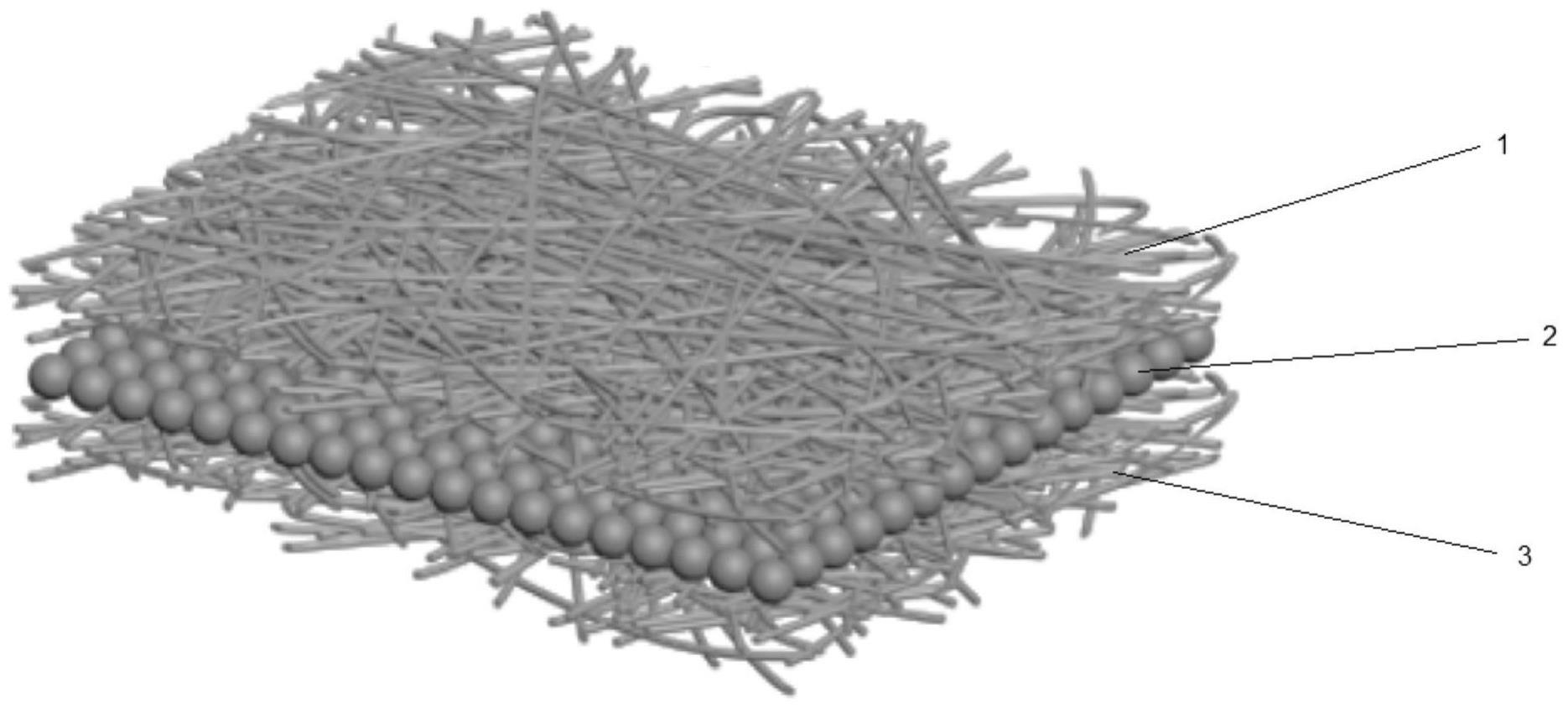
1.本发明涉及锂电池隔膜技术领域,具体涉及一种锂离子电池隔膜及其制备方法和应用。
背景技术:2.电池隔膜(battery separator),是指在电池正极和负极之间一层隔膜材料,是电池中非常关键的部分,对电池安全性和成本有直接影响,其主要作用是:隔离正、负极并使电池内的电子不能自由穿过,让电解液中的离子在正负极之间自由通过。
3.目前,已经商品化的隔膜材料主要是聚烯烃隔膜,具有较为优异的化学稳定性、耐腐蚀性能和较佳的机械性能,但是实践发现,其仍然难以兼顾如下几个问题,存在明显的顾此失彼现象:(1)电解液对其浸润性差;(2)在电池遇到特殊使用情况,温度升高时,热收缩严重,可能导致电池短路;(3)不具备在高温下关闭电池反应的功能,即使具备,也难以有效调节热关断的温度,需要重新改进隔膜,造成研发成本的极大提升。
技术实现要素:4.本发明的目的是克服现有技术的一个或多个不足,提供一种新型的锂离子电池隔膜,该新型的锂离子电池隔膜解决了现有技术中顾此失彼现象的发生。
5.本发明同时还提供了一种上述锂离子电池隔膜的制备方法。
6.本发明同时还提供了一种包含上述锂离子电池隔膜的锂离子电池。
7.为达到上述目的,本发明采用的一种技术方案是:
8.一种锂离子电池隔膜,该电池隔膜包括依次设置的第一聚偏氟乙烯膜层、聚乙烯微球层、第二聚偏氟乙烯膜层;其中,所述第一聚偏氟乙烯膜层、所述第二聚偏氟乙烯膜层分别具有微孔结构,所述聚乙烯微球层通过以聚乙烯微球分散液为原料、采用静电喷涂方式喷涂在所述第一聚偏氟乙烯膜层或所述第二聚偏氟乙烯膜层上获得,所述聚乙烯微球分散液包含聚乙烯微球、卤化锂和分散溶剂。
9.根据本发明的一些优选方面,所述卤化锂为氯化锂和/或溴化锂。
10.本发明中,卤化锂的添加不仅可以使得聚乙烯微球适合静电喷涂,而且对于后期锂离子电池而言,基本没有引入其他阳离子,有利于保证产品质量。
11.根据本发明的一些优选方面,所述分散溶剂为无水乙醇。
12.根据本发明的一些优选方面,以质量百分含量计,所述卤化锂的添加量占所述聚乙烯微球分散液的0.05%-0.3%。
13.根据本发明的一些优选方面,以质量百分含量计,所述聚乙烯微球的添加量占所述聚乙烯微球分散液的8%-12%。
14.根据本发明的一些优选且具体的方面,所述聚乙烯微球的粒径为1-5μm。
15.在本发明的一些优选实施方式中,所述聚乙烯微球分散液的制备方法包括:将聚乙烯微球、分散溶剂和卤化锂分别加入混合容器中,然后在冰水下超声,超声时间控制在
10-30min,获得分散均匀的聚乙烯微球分散液。
16.根据本发明的一些优选方面,所述第一聚偏氟乙烯膜层、所述第二聚偏氟乙烯膜层分别通过以聚偏氟乙烯纺丝液为原料、采用静电纺丝方法纺成。
17.进一步地,所述聚偏氟乙烯纺丝液为将聚偏氟乙烯分散在混合溶剂中制成,所述混合溶剂由n,n-二甲基甲酰胺和四氢呋喃构成。
