兴支柱产业。锂电池是新能源汽车的核心部件。近年来,随着电动汽车在国内大型城市的推广使用,锂离子动力电池也在快速发展。锂离子动力电池的寿命是一般为4~5年,因此我们可以预见早期的新能源汽车锂离子动力电池的集中报废期已经到来。锂离子电池被普遍认为是环保无污染的绿色电池,但锂离子电池的回收不当同样会产生污染。大量的锂离子电池报废会带来环境污染和资源浪费问题。据报道,未来的锂供应危机只能通过100% 锂离子电池回收和至少90%的锂回收率来预防。因此,废磷酸铁锂电池的回收是防止环境污染和资源枯竭的必要条件。因此对报废的动力电池电极材料进行无害化处理以及资源化利用,具有十分重要的意义。
4.废旧磷酸铁锂电池的回收难点在于其提取效率相对较低,回收选择性较低,易产生二次废物。现有的技术通过强酸处理和较长的萃取时间可以实现锂和铁的有效萃取。但是橄榄石结构的磷酸铁锂相当稳定,锂和铁的有效提取必须依靠大量的强酸或者强碱。在这种情况下,二次污染是不可避免的,需要处理过多的酸或碱,这种方法会显著增加工艺成本。而将废旧磷酸铁锂电池正极材料采用机械力化学活化后,活化能降低,反应活性增加,这有望有助于缓解废旧磷酸锂电池回收过程中的上述问题。使用机械法进行活化可以减少酸的消耗,提高锂的回收选择性并减少二次污染的排放。
5.申请号为cn201810014024.0的专利公布了一种从磷酸铁锂正极材料中回收锂的方法及碳酸锂产品,主要流程是采用质量分数为15%~65%的浓硝酸与原料混合,并将混合料液导入水热反应釜中进行水热反应,经过调整ph值,除杂过滤等一系列操作得到碳酸锂产品。此法实验步骤较繁琐,并且使用了反应釜进行水热反应,具有一定的危险性。同时水热反应时需要较高温度,增加了回收成本,对反应设备要求高。
6.申请号为cn202010760821.0的专利公布了一种利用废旧磷酸铁锂正极材料综合利用的方法,该方法将废旧磷酸铁锂正极材料采用酸液浸出,浸出液经过调节铁磷比以及调节ph值至强酸性后,通过氧化反应使亚铁离子转化成铁离子,生成磷酸铁沉淀,液固分离后得到水合磷酸铁和含锂溶液。然后后续通过一系列操作得到锂盐产品。该法虽然工艺简单,但是反应时间较长,过程中引入了重金属沉淀剂,可能引入杂质离子。并且其中利用了高酸度等反应条件,容易造成环境污染。
技术实现要素:7.本发明的目的是提供一种机械法无酸高选择性从磷酸铁锂正极材料中回收锂的方法,以解决现有技术采用酸液浸出和化学反应从磷酸铁锂正极材料中回收锂时存在环境污染的问题。
8.为了达到上述目的,本发明所采用的技术方案为:机械法无酸高选择性从磷酸铁锂正极材料中回收锂的方法,包括以下步骤:步骤1、取用磷酸铁锂正极材料、共磨剂、助磨剂,其中共磨剂采用氧化剂,将磷酸铁锂正极材料、共磨剂、助磨剂三者混合形成混合物;步骤2、将步骤1中的混合物于常温下进行球磨粉碎,得到粉碎产物;步骤3、将步骤2得到的粉碎产物进行水浸浸出,得到浸出液;步骤4、对步骤3得到的浸出液进行过滤,得到的滤液为得到的滤液为含锂溶液。
9.进一步的步骤1中,取用的磷酸铁锂正极材料与共磨剂的质量比为1:1~1:10。
10.进一步的步骤1中,助磨剂采用过氧化氢。
11.进一步的,作为助磨剂的过氧化氢的质量分数为5%~30%,过氧化氢与磷酸铁锂正极材料的液固比为0ml/g~10ml/g。
12.进一步的步骤1中,共磨剂采用的氧化剂为过硫酸钠、过硫酸铵、过硫酸钾、过氧化钠中的任意一种或任意比例的几种。
13.进一步的步骤2中,球磨时间为0min~120min,球粉比为5g/g ~50g/g,球磨的转速为100rpm~700rpm。
14.进一步的步骤3中,向粉碎产物中加入去离子水进行水浸浸出,粉碎产物与去离子水的固液比为10g/l~100 g/l,浸出时于10℃~90℃、0rpm~500rpm的搅拌速度下浸出0min~120min。
15.本发明步骤4过滤后所得富锂滤液中,li
+
的浸出率在90%以上,fe
2+
/fe3的浸出率在5%以下。
16.本发明将电池废旧的磷酸铁锂正极材料与氧化剂进行机械球磨后使用去离子水浸出处理,通过球磨法可在常温常压下利用机械能作为反应驱动力,破坏磷酸铁锂的橄榄石结构,由此能够在后续步骤中直接以水浸浸出方式得到含锂液,此方法中无酸消耗,锂元素的选择性高,并且操作简单,可控性强。
