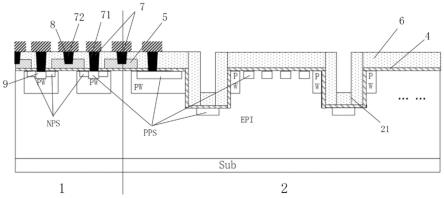
1.本发明涉及半导体技术领域,具体涉及一种碳化硅器件的终端结构及制备方法。
背景技术:2.碳化硅半导体具有禁带宽度大、临界击穿场强高(大约是硅的10倍)、热导率高、载流子饱和漂移速度高等优异的物理和电学特性,使其在高温、高频率、大功率器件电子领域具有广泛地应用前景。
3.目前,碳化硅功率器件的终端结构主要采用vld或者保护环,该终端结构要实现较好的保护需要很大的宽度,通常是外延厚度的8~10倍,所以占用了很大的芯片面积,并且碳化硅衬底的成本相比较硅衬底非常高,现有技术中由于对芯片面积的占用因此需要付出巨大的额外成本。
技术实现要素:4.本发明的目的在于,提供一种碳化硅器件的终端结构,解决以上技术问题;
5.本发明的目的还在于,提供一种碳化硅器件的终端结构的制备方法,解决以上技术问题。
6.本发明所解决的技术问题可以采用以下技术方案来实现:
7.一种碳化硅器件的终端结构,包括,
8.衬底层;
9.外延层,设于所述衬底层上,所述外延层内设有阱区以及位于所述阱区内的源极部,所述外延层上设有至少一个沟槽,所述沟槽穿过所述阱区且延伸至所述外延层内,所述沟槽的底部以及所述外延层的上表面的下方设有注入环;
10.氧化层,设于所述外延层的上表面以及所述沟槽的内表面上;
11.栅极薄膜层,设于所述氧化层上;
12.介质层,设于所述氧化层上并覆盖所述栅极薄膜层,所述沟槽内表面覆盖的所述介质层完全或者部分填充所述沟槽。
13.优选的,包括终端区和原胞区,所述沟槽位于所述终端区内,所述源极部位于所述原胞区内。
14.优选的,位于所述终端区的所述外延层的上表面的下方的各所述注入环间隔一定的距离分布。
15.优选的,位于所述原胞区的一所述阱区内的所述源极部包括第一源极部和第二源极部,一位于所述原胞区的所述注入环设于一所述阱区的所述第一源极部和所述第二源极部之间,所述注入环的两端分别与所述第一源极部和所述第二源极部连接形成源端。
16.优选的,一所述栅极薄膜层的两端分别与相邻的所述阱区相对应设置,靠近一所述栅极薄膜层的第一端的一所述阱区的所述源极部在所述氧化层上的投影至少一部分与所述栅极薄膜层的第一端在所述氧化层上的投影相重合,靠近一所述栅极薄膜层的第二端
的一所述阱区的所述源极部在所述氧化层上的投影至少一部分与所述栅极薄膜层的第二端在所述氧化层上的投影相重合。
17.优选的,所述阱区的上表面和所述源极部的上表面与所述外延层的上表面相重合。
18.优选的,所述外延层为第一导电类型,所述阱区和所述注入环为第二导电类型。
19.优选的,还包括电极孔,所述电极孔内设有金属电极,所述电极孔包括栅极电极孔和源极电极孔,所述栅极电极孔由所述介质层的上表面向下贯穿至所述栅极薄膜层,所述源极电极孔由所述介质层的上表面向下穿过所述氧化层至所述源端的所述注入环。
20.一种碳化硅器件的终端结构的制备方法,用于制作所述的碳化硅器件的终端结构,包括,
21.步骤s1,按照预设定的位置区域于所述外延层内注入所述阱区和所述源极部;
22.步骤s2,按照预设定的位置区域于所述终端区的所述外延层上刻蚀所述沟槽,所述沟槽穿过所述阱区至所述外延层中;
23.步骤s3,沉积第一硬掩模,按照预设定的位置区域于所述第一硬掩模上蚀刻出注入孔;
24.步骤s4,通过所述注入孔注入位于所述沟槽的底部以及所述外延层的上表面的下方的所述注入环,并进行高温退火;
25.步骤s5,去除所述第一硬掩模,于所述外延层的上表面以及所述沟槽的内表面上生长所述氧化层;
26.步骤s6,于所述氧化层上淀积初步的栅极薄膜层;
27.步骤s7,于原胞区的所述初步的栅极薄膜层上沉积第二硬掩模,通过刻蚀去除终端区的所述初步的栅极薄膜层,保留所述原胞区的所述初步的栅极薄膜层;
28.步骤s8,按照预设定的位置区域对所述原胞区的所述初步的栅极薄膜层刻蚀获得所述栅极薄膜层;
29.步骤s9,于所述外延层以及所述栅极薄膜层上沉积所述介质层。
30.优选的,还包括,
31.步骤s10,按照预设定的位置区域于所述介质层上蚀刻出电极孔后沉积金属层,并对所述金属层按照预设定的位置区域刻蚀后形成金属电极。
