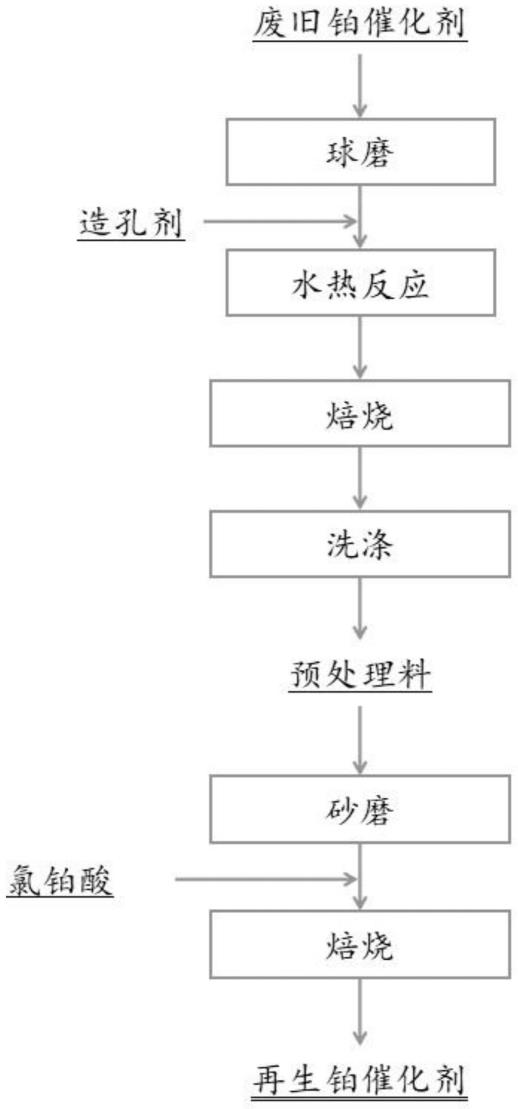
1.本发明涉及氢燃料电池关键材料回收技术领域,具体涉及一种废旧铂催化剂的回收再生方法。
背景技术:2.氢燃料电池由电堆、氢气供给循环系统、空气供给系统、水热管理系统、电控系统等组成。其中,电堆又由双极板、质子交换膜、催化剂和气体扩散层等组成。质子交换膜是氢燃料电池的核心元件,目前主要是全氟磺酸膜。催化剂是燃料电池的关键材料之一,目前主要成份是pt/c。催化剂通过粘接剂粘结在全氟磺酸膜上,再辅以气体扩散层又被称为膜电极。
3.然而,在氢燃料电池服役时,铂因颗粒粒径小(~30nm)易发生团聚、表面积炭、中毒等导致催化剂失活、膜电极失效,致使氢燃料电池退役。退役氢燃料电池的核心组件——膜电极,不仅含铂,还含有f、s、c等多种污染源。若处理不当,将产生环境污染、资源浪费等危害。因此,氢燃料电池废旧组件特别是稀有金属铂的回收再生势在必行。
4.目前,国内外回收铂的技术多以湿法冶金为主,即采用酸、氧化剂共同作用使金属铂溶解,再进行除杂、沉淀等一系列工序回收铂。如专利cn1114362a 公开了一种从含铂的催化剂中回收铂的方法。该方法以γ-al2o3或sio2-al2o3 等为载体的铂系列催化剂为原料,经焙烧、氧化浸出、阴离子分离、提纯后得到高纯度海绵铂。专利cn100348749c公开了一种从废催化剂回收铂和铼的方法,该方法以含氧化铝的多孔载体上的含铂和铼的废催化剂为原料,经过碱溶液浸出、还原剂还原、过滤、阴离子树脂吸附等方法高效率的回收铂。专利 200910133892.1公开了一种从纳米结构的燃料电池催化剂回收铂的方法,该方法通过将纳米结构的燃料电池催化剂材料暴露在酸性氧化溶液中,将铂金属颗粒氧化溶解,再转化为铂盐浸出,煅烧得到金属铂。其酸性氧化溶液通常包括至少一种酸和至少一种氧化剂,养护剂可以是如过氧化氢等。专利201711313215.9公开了废旧燃料电池的回收利用方法,该法将废旧燃料电池拆解获得膜电极,然后浸入有机溶液中去除膜状物。最后,将滤渣在空气中焙烧、溶解获得铂金属。
5.综合有关的文献报导,虽然用以上的方法可以实现铂的回收,但是湿法冶金技术酸使用量大、操作步骤多、回收产品多为铂金属,含碳组分则转化为co2 或废渣。直接在氧气中焙烧的方式获得的产品也是铂金属,含碳组份则转化为 co2,增大了碳排放;铂金属需经溶解、浸渍、焙烧等工艺方能获得铂基催化剂,复杂的工艺流程无疑增大了催化剂的制备成本。
技术实现要素:6.针对上述技术问题,本发明以实际工业生产和废旧材料资源化再生为出发点,采用液相研磨与固相焙烧相结合的方式,合理引入并去除造孔因子,使加入铂离子进入新造孔结构中并还原形成铂原子,从而实现废旧铂催化剂的再生利用。此外,本发明所述废旧材
料中的粘接剂等含碳有机物,在保护气氛下均以无定型炭的形式存在;含有的碳材料仍保持原来状态。焙烧前后,经球磨和砂磨后,降低不同材料颗粒之间的界面结合力,易于再生催化剂的制备和催化性能的发挥。整个工艺流程短且易于工业化生产,实现了经济、环保回收。
7.针对上述目的,本发明实施例提供了一种废旧铂催化剂的回收再生方法,所述方法包括以下步骤:
8.s1:将废旧铂催化剂进行球磨,加入造孔剂后放入反应釜中进行水热反应,烘干、焙烧、洗涤去除造孔剂,获得预处理料。
9.s2:将预处理料砂磨,获得砂磨浆料;向砂磨浆料中加入氯铂酸、焙烧,获得再生铂催化剂。