18.进一步地,所述混合溶剂中,所述n,n-二甲基甲酰胺与所述四氢呋喃的投料质量比为8-10∶1。
19.根据本发明的一些优选方面,所述聚偏氟乙烯纺丝液的质量浓度为16%-20%。
20.在本发明的一些优选实施方式中,所述聚偏氟乙烯纺丝液的制备方法包括:将聚偏氟乙烯、混合溶剂分别加入混合容器中,然后在50-65℃下搅拌,搅拌时间可以为2-8h,获得聚偏氟乙烯纺丝液。
21.根据本发明的一些优选方面,所述静电喷涂方式中,其工艺参数如下:静电喷涂电压为8-12kv,喷涂推进速度为0.8-1.2ml/h,环境湿度为10%-20%,接收器滚筒转速为250-350r/min。
22.根据本发明的一些优选方面,所述静电纺丝方法中,其工艺参数如下:纺丝电压为8-12kv,纺丝推进速度为1.3-1.8ml/h,环境湿度为10%-20%,接收器滚筒转速为250-350r/min。在本发明的一些优选实施方式中,该锂离子电池隔膜的制备过程中,控制所述聚偏氟乙烯纺丝液的质量浓度为16%-20%,所述聚乙烯微球分散液中,所述聚乙烯微球的添加量占8%-12%,当所述聚偏氟乙烯纺丝液的纺丝量为4-6ml时,所述聚乙烯微球分散液的喷涂量为2-4ml,且所述聚偏氟乙烯纺丝液的纺丝量大于所述聚乙烯微球分散液的喷涂量。
23.根据本发明,该锂离子电池隔膜包括工作状态和热关断状态,当该锂离子电池隔膜处于工作状态时,所述聚乙烯微球层具有与所述微孔结构连通的孔隙通道,该锂离子电池隔膜能够导通锂离子;
24.当该锂离子电池隔膜处于热关断状态时,所述聚乙烯微球层发生软化或熔化进而呈致密结构,且存在部分渗透并堵塞在所述微孔结构中,也即封闭了聚偏氟乙烯膜层,该锂离子电池隔膜能够阻隔锂离子通过。
25.本发明提供的又一技术方案:一种上述所述的锂离子电池隔膜的制备方法,该制备方法包括:以聚偏氟乙烯纺丝液为原料、采用静电纺丝方法纺成第一聚偏氟乙烯膜层和第二聚偏氟乙烯膜层中的一个,然后以聚乙烯微球分散液为原料、采用静电喷涂方法在纺成的聚偏氟乙烯膜层上形成聚乙烯微球层,以聚偏氟乙烯纺丝液为原料、采用静电纺丝方法在聚乙烯微球层上形成第一聚偏氟乙烯膜层和第二聚偏氟乙烯膜层中的另一个。
26.本发明提供的又一技术方案:一种锂离子电池,包括正极、负极和隔膜,其中:该隔膜为上述所述的锂离子电池隔膜。
27.由于上述技术方案运用,本发明与现有技术相比具有下列优点:
28.本发明创新提供的一种新型的锂离子电池隔膜,该电池隔膜将聚乙烯微球进行特殊设计以组成聚乙烯微球分散液,使其适于静电喷涂,进而实现无粘接剂即可使得聚乙烯微球与聚偏氟乙烯膜层之间相互贴合组装,不分层,尤其是相互组装之后,不仅赋予了该电池隔膜热关断功能,而且还可以通过调整聚乙烯微球采用的不同聚乙烯材质而实现热关断温度的有效调控,无需重新改进隔膜即可在现有基础上根据需要进行选择聚乙烯微球的材
