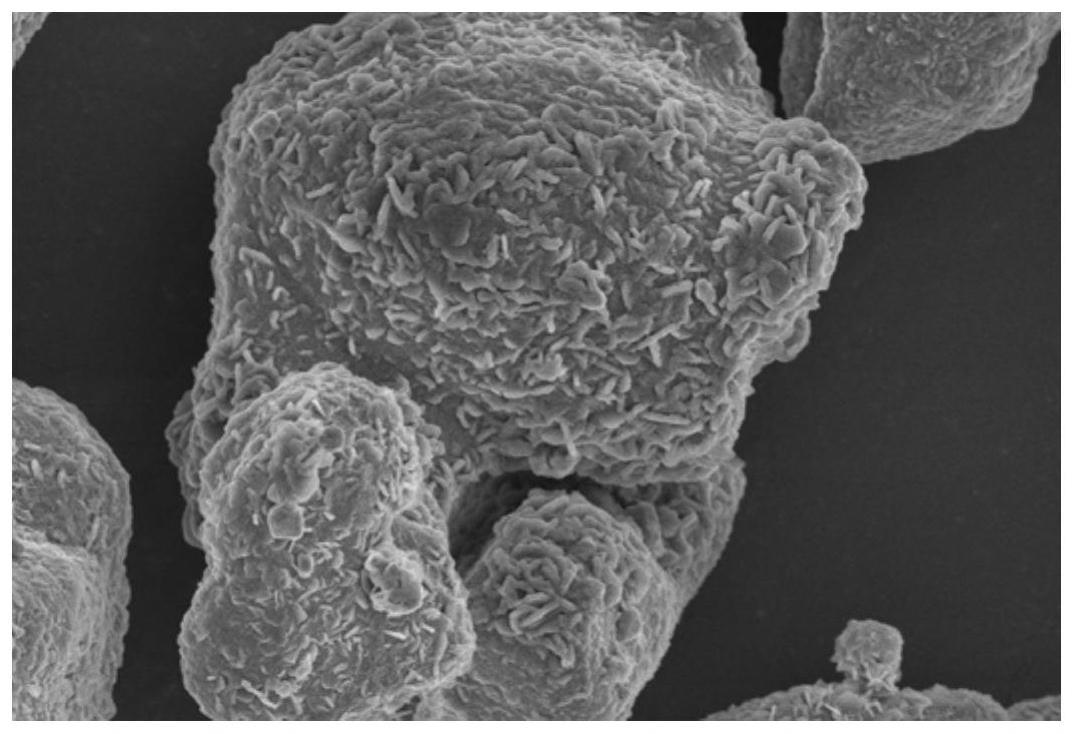
1.本发明属于锂离子电池材料领域,具体涉及一种补锂添加剂及其制备方法和应用。
背景技术:2.锂离子电池作为一种新型的高能电池,在移动通信设备、便携式计算机、摄像机、照相机、mp3等小型设备中得到大量应用,也成为太阳能、风能等发电系统的储备电源,无绳电动工具电源以及混合电动汽车hev、纯电动汽车ev电源。尤其是随着电动汽车和太阳能、风能储能对锂离子电池需求的快速增长,对锂离子电池的安全性、循环性能、倍率性能和高低温性能提出了很高要求。
3.为了满足高比能量电池的设计要求,最有效的方式是选择高比容量的正极和负极材料,例如选择硅、锡、铝、氧化物等作为新型负极材料。但是在锂电池的首次充电过程中,从正极释放出的锂,有部分在负极表面形成了不可逆转的含锂钝化膜(sei),造成了活性锂损失,从而降低了电池的可利用能量。
4.为了弥补这部分锂损失,现行的做法是通过对正极或负极进行预补锂。负极补锂一般是将金属锂粉、箔、片与负极材料发生反应。但这种方式存在锂化试剂化学稳定性差,活泼锂粉存在较大的安全隐患等问题。正极补锂一般是将补锂材料与正极材料按比例混合,调浆后制成电芯,在首次充电过程中,释放出过量的锂,补充负极表面形成sei膜所消耗的锂,从而完成补锂。相比于负极补锂,正极补锂技术无需改变现有电池生产的工艺,因而具有成本低、简单化、安全性高等特点,更加具有工业应用前景。
5.现有的补锂添加剂在电池中一个重要问题是在高温存储或循环下会带来电芯的体积膨胀,产气增加,影响电池的循环稳定性及带来一定的安全隐患。对于产气的问题主要也来源于补锂剂表面的残碱高及其在高电压下强氧化性带来的电解液副反应。
6.因此,如何降低产气,提高电池的电化学性能是一个亟待解决的技术问题。
技术实现要素:7.针对现有技术存在的不足,本发明的目的在于提供一种补锂添加剂及其制备方法和应用。本发明提供了一种具有核壳结构的补锂添加剂,包括m掺杂的内核以及位于所述内核表面的包覆层。通过体相掺杂和表面包覆,制备得到的补锂添加剂不仅可以抑制副反应、稳定材料结构,而且还能减少材料表面的残碱量,从而降低电芯中的产气,提高电池的电化学性能。
8.为达到此发明目的,本发明采用以下技术方案:
9.第一方面,本发明提供一种补锂添加剂,所述补锂添加剂包括m掺杂的内核以及位于所述内核表面的包覆层,所述包覆层的组成为m的氧化物;
10.所述m掺杂的内核的化学组成为li2ni
1-xmx
o2,m为与ni为同一周期的金属元素,0《x《1,例如x可以是0.0001、0.001、0.002、0.005、0.007、0.01、0.05、0.1、0.2、0.3、0.4或0.5
等。
