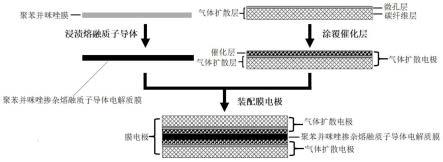
1.本发明属于燃料电池技术领域,具体涉及一种基于熔融质子导体电解质膜的膜电极及其制备方法。
背景技术:2.燃料电池作为一种能量转换装置,可以通过膜电极中的电化学反应将燃料中化学能直接转化为电能。相比常规工作在100℃以下的低温质子交换膜燃料电池(lt-pemfc),工作于100-250℃的高温质子交换膜燃料电池(ht-pemfc)具有特殊优势:(1)膜电极抗co毒化能力显著提高;(2)电化学反应活性增加,催化效率提高;(3)水和热管理系统简化。ht-pemfc具有巨大的应用潜力和市场价值。
3.燃料电池中的电解质膜决定了燃料电池的工作温度,其中聚苯并咪唑(pbi)掺杂磷酸(h3po4)高温质子交换膜为ht-pemfc中常用的质子交换膜。pbi掺杂磷酸高温质子交换膜中,质子导体为磷酸,从室温到工作温度(180℃)均为液态,特别在低温时,液态磷酸易于流失;而且,溶胀率高达200-300%,机械强度显著下降,仅为13.6mpa。
4.另一方面,中国专利cn107331883a与公开文献1(a proton conductor electrolyte based on molten csh5(po4)2for intermediate-temperature fuel cells,rsc advanves,2018,8,5225-5232)报道了pbi掺杂熔融质子导体电解质膜及其制备方法,其中所掺杂的质子导体(csh5(po4)2、kh5(po4)2)室温为固态,温度高于熔点则转变为液态熔融体,该熔融体具有高质子电导率,并且因为在熔点以下为固态,不易发生流失;同时pbi掺杂熔融质子导体膜,溶胀率低,可保持良好机械强度,相比pbi掺杂磷酸高温质子交换膜,pbi掺杂熔融质子导体电解质膜的拉伸强度提高7倍。但是,基于熔融质子导体电解质膜的膜电极的峰值输出功率密度不超过120mw/cm2,没有展现出预期的良好燃料电池输出性能,原因在于其采用常规基于pbi掺杂磷酸高温质子交换膜的膜电极制备方法,在气体扩散电极的催化层中,同样不含质子导体,而是仅含催化剂和粘结剂(兼有疏水剂作用),期望通过掺杂于电解质膜中的熔融质子导体能够像磷酸一样扩散到催化层,提供质子传导,但是熔融质子导体粘度远大于液态磷酸,难以像磷酸一样扩散到催化层中,使得催化层中缺乏质子导体,导致非常低的燃料电池电输出性能,这也成为了该技术产业应用的一大阻碍。
技术实现要素:5.本发明针对现有技术中存在的基于pbi掺杂熔融质子导体电解质膜制备的燃料电池膜电极的催化层中缺乏质子导体的问题,本发明提供一种基于熔融质子导体电解质膜的膜电极制备方法。
6.该方法通过将含有质子导体的催化剂浆料涂覆在气体扩散层表面得到含质子导体气体扩散电极,然后将含质子导体气体扩散电极,贴合于pbi掺杂熔融质子导体电解质膜两侧,制备膜电极,改善了催化层内质子传输,降低了催化层与电解质膜界面间的界面阻力,有效提高了燃料电池膜电极的电输出性能,并且简化工艺流程,提高膜电极制备效率。
7.为实现上述目的,本发明提供一种基于熔融质子导体电解质膜的膜电极制备方法,包括以下步骤:
8.步骤s1、制备聚苯并咪唑(pbi)掺杂熔融质子导体电解质膜;
9.步骤s2、配制含质子导体的催化剂浆料,然后在气体扩散层的微孔层一侧涂覆含质子导体的催化剂浆料,烘干获得气体扩散层上附有含质子导体的催化层的气体扩散电极;
10.步骤s3、将气体扩散电极放置在聚苯并咪唑(pbi)掺杂熔融质子导体电解质膜的两侧组装成燃料电池膜电极。
