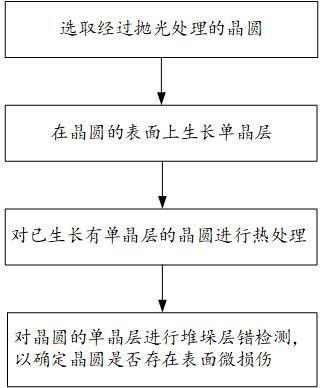
1.本公开涉及晶圆加工制造技术领域,具体地,涉及用于晶圆表面微损伤的检测方法和检测系统。
背景技术:2.在晶圆制造过程中,例如滚磨、切片、研磨的机械加工过程会在晶圆的表面引入机械损伤,为此,会在后续加工中通过例如刻蚀、抛光等工艺去除掉损伤层,由此,经过抛光处理的晶圆的表面通常不再会存在明显损伤。然而,在抛光例如双面抛光过程中,有时仍会存在因硅渣、抛光液中的杂质等颗粒进入抛光区域而在晶圆表面上刮擦从而产生微划痕、局部浅坑等微损伤的情况。这种微损伤在后续的清洗工艺中还会因清洗液中所含化学液对该损伤缺陷的相比于无损伤处更快的腐蚀速率而变得更大更深。微损伤破坏了原有的单晶层,并在器件制造中的薄膜或电路沉积等工艺中容易导致漏电从而引起器件失效。
3.目前,常用的检测晶圆表面损伤的方法包括显微镜观测法和角度抛光法。然而,对于这种在抛光阶段中产生的微损伤,由于尺寸微小,很难通过显微镜或其他检测仪器检测到。至于角度抛光法,首先,其用于检测晶圆切割磨削后产生的损伤层,即在晶圆的整个表面上普遍存在的一层损伤层,而抛光工序中产生的这种微损伤并不存在于整个晶圆表面,而只零散分布在晶圆的局部区域,因此,若采用角度抛光法来检测抛光工序后晶圆表面的微损伤,所选取进行检测的裂解的小片可能不存在微损伤;再者,即便选取进行检测的裂解的小片中存在微损伤,由于角度抛光的磨抛效果远差于晶圆生产工序中的抛光工序的抛光效果,因此也无法借助于利用角度抛光法时所采用的现有检测手段来检测出抛光阶段中产生的微损伤。
技术实现要素:4.本部分提供了本公开的总体概要,而不是对本公开的全部范围或所有特征的全面公开。
5.本公开的一个目的在于提供一种能够检测到晶圆表面上的尺寸微小的微损伤的检测方法。
6.本公开的另一目的在于提供一种能够使零散分布在晶圆的表面上的微损伤都能够被检测到的用于晶圆表面微损伤的检测方法。
7.为了实现上述目的中的一个或多个,根据本公开的一个方面,提供了一种用于晶圆表面微损伤的检测方法,其包括:选取步骤:选取经过抛光处理的晶圆;单晶层生长步骤:在所选取的晶圆的表面上生长单晶层;热处理步骤:对已生长有单晶层的晶圆进行热处理;以及检测步骤:对经过热处理的晶圆的单晶层进行堆垛层错检测,以确定晶圆是否存在表面微损伤。
8.在上述用于晶圆表面微损伤的检测方法中,在进行单晶层生长步骤之前,还可以包括清洗步骤:对所选取的晶圆进行清洗,以去除残留在晶圆的表面上的抛光液。
9.在上述用于晶圆表面微损伤的检测方法中,在所选取的晶圆的表面上生长单晶层可以利用化学气相沉积、物理气相沉积、液相外延、原子层外延或分子束外延来实现。
10.在上述用于晶圆表面微损伤的检测方法中,单晶层的厚度可以为3~6um。
11.在上述用于晶圆表面微损伤的检测方法中,在所选取的晶圆的表面上生长单晶层可以包括利用化学气相沉积由sihcl3与h2在1100~1200℃的条件下反应3~5min以在晶圆的表面上生成单晶层。
12.在上述用于晶圆表面微损伤的检测方法中,对已生长有单晶层的晶圆进行热处理可以包括将晶圆在1100~1200℃的条件下热处理8~16h。
13.在上述用于晶圆表面微损伤的检测方法中,热处理可以在扩散炉中进行,或者在利用化学气相沉积实现在所选取的晶圆的表面上生长单晶层的情况下,热处理可以在通入有保护气体的化学气相沉积反应室中进行。
