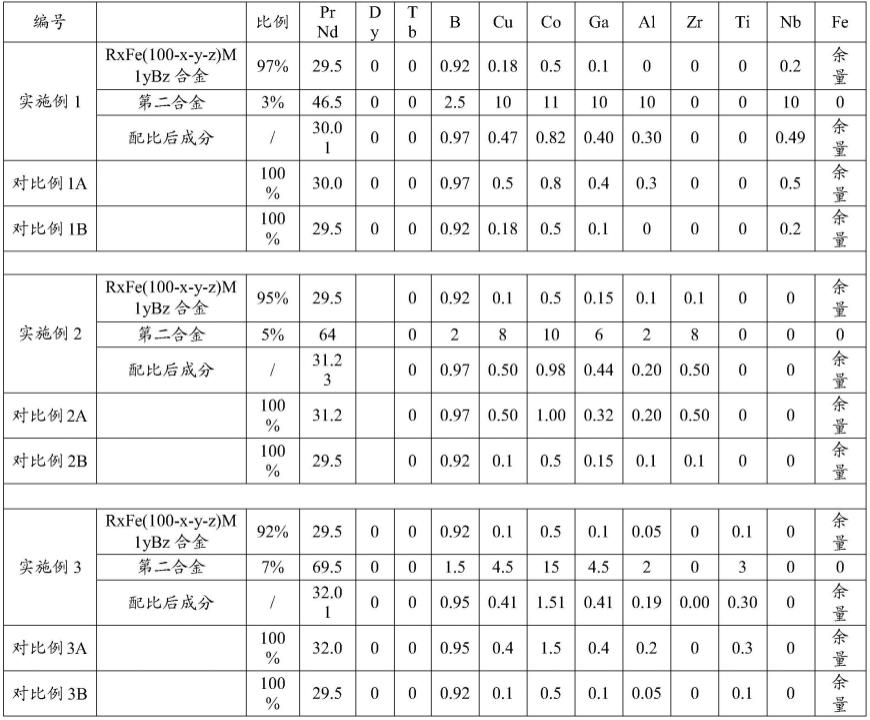
1.本发明属于磁体制备技术领域,尤其涉及一种含钉扎物的稀土永磁体的制备方法。
背景技术:2.钕铁硼系烧结磁体在风力发电、混合动力汽车领域中有广泛的应用。由于工作环境复杂,要求所使用的钕铁硼系烧结磁体具有优异的矫顽力性能。对于采用单合金工艺生产的钕铁硼系烧结磁体,一般通过添加重稀土元素提高磁体的矫顽力,尤其是生产sh、uh和eh以上牌号的磁体时,往往更需过量添加。然而,重稀土资源宝贵,近年来重稀土的原材料市场价格不断上涨,因此,以添加重稀土元素的方式提高磁体的矫顽力面临着沉重的成本压力,目前一般通过在原材料配比中添加ti、nb、zr等微量元素进行熔炼,来实现矫顽力的提升,但是仍需要添加较多的重稀土来达到性能要求。因此,如何能够进一步的提高磁体的综合性能,使得磁体的矫顽力、剩磁与磁能积均能有所提升,而同时又不采用或少采用重稀土元素,已成为业内亟待解决的问题之一。
技术实现要素:3.有鉴于此,本发明的目的在于提供一种含钉扎物的稀土永磁体的制备方法,本发明提供的方法制备的稀土永磁体矫顽力、剩磁与磁能积均较好。
4.本发明提供了一种含钉扎物的稀土永磁体的制备方法,包括:
5.将第一合金粉和第二合金粉混合后进行压制、烧结,得到含钉扎物的稀土永磁体;
6.所述第一合金粉的成分为:rxfe(100-x-y-z)mybz,
7.其中,28.5%≤x≤32.5%,0%≤y≤3%,0.86%≤z≤0.98%,
8.r选自nd、pr、ce、dy、tb、ho中的一种或几种;
9.m选自co、ga、cu、al、hf中的一种或几种;
10.所述第二合金粉体的成分选自pr、nd、co、ga、cu、al、b、ti、zr、2b中的一种或几种。
11.优选的,所述第二合金粉的质量为第一合金粉和第二合金粉总质量的0.5~10%。
12.优选的,所述第一合金粉中pr的质量百分比为0%~14.5%;nd的质量百分比为14%~32.5%;dy的质量百分比为0~4.5%;tb的质量百分比0~4.5%;ce的质量百分比为0%~14.5%;ho的质量百分比为0%~14.5%。
13.优选的,所述第二合金粉中pr和nd总的质量比为20%~80%;co质量百分比为5%~30%;cu的质量百分比为2%~12%;ga的质量百分比为2%~11%;al的质量百分比为2~16%;ti的质量百分比为3%~8%;nb的质量百分比为6%~16%;zr的质量百分比为4%~13%;b的质量百分比为1.5-4%;
14.cu、ga、al、ti/zr/nb的总质量百分比>10%。
15.优选的,所述第一合金粉的平均晶粒尺寸为2~6μm;第二合金粉的平均晶粒尺寸为0.5~4.5μm。
16.优选的,所述压制为取向压制,所述取向压制的磁场强度为1.2~3t。
17.优选的,所述烧结的温度为1010~1060℃。
18.优选的,所述烧结后还包括:
19.进行时效处理;
20.所述时效处理包括:依次进行第一时效处理和第二时效处理。
21.优选的,所述第一时效处理的温度为750~900℃。
22.优选的,所述第二时效处理的温度为350~550℃。
