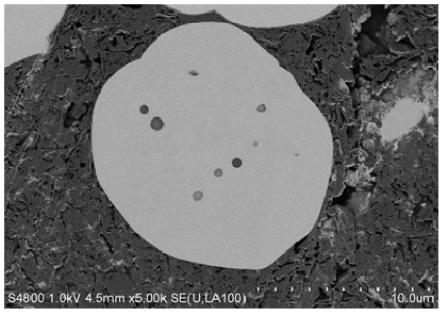
1.本发明涉及锂离子电池领域,具体涉及一种钴铝酸锂正极材料及其制备方法、锂离子电池。
背景技术:2.由于3c电子产品、电动工具、电子烟、航模、穿戴设备等便携式小型装备的稳步发展,市场对钴酸锂电池产品的克容量、压实密度、循环寿命、生产成本控制和安全性能的要求不断提高,这激发了大量围绕高性能钴酸锂电池展开的研究开发工作。
3.钴酸锂(lco)正极材料的性能对锂离子电池的能量密度、循环寿命和安全性等起着至关重要的作用,同时也占据了锂离子电池成本的最高部分。因此对钴酸锂正极材料的研究及改进非常关键。
4.lco具有电压平台高、压实密度高等优点,但近年来,随着市场需求的不断提升,其存在的克容量偏低、循环寿命较差等缺点日益凸显。若能够提升钴酸锂材料颗粒的结构稳定性,从而进一步提高锂离子电池的充放电电压窗口及循环寿命,则可明显提高目前小型锂离子电池的性能,对锂离子电池市场具有重要意义。
技术实现要素:5.本发明的目的是为了克服现有技术常规的钴酸锂(lco)正极材料颗粒结构稳定性差的问题,提供一种单晶型钴铝酸锂(lcao)正极材料及其制备方法、一种锂离子电池,该钴铝酸锂正极材料为单晶型颗粒且颗粒包含单个或多个孔洞结构,由此使得所述正极材料具有较高的颗粒结构稳定性,将其用于锂离子电池后具有明显更高的充放电电压窗口、更高容量保持率(循环寿命)以及更高的安全性。
6.为了实现上述目的,本发明第一方面提供一种钴铝酸锂正极材料,所述钴铝酸锂正极材料为单晶型颗粒;所述正极材料颗粒包含单个或多个孔洞结构。
7.本发明第二方面提供一种钴铝酸锂正极材料的制备方法,其特征在于,所述制备方法包括以下步骤:
8.s1、将钴铝酸锂正极材料前驱体、锂源和可选地添加剂1进行混合,得到混合物i;
9.s2、将所述混合物i进行焙烧、冷却、破碎、筛分,得到钴铝酸锂正极材料过程品;
10.s3、将所述钴铝酸锂正极材料过程品、可选地添加剂2和添加剂3进行混合,得到混合物ii;
11.s4、将所述混合物ii煅烧、冷却、筛分、除磁,得到所述钴铝酸锂正极材料;
12.所述添加剂1为含m’元素的化合物;
13.其中,所述钴铝酸锂正极材料前驱体、所述锂源和所述添加剂1的用量使得0.9≤n(li)/[n(co)+n(al)+n(m’)]≤1.05;
[0014]
0≤n(m’)/[n(co)+n(al)+n(m’)]≤0.02;
[0015]
所述焙烧包括第一焙烧阶段和第二焙烧阶段;控制所述第一焙烧阶段的氧气浓度
vol1与所述第二焙烧阶段的氧气浓度vol2满足:vol2≤vol1。
[0016]
本发明第三方面提供一种由上述制备方法制得的钴铝酸锂正极材料。
[0017]
本发明第四方面提供一种锂离子电池,其特征在于,所述锂离子电池包含上述钴铝酸锂正极材料。
[0018]
通过上述技术方案,本发明提供的钴铝酸锂正极材料及其制备方法、锂离子电池获得以下有益的效果:
[0019]
本发明提供的钴铝酸锂正极材料具有特殊的结构,具体地,该正极材料颗粒为单晶形貌,从该正极材料的颗粒横断面sem图像能够看出,该正极材料颗粒包含单个或多个孔洞结构,该孔洞结构的存在能够缓解正极材料颗粒内部存在的应力,提高正极材料的结构稳定性;该孔洞结构能够部分抵消正极材料在脱/嵌锂过程中存在的体积膨胀/收缩,减缓材料颗粒的开裂和粉化,并且使得正极材料颗粒总体形变减少,进而能够耐受更高的脱/嵌锂程度(即更高的充放电电压窗口)。
[0020]
进一步地,该正极材料颗粒内部存在的孔洞结构,能够缓解正极材料颗粒内部存在的应力,使得该正极材料在长期循环过程中,颗粒不易开裂/破碎或粉化,可进一步提高锂离子电池的循环寿命与安全性。
[0021]
进一步地,将本发明所述的正极材料用于锂离子电池,能够使得锂离子电池具有更高的电压窗口、更长的循环寿命、更低的dcr2增幅及更高的安全性。
附图说明
[0022]
图1是实施例1制得的正极材料的表面sem图像;
[0023]
图2是实施例1制得的正极材料的颗粒横断面sem图像;
[0024]
图3是实施例18制得的正极材料的颗粒横断面sem图像;
[0025]
图4是对比例1制得的正极材料的颗粒横断面sem图像;
[0026]
图5是实施例1制得的正极材料经循环后的颗粒横断面sem图像;
[0027]
图6是对比例1制得的正极材料经循环后的颗粒横断面sem图像。
具体实施方式
[0028]
在本文中所披露的范围的端点和任何值都不限于该精确的范围或值,这些范围或值应当理解为包含接近这些范围或值的值。对于数值范围来说,各个范围的端点值之间、各个范围的端点值和单独的点值之间,以及单独的点值之间可以彼此组合而得到一个或多个新的数值范围,这些数值范围应被视为在本文中具体公开。
[0029]
本发明提供一种钴铝酸锂正极材料,所述钴铝酸锂正极材料为单晶型颗粒;所述正极材料颗粒包含单个或多个孔洞结构。
[0030]
现有技术中的钴酸锂正极材料(lco)或钴铝酸锂正极材料(lcao)的颗粒较大(大颗粒d
50
约12-20μm),常规lco颗粒内部晶畴间应力较大,尤其是在长期的充放电过程中,lco颗粒会随着脱/嵌锂过程的进行而膨胀/收缩,体积变化导致晶畴间应力增大,从而导致颗粒开裂、破碎或粉化等问题,进一步导致锂离子电池循环寿命下降、dcr2增大、lco材料与电解液反应加剧、产气量增加、安全性降低等一系列不良后果。