17.与现有技术相比,本发明的优点为:1、本发明提出的一种机械法无酸高选择性回收废旧锂电池磷酸铁锂正极材料的方法具有酸碱用量为零、方法简单、技术路线合理、制得生产过程对环境无污染,是一种从废锂离子电池中选择性提取和回收有价值金属的有前途的方法,符合绿色化学的概念。
18.2、采用本发明方法,从废旧磷酸铁锂电池正极材料中选择性提取li+的浸出率在90%以上,fe2+/fe3+的浸出率在5%以下。其他有价金属浸出率较低,实现了锂的高选择性提取。
附图说明
19.图1是本发明方法流程框图。
20.图2是本发明实施例中含锂滤液测定结果图。
具体实施方式
21.下面结合附图和实施例对本发明进一步说明。
22.实施例1如图1所示,本实施例包括以下步骤:(1)称取1g废旧磷酸铁锂正极材料和1g作为共磨剂的过硫酸钠,将它们放入100ml的球磨罐中,并向球磨罐中加入1ml质量分数为30%的过氧化氢作为助磨剂。
23.(2)将步骤(1)中的球磨罐于常温下置于行星球磨机中球磨5min,控制行星球磨机的转速为500rpm,球粉比为20g/g。
24.(3)将球磨后的混合物置于250ml的锥形瓶中,并按固液比为30g/l向锥形瓶中加入去离子水,然后于40℃下水浸浸出20min,浸出过程以300rpm的搅拌速度进行搅拌。
25.(4)步骤(3)浸出结束后,将浸出液进行过滤,得到富含锂、铁元素的滤液。后续对滤液进行原子吸收测试。
26.如图2所示,本实施例测定步骤4的滤液中,li
+
的浸出率为98.3%,fe
2+
/fe
3+
的浸出率为2.5%。
27.实施例2本实施例包括以下步骤:(1)称取1g废旧磷酸铁锂正极材料和1g作为共磨剂的过硫酸钠,将它们放入100ml的球磨罐中,并向球磨罐中加入2ml质量分数为30%的过氧化氢的过氧化氢作为助磨剂。
28.(2)将步骤(1)中的球磨罐于常温下置于行星球磨机中进行球磨5min,控制行星球磨机的转速为500rpm,球粉比为20g/g。
29.(3)将球磨后的混合物置于250ml的锥形瓶中,并按固液比为30g/l向锥形瓶中加入去离子水,然后于40℃下浸出20min,浸出过程中以300rpm的搅拌速度(请补充)进行搅拌。
30.(4)步骤(3)浸出结束后,将浸出液进行过滤,得到富含锂、铁元素的滤液。后续对滤液进行原子吸收测试。
31.如图2所示,本实施例测定步骤4的滤液中, li
+
的浸出率为99.3%,fe
2+
/fe
3+
的浸出率为1.5%。
32.实施例3本实施例包括以下步骤:(1)称取1.5g废旧磷酸铁锂电池正极材料和1g作为共磨剂的过硫酸钠,将它们放入100ml的球磨罐中,并向球磨罐中加入1ml质量分数为30%的过氧化氢的过氧化氢作为助磨剂。
33.(2)将步骤(1)中的球磨罐于常温下置于行星球磨机中进行球磨5min,控制行星球磨机的转速为500rpm,球粉比为20g/g。
34.(3)将球磨后的混合物置于250ml的锥形瓶中,并按固液比为30g/l向锥形瓶中加入去离子水,然后于25℃下浸出20min,浸出过程中以300rpm的搅拌速度进行搅拌。
35.(4)步骤(3)浸出结束后,将浸出液进行过滤,得到富含锂、铁元素的滤液。后续对滤液进行原子吸收测试。
36.如图2所示,本实施例测定步骤4的滤液中, li
+
的浸出率为93.3%,fe
2+
/fe
3+
的浸出
率为2.7%。
37.实施例4本实例包括以下步骤:(1)称取1g废旧磷酸铁锂电池正极材料和1g作为共磨剂的过硫酸钠,将它们放入100ml的球磨罐中,并向球磨罐中加入1ml质量分数为30%的过氧化氢的过氧化氢作为助磨剂。
38.(2)将步骤(1)中的球磨罐于常温下置于行星球磨机中进行球磨5min,控制行星球磨机的转速为500rpm,球粉比为20g/g。
39.(3)将球磨后的混合物置于250ml的锥形瓶中,并按固液比为30g/l向锥形瓶中加入去离子水,然后于60℃下浸出20min,浸出过程中以300rpm的搅拌速度进行搅拌。
40.(4)步骤(3)浸出结束后,将浸出液进行过滤,得到富含锂、铁元素的滤液。后续对滤液进行原子吸收测试。
41.如图2所示,本实施例测定步骤4的滤液中, li
+
的浸出率为90%,fe
2+
/fe
3+
的浸出率为2.5%。
42.本发明所述的实施例仅仅是对本发明的优选实施方式进行的描述,并非对本发明构思和范围进行限定,在不脱离本发明设计思想的前提下,本领域中工程技术人员对本发明的技术方案作出的各种变型和改进,均应落入本发明的保护范围,本发明请求保护的技术内容,已经全部记载在权利要求书中。