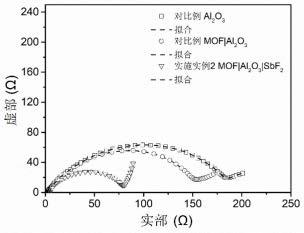
1.本发明属于锂金属电池隔膜技术领域,涉及一种同时抑制锂枝晶和过渡金属溶出的双涂层隔膜及制备方法和应用隔膜的锂金属电池。
背景技术:2.全球新一轮科技革命推动了锂离子电池在便携式电子设备的产业布局,并逐渐在交通动力电源、储能基站、航天军工等新兴领域蓬勃发展。目前传统以licoo2、lifepo4为正极,石墨为负极的商用电池能量密度已接近其理论极限,难以满足市场对能量型储能系统的需求。而将具有超高的理论比容量(3860ma h g-1
)、低电化学势(-3.04vvs标准氢电极)和低密度(0.53g cm-3
)锂金属负极与高电压正极(过渡金属氧化物)匹配被认为是提高整体电池容量和能量密度的必然选择。
3.然而,在商用的电解液中,正负极界面的不稳定性限制了这类电池的发展。目前电化学窗口能满足正极要求的是基于六氟磷酸锂(lipf6)锂盐的碳酸酯基电解液体系,但lipf6对于水分(h2o)敏感,容易发生反应产生氢氟酸(hf),hf会腐蚀正极材料溶出过渡金属离子ni、co、mn,破坏材料结构稳定性,导致电池循环性能迅速衰减。改性的主要方法是构筑正极颗粒表面包覆层隔绝电解液与正极材料的接触、或者引入电解液添加剂捕获电解液中的h2o,然而包覆层的引入通常会增大界面阻抗,电解液添加剂又难以保持在正负极界面同时化学稳定,伴随着氧化还原会被持续消耗。
4.而在负极界面,由于锂金属非常活泼,在电池环境中,锂金属将与液态电解液非质子溶剂反应并形成固体电解质界面膜(sei)。在重复的锂电镀/剥离过程中,锂的不均匀沉积很容易使脆性sei破裂,最终导致正极和电解液中的锂被持续消耗,电池循环寿命缩短。目前,常用改善sei膜的方法有:构建人工保护层、引入电解液成膜添加剂。然而,相比于原位生成的sei,人工构建的离位保护层往往界面粘附力较弱,导致保护层/负极界面离子传输不连续。而电解液成膜添加剂衍生的sei组分通常在高倍率或低温循环条件下阻抗增加,限制电池大功率输出。因此,另一方面,实现均匀的锂沉积行为被认为是获得稳定sei的基本要求。目前,选用可与锂发生合金化反应的“亲锂性”种子(例如ag、au和zn)锚定在沉积基底上用于诱导锂均匀沉积的显著效果已被多个报道证实。而为了避免初始合金化过程中的合金颗粒体积膨胀和严重的不可逆锂消耗,直接采用富锂合金作为负极保护层被认为是可同时实现锂均匀沉积和构筑快离子导通负极保护层的重要方式。研究发现富锂合金表现出与锂金属具有极强的粘附力以及较快的离子传输能力,且在绝缘无机导锂化合物(lii、li2s、lif)协同作用时主要发挥离子传导的作用。然而,苛刻的制备过程(高温、化学预处理)和防潮、惰性气体储存条件大大损害该策略的优异性,导致生产过程效率低下,不易控制。
5.隔膜是可与正负极紧密接触的关键材料,而且在空气中稳定。而表面涂层是改变隔膜物理化学性质如离子电导率、锂迁移数、孔隙率和电解液润湿性的常用策略。如果可以
通过在隔膜上构建多功能涂层来调节电极的界面行为,则可将复杂的电极改性通过简单的隔膜改性来实现。
技术实现要素:6.要解决的技术问题
7.为了避免现有技术的不足之处,本发明提出一种同时抑制锂枝晶和过渡金属溶出的双涂层隔膜及制备方法和应用隔膜的锂金属电池。在电池中,隔膜正对正极一侧的涂层可捕获电解液中的水分,减少hf的生成,抑制过渡金属溶出;隔膜正对负极一侧的涂层与锂负极接触静置后发生原位反应生成富锂合金层以及导锂无机化合物,在循环过程中作为负极隔膜之间的界面层降低界面阻抗并加速锂离子传输,减少枝晶生长。最终,两种涂层双管齐下,共同改善电池容量保持率和循环寿命。
8.技术方案
