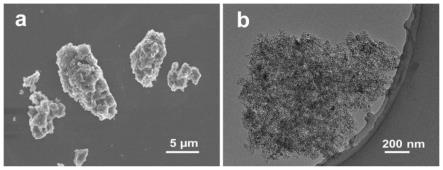
1.本发明涉及锂硫电池技术领域,涉及一种高性能硫@炭/碳化钼复合材料及其制备方法。
背景技术:2.锂硫电池作为下一代高能量密度储能体系,具有能量密度高(2600w h kg-1
)、成本低、环境友好等优点,在电动汽车、无人飞行器、卫星和其他能源储存领域显示了广阔的应用前景。然而基于硫的氧化还原反应机理,硫正极主要存在几个问题,例如高度可溶的多硫化锂易引起“穿梭效应”,导致硫正极循环稳定性变差;固体硫物种(例如s8、li2s和li2s2)在正极上的非均相沉淀导致循环稳定性差。此外,硫导电性较差及在循环过程中体积膨胀严重,易导致硫的利用率降低。因此对硫正极材料的优化设计是从解决锂硫电池存在问题的重要突破口。
3.选择合适的导电硫载体装载硫,借助硫载体的高导电性质改善硫正极输运电子能力,同时可通过物理限域,缓解硫体积膨胀,并束缚多硫化锂溶出,另外引入极性化合物可以通过化学吸附和催化转化,进一步降低多硫化锂在电解液中的累积浓度,有利于抑制长链多硫化锂溶出正极,从而解决单质硫作为电极材料存在的循环稳定性差的问题以及提高硫的利用率。其中,具有中空结构的硫载体更有利于抑制多硫化物的扩散,因为外层的壳可以作为屏障,通过物理/化学阻隔和催化转化来抑制多硫化锂的扩散。
4.传统中空硫载体大多是通过模板法制备的,导致颗粒间无效接触而产生较高的电阻,从而使整体导电性差。此外,由于毛细管冷凝作用,大尺寸内腔使得硫物质难以穿过多孔壳进入腔体,导致硫在充放电过程中产生的多硫化物容易扩散到电解液中。
技术实现要素:5.为了解决现有技术中空硫载体导电性差及硫难进入空腔等问题。本发明提供了一种纳米硫原位封装方法。通过将封装在炭/碳化钼中的硫化锌化学转化为硫,将纳米硫有效封装在具有强物理/化学吸附作用及高效催化多硫化锂作用的炭/碳化钼空腔中,炭/碳化钼的壳壁相互连接,形成导电网络,该制备方法工艺简单方便,不需要通过熔融浸渍负载硫,并保证所有硫都限制在炭/碳化钼空腔内,最终实现高性能锂硫电池正极。
6.本发明的技术方案如下:
7.一种高性能硫@炭/碳化钼复合材料,以具有中空结构的炭/碳化钼为壳,单质硫均匀分散于炭/碳化钼的空腔内,炭/碳化钼壳壁相互连接,形成导电网络。
8.所述炭/碳化钼的空腔大小为6-10nm,空腔间连接更加紧密,具有更高的倍率性能。
9.所述碳化钼均匀分散。
10.本发明还提供一种高性能硫@炭/碳化钼复合材料的制备方法,包括以下步骤:
11.(1)、将氯化锌和一水合柠檬酸、氢氧化钠依次溶解在无水乙醇和去离子水的混合
溶液中,搅拌溶解抽滤后得白色固体氢氧化锌;所述氯化锌和一水合柠檬酸摩尔比为1:0.4-1:1,所述氢氧化钠的摩尔浓度为2-4mol l-1
。
12.(2)、将氢氧化锌固体分散在去离子水中并与九水硫化钠反应,最终抽滤得到白色硫化锌固体,将硫化锌分散在水中,得到硫化锌分散液;
13.(3)、将间苯二酚、甲醛、2,6-二氨基吡啶、四水合钼酸铵及氨水依次搅拌溶解在硫化锌分散液中,然后在水浴中回流处理,经过滤、洗涤及干燥得到得到聚合物包覆硫化锌;所述间苯二酚、甲醛、2,6-二氨基吡啶和四水合钼酸铵的摩尔比为4:8:1:0.28-2.3;
