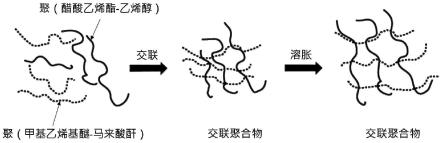
1.本发明涉及锂离子电池相关技术领域,具体地涉及一种锂离子电池涂布隔膜。
背景技术:2.隔膜用于隔离锂离子电池的正负极,除了可提供li
+
迁移的通道与避免电极接触发生短路外,在失控状况下还可闭孔阻止li
+
迁移,确保电池安全。虽然隔膜不直接参与电极反应,但是对锂离子电池的综合性能有着重要影响。
3.常见的锂离子电池隔膜为聚烯烃类隔膜,尤其以聚乙烯(pe) 和聚丙烯(pp)为主。聚烯烃类隔膜熔点较低、机械强度不足,在极端状况下容易导致电池内部短路。此外,聚烯烃类隔膜对电解液的浸润性较差,使得锂离子电池注液与保液效果不佳,多次循环后易发生电解液贫液现象,从而影响锂离子电池的性能,造成使用寿命大打折扣。
4.为解决上述问题,目前主要采用的方法是以聚烯烃类隔膜作为底材,并涂覆陶瓷颗粒涂层和/或有机聚合物涂层。陶瓷材料的机械强度较高,熔点较高,热稳定性较佳,且陶瓷材料通常具有一定的极性,与常用的碳酸酯类溶剂间的亲和性较佳,可增加隔膜的吸液和保液性能。另外,电解质能使有机聚合物涂层溶胀,对li
+
的迁移更为有利,但是有机聚合物涂层的耐热性目前仅能达到150℃。
5.此外,现有涂层隔膜对吸液和保液性能的提升有限,不能完全满足现今追求更高容量、更高倍率、更高循环稳定性、更长寿命、更安全的锂离子电池的要求。
技术实现要素:6.本发明的目的是提供一种锂离子电池涂布隔膜,通过无机陶瓷材料和具有三维网络结构的两亲性粘合剂的使用,以有效提升隔膜的吸液和保液性能。
7.基于此,本发明提出一种锂离子电池涂布隔膜,包括:聚烯烃隔膜基材以及形成于聚烯烃隔膜基材至少一侧的隔膜涂层,隔膜涂层含有γ-al2o3陶瓷颗粒以及具有三维网络结构的两亲性粘合剂。
8.本发明另提出一种制备上述锂离子电池涂布隔膜的方法,包括:涂布含有γ-al2o3陶瓷颗粒及具有三维网络结构的两亲性粘合剂的浆料于聚烯烃隔膜基材的至少一侧;以及干燥浆料形成隔膜涂层。
9.本发明又提出一种锂离子电池,包括上述的锂离子电池涂布隔膜、正极、以及负极,正极与负极分别位于锂离子电池涂布隔膜的二侧。
10.根据本发明,陶瓷颗粒具备高温稳定性与高比表面积,可提高锂离子电池的比容量和循环寿命。此外,陶瓷颗粒的高比表面积可增加隔膜的电解液浸润性,对电解液具有良好的吸收及保持性能,以提高 li
+
的迁移速率及电导率。另外,两亲性粘合剂同时具有亲水端与疏水端,通过疏水端与聚烯烃隔膜基材间同极性的结合,提升隔膜的结构强度,并通过亲水端与电解液间同极性的结合,增加隔膜的电解液浸润性。而且,两亲性粘合剂的三维网络结构可增加与聚烯烃隔膜基材及电解液的结合面积,以提升隔膜的结构强度及电解液浸
润性。
附图说明
11.图1是一示意图,呈现锂离子电池涂布隔膜;
12.图2是一扫描电镜(sem)照片图,呈现陶瓷颗粒;
13.图3是一示意图,呈现两亲性粘合剂的交联形成与溶胀。
14.组件标号说明
[0015]1…
聚烯烃隔膜基材
[0016]2…
隔膜涂层
具体实施方式
[0017]
以下对本发明的具体实施方式结合附图进行详细说明。应当理解的是,此处所描述的具体实施方式仅用于说明和解释本发明,并不用于限制本发明。
[0018]
在本文中所披露的范围的端点和任何值都不限于该精确的范围或值,这些范围或值应当理解为包含接近这些范围或值的值。对于数值范围来说,各个范围的端点值之间、各个范围的端点值和单独的点值之间,以及单独的点值之间可以彼此组合而得到一个或多个新的数值范围,这些数值范围应被视为在本文中具体公开。
[0019]
请参照图1,本发明第一实施方式提出一种锂离子电池涂布隔膜,包括:聚烯烃隔膜基材1以及隔膜涂层2,隔膜涂层2形成于聚烯烃隔膜基材1的至少一侧且含有γ-al2o3陶瓷颗粒及具有三维网络结构的两亲性粘合剂。具体地说,γ-al2o3陶瓷颗粒可形成多孔陶瓷结构层于聚烯烃隔膜基材1的至少一侧,两亲性粘合剂可形成于多孔陶瓷结构层的孔隙内。
