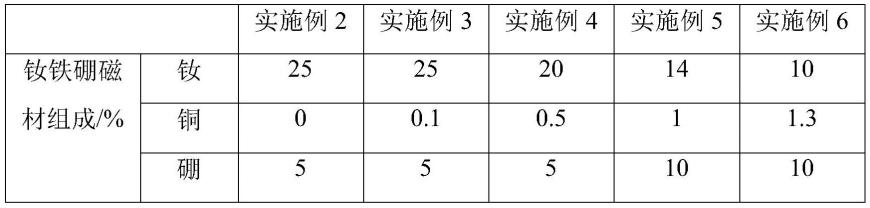
1.本技术涉及钕铁硼磁材技术领域,更具体地说,它涉及一种电机用钕铁硼磁材及其制备方法。
背景技术:2.烧结钕铁硼磁材具有高磁能积、高剩磁和高矫顽力等特点,是目前应用最广泛的稀土永磁材料,尤其是广泛应用于电机领域。在新能源电机中,利用永磁体以激发磁场,在改善电机运行时的性能的同时,降低了电机的电力消耗。
3.针对上述中的相关技术,发明人认为在新能源电机的使用过程中,电机不可避免会发热,当电机长时间使用后,钕铁硼磁体在持续高温下易产生退磁现象。因而,如果能进一步提升现有钕铁硼磁体的内禀矫顽力,就可以进一步提高磁体的高温稳定性,从而降低对电机的散热和最高功率限制的要求,拓宽钕铁硼磁体在电机领域的应用范围。
技术实现要素:4.为了提高钕铁硼磁体的内禀矫顽力,从而提高磁体的高温稳定性,本技术提供一种电机用钕铁硼磁材及其制备方法。
5.本技术提供的一种电机用钕铁硼磁材及其制备方法采用如下的技术方案:第一方面,本技术提供一种电机用钕铁硼磁材,采用如下的技术方案:一种电机用钕铁硼磁材,包括以下重量百分比的组分:钕10-20wt%,铜0.1-1wt%,硼5
‑ꢀ
10wt%,铝0.1-1wt%,钆1-6wt%,铌0.1-1wt%,铈10-25wt%,三氧化二锑0.01-0.15wt%,余量为铁和不可避免的杂质。
6.通过采用上述技术方案,电机用的钕铁硼磁材在使用过程难免会因为电机发热而产生退磁,为了提高钕铁硼磁材的工作寿命,拓宽钕铁硼磁材的应用领域,需要提高钕铁硼磁材的高温稳定性,而内禀矫顽力高的钕铁硼高温稳定性好,考虑到钕铁硼磁材在制备过程中较易产生大晶粒和空洞,而大晶粒和空洞都会严重降低磁体的内禀矫顽力,因此通过添加三氧化二锑以抑制大晶粒的形成,在烧结的过程中,三氧化二锑反应生成尖晶石相,尖晶石相在晶界处偏析,产生钉扎效应,限制了晶界的移动,抑制晶粒的长大,有效提高钕铁硼磁材的内禀矫顽力。
7.优选的,所述三氧化二锑在投料前经聚硅氮烷分散处理,所述聚硅氮烷分散处理的添加重量为所述三氧化二锑的6.7-10倍。
8.优选的,所述聚硅氮烷添加的重量为所述三氧化二锑的8.3倍。
9.通过采用上述技术方案,三氧化二锑是粉状,在烧结过程中易团聚,故通过将三氧化二锑分散于液态的聚硅氮烷内以保证三氧化二锑与其他原料充分接触,由于聚硅氮烷是粘稠状液体,聚硅氮烷同时起到了粘接其他原料的效果,促进原料的致密化,在烧结过程中,聚硅氮烷在高温下裂解产生氮化硅陶瓷,氮化硅本身具有润滑性,起到了填充粉料间缝隙的作用,提高钕铁硼磁材的内禀矫顽力,同时,氮化硅陶瓷具有高温抗氧化性,还能抵抗
冷热冲击,提高了钕铁硼磁材的高温稳定性。随着聚硅氮烷含量的增加,制成的钕铁硼磁材的高温稳定性不断提升,但是聚硅氮烷含量过高时,钕铁硼磁材的磁性受到影响。
10.优选的,所述三氧化二锑的分散处理步骤为:将所述三氧化二锑置于所述聚硅氮烷内,超声处理5-10min,超声完毕后静置5-10min,再次超声处理2-5min,即得经所述聚硅氮烷分散处理的三氧化二锑。
11.通过采用上述技术方案,将三氧化二锑浸润在聚硅氮烷内,使其随着聚硅氮烷一起流动,这样虽然可以在一定程度上促进三氧化二锑与制备钕铁硼的其他原料的接触,但是在溶液中的三氧化二锑仍然存在自发团聚的趋势,三氧化二锑与其他原料的接触不够充分,而超声具有良好的分散质量,采用先后两次超声,抑制三氧化二锑的团聚效应,使得三氧化二锑在聚硅氮烷内分散并均匀分布,从而三氧化二锑可随着聚硅氮烷的流动而与其他原料充分接触,提高三氧化二锑对大晶粒的抑制效果。
