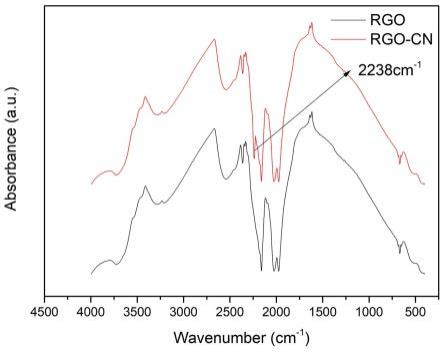
1.本发明涉及石墨烯导电剂领域,特别是涉及一种氰基功能化石墨烯导电剂的制备方法。
背景技术:2.锂电池是储能领域主要的功能部件,特别是新能源汽车和移动式家庭储能设备的发展,推动了锂电池广泛应用。目前主流的锂电池主要以注射液态电解液的锂离子电池为主,当前锂离子电池主要的研究方向是高能量密度和高安全性。特别是在电池安全方面,由于锂离子电池中起离子传导的有机电解液通常具有高反应活性,低稳定性,水、氧敏感等,是造成电芯受外部冲击后热失控的主要因素。锂离子电池中广泛使用的有机电解液为碳酸酯基电解液,由于其碳酸酯基中丰富的的羰基(c=o)具有高反应活性,水、氧高敏感性显著降低锂离子电池的稳定性和安全性。因此,有效抑制有机电解液中含羰基官能团的碳酸酯基组分反应活性可在一定程度上提高锂离子电池的安全系数。在高能量密度研究上,相对于高能量密度的正极高镍三元材料,负极材料的发展相对缓慢,传统的人造石墨负极已逐渐难以满足高能量密度要求。硅及氧化亚硅是目前高能量密度负极材料的主要研究方向,但硅材料普遍存在导电性差,体积膨胀,循环性能较差、与电解液存在副反应等问题。针对硅材料负极的主要改进策略是通过表面包覆、掺杂等手段隔绝硅材料与电解液的直接接触,减少与电解液组分的副反应,同时通过核-壳结构构建、纳米化等手段控制硅材料在充电时体积膨胀问题。其实,在电池首次充放电过程中会在负极形成一层sei膜,sei膜主要是电解液中的碳酸酯基电解液组分与锂离子反应生成碳酸类锂盐,具有隔绝电解液和高离子传导的作用。
技术实现要素:3.为解决上述现有技术中存在的不足,本发明首要目的在于提供一种氰基功能化石墨烯导电剂。本发明的再一目的在于提供一种氰基功能化石墨烯导电剂的制备方法。
4.本发明的目的通过下述技术方案来实现:本发明提供的一种氰基功能化石墨烯导电剂主要制备工艺包括:将还原氧化石墨(rgo)烯粉体卤化处理,获得rgo-x(cl、br、i)。如氯化石墨烯的具体步骤为:s1、将rgo粉体装载在透明石英玻璃容器中等待反应;s2、使用氮气或氩气等惰性气体与氯气(cl2)混合获得n2/cl2混合气体,并通入装有rgo粉体的石英玻璃容器中,尾气使用0.5-1m的硝酸银溶液去除;s3、氯气通过mno2与80-100℃热盐酸反应获得;s4、通过n2鼓入氯气发生装置获得n2/cl2混合气体,通过浓硫酸干燥后通入装有rgo粉体的石英玻璃管中,空排2-10min,排除容器内的空气;s5、排完容器内的空气后,使用254-370nm波长的紫外灯近距离辐照反应0.5-1h,获得rgo-cl样品。其中紫外灯与石英玻璃容器的距离设置<5cm。导电剂选择石墨烯作为导电主材是因为其不仅具有高导电、高导热性能,还是一种二维材料,在导电网络搭建上,相比传统cnt与电极主材的“点-线”接触模式和sp与电极主材
的“点-点”接触模式,石墨烯与电极主材的“点-面”接触模式在电极导电网络搭建上更为理想。此外,石墨烯的二维特性在一定程度上表现出“包覆”效果,可起到隔离电解液与主材的作用。
5.氯化的石墨烯氰基功能化:s6、将步骤s5获得的rgo-cl与nmp溶剂在圆底烧瓶中配置固含为0.5-2%的浆料,加入0.2-1%质量比的氰化亚铜(cucn),并将样品转移至150-240℃油浴锅中磁力搅拌0.5-1h;s7、将s6获得的混合浆料置于500-1000w微波氛围中微波处理10-30min;s8、使用nmp溶剂离心洗涤3-5次,并在50-100℃鼓风干燥柜烘干,获得rgo-cn粉体。本发明通过对还原氧化石墨烯(rgo)进行氰基功能化,抑制碳酸酯基电解液的反应活性。其主要原理是通过功能化的氰基(-cn)与电解液中含有羰基的碳酸酯类电解液组分的偶极-偶极相互作用,提高电解液中的如碳酸乙烯(ec)分子的lumo水平,抑制碳酸乙烯的电化学还原,提高电解液的稳定性。同时,作为负极极片3d导电网络搭建的氰基功能化石墨烯对碳酸酯类电解液组分自由分子的锚定作用,使含羰基组分的自由分子更多的参与到负极sei膜的构建中来,以达到隔绝负极主材与电解液的目的,在一定程度上极大的提升了电池的循环寿命。