11.本发明中,提供了一种具有核壳结构的补锂添加剂,包括m掺杂的内核以及位于所述内核表面的包覆层。m选自ni同一周期内的元素,其金属原子半径接近ni,因此掺入m可以保持li2nio2自身的框架,从而在键合过程中结构能更稳定,并且m的掺入一定程度上还可以提高锂盐利用率,生成的li2nio2纯度更高,残碱值也有所下降。同时,掺杂m元素可以带来一定的晶格能,对于提高材料导电性、金属溶解稳定性以及容量提升等都具有正面作用。此外,m的氧化物作为内核表面的包覆层,可以有效降低补锂添加剂的残碱值,缓解在正极制备过程中残碱中的oh ̄对粘结剂的破坏,达到提升正极片质量的效果。因此,通过体相掺杂和表面包覆,制备得到的补锂添加剂不仅可以抑制副反应、稳定材料结构,而且还能减少材料表面的残碱量,从而降低电芯中的产气,提高电池的电化学性能。
12.本发明中,m的掺杂量低于ni的量,是因为掺杂量过多会破坏li2nio2自身的框架,从而影响电池的循环稳定性。
13.优选地,m选自co、fe、mn、ti、mg、v、cu和mo中的至少一种。
14.本发明中,金属m选自与ni同一周期的元素,其半径接近于ni,因此m的掺入可以保持补锂添加剂的内核li2nio2自身的框架,从而在键合过程中结构能更加稳定。
15.优选地,x为0.002-0.01,优选为0.004-0.008。
16.本发明中,金属m的掺入量对于补锂添加剂的结构以及性能均具有重要影响,当x过大,即金属m的含量过多时,会影响补锂添加剂的主体结构(也即linio2的结构),使得电池循环的过程中结构坍塌,影响电池的电化学性能,而当x过小时,由于金属m的掺入量过少,则不能有效起到掺杂带来的优势。
17.优选地,以所述内核中的主元素的总质量为100%计,所述主元素为li、ni和o,内核的总质量为100%计,所述包覆层的含量为0.3-4%。
18.本发明中,主元素li、ni和o构成的主体可以认为是基体,基体中掺杂m形成内核,内核表面包覆有包覆层形成外壳。
19.本发明中,当包覆层的含量过少时,则不能有效的隔绝材料表面被电解液侵蚀的副反应,而当包覆层的含量过多时,会影响锂离子的迁移,从而降低容量,电化学性能变差。
20.优选地,所述m的氧化物包括四氧化三钴、三氧化二铁、二氧化锰、二氧化钛、氧化镁、五氧化二钒、氧化亚铜和二氧化钼中的至少一种。
21.第二方面,本发明提高一种如第一方面所述的补锂添加剂的制备方法,所述制备方法包括:
22.将li2nio2与m的氧化物干法球磨后烧结,得到所述补锂添加剂;
23.其中,所述烧结的温度大于等于600℃,例如可以是600℃、650℃、700℃、750℃或800℃等。
24.本发明中,球磨过程中借助机械力的作用可以使一部分m氧化物掺入到li2nio2基体中,通过高温烧结一方面使掺入到li2nio2基体中的m向内扩散形成均匀的掺杂效果,另一方面还可以修复因球磨导致的结构破坏,同时,在高温烧结的条件下,没有掺入到li2nio2基体内核的剩余部分掺杂物会在掺杂的基体的外表面形成组成为m的金属氧化物的包覆层,起到包覆效果。此方法可以从掺杂和包覆两方面共同降低补锂添加剂表面的残碱量,进而减少电芯中的产气,提高电池的电化学性能。