[0031]
本发明的发明人研究发现,本发明提供的钴铝酸锂正极材料具有特殊的结构,具
体地,从该正极材料的颗粒横断面sem图像能够看出,该正极材料颗粒包含单个或多个孔洞结构,具有该特殊结构的钴铝酸锂正极材料表现出显著改善的结构稳定性,将该钴铝酸锂正极材料用于锂离子电池时,能够使得锂离子电池具有更高的电压窗口、更长的循环寿命、更低的dcr2增幅及更高的安全性。
[0032]
具体地,第一方面,本发明提供的正极材料颗粒内部具有孔洞结构,可疏导材料存在的内部应力,在材料制备及极片辊压过程中,颗粒不易开裂;第二方面,正极材料颗粒脱/嵌锂过程中存在的体积膨胀/收缩可以部分被孔洞体积抵消,正极材料颗粒总体形变减小,进而能够耐受更高的脱/嵌锂程度(即更高的充放电电压窗口);第三方面,正极材料颗粒内部孔洞结构的存在,缓解了颗粒内部的应力,在长期循环过程中,颗粒不易开裂/破碎或粉化,能够进一步提高锂离子电池的循环寿命与安全性。
[0033]
本发明中,所述钴铝酸锂正极材料中的孔洞结构随机分布于颗粒内部,并且颗粒横断面样品通过离子研磨方法制备,不同颗粒切割位置不尽一致,因此正极材料的颗粒横断面sem图中,存在部分颗粒横断面上未能观察到特殊孔洞结构的情况。另外,将本发明所述钴铝酸锂正极材料与常规钴酸锂正极材料掺混使用时,也存在部分颗粒横断面上未能观察到特殊孔洞结构的情况。
[0034]
根据本发明,所述孔洞结构中的孔洞的长轴与短轴之比为1-1.5:1。
[0035]
本发明中,所述孔洞结构中,孔洞的长轴与短轴之比满足上述范围时,表明所述孔洞结构为圆形或近似圆形,孔洞内部表面能较低,无明显凸起或凹陷等缺陷位点,避免颗粒沿缺陷位点从内部开裂,进而能够增强颗粒结构稳定性,使得包含该正极材料的锂离子电池具有更高的电压窗口、更长的循环寿命、更低的dcr2增幅及更高的安全性。
[0036]
本发明中,所述孔洞的长轴是指正极材料的颗粒横断面sem图像中,孔洞的边缘两点连线经过该孔洞几何中心时的最大值,所述孔洞的短轴是指正极材料的颗粒横断面sem图像中,孔洞的边缘两点连线经过该孔洞几何中心时的最小值。
[0037]
本发明中,所述长轴和所述短轴的长度通过sem图像测得。
[0038]
本发明中,所述孔洞结构呈圆形和/或近似圆形的结构。
[0039]
进一步地,所述孔洞结构中的孔洞的长轴与短轴之比为1-1.2:1。
[0040]
根据本发明,所述钴铝酸锂正极材料的颗粒的平均直径为dc,所述孔洞结构中的孔洞的平均直径为dh,其中,0%《dh/dc×
100%≤20%。
[0041]
本发明中,所述钴铝酸锂正极材料的颗粒的平均直径dc是指1k放大倍数下,正极材料的颗粒横断面sem图像中,所有颗粒直径的平均值;孔洞结构中的孔洞的平均直径dh是指1k放大倍数下,正极材料的颗粒横断面sem图像中,所有孔洞直径的平均值。
[0042]
本发明中,当dc与dk满足上述关系时,孔洞结构的尺寸与其所在颗粒的尺寸比例适中,避免了孔洞结构的尺寸占颗粒尺寸比例过大从而导致钴铝酸锂材料层变薄、脆性增加、颗粒强度降低的问题。这使得正极材料结构稳定性得到进一步改善,进而使得包含该正极材料的锂离子电池具有更高的电压窗口、更长的循环寿命、更低的dcr2增幅及更高的安全性。
[0043]
进一步地,0.1%≤dh/dc×
100%≤15%。
[0044]
根据本发明,所述孔洞结构中的孔洞的平均直径为dh满足:0μm《dh≤5μm。
[0045]
进一步地,0.1μm≤dh≤3μm。
[0046]
根据本发明,所述正极材料颗粒横断面的面积为s0,颗粒中孔洞结构的总面积为s1,其中,0%《s1/s0
×
100%≤30%。
[0047]
根据本发明,在sem图像中,所述正极材料颗粒的体积为v0,颗粒中孔洞结构的总体积为v1,其中,0%《v1/v0
×
100%≤15%。
[0048]
本发明中,所述正极材料颗粒横断面的面积为s0是指1k放大倍数下,正极材料的颗粒横断面sem图像中,所述正极材料颗粒横断面的面积;所述颗粒中孔洞结构的总面积为s1是指1k放大倍数下,正极材料的颗粒横断面sem图像中,颗粒中孔洞结构的面积之和。
[0049]
本发明中,所述正极材料颗粒的体积为v0是指1k放大倍数下,正极材料的颗粒横断面sem图像中,所述正极材料颗粒体积;所述颗粒中孔洞结构的总体积为v1是指1k放大倍数下,正极材料的颗粒横断面sem图像中,颗粒中所有孔洞结构的体积之和。
[0050]
本发明中,当s0与s1或v0与v1满足上述关系时,孔洞结构的尺寸与数量均较适宜,避免了所述孔洞结构的尺寸过大或数量过多从而导致孔洞结构间钴铝酸锂材料层变薄、压实密度降低、脆性增加、颗粒强度降低的问题。这使得正极材料结构稳定性得到进一步改善,进而使得包含该正极材料的锂离子电池具有更高的电压窗口、更长的循环寿命、更低的dcr2增幅及更高的安全性。
[0051]
进一步地,0.1%≤s1/s0
×
100%≤15%;0.01%≤v1/v0
×
100%≤10%。
[0052]
根据本发明,所述钴铝酸锂正极材料的真密度≤5g/cm3,优选为≤4.98g/cm3。
[0053]
根据本发明,所述钴铝酸锂正极材料的粉末压实密度≥4g/cm3,优选为≥4.1g/cm3。