14.(4)、将聚合物包覆硫化锌置于炭化炉之中,在惰性气体保护下进行炭化,得到硫化锌@炭/碳化钼;
15.(5)、将硫化锌@炭/碳化钼分散到六水氯化铁溶液中,连续搅拌,产物经过滤、洗涤及干燥得到硫@炭/碳化钼复合材料。
16.步骤(1)中所述无水乙醇和去离子水的比例为1:7-1:9。
17.步骤(2)中所述反应温度为50-90℃,反应时间为6-7h。
18.步骤(3)中所述回流温度为70-90℃,回流时间为3-6h。
19.步骤(3)中所述氨水用量为0.4-1.0ml。
20.步骤(4)中所述炭化条件为升温速率为1-5℃/min,目标温度为600-900℃,保持时间为1-4h,惰性气体为氮气或氩气。
21.步骤(5)中六水氯化铁溶液的浓度为0.4-1.0mol l-1
,反应时间为48-84h。
22.与现有技术相比,本发明具有以下优势:
23.1.本发明提供的硫正极制备方法工艺简单方便,不需要后续通过熔融浸渍负载硫,在炭/碳化钼中将硫化锌原位转化为硫,保证所有硫都限制在空腔内,解决传统熔融浸渍硫难以进入空腔内的问题。
24.2.本发明制备的硫@炭/碳化钼硫正极材料,可以保证炭/碳化钼初级粒子内硫均匀分布可以提高硫的利用率并促进反应动力学,解决传统熔融浸渍法载硫,硫易团聚的问题。
25.3.本发明制备的硫@炭/碳化钼硫正极材料,微孔炭/碳化钼壳可以通过物理/化学吸附限制多硫化锂,同时促进多硫化锂向硫化锂的催化转化,解决锂硫电池循环稳定性差等问题。
26.4.本发明制备的硫@炭/碳化钼硫正极材料,硫化锌到硫的原位转化存在一定的体积收缩,有助于缓解充放电过程中的体积膨胀,从而保持硫正极复合材料的完整性,解决锂硫电池充放电过程中体积膨胀等问题。
27.5.本发明制备的硫@炭/碳化钼三维硫正极材料,封装有硫纳米颗粒的中空炭/碳化钼紧密连接组成二次微米级粒子硫@炭/碳化钼,以此形成连续的导电网络来增强导电性,解决传统中空硫基质导电性差,硫利用率差等问题。
28.6.本发明制备的硫@炭/碳化钼三维硫正极材料具有1210ma h g-1
的高初始容量、良好的循环稳定性和高倍率性能,在3c高电流密度下,电池的可逆放电容量可以保持在780ma h g-1
。
附图说明
29.图1为本发明实施例1中硫化锌的扫描电镜图(a)及透射电镜图(b)。
30.图2为本发明实施例1中硫化锌、硫化锌@炭/碳化钼及硫@炭/碳化钼的xrd图。
31.图3为本发明实施例1中硫化锌@炭/碳化钼扫描电镜图(a)及透射电镜图(b)。
32.图4为本发明实施例1中硫@炭/碳化钼扫描电镜图(a)及透射电镜图(b)。
33.图5为本发明实施例1中硫@炭/碳化钼透射电镜图(a)及对应的元素分布图(b-d)。
34.图6为本发明实施例1中炭/碳化钼的氮吸附图(a)及孔径分布图(b)。
35.图7为本发明实施例1中硫@炭/碳化钼的xps全谱图(a)及mo 3d的能谱图(b)。
36.图8为本发明实施例1中硫@炭/碳化钼及对比例1中硫@炭的0.5c的循环性能图(a)及倍率性能图(b)。
具体实施方式
37.为了使本领域技术人员更好地理解本发明的技术方案,下面结合具体实施例对本发明作进一步说明,但不限制本发明的范围。
38.实施例1
39.本发明实施例提供了一种硫正极硫@炭/碳化钼复合材料制备方法。
40.具体操作步骤如下:
41.(1)、将1.09g氯化锌和0.841g一水合柠檬酸溶解在20ml无水乙醇和140ml去离子水的混合溶液中,然后在30℃下,以2ml min-1
的滴速向上述溶液中加入20ml氢氧化钠(2.0mol l-1
)水溶液。连续搅拌1h后,将60ml氢氧化钠(2.0mol l-1
)水溶液快速加入悬浮液中,再搅拌混合溶液30min。抽滤后得白色固体氢氧化锌固体。
42.(2)、将步骤(1)所得的氢氧化锌固体分散在100ml水中。将上述得到的分散液与9.6g九水硫化钠在60℃反应7h,溶液由浅黄色变为白色,最后抽滤得到白色硫化锌固体,将0.692g硫化锌分散在400ml水中,得到硫化锌分散液。
43.(3)、将0.220g间苯二酚和293μl甲醛(37wt.%)在30℃溶解在硫化锌分散液中。随后向其中加入0.0546g 2,6-二氨基吡啶并连续搅拌20min,接着,将0.706g四水合钼酸铵溶解到上述混合溶液中,继续搅拌30min,随后加入0.5ml氨水。15min后将上述溶液转移至80℃下回流4h,过滤收集浅绿色产物。
44.(4)、将干燥后的步骤(3)所得固体产物在氩气氛下,从室温以3℃/min升至150℃,恒温120min;再以2℃/min升至炭化终温800℃,恒温180min,炭化得到硫化锌@炭/碳化钼;
45.(5)、将硫化锌@炭/碳化钼分散到0.5mol l-1
六水氯化铁溶液中,连续搅拌72h,产物经过滤、洗涤及干燥得到硫@炭/碳化钼复合材料。
46.本实施例合成的硫化锌见图1,从图1可以看出硫化锌直径为1.0-3.0μm的花状分级纳米结构,这些结构由尺寸约为15nm的纳米颗粒组装而成。图2表明该方法合成的硫化锌为闪锌矿硫化锌。合成的硫化锌@炭/碳化钼见图3,从图3可以看出硫化锌@炭/碳化钼复合材料为直径在1.5-3.0μm范围内的不规则微粒,硫化锌纳米颗粒完美地包裹在厚度约为8nm的致密炭/碳化钼层中。合成的硫@炭/碳化钼见图4,从图4可以看出硫@炭/碳化钼显示出与硫化锌@炭/碳化钼相似的保留良好的微粒结构。其中具有中空结构的炭/碳化钼壳壁相互连接,形成微米级的二次粒子,炭/碳化钼的空腔的大小约为7nm,这是由硫化锌到硫的体积
收缩引起的。合成的硫@炭/碳化钼的元素分布图见图5,从图5可以看出主要元素硫、钼和碳均匀分布在硫@炭/碳化钼复合材料中,且硫均匀分散在腔体内,同时没有残留的锌元素,表明硫化锌已经完全转化为硫。将合成的硫@炭/碳化钼脱硫后得到炭/碳化钼样品,炭/碳化钼壳的孔结构及孔径分布见图6,从图6可以看出炭/碳化钼的孔径分布集中在7nm,与图4中显示的空腔尺寸一致,而且存在微孔体积为0.04cm
3 g-1
,是由炭/碳化钼壳上的微孔造成的,因此可以说明小于7nm的硫被包裹在微孔炭/碳化钼中。将合成的硫@炭/碳化钼的xps结果见图7,从图7可以看出碳化钼的成功制备。
47.将制备的硫@炭/碳化钼复合材料经调浆、涂片,硫含量71.1%,硫面载量为1.60mg cm-2
,接着在氩气手套箱中组装成锂硫电池,并进行电化学性能测试,电化学性能图见图8,从图8可以看出硫正极表现出较高的初始放电容量,良好的循环稳定性和高倍率性能。
48.实施例2