23.本发明针对现有技术中的高性能磁体重稀土用量高,生产成本高的问题,选择细粉搅拌添加复合金粉体方式对稀土永磁体的性能进行优化。同时,针对原材料配比中添加钛元素或锆元素,虽然可一定程度上提高矫顽力,但磁性能提高不显著,并且剩磁与磁能积基本不变或有所降低的缺陷进行改进。本发明通过在细粉搅拌中加入第二合金粉末,并优化设计特定的加入量,钛/锆/铌的采用常规添加方式熔炼时添加大部分会进入主相影响剩磁,而本发明在制粉阶段添加的钛/锆/铌会在富钕相形成钛/锆/铌化合物减少进入主相,从而提高剩磁,同时提高了富钕相的熔点阻止晶粒长大实现晶粒细化,形成钉扎效应进一步提高矫顽力。本发明有效的解决了现有技术利用合金熔点低在晶界起到润湿性,具有减弱磁交换耦合的作用,在烧结中能通过扩散作用进入钕铁硼主相的组织中,提高耐烧结温度,并且不发生晶粒异常长大,但是只能在一定程度上提高矫顽力,对剩磁和磁能积无法提高的固有缺陷。
24.本发明提供的方法可以有效抑制晶粒异常长大的现象,从而提高磁体的矫顽力,而且可更大程度地保留主相,从而使磁体具有优异的剩磁,同时能够在使用或不使用重稀土元素的情况下,均能提高磁体合金的剩磁、矫顽力和磁能积,降低了生产成本,而且工艺简单,适用性广。本发明提供的方法采用了细粉中添加含有钉扎结构的复合金粉体,使制备得到的磁体矫顽力、剩磁与磁能积均能有所提升,同时工艺简单,适合规模化工业生产。
具体实施方式
25.下面将对本发明实施例中的技术方案进行清楚、完整地描述,显然,所描述的实施例仅仅是本发明一部分实施例,而不是全部的实施例。基于本发明中的实施例,本领域普通技术人员在没有做出创造性劳动前提下所获得的所有其他实施例,都属于本发明保护的范围。
26.本发明提供了一种含钉扎物的稀土永磁体的制备方法,包括:
27.将第一合金粉和第二合金粉混合后进行压制、烧结,得到含钉扎物的稀土永磁体;
28.所述第一合金粉的成分为:rxfe(100-x-y-z)mybz,
29.其中,28.5%≤x≤32.5%,0%≤y≤3%,0.86%≤z≤0.98%,
30.r选自nd、pr、ce、dy、tb、ho中的一种或几种;
31.m选自co、ga、cu、al、hf中的一种或几种;
32.所述第二合金粉体的成分选自pr、nd、co、ga、cu、al、b、ti、zr、nb中的一种或几种。
33.在本发明中,所述第一合金粉中的x,y,z为质量百分比,所述x优选为29~31%,更优选为30%;所述y优选为0.5~2.5%,更优选为1~2%,最优选为1.5%;所述z优选为0.9~0.95%,更优选为0.92~0.93%;其中b为硼。
34.在本发明中,所述第一合金粉中优选含有pr、nd、dy、tb、ce和ho;所述pr在第一合金粉中的质量百分比优选为0~14.5%,更优选为0.5~14%,更优选为1~12%,更优选为2~10%,更优选为3~8%,最优选为4~6%;所述nd在第一合金粉中的质量百分比优选为14~32.5%,更优选为20~30%,最优选为25%;所述dy在第一合金粉中的质量含量优选为0~4.5%,更优选为1~4%,更优选为2~3%,最优选为2.5%;所述tb在第一合金粉中的质量含量优选为0~4.5%,更优选为1~4%,更优选为2~3%,最优选为2.5%;所述ce在第一合金粉中的质量含量优选为0~14.5%,更优选为1~14%,更优选为5~10%,最优选为6~8%;所述ho的质量含量优选为0~14.5%,更优选为1~14%,更优选为5~10%,最优选为6~8%。
35.在本发明中,所述第一合金粉的平均晶粒尺寸优选为2~6μm,更优选为3~5μm,最优选为4μm。
36.在本发明中,所述第一合金粉的制备方法优选包括:
37.将合金原料配料后熔炼、铸片,得到第一合金铸片;
38.将所述第一合金铸片进行氢破碎,得到粗粉颗粒;