11.步骤s1中,所述聚苯并咪唑掺杂熔融质子导体电解质膜的制备方法如下:
12.1)将熔融质子导体以高于其熔点0-30℃的温度熔化,使其转为熔融态质子导体;
13.2)将聚苯并咪唑膜浸泡于熔融态质子导体中浸泡,浸泡结束后将聚苯并咪唑膜取出,除去膜表面过量的质子导体,得到聚苯并咪唑掺杂熔融质子导体电解质膜。
14.所述熔融质子导体为,mh5(po4)2,其中m为cs或k。
15.优选地,步骤s1中,所述聚苯并咪唑(pbi)掺杂熔融质子导体电解质膜的制备方法如下:
16.1)将mh5(po4)2(m为cs或k)以高于其熔点0-30℃的温度熔化,使其转为熔融态质子导体;
17.2)将聚苯并咪唑膜浸泡于熔融态质子导体中,浸泡时间为6-72h,浸泡时间结束后将聚苯并咪唑膜取出,除去膜表面过量的质子导体,得到聚苯并咪唑(pbi)掺杂熔融质子导体电解质膜。
18.优选地,步骤s2中,所述催化剂浆料包括:含磷酸的催化剂浆料和/或含磷酸与熔融质子导体的催化剂浆料;
19.当所述催化剂浆料为含磷酸的催化剂浆料和含磷酸与熔融质子导体的催化剂浆料时,在所述气体扩散层的微孔层一侧先涂覆含磷酸与熔融质子导体的催化剂浆料,然后涂覆含磷酸的催化剂浆料。
20.所述含磷酸的催化剂浆料包括:催化剂、粘结剂、磷酸、去离子水、醇。
21.所述含磷酸的催化剂浆料制备方法为:将催化剂、粘结剂、磷酸、去离子水、醇按照质量比为1:0.01~0.1:0.1~1:1~10:5~50混合,超声搅拌得到含磷酸的催化剂浆料;其中粘结剂为聚四氟乙烯(ptfe)、pbi、聚偏二氟乙烯(pvdf)中的一种或多种;醇为乙醇、甲醇、异丙醇、正丙醇中的一种或多种;催化剂为碳载铂催化剂,其中铂与碳载体的质量比为(1-9):(9-1)。
22.所述含磷酸与熔融质子导体的催化剂浆料包括:催化剂、粘结剂、磷酸与熔融质子导体、去离子水。
23.所述含磷酸与熔融质子导体的催化剂浆料的制备方法为:将催化剂、粘结剂、磷酸与熔融质子导体、去离子水按照质量比为1:0.01~0.1:0.1~1:5~50混合,超声搅拌得到含磷酸与熔融质子导体的催化剂浆料;其中磷酸与熔融质子导体的质量比为1:1~10;所述粘结剂为ptfe、pbi、pvdf中的一种或多种;催化剂为碳载铂催化剂,其中铂与碳载体的质量比为(1-9):(9-1)。所述熔融质子导体为mh5(po4)2,其中,m为cs或k。
24.含磷酸与熔融质子导体(mh5(po4)2(m为cs或k))的催化剂浆料的关键在于,催化剂
浆料中不含醇,因为醇会导致mh5(po4)2析出结晶。
25.优选地,所述的燃料电池膜电极的制备方法,步骤s2中,烘干是指在60-200℃干燥。
26.优选地,所述气体扩散电极,实施后处理:表面喷涂磷酸,磷酸含量为1-10mg/cm2。
27.优选地,步骤s2中,所述含质子导体的催化剂浆料的涂覆方式为喷涂、刮涂、狭缝挤出涂覆。
28.与现有技术相比,本发明具有如下有益效果:
29.1)基于pbi掺杂熔融质子导体电解质膜,将含有质子导体的催化剂浆料涂覆在气体扩散层表面,烘干获得气体扩散层上附有含质子导体的催化层的气体扩散电极。催化剂浆料中含有磷酸质子导体、或者磷酸与mh5(po4)2(m为cs和/或k)混合质子导体。该方法在催化剂浆料中引入质子导体,可以实现质子导体在催化层中的均匀分布,形成连续的质子传输通道,降低催化层内的质子传输阻力,并且构筑电极反应的三相(反应气体/质子导体/催化剂)界面。