14.在上述用于晶圆表面微损伤的检测方法中,保护气体可以为氩气。
15.在上述用于晶圆表面微损伤的检测方法中,堆垛层错检测可以利用x射线衍射形貌术或铜雾法进行。
16.根据本公开的另一方面,提供了一种用于晶圆表面微损伤的检测系统,其包括:选取单元,其用于选取经过抛光处理的晶圆;单晶层生长单元:其用于在所选取的晶圆的表面上生长单晶层;热处理单元:其用于对已生长有单晶层的晶圆进行热处理;以及检测单元:其用于对经过热处理的晶圆的单晶层进行堆垛层错检测,以确定晶圆是否存在表面微损伤。
17.根据本公开,通过在晶圆的表面上进行单晶层生长,使得微损伤上形成堆垛层错而将微损伤“放大”至可容易检测到的程度,以间接地实现对尺寸微小的微损伤的检测。此外,单晶层是生长在晶圆的整个表面上的,因此可以将存在于晶圆的整个表面上的所有微损伤都“放大”至可容易检测到的程度,由此可以使零散分布在晶圆的表面上的微损伤都能够被检测到。
18.通过以下结合附图对本公开的示例性实施方式的详细说明,本公开的上述特征和优点以及其他特征和优点将更加清楚。
附图说明
19.图1为根据本公开的实施方式的用于晶圆表面微损伤的检测方法的示意性流程图;图2为利用xrt来检测在晶圆表面上生长出的单晶层中的堆垛层错的示意性流程图;图3示意性地示出了利用xrt来实现对单晶层中的堆垛层错的检测的操作过程;图4为经过单晶层生长步骤和热处理步骤后的晶圆的单晶层的xrt检测图谱,其中,在晶圆的整个区域不存在堆垛层错;图5为经过单晶层生长步骤和热处理步骤后的另一对比晶圆的单晶层的xrt检测
图谱,其中,在晶圆的中心区域存在堆垛层错;以及图6为为了更清楚显示微损伤而经过灰度处理的图5的xrt检测图谱。
具体实施方式
20.下面参照附图、借助于示例性实施方式对本公开进行详细描述。要注意的是,对本公开的以下详细描述仅仅是出于说明目的,而绝不是对本公开的限制。
21.对于在抛光例如双面抛光过程中因硅渣、抛光液中的杂质等颗粒进入抛光区域而在晶圆表面上刮擦从而产生的微划痕、局部浅坑等微损伤,由于其尺寸微小且在晶圆表面上零散分布,很难通过现有的一些检测设备和检测方法及时发现。
22.为解决上述问题,本公开通过将微损伤“放大”至可容易检测到的程度并利用合适的检测手段对该“放大”后的微损伤进行检测来间接地实现对微损伤的检测。
23.具体而言,参照图1,本公开的实施方式提供了一种用于晶圆表面微损伤的检测方法,其包括:选取步骤:选取经过抛光处理的晶圆;单晶层生长步骤:在所选取的晶圆的表面上生长单晶层;热处理步骤:对已生长有单晶层的晶圆进行热处理;以及检测步骤:对经过热处理的晶圆的单晶层进行堆垛层错检测,以确定晶圆是否存在表面微损伤。
24.选取步骤涉及从经过抛光处理的晶圆中选取检测样本,即进行抽样检查。如上文所提到的,在抛光过程中,硅渣、抛光液中的杂质等颗粒有可能进入抛光区域而在晶圆表面上刮擦从而产生微划痕、局部浅坑等微损伤。这时,通过对抛光处理的晶圆进行抽样检查,可以确定出抛光区域是否有颗粒存在,以便及早进行干预处理。
