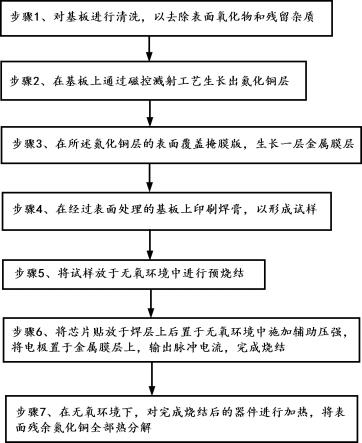
1.本技术涉及脉冲电烧结技术领域,具体涉及一种微纳米金属焊膏脉冲电烧结方法。
背景技术:2.碳化硅器件结温的提升,推动了工业界对高熔点焊膏的需求。微纳米金属焊膏(微纳米铜,微纳米银等)凭借其优异的热电性能和低温烧结高温服役的特点,正被初步应用在车规级碳化硅模块中。现有微纳米金属焊膏普遍采用高温烧结工艺,其相对回流焊工艺耗时较长,在烧结4*4mm2面积以上的芯片时,还需辅助5-10mpa的压强。脉冲电流烧结工艺显著缩短烧结时间,但目前文献中所提及的脉冲电烧结均采用由上到下的垂直烧结模式。该工艺需要的电流通常在1ka以上,若对芯片流通1ka以上的电流,会对芯片造成正向浪涌,导致器件烧毁。因此目前脉冲烧结大多处于试验阶段,远远未达到商业化程度。
3.在现有技术中,基于敷铜基板均匀电流辅助烧结纳米银焊膏温度场的方法,结合敷铜基板铜层形状和印刷纳米银焊膏后电极压头可放置区域,异形电极形状为直角l形,内角为四分之一圆弧过渡,烧结前电极预压在dbc基板两端,施加直流脉冲电流均匀流过焊膏,纳米银焊膏烧结温度场均匀分布,芯片受热均匀。该发明成功解决了电流快速烧结纳米银焊膏过程中存在的温度不均匀的问题,通过设计施加电流的异形电极与位置分布,实现纳米银焊膏脉冲电流辅助烧结过程中温度场的均匀分布,烧结纳米银焊膏igbt芯片/二极管芯片与覆铜陶瓷基板基板的一次性快速烧结连接,获得致密度高达90%以上,大幅提高烧结互连层的机械强度和抗疲劳可靠性,延长使用寿命。现有技术的缺点如下:(1)现有微纳米银/铜焊膏采用高温烧结工艺,耗时较长,在大面积烧结时需要5mpa以上的辅助压强,容易对芯片结构造成损伤;(2)现有焊膏烧结工艺受设备影响较大,烧结参数无法完全匹配实际工艺,在实际应用中还需花时间对烧结参数进行适度调整,提升了推广成本;(3)现有的脉冲烧结工艺电极位于器件的垂直方向,电流从器件上表面方流到基板的背面,该工艺电流达到1ka以上,若应用到实际芯片中,则会造成芯片毁坏;(4)现有方法中电流经由基板上铜层产生欧姆热,对焊膏进行加热,完成烧结,虽可实现芯片平面的电烧结,但该工艺会造成基板表面铜层氧化,不利于接下来键合工艺的实施;另一方面,该方法需要对基板图案进行特殊化处理,无法与现有器件/模块的基板图案相兼容。
技术实现要素:4.为了解决上述技术问题,本技术提出一种微纳米金属焊膏脉冲电烧结方法,本技术所采用的技术方案如下:一种微纳米金属焊膏脉冲电烧结方法,该方法包括如下步骤:步骤1、对基板进行清洗,以去除表面氧化物和残留杂质;
步骤2、在基板上通过磁控溅射工艺生长出氮化铜层;步骤3、在所述氮化铜层的表面覆盖掩膜版,生长一层金属膜层;步骤4、在经过表面处理的基板上印刷焊膏,以形成试样;步骤5、将试样放于无氧环境中进行预烧结;步骤6、将芯片贴放于焊层上后置于无氧环境中施加辅助压强,将电极置于金属膜层上,输出脉冲电流,完成烧结;步骤7、在无氧环境下,对完成烧结后的器件进行加热,将表面残余氮化铜全部热分解。
5.进一步的,所述对基板进行清洗,进一步包括:将基板放置于酸性溶液中进行超声清洗5-10min,以去除铜层表面氧化物。