32.本发明的有益效果:由于采用以上技术方案,本发明通过在器件的终端设计多个沟槽,使传统的平面场限环结构向沟槽中扩展,既能提供较高的击穿电压实现对终端原胞区的保护,又可以减小目前碳化硅器件的终端结构尺寸。
附图说明
33.图1为本发明实施例的碳化硅器件终端结构实施例结构;
34.图2为本发明实施例的碳化硅器件阱区和源极部注入示意图;
35.图3为本发明实施例的碳化硅器件终端结构沟槽刻蚀示意图;
36.图4为本发明实施例的碳化硅器件注入环硬掩模刻蚀示意图;
37.图5为本发明实施例的碳化硅器件注入环形成示意图;
38.图6为本发明实施例的碳化硅器件氧化层形成示意图;
39.图7为本发明实施例的碳化硅器件多晶硅沉积示意图;
40.图8为本发明实施例的碳化硅器件终端区多晶硅刻蚀示意图;
41.图9为本发明实施例的碳化硅器件多晶硅栅形成示意图;
42.图10为本发明实施例的碳化硅器件介质层沉积示意图;
43.图11为本发明实施例的碳化硅器件金属化开孔示意图;
44.图12为本发明实施例的终端结构的制备方法的步骤示意图。
具体实施方式
45.下面将结合本发明实施例中的附图,对本发明实施例中的技术方案进行清楚、完整地描述,显然,所描述的实施例仅仅是本发明一部分实施例,而不是全部的实施例。基于本发明中的实施例,本领域普通技术人员在没有作出创造性劳动的前提下所获得的所有其他实施例,都属于本发明保护的范围。
46.需要说明的是,在不冲突的情况下,本发明中的实施例及实施例中的特征可以相互组合。
47.下面结合附图和具体实施例对本发明作进一步说明,但不作为本发明的限定。
48.一种碳化硅器件的终端结构,如图1所示,包括,
49.衬底层sub;
50.外延层epi,设于衬底层sub上,外延层epi内设有阱区pw以及位于阱区pw内的源极部nps,外延层epi上设有至少一个沟槽21,沟槽21穿过阱区pw且延伸至外延层epi内,沟槽21的底部以及外延层epi的上表面的下方设有注入环pps;
51.氧化层4,设于外延层epi的上表面以及沟槽21的内表面上;
52.栅极薄膜层5,设于氧化层4上;
53.介质层6,设于氧化层4上并覆盖栅极薄膜层5,位于沟槽21内的介质层6完全或部分填充沟槽21。
54.具体的,现有技术中碳化硅功率器件的终端结构主要采用vld或者保护环,现有技术中终端结构要实现较好的保护需要很大的宽度,通常是外延层epi厚度的8~10倍,所以占用了很大的芯片面积;
55.而本发明通过于碳化硅终端结构的终端区2设计了一个或一个以上的沟槽21(沟槽21穿过阱区pw到达外延层epi),使得该结构相比较现有技术中的vld、场限环器件等终端结构具有较小的尺寸。
56.进一步的,沟槽21的底部有不同于外延层epi的第二导电类型的注入环pps,并且非沟槽区有间隔设置的第二导电类型的注入环pps,较优的,本发明的设计使平面场限环结构向沟槽21中扩展,既能提供较高的击穿电压实现对终端区2、原胞区1的保护,又可以减小碳化硅器件的终端结构尺寸。
57.较优的,本发明中第一导电类型为n型或p型,第二导电类型为与第一导电类型相对应的p型或n型,因此本发明中的碳化硅器件可以是n型或p型的,本实施例以制作n型碳化硅mosfet器件为例进行描述,如需制作p型碳化硅器件,只需将描述中导电类型的n型和p型互换。
58.具体的,本发明中沟槽21的两侧包围有阱区pw,进一步具体的,本发明中的阱区pw
为第二导电类型的p阱区,相应的,注入环pps也采用第二导电类型的p型注入环。
59.进一步具体的,本发明中所指的碳化硅器件可以是平面型或沟槽型mosfet器件,也可以是平面型或沟槽型碳化硅igbt器件。
60.在一种较优的实施例中,包括终端区2和原胞区1,沟槽21位于终端区2内,源极部nps位于原胞区1内;
61.具体的,位于终端区2的注入环pps可以起到对碳化硅器件的保护作用。
62.在一种较优的实施例中,位于终端区2的外延层epi的上表面的下方的各注入环间隔一定的距离分布。
63.在一种较优的实施例中,位于原胞区1的一阱区pw内的源极部nps包括第一源极部和第二源极部,一位于原胞区1的注入环pps设于一阱区pw的第一源极部和第二源极部之间,注入环pps的两端分别与第一源极部和第二源极部连接形成源端9。