[0054]
本发明中,所述钴铝酸锂正极材料颗粒内部存在特殊的孔洞结构,使得正极材料的真密度(颗粒密度)略有降低,但是正极材料的抗压性能与颗粒塑性形变得到提升,使得正极材料的压实密度基本不受影响。
[0055]
根据本发明,所述正极材料具有式i所示的组成:
[0056]
lincoaalbm’1-a-b
o2式i
[0057]
其中,0.9≤n≤1.05,0.9≤a≤0.995,0.005≤b≤0.1,0≤1-a-b≤0.02;
[0058]
m’选自na、b、w、mo、v、si、hf、ta、al、y、sr、ba、er、mg、ti、zr、la、ce、p和nb中的至少一种元素。
[0059]
本发明中,发明人研究发现,当钴酸锂和/或钴铝酸锂正极材料中具有低的li含量时,有利于抑制正极材料在高温焙烧过程中,晶核间的快速融合,使得晶核间的空隙能够得以保留,最终形成本发明所述的孔洞结构。
[0060]
进一步地,本发明中,通过控制正极材料中li的含量,能够实现对正极材料中,孔洞结构的数量的调控。
[0061]
更进一步地,为了进一步地提高钴酸锂正极材料(lco)层状结构的稳定性,使得所述孔洞结构能够充分发挥其改善锂离子电池性能的作用,优选地,所述正极材料中包含较高的al掺杂量。
[0062]
由于al
3+
与co
3+
离子半径较接近,al元素可有效替代部分co元素进入钴铝酸锂正极材料(lcao)层状结构中;同时,由于al-o键稳定性高于co-o键,使得o元素脱出难度大幅增加,钴铝酸锂正极材料(lcao)的层状结构稳定性较钴酸锂正极材料(lco)明显提升。即较高的al掺杂量可提高lcao层状结构的稳定性,有效抑制高电压体系下正极材料的失氧行
为;同时,通过控制al元素的掺杂量,能够调节lcao材料层状结构的稳定性,使其适用于不同电压体系的锂离子电池。
[0063]
进一步地,0.95≤n≤1.03,0.95≤a≤0.99,0.01≤b≤0.05,0.001≤1-a-b≤0.01。
[0064]
进一步地,m’选自na、b、al、mg、sr、ba、zr、la和y中的至少一种元素。
[0065]
本发明第二方面提供一种钴铝酸锂正极材料的制备方法,其特征在于,所述制备方法包括以下步骤:
[0066]
s1、将钴铝酸锂正极材料前驱体、锂源和可选地添加剂1进行混合,得到混合物i;
[0067]
s2、将所述混合物i进行焙烧、冷却、破碎、筛分,得到钴铝酸锂正极材料过程品;
[0068]
s3、将所述钴铝酸锂正极材料过程品、可选地添加剂2和添加剂3进行混合,得到混合物ii;
[0069]
s4、将所述混合物ii进行煅烧、冷却、筛分、除磁,得到所述钴铝酸锂正极材料;
[0070]
所述添加剂1为含m’元素的化合物;
[0071]
其中,所述钴铝酸锂正极材料前驱体、所述锂源和所述添加剂1的用量使得0.9≤n(li)/[n(co)+n(al)+n(m’)]≤1.05;
[0072]
0≤n(m’)/[n(co)+n(al)+n(m’)]≤0.02;
[0073]
所述焙烧包括第一焙烧阶段和第二焙烧阶段;控制所述第一焙烧阶段的氧气浓度vol1与所述第二焙烧阶段的氧气浓度vol2满足:vol2≤vol1。
[0074]
本发明中,在钴铝酸锂正极材料的制备过程中,降低锂源的引入量,并通过特殊的焙烧工艺对包含钴铝酸锂正极材料前驱体、锂源和添加剂1的混合物i进行焙烧。具体地:采用两段焙烧阶段实现所述焙烧,并控制第二焙烧阶段的氧气浓度小于等于第一焙烧阶段的氧气浓度。由此使得制得的钴铝酸锂正极材料具有本发明第一方面所述的特征,具体为:所述正极材料的颗粒横断面sem图像中,所述颗粒包含单个或多个孔洞结构。该孔洞结构的存在能够缓解正极材料颗粒内部存在的应力,提高正极材料的结构稳定性;该孔洞结构能够部分抵消正极材料在脱/嵌锂过程中存在的体积膨胀/收缩,减缓材料颗粒的开裂和粉化,并且使得正极材料颗粒总体形变减小,进而能够耐受更高的脱/嵌锂程度(即更高的充放电电压窗口)。
[0075]
进一步地,该正极材料颗粒内部存在的孔洞结构,能够缓解正极材料颗粒内部存在的应力,使得该正极材料在长期循环过程中,颗粒不易开裂/破碎或粉化,可进一步提高锂离子电池的循环寿命与安全性。
[0076]
更进一步地,将本发明所述的正极材料用于锂离子电池,能够使得锂离子电池具有更高的电压窗口、更长的循环寿命、更低的dcr2增幅及更高的安全性。
[0077]
本发明中,发明人研究发现,低的锂源的加入量有利于抑制高温焙烧过程中lco晶核间的快速融合,使得晶核间的空隙能够得以保留,最终形成所述孔洞结构。
[0078]
具体地,常规lco的制备工艺中:
①
首先前驱体与锂源在较低焙烧温度下开始反应,形成大量细小的lco晶核,此阶段晶核间存在大量空隙;
②
随焙烧温度的进一步提升及焙烧时间的延长,在过量锂源的助熔作用下,晶核开始迅速融合,空隙不断沿晶界被排出晶体内部;
③
随焙烧工序的进行,大量晶核不断融合,长大,最终形成完整密实的lco颗粒,所有空隙均沿晶界排出颗粒内部。发明人研究发现在第
②
阶段内过量锂源的存在量降低,晶
核融合将明显受到抑制;但又因为锂源是由颗粒表面扩散至颗粒内部,因此正极材料表面的li浓度较内部更高,导致颗粒表面晶核间的融合速率高于内核,表面优先排出晶粒间空隙形成密实结构层,使得内部部分空隙无法继续排出,从而能够得以留存下来;在进一步的第