10.进一步地,所述的一种废旧铂催化剂的回收再生方法,所述废旧铂催化剂来源于铂碳催化剂与质子交换膜混合时产生的废浆料、生产过程中产生的废膜电极、废旧氢燃料电池中的一种或两种以上的组合。
11.进一步地,所述的一种废旧铂催化剂的回收再生方法,所述球磨溶剂为水、甲醇、乙醇、丙醇、丁醇、烯醇及其上述醇的衍生物中的一种或两种以上的混合。
12.进一步地,所述的一种废旧铂催化剂的回收再生方法,所述造孔剂为金属盐、氧化物、氢氧化物中的一种,优选钠、钾、铝、锰、镁中的盐、氧化物、氢氧化物中的一种;进一步优选nacl、kcl、al2o3、al(oh)3、alcl3、mgcl2、 al(no3)3、al2(so4)3、mno2、mnco3中的一种。
13.进一步地,所述的一种废旧铂催化剂的回收再生方法,所述al2o3、mno2、 mnco3优选纳米级。
14.进一步地,所述的一种废旧铂催化剂的回收再生方法,所述水热反应温度为150-240℃,反应时间为8-26h。
15.进一步地,所述的一种废旧铂催化剂的回收再生方法,所述所述焙烧温度为300-800℃,焙烧时间为0.5-10h,焙烧气氛为氩气、氮气、氢气、氦气中的一种或两种以上的组合。
16.进一步地,所述的一种废旧铂催化剂的回收再生方法,所述洗涤溶剂为水、酸中的一种;酸优选hcl、h2so4、hno3、h3po4中的一种。
17.进一步地,所述的一种废旧铂催化剂的回收再生方法,所述砂磨溶剂为水、甲醇、乙醇、丙醇、丁醇、烯醇中的一种或两种以上的混合,砂磨转速为 2000-20000r/min,砂磨时间为1-12h。
18.进一步地,所述的一种废旧铂催化剂的回收再生方法,所述砂磨浆料固含量为5-40%。
19.进一步地,所述的一种废旧铂催化剂的回收再生方法,所述氯铂酸的加入量为砂磨浆料固含量的0.01-10%。
20.有益效果:本发明实现了无需经溶解、浸渍、焙烧等工艺就能将废旧铂催化剂中铂金属再生利用,整个工艺无废水废酸产生。仅通过加入缺失的铂元素即可实现废旧材料再生利用并且保证催化剂性能完善,其工艺流程短,经济附加值高;加入造孔剂使废料中的炭形成多孔结构,给新加入的铂提供存储空间。而且将废旧材料中的碳材料及含碳有机组份通过焙烧、造孔的方式转化为碳载体,实现废料中的c循环使用,降低了co2或废渣的排放,
实现了固废资源化再生,环境友好。
附图说明
21.图1为本发明一种废旧铂催化剂的回收再生方法工艺流程;
22.图2为实施例1获得的再生铂/碳催化剂的sem;
23.图3为实施例1获得再生铂/碳催化剂的析氢lsv图;
24.图4为实施例6获得再生铂/碳催化剂的析氢lsv图。
具体实施方式
25.为了便于理解本发明,下面将参照相关附图对本发明进行更全面的描述。附图中给出了本发明的较佳实施方式。但是,本发明可以以许多不同的形式来实现,并不限于本文所描述的实施方式。相反地,提供这些实施方式的目的是使对本发明的公开内容理解的更加透彻全面。
26.需要说明的是,当元件被称为“固定于”另一个元件,它可以直接在另一个元件上或者也可以存在居中的元件。当一个元件被认为是“连接”另一个元件,它可以是直接连接到另一个元件或者可能同时存在居中元件。本文所使用的术语“垂直的”、“水平的”、“左”、“右”以及类似的表述只是为了说明的目的,并不表示是唯一的实施方式。
27.本发明实施例提供了一种废旧铂催化剂的回收再生方法,所述方法包括以下步骤:
28.s1:将废旧铂催化剂进行球磨,加入造孔剂后放入反应釜中进行水热反应,烘干、焙烧、洗涤去除造孔剂,获得预处理料。