30.2)作为一个选择,气体扩散电极的催化层中同时存在磷酸和mh5(po4)2(m为cs和/或k),液态的磷酸可以抑制csh5(po4)2或kh5(po4)2低温结晶析出,保证质子导体在催化层中的稳定性,同时提供催化层中的质子传导能力以及质子传导的稳定性。而且催化层中所含mh5(po4)2(m为cs和/或k),在高温工作状态时mh5(po4)2(m为cs和/或k)成为熔融质子导体,粘度高,不易挥发和流失,改善燃料电池稳定性。
31.3)作为一个选择,通过将含有不同质子导体的两种催化剂浆料依次涂覆在气体扩散层表面得到含质子导体的气体扩散电极,靠近气体扩散层的催化剂浆料中含有磷酸和mh5(po4)2(m为cs和/或k),在燃料电池工作温区,熔融态mh5(po4)2具有高粘度,不易挥发,可以缓解质子导体的流失,提升膜电极内质子传导率和质子传导的稳定性。靠近电解质膜的催化剂浆料中质子导体为磷酸,液态磷酸能够在催化层与电解质膜界面间形成液固接触,实现高效质子传导,降低催化层与电解质膜界面间传输阻力,提升燃料电池的电输出性能。
32.4)将含有质子导体的催化剂浆料直接涂覆在气体扩散层上,形成催化层含质子导体的气体扩散电极,便于装配膜电极,可以实现膜电极的快速、高效制备,缩短膜电极的制备时间,提高膜电极制备效率。
附图说明
33.通过阅读参照以下附图对非限制性实施例所作的详细描述,本发明的其它特征、目的和优点将会变得更明显:
34.图1为本发明方法中膜电极制备流程图。
具体实施方式
35.下面结合实施例对本发明进行详细说明。以下实施例将有助于本领域的技术人员进一步理解本发明,但不以任何形式限制本发明。应当指出的是,对本领域的普通技术人员来说,在不脱离本发明构思的前提下,还可以做出若干调整和改进。这些都属于本发明的保护范围。
36.如图1所示,本发明提供一种燃料电池膜电极制备方法,包括以下步骤:
37.步骤s1、制备聚苯并咪唑(pbi)掺杂熔融质子导体电解质膜;
38.步骤s2、配制含质子导体的催化剂浆料,然后在气体扩散层的微孔层一侧涂覆含质子导体的催化剂浆料,60-200℃烘干获得气体扩散层上附有含质子导体的催化层的气体扩散电极。
39.步骤s3、将含质子导体的气体扩散电极放置在pbi掺杂熔融质子导体电解质膜的两侧组装成燃料电池膜电极。
40.接下来结合具体实施例对本发明技术方案做进一步详细描述。
41.实施例1
42.本实施例燃料电池膜电极的制备方法,具体包括以下步骤:
43.步骤s1、制备聚苯并咪唑(pbi)掺杂熔融质子导体电解质膜:将厚度为35μm的pbi膜浸泡于熔融态csh5(po4)2中48h,浸泡温度为150℃,浸泡时间结束后将pbi膜取出,除去膜表面过量的质子导体,得到pbi掺杂熔融质子导体电解质膜。
44.步骤s2、气体扩散电极制备:
45.1)将铂含量为40wt%的碳载铂催化剂、ptfe粘结剂、磷酸与csh5(po4)2、去离子水按照质量比为1:0.02:0.24:20混合,其中磷酸与csh5(po4)2的质量比为1:3,超声搅拌得到含磷酸与csh5(po4)2的催化剂浆料;将铂含量为40wt%的碳载铂催化剂、ptfe粘结剂、磷酸、去离子水、异丙醇按照质量比为1:0.02:0.24:3:25混合,超声搅拌得到含磷酸的催化剂浆料;
46.2)将步骤1)制备的含磷酸与csh5(po4)2的催化剂浆料、以及含磷酸的催化剂浆料,依次涂覆至气体扩散层的微孔层表面,均在涂覆后150℃烘干,形成催化层,从而制得气体扩散电极;
47.步骤s3、将气体扩散电极放置在pbi掺杂熔融质子导体电解质膜的两侧组装成燃料电池膜电极。
48.实施例2
49.本实施例燃料电池膜电极的制备方法,具体包括以下步骤:
50.步骤s1、制备聚苯并咪唑(pbi)掺杂熔融质子导体电解质膜:将厚度为35μm的pbi膜浸(21)泡于熔融态csh5(po4)2中48h,浸泡温度为150℃,浸泡时间结束后将pbi膜取出,除去膜表面过量的质子导体,得到pbi掺杂熔融质子导体电解质膜。
51.步骤s2、气体扩散电极制备:
52.1)先将铂含量为40wt%的碳载铂催化剂、ptfe粘结剂、磷酸与csh5(po4)2、去离子水按照质量比为1:0.02:0.24:20混合,其中磷酸与csh5(po4)2的质量比为1:3,超声搅拌得到含磷酸与csh5(po4)2催化剂浆料;
53.2)将步骤1)制备的含磷酸与csh5(po4)2催化剂浆料涂覆至气体扩散层的微孔层表面,150℃烘干形成催化层,从而制得气体扩散电极;
54.步骤s3、将气体扩散电极放置在pbi掺杂熔融质子导体电解质膜的两侧组装成燃料电池膜电极。
55.实施例3
56.本实施例燃料电池膜电极的制备方法,具体包括以下步骤:
57.步骤s1、制备聚苯并咪唑(pbi)掺杂熔融质子导体电解质膜:将厚度为35μm的pbi
膜(21)浸泡于熔融态csh5(po4)2中48h,浸泡温度为150℃,浸泡时间结束后将pbi膜取出,除去膜表面过量的质子导体,得到pbi掺杂熔融质子导体电解质膜。
58.步骤s2、气体扩散电极制备:
59.1)将铂含量为40wt%的碳载铂催化剂、ptfe粘结剂、磷酸、去离子水、异丙醇按照质量比为1:0.02:0.24:3:25混合,超声搅拌得到含磷酸的催化剂浆料;
60.2)将步骤1)制备的含磷酸的催化剂浆料涂覆至气体扩散层的微孔层表面,150℃烘干形成催化层,从而制得气体扩散电极;
61.步骤s3、将气体扩散电极放置在pbi掺杂熔融质子导体电解质膜的两侧组装成燃料电池膜电极。
62.实施例4
63.本实施例燃料电池膜电极的制备方法,具体包括以下步骤:
64.步骤s1、制备聚苯并咪唑(pbi)掺杂熔融质子导体电解质膜:将厚度为35μm的pbi膜浸(21)泡于熔融态kh5(po4)2中48h,浸泡温度为130℃,浸泡时间结束后将pbi膜取出,除去膜表面过量的质子导体,得到pbi掺杂熔融质子导体电解质膜。
65.步骤s2、气体扩散电极制备:
66.1)将铂含量为40wt%的碳载铂催化剂、ptfe粘结剂、磷酸与kh5(po4)2、去离子水按照质量比为1:0.02:0.24:20混合,其中磷酸与kh5(po4)2的质量比为1:3,超声搅拌得到含磷酸与kh5(po4)2催化剂浆料;将铂含量为40wt%的碳载铂催化剂、ptfe粘结剂、磷酸、去离子水、异丙醇按照质量比为1:0.02:0.24:3:25混合,超声搅拌得到含磷酸的催化剂浆料;
67.2)将步骤1)制备的含磷酸与kh5(po4)2催化剂浆料、以及含磷酸的催化剂浆料,依次涂覆至气体扩散层的微孔层表面,均在涂覆后130℃烘干,形成催化层,从而制得气体扩散电极;
68.步骤s3、将气体扩散电极放置在pbi掺杂熔融质子导体电解质膜的两侧组装成燃料电池膜电极。
69.实施例5
70.本实施例燃料电池膜电极的制备方法,具体包括以下步骤:
71.步骤s1、制备聚苯并咪唑(pbi)掺杂熔融质子导体电解质膜:将厚度为35μm的pbi膜(21)浸泡于熔融态kh5(po4)2中48h,浸泡温度为130℃,浸泡时间结束后将pbi膜取出,除去膜表面过量的质子导体,得到pbi掺杂熔融质子导体电解质膜。
72.步骤s2、气体扩散电极制备:
73.1)先将铂含量为40wt%的碳载铂催化剂、ptfe粘结剂、磷酸与kh5(po4)2、去离子水按照质量比为1:0.02:0.24:20混合,其中磷酸与kh5(po4)2的质量比为1:3,超声搅拌得到含磷酸与kh5(po4)2催化剂浆料;