6.进一步的,所述对铜基板进行清洗,进一步包括:将基板放置于无水乙醇中进行超声清洗2-10min,以去除铜层表面残留杂质,所述残留杂质包括酸性溶液、cu
2+
、cu
+
。
7.进一步的,在步骤2中,靶材为铜,溅射氛围为n2,磁控溅射温度为80-150℃。
8.进一步的,在步骤3中,所述金属膜层的材质为可焊的导电金属,厚度0.05-0.2mm;所述导电金属包括银、铜、金、镍。
9.进一步的,在步骤4中,所述焊膏的材料包括微纳米金属颗粒、碳基材料、以及有机添加物,所述焊膏的厚度为0.08-0.2mm。
10.进一步的,所述微纳米金属颗粒包括微纳米银、微纳米铜,质量比为80-85%;所述碳基材料包括碳纳米管、碳纳米线、片状/粉末状石墨烯,质量比为1-5%;所述有机添加物包括乙二醇、乙醇、松油醇,质量比为10-19%。
11.进一步的,在步骤5中,所述预烧结的温度为110-160℃,时长5-10min。
12.进一步的,在步骤6中,所述辅助压强≤5mpa。
13.进一步的,在步骤7中,所述加热的温度为300-400℃,时长为2-10min。
14.通过本技术实施例,可以获得如下技术效果:(1)本发明所述工艺可以在30s内,完成对器件焊层的烧结,实现芯片和基板互连;本发明工艺步骤简单,无需复杂设计,可兼容现有模块或单管的基板设计;(2)本发明提出的方法,在烧结后不会造成基板铜层氧化,再经过真空加热处理后,可以继续键合;本发明所述工艺中,电极在基板上铜层表面,电流不经过芯片,通过焊层直接加热对微纳米焊膏完成烧结,实现芯片互连,对芯片无损伤。
附图说明
15.为了更清楚地说明本技术实施例中的技术方案,下面将对实施例或现有技术描述中所需要使用的附图作一简单地介绍,显而易见地,下面描述中的附图是本技术的一些实施例,对于本领域普通技术人员来讲,在不付出创造性劳动性的前提下,还可以根据这些附图获得其他的附图。
16.图1 为脉冲烧结工艺截面结构示意图;图2 为脉冲烧结工艺俯视结构示意图;图3为8*8mm2芯片电烧结结构示意图;图4为2*2mm2芯片电烧结结构示意图;
图5为本发明方法的流程示意图。
具体实施方式
17.为使本技术实施例的目的、技术方案和优点更加清楚,下面将结合本技术实施例中的附图,对本技术实施例中的技术方案进行清楚、完整地描述,显然,所描述的实施例是本技术一部分实施例,而不是全部的实施例。基于本技术中的实施例,本领域普通技术人员在没有作出创造性劳动前提下所获得的全部其他实施例,都属于本技术保护的范围。
18.图1 为脉冲烧结工艺截面结构示意图,图2 为脉冲烧结工艺俯视结构示意图。该脉冲烧结的截面从上往下依次是芯片、焊层(80-200um)、金属膜层(银、铜、金等可焊的导电金属,厚度0.05-0.2mm,金属膜层形状不限于矩形、球形、半圆形等基本形状的一种或几种组合,可为单组图形或平行多组图形,每组图形宽度≤2mm,优选1.5mm)、氮化铜层(厚度0.2-2mm)和基板(尺寸参数取决于芯片规格,为市场通用规格,基板的材料包括且不限于纯铜基板、dbc基板、amb基板等,其中焊层底部与氮化铜层接触,两端位于金属膜层上,电极位于金属膜层上,电流按照正电极—金属膜层—焊层—金属膜层—负电极的路径顺序流通。