29.s2:将预处理料砂磨,获得砂磨浆料;向砂磨浆料中加入氯铂酸、焙烧,获得再生铂催化剂。
30.进一步地,所述的一种废旧铂催化剂的回收再生方法,所述废旧铂催化剂来源于铂碳催化剂与质子交换膜混合时产生的废浆料、生产过程中产生的废膜电极、废旧氢燃料电池中的一种或两种以上的组合。
31.进一步地,所述的一种废旧铂催化剂的回收再生方法,所述球磨溶剂为水、甲醇、乙醇、丙醇、丁醇、烯醇及其上述醇的衍生物中的一种或两种以上的混合。
32.进一步地,所述的一种废旧铂催化剂的回收再生方法,所述造孔剂为金属盐、氧化物、氢氧化物中的一种,优选钠、钾、铝、锰、镁中的盐、氧化物、氢氧化物中的一种;进一步优选nacl、kcl、al2o3、al(oh)3、alcl3、mgcl2、 al(no3)3、al2(so4)3、mno2、mnco3中的一种。
33.进一步地,所述的一种废旧铂催化剂的回收再生方法,所述al2o3、mno2、 mnco3优选纳米级。
34.进一步地,所述的一种废旧铂催化剂的回收再生方法,所述水热反应温度为150-240℃,反应时间为8-26h。
35.进一步地,所述的一种废旧铂催化剂的回收再生方法,所述所述焙烧温度为300-800℃,焙烧时间为0.5-10h,焙烧气氛为氩气、氮气、氢气、氦气中的一种或两种以上的组合。
36.进一步地,所述的一种废旧铂催化剂的回收再生方法,所述洗涤溶剂为水、酸中的
一种;酸优选hcl、h2so4、hno3、h3po4中的一种。
37.进一步地,所述的一种废旧铂催化剂的回收再生方法,所述砂磨溶剂为水、甲醇、乙醇、丙醇、丁醇、烯醇中的一种或两种以上的混合,砂磨转速为 2000-20000r/min,砂磨时间为1-12h。
38.进一步地,所述的一种废旧铂催化剂的回收再生方法,所述砂磨浆料固含量为5-40%。
39.进一步地,所述的一种废旧铂催化剂的回收再生方法,所述氯铂酸的加入量为砂磨浆料固含量的0.01-10%。
40.除非另有特别说明,本发明中用到的各种原材料、试剂、仪器和设备等均可通过市场购买得到或者可通过现有方法制备得到。
41.实施例1
42.将废旧氢燃料电池进行拆解、分离得到废旧膜电极,按照水与甲醇的质量比为1:1混合后加入废膜电极中,过滤、烘干,再放入球磨罐中球磨6h。然后取出并加入al(oh)3后放置于反应釜中,加热,在240℃下保温8h,过滤,烘干,获得待焙烧料。将待焙烧料放入管式炉中,在高纯氩气氛下,300℃保温6h,获得焙烧料。将焙烧料放入hcl溶液中,搅拌,过滤,烘干。然后以水为溶剂,配置固含量为40%的浆料在转速为20000r/min下砂磨,获得待焙烧砂磨浆料。向待焙烧砂磨浆料中加入砂磨浆料固含量的10%的氯铂酸,焙烧获得再生铂催化剂。
43.实施例2
44.将铂碳催化剂与质子交换膜混合时产生的废浆料加水,搅拌、过滤、烘干,再放入球磨罐中球磨2h。然后取出并加入nacl后放置于反应釜中,加热,在 220℃下保温10h,过滤,烘干,获得待焙烧料。将待焙烧料放入管式炉中,在高纯氩气氛下,400℃保温2h,获得焙烧料。将焙烧料放入水中,搅拌,过滤,烘干。然后以水和甲醇为混合溶剂,配置固含量为25%的浆料在转速为 12000r/min下砂磨,获得待焙烧砂磨浆料。向待焙烧砂磨浆料中加入砂磨浆料固含量的0.01%的氯铂酸,焙烧获得再生铂催化剂。
45.实施例3