12.优选的,所述聚硅氮烷为全氢聚硅氮烷。
13.通过采用上述技术方案,全氢聚硅氮烷具有良好的防锈、防碱和耐盐性能以及一定的耐酸性能,且对金属的附着力好,可对金属粉末起到良好的粘接作用,同时,全氢聚硅氮烷在较温和条件下即可裂解生成具有良好抗氧化性的氮化硅陶瓷。
14.第二方面,本技术提供一种电机用钕铁硼磁材的制备方法,采用如下的技术方案:一种电机用钕铁硼磁材的制备方法,包括以下步骤:s1、熔融甩带:将钕、铜、硼、铝、钆、铌、铈和铁按照设定的重量比投入真空熔炼炉中,抽真空后充氩气,使这些原料在氩气保护下熔炼,熔炼后浇铸甩带,得到甩带薄片;s2、氢破研磨:将所述甩带薄片投入氢破炉中氢破,得到氢破料,将所述氢破料投入气流磨以进行气流研磨,得到磁粉;s3、球磨制粉:按照设定的重量比称取三氧化二锑,将三氧化二锑在氩气保护下通过球磨机研磨得到三氧化二锑细粉;s4、分散处理:将所述三氧化二锑细粉置于所述聚硅氮烷内并分散;s5、压制成型:将所述磁粉和经所述聚硅氮烷分散处理的三氧化二锑混合均匀后一起置于模具中,压制成型并等静压处理,得到烧结生坯;s6、烧结加工:将所述烧结生坯投入真空烧结炉中,在氮气保护下烧结,烧结完毕后分阶段快速冷却至室温,并回火时效热处理,得到烧结钕铁硼磁材。
15.通过采用上述技术方案,大晶粒的存在抑制了磁材的内禀矫顽力,通过快速冷却使得磁材在形核过程中的温度滞后现象更加明显,造成过冷度的增加,过冷度越大,晶核生成的临界半径越小,则晶粒的尺寸越小;同时,快速冷却使得原子的移动能力减弱,众多晶核形成后来不及充分长大,这也使得晶粒的尺寸减小。
16.优选的,s2中,将所述氢破料在气流磨中粉碎至粒径为3-4μm。
17.通过采用上述技术方案,随着磁粉粒径的减小,磁材主相均匀性不断上升,从而最终制备的磁材的内禀矫顽力提高,但是当磁粉粒径过小时,为了得到该粒径的磁粉,氢破料在气流磨中进行气流研磨的时间增长,磁粉与氧气充分接触,在最终烧结过程中,富钕相与氧元素反应,晶界处孔洞的数量增加,反而影响磁材的内禀矫顽力,因而通过控制磁粉的粒径,确保磁材的内禀矫顽力提高。
18.优选的,s3中,三氧化二锑在球磨机中球磨2-3h。
19.通过采用上述技术方案,随着球磨时间的延长,三氧化二锑的粒径减小,比表面积增大,从而在烧结过程中三氧化二锑与其他原料的接触更加充分,但是粒径过小时,三氧化二锑易发生团聚现象,通过控制球磨的时间,保证三氧化二锑与其他原料充分接触。
20.优选的,s6中,烧结生坯在烧结完毕后,先以5-8℃/min降温至700℃,保温一段时间,再以3-5℃/min降温至室温。
21.通过采用上述技术方案,若烧结过后冷却速度过快,熔融的富钕相产生大量团聚,不能较均匀地沿着主相晶界分布,影响最终制得的钕铁硼磁材的磁性能,通过控制冷却速度,在控制晶粒尺寸大小以提高内禀矫顽力的同时,保证钕铁硼磁材的磁性能。
22.优选的,s6中,当温度降至室温后,以2-4℃/min升温至500℃,保温2-3h后,待真空烧结炉内温度自然降至室温,再以2-4℃升温至350℃,保温3-4h后,等待真空烧结炉内温度降至室温。