[0020]
聚烯烃隔膜基材1可包括重均分子量在200万或以上的超高分子量聚乙烯、线性聚乙烯、支化聚乙烯、密度介于0.941至0.960g/cm3之间的高密度聚乙烯、密度介于0.915至0.940g/cm3之间的低密度聚乙烯、交联聚乙烯、聚丙烯中的一种或多种形成的共聚物,但不限于此。此外,聚烯烃隔膜基材1的孔隙率可介于30至60%之间,但不限于此。另外,聚烯烃隔膜基材1的厚度可介于5至10μm之间,但不限于此。
[0021]
以γ-al2o3陶瓷颗粒与两亲性粘合剂的总重量为100份计,γ-al2o3陶瓷颗粒的重量可介于90.0至95.0份之间,两亲性粘合剂的重量可介于5.0至10.0份之间,但不限于此。隔膜涂层2可形成于聚烯烃隔膜基材1的一侧或二侧,隔膜涂层2的厚度可介于5至7μm 之间,但不限于此。此外,γ-al2o3陶瓷颗粒形成的多孔陶瓷结构层的厚度可介于3至6μm之间,但不限于此。可理解的是,隔膜涂层2 的厚度与γ-al2o3陶瓷颗粒形成的多孔陶瓷结构层的厚度理论上相同,但于不相同的情况下,可能为两亲性粘合剂不仅形成于多孔陶瓷结构层的孔隙内,也形成于多孔陶瓷结构层的至少一表面所导致。
[0022]
γ-al2o3陶瓷颗粒的表面可如图2所示布满微孔,但孔隙率、孔径、颗粒形貌与大小并无特别限制,可依据实际需求进行选择。举例地说,γ-al2o3陶瓷颗粒的中位粒径d50分布范围可介于1.6至5.0μm 之间,但不限于此。
[0023]
两亲性粘合剂可为聚(醋酸乙烯酯-乙烯醇)(pvac-va)与聚 (甲基乙烯基醚-马来酸酐)(pmve-ma)交联形成的共聚物粘合剂或聚乙二醇(peg)与聚(甲基乙烯基醚-马来酸酐)(pmve-ma) 交联形成的共聚物粘合剂,但不限于此。据发现,聚合物粘合剂的交联度升
高会增加三维网络的致密性,使内聚力增大;然而,交联度过度升高反而会导致聚合物粘合剂的流动性变差,不利在粘接界面铺展,影响界面粘接强度。因此,为得到适当的粘接性,两亲性粘合剂的交联度可介于10至20%的范围之间,但不限于此。
[0024]
以下举例说明聚(醋酸乙烯酯-乙烯醇)与聚(甲基乙烯基醚-马来酸酐)交联形成的共聚物粘合剂的制备:
[0025]
首先,对聚醋酸乙烯酯(pvac)水解,得带有部分水解基团-oh 的聚(醋酸乙烯酯-乙烯醇)。可用催化剂加快水解反应,催化剂可为盐酸,但不限于此。具体地说,先将聚醋酸乙烯酯与乙醇水溶液混合得混合物,再于55至60℃下搅拌得均相的聚醋酸乙烯酯溶液,最后滴加催化剂启动水解反应。更具体地说,秤取100至200克聚醋酸乙烯酯并加入至三口烧瓶中,量取500至1000ml乙醇和水的体积比为1:1的混合溶液并倒入三口烧瓶中;于加热温度55至60℃下均匀搅拌,并开启回流冷凝水;约3至4小时后,得均相的聚醋酸乙烯酯溶液;将50至100ml适当浓度的催化剂倒入恒压漏斗并控制滴加速度;滴加反应3至4小时后,将反应产物取出倒入玻璃容器中。由于反应产物整体呈现黏稠状且内部包裹大量副产物醋酸,可采用重复溶解、洗漆来去除。具体地说,将反应产物溶解于乙醇溶液中,缓慢滴加去离子水,使反应产物析出而洗去包裹的醋酸,并重复进行三次后,于50至55℃下真空干燥反应产物直至恒重。
[0026]
接着,对聚(甲基乙烯基醚-马来酸酐)水解与醇解,并与带有部分水解基团-oh的聚(醋酸乙烯酯-乙烯醇)反应生成交联共聚物粘合剂。具体地说,先于含水与醇类的混合溶液中打开聚(甲基乙烯基醚-马来酸酐)的部分酸酐基团以发生水解与醇解反应生成羧酸基或酯基;最后带有部分水解基团-oh的聚(醋酸乙烯酯-乙烯醇)与聚(甲基乙烯基醚-马来酸酐)生成的羧酸基或酯基以及未打开的酸酐基团反应,得交联共聚物粘合剂。更具体地说,秤取10至20克带有部分水解基团-oh的聚(醋酸乙烯酯-乙烯醇)与5至10克聚(甲基乙烯基醚-马来酸酐)并加入三口烧瓶中;将50至100ml乙醇、 50至100ml水与12至24ml丙三醇倒入三口烧瓶中;于油浴温度 78至82℃下均匀搅拌,并开启回流冷凝水;约反应2至2.5小时后,将终产物置于60至65℃的真空烘干箱中干燥。