6.rgo-cn石墨烯导电剂制备:s9、按rgo-cn粉体:pvp-k30分散剂粉体:nmp溶剂=3:1:96的质量比配置rgo-cn导电剂预混浆料,先将pvp-k30粉体通过高速搅拌完全溶解于nmp溶剂中获得母液,然后加入rgo-cn粉体,分散均匀获得预混浆料;s10、将步骤s9获得的预混浆料转移至沙磨机,在1500-2000r/min的条件下沙磨0.5-1h,获得沙磨的rgo-cn浆料;s11、将沙磨后的rgo-cn浆料转移至均质机,在>800mpa.s的条件处理4-10遍,获得粒径d
50
=2-5μm的rgo-cn导电剂。
7.与现有技术相比,本发明具有以下有益效果:1、本发明提供的一种氰基功能化石墨烯导电剂,通过简单的光氯化反应和氰化盐置换反应获得氰基功能化石墨烯粉体。利用rgo-cn导电剂中的氰基官能团与电解液中含羰基官能团的碳酸酯组分形成偶极-偶极相互作用,降低电解液中含羰基的碳酸酯基自由分子电化学还原活性,提高电解液稳定性。
8.2、本发明提供的一种氰基功能化石墨烯导电剂,利用氰基和羰基的相互作用对电解液中的含羰基组分自由分子进行吸附和锚定,使电解质中的盐阴离子更多的参与到sei膜的形成中来,获得富含无机盐组分的固态电解质界面(sei)膜;利用rgo-cn中的氰基,加强导电剂与电极主材颗粒的结合强度,利用rgo-cn中的氰基强负载型,可增强极片中主材颗粒之间的内聚力,构建3d电极导电网络更为理想。
9.3、本发明提供的一种氰基功能化石墨烯导电剂,由于rgo-cn上的氰基有助于sei膜的特性,适用于充放电过程中存在体积膨胀问题的电极主材的导电网络搭建,如硅、硅碳负极;4、本发明提供的一种氰基功能化石墨烯导电剂,可极大的提高富含碳酸乙烯(ec,含有羰基)组分电解液的稳定性,并改善其在高压条件下充放电的稳定性和安全性;5、本发明提供的一种氰基功能化石墨烯导电剂,通过提高电解液组分氧化还原活性,提高锂离子电池的高温性能和安全性能。
10.附图说明
11.图1为本发明实施例1方法制备获得的rgo-cn的红外光谱图。
12.具体实施方式
13.下面结合具体实施例进一步说明本发明的内容,但不应理解为对本发明的限制。若未特别指明,实施例中所用的技术手段为本领域技术人员所熟知的常规手段。除非特别说明,本发明采用的试剂、方法和设备为本技术领域常规试剂、方法和设备。
14.以下为具体实施例部分:实施例1本发明提出的一种氰基功能化石墨烯导电剂的制备方法,具体步骤如下:1)将还原氧化石墨(rgo)烯粉体卤化处理,获得rgo-x(cl、br、i)。氯化石墨烯的具体步骤为:s1、将干燥的rgo粉体装载在透明石英玻璃容器中,等待反应;s2、使用氮气与氯气(cl2)混合获得n2/cl2混合气体,并通入装有rgo粉体的石英玻璃容器中,尾气使用1m的硝酸银溶液去除;s3、氯气通过mno2与90℃热盐酸反应获得,在cl发生过程中持续通入氮气,形成混合气体并引出反应产生的氯气;s4、通过n2鼓入氯气发生装置获得n2/cl2混合气体,获得的混合气体通过浓硫酸干燥后通入步骤s1装有的rgo粉体的石英玻璃管中,空排5min,其目的在于排除容器内的空气;s5、排完容器内的空气后,使用254nm波长的紫外灯在装有rgo粉体的透明实石英玻璃3cm距离处进行辐照,促使氯气与rgo粉体发生光氯化反应,辐照反应60min后结束,获得rgo-cl粉体样品;2)氯化的石墨烯氰基功能化:s6、将步骤s5获得的rgo-cl与nmp溶剂在圆底烧瓶中配置固含为1%的石墨烯浆料,加入0.5%质量比的氰化亚铜(cucn),并将样品转移至180℃油浴锅中磁力搅拌0.5h;s7、将步骤s6获得的混合浆料置于800w微波氛围中微波处理15min;s8、使用nmp溶剂离心洗涤5次,并在80℃鼓风干燥柜烘干,获得rgo-cn粉体。将获得的粉体进行红外光谱表征,图1为rgo和rgo-cn的红外吸收光谱图,图谱显示rgo-cn在2238cm-1