23.通过采用上述技术方案,在烧结时,晶界处的富钕相和少量钕铁硼主相熔融成液态,此时富钕相中掺杂有较多的铁元素,由于冷却速度较快,富钕相的团聚现象严重,不能完全沿主相晶界析出,影响了钕铁硼磁材的磁性,通过回火使得在晶界交隅的富钕相重新熔融并弥散分布在钕铁硼主相的周围,从而富钕相更好地起到了隔离钕铁硼主相的作用,减少了晶粒件的磁交换耦合作用,提高了最终制得的钕铁硼磁材的内禀矫顽力。
24.综上所述,本技术具有以下有益效果:1、由于电机在使用过程中会发热,故对应用于电机领域的钕铁硼磁材的高温稳定性有一定要求,本技术通过添加三氧化二锑以抑制大晶粒的形成,在烧结的过程中,三氧化二锑反应生成尖晶石相,尖晶石相在晶界处偏析,产生钉扎效应,限制了晶界的移动,抑制晶粒的长大,有效提高钕铁硼磁材的内禀矫顽力,从而提高了钕铁硼磁材的高温稳定性,有效延长了应用于电机领域的钕铁硼磁材的工作寿命。
25.2、三氧化二锑是粉状,在烧结过程中易团聚,本技术通过将三氧化二锑分散于液态的聚硅氮烷内以保证三氧化二锑与其他原料充分接触,由于聚硅氮烷是粘稠状液体,聚硅氮烷同时起到了粘接其他原料的效果,促进原料的致密化,在烧结过程中,聚硅氮烷在高温下裂解产生氮化硅陶瓷,氮化硅本身具有润滑性,起到了填充粉料间缝隙的作用,提高钕铁硼磁材的内禀矫顽力,同时,氮化硅陶瓷具有高温时抗氧化,还能抵抗冷热冲击,提高了钕铁硼磁材的高温稳定性。
26.3、大晶粒的存在抑制了磁材的内禀矫顽力,本技术通过快速冷却使得磁材在形核过程中的温度滞后现象更加明显,从而提高过冷度的增加,过冷度越大,晶核生成的临界半径越小,则晶粒的尺寸越小,有效提高了磁材的内禀矫顽力。
具体实施方式
27.以下结合实施例对本技术作进一步详细说明。
28.原料钕粉、铜粉、铝粉、钆粉、铌粉、铈粉:金属的含量均≥99.99%,其粒度可以根据需要加以调整,本实施例具体以4-6μm为例进行说明。
29.硼铁粉:低碳硼铁粉(c≤0.05%),硼含量为21%-25%,其粒度可以根据需要加以调整,本实施例以4-6μm为例进行说明。
30.铁粉:铁含量为≥98.8%,其粒度可以根据需要加以调整,本实施例以4-6μm为例进行说明。
31.三氧化二锑:含量≥99.99%,其粒度可以根据需要加以调整,本实施例具体以0.1
‑ꢀ
0.25mm为例进行说明。
32.全氢聚硅氮烷:液体时密度1.16-1.31g/ml,固含量为20-35%。
33.甲基聚硅氮烷(psn1):粘度为30000-100000cp,固含量为100%。实施例
34.实施例1一种电机用钕铁硼磁材,包括钕15wt%,铜1t%,硼5wt%,铝1wt%,钆3wt%,铌1wt%,铈15wt%,三氧化二锑0.01wt%,余量为铁和不可避免的杂质。
35.上述钕铁硼磁材的制备方法,包括以下步骤:s1、熔融甩带:将钕粉、铜粉、硼铁粉、铝粉、钆粉、铌粉、铈粉和铁粉按照设定的重量比投入真空熔炼炉中,抽真空至≤1pa后充氩气,加热至1300℃,恒温4h,投入真空熔炼炉的原料在氩气保护下进行熔炼,熔炼后浇铸甩带,得到甩带薄片;s2、氢破研磨:将甩带薄片投入氢破炉中,抽真空至≤1pa后充氢气,氢破3.5h,得到氢破料,将气流磨抽真空并充氮气至真空度为0.25mpa后,将氢破料投入气流磨以进行气流研磨,得到尺寸为3-4μm的磁粉;s3、球磨制粉:按照设定的重量比称取三氧化二锑,将三氧化二锑投入球磨机中,在氩气保护下球磨2.5h,得到三氧化二锑细粉;s4、分散处理:将三氧化二锑细粉置于聚硅氮烷内,聚硅氮烷添加的重量为三氧化二锑的 10倍,超声处理5-10min,超声完毕后静置5-10min,再次超声处理2-5min,即得经聚硅氮烷分散处理的三氧化二锑。