74.2)将步骤1)制备的含磷酸与kh5(po4)2催化剂浆料涂覆至气体扩散层的微孔层表面,130℃烘干形成催化层,从而制得气体扩散电极;
75.步骤s3、将气体扩散电极放置在pbi掺杂熔融质子导体电解质膜的两侧组装成燃料电池膜电极。
76.实施例6
77.本实施例燃料电池膜电极的制备方法,具体包括以下步骤:
78.步骤s1、制备聚苯并咪唑(pbi)掺杂熔融质子导体电解质膜:将厚度为35μm的pbi膜(21)浸泡于熔融态kh5(po4)2中48h,浸泡温度为130℃,浸泡时间结束后将pbi膜取出,除去膜表面过量的质子导体,得到pbi掺杂熔融质子导体(kh5(po4)2)电解质膜(22)。
79.步骤s2、气体扩散电极制备:
80.1)将铂含量为40wt%的碳载铂催化剂、ptfe粘结剂、磷酸、去离子水、异丙醇按照质量比为1:0.02:0.24:3:25混合,超声搅拌得到含磷酸的催化剂浆料;
81.2)将步骤1)制备的含磷酸的催化剂浆料涂覆至气体扩散层的微孔层表面,130℃烘干形成催化层,从而制得气体扩散电极;
82.步骤s3、将气体扩散电极放置在pbi掺杂熔融质子导体电解质膜的两侧组装成燃料电池膜电极。
83.对比例1
84.本对比例与实施例3的区别在于,催化层不含质子导体。
85.本对比例燃料电池膜电极的制备方法,具体包括以下步骤:
86.步骤s1、制备聚苯并咪唑(pbi)掺杂熔融质子导体电解质膜:将厚度为35μm的pbi膜(21)浸泡于熔融态csh5(po4)2中48h,浸泡温度为150℃,浸泡时间结束后将pbi膜取出,除去膜表面过量的质子导体,得到pbi掺杂熔融质子导体电解质膜。
87.步骤s2、气体扩散电极制备:
88.1)将铂含量为40wt%的碳载铂催化剂、ptfe粘结剂、去离子水、异丙醇按照质量比为1:0.02:3:25混合,超声搅拌得到不含质子导体的催化剂浆料;
89.2)将步骤1)制备的不含质子导体的催化剂浆料涂覆至气体扩散层的微孔层表面,150℃烘干形成催化层,从而制得气体扩散电极;
90.步骤s3、将气体扩散电极放置在pbi掺杂熔融质子导体电解质膜的两侧组装成燃料电池膜电极。
91.对比例2
92.本对比例与实施例3的区别在于催化层不含质子导体,而是实施气体扩散电极后处理即在气体扩散电极上喷磷酸。
93.本对比例燃料电池膜电极的制备方法,具体包括以下步骤:
94.步骤s1、制备聚苯并咪唑(pbi)掺杂熔融质子导体电解质膜:将厚度为35μm的pbi膜(21)浸泡于熔融态csh5(po4)2中48h,浸泡温度为150℃,浸泡时间结束后将pbi膜取出,除去膜表面过量的质子导体,得到pbi掺杂熔融质子导体电解质膜。
95.步骤s2、气体扩散电极制备:
96.1)将铂含量为40wt%的碳载铂催化剂、ptfe粘结剂、去离子水、异丙醇按照质量比为1:0.02:3:25混合,超声搅拌得到不含质子导体的催化剂浆料;
97.2)将步骤1)制备的不含质子导体的催化剂浆料涂覆至气体扩散层的微孔层表面,150℃烘干形成催化层,从而制得气体扩散电极;
98.步骤s3、实施气体扩散电极后处理:使用喷枪将磷酸的乙醇溶液(浓磷酸:乙醇的体积比=1:4)喷涂至气体扩散电极上的催化层的表面,磷酸喷涂量为3mg/cm2)。然后,将实施了后处理的气体扩散电极放置在pbi掺杂熔融质子导体电解质膜的两侧组装成燃料电池膜电极。
99.对比例3
100.本对比例与实施例2的区别在于:将催化层含磷酸与csh5(po4)2的气体扩散电极替换为催化层含csh5(po4)2的气体扩散电极。