[0027]
请参看图3,线型聚合物聚(醋酸乙烯酯-乙烯醇)与线型聚合物聚(甲基乙烯基醚-马来酸酐)反应形成交联共聚物粘合剂,而交联共聚物粘合剂会于水(如电解液中的水)中溶胀,以强化交联共聚物粘合剂的功能。
[0028]
本发明第二实施方式提出一种制备上述的锂离子电池涂布隔膜的方法,涂布含有γ-al2o3陶瓷颗粒及具有三维网络结构的两亲性粘合剂的浆料于聚烯烃隔膜基材的至少一侧;以及干燥浆料形成隔膜涂层。
[0029]
为便于铺展浆料于聚烯烃隔膜基材的至少一侧,浆料更可含有溶剂,溶剂可为水,但不限于此。须说明的是,溶剂为水的好处在于可使两亲性粘合剂溶胀。具体地说,先将两亲性粘合剂加入溶剂中搅拌,至于搅拌设备、速度与时间并无特别限制,只要能得到均匀的粘合剂溶液即可;再将γ-al2o3陶瓷颗粒加入至得到的粘合剂溶液并搅拌分散,至于搅拌分散设备、速度与时间并无特别限制,只要γ-al2o3陶瓷颗粒能均匀的分布于浆料即可。
[0030]
浆料的涂布可采用凹版涂布、喷涂、浸涂及线棒涂布中的一种,但不限于此。
[0031]
本发明第三实施方式提出一种锂离子电池,包括上述的锂离子电池涂布隔膜、正极、以及负极,正极与负极分别位于锂离子电池涂布隔膜的二侧。
[0032]
于此主要改进之处在于采用新的锂离子电池涂布隔膜作为锂离子电池隔膜,而正极与负极的选择可以与现有技术相同,对此本领域技术人员均能知悉,在此不作赘述。
[0033]
兹以下列实施例例示说明本发明:
[0034]
实施例1
[0035]
本实施例的锂离子电池隔膜涂层的成分和含量为:95.0重量份γ-al2o3(d50粒径5μm);5.0重量份pvac-va与pmve-ma交联 (交联度15%)形成的共聚物粘合剂。
[0036]
将上述隔膜涂层的浆液通过凹版辊涂布机涂布在厚度10μm的pe微孔基材膜上,最终经过烘箱烘烤后,形成一厚度6μm的涂层于 pe微孔基材膜的单面上,并取得总厚度16μm的陶瓷涂布隔膜。
[0037]
实施例2
[0038]
本实施例的锂离子电池隔膜涂层的成分和含量为:90.0重量份γ-al2o3(d50粒径1.6μm);10.0重量份pvac-va与pmve-ma交联(交联度15%)形成的共聚物粘合剂。
[0039]
将上述隔膜涂层的浆液通过线棒型涂布机涂布在厚度7μm的pe 微孔基材膜上,最终经过悬浮烘箱烘烤后,形成二每一厚度2.5μm的涂层于pe微孔基材膜的双面上,并取得总厚度12μm的陶瓷涂布隔膜。
[0040]
实施例3
[0041]
本实施例的锂离子电池隔膜涂层的成分和含量为:93.0重量份γ-al2o3(d50粒径3.0μm);7.0重量份pvac-va与pmve-ma交联 (交联度15%)形成的共聚物粘合剂。
[0042]
将上述隔膜涂层的浆液通过线棒型涂布机涂布在厚度5μm的pe 微孔基材膜上,最终经过悬浮烘箱烘烤后,形成二每一厚度3.5μm的涂层于pe微孔基材膜的双面上,并取得总厚度12μm的陶瓷涂布隔膜。
[0043]
实施例4
[0044]
本实施例的锂离子电池隔膜涂层的成分和含量为:90.0重量份γ-al2o3(d50粒径1.6μm);10.0重量份peg与pmve-ma交联(交联度15%)形成的共聚物粘合剂。
[0045]
将上述隔膜涂层的浆液通过线棒型涂布机涂布在厚度7μm的pe 微孔基材膜上,最终经过悬浮烘箱烘烤后,形成二每一厚度2.5μm的涂层于pe微孔基材膜的双面上,并取得总厚度12μm的陶瓷涂布隔膜。
[0046]
实施例5
[0047]
本实施例的锂离子电池隔膜涂层的成分和含量为:90.0重量份γ-al2o3(d50粒径1.0μm);10.0重量份pvac-va与pmve-ma交联(交联度15%)形成的共聚物粘合剂。
[0048]
将上述隔膜涂层的浆液通过线棒型涂布机涂布在厚度7μm的pe 微孔基材膜上,最终经过悬浮烘箱烘烤后,形成二每一厚度2.5μm的涂层于pe微孔基材膜的双面上,并取得总厚度12μm的陶瓷涂布隔膜。