39.将所述粗粉颗粒进行气流磨粉碎,得到第一合金粉(合金细粉)。
40.在本发明中,本发明对所述合金原料配料没有特殊的限制,采用本领域技术人员熟知的方法按照预获得的第一合金粉的成分进行配料即可。
41.在本发明中,所述熔炼的温度优选为1450~1500℃,更优选为1460~1490℃,最优选为1470~1480℃;所述熔炼优选在高频真空感应熔炼炉中进行熔炼;优选将合金原料放入氧化铝坩埚中在高频真空感应熔炼炉中进行熔炼。
42.在本发明中,所述铸片的方法优选为在铜辊上冷却,所述铜辊的转速优选为35~45转/分,更优选为40转/分。
43.在本发明中,所述第一合金铸片的厚度优选为0.1~0.6mm,更优选为0.2~0.5mm,最优选为0.3~0.4mm。
44.在本发明中,所述氢破碎过程中的吸氢时间优选为1~3h,更优选为1.5~2.5h,最优选为2h;吸氢温度优选为20~300℃,更优选为50~250℃,更优选为100~200℃,最优选为150℃;脱氢时间优选为3~7h,更优选为4~6h,最优选为5h;脱氢温度优选为550~600℃,更优选为560~590℃,最优选为570~580℃。
45.在本发明中,所述气流磨过程中优选加入润滑剂进行磨粉;所述润滑剂的加入量优选为粗粉颗粒质量的0.02~0.1%,更优选为0.05~0.08%,最优选为0.06%。
46.在本发明中,所述第二合金粉中优选含有pr、nd、co、cu、ga、al、ti、nb、zr和b;所述pr和nd在第二合金粉中的总质量百分比优选为20~80%,更优选为30~70%,更优选为40~60%,最优选为50%;所述co在第二合金粉中的质量百分比优选为5~30%,更优选为10~25%,最优选为15~20%;所述cu在第二合金粉中的质量百分比优选为2~12%,更优选为5~10%,最优选为6~8%;所述ca在第二合金粉中的质量百分比优选为2~11%,更优选为5~10%,最优选为6~8%;所述al在第二合金粉中的质量百分比优选为2~16%,更优选为5~15%,更优选为8~12%,最优选为10%;所述ti在第二合金粉中的质量百分比优选为3~8%,更优选为4~7%,最优选为5~6%;所述nb在第二合金粉中的质量百分比优选为6~16%,更优选为8~12%,最优选为10%;所述zr在第二合金粉中的质量百分比优选为4~
13%,更优选为5~10%,最优选为6~8%;所述b在第二合金粉中的质量百分比优选为1.5~4%,更优选为2~3.5%,最优选为2.5~3%;所述cu、ca、al、ti/zr/nb总的(cu+ga+al+ti/zr/nb)的质量百分比优选>10%,ti/zr/nb指的是ti、zr和nb中的一种或几种。
47.在本发明中,所述第二合金粉的平均晶粒尺寸优选为0.5~4.5μm,更优选为1~4μm,更优选为2~3μm,最优选为2.5μm。
48.在本发明中,所述第二合金粉的制备方法以及工艺参数与上述技术方案所述第一合金粉的制备方法相同,工艺参数选择范围相同,在此不再赘述。
49.在本发明中,所述第二合金粉的质量优选为第一合金粉和第二合金粉总质量的0.5~10%,更优选为1~8%,更优选为2~6%,最优选为3~5%。
50.在本发明中,所述压制优选在氮气的保护下进行;所述压制优选为磁场取向成型;所述压制优选包括:
51.依次进行取向压制和等静压成型。
52.在本发明中,所述取向压制过程中的磁场强度优选为1.2~3t,更优选为1.5~1.8t,最优选为1.6t;所述取向压制优选在密封无氧的手套箱中进行。
