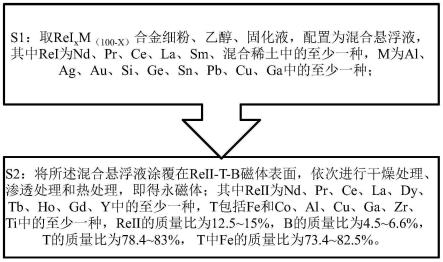
1.本发明涉及钕铁硼材料相关技术领域。更具体地说,本发明涉及一种永磁体及其制备方法。
背景技术:2.稀土nd2fe
14
b永磁体作为全球稀土永磁材料的高产量代表,已经进入高速增长时期。随着烧结钕铁硼磁体在风力发电、混合动力汽车及纯电动汽车和节能家电等低碳经济领域中的应用,双高磁性能磁体及低成本磁体已成为研究的主要目标,以适应烧结钕铁硼在新领域的应用要求和原材价格上涨的新形势,同时也促进了稀土资源的高效利用。
3.当前双高性能磁体主要的技术为,由传统工艺通过添加一定量的重稀土dy、tb、ho来实现制备高剩磁的h及以上牌号永磁体,另一种方式是采用晶界扩散dy、tb、ho制作高剩磁的uh及以上牌号永磁体;这两种制备方法,都用到了比较高含量的重稀土,在应用领域上的成本优势很弱,同时对于稀土资源的平衡及高效利用也处于不利的局势。
技术实现要素:4.本发明的一个目的是提供一种永磁体及其制备方法,其不使用重稀土dy或tb,或者使用非常少的量,成本较低。
5.为了实现本发明的这些目的和其它优点,根据本发明的一个方面,本发明提供了永磁体制备方法,包括:取reⅰxm(100-x)
合金细粉、乙醇、固化液,配置为混合悬浮液,其中reⅰ为nd、pr、ce、la、sm、混合稀土中的至少一种,m为al、ag、au、si、ge、sn、pb、cu、ga中的至少一种;将所述混合悬浮液涂覆在re
ⅱ‑
t-b磁体表面,依次进行干燥处理、渗透处理和热处理,即得永磁体;其中reⅱ为nd、pr、ce、la、dy、tb、ho、gd、y中的至少一种,t包括fe和co、al、cu、ga、zr、ti中的至少一种,reⅱ的质量比为12.5~15%,b的质量比为4.5~6.6%,t的质量比为78.4~83%,t中fe的质量比为73.4~82.5%。
6.进一步地,所述混合悬浮液中,reⅰxm(100-x)
合金细粉的质量比为40~60%。
7.进一步地,所述固化液由聚乙烯醇缩丁醛和松油醇按质量比1:9~11配制得到。
8.进一步地,所述混合悬浮液中,所述乙醇与所述固化液的质量比为1:8~10。
9.进一步地,所述混合悬浮液的涂覆量为re
ⅱ‑
t-b磁体质量的0.2~2%。
10.进一步地,所述混合悬浮液中还包括质量比为0~10%的dy粉或tb粉。
11.进一步地,所述渗透处理的方法包括:将涂覆有所述混合悬浮液的re
ⅱ‑
t-b磁体放入渗透炉内,抽真空至真空度为1.0
×
10-2pa以下,升温至140~160℃,保温1~2h,继续升温至350~550℃,保温2~5h,继续升温至700~800℃,充入氩气或氦气使真空度保持在5.0
×
10-2
~1.0
×
10-1
pa之间,保温3~10h,抽真空至真空度为1.0
×
10-2
pa以下,继续升温至850~950℃,保温5~15h,充入氩气或氦气至85~100kpa进行冷却。
12.进一步地,所述渗透炉内氧含量不高于50ppm。
13.进一步地,所述热处理的方法包括:将经过所述渗透处理的re
ⅱ‑
t-b磁体转入热
处理炉,在真空度1pa以下,温度450~650℃下进行所述热处理。
14.根据本发明的另一个方面,还提供了永磁体,采用所述的永磁体制备方法制备得到。
15.本发明至少包括以下有益效果:
16.本发明相比于传统高性能磁体制备工艺,不使用重稀土dy或tb,或使用量非常少,从而成本上可以降低3~10%,而磁性能能够接近或超过传统高性能磁体。
17.本发明的其它优点、目标和特征将部分通过下面的说明体现,部分还将通过对本发明的研究和实践而为本领域的技术人员所理解。
附图说明
18.图1为本发明一个实施例的流程图。
具体实施方式
19.下面结合附图对本发明做进一步的详细说明,以令本领域技术人员参照说明书文字能够据以实施。
20.应当理解,本文所使用的诸如“具有”、“包含”以及“包括”术语并不排除一个或多个其它元件或其组合的存在或添加。
21.如图1所示,本技术的实施例提供了永磁体制备方法,包括:
22.s1:取reⅰxm(100-x)
合金细粉、乙醇、固化液,配置为混合悬浮液,x小于100,其中reⅰ为nd、pr、ce、la、sm、混合稀土中的至少一种,m为al、ag、au、si、ge、sn、pb、cu、ga中的至少一种;混合稀土可以是celandpr;乙醇和固化液用于将合金细粉充分分散,并使其便于黏附在钕铁硼磁体表面;