[0049]
实施例6
[0050]
本实施例的锂离子电池隔膜涂层的成分和含量为:95.0重量份γ-al2o3(d50粒径6.0μm);5.0重量份pvac-va与pmve-ma交联 (交联度15%)形成的共聚物粘合剂。
[0051]
将上述隔膜涂层的浆液通过凹版辊涂布机涂布在厚度10μm的 pe微孔基材膜上,最终经过烘箱烘烤后,形成一厚度6μm的涂层于 pe微孔基材膜的单面上,并取得总厚度16μm的陶瓷涂布隔膜。
[0052]
实施例7
[0053]
本实施例的锂离子电池隔膜涂层的成分和含量为:90.0重量份γ-al2o3(d50粒径1.6μm);10.0重量份pvac-va与pmve-ma交联(交联度5%)形成的共聚物粘合剂。
[0054]
将上述隔膜涂层的浆液通过线棒型涂布机涂布在厚度7μm的pe 微孔基材膜上,最终经过悬浮烘箱烘烤后,形成二每一厚度2.5μm的涂层于pe微孔基材膜的双面上,并取得总厚度12μm的陶瓷涂布隔膜。
[0055]
实施例8
[0056]
本实施例的锂离子电池隔膜涂层的成分和含量为:90.0重量份γ-al2o3(d50粒径1.6μm);10.0重量份pvac-va与pmve-ma交联(交联度25%)形成的共聚物粘合剂。
[0057]
将上述隔膜涂层的浆液通过线棒型涂布机涂布在厚度7μm的pe 微孔基材膜上,最终经过悬浮烘箱烘烤后,形成二每一厚度2.5μm的涂层于pe微孔基材膜的双面上,并取得总厚度12μm的陶瓷涂布隔膜。
[0058]
实施例9
[0059]
本实施例的锂离子电池隔膜涂层的成分和含量为:90.0重量份γ-al2o3(d50粒径1.0μm);10.0重量份peg与pmve-ma交联(交联度15%)形成的共聚物粘合剂。
[0060]
将上述隔膜涂层的浆液通过线棒型涂布机涂布在厚度7μm的pe 微孔基材膜上,最终经过悬浮烘箱烘烤后,形成二每一厚度2.5μm的涂层于pe微孔基材膜的双面上,并取得总厚度12μm的陶瓷涂布隔膜。
[0061]
实施例10
[0062]
本实施例的锂离子电池隔膜涂层的成分和含量为:95.0重量份γ-al2o3(d50粒径6.0μm);5.0重量份peg与pmve-ma交联(交联度15%)形成的共聚物粘合剂。
[0063]
将上述隔膜涂层的浆液通过凹版辊涂布机涂布在厚度10μm的 pe微孔基材膜上,最终经过烘箱烘烤后,形成一厚度6μm的涂层于 pe微孔基材膜的单面上,并取得总厚度16μm的陶瓷涂布隔膜。
[0064]
实施例11
[0065]
本实施例的锂离子电池隔膜涂层的成分和含量为:90.0重量份γ-al2o3(d50粒径1.6μm);10.0重量份peg与pmve-ma交联(交联度5%)形成的共聚物粘合剂。
[0066]
将上述隔膜涂层的浆液通过线棒型涂布机涂布在厚度7μm的pe 微孔基材膜上,最终经过悬浮烘箱烘烤后,形成二每一厚度2.5μm的涂层于pe微孔基材膜的双面上,并取得总厚度12μm的陶瓷涂布隔膜。
[0067]
实施例12
[0068]
本实施例的锂离子电池隔膜涂层的成分和含量为:90.0重量份γ-al2o3(d50粒径1.6μm);10.0重量份peg与pmve-ma交联(交联度25%)形成的共聚物粘合剂。
[0069]
将上述隔膜涂层的浆液通过线棒型涂布机涂布在厚度7μm的pe 微孔基材膜上,最终经过悬浮烘箱烘烤后,形成二每一厚度2.5μm的涂层于pe微孔基材膜的双面上,并取得总厚度12μm的陶瓷涂布隔膜。
[0070]
实施例13
[0071]
本实施例的锂离子电池隔膜涂层的成分和含量为:90.0重量份γ-al2o3(d50粒径1.0μm);10.0重量份pvac-va与pmve-ma交联(交联度5%)形成的共聚物粘合剂。
[0072]
将上述隔膜涂层的浆液通过线棒型涂布机涂布在厚度7μm的pe 微孔基材膜上,最终经过悬浮烘箱烘烤后,形成二每一厚度2.5μm的涂层于pe微孔基材膜的双面上,并取得总厚度12μm的陶瓷涂布隔膜。