49.(1)、将0.220g间苯二酚和293μl甲醛(37wt.%)在30℃溶解在实施例1得到的硫化锌分散液中。随后向其中加入0.0546g 2,6-二氨基吡啶并连续搅拌20min。接着,将1.412g四水合钼酸铵溶解到上述混合溶液中,继续搅拌30min,随后加入0.5ml氨水。15min后将上述溶液转移至80℃下回流4h,过滤收集浅绿色产物。
50.(2)、将干燥后的步骤(1)所得固体产物在氩气氛下,,从室温以3℃/min升至150℃,恒温120min;再以2℃/min升至炭化终温800℃,恒温180min,炭化得到硫化锌@炭/碳化钼;
51.(3)、将硫化锌@炭/碳化钼分散到0.5mol l-1
六水氯化铁溶液中,连续搅拌72h,产物经过滤、洗涤及干燥得到硫@炭/碳化钼复合材料。
52.将制备的硫@炭/碳化钼复合材料经调浆、涂片,硫含量48.9%,硫面载量为1.02mg cm-2
。
53.实施例3
54.(1)、将0.220g间苯二酚和293μl甲醛(37wt.%)在30℃溶解在实施例1得到的硫化锌分散液中。随后向其中加入0.0546g 2,6-二氨基吡啶并连续搅拌20min。接着,将0.351g钼酸铵四水合物溶解到上述混合溶液中,继续搅拌30min,随后加入0.5ml氨水。15min后将上述溶液转移至80℃下回流4h,过滤收集浅绿色产物。
55.(2)、将干燥后的步骤(1)所得固体产物在氩气氛下,从室温以3℃/min升至150℃,恒温120min;再以2℃/min升至炭化终温800℃,恒温180min,炭化得到硫化锌@炭/碳化钼;
56.(3)、将硫化锌@炭/碳化钼分散到0.5mol l-1
六水氯化铁溶液中去,连续搅拌72h,产物经过滤、洗涤及干燥得到硫@炭/碳化钼复合材料。
57.将制备的硫@炭/碳化钼复合材料经调浆、涂片,硫含量68.3%,硫面载量为1.57mg cm-2
。
58.实施例4
59.(1)、将0.220g间苯二酚和293μl甲醛(37wt.%)在30℃溶解在实施例1得到的硫化锌分散液中。随后向其中加入0.0546g 2,6-二氨基吡啶并连续搅拌20min。接着,将0.0245g四水合钼酸溶解到上述混合溶液中,继续搅拌30min,随后加入0.5ml氨水。15min后将上述溶液转移至80℃下回流4h,过滤收集浅绿色产物。
60.(2)、将干燥后的步骤(1)所得固体产物在氩气氛下,从室温以3℃/min升至150℃,
恒温120min;再以2℃/min升至炭化终温800℃,恒温180min,炭化得到硫化锌@炭/碳化钼;
61.(3)、将硫化锌@炭/碳化钼分散到0.5mol l-1
六水氯化铁溶液中,连续搅拌72h,产物经过滤、洗涤及干燥得到硫@炭/碳化钼复合材料。
62.将制备的硫@炭/碳化钼复合材料经调浆、涂片,硫含量47.1%,硫面载量为1.02mg cm-2
。
63.实施例5
64.(1)、将0.220g间苯二酚和293μl甲醛(37wt.%)在30℃溶解在实施例1得到的硫化锌分散液中。随后向其中加入0.0546g 2,6-二氨基吡啶并连续搅拌20min。接着,将0.176g钼酸铵四水合物溶解到上述混合溶液中,继续搅拌30min,随后加入0.5ml氨水。15min后将上述溶液转移至80℃下回流4h,过滤收集浅绿色产物。