③
阶段内,随焙烧温度的升高及时间的延长,颗粒内部晶核也逐渐融合形成完整的单晶lco颗粒,最终形状不规则的空隙在表面张力(或表面能趋小)等作用下形成圆形或近似圆形的孔洞结构随机分布于单晶颗粒内部。
[0079]
进一步地,本发明中,通过控制正极材料中li的含量,能够实现对正极材料中,孔洞结构的数量的调控。
[0080]
进一步地,所述钴铝酸锂正极材料前驱体、所述锂源和所述添加剂1的用量使得0.95≤n(li)/[n(co)+n(al)+n(m’)]≤1.03;
[0081]
0.001≤n(m’)/[n(co)+n(al)+n(m’)]≤0.01。
[0082]
进一步地,本发明的发明人研究发现,采用本发明所述特殊的焙烧工艺对混合物i进行焙烧,有利于加快高温焙烧过程中lco晶核的形成,使得晶核数量增加,晶核间空隙数量增多、尺寸减小,最终形成数量较多、直径较小的孔洞结构。
[0083]
具体地,所述焙烧工艺包含第一焙烧阶段和第二焙烧阶段,并且控制第二焙烧阶段的氧气浓度小于等于第一焙烧阶段的氧气浓度。控制第一焙烧阶段的氧气浓度在较高水平,能够加快钴铝酸锂正极材料前驱体与锂源的反应速率,进而形成大量lco的细小晶核,增加晶核间空隙的数量。控制第二焙烧阶段的氧气浓度小于等于第一焙烧阶段的氧气浓度,能够保持较高的焙烧温度并加快晶核间的融合,使得多个lco晶核形成的颗粒充分反应,由外而内地逐步融合为一个完整单晶颗粒,并将部分晶核间空隙保留在单晶颗粒内部,最终形成本发明第一方面所述的孔洞结构。
[0084]
进一步地,本发明中,通过控制焙烧阶段的氧气浓度,实现对孔洞结构的形成数量及大小的调控。
[0085]
根据本发明,所述第一焙烧阶段的氧气浓度vol1与所述第二焙烧阶段的氧气浓度vol2满足:vol1-vol2为0-80vol%,vol1≥21vol%。
[0086]
本发明中,进一步地控制第一焙烧阶段的氧气浓度vol1与第二焙烧阶段的氧气浓度vol2满足上述关系时,易于生成孔洞结构且能够防止孔洞结构尺寸过大,若vol1《vol2,则第一焙烧阶段内成核反应进行较慢,晶核间空隙较少,到第二焙烧阶段成核反应及晶核间的融合反应均加快,晶核间空隙沿晶界排出无法留存于颗粒内部,导致无法形成所述孔洞结构;若vol1≥vol2,但vol1《21vol%,则第一焙烧阶段内成核反应进行较慢,晶核间空隙亦较少,但到第二焙烧阶段成核反应速率进一步降低,第一焙烧阶段形成的少量晶核及空隙均迅速变大,导致孔洞结构尺寸大幅增加,从而导致钴铝酸锂材料层变薄、压实密度降低、脆性增加、颗粒强度降低的问题。通过合理控制vol1与vol2能够使得正极材料结构稳定性得到进一步改善,进而使得包含该正极材料的锂离子电池具有更高的电压窗口、更长的循环寿命、更低的dcr2增幅及更高的安全性。
[0087]
进一步地,vol1-vol2为20-60vol%,且vol1≥40vol%。
[0088]
根据本发明,所述焙烧按照以下步骤进行:
[0089]
(a)第一焙烧阶段:在氧气浓度为vol1的含氧气氛中,由0℃升温至t1℃,并在t1-10℃至t1+10℃的温度范围内保温t1小时;
[0090]
(b)第二焙烧阶段:在氧气浓度为vol2的含氧气氛中,由t1℃升温至t2℃,并在t2-10℃至t2+10℃范围内保温t2小时;
[0091]
其中,t1为第一焙烧温度,600℃≤t1≤900℃,t1为第一焙烧时间,2h≤t1≤6h;t2为第二焙烧温度,900℃≤t2≤1100℃,t2为第二焙烧时间,6h≤t2≤15h。
[0092]
本发明中,所述第一焙烧温度t1和所述第二焙烧温度t2不同时为900℃,优选地,t2-t1≥50℃。
[0093]
本发明中,采用上述焙烧工艺对包含钴铝酸锂正极材料前驱体、锂源和添加剂1的混合物i进行焙烧,能够使得将钴铝酸锂材料生成过程中的第
①
反应阶段和第
②
反应阶段分开进行,使其充分完成了第
①
阶段的反应才能进入第
②
阶段的反应,进而有效控制生成的钴铝酸锂颗粒内部所含孔洞结构的数量、尺寸。
[0094]
进一步地,所述焙烧按照以下步骤进行:
[0095]
(a)第一焙烧阶段:在氧气浓度为vol1的含氧气氛中,由20-30℃升温至t1℃,并在t1-5℃至t1+5℃的温度范围内保温t1小时;
[0096]
(b)第二焙烧阶段:在氧气浓度为vol2的含氧气氛中,由t1℃升温至t2℃,并在t2-5℃至t2+5℃范围内保温t2小时;
[0097]
其中,t1为第一焙烧温度,700℃≤t1≤880℃,t1为第一焙烧时间,3h≤t1≤5h,t2为第二焙烧温度,950℃≤t2≤1080℃,t2为第二焙烧时间,7h≤t2≤12h。
[0098]
根据本发明,所述添加剂2为含m’元素的化合物。
[0099]
本发明中,所述添加剂1和所述添加剂2可以相同,也可以不同,各自独立地选自含m’元素的化合物。
[0100]
根据本发明,m’选自na、b、w、mo、v、si、hf、ta、al、y、sr、ba、er、mg、ti、zr、la、ce、p和nb中的至少一种元素。
[0101]
根据本发明,所述钴铝酸锂正极材料过程品与所述添加剂2的用量使得0≤n(m’)/[n(co)+n(al)+n(m’)]≤0.02。
[0102]
