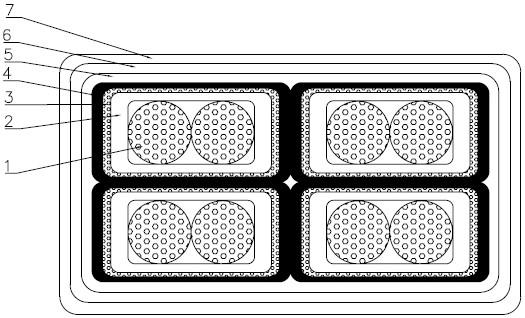
1.本发明涉及一种电缆,具体涉及一种新能源汽车高压电缆。
背景技术:2.随着国内新能源汽车的旋风般普及,国家和地方对新能源汽车的政策激励,外加上北上广深杭等超一线城市对传统燃油车的号牌严格管制和限行政令,促进了我国新能源汽车的飞速发展。
3.由于新能源纯电动汽车对充电要求的快速化程度以及对充电后续航里程的要求越来越高,之前慢充新能源充电和大截面大电流新能源充电模式,在新能源充电时效性和超重量化及人性化操作方便性方面遇到了很大的技术挑战。
4.首先,新能源纯电动车的高电压,大电流充电会给新能源汽车带来充电手提充电枪重量过载的压力,使用起来非常不方便。普遍一条ev汽车充电线含充电枪在内重量均超过20kg。
5.其次,新能源纯电动汽车在满足高电压和大电流情况下,新能源汽车电池高压包和高压盒及高压线的散热瓶颈,却始终严峻存在,直接影响到高压蓄电池和锂电池及其他能源类电池的使用寿命,存在极大的安全行驶隐患,并且更换电池也是相当大的一次高成本付出。
6.为了提升新能源汽车电池和快速充电散热能力,解决大众化人们正常充电轻量化的瓶颈问题,解决大电流、高电压、快速充电过程中存在的电池热能损耗和导体发热引发的涡轮损耗,增加常规铜导体的抗压强度和抗弯强度,解决车辆高强度振动时电缆本身自发带来的能量损失,增强车辆的吸声和隔音效果,增强电缆对高频电磁波的屏蔽效果。鉴于此,重点投入人力和财力开发一种自降温式新能源汽车高压电缆产品,意义重大。
7.作为新兴液冷充电桩电线电缆,在最大优势上解决了快充充电发热问题,但总重量方面并没减轻多少,在整体重量和导体成本问题上,依然面对需要解决的实际问题。
8.再者,当前所有的汽车高压电缆,主要结构有二类:单绝缘结构以无氧铜绞合多股紧压导体+交联pe材质绝缘,或者以无氧铜绞合多股紧压导体+气相型高回弹混炼型阻燃硅橡胶组成;双绝缘结构以无氧铜绞合多股紧压导体+气相型高回弹混炼型阻燃硅橡胶绝缘(或者加单面铝箔)+高屏蔽编织结构+耐高温铝箔麦拉屏蔽包带+气相型高回弹混炼型阻燃硅橡胶护套组成;无论是单绝缘或双绝缘单屏蔽和双屏蔽结构电缆,在轻量化结构成本设计上和散热性能设计上,全部存在严重的材料和结构短板(铜导体整体重量偏重,并且成本一直高高在上;快充充电电缆发热发烫,直接影响汽车高压电缆使用寿命和间接减少了充电电池生命延续时间)。
9.所以对于一种自降温式新能源汽车高压电缆的材料开发,工艺开发,结构开发,生产设备开发,各大功能或产品性能验证均需通过技术革命性的创新和改进。
技术实现要素:10.为了克服背景技术的不足,本发明提供一种新能源汽车高压电缆。
11.本发明所采用的技术方案:一种新能源汽车高压电缆,包括从内至外依次设置的缆芯、第二包带层、第三包带层、护套;所述缆芯包括4条芯线,每条芯线均包括从内至外依次设置的导体、绝缘层、第一包带层、编织层;所述导体由若干根导线编织而成,并压延形成矩形结构,每根导线沿其长度方向均形成有均匀间隔分布的第一散热孔;所述绝缘层采用热硫化硅橡胶混炼胶料,并通过挤出工艺成型在导体外;所述第一包带层采用复合铜箔带,并通过拖包工艺包覆在绝缘层外;所述编织层采用镀锡铜线,并通过编织工艺包覆在第一包带层外,所述镀锡铜线沿其长度方向均形成有若干均匀间隔分布的第二散热孔;所述第二包带层采用eptfe包带,并通过拖包工艺包覆在缆芯外;所述第三包带层采用铜箔麦拉包带,并通过拖包工艺包覆在第二包带层外;所述护套采用碳化硅复合硅橡胶材料,并通过挤出工艺成型在第三包带层外。
12.所述导线采用镀镍无氧铜铜合金,其横截面呈0.52mm厚*0.52mm宽且倒圆角的类矩形结构,所述第一散热孔的孔径为0.2mm,且相邻第一散热孔之间的间距为7.8mm。
