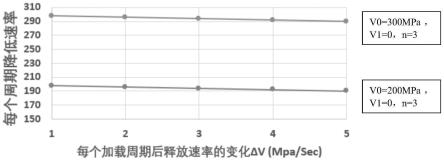
1.本发明涉及半导体器件的制造技术领域,尤其涉及一种采用静态高压在硅上形成致密氧化层的方法。
背景技术:2.在半导体器件、功率器件与大规模及超大规模集成电路的制造工艺,尤其是集成电路模块的制造工艺中,栅极薄膜与硅结构过渡层的厚度和致密性,以及这些参数在结构表面上分布均匀度是一个需要持续改进的问题。
3.目前常用的改进半导体集成电路中栅极薄膜与硅结构过渡层的厚度和致密性,以及这些参数在结构表面上分布均匀度的方法,主要有两种,一种是高温下的干燥氧气流中对硅片进行热氧化来生产结构硅-二氧化硅形成氧化层,另一种是通过在干燥-湿-干燥氧气中连续氧化硅来获得薄膜形成氧化层。
4.高温下的干燥氧气流中对硅片进行热氧化来生产结构硅-二氧化硅形成氧化层;该方法的缺点是膜的生长速率低。因此,在实践中,通过在干燥-湿-干燥氧气中连续氧化硅来获得薄膜形成氧化层。然而,这样的膜更加有缺陷,特别是具有增加的微孔密度。微孔对二氧化硅的介电和掩蔽性能产生负面影响,并降低其机械强度。其结果是降低了包含这种膜元件的成品率。
5.因此亟待研究一种在硅上形成厚度和致密性均能得到改善的氧化层的方法。
技术实现要素:6.基于背景技术存在的问题,本发明提供了一种采用静态高压在硅上形成致密氧化层的方法。
7.静水压力是均质流体作用于一个物体上的压力。这是一种全方位的力,并均匀地施向物体表面的各个部位。静水压力增大,会使受力物体的体积缩小,但不会改变其形状。
8.本发明的目的提供了一种采用静态高压在硅上形成致密氧化层的方法,对硅上沉积二氧化硅膜或硅上沉积二氧化硅膜与氮化硅双重膜用静水压力进行循环处理,大大降低了氧化层与硅之间过渡层的厚度,改善了氧化层的致密性和孔隙率,以及这些参数在结构表面上分布均匀度,显著降低了氧化层与硅结构的平均机械应力,并同时提高包含这种氧化层元件的成品率。
9.本发明通过以下技术方案实施:
10.一种采用静态高压在硅上形成致密氧化层的方法,包括以下步骤:
11.s01、在硅上形成氧化层;
12.s02、对氧化层用静水压力进行循环处理。
13.进一步地,所述氧化层为硅上沉积二氧化硅膜或硅上沉积二氧化硅膜与氮化硅双重膜。
14.进一步地,所述静水压力处理时间为3
×
10
3-7
×
103s,当静水压力处理时间少于3
×
103s时,膜中的松弛过程没有足够的发生时间;当静水压力处理时间超过7
×
103s时,薄膜已获得了最佳的效果,特性几乎没有变化,过长的时间会产生时间与能量的非生产性损失。
15.进一步地,所述用静水压力进行循环处理为,将作用在氧化层上的静水压力以一定的提升速率从大气压升到给定压力,然后将静水压力以一定的压力释放速率从给定压力释放至大气压,如此完成一次恢复静水压力和释放静水压力为一个循环周期。
16.本发明中,由于氧化层外静水压力周期性变化的影响,氧化层中薄膜发生逐空位的扩散的细孔溶解。静水压力从大气压缓慢升高到给定水平,整个过程中压力提高速率保持恒定,可以抑制不连续的过程和避免随着拉伸应力的增加造成膜破裂。
17.进一步地,所述提升速率为1-5mpa/s。
18.进一步地,所述给定压力为700-900mpa。
19.进一步地,所述压力释放速率v由以下公式确定:
20.v=v
0-(n-1)cδv+v121.其中,v0为170-300mpa/s,是第一个加载周期后的压力释放速率;
22.c是压力系数,与压力介质的种类相关;
23.δv为1-5mpa/s,是每个加载周期后的压力释放速率的变化;
24.n为1、2、3
…
是下一个加载周期的序号;
[0025]v1
是与薄膜层数相关的附加速率,若薄膜为二氧化硅膜时,v1=0,若薄膜为二氧化硅与氮化硅双重膜时,v1的范围与多层薄膜的特性相关,本发明中选用低压等离子体增强化学气相淀积薄膜,v1为50-150mpa/s。
[0026]
在第一循环中静水压力急剧下降允许保持膜中本征点缺陷的不平衡浓度,这是造成氧化膜致密化的原因。随着膜变得更加致密并且其对外部机械负载的抵抗力的增加,即对静水压力变化的抵抗力的增加,在结构卸载期间不连续的可能会增加。为了避免这种情况,卸载速率逐周期地逐渐降低,使得在压力从给定压力降低至大气压水平的过程中,薄膜中发生了松弛过程。随着循环次数增加,压力释放速率的降低也有助于薄膜中点缺陷子系统中更完全的恢复平衡,为此,由于缺陷在薄膜中溶解而使它们在薄膜中的总浓度下降,导致其到漏极的扩散路径的增加。