本发明中,对于所述添加剂1和所述添加剂2各自的用量没有特别限定,只要使得钴铝酸锂正极材料,m’的总用量满足上述范围即可。
[0103]
进一步地,所述钴铝酸锂正极材料过程品与所述添加剂2的用量使得0.001≤n(m’)/[n(co)+n(al)+n(m’)]≤0.01。
[0104]
根据本发明,所述添加剂3为含co元素的化合物。
[0105]
根据本发明,所述钴铝酸锂正极材料过程品与所述添加剂3的用量使得钴铝酸锂正极材料过程品中co元素的摩尔量与添加剂3中co元素的摩尔量之比为1:0.01-0.1。
[0106]
本发明中,所述钴铝酸锂正极材料过程品中co元素的含量与所述添加剂3中co元素的含量之和为钴铝酸锂正极材料中的co元素含量。
[0107]
进一步地,所述钴铝酸锂正极材料过程品与所述添加剂3的用量使得钴铝酸锂正极材料过程品中co元素的摩尔量与添加剂3中co元素的摩尔量之比为1:0.02-0.08。
[0108]
根据本发明,所述煅烧的条件包括:煅烧温度为800-1000℃,煅烧时间为4-10h。
[0109]
进一步地,所述煅烧的条件包括:煅烧温度为850-950℃,煅烧时间为6-8h。
[0110]
本发明中,对于所述钴铝酸锂正极材料前驱体没有特别限定,可以采用本领域常规的制备方法制备,例如,所述钴铝酸锂正极材料前驱体按照以下步骤制备:
[0111]
(1)将钴盐、铝盐配制为混合盐溶液;将沉淀剂和络合剂分别配制为沉淀剂溶液和络合剂溶液;
[0112]
(2)将所述混合盐溶液、沉淀剂溶液和络合剂溶液同时、分别通入反应釜,进行反应、陈化,得到固液混合物;
[0113]
(3)将所述固液混合物进行压滤,得到滤饼,将滤饼进行洗涤、烘干、低温热处理得到所述钴铝酸锂正极材料前驱体。
[0114]
本发明中,对钴盐的种类没有特别限定,可以为本领域中常规的钴盐,例如硫酸钴、氯化钴、硝酸钴和醋酸钴中的至少一种。
[0115]
本发明中,对铝盐的种类没有特别限定,可以为本领域中常规的铝盐,例如硫酸铝、氯化铝、硝酸铝和磷酸铝中的至少一种。
[0116]
本发明中,对沉淀剂的种类没有特别限定,可以为本领域中常规的沉淀剂,例如选自碳酸铵、碳酸氢铵、碳酸钠、碳酸氢钠、碳酸钾和碳酸氢钾中的至少一种。
[0117]
本发明中,对络合剂的种类没有特别限定,可以为本领域中常规的络合剂,例如选自氨水、乙二胺四乙酸二钠、硝酸铵、氯化铵和硫酸铵中的至少一种。
[0118]
根据本发明,所述钴盐与所述铝盐按照n(co):n(al)=(0.8-0.985):(0.005-0.1)的摩尔比配置为混合盐溶液。
[0119]
进一步地,所述钴盐与所述铝盐按照n(co):n(al)=(0.87-0.97):(0.01-0.05)的摩尔比配置为混合盐溶液。
[0120]
根据本发明,所述反应的条件包括:反应温度为40-70℃,ph值控制范围为7-9。
[0121]
进一步地,所述反应的条件包括:反应温度为45-65℃,ph值控制范围为7.5-8.5。
[0122]
根据本发明,所述陈化的时间为2-12h。
[0123]
进一步地,所述陈化的时间为4-10h。
[0124]
根据本发明,所述低温热处理的条件包括:在空气和/或氧气的存在下,在500-900℃的温度下处理1-5h。
[0125]
进一步地,所述低温热处理的条件包括:在空气和/或氧气的存在下,在600-850℃的温度下处理2-4h。
[0126]
本发明第三方面提供一种由上述制备方法制得的钴铝酸锂正极材料。
[0127]
本发明第四方面提供一种锂离子电池,其特征在于,所述锂离子电池包含上述钴铝酸锂正极材料。
[0128]
本发明中,本发明所述的钴铝酸锂正极材料可以单独作为正极材料用于锂离子电池,也可以与常规的钴酸锂正极材料(lco)或多元材料(ncm)等其他锂离子电池正极材料掺混后作为正极材料用于锂离子电池。
[0129]
以下将通过实施例对本发明进行详细描述。以下实施例中,
[0130]
正极材料的形貌以及颗粒横断面的结构采用sem进行测试,所使用仪器为日立s4800,正极材料的形貌测试条件为电压5kv,颗粒横断面测试条件为1kv;
[0131]
颗粒横断面样品的制备采用离子研磨机进行,所使用仪器为日立im4000,研磨速度为100μm/h,研磨时间为30min;
[0132]
正极材料的粉末压实密度采用粉末压实方法测得;所使用仪器为粉末压实仪(mcp-pd51),测试条件为20kn。
[0133]
正极材料的真密度采用气体置换法方法测得,所使用仪器为accupyc 1345,测试条件为吹扫次数10次,测试次数10次,平衡条件≤0.005psig/min。
[0134]
正极材料的组成采用icp方法测得;所用仪器为pe optima 7000dv,测试条件为0.1g样品完全溶解于3ml hno3+9ml hcl的混合酸溶液中,稀释至250ml进行测试。
[0135]
锂离子电池的循环寿命以及dcr2增幅通过扣式电池方法测得;所用仪器为新威电池测试柜(ct3008)。
[0136]
锂离子电池的安全性能采用产气鼓胀率指标表征,并采用软包电池方法测得;所用仪器为新威电池测试柜(ct3008)、游标卡尺、鼓风式恒温烘箱。。
[0137]
实施例以及对比例所用原料均为市售品。
[0138]
实施例1
[0139]