53.在本发明中,所述等静压成型的压力优选为150~250mpa,更优选为180~220mpa,最优选为200mpa。
54.在本发明中,所述烧结的温度优选为1010~1060℃,更优选为1020~1050℃,最优选为1030~1040℃;所述烧结的时间优选为6~10h,更优选为7~9h,最优选为8h。
55.在本发明中,所述烧结后优选包括:
56.依次进行第一时效处理和第二时效处理。
57.在本发明中,所述第一时效处理的温度优选为750~900℃,更优选为800~850℃,所述第一时效处理的时间优选为3~13h,更优选为5~10h,最优选为6~8h。
58.在本发明中,所述第二时效处理的时间优选为350~550℃,更优选为400~500℃,最优选为450℃;所述第二时效处理的时间优选为1~8小时,更优选为2~6小时,最优选为3~4小时。
59.本发明提供的方法可以有效抑制晶粒异常长大的现象,从而提高磁体的矫顽力,而且可更大程度地保留主相,从而使磁体具有优异的剩磁,同时能够在使用或不使用重稀土元素的情况下,均能提高磁体合金的剩磁、矫顽力和磁能积,降低了生产成本,而且工艺简单,适用性广。本发明提供的方法采用了细粉中添加含有钉扎结构的复合金粉体,使制备得到的磁体矫顽力、剩磁与磁能积均能有所提升,同时工艺简单,适合规模化工业生产。
60.对比例1a和对比例1b
61.按表1中对比例1a和对比例1b的配比原料将其放入氧化铝坩埚,置于高频真空感应熔炼炉中熔炼,将得到熔液在1460℃浇铸,在转速为40转/分的铜辊上冷却,得到平均厚度为0.30mm钕铁硼合金铸片;
62.将上述得到的铸片进行氢破碎,所述氢破碎过程中的吸氢时间为1小时,脱氢时间5小时,脱氢温度为600℃,冷却2小时,制得粗粉;
63.将上述得到的粗品进行气流磨,得到粒度为3.4微米的粉末;
64.将上述得到的粉末在密封无氧的手套箱中1.7t磁场下进行磁场取向成型处理,然后在200mpa下进行等静压处理,得到磁体坯体;
65.将上述得到的磁体坯体在1040℃下烧结6小时,然后在890℃下进行2小时的时效处理,最后在525℃下进行5小时的时效处理,得到稀土永磁体。
66.实施例1
67.按表1中实施例1的成分配比,配置rxfe(100-x-y-z)m1ybz合金原材料(第一合金原料)和第二合金原材料;
68.分别将两种合金原料放入氧化铝坩埚,置于高频真空感应熔炼炉,将得到的两种熔液分别在1460℃浇铸,在转速为40转/分的铜辊上冷却,得到平均厚度为0.30mm两种合金铸片;
69.将得到的两种合金铸片分别进行氢破碎,氢破碎过程中的吸氢时间为1小时,脱氢时间5小时,脱氢温度为600℃,冷却2小时,得到第一合金粗粉和第二合金粗粉;
70.将第一合金粗粉进行气流磨,得到粒度为3.4微米的第一合金细粉;将第二合金粗粉进行气流磨,得到2.5微米的第二合金细粉。
71.将第二合金细粉按添加量为总质量的3wt%和第一合金细粉混合,使用三维搅拌机搅拌30min,得到混合细粉;
72.将得到的混合细粉在密封无氧的手套箱中1.7t磁场下进行磁场取向成型处理,在200mpa下进行等静压处理,得到磁体坯体;
73.将上述得到的磁体坯体在1040℃下烧结6小时,然后在890℃下进行2小时的时效处理,最后在525℃下进行5小时的时效处理,得到稀土永磁体。
74.对本发明对比例1a、对比例1b和实施例1制备的稀土永磁体按照gb/t-3217-2013《永磁(硬磁)材料磁性试验方法》方法进行性能检测,检测结果为:
[0075] br(kgs)hcj(koe)hk/hcj实施例114.0519.50.98对比例1a14.0418.90.98对比例1b14.7213.50.95
[0076]
可以看出,在磁体成分相同条件下,通过在细粉搅拌中添加3wt%的第二合金粉,矫顽力提高6.0koe,相比熔炼添加的方式提高了0.6koe。
[0077]
对比例2a和对比例2b
[0078]
按表1中对比例2a和对比例2b的配比将原料放入氧化铝坩埚,置于高频真空感应熔炼炉,将得到的熔液在1460℃浇铸,在转速为40转/分的铜辊上冷却,得到平均厚度为0.30mm钕铁硼合金铸片;
[0079]
将上述得到的铸片进行氢破碎,所述氢破碎过程中的吸氢时间为1小时,脱氢时间5小时,脱氢温度为600℃,冷却2小时,制得粗粉;
[0080]
将上述得到的粗粉进行气流磨,得到粒度为3.4微米的粉末;
[0081]
将上述得到的粉末在密封无氧的手套箱中1.7t磁场下进行磁场取向成型处理,然后在200mpa下进行等静压处理,得到磁体坯体;
[0082]
将上述得到的磁体坯体在1040℃下烧结6小时,然后在890℃下进行2小时的时效处理,最后在525℃下进行5小时的时效处理,得到稀土永磁体。
[0083]
实施例2
[0084]
按表1中实施例2的成分配比,配置rxfe(100-x-y-z)m1ybz合金原材料(第一合金
原料)和第二合金原材料;
[0085]
分别将两种合金原料放入氧化铝坩埚,置于高频真空感应熔炼炉,将得到的两种熔液分别在1460℃浇铸,在转速为40转/分的铜辊上冷却,得到平均厚度为0.30mm的两种铸片;
[0086]
将得到的两种铸片分别进行氢破碎,所述氢破碎过程中的吸氢时间为1小时,脱氢时间5小时,脱氢温度为600℃,冷却2小时,得到第一合金粗粉和第二合金粗粉;
[0087]
将第一合金粗粉进行气流磨,得到粒度为3.4微米的第一合金细粉;
[0088]
将第二合金粗粉进行气流磨,得到粒度为2.5微米的第二合金细粉;
[0089]
按照第二合金细粉添加量占总质量的5wt%将第一合金细粉和第二合金细粉进行混合,使用三维搅拌机搅拌30min,得到混合细粉;
[0090]
将得到的混合细粉在密封无氧的手套箱中1.7t磁场下进行磁场取向成型处理,然后在200mpa下进行等静压处理,得到磁体坯体;
[0091]
将得到的磁体坯体在1040℃下烧结6小时,然后在890℃下进行2小时的时效处理,最后在525℃下进行5小时的时效处理,得到稀土永磁体。
[0092]
按照实施例1的方法,对本发明对比例2a、对比例2b和实施例2制备的稀土永磁体进行性能检测,检测结果为:
[0093] br(kgs)hcj(koe)hk/hcj实施例213.7520.60.97对比例2a13.7320.20.98对比例2b14.6813.70.95
[0094]
可以看出,磁体成分相同条件下,通过在细粉搅拌中添加5wt%的第二合金粉,矫顽力提高6.9koe,相比熔炼添加的方式提高了0.4koe。
[0095]
对比例3a和对比例3b
[0096]
按表1中的对比例3a和对比例3b的配比将原料放入氧化铝坩埚,置于高频真空感应熔炼炉,将得到的熔液在1460℃浇铸,在转速为40转/分的铜辊上冷却,得到平均厚度为0.30mm钕铁硼合金铸片;
[0097]