9.一种同时抑制锂枝晶和过渡金属溶出的双涂层隔膜,其特征在于包括基膜,以及附着在基膜两侧的涂层,分别正对正极或负极;所述涂层中含有质量比为1﹕2-20的聚合物粘结剂和功能材料,其中:正对正极一侧涂层中的功能材料是可吸湿性材料即可储存h2o分子的多孔无机材料;正对负极一侧涂层中的功能材料是能够与锂发生化学和合金反应的无机物,即富锂合金中非锂元素以及可与锂形成稳定无机化合物的非金属元素组成。
10.所述聚合物粘结剂和功能材料的质量比为1:(2-20)(聚合物粘结剂含量过高会影响涂层作用的发挥,若含量过低,则粘结力不足、涂层易脱落)。
11.优选地,所述隔膜正对正极一侧涂层的功能材料是可吸湿性材料,具体地是指可储存h2o分子的多孔材料。例如:多孔sio2、mof、分子筛中的一种或几种的组合。
12.优选地,所述的隔膜正对负极一侧涂层的功能材料是可与锂发生化学和合金反应的无机物,具体地是由富锂合金中非锂元素以及可与锂形成稳定无机化合物的非金属元素组成。例如:agse、inf2、sns2、sncl2、sbf2、alf3、zns、znse、mgs、mgse中的一种或几种的组合。所述的可与锂发生化学反应和合金反应指的是在电解液环境中涂层与锂负极接触静置后,可原位反应转化为含锂合金以及含锂无机物。
13.所述基膜为陶瓷基膜、聚乙烯pe基膜、聚丙烯pp基膜、聚丙烯/聚乙烯/聚丙烯多层基膜、对苯二甲酸乙二醇酯pet基膜、聚丙烯腈pan基膜、玻璃纤维基膜、纤维素基膜或聚偏氟乙烯pvdf基膜。
14.所述聚合物粘结剂为:羧甲基纤维素钠cmc、丁苯乳胶sbr、聚偏氟乙烯pvdf、聚(偏二氟乙烯-六氟丙烯)pvdf-hfp、聚环氧乙烷peo、聚丙烯酸paa或聚乙烯吡咯烷酮pvp中的一种或几种的组合,其重均分子量为5万~300万。
15.所述的隔膜正对正极一侧的涂层厚度为0.1-5μm,正对负极一侧的涂层厚度为0.2-15μm。
16.优选地,所述隔膜正对正极一侧的涂层厚度为0.1-5μm(若涂层过厚,增加隔膜质量,不利于电池能量密度提升;若厚度过低,则不足以充分吸附电解液中的h2o)。正对负极一侧的涂层厚度为0.2-15μm。(若厚度过厚,则会在与锂接触原位反应时大量消耗锂源,影响电池寿命;若厚度过低,则机械稳定较差,影响保护层有效寿命)。
17.所述涂层中的功能材料粒径大小为0.1-1μm。
18.一种制备所述同时抑制锂枝晶和过渡金属溶出的双涂层隔膜的方法,其特征在于步骤如下:
19.步骤1:以聚合物粘结剂为溶质,溶解于溶剂中,加入隔膜正对负极一侧的涂层功能材料混合均匀,得到涂覆浆料;所述聚合物粘结剂与溶剂的质量比为1:50~2:3;
20.聚合物粘结剂与溶剂的质量比为1:50~2:3(若浆料过稀,涂布面密度不稳定、浆料易沉降,若浆料过稠,不利于搅拌、无机物分散不均匀)。
21.步骤2:将所得浆料涂覆在基膜的一侧,干燥使得溶剂蒸发,即在基膜上形成涂层;
22.步骤3:以聚合物粘结剂为溶质,溶解于溶剂中,加入隔膜正对正极一侧的涂层功能材料混合均匀,得到涂覆浆料;所述聚合物粘结剂与溶剂的质量比为1:50~2:3;
23.步骤4:再将所得浆料涂覆在上述制备的含有涂层基膜的另一侧,干燥使得溶剂蒸发,即获得双涂层隔膜。
24.所述步骤1和步骤3中,所用的溶剂选自n-甲基吡咯烷酮、n,n-二甲基甲酰胺、乙醇、甲醇、丙酮或水中的任一种或几种的组合。
25.所述步骤2和步骤4中,干燥温度为20-100℃,干燥时间为10-24h。
26.涂覆的干燥温度为20-100℃(干燥温度过高,隔膜基膜会发生尺寸变形或者微观结构变化,影响电池性能;若温度过低,则溶剂难以挥发彻底,影响电池性能)。干燥时间为10-24h(干燥时间过短,溶剂难以挥发彻底;干燥时间过长,基膜隔膜微观结构受到影响)。
