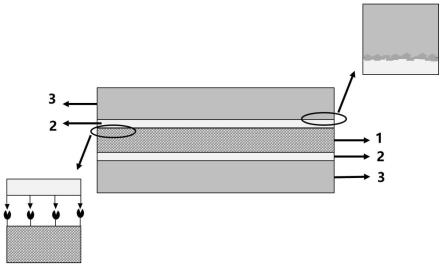
1.本发明涉及一种锂金属负极、制备方法及锂金属电池,属于锂金属电池技术领域。
背景技术:2.在占据消费电子市场后,锂离子电池正迅速扩展其在电动汽车和电能存储领域的应用。然而,各种新兴领域对锂电池的能量密度需求是基于锂离子插层化学的传统锂电池所无法满足的。在这种情况下,以高能量密度著称的锂金属电池作为下一代先进储能技术再次引起人们的关注。这是因为锂金属负极具有低密度(0.54g/cm3)和非常低的标准还原电位(-3.045v she)。
3.然而,在实际研究中发现,以纯锂带为负极的一次或二次电池的应用面临着较多困难而难以实现广泛应用。高比能锂金属一次或二次电池的n/p通常小于2,甚至更低,因此采用的纯锂带负极一般很薄,其厚度通常低于150μm,质地柔软,不易用于电池制作。由于锂金属具有极高的化学反应活性,会不断消耗电解液,导致金属锂不断粉化,形成死锂,增大电池阻抗,而纯锂带的无宿主本质使得锂金属一次电池在放电末期或是锂二次电池循环后期由于锂的大量消耗容易导致导电通路断开,从而导致电池性能急剧恶化。同时极易形成锂枝晶从而产生安全问题。为了解决上述问题,常常将金属锂与铜箔金属集流体复合后作为负极极片使用,避免由于金属锂消耗导致的负极集流导电性能失效。但铜箔的厚度一般6μm~12μm,重量较高,这对提高锂金属电池的能量密度不利。另一些研究者提出采用高分子材料基底作为集流体构建锂金属负极,降低集流体的重量。但未考虑锂金属与高分子材料间由于热膨胀系数的巨大差异导致高分子基底与锂金属接触稳定性低,以及电池热失效时导致高分子热分解加剧电池燃烧等问题,使得锂金属负极性能降低,以及存在安全隐患。
技术实现要素:4.本发明的目的在于克服上述缺陷,提供一种锂金属负极、制备方法及锂金属电池,解决现有高分子材料集流体与锂金属接触稳定性低,安全性需进一步提高的难题,从而提高锂金属电池的循环稳定性和安全性。
5.为实现上述发明目的,本发明提供如下技术方案:
6.一种锂金属负极的制备方法,包括:
7.制备高分子材料基底,所述高分子材料基底为热塑性聚酯和阻燃剂原位复合薄膜;
8.对高分子材料基底进行大气压下氧气介质阻挡等离子体处理;
9.在大气压下氧气介质阻挡等离子体处理后的高分子材料基底表面制备第一金属层;
10.对第一金属层进行大气压下氮气介质阻挡等离子体处理;
11.在大气压下氮气介质阻挡等离子体处理后的第一金属层表面制备第二金属层;所述第二金属层为锂金属层。
12.进一步的,高分子材料基底的制备方法为:
13.采用溶液法得到热塑性聚酯的预聚体溶液;
14.在预聚体溶液中加入阻燃剂,得到混合溶液;
15.将混合溶液采用刮涂法或流延法制成复合薄膜;
16.将复合薄膜在60℃~80℃下烘干后,再在100℃~300℃下固化得到高分子材料基底。
17.进一步的,大气压下氧气介质阻挡等离子体处理条件为放电功率为10kw~50kw,放电时间为10s~120s;气压下氮气介质阻挡等离子体处理条件为放电功率为30kw~80kw,放电时间为30s~150s。
18.进一步的,在高分子材料基底表面制备第一金属层的方法为,先真空镀,后电解镀;
19.所述真空镀为真空蒸镀、磁控溅射镀或离子镀;
20.第一金属层中,真空镀的厚度为3nm~30nm;