13.所述导体包含24根导线,所述导体的加工方法包括如下步骤:步骤一、24根导线通过36锭重型编织机进行编织,编织节距为36mm,编织角度为45度,编织完成后先进行收线;步骤二、将步骤一获得的编织半成品进行放线,并通过0.49mm厚*1.98mm宽的矩形压延成型模具,将编织半成品压延形成0.49mm厚*1.98mm宽的扁平矩形结构,延形成型后进行收线。
14.所述复合铜箔带包括铜箔带,所述铜箔带一面涂覆散热涂层,另一面通过涂胶贴合离型膜,所述复合铜箔带的尺寸规格为13~15mm宽/0.05~0.11mm厚,屏蔽率125%。
15.所述镀锡铜线的横截面呈0.52mm宽*0.52mm的矩形结构,所述第二散热孔的孔径为0.2mm,且相邻第二散热孔之间的间距为7.8mm。
16.所述编织层的编织节距为38mm,编织角度为45度,屏蔽率90%以上。
17.所述eptfe包带的尺寸规格为15~18mm宽/0.05~0.4mm厚,屏蔽率135%。
18.所述铜箔麦拉包带的尺寸规格为20~25mm宽/ 0.035mm厚,屏蔽率125%。
19.所述碳化硅复合硅橡胶材料的sic粉末添加比例为0.035%。
20.本发明的有益效果是:1、导体的导线以及编织层的镀锡铜线在长度方向上均形成有均匀间隔分布的散热孔,导体比表面积大,在大功率和大电流充电过程中,当热量流经时,其较大的比表面积使散布在其中的流体产生复杂的三维流动,从而具有较高的自身散热能力;其次,复合铜箔带、铜箔麦拉包带、碳化硅复合硅橡胶材料的散热性能好,从里到外全部均选择高散热性能材料,让快速充电过程中自行完成了散热效率的提升;2、导体的导线以及编织层的镀锡铜线在长度方向上均形成有均匀间隔分布的散热孔,实现了轻松常态减重,大大降低整体重量,实现轻量化设计;3、复合铜箔带、eptfe包带、铜箔麦拉包带、碳化硅复合硅橡胶材料具有较好的屏
蔽综合性能以及弯曲性能,能够满足新能源汽车电池和高压空间狭小空间布线的现实要求;4、每条芯线均设置有独立的编织层,实现了各芯线之间信号独立隔离和独立单向快速传输的功能,同时散热孔的存在,当高频电磁场通过时,会产生感应电动势并形成感应涡流,与原磁场反向的涡流磁场产生互相抵消,从而达到屏蔽电磁场的可靠作用,使得电磁波屏蔽效果好;5、由于导体压延呈矩形,每条芯线也相应呈矩形,受力面积较大,在车辆高速震动运行工作状态中,可以化解矩形四角八面来的综合阻力,让每条芯线受力均匀,达到减震均衡目的。
附图说明
21.图1为本发明实施例新能源汽车高压电缆的结构示意图。
具体实施方式
22.下面结合附图对本发明实施例作进一步说明。
23.如图1所示,一种新能源汽车高压电缆,包括从内至外依次设置的缆芯、第二包带层5、第三包带层6、护套7,所述缆芯包括4条芯线,每条芯线均包括从内至外依次设置的导体1、绝缘层2、第一包带层3、编织层4。
24.所述导体1采用镀镍无氧铜铜合金,其横截面呈0.52mm厚*0.52mm宽且倒圆角的类矩形结构,每根导线沿其长度方向均形成有均匀间隔分布的第一散热孔,所述第一散热孔的孔径为0.2mm,且相邻第一散热孔之间的间距为7.8mm。
25.所述导体1包含24根导线,所述导体的加工方法包括如下步骤:步骤一、24根导线通过36锭重型编织机进行编织,编织节距为36mm,编织角度为45度,编织完成后先进行收线;步骤二、将步骤一获得的编织半成品进行放线,并通过0.49mm厚*1.98mm宽的矩形压延成型模具,将编织半成品压延形成0.49mm厚*1.98mm宽的扁平矩形结构,延形成型后进行收线。
26.其中,编织半成品在进入矩形压延成型模具之前,可先通过第一道定位矩形模具与第二道紧压定形模具,以保证压延成型质量。
27.上述导体1具有耐腐蚀、高模量、热膨胀系数小的特性,具有良好的导电导热性能、抗冲击能力强,同时设置第一散热孔,增加比表面积,提高散热性能,且具有吸振和吸音性能。
28.所述绝缘层2采用热硫化硅橡胶混炼胶料,并通过挤出工艺成型在导体1外,热硫化硅橡胶混炼胶料耐盐雾腐蚀,耐大气臭氧,耐日光照射,耐特殊野外高温环境,具有高拉伸强度高撕裂强度,综合性能优异,具有良好的机械强度,优异的电性能,满足rohs10项和reach环保性能检测。