质进而调整热关断温度,极大地节约了研发成本;同时,发明人意外发现,本发明依次设置的第一聚偏氟乙烯膜层、聚乙烯微球层、第二聚偏氟乙烯膜层组装之后,在高温下仍然能够保持良好的热尺寸稳定性,进而保证在高温下电池隔膜仍然可以有效地隔断正负极,避免短路情况的发生(一般地,由于电池要求小型化,体积比较小,因此其正负极间距较小,相互邻近,如若隔膜发生较为显著的热收缩现象,容易使电池正负极发生接触而短路);而且,聚乙烯微球层位于中间,使得聚乙烯微球不易脱落。
29.此外,本发明的电池隔膜还具有高孔隙率以及高吸液率,对电解液的浸润性好,可以为锂离子的传输提供充足的空间。
附图说明
30.图1为本发明实施例中实施例1制备的锂离子电池隔膜结构示意图;
31.图2为本发明实施例中实施例1制备的锂离子电池隔膜结构示意图(热关断后);
32.图3为本发明实施例中实施例1制备的锂离子电池隔膜、市场上商业化ceglard2325隔膜和单独的pvdf纳米纤维薄膜(该pvdf纳米纤维薄膜的制备方法同实施例1)经160℃热处理20min后的示意图;
33.图4为本发明实施例中实施例1制备的锂离子电池隔膜经过110℃热处理后的断面扫描电镜图像;
34.图5为本发明实施例中采用实施例1制备的锂离子电池隔膜组装的电池在加热过程中的开路电压变化示意图;
35.图6为本发明实施例中采用实施例1制备的锂离子电池隔膜组装的电池在室温下的充放电曲线图;
36.图7为本发明实施例中采用实施例1制备的锂离子电池隔膜组装的电池在110℃下的充放电曲线图。
具体实施方式
37.以下结合具体实施例对上述方案做进一步说明;应理解,这些实施例是用于说明本发明的基本原理、主要特征和优点,而本发明不受以下实施例的范围限制;实施例中采用的实施条件可以根据具体要求做进一步调整,未注明的实施条件通常为常规实验中的条件。
38.下述实施例中未作特殊说明,所有原料均来自于商购或通过本领域的常规方法制备而得。下述中,聚偏氟乙烯粉末购自法国阿科玛公司,牌号kynar 761;聚乙烯微球购自青岛赛诺新材料有限公司。
39.实施例1
40.本实施例提供一种锂离子电池隔膜,该电池隔膜包括依次设置的第一聚偏氟乙烯膜层、聚乙烯微球层、第二聚偏氟乙烯膜层;其中,所述第一聚偏氟乙烯膜层、所述第二聚偏氟乙烯膜层分别具有微孔结构,所述聚乙烯微球层通过以聚乙烯微球分散液为原料、采用静电喷涂方式喷涂在所述第一聚偏氟乙烯膜层上获得,所述第一聚偏氟乙烯膜层、所述第二聚偏氟乙烯膜层分别通过以聚偏氟乙烯纺丝液为原料、采用静电纺丝方法纺成。
41.具体地,聚乙烯微球分散液通过如下方法制备:称取1g的聚乙烯微球于50ml的烧
杯中,再向烧杯中加入9g无水乙醇,加入0.02g的licl。在冰水下超声20min,得到分散均匀的聚乙烯微球分散液。
42.聚偏氟乙烯纺丝液通过如下方法制备:取2.21g干燥的聚偏氟乙烯粉末倒入三口瓶中,再向三口瓶中加入9g n,n-二甲基甲酰胺和1g四氢呋喃。将混合物在60℃左右充分搅拌6h,使聚偏氟乙烯粉末充分溶解于混合溶剂中,得到聚偏氟乙烯纺丝液。
43.该电池隔膜的制备方法包括:
44.通过静电纺丝的方法采用聚偏氟乙烯纺丝液制备pvdf纳米纤维膜(本例为第一聚偏氟乙烯膜层),推进速度为0.15ml/h;
45.待纺制5ml纺丝液后更换聚乙烯微球分散液,通过静电喷涂的方法向第一聚偏氟乙烯膜层表面喷涂聚乙烯微球分散液,推进速度调整为1ml/h;
46.喷涂3ml的聚乙烯微球分散液后更换聚偏氟乙烯纺丝液,最后以0.15ml/h的推进速度纺制pvdf纳米纤维膜(本例为第二聚偏氟乙烯膜层),待纺制5ml纺丝液后停止纺丝;
47.整个纺丝过程的电压约为10kv,滚筒转速约为300r/min,湿度控制在10%左右。
48.实施例2
49.本实施例提供一种锂离子电池隔膜,该电池隔膜包括依次设置的第一聚偏氟乙烯膜层、聚乙烯微球层、第二聚偏氟乙烯膜层;其中,所述第一聚偏氟乙烯膜层、所述第二聚偏氟乙烯膜层分别具有微孔结构,所述聚乙烯微球层通过以聚乙烯微球分散液为原料、采用静电喷涂方式喷涂在所述第一聚偏氟乙烯膜层上获得,所述第一聚偏氟乙烯膜层、所述第二聚偏氟乙烯膜层分别通过以聚偏氟乙烯纺丝液为原料、采用静电纺丝方法纺成。
50.具体地,聚乙烯微球分散液通过如下方法制备:称取1.2g的聚乙烯微球于50ml的烧杯中,再向烧杯中加入9g无水乙醇,加入0.02g的licl。在冰水下超声20min,得到分散均匀的聚乙烯微球分散液。
51.聚偏氟乙烯纺丝液通过如下方法制备:取2.5g干燥的聚偏氟乙烯粉末倒入三口瓶中,再向三口瓶中加入9g n,n-二甲基甲酰胺和1g四氢呋喃。将混合物在60℃左右充分搅拌6h,使聚偏氟乙烯粉末充分溶解于混合溶剂中,得到聚偏氟乙烯纺丝液。
52.该电池隔膜的制备方法包括:
53.通过静电纺丝的方法采用聚偏氟乙烯纺丝液制备pvdf纳米纤维膜(本例为第一聚偏氟乙烯膜层),推进速度为0.15ml/h;
54.待纺制5ml纺丝液后更换聚乙烯微球分散液,通过静电喷涂的方法向第一聚偏氟乙烯膜层表面喷涂聚乙烯微球分散液,推进速度调整为1ml/h;
55.喷涂3ml的聚乙烯微球分散液后更换聚偏氟乙烯纺丝液,最后以0.15ml/h的推进速度纺制pvdf纳米纤维膜(本例为第二聚偏氟乙烯膜层),待纺制5ml纺丝液后停止纺丝;
56.整个纺丝过程的电压约为10kv,滚筒转速约为300r/min,湿度控制在10%左右。所得到的纤维薄膜纤维直径较实施例1略粗,在相同时间内pe中间层较厚。
57.实施例3
58.本实施例提供一种锂离子电池隔膜,该电池隔膜包括依次设置的第一聚偏氟乙烯膜层、聚乙烯微球层、第二聚偏氟乙烯膜层;其中,所述第一聚偏氟乙烯膜层、所述第二聚偏氟乙烯膜层分别具有微孔结构,所述聚乙烯微球层通过以聚乙烯微球分散液为原料、采用静电喷涂方式喷涂在所述第一聚偏氟乙烯膜层上获得,所述第一聚偏氟乙烯膜层、所述第
二聚偏氟乙烯膜层分别通过以聚偏氟乙烯纺丝液为原料、采用静电纺丝方法纺成。
59.具体地,聚乙烯微球分散液通过如下方法制备:称取1.1g的聚乙烯微球于50ml的烧杯中,再向烧杯中加入9g无水乙醇,加入0.02g的licl。在冰水下超声20min,得到分散均匀的聚乙烯微球分散液。