[0073]
实施例14
[0074]
本实施例的锂离子电池隔膜涂层的成分和含量为:90.0重量份γ-al2o3(d50粒径1.0μm);10.0重量份pvac-va与pmve-ma交联(交联度25%)形成的共聚物粘合剂。
[0075]
将上述隔膜涂层的浆液通过线棒型涂布机涂布在厚度7μm的pe 微孔基材膜上,最终经过悬浮烘箱烘烤后,形成二每一厚度2.5μm的涂层于pe微孔基材膜的双面上,并取得总厚度12μm的陶瓷涂布隔膜。
[0076]
实施例15
[0077]
本实施例的锂离子电池隔膜涂层的成分和含量为:95.0重量份γ-al2o3(d50粒径6.0μm);5.0重量份pvac-va与pmve-ma交联 (交联度5%)形成的共聚物粘合剂。
[0078]
将上述隔膜涂层的浆液通过凹版辊涂布机涂布在厚度10μm的 pe微孔基材膜上,最终经过烘箱烘烤后,形成一厚度6μm的涂层于pe微孔基材膜的单面上,并取得总厚度16μm的陶瓷涂布隔膜。
[0079]
实施例16
[0080]
本实施例的锂离子电池隔膜涂层的成分和含量为:95.0重量份γ-al2o3(d50粒径6.0μm);5.0重量份pvac-va与pmve-ma交联 (交联度25%)形成的共聚物粘合剂。
[0081]
将上述隔膜涂层的浆液通过凹版辊涂布机涂布在厚度10μm的 pe微孔基材膜上,最终经过烘箱烘烤后,形成一厚度6μm的涂层于 pe微孔基材膜的单面上,并取得总厚度16μm的陶瓷涂布隔膜。
[0082]
实施例17
[0083]
本实施例的锂离子电池隔膜涂层的成分和含量为:90.0重量份γ-al2o3(d50粒径1.6μm);10.0重量份pvac-va与pmve-ma交联(交联度10%)形成的共聚物粘合剂。
[0084]
将上述隔膜涂层的浆液通过线棒型涂布机涂布在厚度7μm的pe 微孔基材膜上,最终经过悬浮烘箱烘烤后,形成二每一厚度2.5μm的涂层于pe微孔基材膜的双面上,并取得总厚度12μm的陶瓷涂布隔膜。
[0085]
实施例18
[0086]
本实施例的锂离子电池隔膜涂层的成分和含量为:90.0重量份γ-al2o3(d50粒径1.6μm);10.0重量份pvac-va与pmve-ma交联(交联度20%)形成的共聚物粘合剂。
[0087]
将上述隔膜涂层的浆液通过线棒型涂布机涂布在厚度7μm的pe 微孔基材膜上,最终经过悬浮烘箱烘烤后,形成二每一厚度2.5μm的涂层于pe微孔基材膜的双面上,并取得总厚度12μm的陶瓷涂布隔膜。
[0088]
实施例19
[0089]
本实施例的锂离子电池隔膜涂层的成分和含量为:93.0重量份γ-al2o3(d50粒径3.0μm);7.0重量份pvac-va与pmve-ma交联 (交联度15%)形成的共聚物粘合剂。
[0090]
将上述隔膜涂层的浆液通过凹版辊涂布机涂布在厚度7μm的pe 微孔基材膜上,最终经过烘箱烘烤后,形成一厚度5μm的涂层于pe 微孔基材膜的单面上,并取得总厚度12μm的陶瓷涂布隔膜。
[0091]
实施例20
[0092]
本实施例的锂离子电池隔膜涂层的成分和含量为:95.0重量份γ-al2o3(d50粒径5.0μm);5.0重量份pvac-va与pmve-ma交联 (交联度15%)形成的共聚物粘合剂。
[0093]
将上述隔膜涂层的浆液通过凹版辊涂布机涂布在厚度7μm的pe 微孔基材膜上,最终经过烘箱烘烤后,形成一厚度5μm的涂层于pe 微孔基材膜的单面上,并取得总厚度12μm的陶瓷涂布隔膜。
[0094]
对比例1
[0095]
本对比例的锂离子电池隔膜涂层的成分和含量为:90.0重量份γ-al2o3(d50粒径1.6μm);10.0重量份普通型聚丙烯酸酯类粘合剂。
[0096]
将上述隔膜涂层的浆液通过线棒型涂布机涂布在厚度7μm的pe 微孔基材膜上,最终经过悬浮烘箱烘烤后,形成二每一厚度2.5μm的涂层于pe微孔基材膜的双面上,并取得总厚度12μm的陶瓷涂布隔膜。