21.在大气压下氮气介质阻挡等离子体处理后的第一金属层表面制备第二金属层的方法为电化学镀、真空电镀或层压方法。
22.进一步的,热塑性聚酯包括聚酰亚胺、聚氨酯、聚对苯二甲酸乙二醇酯、聚对苯二甲酸丁二醇酯、聚对苯二甲酸1,4环己二甲醇酯、聚萘二甲酸乙二醇酯、聚萘二甲酸丁二醇酯或聚芳酯中的一种以上;
23.阻燃剂包括有机卤素类阻燃剂或有机磷类阻燃剂中的一种以上;
24.有机卤素类阻燃剂包括十溴联苯酸、四溴双酚a、十溴二苯醚、溴化聚苯乙烯、十溴二苯乙烷或氯化石蜡中的一种以上;
25.有机磷类阻燃剂为磷酸酯或亚磷酸酯中的一种以上。
26.进一步的,高分子材料基底中,阻燃剂和热塑性聚酯的质量比为1:10~2:5。
27.进一步的,第一金属层为金属铜、金属铝、金属银、金属钛、金属锡或金属合金中的一种以上;
28.金属合金为以金属铜、金属铝、金属银或金属锡中的一种以上为金属主体,在金属主体中添加其它金属单质形成的合金,所述其它金属单质为金、钨、铂、铁、钴、镍、镁、锌或铬中的一种以上;
29.其它金属单质的质量不高于金属主体质量的5%。
30.进一步的,高分子材料基底的厚度为5μm~15μm;
31.第一金属层的厚度为50nm~900nm;
32.第二金属层的厚度为50μm~150μm。
33.一种锂金属负极,采用上述锂金属负极的制备方法得到,包含高分子材料基底、第一金属层和第二金属层;
34.高分子材料基底为热塑性聚酯和阻燃剂原位复合薄膜;
35.第二金属层为锂金属层;
36.第一金属层附着于高分子材料基底的单侧表面或双侧表面,第二金属层附着于第一金属层表面。
37.进一步的,高分子材料基底的抗拉强度为25n/mm2~50n/mm2,自熄灭时间为0,耐热
温度范围230℃~350℃,热膨胀系数为5
×
10-5
/℃~2
×
10-6
/℃,100℃下保温1h的纵向及横向热伸缩性《1.0%。
38.一种锂金属电池,包括正极、隔膜和上述锂金属负极;
39.所述锂金属电池包括锂金属一次电池和锂金属二次电池;
40.锂金属一次电池的正极为氟化碳、氧化铬或二氧化锰中的一种;
41.锂金属二次电池的正极为镍质量百分含量大于80%的层状镍钴锰酸锂、镍质量百分含量大于80%的层状镍钴铝、层状钴酸锂、尖晶石型镍锰酸锂、橄榄石型磷酸铁锰锂中的一种以上。
42.本发明与现有技术相比具有如下至少一种有益效果:
43.(1)本发明创造性的提出一种基于高分子材料基底的锂金属电池,有利于降低锂金属负极重量,提高高比能量锂金属电池的能量密度;
44.(2)本发明高分子材料基底采用阻燃剂和热塑性聚酯原位固化形成,将阻燃添加剂溶解在预聚体溶液中,解决阻燃添加剂在聚酯中分散性低、易渗出的难题,有效降低高分材料的自熄灭时间,提高了高分子材料的阻燃特性,有利于减小短路电流及减少短路产热,提高电池的安全性能;
45.(3)本发明高分子材料基层的具有较强的抗拉伸强度。当电池发生切断、穿钉等滥用情况时,高分子材料基层可以很好地包裹锂基金属层的毛刺,增大短路电阻,甚至切断穿钉局部的导电通路,提高电池的安全性能;
46.(4)本发明设计的第一金属层作为一种过渡层,除了提高集流体的导电性外,还起到改善高分子材料基底与金属锂层接触稳定性的作用,并为锂金属在反复沉积过程中提供金属晶核位点,有利于提高锂沉积的均匀性,降低锂枝晶产生的概率,提高锂金属电池循环稳定性的同时,改善电池的安全性;