步骤一、钴铝酸锂正极材料前驱体的制备
[0140]
(1)将钴盐(氯化钴)、铝盐(硫酸铝)按照一定摩尔比配制为混合盐溶液;将沉淀剂(碳酸铵)和络合剂(乙二胺四乙酸二钠)分别配制为沉淀剂溶液和络合剂溶液;
[0141]
(2)将所述混合盐溶液、沉淀剂溶液和络合剂溶液同时、分别通入反应釜,进行反应(温度为50℃,ph值为7.5)、陈化(时间为8h),得到固液混合物;
[0142]
(3)将所述固液混合物进行压滤,得到滤饼,将滤饼进行洗涤、烘干、低温热处理(气氛为空气,温度为850℃,时间为3h)得到钴铝酸锂正极材料前驱体。
[0143]
步骤二、钴铝酸锂正极材料的制备
[0144]
s1、将所述钴铝酸锂正极材料前驱体、锂源和可选地添加剂1进行混合,得到混合物i;
[0145]
s2、将所述混合物i进行焙烧、冷却、破碎、筛分,得到钴铝酸锂正极材料过程品;
[0146]
s3、将所述钴铝酸锂正极材料过程品、可选地添加剂2和添加剂3进行混合,得到混合物ii;
[0147]
s4、将混合物ii进行煅烧、冷却、筛分、除磁,得到所述lcao材料。
[0148]
具体的原料种类及配比、操作步骤及工艺条件如表1所示。
[0149]
实施例2-22以及对比例1-7。
[0150]
按照实施例1的方法制备,具体的原料种类及配比、操作步骤及工艺条件如表1所示。
[0151]
表1
[0152]
[0153][0154]
注:co’是指钴铝酸锂正极材料过程品中co元素的摩尔量;co3是指添加剂3中co元素的摩尔量。
[0155]
表1(续)
[0156]
序号s8s9s10s11s12s13s14前驱体
ꢀꢀꢀꢀꢀꢀꢀ
co:al0.955:0.020.955:0.020.955:0.020.955:0.020.955:0.020.955:0.020.955:0.02正极材料
ꢀꢀꢀꢀꢀꢀꢀ
li/me1.031.031.011.031.031.031.03添加剂1mgco3mgco3mgco3mgco3mgco3mgco3mgco3m’/(co+al+m’)0.0040.0040.0040.0040.0040.0040.004第一烧结
ꢀꢀꢀꢀꢀꢀꢀ
vol160%40%21%50%50%50%50%t1/℃750800850750750750750t1/h4454444第二烧结
ꢀꢀꢀꢀꢀꢀꢀ
vol221%21%21%15%30%35%40%t2/℃1050105010501055106010651070t2/h8888.599.510vol1-vol239%19%0%35%20%15%10%添加剂2y2o3y2o3y2o3y2o3y2o3y2o3y2o3m’/(co+al+m’)0.0010.0010.0010.0010.0010.0010.001添加剂3co(oh)2co(oh)2co(oh)2co(oh)2co(oh)2co(oh)2co(oh)2co3/co’0.020.020.020.020.020.020.02煅烧温度/℃900900900900900900900煅烧时间/h8888888
[0157]
注:co’是指钴铝酸锂正极材料过程品中co元素的摩尔量;co3是指添加剂3中co元素的摩尔量。
[0158]
表1(续)
[0159]
序号s15s16s17s18s19s20s21s22前驱体
ꢀꢀꢀꢀꢀꢀꢀꢀ
co:al0.955:0.020.951:0.020.951:0.020.9507:0.020.9496:0.020.895:0.080.97:0.0050.96:0.02
正极材料
ꢀꢀꢀꢀꢀꢀꢀꢀ
li/me1.031.031.031.031.031.031.031.03添加剂1mgco3mgco3mgco3mgco3mgco3mgco3mgco3/m’/(co+al+m’)0.0040.0040.0040.0040.0040.0040.004/第一烧结
ꢀꢀꢀꢀꢀꢀꢀꢀ
vol150%50%50%50%50%50%50%50%t1/℃750750750750750750750750t1/h44444444.0第二烧结
ꢀꢀꢀꢀꢀꢀꢀꢀ
vol221%21%21%21%21%21%21%21%t2/℃9801050105010501050105010501050t2/h12.08.08.08.08.08.08.08.0vol1-vol229%29%29%29%29%29%29%29%添加剂2y2o3al2o3tio2zro2la2o5y2o3y2o3/m’/(co+al+m’)0.0010.0030.0010.00030.00040.0010.001/添加剂3co(oh)2cooohcooohcooohcooohco(oh)2co(oh)2co(oh)2co3/co’0.020.0220.0240.0250.0260.020.020.02煅烧温度/℃900850875925950900900900煅烧时间/h87.576.56888
[0160]
注:co’是指钴铝酸锂正极材料过程品中co元素的摩尔量;co3是指添加剂3中co元素的摩尔量。
[0161]
表1(续)
[0162][0163][0164]
注:co’是指钴铝酸锂正极材料过程品中co元素的摩尔量;co3是指添加剂3中co元素的摩尔量。
[0165]