29.所述第一包带层3采用复合铜箔带,并通过拖包工艺包覆在绝缘层2外。所述复合铜箔带包括铜箔带,所述铜箔带一面涂覆散热涂层,另一面通过涂胶贴合离型膜,所述复合铜箔带的尺寸规格为13~15mm宽/0.05~0.11mm厚,屏蔽率125%,其具有粘性强、散热效果好、
屏蔽性能优异等优点。
30.所述编织层4采用镀锡铜线,该镀锡铜线的横截面呈0.52mm宽*0.52mm的矩形结构,所述镀锡铜线沿其长度方向均形成有若干均匀间隔分布的第二散热孔,所述第二散热孔的孔径为0.2mm,且相邻第二散热孔之间的间距为7.8mm。
31.所述镀锡铜线通过编织工艺包覆在第一包带层3外,所述编织层4的编织节距为38mm,编织角度为45度,屏蔽率90%以上。
32.上述编织层4具有耐腐蚀、高模量、热膨胀系数小的特性,具有良好的导电导热性能、抗冲击能力强,同时设置第二散热孔,增加比表面积,提高散热性能,且具有吸振和吸音性能,具有优良的电磁能散热功效。
33.所述第二包带层5采用eptfe包带,并通过拖包工艺包覆在缆芯外。本eptfe包带具有柔软光滑,低介电常数,耐温性能优异的特点,能在汽车高压电池包和夏季高温范围内长期使用,介质损耗小,厚度薄,密度小,重量轻,耐高低温,耐腐蚀性,耐摩擦,耐磨性能好,密度均匀。
34.所述第三包带层6采用铜箔麦拉包带,并通过拖包工艺包覆在第二包带层5外,铜箔麦拉包带包括铜箔,铜箔表面通过粘合剂贴合pet聚脂薄膜,具有低表面氧气特性,同时兼有高强度,高弯曲性和延展性,导电性能好,散热性能好,表面光泽度好的综合应用效果。
35.所述护套7采用碳化硅复合硅橡胶材料,并通过挤出工艺成型在第三包带层6外,其中碳化硅复合硅橡胶材料中的sic粉末添加比例为0.035%,从很大程度上改善了电线结构的散热能力。
36.上述护套7耐臭氧,耐老化,耐紫外线照射,耐高低温,耐拉扯,耐挠曲性能良好,收缩率小;由于添加了一定比例的sic粉末,在很大程度上提高了护套本身的热传导系数,使护套热阻数值变小,耐温效果更高;并且增加了护套的耐击穿电压的性能。其次,增加了护套的高回弹性和耐压缩变形性。经现场火花试验结果,护套最高可耐火花电压15kv以上,充分满足ul vw-1阻燃要求和rohs10项及reach环保性能检测。
37.上述新能源汽车高压电缆主要应用在新能源汽车以及新能源汽车充电桩,其优点在于: 1、导体的导线以及编织层的镀锡铜线在长度方向上均形成有均匀间隔分布的散热孔,导体比表面积大,在大功率和大电流充电过程中,当热量流经时,其较大的比表面积使散布在其中的流体产生复杂的三维流动,从而具有较高的自身散热能力;其次,复合铜箔带、铜箔麦拉包带、碳化硅复合硅橡胶材料的散热性能好,从里到外全部均选择高散热性能材料,让快速充电过程中自行完成了散热效率的提升;2、导体的导线以及编织层的镀锡铜线在长度方向上均形成有均匀间隔分布的散热孔,实现了轻松常态减重,大大降低整体重量,实现轻量化设计;3、复合铜箔带、eptfe包带、铜箔麦拉包带、碳化硅复合硅橡胶材料具有较好的屏蔽综合性能以及弯曲性能,能够满足新能源汽车电池和高压空间狭小空间布线的现实要求;4、每条芯线均设置有独立的编织层,实现了各芯线之间信号独立隔离和独立单向快速传输的功能,同时散热孔的存在,当高频电磁场通过时,会产生感应电动势并形成感应涡流,与原磁场反向的涡流磁场产生互相抵消,从而达到屏蔽电磁场的可靠作用,使得电磁
波屏蔽效果好;5、由于导体压延呈矩形,每条芯线也相应呈矩形,受力面积较大,在车辆高速震动运行工作状态中,可以化解矩形四角八面来的综合阻力,让每条芯线受力均匀,达到减震均衡目的。
38.各位技术人员须知:虽然本发明已按照上述具体实施方式做了描述,但是本发明的发明思想并不仅限于此发明,任何运用本发明思想的改装,都将纳入本专利专利权保护范围内。