47.(5)本发明采用大气压下氧气介质阻挡等离子体处理高分子材料基底,使高分子材料基底表面的共价键发生断裂,并在新的断裂位点上引入羟基、羰基、羧基等极性的含氧官能团,从而形成具有活性的致密交联层表面,有效提高了基底与第一金属层的界面相容性,提高二者的结合强度,进而提高锂金属电池的循环稳定性能;
48.(6)本发明提出的大气压下氮气介质阻挡等离子体处理第一金属层表面,形成氮掺杂三维多孔铜氧化物纳米片,有利于在第一金属和金属锂之间形成金属键以及共价键,从而提高第一金属层和第二锂金属层的粘合程度,进而提高锂金属电池的循环稳定性能。
附图说明
49.图1为本发明锂金属负极的截面结构示意图;
50.图2为本发明一种优选的实施方式中锂金属负极的制备方法流程示意图;
51.图3为本发明实施例1经过大气压下氧气介质阻挡等离子体处理后的高分子材料基底xps谱图;
52.图4为本发明实施例1镀铜层经过大气压下氮气介质阻挡等离子体处理的表面电镜图片;
53.图5为本发明对比例2未经大气压下氧气介质阻挡等离子体处理的高分子材料基底xps谱图。
具体实施方式
54.下面通过对本发明进行详细说明,本发明的特点和优点将随着这些说明而变得更为清楚、明确。
55.在这里专用的词“示例性”意为“用作例子、实施例或说明性”。这里作为“示例性”所说明的任何实施例不必解释为优于或好于其它实施例。尽管在附图中示出了实施例的各种方面,但是除非特别指出,不必按比例绘制附图。
56.本发明提供一种重量轻且能改善锂金属电池循环稳定性和安全性的锂金属负极,以及它的制备方法和应用该锂金属负极的锂金属一次、二次电池。
57.如图1,在本发明的第一方面,本发明提出了一种锂金属负极,包括:高分子材料基底1、第一金属层2和第二锂金属层3。高分子材料基底为热塑性聚酯和有机阻燃添加剂原位复合薄膜。
58.锂金属负极中第一金属层和第二锂金属层可以附于高分子材料基底的一面或是双面。
59.在一种优选的实施方式中,高分子材料基底的厚度为2μm~30μm。若高分子材料基底的厚度过薄,其机械强度不足,使得锂金属负极在加工过程及电池循环过程中容易发生断裂,对锂金属层无法起到支撑和保护作用,从而导致电池性能恶化。若高分子材料基底的厚度过厚,将使得锂金属负极具有过高的体积和质量,不利于提高锂金属电池的体积能量密度和质量能量密度。优选的,高分子基底的厚度为5μm~15μm。
60.高分子材料基底的抗拉强度为10n/mm2~100n/mm2。若高分子材料基底的抗拉强度过低,则在使用过程中易发生过大的延展或变形并且容易发生断裂,从而导致金属层发生断带,或是金属层发生剥离。若高分子基底材料的抗拉强度过高,则材料的可焊性变差,难以实现锂金属负极的极耳有效焊接。优选的,高分子材料基底的抗拉强度为25n/mm2~50n/mm2。
61.高分子材料基底的自熄灭时间为0。即高分子材料基底具有不燃性,电池在发生热失控或着火情况下时,可以阻止燃烧的大面积蔓延,同时高分子材料基底可以产生卤化氢、二氧化碳等不燃性气体,起到阻燃的作用,提高锂金属电池的安全性。
62.高分子材料基底的长期耐热温度范围200℃~500℃。若高分子材料基底的长期耐热温度过低,在使用过程中可能发生变形,无法起到对金属层支撑和保护的作用,从而影响电池循环稳定性。若高分子材料基底的长期耐热温度过高,则容易导致其可加工性差,不利制成薄膜。优选的,高分子材料基底的长期耐热温度范围230℃~350℃。
