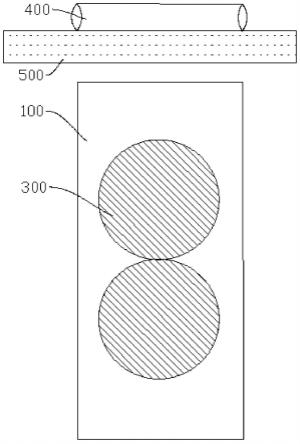
1.本发明涉及晶圆加工领域,特别涉及一种晶圆贴膜设备及晶圆贴膜方法。
背景技术:2.相关技术中,在布置晶圆上的线路时,制作方法一般为在溅镀好的晶圆上涂上一层感光材料,通常采用旋涂技术将感光材料铺于表面,旋涂的光刻胶固化后厚度仅为几微米,而在电镀过程中,感光材料的厚度很难达到电镀铜的厚度,且当电镀铜的厚度大于感光材料的厚度时,容易产生夹膜的现象,从而在蚀刻的时候会造成一些开路。
技术实现要素:3.本发明旨在至少解决现有技术中存在的技术问题之一。为此,本发明提出一种晶圆贴膜设备,能够避免在电镀过程中产生夹膜的现象。
4.本发明还提出一种具有上述晶圆贴膜设备的晶圆贴膜方法。
5.根据本发明的第一方面实施例的晶圆贴膜设备,所述晶圆贴膜设备用于向所述晶圆贴附干膜,所述晶圆贴膜设备包括:
6.第一板,所述第一板开设有凹槽,所述凹槽用于放置所述晶圆;
7.送料机构,所述送料机构能够将所述干膜贴附于所述晶圆;
8.切割工具,所述切割工具能够沿所述晶圆的边缘切割所述干膜。
9.根据本发明实施例的晶圆贴膜设备,至少具有如下有益效果:通过晶圆贴膜设置向晶圆表面贴附相应大小的干膜,由于干膜厚度多种多样,能够适应不同电镀铜的铜厚,通过选择合适厚度的干膜可以避免在电镀过程中产生夹膜的现象。
10.根据本发明的一些实施例,所述晶圆贴膜设备还包括第二板,所述凹槽贯穿所述第一板,所述第二板叠放于所述第一板的下方。
11.根据本发明的一些实施例,所述晶圆贴膜设备还包括夹持件,所述夹持件夹持所述第一板和所述第二板。
12.根据本发明的一些实施例,所述凹槽的深度与所述晶圆的厚度相同。
13.根据本发明的第二方面实施例的晶圆贴膜方法,采用第一方面实施例的晶圆贴膜设备向所述晶圆贴附干膜,所述晶圆贴膜方法包括如下步骤:
14.s1、准备所述晶圆贴膜设备和预设厚度的所述干膜;
15.s2、将所述晶圆放置于所述凹槽中;
16.s3、将所述干膜贴附于所述晶圆上;
17.s4、沿所述晶圆的边缘切割所述干膜。
18.根据本发明实施例的晶圆贴膜方法,至少具有如下有益效果:采用向晶圆贴附干膜的方式,通过晶圆贴膜设备向晶圆贴附预设厚度的干膜,以满足电镀铜的铜厚需求,可以避免在电镀过程中产生夹膜的现象。
19.根据本发明的一些实施例,所述晶圆贴膜方法还包括:
20.s5、依次对所述干膜进行曝光、显影,在所述干膜上形成预设图案;
21.s6、向所述预设图案区域电镀。
22.根据本发明的一些实施例,所述s1包括:
23.s1.1、裁切所述凹槽以使所述凹槽贯穿所述第一板;
24.s1.2、准备第二板,将所述第二板叠放于所述第一板下方。
25.根据本发明的一些实施例,在所述s1.2步骤后夹持所述第一板与所述第二板。
26.根据本发明的一些实施例,所述晶圆贴膜方法还包括:在所述干膜贴向所述晶圆贴附过程中,所述第二板对所述晶圆进行临时固定。
27.根据本发明的一些实施例,所述晶圆贴膜方法在所述s6步骤后还设有:
28.s7、退膜,使用腐蚀剂将所述干膜溶解,以将所述干膜从所述晶圆上去除。
29.本发明的附加方面和优点将在下面的描述中部分给出,部分将从下面的描述中变得明显,或通过本发明的实践了解到。
附图说明
30.下面结合附图和实施例对本发明做进一步的说明,其中:
31.图1为本发明实施例的第一板的结构示意图;
32.图2为本发明实施例的结构示意图;
33.图3为本发明实施例的第二板的结构示意图;
34.图4为本发明实施例的第一板和第二板配合的截面图;
35.图5为本发明实施例的晶圆贴膜后的结构示意图。