实施例以及对比例制得的正极材料的组成如表2所示。
[0166]
表2
[0167][0168][0169]
对实施例以及对比例制得的正极材料的结构、真密度以及压实密度进行测试,具体地:所述颗粒平均尺寸为1k放大倍数下,横断面sem图像中所有颗粒直径的平均值;所述孔洞平均尺寸为1k放大倍数下,横断面sem图像中所有孔洞直径的平均值;所述正极材料颗粒横断面的面积s0为1k放大倍数下,横断面sem图像中,正极材料颗粒横断面的面积总和;所述颗粒中孔洞结构的总面积s1为1k放大倍数下,横断面sem图像中,所有孔洞结构中孔洞的面积之和;所述正极材料颗粒的体积v0为1k放大倍数下,横断面sem图像中,所述正极材料颗粒体积的总和;所述颗粒中孔洞结构的总体积v1为1k放大倍数下,横断面sem图像中,所有孔洞结构中孔洞的体积之和;结果如表3所示。
[0170]
表3
[0171][0172][0173]
表3(续)
[0174] s8s9s10s11s12s13s14dc/μm14.615.516.218.315.214.412.7dh/μm0.231.372.191.210.960.880.74dh/dc×
100%1.58%8.84%13.52%6.61%6.32%6.11%5.83%s0/μm21556.171584.211359.701419.60816.15634.83379.84s1/μm2119.72103.96164.0033.5114.659.253.87s1/s0
×
100%7.69%6.56%12.06%2.36%1.80%1.46%1.02%v0/μm30.118422.607372.557910.01294.16712.78181.2724v1/μm30.00010.13111.18310.01560.00470.00250.0008v1/v0
×
100%0.121%0.580%1.631%0.156%0.113%0.089%0.059%长轴/短轴1.061.031.2111.081.111.09真密度/g/cm34.944.944.954.954.954.954.96pd/g/cm34.214.194.164.184.164.174.19
[0175]
表3(续)
[0176] s15s16s17s18s19s20s21s22dc/μm2.713.813.713.613.814.215.614.7dh/μm0.111.180.940.831.061.131.081.24dh/dc×
100%4.07%8.55%6.86%6.10%7.68%7.96%6.92%8.44%s0/μm2137.34717.58839.821001.84941.82854.751260.85610.67s1/μm25.4725.1822.5425.7535.0129.2339.8815.64s1/s0
×
100%3.98%3.51%2.68%2.57%3.72%3.42%3.16%2.56%v0/μm30.03348.25464.95534.12947.85368.15538.70217.1842v1/μm30.00050.02480.00910.00650.02240.02220.01910.0155v1/v0
×
100%1.623%0.300%0.184%0.157%0.286%0.272%0.219%0.216%长轴/短轴1.041.071.081.1211.151.071.06真密度/g/cm34.964.954.954.944.944.954.964.96
pd/g/cm33.824.174.184.184.194.174.204.18
[0177]
表3(续)
[0178][0179][0180]
由表3可以看出,所有实施例均含有孔洞结构,所有对比例均不含孔洞结构,实施例较对比例真密度略低,压实密度pd相当。实施例1-实施例3中,随li/me的提升,孔洞结构平均尺寸减小,孔洞结构所占颗粒尺寸、颗粒横断面积、颗粒体积的比例迅速降低;实施例6-实施例9中,随vol1的减小,孔洞结构所占颗粒横断面积、颗粒体积的比例增大;实施例11-实施例14中,随vol2的增大,孔洞结构平均尺寸减小,孔洞结构所占颗粒尺寸、颗粒横断面积、颗粒体积的比例逐渐降低。
[0181]
图1是实施例1制得的正极材料的表面sem图像。由图1可以看出,在500倍放大倍数下实施例1制得的正极材料颗基本上均为单晶颗粒,少数颗粒为不超过5个一次颗粒团聚形成的二次颗粒。
[0182]
图2是实施例1制得的正极材料的颗粒横断面sem图像,由图2可以看出,在5k倍放大倍数下本发明实施例1制得的钴铝酸锂正极材料的颗粒横断面包含单个或多个孔洞结构。具体地,图2所示该颗粒含有多个孔洞,且孔洞形状为圆形和/或近似圆形。经测试,该颗粒的直径为14.4μm;含有9个孔洞结构;该正极材料颗粒中,孔洞的平均直径为0.48μm,最大的直径为0.79μm,最小的直径为0.12μm。由于该样品含有所述特殊孔洞结构,颗粒内部应力较小,未出现明显开裂的情况。
[0183]
图3是实施例18制得的正极材料s18的颗粒横断面sem图像,由图3可以看出,在1k倍放大倍数下,正极材料s18的颗粒横断面sem图像中,颗粒总数量为56个,含有孔洞结构的颗粒数量为13个;颗粒的平均直径dc为13.6μm;孔洞的平均直径dh为0.83μm;孔洞结构中的孔洞的平均直径dh占颗粒的平均直径dc的比例dh/dc×