27.一种采用所述同时抑制锂枝晶和过渡金属溶出的双涂层隔膜的锂金属电池,其特征在于:与双涂层隔膜的正极涂层一侧的正极为钴酸锂正极licoo2、锰酸锂正极limn2o4、镍钴锰三元正极lini
x
coymn
1-x-y
o2、镍钴铝三元正极lini
x
coyal
1-x-y
o2或富锂锰基正极(xli2mno3·
(1-x)limo2);与双涂层隔膜的负极涂层一侧的锂负极为锂片以及含金属锂负极;电解液为碳酸酯类电解液。
28.所述的锂金属电池在循环前需进行静置2-24h。
29.有益效果
30.本发明提出的一种同时抑制锂枝晶和过渡金属溶出的双涂层隔膜及制备方法和应用隔膜的锂金属电池,双涂层隔膜包括隔膜以及涂覆于隔膜两侧的涂层,分别正对正负极。所述隔膜正对正极一侧涂层含有聚合物粘结剂和可吸湿材料。所述隔膜正对负极一侧涂层含有聚合物粘结剂和可与锂发生化学和合金反应的无机物。与现有技术相比,本发明制备的隔膜正对正极一侧的涂层可吸附电池电解液中的水分,减少氢氟酸的生成,进而减缓正极过渡金属溶出;正对负极一侧的涂层在电解液环境中与锂负极接触并静置一段时间后,涂层中无机物可与锂发生原位反应并最终转化为含锂合金以及含锂无机物,在循环过程中作为负极隔膜之间的界面层降低界面阻抗并加速锂离子传输,减少枝晶生成。通过两种涂层各自的优异性能,双管齐下,改善电池容量保持率和循环寿命。
31.有益效果
32.(1)本发明提供了一种同时抑制锂枝晶和过渡金属溶出的双涂层隔膜,涉及的隔膜材料空气稳定性良好,生产过程简单,步骤简便,可大规模生产。
33.(2)本发明提供了一种同时抑制锂枝晶和过渡金属溶出的双涂层隔膜用于吸附电解液中的水分,抑制电解液分解,减缓高压正极(过渡金属氧化物)中的过渡金属溶出。
34.(2)本发明提供了一种同时抑制锂枝晶和过渡金属溶出的双涂层隔膜用于通过化
学和合金反应原位生成隔膜与锂金属负极之间的界面层(含锂合金以及含锂无机物),减少负极枝晶生长。
35.(3)本发明提供的同时抑制锂枝晶和过渡金属溶出的双涂层隔膜组装的电池可显示出稳定的循环性能,综合性能明显优于目前商业化普通隔膜组装的锂金属电池。
附图说明
36.图1是本发明实施实例1中所选用的pp基膜、步骤二所得的单涂层隔膜、以及步骤四所得的双涂层隔膜分别组装的lini
0.8
mn
0.1
co
0.1
o2|li电池所获得的充放电循环图。
37.图2为图1中的电池循环后通过电感耦合等离子质谱法测得的电解液中的过渡金属元素浓度。
38.图3是本发明实施实例2中所选用的al2o3陶瓷基膜、步骤二所得的单涂层隔膜、以及步骤四所得的双涂层隔膜分别组装lini
0.8
mn
0.1
co
0.1
o2|li通过交流阻抗法测试获得的阻抗谱。
39.图4是图3中阻抗谱拟合所使用的等效电路。
40.图5是本发明实施实例3中所选用的pe基膜、步骤二所得的单涂层隔膜、以及步骤四所得的双涂层隔膜分别组装的limn2o4|li电池所获得的充放电循环图。
具体实施方式
41.现结合实施例、附图对本发明作进一步描述:
42.实施实例1
43.一方面,本实施实例提供了一种同时抑制锂枝晶和过渡金属溶出的双涂层隔膜的制备方法,包括以下步骤:
44.步骤一:以分子量为130万的聚合物粘结剂pvdf为溶质、n-甲基吡咯烷酮为溶剂,溶质与溶剂按质量比1∶5混合,使溶质完全溶解于溶剂中,然后加入粒径为200nm左右的分子筛(ms)粉末,pvdf与分子筛的质量比为1:19,搅拌8h,配置成浆料待用。
45.步骤二:选取大小为100mm
×