65.(2)、将干燥后的步骤(2)所得固体产物在氩气氛下,从室温以3℃/min升至150℃,恒温120min;再以2℃/min升至炭化终温800℃,恒温180min,炭化得到硫化锌@炭/碳化钼;
66.(5)、将硫化锌@炭/碳化钼分散到0.5mol l-1
六水氯化铁溶液,连续搅拌72h,产物经过滤、洗涤及干燥得到硫@炭/碳化钼复合材料。
67.将制备的硫@炭/碳化钼复合材料经调浆、涂片,硫含量73.5%,硫面载量为1.60mg cm-2
。
68.对比例1
69.(1)、将0.220g间苯二酚和293μl甲醛(37wt.%)在30℃溶解在实施例1得到的硫化锌分散液中。随后向其中加入0.0546g 2,6-二氨基吡啶并连续搅拌20min。随后加入0.5ml氨水。15min后将上述溶液转移至80℃下回流4h,过滤收集砖红色产物。
70.(2)、将干燥后的步骤(1)所得固体产物在氩气氛下,从室温以3℃/min升至150℃,恒温120min;再以2℃/min升至炭化终温800℃,恒温180min,炭化得到硫化锌@炭;
71.(3)、将硫化锌@炭分散到0.5mol l-1
六水氯化铁溶液中,连续搅拌72h,产物经过滤、洗涤及干燥得到硫@炭复合材料。
72.将制备的硫@炭复合材料经调浆、涂片,硫含量50.0%,硫面载量为1.07mg cm-2
。接着在氩气手套箱中组装成锂硫电池,并进行电化学性能测试,电化学性能图见图7,从图7可以看出硫@炭正极初始放电容量及倍率性能低于实施例1-5。
73.对比例2
74.(1)、将实施例1所得的硫@炭/碳化钼复合材料溶解到100ml 1.0m盐酸溶液连续搅拌72h,以除去其中zns纳米颗粒,得到炭/碳化钼。
75.(2)、称取80mg步骤(1)所得炭/碳化钼,206mg单质硫,放入研钵中混合研磨10-15min,研磨至混合物颜色均匀。
76.(3)、将步骤(3)混合后的样品转移至石英舟中,放入浸硫釜中。
77.(4)、将浸硫釜转移至马弗炉中,进行加热,先以3℃/min升温到155℃,保温10h,然后3℃/min升温到400℃,保温2h,然后自然冷却得到炭/碳化钼/硫。
78.将制备的硫@炭/碳化钼复合材料经调浆、涂片,硫含量71.9%,硫面载量为1.65mg cm-2
。
79.对比例3
80.(1)、将0.220g间苯二酚和293μl甲醛(37wt.%)在30℃溶解在实施例1得到的硫化
锌分散液中。随后向其中加入0.0581g己二胺并连续搅拌20min。接着,将0.703g四水合钼酸铵溶解到上述混合溶液中,继续搅拌30min,随后加入0.5ml氨水。15min后将上述溶液转移至80℃下回流4h,过滤收集砖红色产物。
81.(2)、将干燥后的步骤(1)所得固体产物在氩气氛下,从室温以3℃/min升至150℃,恒温120min;再以2℃/min升至炭化终温800℃,恒温180min,炭化得到硫化锌@炭/碳化钼;
82.(3)、将硫化锌@炭/碳化钼分散到0.5mol l-1
六水氯化铁溶液中去,连续搅拌72h,产物经过滤、洗涤及干燥得到硫@炭/碳化钼复合材料。
83.将制备的硫@炭/碳化钼复合材料经调浆、涂片,硫含量49.7%,硫面载量为1.02mg cm-2
。
84.将实施例1~实施例5以及对比例1~对比例3中制得的扣式锂硫电池测试结果记录在表1。
85.表1.锂硫电池测试结果
86.