36.附图标记:第一板100、凹槽110、第二板200、晶圆300、干膜400、送料机构500、夹持件600。
具体实施方式
37.下面详细描述本发明的实施例,所述实施例的示例在附图中示出,其中自始至终相同或类似的标号表示相同或类似的元件或具有相同或类似功能的元件。下面通过参考附图描述的实施例是示例性的,仅用于解释本发明,而不能理解为对本发明的限制。
38.在本发明的描述中,需要理解的是,涉及到方位描述,例如上、下、前、后、左、右等指示的方位或位置关系为基于附图所示的方位或位置关系,仅是为了便于描述本发明和简化描述,而不是指示或暗示所指的装置或元件必须具有特定的方位、以特定的方位构造和操作,因此不能理解为对本发明的限制。
39.在本发明的描述中,若干的含义是一个以上,多个的含义是两个以上,大于、小于、超过等理解为不包括本数,以上、以下、以内等理解为包括本数。如果有描述到第一、第二只是用于区分技术特征为目的,而不能理解为指示或暗示相对重要性或者隐含指明所指示的技术特征的数量或者隐含指明所指示的技术特征的先后关系。
40.本发明的描述中,除非另有明确的限定,设置、安装、连接等词语应做广义理解,所属技术领域技术人员可以结合技术方案的具体内容合理确定上述词语在本发明中的具体含义。
41.本发明的描述中,参考术语“一个实施例”、“一些实施例”、“示意性实施例”、“示
例”、“具体示例”、或“一些示例”等的描述意指结合该实施例或示例描述的具体特征、结构、材料或者特点包含于本发明的至少一个实施例或示例中。在本说明书中,对上述术语的示意性表述不一定指的是相同的实施例或示例。而且,描述的具体特征、结构、材料或者特点可以在任何的一个或多个实施例或示例中以合适的方式结合。
42.在本发明第一方面实施例中,参考图1和图2,晶圆贴膜设备用于向晶圆300贴附干膜400,晶圆贴膜设备包括:第一板100、送料机构500、切割工具(本发明中的切割工具为刀具,至此不在附图中标出),其中,第一板100开设有凹槽110,凹槽110用于放置晶圆300;送料机构500能够将干膜400贴附于晶圆300;切割工具能够沿晶圆300的边缘切割干膜400。通过将晶圆300放置于凹槽110中,利用送料机构500将干膜400贴附于晶圆300上,随之利用切割工具沿晶圆300的边缘将贴附于晶圆300上的干膜400切割。传统技术中于晶圆300上涂抹一层感光材料,并使用旋涂技术将感光材料铺于晶圆300表面,而旋涂的光刻胶固化后的厚度仍达不到与电镀铜所需的标准,因此会导致对晶圆300进行电镀铜的过程中产生夹膜现象,本技术采用向晶圆贴附干膜替换传统的旋涂感光材料的方式,通过晶圆贴膜治具向晶圆表面贴附相应大小的干膜,由于干膜400厚度多种多样,能够适应不同电镀铜的铜厚,通过选择合适厚度的干膜400可以避免在电镀过程中产生夹膜的现象,并且干膜为固态结构,干膜贴附于晶圆后即可进行后续加工,无需等待固化,晶圆的加工工艺简单,提高了晶圆的加工效率。另一方面,本发明采用的晶圆贴膜设备仅需要准备第一板100,并在第一板100上开设凹槽110,便可以将晶圆300放置于第一板100上,且将第一板100送至送料机构500,利用送料机构500将干膜400贴附于第一板100上便可实现将干膜400贴附于晶圆300上,该工艺简单且操作方便,实用度高。