23.s2:将所述混合悬浮液涂覆在re
ⅱ‑
t-b磁体表面,依次进行干燥处理、渗透处理和热处理,即得永磁体;其中reⅱ为nd、pr、ce、la、dy、tb、ho、gd、y中的至少一种,t包括fe和co、al、cu、ga、zr、ti中的至少一种,reⅱ的质量比为12.5~15%,b的质量比为4.5~6.6%,t的质量比为78.4~83%,t中fe的质量比为73.4~82.5%,剩余为co、al、cu、ga、zr、ti中的至少一种;如pr3nd
10
ce
0.7b5.54
cu
0.15
co
1.66
ga
0.2
zr
0.12
fe
78.63
磁体;可选地,为真空干燥,渗透处理在700~1000℃下进行,热处理在400~700℃下进行;
24.本实施例将混合悬浮液涂覆在re
ⅱ‑
t-b磁体表面,通过渗透处理和热处理,将reⅰxm(100-x)
引入re
ⅱ‑
t-b磁体,使其与re
ⅱ‑
t-b磁体协同作用,得到具有剩磁、矫顽力双高的永磁体,基本能够达到传统高性能磁体制备工艺;而且相比于传统高性能磁体制备工艺,本实施例,工艺流程相对简单,工艺设备要求不高,且未引入dy和tb,成本相对更低。
25.在另一些实施例中,所述混合悬浮液中,reⅰxm(100-x)
合金细粉的质量比为40~60%;可选地,质量比为50%。
26.在另一些实施例中,所述固化液由聚乙烯醇缩丁醛和松油醇按质量比1:9~11配制得到;可选地,为1:10。
27.在另一些实施例中,所述混合悬浮液中,所述乙醇与所述固化液的质量比为1:8~10;可选地,为1:9。
28.在另一些实施例中,所述混合悬浮液的涂覆量为钕铁硼磁体质量的0.2~2%;可
选地,为0.5~1.5%。
29.在另一些实施例中,所述混合悬浮液中还包括质量比为0~10%的dy粉或tb粉;可以一定程度引入dy和tb,以进一步提升永磁体的性能。
30.在另一些实施例中,所述渗透处理的方法包括:将涂覆有所述混合悬浮液的钕铁硼磁体放入渗透炉内,抽真空至真空度为1.0
×
10-2
pa以下,升温至140~160℃,保温1~2h,继续升温至350~550℃,保温2~5h,继续升温至700~800℃,充入氩气或氦气使真空度保持在5.0
×
10-2
~1.0
×
10-1
pa之间,保温3~10h,抽真空至真空度为1.0
×
10-2
pa以下,继续升温至850~950℃,保温5~15h,充入氩气或氦气至85~100kpa进行冷却。
31.在另一些实施例中,所述渗透炉内氧含量不高于50ppm。
32.在另一些实施例中,所述热处理的方法包括:将经过所述渗透处理的钕铁硼磁体转入热处理炉,在真空度1pa以下,温度450~650℃下进行所述热处理。
33.本技术的实施例还提供了永磁体,采用以上实施例的方法制备得到。
34.以下以两个具体实施例说明。
35.实施例1:
36.1.将pr
70
ce
10
al
20
合金细粉,按55%质量比与无水乙醇、固化液的混合溶液配制成混合悬浮液;固化液由聚乙烯醇缩丁醛和松油醇按质量比1:10配制得到,乙醇与固化液的质量比为1:9。
37.2.在氧含量20ppm的密闭环境中,将悬浮溶液通过旋转辊轮涂覆于成分为pr3nd
10
ce
0.7b5.54
cu
0.15
co
1.66
ga
0.2
zr
0.12
fe
78.63
烧结钕铁硼磁片的表面上,涂覆量为1%,然后在真空度为5pa,温度为150℃的真空恒温箱中,将悬浮溶液中无水乙醇及表面吸附的水分烘干除掉。
38.3.处理后的片在氧含量20ppm的封闭码片箱中,集中码于密度为1.82g/cm3的石墨料舟内,码片箱对接真空渗透炉,在渗透炉的氧含量达到20ppm,升起渗透炉门,将码好的片送入渗透炉内。
39.4.对渗透炉抽真空,真空度为5.0
×
10-3
pa,持续10min后开始加热升温至150℃,保温2h,继续升温至350℃保温3h,继续升温至750℃,保温1h后充入氩气或氦气,使真空度保持在5.0
×
10-2
~1.0
×
10-1
pa之间,保温8h。继续抽真空,使真空度为5.0
×
10-3