100%为6.1%;正极材料颗粒横断面的面积s0的总和为1001.84μm2;颗粒中孔洞结构的总面积s1为25.75μm2;孔洞结构的总面积占其所在颗粒横断面的面积的比例s1/s0
×
100%为2.57%;正极材料颗粒的体积v0为4.1294μm3;颗粒中孔洞结构的总体积为0.0065μm3;孔洞结构的总体积占其所在颗粒总体积的比例v1/v0
×
100%为0.157%。
[0184]
图4是对比例1制得的正极材料的颗粒横断面sem图像。由图4可以看出,在5k倍放大倍数下,对比例1制得的正极材料颗粒中不含有孔洞结构,颗粒内容的应力较大,颗粒的
结构稳定性较差,导致内部出现较明显的裂纹。
[0185]
测试例
[0186]
将实施例以及对比例制得的正极材料组装成电池,电池的组装步骤如下:
[0187]
扣式电池按照以下步骤制备:
[0188]
将9.2g正极材料、0.4g乙炔黑及0.4g聚偏二氟乙烯(pvdf)进行混合,涂覆在铝箔上并进行烘干处理,用100mpa的压力冲压成型,得到直径为12mm,厚度为120μm的正极极片,然后将该正极极片放入真空烘干箱中在120℃下烘干12h。
[0189]
负极使用直径为17mm,厚度为1mm的li金属片;隔膜使用厚度为25μm的聚乙烯多孔膜;电解液使用以1mol/l的lipf6为电解质的碳酸乙烯酯(ec)和碳酸二乙酯(dec)的等量混合液。
[0190]
将正极极片、隔膜、负极极片及电解液在水含量与氧含量均小于5ppm的ar气手套箱内组装成2025型扣式电池。
[0191]
软包电池按照以下步骤制备:
[0192]
将920g正极材料、40g乙炔黑及40g聚偏二氟乙烯(pvdf)进行混合,加入nmp进行制浆,涂覆在铝箔上并进行烘干、辊压、裁片处理,得到长度为400mm,宽度为50mm的正极极片,然后将该正极极片放入真空烘干箱中在120℃下烘干12h。
[0193]
负极使用天然石墨材料涂覆于铜箔上,与正极类似的方法制作成长度为402mm,宽度为50mm的负极极片;隔膜使用厚度为25μm的聚乙烯多孔膜,宽度为52mm;电解液使用以1mol/l的lipf6为电解质的碳酸乙烯酯(ec)和碳酸二乙酯(dec)的等量混合液。
[0194]
将正极极片、隔膜、负极极片、铝塑壳及电解液在水含量与氧含量均小于5ppm的ar气手套箱内组装成52*30mm的小型软包电池。
[0195]
对电池的性能进行测试,具体地,测试方法如下:
[0196]
容量保持率(循环寿命)以及dcr2增幅采用扣式电池方法测得;所用仪器为新威电池测试柜(ct3008),测试条件为1.0c@3-4.57/4.55v,45℃,循环过程中容量保持率越高,表明材料稳定性越高,电池体系循环寿命越好。dcr2增幅越小,表明材料稳定性越高,颗粒开裂、粉化等现象越少。
[0197]
安全性采用产气鼓胀率表征,测试方法为:
①
0.1c@3-4.5v,25℃,恒流恒压充电+恒流放电循环3次(恒压截止电流为0.01c),然后相同制度充至满电状态并测试电池初始厚度,记为d1;
②
将步骤
①
中的电池置于60℃恒温烘箱保温30天;
③
将步骤
②
中电池取出,自然冷却至室温后测试厚度记录为d2;
④
计算产气鼓胀率=(d2/d1-1)*100%。
[0198]
测试结果如表4所示。
[0199]
表4
[0200]
[0201][0202]
通过表4的结果可以看出,相对于对比例1-7,由本发明实施例1-实施例22制得的含有孔洞结构的锂离子电池正极材料组装得到的锂离子电池具有更高的容量保持率、更低的dcr2增幅、更高的使用电压窗口和更低的鼓胀率。
[0203]
进一步地,实施例1-实施例3中,随li/me的升高,容量保持率下降,dcr2增幅升高,鼓胀率增大;实施例6-实施例9中随vol1的减小,容量保持率呈下降趋势,dcr2增幅及鼓胀率呈升高趋势;实施例11-实施例14中,随vol2的增大,容量保持率呈上升趋势,dcr2增幅及鼓胀率呈降低趋势。
[0204]
实施例21采用了较低的al掺杂量,相较于实施例1-实施例20容量保持率较低,dcr2增幅及鼓胀率较高;实施例22相较于实施例2仅采用了al掺杂,未使用其他元素掺杂,容量保持率降低,dcr2增幅及鼓胀率升高。
[0205]
图5是实施例1制得的正极材料经循环后的颗粒横断面sem图像。由图5可以看出,在5k倍放大倍数下,由于本发明实施例1的正极材料的颗粒包含单个或多个孔洞结构,使得正极材料s1的颗粒内部应力较小,经循环后,正极材料的颗粒仍基本保持循环前的状态,仅在颗粒边缘处出现少量微裂纹,颗粒内部无开裂情况。
[0206]
图6是对比例1制得的正极材料经循环后的颗粒横断面sem图像。由图6可以看出,
在5k倍放大倍速下,由于对比例1的正极材料的颗粒中不含有孔洞结构,导致正极材料d1的颗粒内部应力较大,经循环后,正极材料的颗粒的内部以及表面均出现大量的裂纹,颗粒出现开裂情况。
[0207]
以上详细描述了本发明的优选实施方式,但是,本发明并不限于此。在本发明的技术构思范围内,可以对本发明的技术方案进行多种简单变型,包括各个技术特征以任何其它的合适方式进行组合,这些简单变型和组合同样应当视为本发明所公开的内容,均属于本发明的保护范围。