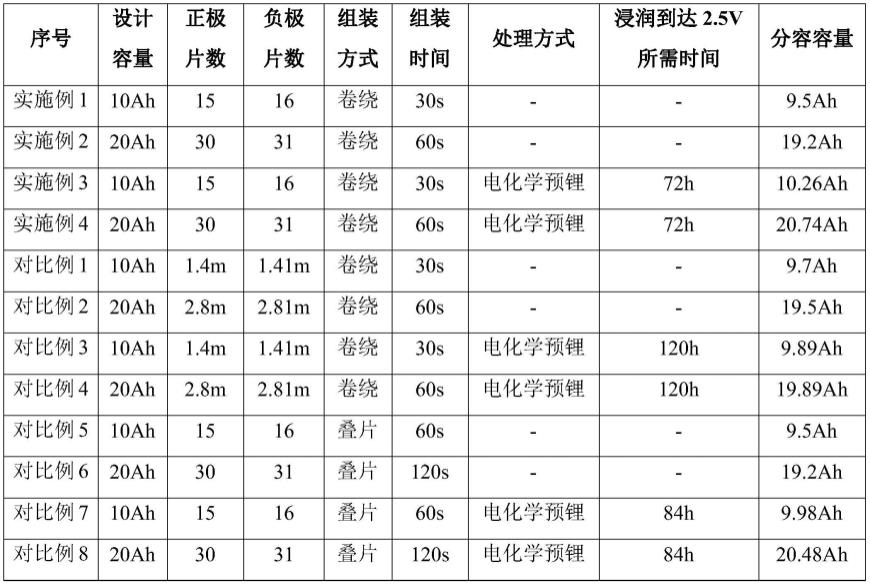
1.本发明涉及一种用于电化学预锂的电芯卷绕方法,属于电芯预锂领域。
背景技术:2.近年来,锂离子电池由于其能量密度高,使用寿命长以及无记忆效应等特点被广泛应用于消费电子领域。最近受国际环境影响,锂电池价格上升,整车单价提高;而且铁锂电芯能量密度提升缓慢,采用高能量密度的三元电芯又存在安全风险。因此,如何开发出安全性高、价格低廉、能量密度高的锂离子电池是未来一段时期急需解决的重大课题。目前,锂电池的研究主要集中在电极材料、电解液、隔膜等方面。尤其是电极材料方面,例如,硅由于其较高的比容量(4200mah/g),硅及其复合材料成为目前锂离子电池负极材料的研究热点。过去20年,锂离子电池取得了许多重要突破,主要朝两个方向发展:一个是高功率,一个是高能量密度。高功率的电池设计,需要活性物质向小粒径、多功能结构和晶体缺陷设计等方向发展。因为材料采用这种设计可以有效缩短锂离子迁移距离、增加电化学反应面积以及提高锂离子扩散速率。高能量密度的电池设计,需要促使嵌锂材料从碳基材料向可锂化金属材料和金属复合材料方向发展。这些设计都会导致锂电池首效降低,首次容量损失增加。
3.预锂化技术的出现为解决锂电池首效低提供了一种有效的解决方法,目前分为压延预锂、蒸镀预锂、粉体预锂、电化学预锂、电解锂盐水溶液预锂和材料预锂等,其中电化学预锂由于产线改动小、与产品兼容性高、预锂效果好等优点,受到科研人员的青睐。叠片电芯四周未封闭,锂离子可以依托电解液的流动从四周进入电芯内部,嵌锂通道多,预锂效率高而且预锂效果好,电性能改善明显,可以明显提升电芯分容容量和电芯循环性能。而卷绕电芯采用电化学预锂时,锂离子只能跟随电解液从极耳侧和背离极耳一侧进入电芯内部,锂离子迁移通道较少导致预锂效率低下。但是卷绕式电芯的制备速率较高,产线生产效率高。因此需要对现有电芯卷绕方法进行改进以提高卷绕电芯的预锂速率。
技术实现要素:4.本发明的目的是提供一种用于电化学预锂的电芯卷绕方法,以解决现有卷绕电芯的电化学预锂速率低,预锂后锂离子分布不均匀和预锂量低等问题。
5.本发明提供的用于电化学预锂的电芯卷绕方法,包括如下步骤:
6.在正极或负极的箔材上进行间歇式涂布得到正极片或负极片;进行卷绕式组装即得到电芯;
7.所述正极和所述负极上的未敷料区的箔材进行多孔处理;
8.所述箔材为铝箔(正极)和铜箔(负极)。
9.所述未敷料区的孔直径为0.5~5.0mm,孔隙率为50%~90%。
10.优选地,所述正极上每片正极片的尺寸相同,所述负极上每片负极片的尺寸相同;
11.所述正极上未敷料区的区域逐渐增大;
12.所述负极上未敷料区的区域逐渐增大。
13.优选地,所述正极上未敷料区的区域呈等差数列增大;
14.所述负极上未敷料区的区域呈等差数列增大。
15.优选地,卷绕时,将所述正极和所述负极从两个方向同步进行卷绕;
16.所述正极片对应所述负极片;
17.所述正极上未敷料区对应所述负极上未敷料区。
18.卷绕后的电芯为方形,正极和负极敷料区极片垂直叠放,多孔区域位于电芯两侧;
19.本发明方法能够提高电化学预锂速率;促进预锂后锂离子分布均匀;提高电化学预锂量。
附图说明
20.图1为正极和负极间歇式涂布示意图。
21.图2为电芯与锂复合后的示意图。
具体实施方式
22.下述实施例中所使用的实验方法如无特殊说明,均为常规方法。
23.下述实施例中所用的材料、试剂等,如无特殊说明,均可从商业途径得到。
24.实施例1、电化学预锂用电芯卷绕工艺
25.正负极采用间歇式涂布,敷料区尺寸保持不变,未敷料区宽度成等差数列增大,如图1、图2所示。未敷料区为多孔箔材,孔隙率80%,孔径2mm。采用卷绕式组装方式,设计容量10ah,正极15片负极16片,记录组装所用时间。经过化成分容等工序,记录浸润达到2.5v时所需要的时间和分容容量。
26.实施例2、电化学预锂用电芯卷绕工艺