[0097]
对比例2
[0098]
本对比例的锂离子电池隔膜涂层的成分和含量为:90.0重量份α-al2o3(d50粒径1.6μm);10.0重量份pvac-va与pmve-ma交联形成的共聚物粘合剂。
[0099]
将上述隔膜涂层的浆液通过线棒型涂布机涂布在厚度7μm的pe 微孔基材膜上,最终经过悬浮烘箱烘烤后,形成二每一厚度2.5μm的涂层于pe微孔基材膜的双面上,并取得总厚度12μm的陶瓷涂布隔膜。
[0100]
对比例3
[0101]
本对比例的锂离子电池隔膜涂层的成分和含量为:90.0重量份α-al2o3(d50粒径1.6μm);10.0重量份普通型聚丙烯酸酯类粘合剂。
[0102]
将上述隔膜涂层的浆液通过线棒型涂布机涂布在厚度7μm的pe 微孔基材膜上,最终经过悬浮烘箱烘烤后,形成二每一厚度2.5μm的涂层于pe微孔基材膜的双面上,并取得总厚度12μm的陶瓷涂布隔膜。
[0103]
对比例4
[0104]
本对比例的锂离子电池隔膜涂层的成分和含量为:90.0重量份γ
ꢀ‑
al2o3(d50粒径1.6μm);10.0重量份pvac-va与pmve-ma的混合物粘合剂。
[0105]
将上述隔膜涂层的浆液通过线棒型涂布机涂布在厚度7μm的pe 微孔基材膜上,最终经过悬浮烘箱烘烤后,形成二每一厚度2.5μm的涂层于pe微孔基材膜的双面上,并取得总厚度12μm的陶瓷涂布隔膜。
[0106]
具体测试方法介绍如下:
[0107]
1、厚度(gb/t 6672-2001)
[0108]
采用马尔薄膜测厚仪(millimar c1208,德国马尔公司)测定。
[0109]
2、热收缩(gb/t 12027-2004)
[0110]
在室温下分别测定试样沿机器行进方向原始长度l0,垂直于机器行进方向原始长度t0。
[0111]
将试样在恒温恒湿可控烘箱中,按照规定时间以试验温度加热后冷却至原始测试条件下,测定此时试样沿机器行进方向长度l1和垂直于机器行进方向长度t1,计算公式如下:
[0112]
md%=[(l1-l0)/l0]x100%;
[0113]
td%=[(t1-t0)/t0]x100%。
[0114]
3、剥离强度(gb 2792-1998)
[0115]
3-1拉伸仪
[0116]
示值在记录仪满值的10至90%之间,示值误差应在
±
1%以内;试样机应不引起试样在夹具处断裂,施加任何负荷时,试验机上的夹具应能立即对准成一条线。
[0117]
3-2样条取样器
[0118]
直条型标准件,总长200mm,平行部分宽度15
±
0.5mm。
[0119]
3-3千分尺
[0120]
符合gb 6672-2001的要求。
[0121]
3-4胶带
[0122]
scotch brand tape,3m products,core series xq,宽度19mm。
[0123]
3-5试样
[0124]
a.取样方法:采用取样器,沿着md方向采取200mmx15mm(长 x宽)样品。
[0125]
b.使用辅助工具,手推式滚轮,为20n。
[0126]
c.在样片上从下往上推一次。
[0127]
d.放上仪器确定位置。
[0128]
e.确定试样边缘平滑无缺口,可使用投影仪检查试样边缘。
[0129]
f.确定试样外观,应平整、均匀,不得有垃圾、孔洞、针眼、皱折、油污和划伤等缺陷。
[0130]
3-6试验条件
[0131]
a.试验速度:50mm/min;初始夹距:25
±
1mm。
[0132]
b.环境:温度23
±
4℃;湿度20至80%;大气压86至106kpa。
[0133]
3-7试验步骤
[0134]
a.将50mmx19mm(长x宽)的3m双面胶带贴于钢板的上端。
[0135]
b.将待测隔膜的涂布面贴于胶带上,隔膜应平行于钢板。
[0136]
c.将钢板的下端固定在下夹具上,将未贴胶带一端的待测隔膜夹于上夹具中。