101.本对比例燃料电池膜电极的制备方法,具体包括以下步骤:
102.步骤s1、制备聚苯并咪唑(pbi)掺杂熔融质子导体电解质膜:将厚度为35μm的pbi膜(21)浸泡于熔融态csh5(po4)2中48h,浸泡温度为150℃,浸泡时间结束后将pbi膜取出,除去膜表面过量的质子导体,得到pbi掺杂熔融质子导体电解质膜。
103.步骤s2、催化剂涂覆膜制备:1)先将铂含量为40wt%的碳载铂催化剂、ptfe粘结剂、csh5(po4)2、去离子水按照质量比为1:0.02:0.24:20混合,超声搅拌得到含csh5(po4)2催化剂浆料;2)将步骤1)制备的含csh5(po4)2催化剂浆料涂覆至气体扩散层的微孔层表面,150℃烘干形成催化层,从而制得气体扩散电极;
104.步骤s3、将气体扩散电极放置在pbi掺杂熔融质子导体电解质膜的两侧组装成燃料电池膜电极。
105.对比例4
106.本对比例与实施例6的区别在于,催化层不含质子导体。
107.本对比例燃料电池膜电极的制备方法,具体包括以下步骤:
108.步骤s1、制备聚苯并咪唑(pbi)掺杂熔融质子导体电解质膜:将厚度为35μm的pbi膜(21)浸泡于熔融态kh5(po4)2中48h,浸泡温度为130℃,浸泡时间结束后将pbi膜取出,除去膜表面过量的质子导体,得到pbi掺杂熔融质子导体电解质膜。
109.步骤s2、气体扩散电极制备:1)将铂含量为40wt%的碳载铂催化剂、ptfe粘结剂、去离子水、异丙醇按照质量比为1:0.02:3:25混合,超声搅拌得到含磷酸的催化剂浆料;2)将步骤1)制备的不含质子导体的催化剂浆料涂覆至气体扩散层的微孔层表面,130℃烘干形成催化层,从而制得气体扩散电极;
110.步骤s3、将气体扩散电极放置在pbi掺杂熔融质子导体电解质膜的两侧组装成燃料电池膜电极。
111.实施例与对比例的性能测试
112.对各实施例和对比例制备的膜电极装配的燃料电池单电池的输出性能和稳定性进行测试。
113.1、测试方法
114.燃料单电池的输出性能测试方法:将实施例与对比例所得膜电极组装成单电池进行测试,单电池的阴极和阳极分别通入氧气和氢气,无背压,氢气和氧气的气体流量均为0.4l/min,使用菊水电子负载(plz164wa),测试i-v曲线,获得燃料电池输出性能。并且,基于pbi掺杂熔融质子导体(csh5(po4)2)电解质膜的膜电极所装配的燃料电池,运行温度为180℃;基于pbi掺杂熔融质子导体(kh5(po4)2)电解质膜的膜电极所装配的燃料电池,运行温度为160℃。
115.稳定性测试方法:
116.测试条件同上,在0.2a/cm2额定电流密度下,连续运行48h,确认电压稳定性。
117.2、测试结果
118.各实施例和对比例中所制备燃料电池膜电极的编号和主要特征,以及使用所制备
膜电极装配的燃料电池的输出性能,如表1所示。
119.表1
[0120][0121]
燃料电池输出性能:特优(峰值功率密度≥600mw/cm2)、优(400≤峰值功率密度≤600mw/cm2)、中(200≤峰值功率密度≤400mw/cm2)、差(峰值功率密度≤200mw/cm2);
[0122]
燃料电池稳定性:特优(电压衰减率≤0.2mv/h)、优(0.2mv/h≤电压衰减率≤1mv/h)、中(电压衰减率≥1mv/h)。
[0123]