27.正负极采用间歇式涂布,敷料区尺寸保持不变,未敷料区宽度成等差数列增大,如图1、图2所示。未敷料区为多孔箔材,孔隙率80%,孔径2mm。采用卷绕式组装方式,设计容量10ah,正极30片负极31片,记录组装所用时间。经过化成分容等工序,记录浸润达到2.5v时所需要的时间和分容容量。
28.实施例3、电化学预锂用电芯卷绕工艺
29.正负极采用间歇式涂布,敷料区尺寸保持不变,未敷料区宽度成等差数列增大,如图1、图2所示。未敷料区为多孔箔材,孔隙率80%,孔径2mm。采用卷绕式组装方式,设计容量10ah,正极15片负极16片,记录组装所用时间。采用电化学预锂方式,锂铜复合带焊接负极耳,经过化成分容等工序,记录浸润达到2.5v时所需要的时间和分容容量。
30.实施例4、电化学预锂用电芯卷绕工艺
31.正负极采用间歇式涂布,敷料区尺寸保持不变,未敷料区宽度成等差数列增大,如图1、图2所示。未敷料区为多孔箔材,孔隙率80%,孔径2mm。采用卷绕式组装方式,设计容量10ah,正极30片负极31片,记录组装所用时间。采用电化学预锂方式,锂铜复合带焊接负极耳,经过化成分容等工序,记录浸润达到2.5v时所需要的时间和分容容量。
32.对比例1、电化学预锂用电芯卷绕工艺
33.正负极采用连续涂布,组装方式为卷绕,设计容量10ah,正极长1.4m负极长1.41m,
记录组装所用时间。经过化成分容等工序,记录分容容量。
34.对比例2、电化学预锂用电芯卷绕工艺
35.正负极采用连续涂布,组装方式为卷绕,设计容量20ah,正极长2.8m负极长2.81m,记录组装所用时间。经过化成分容等工序,记录分容容量。
36.对比例3、电化学预锂用电芯卷绕工艺
37.正负极采用连续涂布,组装方式为卷绕,设计容量10ah,正极长1.4m负极长1.41m,记录组装所用时间。采用电化学预锂方式,锂铜复合带焊接负极耳,经过化成分容等工序,记录浸润达到2.5v时所需要的时间和分容容量。
38.对比例4、电化学预锂用电芯卷绕工艺
39.正负极采用连续涂布,组装方式为卷绕,设计容量20ah,正极长2.8m负极长2.81m,记录组装所用时间。采用电化学预锂方式,锂铜复合带焊接负极耳,经过化成分容等工序,记录浸润达到2.5v时所需要的时间和分容容量。
40.对比例5、
41.正负极采用连续涂布,组装方式为叠片,设计容量10ah,正极15片负极16片,记录组装所用时间。经过化成分容等工序,记录分容容量。
42.对比例6、
43.正负极采用连续涂布,组装方式为叠片,设计容量20ah,正极30片负极31片,记录组装所用时间。经过化成分容等工序,记录分容容量。
44.对比例7、
45.正负极采用连续涂布,组装方式为叠片,设计容量10ah,正极15片负极16片,记录组装所用时间。采用电化学预锂方式,锂铜复合带焊接负极耳,经过化成分容等工序,记录浸润达到2.5v时所需要的时间和分容容量。
46.对比例8、
47.正负极采用连续涂布,组装方式为叠片,设计容量20ah,正极30片负极31片,记录组装所用时间。采用电化学预锂方式,锂铜复合带焊接负极耳,经过化成分容等工序,记录浸润达到2.5v时所需要的时间和分容容量。
48.实验结果的分析:
49.实施例1/2都采用间歇式涂布,随着电芯设计容量的提升,卷绕组装时间增加;实施例3/4采用间歇式涂布后,进行电化学预锂,可以发现浸润时到达2.5v所需要的时间相同为72h,分容后容量较实施例1/2均有所提升,约8%左右。
50.实施例1/2和对比例1/2比较,新型组装所用时间同传统组装;但是同对比例5/6比较,相同正负极片数的情况下,新型组装所用的时间是传统组装的一半,时间节省50%;实施例1/2的分容容量同对比例5/6,都低于对比例1/2,原因是每片负极都留overhang区域消耗了一小部分锂离子。
51.本发明的特点在于未敷料区进行多孔处理,同时孔分布在电芯两侧,这样的设计有利于电解液从极片四周浸润,在保留卷绕方式高效生产的同时兼具叠片电芯的优点,应用于电化学预锂时,生产效率提升,预锂效果提升。
52.表1各实施例和对比例的工艺参数和性能
53.