63.高分子材料基底的热膨胀系数为1
×
10-4
/℃~1
×
10-7
/℃。由于电池使用过程中会产热或是工作环境为高温,若高分子材料基底的热膨胀系数过低,在使用过程中可能发生热膨胀而产生热应力,使得基底和金属层间的粘合性降低,容易导致金属层发生裂纹或剥落,破坏导电通路,无法起到对金属层支撑和保护的作用,从而影响电池循环稳定性。若高分子材料基底的热膨胀系数过高,若高分子材料基底的长期耐热温度过高,则容易导致其可加工性差,不利制成薄膜。优选的,高分子材料基底的热膨胀系数为5
×
10-5
/℃~2
×
10-6
/℃。
64.高分材料基底在100℃下保温1h的纵向及横向热伸缩性《1.0%。高分子材料基底应具有适当的热伸缩性,若高分子材料基底的热伸缩性较大时,在使用过程中由于和金属
层之间具有大的热应力,将使得金属层容易出现裂纹或剥落,导致导电通路断裂,从而影响电池的循环稳定性。
65.在一种优选的实施方式中,热塑性聚酯包括聚酰亚胺pi、聚氨酯pu、聚对苯二甲酸乙二醇酯、聚对苯二甲酸丁二醇酯、聚对苯二甲酸1,4环己二甲醇酯、聚萘二甲酸乙二醇酯、聚萘二甲酸丁二醇酯或聚芳酯中的一种以上;
66.有机阻燃添加剂包括有机卤素类阻燃剂,包括十溴联苯酸、四溴双酚a、十溴二苯醚、溴化聚苯乙烯、十溴二苯乙烷或氯化石蜡中的一种或几种,或是有机磷类阻燃剂,包括磷酸酯、亚磷酸酯中的一种或几种。
67.在一种优选的实施方式中,高分子材料基底中阻燃添加剂与热塑性聚酯的质量比为1:10~2:5。聚酯与阻燃添加剂的比例在合适的范围内,可以确保高分子材料基底的自熄灭时间为0,同时具有合适的机械强度。若比例过低,则由于阻燃添加剂的含量过少导致高分子材料基底的自熄灭时间过长,容易导致锂金属电池安全性问题。若比例过高,则由于阻燃添加剂含量过高,导致高分子材料基底的机械强度不足,容易发生断裂,容易导致金属层发生裂纹或剥落,破坏导电通路,无法起到对金属层支撑和保护的作用,从而影响电池循环稳定性。
68.在一种优选的实施方式中,第一金属层包括金属铜、金属铝、金属银、金属钛、金属锡中的一种或多种,还可以少量添加一些其它金属单质与上述金属主体的一种或者多种形成金属合金,用以提高金属层的电导率和改善金属层表面的表面张力。其中,添加的金属单质包括金、钨、铂、铁、钴、镍、镁、锌、铬中的一种或多种,添加比例控制在与金属主体相比质量分数的5%以内。优选地,第一金属层为金属铜。
69.在一种优选的实施方式中,第一金属层的厚度为50nm~900nm。若第一金属层的厚度过高,将增加锂金属负极的质量,不利于提高锂金属电池的能量密度。若第一金属层的厚度过薄,在高分子材料基底表面无法形成连贯的导电网络层,无法起到集流导电和提高高分子材料基底与锂金属接触稳定性的作用,当锂金属一次电池在放电末期或是锂金属二次电池在循环过程中,由于大量活性锂被消耗掉,锂金属负极的导电子能力将显著降低,从而导致锂金属电池性能快速恶化。
70.第二锂金属层的厚度为30μm~180μm,优选为50μm~150μm。
71.在本发明的第二方面,本发明提出了一种锂金属负极的制备方法,如图2,在一种优选的实施方式中本发明制备方法包括:
72.(1)高分子材料基底采用溶液法预聚制备得到预聚体溶液,然后将阻燃剂添加剂加入预聚体溶液中溶解,混合均匀后采用刮涂法或流延法制成复合薄膜,将复合薄膜在60℃~80℃下烘干后,再在100℃~300℃下高温固化得到高分子材料基底。
73.(2)高分子材料基底经过大气压下氧气介质阻挡等离子体处理后,在高分子材料基底表面采用先真空电镀,再电解电镀的方式制备第一金属层。其中,所采用的真空电镀可以为真空蒸镀、磁控溅射镀或离子镀几种类型等方式实现。所采用的电镀是利用电解原理形成金属镀层。真空电镀的厚度为3nm~30nm。
74.(3)第一金属层经过大气压下氮气介质阻挡等离子体处理后,在第一金属层表面采用电化学镀、真空电镀或层压方式制备第二金属层。其中,所采用的真空电镀可以为真空蒸镀、磁控溅射镀或离子镀几种类型等方式实现。
75.在一种优选的实施方式中,大气压下氧气介质阻挡等离子体处理条件为放电功率为10kw~50kw,放电时间为10s~120s。气压下氧气介质阻挡等离子体处理时放电功率过高,或放电时间过长,使得放电能量过高,容易损伤高分子材料的表面基能。等离子体处理时间放电功率过低或放电时间过短,使得放电能量过小,则无法在高分子材料表面形成致密交联层,无法有效提高高分子材料基底和第一金属层之间的接触强度。
76.在一种优选的实施方式中,大气压下氮气介质阻挡等离子体处理条件为放电功率为30kw~80kw,放电时间为30s~150s。大气压下氮气介质阻挡等离子体处理时放电功率过高,或放电时间过长,使得放电能量过高,容易损伤第一金属层的表面基能。等离子体处理时间放电功率过低或放电时间过短,使得放电能量过小,则无法在第一金属层表面形成连续的氮掺杂三维多孔铜氧化物纳米片,无法构建足够的诱导锂沉积活性位点,不利于第一金属层和第二金属层之间的接触稳定性。
77.在本发明的第三方面,本发明提出了一种锂金属电池,包括正极、隔膜和上述的锂金属负极。正极可以为氟化碳、氧化铬、二氧化锰中的一种,制成锂金属一次电池,正极也可以为镍质量百分含量大于80%的层状镍钴锰酸锂、为镍质量百分含量大于80%的层状镍钴铝、层状钴酸锂、尖晶石型镍锰酸锂、橄榄石型磷酸铁锰锂中的一种或几种,制成锂金属二次电池。
78.本发明以高分子材料作为金属层的基底,能起到支撑和保护锂基金属层的作用,并且由于高分子材料基底的密度显著小于常规的铜箔金属集流体,对增加锂金属负极重量的贡献较小,因此有利于提高高比能量锂金属电池的能量密度。同时,当电池发生内短路时,高分子材料基层阻燃特性,能够增大短路电阻,减小短路电流及减少短路产热,甚至切断内短路的导电通路,由此能提高电池的安全性能。或者,当电池发生穿钉等异常情况时,由于高分子材料基层的具有较强的抗拉伸强度,由此高分子材料基层可以很好地包裹锂基金属层的毛刺,增大短路电阻,甚至切断穿钉局部的导电通路。这样,穿钉造成的损坏局限于刺穿位点,形成点断路,从而使得电池能够在一定时间内正常工作。设计的第一金属层作为一种过渡层,除了提高集流体的导电性外,还起到改善高分子材料基底与金属锂层接触稳定性的作用,并为锂金属在反复沉积过程中提供金属晶核位点,有利于提高锂沉积的均匀性,降低锂枝晶产生的概率。