19.cu3n在300℃下具备热稳定性,当温度超过300℃时cu3n开始逐步热分解为cu单质和n
2,
cu3n的电阻率范围为1-20ω.m。而微纳米金属焊膏在预烧结工艺后随着有机物的分解和挥发,焊膏电阻率从10
10
降低到10-4-10-7
ω.m,若此时正电极输出脉冲电流,电流将会从焊层经过流向负电极,根据欧姆定律,焊层会瞬间升温完成微纳米金属的烧结过程,同时产生的焦耳热会向四周扩散,cu3n在温度提升到300℃后,分解为氮气和单质铜。在烧结过程中,芯片上方会施加不超过5mpa的辅助压强。压强的参与有助于焊层间的金属颗粒形成肩颈结构,提升焊层结构的致密度,降低焊层的空洞率。
20.为实现器件的充分烧结,脉冲电流峰值电压≤1kv,峰值电流范围在1-2ka,脉冲波形单周期为ms数量级,共持续0.1-10s。同时在焊层中可掺杂少量碳基材料(cnts,石墨烯等)提升焊层的电导率,进一步造成焊层与氮化铜层的电阻率数量级差异,保证电流路径按照需求进行。
21.氮化铜层厚度与电压有正向关系,太薄会导致被电压击穿,造成烧结失败,太厚则会导致氮化铜层热扩散不完全,氮化铜为充分热分解,阻碍了焊层与基板上铜层的连接,因此优选厚度范围为0.2-2mm。另一方面,氮化铜层会保护基板在电烧结时被氧气氧化,阻碍后续键合。在完成烧结后,将器件放置于无氧环境(真空,氮气或混氢),加热至300℃-400℃,时长2-10min,将芯片外区域的氮化铜层热分解,从而直接进行下一步工艺。
22.金属膜层是为了供电极放置提供空间,其与焊层边缘连接,有效规划了电流的流通路径。金属膜层形状不限于矩形,可以根据需求设计,如为均匀电流分布,可将金属膜层设计为圆弧状。
23.图5为本发明方法的流程示意图,该微纳米金属焊膏脉冲电烧结方法,包括如下步骤:步骤1、对基板进行清洗,以去除表面氧化物和残留杂质;步骤2、在基板上通过磁控溅射工艺生长出氮化铜层;步骤3、在所述氮化铜层的表面覆盖掩膜版,生长一层金属膜层;步骤4、在经过表面处理的基板上印刷焊膏,以形成试样;
步骤5、将试样放于无氧环境中进行预烧结;步骤6、将芯片贴放于焊层上后置于无氧环境中施加辅助压强,将电极置于金属膜层上,输出脉冲电流,完成烧结;步骤7、在无氧环境下,对完成烧结后的器件进行加热,将表面残余氮化铜全部热分解。
24.所述对基板进行清洗,进一步包括:将基板放置于酸性溶液中进行超声清洗5-10min,以去除铜层表面氧化物。
25.所述对铜基板进行清洗,进一步包括:将基板放置于无水乙醇中进行超声清洗2-10min,以去除铜层表面残留杂质,所述残留杂质包括酸性溶液、cu
2+
、cu
+
。
26.在步骤2中,靶材为铜,溅射氛围为n2,磁控溅射温度为80-150℃。
27.在步骤3中,所述金属膜层的材质为可焊的导电金属,厚度0.05-0.2mm;所述导电金属包括银、铜、金、镍。
28.在步骤4中,所述焊膏的材料包括微纳米金属颗粒、碳基材料、以及有机添加物,所述焊膏的厚度为0.08-0.2mm。
29.所述微纳米金属颗粒包括微纳米银、微纳米铜,质量比为80-85%;所述碳基材料包括碳纳米管、碳纳米线、片状/粉末状石墨烯,质量比为1-5%;所述有机添加物包括乙二醇、乙醇、松油醇,质量比为10-19%。
