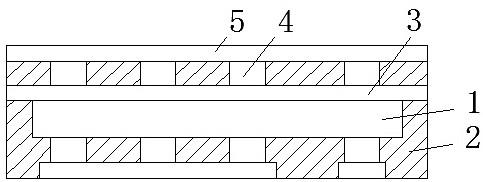
1.本发明属于半导体封装技术领域,尤其涉及一种散发芯片内部热量结构稳定的芯片散热结构、工艺及半导体器件。
背景技术:2.晶圆一般采用封装的方式进行包裹形成封装体,进而形成芯片,大功率半导体器件是其中的一种,塑封为封装中较常见的一种方式,目前比较常用的塑封材料为环氧树脂塑封料,功率半导体器件在工作的时候会产生越来越多的热量,为了保证其正常工作,需要维持芯片的结温在正常的范围以内,即需要对芯片进行散热。
3.芯片的散热方向为:热源即硅片向外部环境散热,此过程中包含硅片到外封装的热阻jc,芯片外封装到散热片的热阻cs,散热片到环境的热阻sa,因此从硅片到环境的总热阻称为ja,因此满足:ja=jc+cs+sa。
4.目前常见的半导体芯片散热方式,是在芯片的输出管脚处连接焊盘,焊盘用于散热,为了加强散热效果,会进一步形成底部散热片,构成双面散热,底部散热片的结构主要有两种:一种是底部散热片直接和芯片连接,这种连接的风险在于金属散热片的热膨胀系数和半导体芯片材料硅的热膨胀系数相差比较大,在高低温冲击下产生很大的应力导致芯片损坏,使得器件失效;第二种方式是在芯片的背面先做一层高分子材料(如环氧树脂塑封料,然后在高分子材料上制作底部散热片,也可继续在侧面形成散热片,这种结构可以避免高低温热应力对芯片的冲击,但由于高分子材料的热导率偏低,从而形成热阻,ja值较高,散热效率较低。
技术实现要素:5.为解决上述现有技术中的问题,本发明提供了一种可缓冲热应力、散热效果更好的芯片散热结构、工艺及半导体器件。
6.封装体制作过程中,为了满足散热需要,在芯片的背面直接形成底部散热片如图1a,图1b是在图1a的基础上在芯片的侧面形成侧面散热板,整体构成多面金属板散热,如五面金属板散热,芯片硅的热膨胀系数是2.5,测定温度条件为26.85℃,本技术中底部散热片和中部导热层、导热凸起的材料主要是金属铜,且本领域散热片也常用铜材料,铜的热膨胀系数为17.5,测定温度条件为20℃,膨胀系数是表征物体热膨胀性质的物理量,即表征物体受热时其长度、面积、体积增大程度的物理量,热膨胀系数越低,说明在受热的状况下,自身体积膨胀变化小,热膨胀系数越大,热应力越大,热应力又称变温应力,即物体单位面积上所承受的力越大,芯片硅和金属铜的热膨胀系数相差较大,散热片铜料和硅直接连接,高温时铜单位面积上承受的力较大挤压硅片,使得芯片损坏,器件失效。
7.如果在芯片的背面先做一层高分子材料,如环氧树脂塑封料,即本领域常见的emc塑封料,内应力低且热导率也相应的低,然后在高分子材料上制作底部散热片,如图2a,图2b是在图2a的基础上在塑封料的侧面形成侧面散热板,整体构成多面金属板散热,如五面
金属板散热,但是环氧树脂的导热系数为0.2~2.2 w/mk,铜的导热系数为429
ꢁ
w/mk,硅的导热系数为611
ꢁ
w/mk,其中“w”指热功率单位,“m”代表长度单位米,而“k”为绝对温度单位,虽然中间的环氧树脂料缓冲内应力,保护硅,但是铜的导热系数远远大于环氧树脂塑封料,故环氧树脂塑封料处的热阻很大,散热片铜难以将芯片硅的热量散发,散热效果极差。
8.为实现上述目的,本发明的一种芯片散热结构,包括至少一芯片及封装层,所述封装层包封所述芯片,所述芯片的一侧电性连接有焊盘和输出管脚,所述输出管脚穿过所述封装层与所述芯片电性连接,所述封装层远离芯片焊盘的一侧整个表面设置有底部散热片,所述封装层的内部设置有用以对封装层内部结构产生的变温应力进行缓冲且传导内部热量的中部结构。
9.进一步,所述中部结构包括中部导热层和至少一导热凸起,所述中部结构将晶片与底部散热片连接;所述晶片将封装层分割为对称的上下两层,且上层封装层包封的多个导热凸起和下层封装层包封的晶片植球结构对称。