79.本发明中高分子材料基底中将阻燃添加剂和高分子聚合物原位固化形成复合膜,将阻燃添加剂溶解在预聚体溶液中,解决阻燃添加剂在聚酯中分散性低、易渗出的难题,有效降低高分材料的自熄灭时间,提高了高分子材料的阻燃特性,有利于提高锂金属负极的安全性。
80.本发明中提出的采用大气压下氧气介质阻挡等离子体处理高分子材料基底,从而构建具有活性的致密交联层高分子基底表面。这是由于大气压下氧气介质阻挡放电产生的等离子体能在高分子材料基底表面发生氧化作用,氧气容易被激发形成氧原子、氧正离子、氧负离子等活性基团,从而使高分子材料基底表面的共价键发生断裂,并在新的断裂位点上引入羟基、羰基、羧基等极性的含氧官能团,从而形成活性表面。这种活性表面与金属表面产生化学键合作用,从而改善其界面相容性,提高高分子基底与金属层的接触强度。
81.本发明中提出的大气压下氮气介质阻挡等离子体处理第一金属层表面,从而在第一金属层表面构建出氮掺杂三维多孔铜氧化物纳米片,增加了诱导锂沉积的活性位点,有
利于在第一金属和金属锂之间形成金属键以及共价键,从而提高第一金属层和第二锂金属层的接触强度。
82.实施例1
83.本实施例锂金属负极的制备方法如下:
84.(1)采用溶液法预聚制备得到聚酰亚胺预聚体溶液,然后将十溴二苯乙烷阻燃剂添加剂加入预聚体溶液中溶解,十溴二苯乙烷与聚酰亚胺的比例为3:20,混合均匀后采用刮涂法制成复合薄膜,将复合薄膜在60℃下烘干后,再在200℃下高温固化得到高分子材料基底。
85.(2)将高分子材料基底经过大气压下氧气介质阻挡等离子体处理后,放电功率为20kw,放电时间为60s。之后,以真空蒸镀方式镀铜20nm,电解镀铜480nm。
86.(3)将镀铜层经过大气压下氮气介质阻挡等离子体处理后,放电功率为30kw,放电时间为80s。采用电化学镀锂厚度90μm,形成锂金属负极。
87.第一金属层和第二金属层附着于高分子材料基底双侧表面;
88.上述高分子材料基底的厚度为6μm,抗拉强度为35n/mm2,自熄灭时间为0,耐热温度范围312℃,热膨胀系数为1
×
10-5
/℃,100℃下保温1h的纵向及横向热伸缩性为0.8%。
89.正极选用镍钴锰酸锂(ncm811)材料,隔膜选用pe隔膜,组装成1ah锂金属二次电池。对电池进行能量密度、0.1c充/0.2c放循环以及穿钉安全性测试,测试的结果如表1。图3显示了高分子材料基底经过大气压下氧气介质阻挡等离子体处理后的xps谱图。图中c2代表c-o或c-oh化学键,c3代表c=o或o-c-o化学键,c4代表o-c=o或cooh化学键。由图可知,等离子体处理后的表面有大量含氧基团存在。图4显示了镀铜层经过大气压下氮气介质阻挡等离子体处理的表面电镜图片。从图中可以看到,表面层粗糙且有片状物存在。
90.实施例2
91.本实施例锂金属负极的制备方法如下:
92.(1)采用溶液法预聚制备得到聚氨酯预聚体溶液,然后将磷酸酯阻燃剂添加剂加入预聚体溶液中溶解,磷酸酯与聚氨酯的比例为1:10,混合均匀后采用刮涂法制成复合薄膜,将复合薄膜在60℃下烘干后,再在200℃下高温固化得到高分子材料基底。
93.(2)将高分子材料基底经过大气压下氧气介质阻挡等离子体处理后,放电功率为20kw,放电时间为60s。之后,以真空蒸镀方式镀铜3nm,电解镀铜70nm。(3)将镀铜层经过大气压下氮气介质阻挡等离子体处理后,放电功率为30kw,放电时间为80s。采用电化学镀锂厚度50μm,形成锂金属负极。