将上述得到的铸片进行氢破碎,所述氢破碎过程中的吸氢时间为1小时,脱氢时间5小时,脱氢温度为600℃,冷却2小时,得到粗粉;
[0098]
将得到的粗粉进行气流磨,得到粒度为3.4微米的粉末;
[0099]
将得到的粉末在密封无氧的手套箱中1.7t磁场下进行磁场取向成型处理,然后在200mpa下进行等静压处理,得到磁体坯体;
[0100]
将得到的磁体坯体在1040℃下烧结6小时,然后在890℃下进行2小时的时效处理,最后在525℃下进行5小时的时效处理,得到稀土永磁体。
[0101]
实施例3
[0102]
按表1中实施例3的成分配比,配置rxfe(100-x-y-z)m1ybz合金原材料(第一合金原料)和第二合金原材料;
[0103]
分别将两种合金原料放入氧化铝坩埚,置于高频真空感应熔炼炉,将得到的两种熔液分别在1460℃浇铸,在转速为40转/分的铜辊上冷却,得到平均厚度为0.30mm两种合金铸片;
[0104]
将得到的两种合金铸片进行分别进行氢破碎,所述氢破碎过程中的吸氢时间为1小时,脱氢时间5小时,脱氢温度为600℃,冷却2小时,得到第一合金粗粉和第二合金粗粉;
[0105]
将第一合金粗粉进行气流磨,得到粒度为3.4微米的第一合金细粉;
[0106]
将第二合金粗粉进行气流磨,得到粒度为2.5微米的第二合金细粉;
[0107]
将第二合金细粉按添加量占总质量的3wt%将第一合金细粉和第二合金细粉混合,使用三维搅拌机搅拌30min;制得混合细粉;
[0108]
将得到的混合细粉在密封无氧的手套箱中1.7t磁场下进行磁场取向成型处理,然后在200mpa下进行等静压处理,得到磁体坯体;
[0109]
将得到的磁体坯体在1040℃下烧结6小时,然后在890℃下进行2小时的时效处理,最后在525℃下进行5小时的时效处理,得到稀土永磁体。
[0110]
按照实施例1的方法,对本发明对比例3a、对比例3b和实施例3制备的稀土永磁体进行性能检测,检测结果为:
[0111] br(kgs)hcj(koe)hk/hcj实施例313.5421.10.97对比例3a13.5720.40.97对比例3b14.6313.50.96
[0112]
可以看出,磁体成分相同条件下,在细粉搅拌中添加3wt%的第二合金粉,矫顽力提高7.6koe,相比熔炼添加的方式提高了0.7koe。
[0113]
表1实施例和对比例中的成分配比(数字单位为wt%)
[0114]
[0115]
本发明提供的方法可以有效抑制晶粒异常长大的现象,从而提高磁体的矫顽力,而且可更大程度地保留主相,从而使磁体具有优异的剩磁,同时能够在使用或不使用重稀土元素的情况下,均能提高磁体合金的剩磁、矫顽力和磁能积,降低了生产成本,而且工艺简单,适用性广。本发明提供的方法采用了细粉中添加含有钉扎结构的复合金粉体,使制备得到的磁体矫顽力、剩磁与磁能积均能有所提升,同时工艺简单,适合规模化工业生产。
[0116]
虽然已参考本发明的特定实施例描述并说明本发明,但是这些描述和说明并不限制本发明。所属领域的技术人员可清晰地理解,在不脱离如由所附权利要求书定义的本发明的真实精神和范围的情况下,可进行各种改变,以使特定情形、材料、物质组成、物质、方法或过程适宜于本技术的目标、精神和范围。所有此类修改都意图在此所附权利要求书的范围内。虽然已参考按特定次序执行的特定操作描述本文中所公开的方法,但应理解,可在不脱离本发明的教示的情况下组合、细分或重新排序这些操作以形成等效方法。因此,除非本文中特别指示,否则操作的次序和分组并非本技术的限制。