25mm、厚度为25μm的pp隔膜为基膜,将配制的浆料均匀涂覆在基膜的一侧。然后将涂覆后的基膜放入烘箱中,在40℃下真空干燥4h后80℃干燥12h,使溶剂完全蒸发,得到正对正极一侧涂层厚度为1μm的ms|pp单涂层隔膜。
46.步骤三:以分子量为130万的聚合物粘结剂pvdf为溶质、n-甲基吡咯烷酮为溶剂,溶质与溶剂按质量比1∶5混合,使溶质完全溶解于溶剂中,然后加入粒径约为500nm的agse颗粒,pvdf与分子筛的质量比为1:9,搅拌8h,配置成浆料待用。
47.步骤四:将配制的浆料均匀的涂覆在步骤二中所得隔膜的另一侧。将涂覆后的隔膜放入真空烘箱中,在40℃下真空干燥4h后80℃干燥12h,使溶剂完全蒸发,得到正对正极一侧涂层厚度为1μm,正对负极一侧涂层厚度为5μm的ms|pp|agse双涂层隔膜。
48.步骤五:将上述所用基膜、步骤二所得的ms|pp单涂层隔膜,步骤四所得的ms|pp|agse双涂层隔膜使用模具冲成圆片,并与lini
0.8
mn
0.1
co
0.1
o2正极,锂片匹配,选用含10wt%氟代碳酸乙烯酯的1m lipf6/ec:dec(体积比1:1)为电解液组装纽扣电池,组装时正极一侧涂层正对正极,负极一侧涂层正对负极。静置12h后,对其进行充放电测试。
49.图1为本实施实例选用的pp基膜,步骤二所得的ms|pp单涂层隔膜,步骤四所得的
ms|pp|agse双涂层隔膜分别组装的lini
0.8
mn
0.1
co
0.1
o2|li电池的充放电循环图,其中pp基膜、ms|pp单涂层隔膜为对比例。由图1可知,ms|pp|agse双涂层隔膜组装的电池表现出优异的循环稳定性,循环100圈后容量保持率高达98.9%,高于含单涂层ms|pp隔膜(92.4%)和pp基膜(83%)分别组装的电池在100圈后的循环保持率。图2为图1中的电池循环后通过电感耦合等离子质谱法测得的电解液中的过渡金属元素浓度。ms|pp|agse双涂层隔膜循环过后电解液中含有的过渡金属元素浓度与单涂层隔膜相近,远远低于pp基膜,说明隔膜正对正极一侧涂层成功抑制了过渡金属溶出。
50.实施实例2
51.一方面,本实施实例提供了一种同时抑制锂枝晶和过渡金属溶出的双涂层隔膜的制备方法,包括以下步骤:
52.步骤一:以分子量为200万的聚合物粘结剂pvdf-hfp为溶质、四氢呋喃为溶剂,溶质与溶剂按质量比1∶6混合,使溶质完全溶解于溶剂中,然后加入粒径为500nm左右的mof粉末,pvdf-hfp与mof的质量比为1﹕20,搅拌8h,配置成浆料待用。
53.步骤二:选取大小为100mm
×
25mm、厚度为20μm的al2o3陶瓷隔膜为基膜,将配制的浆料均匀涂覆在基膜的一侧。将涂覆后的基膜放入真空烘箱中,在25℃下真空干燥2h后60℃干燥12h,使溶剂完全蒸发,得到正对正极一侧涂层厚度为5μm的mof|al2o3单涂层隔膜。
54.步骤三:以分子量为200万的聚合物粘结剂pvdf-hfp为溶质、四氢呋喃为溶剂,溶质与溶剂按质量比1∶6混合,使溶质完全溶解于溶剂中,然后加入粒径为200nm左右的sbf2粉末,pvdf-hfp与sbf2的质量比为1﹕18,搅拌8h,配置成浆料待用。
55.步骤四:将配制的浆料均匀的涂覆在步骤二中所得隔膜的另一侧。将涂覆后的隔膜放入真空烘箱中,25℃下真空干燥2h后60℃干燥12h,使溶剂完全蒸发,得到正对正极一侧涂层厚度为5μm,正对负极一侧涂层厚度为4μm的mof|al2o3|sbf2双涂层隔膜。
56.步骤五:将上述所用的al2o3陶瓷基膜、步骤二获得的mof|al2o3单涂层隔膜和步骤四获得的mof|al2o3|sbf2双涂层隔膜使用模具冲成圆片,并分别与lini
0.8
mn
0.1
co
0.1