10.进一步,所述中部导热层设置在晶片背面和此背面对应的封装层的外表面,所述中部导热层的材料为金属铜、钨、镍或钽。
11.进一步,每个所述导热凸起设置在中部导热层远离晶片的一侧,每个所述导热凸起的形状为规则圆柱形或长方体形,且倾斜或竖直的设置在中部导热层的表面。
12.进一步,每个所述导热凸起远离中部导热层的一端与底部散热片连接。
13.进一步,所述中部导热层、导热凸起和底部散热片所形成的方式为电镀或溅射。
14.进一步,所述封装层的一个侧壁、两个侧壁、三个侧壁或者四个侧壁上均设置有侧壁散热片,所述侧壁散热片分别与底部散热片和中部导热层连接。
15.一种半导体器件,包括上述芯片散热结构。
16.一种芯片散热工艺,包括以下步骤:封装步骤:采用注塑封装方式将中部结构、芯片和芯片的电性连接处焊盘和输出管脚均包封在封装层内;表面处理步骤:在芯片远离焊盘的一侧通过表面处理形成中部导热层;在中部导热层远离芯片的一侧通过表面处理形成至少一个导热凸起;在每个导热凸起暴露于封装层的一端再次表面处理形成底部散热片,表面处理的方式为电镀或者溅射;每个所述导热凸起和中部导热层构成中部结构,所述中部结构将底部散热片和芯片连接起来,缓冲底部散热片的变温应力对芯片的挤压同时保证热量传导;暴露步骤:研磨或钻孔暴露出导热凸起、芯片电性连接处焊盘和输出管脚。
17.进一步,还包括在所述封装层的一个侧壁、两个侧壁、三个侧壁或者四个侧壁上均设置有侧壁散热片,所述侧壁散热片与底部散热片和中部导热层连接。
18.有益效果:1、芯片硅产生的热量通过中部导热层传递给每个导热凸起,通过底部散热片散热,芯片前面的焊盘也可以用于散热,配合底部散热片构成双面散热,整体结构ja值较小,热传导快,散热效果好;2、由于芯片的上下都有高分子材料做保护,且结构交相对对称,能够平衡高低温形成的应力作用,器件可靠性增加,底部散热片的热应力不直接挤压芯片,保护芯片,避免
损坏;3、本技术中部结构的制作成本低,相对于有同样功效的其他结构而言,本技术制作步骤简单,制作效率高,我司生产线工艺完全可以快速制作出,不需要额外增加其他步骤。
附图说明
19.图1a为现有的第一种封装体芯片散热的结构示意图;图1b为在现有的第一种封装体芯片散热上形成侧面散热的结构示意图;图2a为现有的第二种封装体芯片散热的结构示意图;图2b为在现有的第二种封装体芯片散热上形成侧面散热的结构示意图;图3为本发明一种芯片散热工艺的第一实施例的步骤示意图;图4a为本发明一种芯片散热工艺的第一实施例的工艺流程图中的载板示意图;图4b为工艺流程中的晶圆植球步骤示意图;图4c为工艺流程中的晶圆放置步骤示意图;图4d为工艺流程中的将晶圆和植球包封步骤示意图;图4e为工艺流程中的暴露植球步骤示意图;图4f为工艺流程中的形成焊盘和输出管脚步骤示意图;图4g为工艺流程中的将焊盘和输出管脚包封步骤示意图;图4h为工艺流程中的暴露焊盘和输出管脚步骤示意图;图4i为工艺流程中的去除载板步骤示意图;图4j为工艺流程中的形成中部导热层步骤示意图;图4k为工艺流程中的形成导热凸起步骤示意图;图4l为工艺流程中的包封导热凸起步骤示意图;图4m为工艺流程中的暴露导热凸起步骤示意图;图4n为工艺流程中的形成底部散热片步骤示意图;图5为本发明一种芯片散热工艺的第二实施例的步骤示意图;图6为本发明一种芯片散热结构、半导体器件的第一实施例的结构示意图;图7为本发明一种芯片散热结构、半导体器件的第二实施例的结构示意图。
20.图中标记说明:芯片1、封装层2、中部导热层3、导热凸起4、底部散热片5、侧壁散热片6。
具体实施方式
21.为了更好地了解本发明的目的、结构及功能,下面结合附图1-7,对本发明提出的一种芯片散热结构、工艺及半导体器件,做进一步详细的描述。