pa以下,继续升温至900℃,保温10h,充入氩气或氦气至85~100kpa进行冷却。5.待冷却至70℃以下后,转入热处理炉,抽真空至0.5pa,开始升温,热处理温度为480℃。对比例1(传统高性能磁体制备工艺):
40.将原材料按照成分为pr3nd
10
dy
0.35
tb
0.1
al
0.24b5.33
cu
0.15
co
1.66
ga
0.2
zr
0.12
fe
78.85
的配比要求配好,通过真空熔炼(sc)将配好的原材料在中频感应加热的条件下熔化金属,最终获得片状的具有柱状晶结构的快淬钕铁硼合金。然后在氢破炉中吸氢脱氢破碎成毫米级的粗颗粒,再通过气流磨用高压氮气磨出粒度均匀微米级的粉末,经过磁场取向压机压制成生坯,在真空烧结炉中致密化,热处理炉中回火得到毛坯。
41.测试:
42.对实施例1和对比例1得到的永磁体进行测试,将pr3nd
10
ce
0.7b5.54
cu
0.15
co
1.66
ga
0.2
zr
0.12
fe
78.63
烧结钕铁硼磁片作为空白组1也进行测试,结果见表1。
43.可以看出,相较于空白组1,实施例1和对比例1的剩磁、常温和高温矫顽力均有明
显提升,实施例1未使用dy、tb等重稀土元素,而剩磁和矫顽力均达到或超过对比例1的水平,经过方案成本和原料成本测算,相比于对比例1,实施例1的成本优化比例达到3.5%。
44.表1剩磁(br)和矫顽力(hcj)测试结果
[0045][0046]
实施例2:
[0047]
1.将pr
80
la
10
ga
10
合金细粉,按50%质量比与10%质量比的tb粉、无水乙醇、固化液的混合溶液配制成混合悬浮液;固化液由聚乙烯醇缩丁醛和松油醇按质量比1:10配制得到,乙醇与固化液的质量比为1:9。
[0048]
2.在氧含量10ppm的密闭环境中,将悬浮溶液通过旋转辊轮涂覆于成分为pr
3.3
nd
10
ce1b
5.4
cu
0.36
co
0.6
ga
0.28
ti
0.23
fe
78.83
烧结钕铁硼磁片的表面上,涂覆量为0.4%,然后在真空度为2pa,温度为130℃的真空恒温箱中,将悬浮溶液中无水乙醇及表面吸附的水分烘干除掉。
[0049]
3.处理后的片在氧含量10ppm的封闭码片箱中,集中码于密度为1.84g/cm3的石墨料舟内,码片箱对接真空渗透炉,在渗透炉的氧含量达到10ppm,升起渗透炉门,将码好的片送入渗透炉内。
[0050]
4.对渗透炉抽真空,真空度为2.0
×
10-3
pa,持续20min后开始加热升温至130℃,保温1.5h,继续升温至400℃保温2h,继续升温至800℃,保温1.5h后充入氩气或氦气,使真空度保持在5.0
×
10-2
~1.0
×
10-1
pa之间,保温10h。继续抽真空,使真空度为2.0
×
10-3
pa以下,继续升温至920℃,保温7h,充入氩气或氦气至85~100kpa进行冷却。
[0051]
5.待冷却至70℃以下后,转入热处理炉,抽真空至0.2pa,开始升温,热处理温度为530℃。
[0052]
对比例2:
[0053]
1.将tb粉按50%质量比与无水乙醇、固化液的混合溶液配制成混合悬浮液;固化液由聚乙烯醇缩丁醛和松油醇按质量比1:10配制得到,乙醇与固化液的质量比为1:9。
[0054]
2.在氧含量10ppm的密闭环境中,将悬浮溶液通过旋转辊轮涂覆于成分为pr
3.3
nd
10
ce1b
5.4
cu
0.36
co
0.6
ga
0.28
ti
0.23
fe
78.83
烧结钕铁硼磁片的表面上,涂覆量为0.4%,然后在真空度为2pa,温度为130℃的真空恒温箱中,将悬浮溶液中无水乙醇及表面吸附的水分烘干除掉。
[0055]
3.处理后的片在氧含量10ppm的封闭码片箱中,集中码于密度为1.84g/cm3的石墨料舟内,码片箱对接真空渗透炉,在渗透炉的氧含量达到10ppm,升起渗透炉门,将码好的片送入渗透炉内。
[0056]
4.对渗透炉抽真空,真空度为2.0
×
10-3
pa,持续20min后开始加热升温至130℃,保
温1.5h,继续升温至400℃保温2h,继续升温至800℃,保温1.5h后充入氩气或氦气,使真空度保持在5.0
×
10-2~1.0
×
10-1pa之间,保温10h。继续抽真空,使真空度为2.0
×
10-3