附近出现氰基的特征吸收峰,其他吸收峰基本吻合,这说明rgo成功实现了氰基功能化。
15.3)rgo-cn石墨烯导电剂制备:s9、按rgo-cn粉体:pvp-k30分散剂粉体:nmp溶剂=3:1:96的质量比配置rgo-cn导电剂预混浆料,先将pvp-k30粉体通过高速搅拌完全溶解于nmp溶剂中获得母液,然后加入rgo-cn粉体,分散均匀获得预混浆料;s10、将步骤s9获得的预混浆料转移至沙磨机,在2000r/min的条件下沙磨0.5-1h,
获得沙磨的rgo-cn浆料;s11、将沙磨后的rgo-cn浆料转移至均质机,在800mpa.s的条件处理4-10遍,获得粒径d
50
=3μm的rgo-cn导电剂。
16.电池性能测试:使用1μm的硅碳材料作为负极主材进行负极浆料制备,其中rgo-cn的质量添加比为2%(这里的添加比是指在正极浆料打料过程中导电剂添加量,这里的添加量按导电剂固含计算,即极片烘干后极片中导电剂剩余质量,也就是导电剂的固体含量,简称固含,是nmp蒸发后剩余物质),硅负极材料质量添加比为96%,其余为粘接剂组分。获得的负极极片与锂金属组成扣式半电池,并进行电池性能测试。在45℃条件下1c/1c高温循环时,rgo-cn的首效低0.7%,rgo-cn实验组1c放电容量为455.41mah/g,在高温循环性能上,rgo-cn在127周循环后容量保持率为88.3%。
17.实施例2本实施例与实施例1的区别在于,所述卤素元素选用br,获得rgo-br,具体步骤如下:该实施例与实施例1的区别在于rgo卤化所用气体为溴气。所述溴气通过溴化钾粉体与过氧化氢反应获得,通过浓硫酸剔除溴气中的水蒸气获得干燥的溴气通如载有rgo粉体的石英管中参与反应。其他步骤均与实施例1相同不再赘述。其目的在于探究卤化步骤对rgo改性的影响。红外吸收光谱显示溴化获得的rgo-cn样品和氯化获得的rgo-cn样品的氰基吸收峰吻合度很高,说明rgo氰基化程度相近。
18.实施例3本实施例与实施例1的区别在于,所述卤素元素选用i,获得rgo-i,具体步骤如下:碘单质颗粒放置在石英舟内,并转移至石英管中,使用氮气排空管内空气后通过管式炉控制加热温度(70℃)将碘单质颗粒升华获得气态碘,气态碘通过阀门导入载有rgo粉体的石英管中参与反应。除石墨烯卤化步骤存在区别,其他步骤均与实施例1相同不再赘述。其目的在于探究卤化步骤对rgo改性的影响。结果显示,相对氯化,红外吸收光谱显示碘化获得的rgo-cn的氰基吸收峰较低,说明rgo氰基化程度相对较弱。这可归因于i容易凝华,当温度降低时容易在反应容器的侧壁上形成紫红色的凝华层,导致i的供应量不足;另外i的化学活性不如cl和br,在相同的条件下其卤化程度不高,从而导致最终的置换反应时,氰基化程度弱。
19.实施例4本实施例与实施例1的区别在于,步骤s5中使用365nm紫光作为光源进行辅助光氯化反应,其他步骤均与实施例1相同,不再赘述,其目的在于探究辅助光源对rgo-cn性能的影响。结果显示,在45℃条件下1c/1c高温循环时,rgo-cn比rgo对照组首效低0.3%,rgo-cn体系在67周循环后容量保持率<80%,这可归因于在长波紫光辐照下rgo粉体的氯化程度不高,导致rgo氰基功能化程度较低。
20.实施例5本实施例与实施例1的区别在于,步骤s7中将样品置于250℃油浴锅中反应,替代微波反应,其他步骤均与实施例1相同,不再赘述,其目的在于探究氰基功能化反应条件对rgo-cn性能的影响。结果显示,在45℃条件下1c/1c高温循环时,rgo-cn比rgo对照组首效低0.37%,rgo-cn体系在83周循环后容量保持率<80%,这可归因于油浴反应效果低于微波反应效果。