;s5、压制成型:按照设定的重量比称取磁粉和经聚硅氮烷分散处理的三氧化二锑,将磁粉和晶粒抑制剂混合均匀后在氮气的保护下一起装入成型压机模具中,加6t的脉冲磁场对磁粉进行压制,将压制得到的产物用塑料薄膜包好后置于等静压压机中,在300mpa油压下压制成型,得到烧结生坯;s6、烧结加工:将烧结生坯投入真空烧结炉中,在氮气保护下烧结,烧结完毕后先以6℃ /min降温至700℃,保温3h,再以4℃/min降温至室温。当温度降至室温后,以3℃/min升温至500℃,保温2.5h,待真空烧结炉内温度自然降至室温后,再以2℃升温至350℃,保温3.5h,等待真空烧结炉内温度降至室温后取出,即得到钕铁硼磁材。
36.实施例2-6实施例2-6在实施例1的制备方法的基础上,调整了各组分的配比,具体配比如表1所示。
37.表1实施例2-6组分配比
对比例对比例1对比例1中基本原料与实施例4的不同之处在于,对比例1中未添加三氧化二锑和聚硅氮烷。
38.对比例2对比例2中基本原料与实施例4的不同之处在于,对比例1中未添加三氧化二锑。
39.对比例3对比例1中基本原料与实施例4的不同之处在于,对比例1中未添加聚硅氮烷。
40.性能检测试验1.磁性能将本技术实施例1-6和对比例1-3提供的钕铁硼磁材根据gb/t3217永磁(硬磁)材料磁性试验方法进行磁性能检测。
41.2.高温稳定性将本技术实施例1-6置于100℃环境下,恒温24h后取出,根据根据gb/t3217永磁(硬磁) 材料磁性试验方法进行磁性能检测,检测结果如表2。
42.表2实施例1-6和对比例1-3的性能检测数据表3的性能检测数据表参见表2,结合实施例1-6的检测结果可知,通过添加少量的铜、少量铝和少量的铌可显著提升钕铁硼磁材的内禀矫顽力,且几乎不影响剩磁,但是添加过量后会使内禀矫顽力迅速下降;钆和铈在重稀土金属中相对储量较高,因而价格较低,添加部分的钆和部分的铈以取代部分的钕,可有效降低生产成本,但是铈铁硼的稳定性较差,随着铈含量的增加,钕铁硼的内禀矫顽力、剩磁和高温稳定性均有一定程度的下降,本技术通过控制各个组分的比例,在保证内禀矫顽力和剩磁的同时,尽量压缩了成本。
43.结合实施例4和对比例1-3的检测结果可知,添加三氧化二锑可有效抑制大晶粒的形成,从而提高钕铁硼磁材的内禀矫顽力;实施例4的钕铁硼磁材的内禀矫顽力优于对比例3,是因为三氧化二锑随着聚硅氮烷流动,从而聚硅氮烷促进了三氧化二锑与其他原料的充分接触,这使得钕铁硼磁材的内禀矫顽力进一步提升;同时,实施例4的钕铁硼磁材的高温稳定性优于对比例3的钕铁硼磁材,是因为氮化硅在高温下裂解生成了氮化硅陶瓷,氮化硅具有高温抗氧化性,还能抵抗冷热冲击。
44.为进一步研究各组分及制备参数对圆柱体磁块性能的影响,本技术进一步开展如下实施例验证。
45.实施例7-11实施例7-11在实施例4的制备方法的基础上,保证其他原料不变,调整了三氧化二锑的含量。实施例7中添加的三氧化二锑含量为0.05wt%,实施例8中添加的三氧化二锑含量为 0.1wt%,实施例9中添加的三氧化二锑含量为0.13wt%,实施例10中添加的三氧化二锑含量为0.15wt%,实施例11中添加的三氧化二锑含量为0.2wt%。