pa以下,继续升温至920℃,保温7h,充入氩气或氦气至85~100kpa进行冷却。
[0057]
5.待冷却至70℃以下后,转入热处理炉,抽真空至0.2pa,开始升温,热处理温度为530℃。
[0058]
测试:
[0059]
对实施例2和对比例2得到的永磁体进行测试,将ppr
3.3
nd
10
ce1b
5.4
cu
0.36
co
0.6
ga
0.28
ti
0.23
fe
78.83
烧结钕铁硼磁片作为空白组2也进行测试,结果见表2。
[0060]
可以看出,相较于空白组2,实施例2和对比例2的剩磁、常温矫顽力、特别是高温矫顽力均有明显提升,实施例2使用的tb重稀土元素量远少于对比例2,而剩磁和矫顽力均达到或超过对比例2的水平,经过方案成本和原料成本测算,相比于对比例2,实施例2的成本优化比例达到13%。
[0061]
表2剩磁和矫顽力测试结果
[0062][0063]
实施例3:
[0064]
1.将pr
40
nd
20
sm
20
cu
10
ge
10
合金细粉,按55%质量比与无水乙醇、固化液的混合溶液配制成混合悬浮液;固化液由聚乙烯醇缩丁醛和松油醇按质量比1:10配制得到,乙醇与固化液的质量比为1:9。。
[0065]
2.在氧含量20ppm的密闭环境中,将悬浮溶液通过旋转辊轮涂覆于成分为pr3nd
10
ce
1.5b5.48
cu
0.35
co
1.06
ga
0.28
zr
0.06
ti
0.13
fe
78.14
烧结钕铁硼磁片的表面上,涂覆量为1.1%,然后在真空度为5pa,温度为150℃的真空恒温箱中,将悬浮溶液中无水乙醇及表面吸附的水分烘干除掉。
[0066]
3.处理后的片在氧含量20ppm的封闭码片箱中,集中码于密度为1.82g/cm3的石墨料舟内,码片箱对接真空渗透炉,在渗透炉的氧含量达到20ppm,升起渗透炉门,将码好的片送入渗透炉内。
[0067]
4.对渗透炉抽真空,真空度为5.0
×
10-3
pa,持续10min后开始加热升温至150℃,保温2h,继续升温至350℃保温3h,继续升温至750℃,保温1h后充入氩气或氦气,使真空度保持在5.0
×
10-2
~1.0
×
10-1
pa之间,保温8h。继续抽真空,使真空度为5.0
×
10-3
pa以下,继续升温至900℃,保温10h,充入氩气或氦气至85~100kpa进行冷却。
[0068]
5.待冷却至70℃以下后,转入热处理炉,抽真空至0.5pa,开始升温,热处理温度为480℃。
[0069]
对比例3(传统高性能磁体制备工艺):
[0070]
将原材料按照成分为pr4nd
10
dy
0.6
al
0.85b5.35
cu
0.15
co
1.7
ga
0.2
zr
0.12
fe
77.03
的配比要求配好,通过真空熔炼(sc)将配好的原材料在中频感应加热的条件下熔化金属,最终获得片状的具有柱状晶结构的快淬钕铁硼合金。然后在氢破炉中吸氢脱氢破碎成毫米级的粗颗粒,再通过气流磨用高压氮气磨出粒度均匀微米级的粉末,经过磁场取向压机压制成生坯,在真空烧结炉中致密化,热处理炉中回火得到毛坯。
[0071]
测试:
[0072]
对实施例3和对比例3得到的永磁体进行测试,将pr3nd
10
ce
1.5b5.48
cu
0.35
co
1.06
ga
0.28
zr
0.06
ti
0.13
fe
78.14
烧结钕铁硼磁片作为空白组3也进行测试,结果见表3。
[0073]
可以看出,相较于空白组3,实施例3和对比例3的剩磁、常温和高温矫顽力均有明显提升,实施例3未使用dy、tb等重稀土元素,而剩磁和矫顽力均达到或超过对比例3的水平,经过方案成本和原料成本测算,相比于对比例3,实施例3的成本优化比例达到4.3%。
[0074]
表3剩磁和矫顽力测试结果
[0075][0076]
这里说明的设备数量和处理规模是用来简化本发明的说明的。对本发明永磁体及其制备方法的应用、修改和变化对本领域的技术人员来说是显而易见的。
[0077]
尽管本发明的实施方案已公开如上,但其并不仅仅限于说明书和实施方式中所列运用,它完全可以被适用于各种适合本发明的领域,对于熟悉本领域的人员而言,可容易地实现另外的修改,因此在不背离权利要求及等同范围所限定的一般概念下,本发明并不限于特定的细节和这里示出与描述的图例。