25.根据本公开的实施方式,在所选取或说抽检的晶圆的表面上需要进行单晶层生长,从而在晶圆表面上生长出单晶层。在晶圆表面存在微损伤的情况下,在进行单晶层生长时,单晶原子会在该微损伤的微坑或凹陷处向上堆积,微坑或凹陷将在堆积生长出的单晶层中引入应力并由此造成位错。随着单晶层的生长并且因此单晶层厚度的增加,位错会形成堆垛层错,该堆垛层错还会随着单晶层厚度的继续增加而在单晶层中延展,从而相对于单晶层的完美晶格部分变得明显,由此使该微损伤被“放大”。
26.在单晶层生长结束后,需要对已生长有单晶层的晶圆再进行热处理。该热处理可以使单晶层中的堆垛层错被进一步放大,从而相对于单晶层的完美晶格部分变得更加明显,以至能够被容易地检测到,由此实现了将该微损伤“放大”至可容易检测到的程度。
27.在这种情况下,允许通过对在晶圆表面上生长出的单晶层中的堆垛层错的检测来间接实现对微损伤的检测。由于堆垛层错是因微损伤而在生长出的单晶层中产生的,且堆垛层错是容易例如通过某些现有检测设备或方法检测到的,因此,如果检测到存在堆垛层错,则可间接地确定存在微损伤,由此间接地实现了对微损伤的检测。
28.在该方法中,通过在晶圆的表面上进行单晶层生长以使尺寸微小而不容易检测到的微损伤上形成能够相对于单晶层的完美晶格部分明显辨别的堆垛层错来将微损伤“放大”至可容易检测到的程度,以间接地实现对尺寸微小的微损伤的检测。而且,单晶层是生长在晶圆的整个表面上的,因此可以将存在于晶圆的整个表面上的所有微损伤都“放大”至
可容易检测到的程度,由此可以使零散分布在晶圆的表面上的微损伤都能够被检测到。
29.在根据本公开的实施方式中,在进行单晶层生长步骤之前,还可以包括清洗步骤:对所选取的晶圆进行清洗,以去除残留在晶圆上的抛光液。
30.经过抛光处理的晶圆的表面上可能仍残存有抛光液,这会对在晶圆表面上生长单晶层产生不利影响。可以利用例如水对晶圆表面进行清洗,以去除残留的抛光液,在经过干燥之后即可继续进行单晶层生长步骤。
31.可以理解的是,单晶层为与晶圆同质的材料,即,单晶层为硅单晶层。在这种情况下,生长的单晶层可以与晶圆连接成相同的晶格结构,相比之下,在微损伤处则会出现晶格连接失败从而导致晶格错误,由此使得可相对于单晶层的完美晶格部分显示出明显不同,以便能够通过检测出这种晶格错误即堆垛层错来间接检测出微损伤。
32.在本公开的实施方式中,在晶圆的表面上生长单晶层可以利用化学气相沉积(cvd)、物理气相沉积(pvd)、液相外延(lpe)、原子层外延(ale)或分子束外延(mbe)来实现。
33.可以设想的是,在晶圆的表面上生长单晶层还可以利用其他薄膜沉积方法来实现。
34.在根据本公开的实施方式中,单晶层的厚度可以为3~6um。
35.例如,在利用化学气相沉积来在晶圆的表面上生长单晶层时,可以将sihcl3与h2作为原料通入到化学气相沉积反应室中,在1100~1200℃的条件下反应3~5min以在晶圆的表面上生成单晶层。以此方式,可使所生成的硅单晶层的厚度大致在3~6um。
36.在根据本公开的实施方式中,对已生长有单晶层的晶圆进行热处理可以包括将晶圆在1100~1200℃的条件下热处理8~16h。
37.该热处理可以在扩散炉中在1100~1200℃的条件下进行8~16h,或者在利用化学气相沉积实现在晶圆的表面上生长单晶层的情况下,可以在通入有保护气体例如氩(ar)气的化学气相沉积反应室中在1100~1200℃的条件下进行8~16h。