64.在一种较优的实施例中,一栅极薄膜层5的两端分别与相邻的阱区pw相对应设置,靠近一栅极薄膜层5的第一端的一阱区pw的源极部nps在氧化层4上的投影至少一部分与栅极薄膜层5的第一端在氧化层4上的投影相重合,靠近一栅极薄膜层5的第二端的一阱区pw的源极部nps在氧化层4上的投影至少一部分与栅极薄膜层5的第二端在氧化层4上的投影相重合。
65.具体的,本发明中栅极薄膜层5为多晶硅。
66.在一种较优的实施例中,阱区pw的上表面和源极部nps的上表面与外延层epi的上表面相重合。
67.在一种较优的实施例中,外延层epi为第一导电类型,阱区pw和注入环pps为第二导电类型。
68.在一种较优的实施例中,还包括电极孔7,电极孔7内设有金属电极8,电极孔7包括栅极电极孔72和源极电极孔71,栅极电极孔72由介质层6的上表面向下贯穿至栅极薄膜层5,源极电极孔71由介质层6的上表面向下穿过氧化层4至源端9的注入环pps。
69.一种碳化硅器件的终端结构的制备方法,用于制作任意一项实施例中的碳化硅器件的终端结构,如图12所示,包括,
70.步骤s1,按照预设定的位置区域于外延层epi内注入阱区pw和源极部nps;具体的,本发明通过沉积硬掩模,通过光刻版定义出图形来设定阱区pw和源极部nps的注入区域;如图2所示;
71.步骤s2,按照预设定的位置区域于终端区2的外延层epi上刻蚀沟槽21,沟槽21穿过阱区pw至外延层epi中;具体的,本发明通过沉积硬掩模,通过光刻版定义出图形来设定沟槽21的蚀刻区域;如图3所示;
72.步骤s3,沉积第一硬掩模11,按照预设定的位置区域于第一硬掩模11上蚀刻出注入孔111;如图4所示;
73.步骤s4,通过注入孔111注入位于沟槽21的底部以及外延层epi的上表面的下方的注入环pps,并进行高温退火;如图5所示;
74.步骤s5,去除第一硬掩模11,于外延层epi的上表面以及沟槽21的内表面上生长氧化层4;如图6所示;
75.步骤s6,于氧化层4上淀积初步的栅极薄膜层51;如图7所示;
76.步骤s7,于原胞区1的初步的栅极薄膜层51上沉积第二硬掩模12,通过刻蚀去除终端区2的初步的栅极薄膜层51,保留原胞区1的初步的栅极薄膜层51;如图8所示;
77.步骤s8,按照预设定的位置区域对原胞区1的初步的栅极薄膜层51刻蚀获得栅极薄膜层5;如图9所示;
78.步骤s9,于外延层epi以及栅极薄膜层5上沉积介质层6;如图10所示。
79.在一种较优的实施例中,还包括,
80.步骤s10,按照预设定的位置区域于介质层6上蚀刻出电极孔7后沉积金属层,并进一步对金属层按照预设定的位置区域刻蚀后形成金属电极8;如图11所示。
81.在一种具体的实施例中,本发明中终端结构的制作过程为,
82.于外延层epi注入p阱区pw和源极部nps后,在终端区2进行沟槽21刻蚀,沟槽21穿过p阱区pw到达外延层epi;
83.沉积硬掩模,通过光刻版定义出图形,进行硬掩模干法刻蚀后注入注入环pps,在原胞区1、终端区2同时形成第二导电类型的注入环pps;
84.去除硬掩模后,进行栅氧化层4生长,原胞区1终端区2都覆盖一层氧化层4;
85.沉积多晶硅,通过光刻版定义图形,湿法刻蚀去掉终端区2沟槽21内及外延层epi表面的多晶硅层,之后通过光刻版定义图形,干法刻蚀多晶硅形成原胞区1的多晶硅材质的栅极薄膜层5;
86.沉积介质层6,进行电极孔7的光刻刻蚀;
87.沉积金属层,光刻刻蚀后形成器件的栅电极和源电极;钝化层沉积,使沟槽21完全填充。
88.综上,本发明在碳化硅器件的终端结构的终端区2设计了若干沟槽21,沟槽21都穿过阱区pw到达外延层epi,沟槽21的两侧也有阱区pw包围,同时沟槽21底部及终端的非沟槽区间隔分布着注入环pps,使得本发明的碳化硅器件的终端结构既能提供较高的击穿电压实现对终端原胞区的保护,又可以减小目前碳化硅器件的终端结构尺寸,从而降低了器件的成本。
89.以上所述仅为本发明较佳的实施例,并非因此限制本发明的实施方式及保护范围,对于本领域技术人员而言,应当能够意识到凡运用本发明说明书及图示内容所作出的等同替换和显而易见的变化所得到的方案,均应当包含在本发明的保护范围内。