43.需要说明的是,传统的自动贴膜机通常利用吸盘吸附干膜400贴附于第一板100的表面,且自动贴膜机只适用于对大尺寸的方形板进行贴膜,晶圆300尺寸较小且通常为圆形,自动贴膜机无法直接对尺寸较小的晶圆300进行贴膜。通过利用本技术中的晶圆贴膜设备,可以使尺寸较小的晶圆300亦能适用于传统的送料机构500中的贴膜工序。可以理解的是,本领域技术人员可以通过选择合适的第一板100的尺寸,将晶圆300置于第一板100上的凹槽110后,便可以使自动贴膜机能够用于对晶圆300贴附干膜400,从而,借助现有的自动贴膜机即可实现向晶圆贴附干膜,并能克服电镀时夹膜的缺陷,同时可以节省成本,减少人工劳动力。
44.为了提高第一板100的空间利用率和提高晶圆300的贴膜效率,第一板100设有多个凹槽110,凹槽110可以在第一板100上阵列排布,以提高第一板100的空间利用率,同时也能提高贴膜效率;在一个实施例中,如图1所示,本发明的第一板100开设了两个凹槽110,以使第一板100的空间利用率达到最大,第一板100上设置两个凹槽110,便可以使送料机构500可以一次性对两个晶圆300同时进行贴膜,提高了贴膜效率。
45.在一些实施例中,为了使干膜400对晶圆300的贴附效果更佳,凹槽110的深度与晶圆300的厚度相同,由于凹槽110的深度与晶圆300的厚度相同,致使晶圆300放置于凹槽110中时,晶圆300的表面能够与第一板100的表面持平,从而使送料机构500将干膜400贴附于第一板100表面的同时还能够将干膜400贴附于晶圆300的表面。
46.在一些实施例中,参考图3和图4,由于仅仅使用第一板100以实现对晶圆300的固定的过程中,为了使干膜400更好地贴附于晶圆300上,需要将凹槽110的深度开设与晶圆
300的厚度相同,其对凹槽110深度的开设过程需要一定的精度,操作非常不方便,至此,本发明还设置了第二板200,仅需选择第一板100的厚度与晶圆300的厚度相同,再通过将凹槽110贯穿第一板100,将第二板200叠放于第一板100下方,即可实现对晶圆300的固定。
47.可以理解的,由于设置了第二板200,避开了第一板100中凹槽110深度的开设精度的控制,能够减少人工劳动力。
48.在一些实施例中,参考图4,晶圆贴膜设备还包括夹持件600,夹持件600夹持第一板100和第二板200,设置夹持件600可以将第一板100和第二板200进行夹持,以防第一板100、第二板200在贴膜过程中互相分离。
49.可以理解的是,由于第一板100叠放于第二板200上时,第一板100与第二板200之间仍具有一定的缝隙,从而导致晶圆300容置于凹槽110中时,晶圆300上存在部分待贴膜的表面低于第一板100的表面,进而导致低于第一板100的晶圆300表面与干膜400之间的贴附能力低。因此通过设置夹持件600,还可以使第一板100和第二板200之间能够紧密连接,从而消除了第一板100与第二板200之间存在间隙而导致晶圆300表面低于第一板100表面的情况发生。
50.在本发明的第二方面实施例中提供了一种晶圆贴膜方法,采用上述的晶圆贴膜设备向晶圆300贴附干膜400,晶圆贴膜方法包括如下步骤:
51.s1、准备晶圆贴膜设备和预设厚度的干膜400,为了满足所需的电镀铜的厚度,预设的干膜400的膜厚大于所需电镀铜的铜厚;
52.s2、将晶圆300放置于凹槽110中,使晶圆300能够跟随第一板100一同进入送料机构500中;
53.s3、将干膜400贴附于晶圆300上,通过送料机构500将干膜400贴附于第一板100上,由于晶圆300位于第一板100上的凹槽110中,从而,干膜400能贴附于晶圆300上;
54.s4、沿晶圆300的边缘切割干膜400,本发明使用刀具沿晶圆300的边缘对干膜400进行切割。