38.在经过上述热处理后,对单晶层进行堆垛层错检测以实现对微损伤的检测。在根据本公开的实施方式中,堆垛层错检测可以利用x射线衍射形貌术(xrt)或铜雾法进行。可以理解的是,对单晶层中的堆垛层错的检测还可以利用其他合适的方法来实现。
39.以下,结合图2至图6对利用xrt来进行的对该堆垛层错的检测的过程进行进一步描述。
40.如图2和图3中所示,在对晶圆进行过清洗步骤、单晶层生长步骤和热处理步骤之后,可以利用xrt来进行对单晶层中堆垛层错的检测,包括以下步骤:将经过上述步骤处理的晶圆100放置在待测基座10上;选择测试晶面,设定参数;以及打开x射线源对整片晶圆进行透射扫描,即,通过由发射端11向测试晶面发射x射线并由接收端12接收经衍射的x射线,从而获得整片晶圆的投射图样。
41.在xrt中,存在缺陷比如堆垛层错的区域不满足布拉格衍射的角度要求,导致该区域的xrt图样与完美区域的xrt图样存在对比度的差异,从而可以显示出该缺陷。
42.参照图4至图6,分别示出了检测出不存在堆垛层错时的xrt图谱、检测出存在堆垛层错时的xrt图谱、以及经过灰度处理过的检测出存在堆垛层错时的xrt图谱。
43.可以清楚地看到,在图5中并且更明显地在图6中,所显示的检测晶圆的中心区域
处出现了很明显的一条弧形痕迹,其即为堆垛层错。由此,可以确定图5和图6中所示的检测晶圆中存在微损伤。
44.另外,需要注意的是,在图4至图6中所示的xrt图谱中,晶圆的边缘部分同样存在多条痕迹,但其仅是晶圆在热处理时与炉子接触造成的损伤所导致的边缘层错,与在抛光阶段中产生的微损伤无关,可以忽略。
45.还可以使用铜雾法来对单晶层中的堆垛层错进行检测。
46.在对晶圆进行过清洗步骤、单晶层生长步骤和热处理步骤之后,可以利用铜雾法来进行对单晶层中堆垛层错的检测,包括以下步骤:将晶圆浸泡在铜盐溶液比如氯化铜溶液或硝酸铜溶液中5h;对晶圆进行干燥并在1100℃的条件下热处理1h,并在之后将晶圆温度降至室温;以及使用显微镜对晶圆的表面进行观察,以确定堆垛层错区域。
47.在铜雾法中,由于在高温下硅中铜离子的固溶度非常大,离子容易进入晶圆中,相对的低温下铜离子固溶度骤降,铜离子向外析出,降温过程中铜离子在硅中倾向于聚集在堆垛层错区域而不向外析出,故降温后表面不存在铜析出的区域即为堆垛层错区域。
48.因此,在利用显微镜对晶圆的表面进行观察时,如果表面出现没有铜析出的部分,则该部分即为堆垛层错区域,由此,可以确定检测晶圆中存在微损伤。
49.根据本公开的另一方面,还提供了一种用于晶圆表面微损伤的检测系统,其包括:选取单元,其用于选取经过抛光处理的晶圆;单晶层生长单元:其用于在所选取的晶圆的表面上生长单晶层;热处理单元:其用于对已生长有单晶层的晶圆进行热处理;以及检测单元:其用于对经过热处理的晶圆的单晶层进行堆垛层错检测,以确定晶圆是否存在表面微损伤。
50.根据本公开的实施方式,该用于晶圆表面微损伤的检测系统还可以包括清洗单元,其用于在单晶层生长单元进行在所选取的晶圆的表面上生长单晶层之前对所选取的晶圆进行清洗,以去除残留在晶圆的表面上的抛光液。
51.以上所述,仅为本公开的具体实施方式,但本公开的保护范围并不局限于此,任何熟悉本技术领域的技术人员在本公开揭露的技术范围内,可轻易想到的变化或替换,都应涵盖在本公开的保护范围之内。因此,本公开的保护范围应以所述权利要求的保护范围为准。