[0027]
进一步地,所述静水压力通过压力控制系统控制。
[0028]
进一步地,所述压力控制系统执行如下操作:
[0029]
a、获取静水压力强度的流量曲线,将每个循环的流量曲线分成6-9段,计算各段施加静水压力的流量的峰值,每段流量曲线的流量峰值为该段流量曲线的各流量峰值的最大值,再计算每次流量曲线的流量基准值;
[0030]
b、确定控制系统的前馈系数,计算每个循环的流量曲线的前馈输出值,其计算公式如下:
[0031]
前馈系数为:
[0032][0033]
前馈输出值为:
[0034]ri
=ti×
mi[0035]
将前馈系数带入得到:
[0036][0037]
其中,ri为第i段流量前馈输出值;ti为前馈系数;i为第i段曲线,n为每次循环流量曲线总段数;b为控制输出比例系数的基准,取66%,q为实时控制流量输出,mi为第i段流量曲线的流量基准值;
[0038]
c、计算出每次压力循环中各段流量曲线的控制输出值,其计算公式如下:
[0039]rout-i
=(αr
pid
+βri)
×2[0040]
其中,r
out-i
为第i段流量的实际控制输出量,r
pid
为控制器输出控制量,α、β分别为系数,取α为0.5c,则β为1-0.5c,其中c为pid控制器的延迟系数,其中,0.9≤c≤1;
[0041]
d、根据各段流量曲线的控制输出值进行静水压力试验。
[0042]
本发明的有益效果:
[0043]
(1)本发明的静态高压在硅上形成致密氧化层的方法,可以改善硅上氧化层的致密性和孔隙率,以及这些参数再结构表面上分布均匀度,降低氧化层与硅结构的平均机械应力,从而改善半导体器件的可靠性与产品性能。
[0044]
(2)本发明的静态高压在硅上形成致密氧化层的方法,不仅可以用于改善硅基的半导体器件与集成电路的绝缘膜的致密性,也可以推广应用于改善化合物半导体功率器件与集成电路的绝缘膜的致密性与粘附性,提高元件的可靠性。
附图说明
[0045]
图1为从给定压力释放到大气压力的流程以每个周期降低速率与每个加载周期后的压力释放速率变化的关系(c=1,v1=0,v0分别为200mpa/sec和300mpa/sec);
[0046]
图2为从给定压力释放到大气压力的流程的每个周期降低速率与每个加载周期后的压力释放速率变化的关系(c=1,v0=300mpa/sec,v1分别为0和100mpa/sec);
[0047]
图3为二氧化硅(sio2)与硅(si)交界处过渡层的厚度与流体静压力的关系。
具体实施方式
[0048]
下面结合具体实施例对本发明的技术方案做进一步的详述,但本发明的保护范围并不仅限于以下实施例。
[0049]
一种在硅上形成氧化层的方法,包括在硅片上沉积二氧化硅膜并用静水压力进行循环处理,包括采用二氧化硅膜加上氮化硅膜进行静水压力循环处理,其特征在于对其施加的(3-7)
×
103sec的压力处理,定期提高压力,以1-5mpa/s的速率从大气压到700-900mpa的压力,然后下降到大气压,每个循环的压力释放率v由下式确定:
[0050]
v=vo-(n-1)cδv+v1eq
ꢀꢀ
(1)
[0051]
式中
[0052]
vo为170-300mpa/s,是第一个循环后的压力释放率;
[0053]
c为压力系数,与压力介质相关;
[0054]
δv=1-5mpa/s,是每个加载周期后的放电速率变化;
[0055]
n为1,2,3,是下一个加载周期的序号。
[0056]v1
为与薄膜层数相关的附加速率;
[0057]
薄膜为二氧化硅膜时,v1=0;
[0058]
薄膜为二氧化硅膜与氮化硅双重膜时,v1的范围与多层薄膜的特性相关,如对于低压等离子体增强化学气相淀积(lp-pecvd)薄膜,在50-150mpa/sec范围。
[0059]
这改善了氧化硅膜的结构(其连续性)并提高了其成品率。详见图3。
[0060]