60.聚偏氟乙烯纺丝液通过如下方法制备:取2.21g干燥的聚偏氟乙烯粉末倒入三口瓶中,再向三口瓶中加入9g n,n-二甲基甲酰胺和1g四氢呋喃。将混合物在60℃左右充分搅拌6h,使聚偏氟乙烯粉末充分溶解于混合溶剂中,得到聚偏氟乙烯纺丝液。
61.该电池隔膜的制备方法包括:
62.通过静电纺丝的方法采用聚偏氟乙烯纺丝液制备pvdf纳米纤维膜(本例为第一聚偏氟乙烯膜层),推进速度为0.16ml/h;
63.待纺制5ml纺丝液后更换聚乙烯微球分散液,通过静电喷涂的方法向第一聚偏氟乙烯膜层表面喷涂聚乙烯微球分散液,推进速度调整为1ml/h;
64.喷涂3ml的聚乙烯微球分散液后更换聚偏氟乙烯纺丝液,最后以0.16ml/h的推进速度纺制pvdf纳米纤维膜(本例为第二聚偏氟乙烯膜层),待纺制5ml纺丝液后停止纺丝;
65.整个纺丝过程的电压约为10kv,滚筒转速约为300r/min,湿度控制在10%左右。
66.所得到的纤维膜较实施例1纤维直径较细。
67.性能测试
68.将实施例1制备的锂离子电池隔膜、市场上商业化ceglard2325隔膜和单独的pvdf纳米纤维薄膜(该pvdf纳米纤维薄膜的制备方法同实施例1)分别进行性能测试。
69.实施例1制备的锂离子电池隔膜结构如图1所示,包括依次设置的第一聚偏氟乙烯膜层1、聚乙烯微球层2、第二聚偏氟乙烯膜层3,此时,聚乙烯微球层2具有分别与第一聚偏氟乙烯膜层1和第二聚偏氟乙烯膜层3的微孔结构连通的孔隙通道,该锂离子电池隔膜能够导通锂离子;
70.当该锂离子电池隔膜处于热关断状态时,如图2所示,聚乙烯微球层2’发生软化或熔化进而呈致密结构,且存在部分渗透并堵塞在第一聚偏氟乙烯膜层1’和第二聚偏氟乙烯膜层3’的微孔结构中,也即封闭了聚偏氟乙烯膜层,该锂离子电池隔膜能够阻隔锂离子通过,实现了热关断。
71.热尺寸稳定性试验结果参见图3所示,将celgard2325、pvdf纳米纤维薄膜、实施例1制备的锂离子电池隔膜分别在160℃热处理20min后,观察薄膜的尺寸稳定性。celgard2325的热尺寸收缩率达到了57.2%,pvdf纳米纤维薄膜的热尺寸收缩为8.3%,实施例1制备的锂离子电池隔膜的热尺寸收缩为11.0%,说明实施例1制备的锂离子电池隔膜具有较好的热尺寸稳定性,尤其是在pvdf纳米纤维薄膜上增加了会热熔的聚乙烯微球之后,对于热尺寸收缩量影响很小,符合使用需求。
72.图4为实施例1制备的锂离子电池隔膜经过110℃热处理后的断面扫描电镜图像。从图中可以看到清晰的三层结构,存在较清晰的界线,在中间层的聚乙烯微球熔化后,中间层的聚乙烯会渗透到上下层的聚偏氟乙烯膜层中,可以完全地堵塞纤维膜的微孔结构。
73.按照正极壳/正极/隔膜/负极/钢片/弹片/负极壳的顺序进行纽扣全电池的组装,其中正极材料为三元镍钴锰(ncm523),负极材料为石墨负极。
74.图5为采用实施例1制备的锂离子电池隔膜组装的电池在加热过程中的开路电压