46.将实施例7-11制得的钕铁硼磁材进行如上磁性能检测和高温稳定性检测,测试结果见表3。
47.表3实施例4和实施例7-11的性能检测数据表
结合实施例4和实施例7-11的检测结果可知,随着三氧化二锑含量的增加,内禀矫顽力逐渐增大,这是因为在烧结的过程中,三氧化二锑反应生成尖晶石相,尖晶石相在晶界处偏析,产生钉扎效应,限制了晶界的移动,抑制了晶粒的长大。但是由于三氧化二锑是粉状,结合实施例10和实施例11可知,当三氧化二锑过多时,三氧化二锑在烧结过程中易团聚,影响磁材的内禀矫顽力;故本技术控制了三氧化二锑的含量,同时将三氧化二锑分散于液态的聚硅氮烷内以保证三氧化二锑与其他原料充分接触,但是结合实施例8-10可知,当三氧化二锑和聚硅氮烷的比例过大时,聚硅氮烷不能很好起到分散三氧化二锑的作用。
48.实施例12-16实施例12-16在实施例9的制备方法的基础上,保证其他原料不变,调整了聚硅氮烷的含量。实施例12中添加的聚硅氮烷的重量为三氧化二锑的5倍;实施例13中添加的聚硅氮烷的重量为三氧化二锑的6.7倍;实施例14中添加的聚硅氮烷的重量为三氧化二锑的8.3倍;实施例15中添加的聚硅氮烷的重量为三氧化二锑的10倍;实施例16中添加的聚硅氮烷的重量为三氧化二锑的13倍。
49.将实施例12-16制得的钕铁硼磁材进行如上磁性能检测和高温稳定性检测,测试结果见表4。
50.表4实施例9和实施例12-16的性能检测数据表16的性能检测数据表结合实施例9和实施例12-16的检测结果可知,随着聚硅氮烷含量的增加,聚硅氮烷与三氧化二锑的比例逐渐趋于合适,三氧化二锑在聚硅氮烷内的分散性良好,从而制备
的钕铁硼磁材的内禀矫顽力较好,钕铁硼磁材的高温稳定性也越来越好。但是当聚硅氮烷过量后,聚硅氮烷裂解生成了过多的氮化硅陶瓷,反而影响了钕铁硼磁材的磁性能。
51.实施例17实施例17在实施例14的组分含量的基础上,调整了s4中分散处理时的制备方法,实施例 17中将三氧化二锑置于聚硅氮烷内,50rpm/min搅拌30min,即得到晶粒抑制剂。
52.将实施例17制得的钕铁硼磁材进行如上磁性能检测和高温稳定性检测,测试结果见表5。
53.表5实施例14和实施例17的性能检测数据表结合实施例14和实施例17的检测结果可知,将三氧化二锑浸润在聚硅氮烷内并低速搅拌后,虽然三氧化二锑可以随着聚硅氮烷一起流动,但是溶液中的三氧化二锑仍然存在自发团聚的趋势,不能充分发挥提升钕铁硼磁材内禀矫顽力的效果。
54.实施例18实施例18在实施例14的制备方法和组分含量的基础上,用甲基聚硅氮烷(psn1)替换基本原料中的全氢聚硅氮烷。
55.将实施例18制得的钕铁硼磁材进行如上磁性能检测和高温稳定性检测,测试结果见表6。
56.表6实施例14和实施例18的性能检测数据表结合实施例14和实施例18的检测结果可知,实施例14的整体性能优于实施例18,这可能是因为甲基聚硅氮烷(psn1)的粘度较大,流动性相对较差,不能很好地填补钕铁硼磁材中的缝隙,且甲基聚硅氮烷裂解会产生碳化硅陶瓷,碳元素的引入在一定程度上影响了磁材的磁性能。