由图1可以看出,当流体介质为纯水(h2o),c=1,v1=0(仅有二氧化硅薄膜时),从给定压力释放到大气压力的每个周期降低速率与第一个循环后的压力释放率v0强相关,而与每个加载周期后的压力释放速率的变化弱相关,在加高压后缓慢地释放压力对保证薄膜的质量十分重要。
[0061]
图2给出了从给定压力释放到大气压力的流程的每个周期降低速率与每个加载周期后的压力释放速率变化的关系。从图2可以看出,从给定压力释放到大气压力的流程的每个周期降低速率与薄膜层数相关的附加速率v1有较强的对应关系,当采用二氧化硅与氮化硅膜的双层结构时,由于用低压等离子体增强化学气相淀积(lp-pecvd)工艺生长的氮化硅膜具有压缩性的张量值,当调整用(lp-pecvd)工艺生长的氮化硅膜的厚度与工艺参数使v1=100时,每个周期压力降低速率将减少30%以上,这将进一步降低二氧化硅薄膜在压力降低时压力差,减低二氧化硅薄膜与硅界面的应力,从而改进薄膜质量。
[0062]
方法一:在硅上生长二氧化硅薄膜然后进行静水压力处理:
[0063]
将该薄膜结构在700-900mpa范围内的静水压力下处理(3-7)
×
103秒(sec)。在处理过程中,定期提升(例如,在液压设备,其中去离子水与乙醇或异丙醇的50%混合物用作压力传递液)和降低工作腔中的压力。根据线性定律eq(1),在每个循环中以5-10mpa/s的速率进行压力升高,并且以循环比循环的降低速率进行释放。在通过压力处理结构之后,将其转移到随后的技术工艺中以形成半导体器件。
[0064]
二氧化硅膜的致密化在该方法起到积极的作用,该膜中,在外部周期性变化的压力的影响下发生逐空位的扩散的细孔溶解。压力从大气压缓慢升高到给定水平(在整个处理过程中压力提高速率保持恒定)可抑制不连续的过程和避免随着拉伸应力的增加造成膜破裂。在薄膜中的破裂是由于硅(100gpa)和二氧化硅(38gpa)的压缩模量不同而造成。
[0065]
另一方面,在第一加工循环中压力的急剧下降允许保持膜中本征点缺陷的不平衡浓度,这是造成致密化的原因。随着膜变得更致密并且其对外部机械负载的抵抗力的增加,即对静水压力变化的抵抗力的增加,在结构卸载期间不连续的可能性会增加。为了避免这种情况,卸载速率逐周期地逐渐降低,使得在压力从工作压力降低至大气压水平的过程中,薄膜中发生了松弛过程。随着循环次数的增加,压力释放速率的降低也有助于薄膜中点缺陷子系统中更完全的恢复平衡,为此,随着时间的流逝,由于缺陷在薄膜中溶解而使它们在薄膜中的总浓度下降,导致其到漏极的扩散路径的增加。
[0066]
方法二:在硅上生长二氧化硅薄膜然后在二氧化硅膜上淀积氮化硅薄膜,之后再进行静水压力处理:
[0067]
根据该方法对薄膜结构进行的处理方式是在厚度为600-650微米(μm)的(i00)或(111)晶向硅晶片上先采用干氧与湿氧方法在1120-1200℃的温度下热氧化而获得的二氧化硅薄膜,然后用低压等离子体增强化学气相淀积(lp-pecvd)的方法生长厚度为300至1000埃的氮化硅薄膜。通过控制lp-pecvd工艺气体的组成,如含氢量的多少,以及氮化
硅薄膜的厚度来控制由氮化硅薄膜对二氧化硅薄膜以及二氧化硅与硅的界面所产生的附加压力,该压力的范围500至1000兆帕(mpa)之间。
[0068]
二氧化硅膜的厚度为100埃至0.1微米(μm),生长模式对薄膜质量的影响可通过在自动椭圆偏振仪上测量的折射率和通过电子照相法记录的细孔的浓度来评估。未经处理的晶片的一半作为校对样品。对于每种处理方式,5以上所述个样品经过静水压降低为准。压力处理之前的批次结构参数的平均值为:
[0069]-二氧化硅热膜中细孔的浓度为97
±
9孔/cm2;
[0070]-二氧化硅热膜折射率分别为1.42
±
0.05。
[0071]
由对以上所述样品进行静水压力实验的测试结果可以归纳出以下计算公式:
[0072]
1二氧化硅薄膜细孔浓度的相对变化率与液体压力提升速率的关系
[0073]
p=-0.0086
×v2
+0.1338
×
v+0.1801eq
ꢀꢀ
(1)
[0074]
式中:
[0075]
p:二氧化硅薄膜细孔浓度的相对变化率;
[0076]
v:液体压力提升速率,兆帕/秒(mpa/sec);
[0077]