实施例1、2、3,均基于聚苯并咪唑(pbi)掺杂熔融质子导体(csh5(po4)2)电解质膜,并且均采用含有质子导体的催化剂浆料,使得气体扩散电极催化层中均含有质子导体,对比燃料电池输出性能发现,均是优以上。说明在催化剂浆料中直接加入质子导体,获得含质子导体催化层,可以实现质子导体在催化层中的均匀分布,形成连续的质子传输通道,可以降低催化层内的质子传输阻力,并且建立燃料电池电化学反应三相界面。进一步比较,实施例3(燃料电池输出性能为优和稳定性为优),催化层中仅含有磷酸质子导体,磷酸为液体,粘度较低,在燃料电池运行过程中有流失的风险,燃料电池稳定性劣于实施例1和2;实施例2(燃料电池输出性能为优和稳定性为特优),催化层中含有磷酸与csh5(po4)2质子导体,燃料电池工作状态,处于熔融态的csh5(po4)2具有高粘度,不易挥发,可以对磷酸进行固定,减缓磷酸的流失,而磷酸又可以保证mh5(po4)2不结晶析出,提升膜电极内质子传导率和质子传导的稳定性,保证燃料电池运行稳定性;实施例1(燃料电池输出性能为优和稳定性为特优),催化层中含有磷酸与csh5(po4)2质子导体(首层)、以及磷酸质子导体(次层),这是将含有不同质子导体的两种催化剂浆料依次涂覆在气体扩散层表面得到含质子导体的气体扩散电极,靠近气体扩散层的催化层中含有磷酸和csh5(po4)2质子导体,在燃料电池工作状态,处于熔融态的csh5(po4)2具有高粘度,不易挥发,可以缓解质子导体的流失,提升膜电极内质子传导率和质子传导的稳定性,保证燃料电池运行稳定性。靠近电解质膜的催化层中,质子导体为磷酸,液态磷酸能够在催化层与电解质膜界面间形成液固接触,实现高效质子传导,降低催化层与电解质膜界面间质子传输阻力,使得燃料电池的电输出性能与燃料电池稳定性均为特优。
[0124]
相比较,对比例1和对比例2,虽然同样基于聚苯并咪唑(pbi)掺杂熔融质子导体(csh5(po4)2)电解质膜,但是,对比例1,催化剂浆料中不含质子导体,使得所获气体扩散电
极的催化层不含质子导体,无法为燃料电池提供电化学反应所需三相界面,导致对比例1性能为差;对比例2,催化剂浆料中同样不含质子导体,使得所获催化层不含质子导体,但是通过气体扩散电极后处理,在气体扩散电极上喷涂磷酸,磷酸扩散到催化层,为催化层补充质子导体,但是催化层中质子导体分布不均匀,导致燃料电池输出性能和稳定性为中,劣于实施例1、2、3。
[0125]
相比实施例1、2、3,对比例3的主要区别在于,对比例3中催化剂浆料中质子导体为csh5(po4)2。在燃料电池测试过程中,发现燃料电池电输出性能为差,测试结束后对膜电极进行拆解,发现催化层表面有白色csh5(po4)2晶体析出。这可以解释为由于csh5(po4)2在室温下会从催化层析出,而csh5(po4)2结晶体会导致催化层与气体扩散层之间绝缘,故燃料电池测试电输出性能为差,稳定性难以测试。
[0126]
分别对应实施例1、2、3,实施例4、5、6采用kh5(po4)2替代csh5(po4)2,均基于聚苯并咪唑(pbi)掺杂熔融质子导体(kh5(po4)2)电解质膜,催化层分别含磷酸与csh5(po4)2质子导体(首层)和磷酸质子导体(次层)、含磷酸与kh5(po4)2质子导体、以及磷酸质子导体。所制膜电极的燃料电池输出性能与稳定性均为优以上。与实施例4、5、6比较,对比例4,虽然同样基于聚苯并咪唑(pbi)掺杂熔融质子导体(kh5(po4)2)电解质膜,但是,对比例4催化剂浆料中不含质子导体,使得所获催化层不含质子导体,无法为燃料电池电化学反应提供三相界面,导致对比例4燃料电池输出性能为差。
[0127]
以上对本发明的具体实施例进行了描述。需要理解的是,本发明并不局限于上述特定实施方式,本领域技术人员可以在权利要求的范围内做出各种变形或修改,这并不影响本发明的实质内容。