57.实施例19-22实施例19-22在实施例14的组分含量的基础上,调整了s6处烧结后的操作。实施例19中的烧结生坯在烧结完毕后,自然降至室温,随后取出,即得到钕铁硼磁材;实施例20中的烧结生坯在烧结完毕后,自然降至室温,随后以3℃/min升温至500℃,保温2.5h,待真空烧结炉内温度自然降至室温后,再以2℃升温至350℃,保温3.5h,等待真空烧结炉内温度降至室温后取出,即得到钕铁硼磁材;实施例21中的烧结生坯在烧结完毕后,先以6℃/min 降温至700℃,保温3h,再以4℃/min降温至室温,即得到烧结钕铁硼磁材;实施例22中的烧结
生坯在烧结完毕后,先以10c/min降温至700℃,保温3h,再以6℃/min降温至室温,即得到烧结钕铁硼磁材。
58.将实施例19-22制得的钕铁硼磁材进行如上磁性能检测和高温稳定性检测,测试结果见表7。
59.表7实施例14和实施例19-22的性能检测数据表结合实施例14和实施例19-21的检测结果可知,在烧结完毕后快速冷却或者回火都可以提升磁材的内禀矫顽力,二者配合效果更好。对于快速冷却而言,这是因为通过快速冷却造成磁材的过冷度增大,一方面使得晶核生成的临界半径减小,从而晶粒尺寸减小,另一方面使得远离的移动能力减弱,众多晶核形成后来不及充分长大;对于回火而言,回火使在晶界交隅的富钕相重新熔融并弥散分布在钕铁硼主相的周围,从而富钕相更好地起到了隔离钕铁硼主相的作用,减少了晶粒件的磁交换耦合作用,提高了最终制得的钕铁硼磁材的内禀矫顽力。
60.结合实施例14和实施例22的检测结果可知,若少结果后冷却速度过快,反而影响了磁材的磁性能,这是因为由于冷却速度过快,熔融的富钕相产生大量团聚,不能较均匀地沿着主相晶界分布,从而不能很好地隔离钕铁硼主相。
61.实施例23、24实施例23、24在实施例14的组分含量的基础上,调整了s2中气流研磨时的操作。实施例 23中氢破料在气流磨中粉碎至粒径为1-2μm;实施例24中氢破料在气流磨中粉碎至粒径为 5-6μm。
62.将实施例23制得的钕铁硼磁材进行如上磁性能检测和高温稳定性检测,测试结果见表8。
63.表8实施例14和实施例23、24的性能检测数据表结合实施例14和实施例24的检测结果可知,随着磁粉粒径的减小,磁材的内禀矫
顽力提高;结果实施例14和实施例23的检测结果可知,当磁粉粒径过小后,磁材内禀矫顽力反而下降,这是因为为了得到该粒径的磁粉,氢破料在气流磨中进行气流研磨的时间增长,磁粉与氧气充分接触,在最终烧结过程中,富钕相与氧元素反应,晶界处孔洞的数量增加。
64.实施例25、26实施例25、26在实施例14的组分含量的基础上,调整了s3中球磨时的操作。实施例25中三氧化二锑在球磨机中球磨5h;实施例26中三氧化二锑在球磨机中球磨1h。
65.将实施例25、26制得的钕铁硼磁材进行如上磁性能检测和高温稳定性检测,测试结果见表9。
66.表9实施例14和实施例25、26的性能检测数据表结合实施例14和实施例26的检测结果可知,随着三氧化二锑的粒径的减小,三氧化二锑与其他原料的接触更加充分;结合实施例14与实施例25的检测结果可知,当三氧化二锑的粒径过小时,最终得到的钕铁硼磁材的磁性受到一定影响,这可能是因为当粒径过小时,三氧化二锑更易发生团聚现象,团聚的三氧化二锑掺杂在钕铁硼磁材中,影响了钕铁硼磁材的磁性能。
67.本具体实施例仅仅是对本技术的解释,其并不是对本技术的限制,本领域技术人员在阅读完本说明书后可以根据需要对本实施例做出没有创造性贡献的修改,但只要在本技术的权利要求范围内都受到专利法的保护。