55.通过s1-s4将干膜400贴附于晶圆300上,步骤简单且操作方便,能够大大减少人工劳动力。
56.可以理解的是,传统技术中于晶圆300上涂抹一层感光材料,并使用旋涂技术将感光材料铺于晶圆300表面,而旋涂的光刻胶固化后的厚度仍达不到与电镀铜所需的标准,因此会导致对晶圆300进行电镀铜的过程中产生夹膜现象,本发明通过将干膜400的厚度与电镀铜的铜厚达到一致,可以避免电镀铜和干膜400之间产生夹膜的现象。
57.在一些实施例中,晶圆贴膜方法还有:s5、依次对干膜400进行曝光、显影,在干膜400上形成预设图案;s6、向预设图案区域电镀。具体的,选用与预设图案匹配的掩膜板,曝光过程中掩膜板遮挡干膜,曝光后干膜的表面凸显出预设的图案,预设图案区域的干膜呈凹陷状态,在电镀过程中,晶圆300上包括需要电镀的部分(即预设图案区域)和不需要电镀的部分,其中,不需要电镀的部分由干膜400进行绝缘,需要电镀的部分向预设图案区域电镀铜上。传统加工方式中,受旋涂工艺的限制,电镀铜的厚度容易大于感光材料层的厚度,而产生夹膜的现象,本发明通过选用合适厚度的干膜400,利用干膜400的厚度大于电镀铜的厚度,所以在s6的电镀过程中能够避免产生夹膜的问题。
58.在一些实施例中,s1还可以包括:
59.s1.1、选择第一板100的厚度和晶圆300的厚度相同,裁切凹槽110以使凹槽110贯穿第一板100;
60.s1.2、准备第二板200,将第二板200叠放于第一板100下方。
61.由于设置了第二板200,仅需选择第一板100的厚度与晶圆300的厚度相同,再通过将凹槽110贯穿第一板100,将第二板200叠放于第一板100下方,即可实现对晶圆300的固定。
62.在一些实施例中,在s1.2步骤后夹持第一板100与第二板200,根据第一方面实施例中所提及的,将第一板100和第二板200夹持后能避免晶圆300在贴膜过程中与第一板100、第二板200分离的风险。
63.在一些实施例中,为了避免放置于凹槽110中的晶圆300与第一板100的固定不充分,晶圆贴膜方法还有:在干膜400贴向晶圆300贴附过程中,第二板200对晶圆300进行临时固定。
64.可以理解的是,送料机构500将干膜400贴附于晶圆300后,在脱离晶圆300的过程中,送料机构500容易将晶圆300带离凹槽110,导致干膜400与第一板100的表面存在空隙而贴附不全面,且影响后续的切割过程,因此本发明设置了双面胶置于第二板200上以对晶圆300进行临时固定。可以理解的是,在其他实施例中,亦可以利用胶水对晶圆300进行临时固定;还可以将第二板200开设贯穿的通孔,利用吸附工具于第二板200背离第一板100的一侧朝通孔的方向进行抽吸,从而晶圆300被吸附固定于第二板200表面。
65.在一些实施例中,本发明的晶圆贴膜方法在s6步骤后还设有:s7、退膜,使用腐蚀剂将干膜400溶解,以将干膜400从晶圆300上去除。
66.可以理解的,在将电镀铜电镀于晶圆300上后,需要将干膜400从晶圆300的表面去掉,而由于电镀后的电镀铜被干膜400包覆,从而增大了将干膜400从晶圆300上退去的工作难度,至此,本发明利用腐蚀剂将干膜400溶解便可以很好地将干膜400从晶圆300上除去,通过对晶圆300上的腐蚀液和残留的干膜400进行清洗便可以很好地清理电镀后的晶圆300的表面。
67.上面结合附图对本发明实施例作了详细说明,但是本发明不限于上述实施例,在所属技术领域普通技术人员所具备的知识范围内,还可以在不脱离本发明宗旨的前提下作出各种变化。此外,在不冲突的情况下,本发明的实施例及实施例中的特征可以相互组合。