[0137]
d.按规定试验条件,按照拉伸试验机操作规定开动试验机,进行试验。
[0138]
e.试样剥离后,读取最大剥离强度。
[0139]
f.按以上步骤测试所有待测样品。
[0140]
3-8计算公式
[0141]
σt=(p/b)x1000
[0142]
σt:剥离强度,n/m;
[0143]
p:最大剥离力,n;
[0144]
b:样品试验宽度,mm;
[0145]
记录每次所测的剥离强度,报告每组的算术平均值,结果精确至整数位。
[0146]
4、锂离子电池的电解液的成分和含量
[0147]
1mol lipf6,ec/emc/dmc=1:1:1(vol%)。
[0148]
5、粘合剂交联度的测定
[0149]
秤取4g干燥交联粘合剂,量取200ml丙酮溶液加入索氏提取器中,开启恒温油浴和回流冷凝水,加热温度为85℃,保持加热回流5 天,期间定时测定它的质量变化;取出样品,用大量水洗去表面的丙酮,然后65℃下真空干燥20小时,直至恒重。
[0150]
6、粘合剂红外光谱的测定
[0151]
运用nicolet is10型傅里叶变换红外(ft-ir)光谱测试交联聚合物粘合剂的结构。在4000~400cm-1
范围内扫描并记录。
[0152]
通过ft-ir方法验证聚(醋酸乙烯酯-乙烯醇)(pvac-va)与聚(甲基乙烯基醚-马来酸酐)(pmve-ma)之间发生交联反应。单纯的pmve-ma上的羰基(c=o)在1708cm-1
处有红外吸收峰。交联反应后,可以发现pmve-ma上的羰基(c=o)转移至1708至1798cm-1
处,显现出现酯基的羰基(c=o)峰,证实交联反应确实发生。
[0153]
表1、隔膜物理性能
[0154]
[0155]
[0156]
[0157][0158]
实施例1的涂层厚度为单面6.0μm,组成为γ-al2o3(d50=5.0μm) 和pvac-va与pmve-ma的交联(交联度15%)共聚物的组合,具有相对高的耐热性能,亦即于150℃情况下热收缩率小于3.0%,具有相对高的粘接性能,亦即于剥离强度大于150n/m,具有相对最高的吸液与保液性能;实施例6和实施例1的不同在于采用d50=6.0μm 的γ-al2o3,150℃情况下热收缩率大于6.0%,虽然其他性能劣势不明显,但是折损耐热性能。实施例10和实施例6的不同在于采用其他种类的两亲性交联共聚物,具体为peg与pmve-ma的交联(交联度15%)共聚物,耐热性和粘接性能明显劣势,吸液与保液性能略显劣势。实施例15和实施例6的不同在于采用交联度5%的pvac-va 与pmve-ma的交联共聚物,耐热性、粘接性和吸液与保液性能均显劣势,且粘接性能明显劣势。实施例16和实施例6的不同在于采用交联度25%的pvac-va与pmve-ma的交联共聚物,耐热性、粘接性和吸液与保液性能均显劣势,且粘接性能明显劣势。
[0159]
实施例2的涂层厚度为2.5μm+2.5μm,组成为γ-al2o
3 (d50=1.6μm)与pvac-va与pmve-ma的交联(交联度15%)共聚物的组合,具有相对高的耐热性能,亦即于150℃情况下热收缩率小于2.0%,具有相对高的粘接性能,亦即于剥离强度大于130n/m,具有相对高的吸液与保液性能;实施例4和实施例2的不同在于采用其他种类的两亲性交联共聚物,具体为peg与pmve-ma的交联(交联度15%)共聚物,耐热性和粘接性能明显劣势,吸液与保液性能略显劣势。实施例5和实施例2的不同在于采用d50=1.0μm的γ-al2o3,耐热性能、吸液与保液性能更优,但是粘接性能明显劣势。实施例7 和8与实施例2的不同在于分别采用交联度5%和25%的pvac-va与 pmve-ma的交联共聚物,耐热性、粘接性和吸液与保液性能均显劣势,且粘接性能明显劣势。实施例17和18与实施例2的不同在于分别采用交联度10%和20%的pvac-va与pmve-ma的交联共聚物,耐热性、粘接性和吸液与保液性能稍显逊色。
[0160]