22.图6显示出本发明改进后的芯片散热结构、半导体器件,与现有的封装体芯片散热结构相同的是,本发明也是在封装体的外侧形成金属板用于散热,金属板通过塑封料间隔,与现有技术不同的是,本发明在塑封料间隔处设置中部结构,中部结构包括至少一个导热凸起4和中部导热层3。
23.至少一个导热凸起4,用于缓冲应力、传导热量和支撑结构,防止芯片损坏,散热效
果佳。
24.此外在导热凸起4与硅之间设置中部导热层3,既可保证热量传递,又可方便导热凸起4的加工形成,同时厚度薄,热应力对器件影响较小,底部散热片5的热应力不直接挤压芯片,保护芯片,避免损坏。
25.芯片1将封装层2分割为对称的上下两层,且上层封装层包封的多个导热凸起4和下层封装层包封的芯片1电性连接处如植球结构对称,整个封装体的上下结构较为对称,结构稳定,器件的可靠性强。
26.本技术中部结构的制作成本很低,相对于有同样功效的其他结构而言,本技术制作步骤简单,制作效率高,我司生产线工艺完全可以快速制作出,不需要额外增加其他步骤,研究成本低,成本能够有效控制,散热和保护芯片的效果较好。
27.实施例1图3为本发明一种芯片散热工艺第一实施例的步骤示意图,包括以下步骤:s1,提供一载板,在晶圆上形成电性连接处,即植球,后切割为单一芯片1,将一个或者多个芯片1放置在载板上并包封封装,后暴露出植球;s2,在塑封料上形成与植球连通的焊盘和输出管脚并再次包封封装,后暴露出焊盘和输出管脚,并移走载板;s3,在芯片背面和塑封料表面通过表面处理形成中部导热层3,如金属板;s4,在中部导热层3远离芯片1的一侧表面处理形成至少一个导热凸起4,如铜柱;s5,包封每个导热凸起4,后暴露出每个导热凸起4远离中部导热层3的一侧,此时整体为封装层2;s6,封装层2远离芯片1焊盘的一侧整个表面通过表面处理形成底部散热片5,每个导热凸起4与底部散热片5连接,若载板上放置多个芯片1,最后需要进行成品切割工序。
28.在封装层2的内部形成中部结构,即中部导热层3和至少一个导热凸起4,其将底部散热片5和芯片1背面连接起来,芯片硅产生的热量通过中部导热层3传递给每个导热凸起4,通过底部散热片5散热,热传导快,散热效果好,芯片两面结构较为对称,能够平衡高低温形成的应力作用,器件可靠性增加,芯片前面的焊盘也可以用于散热,配合背面的底部散热片5构成双面散热,且中部导热层3的厚度薄热应力对芯片硅影响较小,底部散热片5的热应力挤压环氧树脂塑封料,保护芯片,避免损坏,芯片1将封装层2分割为对称的上下两层,且上层封装层包封的多个导热凸起4和下层封装层包封的芯片1植球结构对称。
29.请参阅s1、图4a~图4e和图6,将晶圆通过植球机植球后切割为单一芯片1,将多个或者一个芯片1放置到载板上,即本领域常见的面板级或晶圆级封装,本发明在载板上放置一个芯片1,载板为本领域常用载板,如fr-4板,然后进行封装,芯片1放置到载板的过程为装片,装片方式采用常见的点胶方式,芯片1与载板结合牢固,本发明采用环氧树脂塑料料进行包封,即本领域常见的emc塑封料,emc-epoxy
ꢁ
molding
ꢁ
compound
ꢁ
即环氧树脂模塑料、环氧塑封料,是由环氧树脂为基体树脂,以高性能酚醛树脂为固化剂,加入硅微粉等为填料,以及添加多种助剂混配而成的粉状模塑料,内应力低且热导率也相应的低,包封后进行固化,保证胶接强度,通过研磨或者钻孔的方式暴露出植球远离芯片1的一侧。
30.点胶装片:在芯片1的背面贴daf膜(die
ꢁ
attach
ꢁ
film),daf膜是本领域常用膜,由两层胶面和中间层高导热树脂层组成,一侧胶面与半导体芯片粘接,常用于半导体元件的封装;在装片载板上点涂环氧树脂,然后将芯片放置,使得在装片的同时芯片与载板结合,装片完成做175℃高温烘烤1h,达到环氧树脂固化使得芯片与载板的结合更加牢固。