由公式(1)可以看出随着液体压力提升速率的提高,二氧化硅薄膜细孔浓度的相对变化率会显现线性上升趋势,而后趋于平缓。
[0078]
2二氧化硅薄膜细孔浓度的相对变化率与每个加载周期后液体压力后释放速率的关系
[0079]
p=-0.0952
×
t2+0.4352
×
t+0.0314eq
ꢀꢀ
(2)
[0080]
式中:
[0081]
p:二氧化硅薄膜细孔浓度的相对变化率;
[0082]
t:每个加载周期后液体压力释放速率,兆帕/秒(mpa/sec);
[0083]
由公式(2)可以看出随着液体压力提升速率的提高,二氧化硅薄膜细孔浓度的相对变化率会显现线性上升趋势,而后趋于平缓。
[0084]
将该薄膜结构在700-900mpa范围内的静水压力下处理(3-7)
×
103秒(sec)。
[0085]
实验结果显示在7
×
103秒(second)的处理时长下,压力值从大气压到800mpa的压力升高速率所引起的细孔浓度的相对变化由0.2线性上升到0.65,然后在3-7mpa/sec的区间趋于平缓。因此,在3-5mpa/s的提升速率下可获得最佳的效果。第一次加载周期后的压力释放率为300mpa/sec,在随后的循环中压力释放率由公式eq(2)确定。
[0086]
实验结果显示了当压力值在从700mpa到大气水平的第一个加载周期后的压力释放速率会引起二氧化硅薄膜的折射率的变化。随着压力释放速率的增加,折射率同时增加并接近1.44的水平,并在压力释放速率为300mpa/s时达到最大值。
[0087]
实验结果表明在每个随后的压力处理循环中,细孔浓度与压力释放速率的各种增量的相对降低的依赖性,提升速率最佳范围为1-5mpa/s。静水压力持续时间为(3-7)
×
103秒(second),具体条件由以下情况决定:当暴露时间少于3
×
103秒(second)时,膜中的松弛过程没有足够的发生时间;当暴露时间超过7
×
103秒(second)时,薄膜的特性几乎没有变化(获得了最佳的效果),过长的时间会产生时间与能量的非生产性损失。
[0088]
根据上述方法发现的硅-二氧化硅结构的处理模式的效率已经通过实际测试的结果所证实。
[0089]
具体实施的例子
[0090]
对五批在1180c温度下的具有(i00)晶向并且通过干氧与湿氧中热氧化获得的厚度为1000-1100埃的二氧化硅薄膜的单晶硅的结构进行了静水压力处理(压力为700mpa,压力上升速率25mpa/s,持续时间7200s)。实验结果表明,当流体静压力在700至900兆帕/秒(mpa/sec)范围内,处理时间为3000至7000秒时,二氧化硅薄膜的细孔浓度变化很小,在每立方厘米25至35细孔的范围。但是当流体静压力低于700兆帕/秒(mpa/sec),或是流体静压力处理时间少于3000秒时,二氧化硅薄膜的细孔浓度会逐步增加。
[0091]
在以最佳模式处理的结构上,通过椭圆偏振法测量衬底与二氧化硅化学计量组成的薄膜之间的过渡层的厚度(过渡层厚会引起表面态密度增加,直接影响器件性能),以及使用三晶体x-射线光谱仪确定样品薄膜中残留机械应力的值。连同所有参数一起,通过在每个样品表面进行12个点参数测量参数的平均值,同时确定参数在结构中的分布。测量结果示于图3。
[0092]
综上所述,从实施例的数据中观察到本发明的方法可以根据细孔浓度的相对变化率与液体压力提升速率的关系确定最佳压力提升速率,根据细孔浓度的相对变化率与循环加载周期液体压力释放速率的关系可以确定最佳压力释放速率。本发明所采用的用循环静态高压在硅上形成致密氧化层的方法,不仅可以用于改善硅基的半导体器件与集成电路的绝缘膜的致密性,也可以推广应用于改善化合物半导体功率器件与集成电路的绝缘膜的致密性与粘附性,提高器件的可靠性。可以显着降低二氧化硅膜的平均机械应力,过渡层的厚度(测量方法的灵敏度极限)和孔隙率,以及这些参数在结构表面上的分布,从而改善半导体器件的可靠性与产品性能。
[0093]
最后应说明的是:以上所述实施例仅表达了本发明的几种实施方式,并不用以限制本发明创造,对于本领域的普通技术人员来说,在不脱离本发明构思的前提下,所作的任何修改、等同替换、改进等,均应包含在本发明创造的保护范围之内。因此,本发明专利的保护范围应以所附权利要求为准。