46.将废旧氢燃料电池进行拆解、分离得到废旧膜电极,按照水与无水乙醇的质量比为5:1混合后加入废膜电极中,过滤、烘干,再放入球磨罐中球磨10h。然后取出并加入mnco3后放置于反应釜中,加热,在200℃下保温12h,过滤,烘干,获得待焙烧料。将待焙烧料放入管式炉中,在高纯氩气氛下,400℃保温 1h,获得焙烧料。将焙烧料放入h3po4溶液中,搅拌、过滤、烘干。然后以丁醇为溶剂,配置固含量为30%的浆料在转速为13000r/min下砂磨,获得待焙烧砂磨浆料。向待焙烧砂磨浆料中加入砂磨浆料固含量的8%的氯铂酸,焙烧获得再生铂催化剂。
47.实施例4
48.将铂碳催化剂与质子交换膜混合时产生的废浆料加乙醇,搅拌、过滤、烘干,再放入球磨罐中球磨2h。然后取出并加入al(oh)3后放置于反应釜中,加热,在180℃下保温20h,过滤,烘干,获得待焙烧料。将待焙烧料放入管式炉中,在高纯氩气氛下,300℃保温10h,获得焙烧料。将焙烧料放入h2so4溶液中,搅拌、过滤、烘干。然后以烯醇为溶剂,配置固含量为15%的浆料在转速为 8000r/min下砂磨,获得待焙烧砂磨浆料。向待焙烧砂磨浆料中加入
砂磨浆料固含量的0.5%的氯铂酸,焙烧获得再生铂催化剂。
49.实施例5
50.将生产过程中产生的废膜电极剪碎,按丁醇与剪碎的废膜电极混合,搅拌、过滤、烘干,再放入球磨罐中球磨1h。然后取出并加入al(oh)3后放置于反应釜中,加热,在150℃下保温26h,过滤,烘干,获得待焙烧料。将待焙烧料放入管式炉中,在高纯氩气氛下,350℃保温3h,获得焙烧料。将焙烧料放入h2so4 溶液中,搅拌、过滤、烘干。然后以乙醇为溶剂,配置固含量为20%的浆料在转速为10000r/min下砂磨,获得待焙烧砂磨浆料。向待焙烧砂磨浆料中加入砂磨浆料固含量的4%的氯铂酸,焙烧获得再生铂催化剂。
51.实施例6
52.将来自于废旧氢燃料电池废膜电极剪碎,按照水与无水乙醇的质量比为1:2 混合后加入剪碎的废膜电极中,过滤、烘干,获得待焙烧料。将待焙烧料放入管式炉中,在高纯氩气氛下,800℃保温0.5h,获得焙烧料。将焙烧料放入球磨罐中球磨2h,然后取出并加入alcl3后放置于反应釜中,加热,在200℃下保温8h,过滤,烘干,然后放入h2o中,搅拌、过滤、烘干。然后以乙醇为溶剂,配置固含量为10%的浆料在转速为6000r/min下砂磨,获得待焙烧砂磨浆料。向待焙烧砂磨浆料中加入砂磨浆料固含量的1%的氯铂酸,焙烧获得再生铂催化剂。
53.实施例7
54.将来自于废旧氢燃料电池废膜电极剪碎,按照水与丙醇的质量比为1:5混合后加入剪碎的废膜电极中,过滤、烘干,获得待焙烧料。将待焙烧料放入管式炉中,在高纯氩气氛下,300℃保温5h,获得焙烧料。将焙烧料放入球磨罐中球磨2h,然后取出并加入kcl后放置于反应釜中,加热,在180℃下保温15h,过滤,烘干,然后放入hno3中,搅拌、过滤、烘干。然后以水为溶剂,配置固含量为5%的浆料在转速为20000r/min下砂磨,获得待焙烧砂磨浆料。向待焙烧砂磨浆料中加入砂磨浆料固含量的2%的氯铂酸,焙烧获得再生铂催化剂。
55.以上所述实施例的各技术特征可以进行任意的组合,为使描述简洁,未对上述实施例中的各个技术特征所有可能的组合都进行描述,然而,只要这些技术特征的组合不存在矛盾,都应当认为是本说明书记载的范围。
56.以上所述实施例仅表达了本发明的几种实施方式,其描述较为具体和详细,但并不能因此而理解为对发明专利范围的限制。应当指出的是,对于本领域的普通技术人员来说,在不脱离本发明构思的前提下,还可以做出若干变形和改进,这些都属于本发明的保护范围。因此,本发明专利的保护范围应以所附权利要求为准。