21.对比例1与实施例1不同的是,对比例1采用市售普通的rgo作为原料,其他步骤均不改变,制备rgo导电剂。将获得的导电剂用于制备电池并且进行电池性能测试:使用1μm的硅碳材料作为负极主材进行负极浆料制备,其中石墨烯的质量添加比为2%,硅负极材料质量添加比为96%,其余为粘接剂组分。获得的负极极片与锂金属组成扣式半电池,并进行电池性能测试。
22.2)电池制备及测试:s12、使用1μm的硅碳材料作为负极主材进行负极浆料制备,其中石墨烯的质量添加比为2%,硅负极材料质量添加比为96%,其余为粘接剂组分。获得的负极极片与锂金属组成扣式半电池,并进行电池性能测试。
23.测试结果如表1显示:在45℃条件下1c/1c高温循环时,rgo-cn比rgo对照组首效低0.7%,rgo-cn实验组1c放电容量为455.41mah/g,rgo导电剂对照组1c放电容量为458.32mah/g,但在高温循环性能上,rgo-cn远胜rgo对照组,其中未改性的rgo导电剂对照组在48周循环后容量保持率低于80%,rgo-cn在127周循环后仍有88.3%的容量保持率。这可归因于rgo-cn上的氰基与电解液中含羰基官能团的自由分子强的偶极-偶极相互作用,使含羰基组分多负载与负极表面,形成理想的sei膜,同时也导致rgo-cn实验组不可逆耗锂增加,首效下降;同时,氰基-羰基的强强相互作用也降低了电解液中碳酸酯组分分子的氧化还原活性,提高了电解液的稳定性,这可从电池的高温循环性能中表现出来。
24.表1:实验组别首效n周循环后容量保持率<80%1c放电容量实施例188.21%n>127周455.41mah/g实施例288.42%n>115周455.72mah/g实施例388.60%n>102周456.68mah/g实施例488.57%n=67周456.53mah/g实施例588.73%n=83周457.42mah/g对比例188.95%n=48周458.32mah/g对于上述实验结果进行分析,rgo-cn作为硅或氧化亚硅等高容量低导电性的负极导电剂,除了在极片中搭建3d导电网络的作用以外,主要针对电解液中含羰基的碳酸酯类分子的稳定性提升,具体表面在氰基-cn与羰基具有强相互作用,相互作用下使碳酸酯往负极表面富集并与负极表面的rgo-cn中的氰基结合,降低其羰基自由能,提高稳定性,同时该类碳酸酯可在第一次锂离子脱嵌使形成致密的sei膜,对负极活性物质形成理想的保护外壳,sei膜的形成会造成不可逆耗锂,因此,rgo-cn体系的首效会略低于rgo体系,但因完整的sei膜构建加大的增加了电池的循环寿命。因此在循环性能上,实施例1-3在循环127周后容量保持率依然大于80%,实施例4和实施例5由于反应条件的变化,导致rgo氰基功能化程度较低,因此在sei膜的构建效果上不如实施例1-3,分别在循环67周和83周后容量保持率小于80%。
25.实施例6参照实施例1的方法获得rgo-cn,将rgo-cn导电剂运用于ncm-523正极体系。ncm-523正极体系中rgo-cn导电剂添加比例为2%。使用200微米四面涂布器分别在铝箔上涂布
ncm-523正极体系浆料,在80℃鼓风干燥箱中烘干后使用拉力测试仪进行极片内聚力测试,剥离角度设计为180
°
。结果显示rgo-cn导电剂实验组极片内聚力为101.8n/m。
26.对比例2本实施例与实施例4的区别在于,使用没有改性的rgo导电剂运用于ncm-523正极体系。在相同条件下发现,在极片内聚力表现上,实施例6获得的正极极片内聚力为101.8n/m,对比例2获得的正极极片内聚力为42.4n/m,rgo-cn实验组比rgo对照组的极片内聚力提升60n/m,所谓内聚力即正极涂层中颗粒物与颗粒物之间的结合力。这可归因于rgo-cn上的氰基与主材颗粒物具有较强的相互作用,增强极片涂层中有效物质的粘接,因此获得的附着能力增强,这有利于长循环条件极片稳定性的提升。