o2正极,锂片匹配,选用1m的lipf6/ec:dec:emc(体积比1:1)为电解液组装纽扣电池,组装时正极一侧涂层正对正极,负极一侧涂层正对负极。静置12h后,使用交流阻抗法测试其阻抗谱。
57.附图3为本实施实例所用的al2o3陶瓷基膜、步骤二所得的mof|al2o3单涂层隔膜和步骤四所得的mof|al2o3|sbf2双涂层隔膜分别组装的lini
0.8
mn
0.1
co
0.1
o2|li电池的阻抗谱图,附表1为其阻抗谱拟合结果,其中al2o3陶瓷基膜和mof|al2o3单涂层隔膜为对比例。明显地,含sbf2涂层的隔膜与电极的界面阻抗低至79.4ω,远远低于al2o3陶瓷基膜与电极的界面阻抗(153ω)和mof|al2o3单涂层隔膜(183.6ω)。图4为拟合图3中的阻抗谱所用的等效电路。此外,表1中的拟合结果显示sbf2复合涂层的引入使得al2o3基膜以及mof|al2o3隔膜与电极的界面离子转移阻抗和电荷转移阻抗分别从70.2ω和111.4ω,50.2ω和101.4ω降低至12.1ω和64.3ω,这说明正对负极一侧的隔膜涂层的引入大大提高了隔膜电极之间的离子电荷传输速率。
58.实施实例3
59.一方面,本实施实例提供了一种同时抑制锂枝晶和过渡金属溶出的双涂层隔膜的制备方法,包括以下步骤:
60.步骤一:以分子量为130万的聚合物粘结剂pvdf为溶质、n-甲基吡咯烷酮为溶剂,
溶质与溶剂按质量比1∶5混合,使溶质完全溶解于溶剂中,然后加入粒径为100nm左右的多孔sio2粉末,pvdf与sio2的质量比为1﹕18,搅拌10h,配置成浆料待用。
61.步骤二:选取大小为100mm
×
25mm、厚度为15μm的pe隔膜为基膜,将配制的浆料均匀涂覆在基膜的一侧。将涂覆后的基膜放入真空烘箱中,在40℃下真空干燥4h后80℃干燥12h,使溶剂完全蒸发,得到正对正极一侧涂层厚度为1μm的sio2|pe单涂层隔膜。
62.步骤三:以分子量为5万的聚合物粘结剂paa为溶质、水为溶剂,溶质与溶剂按质量比1∶7混合,使溶质完全溶解于溶剂中,然后加入粒径为100nm左右的sncl2和agse粉末,比例为1:1,paa与粉末总质量的质量比为1﹕17,搅拌10h,配置成浆料待用。
63.步骤四:将配制的浆料均匀的涂覆在步骤二中所得隔膜的另一侧。将涂覆后的隔膜放入真空烘箱中,在50℃下真空干燥4小时后80℃干燥12h,使溶剂完全蒸发,得到正对正极一侧涂层厚度为2μm,正对负极一侧涂层厚度为2μm的sio2|pe|sncl2|agse双涂层隔膜。
64.步骤五:将上述所用的pe基膜、步骤二所得的sio2|pe单涂层隔膜和步骤四所得的sio2|pe|sncl2|agse双涂层隔膜使用模具冲成圆片,并分别与limn2o4正极,锂片匹配,选用1m的lipf6/ec:dec:emc(体积比1:1)为电解液组装纽扣电池,组装时正极一侧涂层正对正极,负极一侧涂层正对负极。静置14h后,对其进行充放电测试。
65.图5为本实施实例所用的pe基膜,步骤二所得的sio2|pe单涂层隔膜,步骤四所得的sio2|pe|sncl2|agse双涂层隔膜分别组装的limn2o4|li电池的充放电循环图,其中pe基膜和sio2|pe单涂层隔膜为对比例。由图5可知,sio2|pe|sncl2|agse双涂层隔膜组装的电池表现出优异的循环稳定性,1c倍率充放电循环100圈后容量保持率高达92%,高于sio2|pe单涂层隔膜(81.6%)和pe基膜(72.5%)分别组装的电池在100圈后的循环保持率。
66.表1是图3所示阻抗谱等效电路拟合的结果
[0067][0068]
注:其中,rb代表本体阻抗,rf代表离子转移阻抗,r
ct
代表电荷转移阻抗,r
int
代表界面阻抗,由离子转移阻抗和电荷转移阻抗组成。