30.在步骤5中,所述预烧结的温度为110-160℃,时长5-10min。
31.在步骤6中,所述辅助压强≤5mpa。
32.在步骤7中,所述加热的温度为300-400℃,时长为2-10min。
33.在一种实施方式中,8*8mm2芯片所采用的微纳米金属焊膏脉冲电烧结方法如下:1、将基板放置于稀盐酸中超声清洗5min去除铜层表面氧化物;2、将基板放置于无水乙醇中超声清洗5min去除铜层表面酸性溶液、cucl2、cucl等残留杂质;3、通过磁控溅射工艺生长一层氮化铜,厚度0.3mm,靶材为铜,溅射氛围为n2,溅射温度100℃;4、在氮化铜层表面覆盖掩膜版,生长一层金属膜层,材质为银,厚度0.1mm;5、金属膜层为四组重复图形,每组图形间隔0.3mm,图形由矩形和半圆组成,矩形居中,矩形长度8mm,宽度2mm,半圆为两端,半圆直径2mm;6、按照图3所示位置,在经过表面处理的基板上印刷焊膏,焊膏材料主体为纳米铜,粒径50-100nm,质量比为80%,掺杂有碳基材料单壁cnts,质量比为4%,焊膏其余为有机添加物(乙二醇,乙醇,松油醇等),焊层厚度在0.1mm;7、将试样放于无氧环境中进行预烧结,预烧结温度140℃,时长5min;8、将芯片贴放于焊层上,再将器件置于无氧环境中施加辅助压强,压强5mpa,将电极置于金属膜层上,输出1kv/1.2ka脉冲电流6s,完成烧结;9、对烧结后的器件在无氧环境下加热350℃,时长10min,将表面残余氮化铜全部热分解;10、烧结后器件焊层孔隙率为3.2%,最大单一孔隙率为0.6%,剪切强度超过28mpa。
34.在另一种实施方式中,2*2mm2芯片所采用的微纳米金属焊膏脉冲电烧结方法如
下:1、将基板放置于稀硫酸中超声清洗6min去除铜层表面氧化物;2、将基板放置于无水乙醇中超声清洗5min去除铜层表面酸性溶液、cuso4、cu2so4等残留杂质;3、通过磁控溅射工艺生长一层氮化铜,厚度0.2mm,靶材为铜,溅射氛围为n2,溅射温度120℃;4、在氮化铜层表面覆盖掩膜版,生长一层金属膜层,材质为金,厚度0.05mm,宽度0.15mm;5、按照图4所示位置,在经过表面处理的基板上印刷焊膏,焊膏材料主体为纳米银,粒径200-1000nm,质量比为83%,掺杂有碳基材料石墨烯,质量比为3%,焊膏其余为有机添加物(乙二醇,乙醇,松油醇等),焊层厚度在0.15mm;6、将试样放于真空中进行预烧结,预烧结温度120℃,时长5min;7、将芯片贴放于焊层上,再将器件置于氮气中施加辅助压强,压强2mpa,将电极置于金属膜层上,输出800v/1.2ka脉冲电流2s,完成烧结;8、对烧结后的器件在无氧环境下加热320℃,时长5min,将表面残余氮化铜全部热分解;9、烧结后器件焊层孔隙率为2.7%,最大单一孔隙率为0.4%,剪切强度超过35mpa。
35.虽然以上描述了本发明的具体实施方式,但是本领域的技术人员应当理解,这些仅是举例说明,本发明的保护范围是由所附权利要求书限定的。本领域的技术人员在不背离本发明的原理和实质的前提下,可以对这些实施方式作出多种变更或修改,但这些变更和修改均落入本发明的保护范围。