94.第一金属层和第二金属层附着于高分子材料基底双侧表面;
95.上述高分子材料基底的厚度为8μm,抗拉强度为39n/mm2,自熄灭时间为0,耐热温度范围264℃,热膨胀系数为7
×
10-6
/℃,100℃下保温1h的纵向及横向热伸缩性为0.9%。正极选用氟化碳材料,隔膜选用pe隔膜,组装成1ah锂金属一次电池。对电池进行能量密度和穿钉安全性测试,测试的结果如表1。
96.实施例3
97.本实施例锂金属负极的制备方法如下:
98.(1)采用溶液法预聚制备得到聚对苯二甲酸乙二醇酯预聚体溶液,然后将溴化聚苯乙烯阻燃剂添加剂加入预聚体溶液中溶解,聚对苯二甲酸乙二醇酯与溴化聚苯乙烯的比
例为2:5,混合均匀后采用刮涂法制成复合薄膜,将复合薄膜在60℃下烘干后,再在200℃下高温固化得到高分子材料基底。
99.(2)将高分子材料基底经过大气压下氧气介质阻挡等离子体处理后,放电功率为30kw,放电时间为80s。之后,以真空蒸镀方式镀铜30nm,电解镀铜870nm。
100.(3)将镀铜层经过大气压下氮气介质阻挡等离子体处理后,放电功率为50kw,放电时间为120s。采用电化学镀锂厚度150μm,形成锂金属负极。
101.第一金属层和第二金属层附着于高分子材料基底双侧表面;
102.上述高分子材料基底的厚度为10μm,抗拉强度为42n/mm2,自熄灭时间为0,耐热温度范围294℃,热膨胀系数为9
×
10-6
/℃,100℃下保温1h的纵向及横向热伸缩性为0.85%。
103.正极选用橄榄石型磷酸铁锰锂材料,隔膜选用pe隔膜,组装成1ah锂金属二次电池。对电池进行能量密度、0.1c充/0.2c放循环以及穿钉安全性测试,测试的结果如表1。
104.对比例1
105.本对比例与实施例1的区别在于,以常规铜箔替代高分子材料基底和第一金属层,本对比例中铜箔的厚度与实施例1中高分子材料基底和第一金属层的总厚度相等。
106.如表1所示,本对比例的锂金属电池的能量密度小于实施例1所得锂金属电池的能量密度。电池在穿钉滥用情况下,本对比例电池发生起火、燃烧。
107.对比例2
108.本对比例与实施例1的区别在于,不采用大气压下氧气介质阻挡等离子体处理高分子材料基底。
109.由测试结果可知,未经大气压下氧气介质阻挡等离子体处理的高分子材料基底表面无法引入含氧官能团,高分子材料基底与第一金属层的胶合强度较差,所得锂金属二次电池的循环性能下降。图5为未经大气压下氧气介质阻挡等离子体处理的高分子材料基底表面xps谱。由图可知,未处理的表面没有大量的含氧基团存在。
110.对比例3
111.本对比例与实施例1的区别在于,不采用大气压下氮气介质阻挡等离子体处理第一金属层表面。
112.由测试结果可知,未经等离子强化处理的第一金属层表面不能与金属锂之间形成金属键以及共价键,所得锂金属电池的循环性能下降。
113.表1 性能测试结果表
[0114][0115][0116]
以上结合具体实施方式和范例性实例对本发明进行了详细说明,不过这些说明并不能理解为对本发明的限制。本领域技术人员理解,在不偏离本发明精神和范围的情况下,可以对本发明技术方案及其实施方式进行多种等价替换、修饰或改进,这些均落入本发明的范围内。本发明的保护范围以所附权利要求为准。
[0117]
本发明说明书中未作详细描述的内容属本领域技术人员的公知技术。