变化情况,可以看出,室温下电池的开路电压保持在3.15v左右,将电池放入110℃的恒温加热装置中,电池电压发生了一定幅度的下降,然后在某个阶段突然在大概16s的时间内骤降到0。这表明,在电池工作的过程中,实施例1制备的锂离子电池隔膜可以迅速做出热响应。当电池内部突然升温到聚乙烯微球的熔融温度时,实施例1制备的锂离子电池隔膜的聚乙烯微球层可以快速熔化,迅速堵塞纤维膜的微孔结构,达到阻止锂离子传输的效果,使得电压迅速下降为0。
75.将组装好的电池分别进行室温下和100℃的充放电,测试结果如图6-7所示;
76.在充放电工步之间设置1min的搁置时间,在完成恒流恒压充电步骤后,在电池搁置期间将电池放入110℃恒温加热装置中放电,测试电池在110℃下放电容量;
77.在室温下电池可以进行正常的充放电,显示出了良好的放电容量,为162.47mah/g;
78.但是当电池在110℃下进行放电时,电池的放电容量下降到了0.03mah/g,不能进行正常的放电。这是由于当电池内部的温度达到110℃时,聚乙烯微球层的聚乙烯微球快速熔化并形成了致密层,使得隔膜原有的孔隙失效。这表明本发明的锂离子电池隔膜可以在110℃下有效地关断电池的反应。
79.此外,本发明还对实施例1制备的锂离子电池隔膜进行了孔隙率和吸液率的测试,结果表明:其具有68.8%的高孔隙率,以及484%的高吸液率。
80.孔隙率测试
81.使用正丁醇吸液法对隔膜的孔隙率进行测试。将隔膜制成2
×
2cm2的正方形。将待测隔膜放置于正丁醇中,隔膜需完全浸泡在正丁醇液体中4h。将浸泡完的隔膜夹在两片滤纸之间,使用20g的砝码压10s,目的是吸收掉隔膜表面的正丁醇,称重,记为m1。根据公式(1)计算孔隙率。
82.孔隙率(%)=(m
1-m0)/ρ
bvꢀꢀꢀ
(1);
83.其中:m0为隔膜的质量,m1为浸泡正丁醇后隔膜的质量,ρb为正丁醇的密度,v为隔膜体积。
84.吸液率测试
85.使用称重法对隔膜进行吸液率测试。将干燥的待测隔膜在足量的电解液中充分浸泡,每10min取出一次,并用滤纸吸掉隔膜表面的电解液,称重,记为mi。测量至隔膜的质量不再发生变化,并根据公式(2-2)计算吸液率。
86.吸液率(%)=[(m
i-m0)/m0]
×
100%
ꢀꢀꢀ
(2-2);
[0087]
其中:m0为隔膜的干重,mi为隔膜的湿重。
[0088]
上述实施例只为说明本发明的技术构思及特点,其目的在于让熟悉此项技术的人士能够了解本发明的内容并据以实施,并不能以此限制本发明的保护范围。凡根据本发明精神实质所作的等效变化或修饰,都应涵盖在本发明的保护范围之内。
[0089]
在本文中所披露的范围的端点和任何值都不限于该精确的范围或值,这些范围或值应当理解为包含接近这些范围或值的值。对于数值范围来说,各个范围的端点值之间、各个范围的端点值和单独的点值之间,以及单独的点值之间可以彼此组合而得到一个或多个新的数值范围,这些数值范围应被视为在本文中具体公开。