31.请参阅s2和图4f-4i,对塑封料的一面电镀形成焊盘,本发明所有电镀工艺前都先形成表面金属种子层,该种子层的形成方式也是本领域常见的方式,例如沉铜,在金属种子层上涂胶、光刻、显影和剥胶后电镀形成焊盘,此过程也是本领域常见的操作手段,焊盘与暴露的植球电性连通,后再次包封,将焊盘塑封,通过研磨或者钻孔的方式将焊盘处对应的塑封料去除,暴露出焊盘远离植球的一侧,然后移去载板。
32.请参阅s3-s7、图4j-4n和图6,在芯片背面和塑封料表面通表面处理形成中部导热层3,通表面处理的方式有电镀和溅射,包封中部导热层3,继续在中部导热层3表面通过电镀或者溅射的方式形成至少一个导热凸起4,包封每个导热凸起4,后通过研磨或者钻孔的方式暴露出每个导热凸起4远离中部导热层3的一侧,此时整体为封装层2,在封装层2远离芯片1焊盘的一侧通过电镀形成底部散热片5,每个导热凸起4的两端分别与中部导热层3和底部散热片5连接,且导热凸起4、中部导热层3和底部散热片5的材质为铜、钨或者钽,每个导热凸起4的形状为规则圆柱形或长方体形,且倾斜或竖直的设置在中部导热层3的表面,中部导热层3和底部散热片5为规则的板或者其他不规则形状,如波浪,也实现上述连接导热的作用即可。
33.中部导热层3的厚度可控,厚度范围为23~27μm,此实施例公开中部导热层3厚度为25μm,中部导热层3的厚度为底部散热片5厚度的0.1~0.8,后续可以在本技术的基础上于植球或者芯片输出管脚处形成重布线组(rdl)以实现电路电性连接。
34.实施例2图5为本发明一种芯片散热工艺第二实施例的步骤示意图,包括以下步骤:s1,提供一载板,在晶圆上植球后切割为单一芯片1,将一个或者多个芯片1放置在载板上并包封封装,后暴露出植球;s2,在塑封料上形成与植球连通的焊盘和输出管脚并再次包封封装,后暴露出焊盘和输出管脚,并移走载板;s3,在芯片背面和塑封料表面通过表面处理形成中部导热层3;
ꢁ
s4,在中部导热层3远离芯片1的一侧表面处理形成至少一个导热凸起4;s5,包封每个导热凸起4,后暴露出每个导热凸起4远离中部导热层3的一侧,此时整体为封装层2;s6,封装层2远离芯片1焊盘的一侧通过表面处理形成底部散热片5,每个导热凸起4与底部散热片5连接,s7,在封装层2的一侧侧壁、两个侧壁、三个侧壁或者四个侧壁上均设置有侧壁散热片6,形成多面散热,如五面散热,若载板上放置多个芯片1,最后需要进行成品切割工序。
35.请参阅图7,与实施例一相比,实施例二在原有实施例一的基础上增加了s7,即在多个侧面形成周围金属保护,周围的金属板同样采用电镀或者溅射的方式形成,底部散热片5和封装层2四周的侧壁散热片6在同一步骤形成,侧壁散热片6分别与底部散热片5和中部导热层3连接,侧壁散热片6配合底部散热片5共形成多面金属板,如五面金属板,散热效果更强,且保护性强。
36.本发明通过继续在多个侧面形成侧壁散热片6,如构成五面散热,同时器件周围形成金属保护,如四周,芯片硅产生的热量通过导热凸起4传递给底部散热片5和侧壁散热片6散热,热传导较快,且芯片两面结构较为对称,能平衡高低温形成的应力作用,器件可靠性增加,且中部导热层3的厚度薄热应力对芯片硅影响较小,底部散热片5的热应力挤压环氧树脂塑封料,避免芯片损坏。
37.可以理解,本发明是通过一些实施例进行描述的,本领域技术人员知悉的,在不脱
离本发明的精神和范围的情况下,可以对这些特征和实施例进行各种改变或等效替换。另外,在本发明的教导下,可以对这些特征和实施例进行修改以适应具体的情况及材料而不会脱离本发明的精神和范围。因此,本发明不受此处所公开的具体实施例的限制,所有落入本技术的权利要求范围内的实施例都属于本发明所保护的范围内。