实施例9和实施例4的不同在于采用d50=1.0μm的γ-al2o3,耐热性能、吸液与保液
性能更优,但是粘接性能显劣势。实施例11和实施例12与实施例4的不同在于分别采用交联度5%和25%的peg 与pmve-ma的交联共聚物,耐热性、粘接性和吸液与保液性能均显劣势,且粘接性能明显劣势。实施例13和实施例14与实施例5的不同在于分别采用交联度5%和25%的peg与pmve-ma的交联共聚物,耐热性、粘接性和吸液与保液性能均显劣势,且粘接性能明显劣势。
[0161]
实施例19的涂层厚度为单面5.0μm,组成为γ-al2o3(d50=3.0μm) 和pvac-va与pmve-ma的交联(交联度15%)共聚物的组合,具有相对高的耐热性能,亦即于150℃情况下热收缩率小于2.0%,具有相对高的粘接性能,亦即于剥离强度大于140n/m,具有相对最高的吸液与保液性能。
[0162]
实施例20的涂层厚度为单面5.0μm,组成为γ-al2o3(d50=5.0μm) 和pvac-va与pmve-ma的交联(交联度15%)共聚物的组合,具有尚好的耐热性能,亦即于150℃情况下热收缩率小于3.0%,具有相对高的粘接性能,亦即于剥离强度大于150n/m,具有相对最高的吸液与保液性能;
[0163]
对比例1的涂层组成为γ-al2o3与普通型聚丙烯酸酯类的组合,对比例2的涂层组成为α-al2o3和pvac与pmve-ma的交联共聚物的组合,对比例3的涂层组成为α-al2o3与普通型聚丙烯酸酯类的组合,对比例4的涂层组成为γ-al2o3和pvac与pmve-ma的混合物经比较可知,实施例的隔膜具有相对高的吸液与保液性能,亦即电解液扩散至最大直径所需的时间减少一半,且电解液保液率提升两倍以上。而且,实施例的隔膜更具有相对高的耐热性能,亦即于150℃情况下热收缩率小于3.0%。此外,实施例的涂层与基材膜具有较好的粘结性能。
[0164]
经比较实施例2与对比例1可知,将普通型聚丙烯酸酯类替换成 pmve-ma的交联共聚物后电解液保持率自125.4%上升至180.6%,增加55.2%;经比较实施例2与对比例2可知,将α-al2o3替换成γ-al2o3后电解液保持率自140.9%上升至180.6%,增加39.7%。藉此,可知pvac-va与pmve-ma的交联共聚物较γ-al2o3对吸液与保液性能的贡献度为高。
[0165]
经比较对比例1与3可知,将α-al2o3替换成γ-al2o3后md与 td热收缩率均减少0.2%,剥离强度提升22n/m,电解液接触角减少 3度,电解液扩散至最大直径所需时间减少5秒,电解液保持率增加 38%;经比较对比例2与3可知,将普通型聚丙烯酸酯类替换成 pmve-ma的交联共聚物后md与td热收缩率分别减少0.5%与 0.4%,剥离强度提升30n/m,电解液接触角减少4.1度,电解液扩散至最大直径所需时间减少7秒,电解液保持率增加53.5%。藉此,也可知pmve-ma的交联共聚物较γ-al2o3对热收缩率、剥离强度、吸液与保液性能的贡献度为高。另经比较实施例2与对比例3可知,将α-al2o3替换成γ-al2o3且将普通型聚丙烯酸酯类替换成pmve-ma 的交联共聚物后md与td热收缩率分别减少0.9%与1.0%,剥离强度提升63n/m,电解液接触角减少7.2度,电解液扩散至最大直径所需时间减少13秒,电解液保持率增加103.1%。藉此,也可知γ-al2o3与pmve-ma的交联共聚物的共同作用对md与td热收缩率、剥离强度、吸液与保液性能的贡献度优于所有单一材料取代的贡献度的总和。
[0166]
以上涉及到公知常识的内容不作详细描述,本领域的技术人员能够理解。
[0167]
以上所述仅为本发明的一些具体实施例而已,并不用以限制本发明,凡在本发明的精神和原则之内,所作的任何修改、等同替换、改进等,均应包含在本发明的保护范围之
内。本项发明的技术性范围并不局限于说明书上的内容,必须要根据权利要求范围来确定其技术性范围。