25.本发明中,球磨产生的掺杂效果有限,局限于近表面,掺杂效果差,烧结的温度过低时,无法有效改善体相掺入的效果,而且球磨导致的结构破坏难以修复。
26.优选地,所述m的氧化物的粒径d50《50nm,例如可以是10nm、20nm、30nm、40nm或50nm等。
27.本发明中,m的氧化物的粒径过大时,m的氧化物不能有效掺杂进入到晶格中,也无法起到包覆效果。
28.优选地,所述m的氧化物的添加量占li2nio2的质量的0.5-5%,例如0.5%、1%、1.5%、2%、2.5%、3%、3.5%、4%、4.5%或5%等。
29.本发明中,m的氧化物的添加量一部分用于体相掺杂,一部分用于表面包覆,若添加量过大,则会影响li2nio2的结构,使得结构的稳定性下降,影响电池的性能,若添加量过小,则不能有效起到体相掺杂的效果,且包覆效果更差。优选地,所述li2nio2通过下述方法制备得到,所述方法包括:
30.将锂盐和镍盐在溶剂中搅拌混合,得到混合液,干燥并煅烧,得到li2nio2。
31.本发明对干燥的方式不做限定,示例性的,干燥可以是鼓风烘干、真空烘干或喷雾干燥等。
32.优选地,所述锂盐包括氧化锂、碳酸锂、氢氧化锂、氟化锂、磷酸锂和磷酸二氢锂中的至少一种。
33.优选地,所述锂盐的粒径d50为5-50μm,d50为颗粒的中值粒径,例如可以是5μm、10μm、15μm、20μm、25μm、30μm、35μm、40μm、45μm或50μm等。
34.优选地,所述镍盐包括氧化亚镍、三氧化二镍、二氧化镍、氢氧化镍、氧化氢氧化镍、碳酸镍、草酸镍和乙酸镍中的至少一种。
35.优选地,所述镍盐的粒径d50为5-50μm,例如可以是5μm、10μm、15μm、20μm、25μm、30μm、35μm、40μm、45μm或50μm等。
36.优选地,所述锂盐和镍盐的摩尔比为(1.9-2.2):1,例如可以是1.9:1、2.0:1、2.1:1或2.2:1等。
37.优选地,所述溶剂包括水、乙醇和丙酮中的至少一种。
38.优选地,所述混合液中的固含量为15-60%,例如可以是15%、20%、25%、30%、35%、40%、45%、50%、55%或60%等。
39.优选地,所述煅烧的温度为600-770℃,例如可以是600℃、630℃、660℃、690℃、720℃、750℃或770℃等。优选地,所述煅烧的升温速率为2-10℃/min,例如可以是2℃/min、3℃/min、4℃/min、5℃/min、6℃/min、7℃/min、8℃/min、9℃/min或10℃/min等。
40.优选地,所述煅烧的时间为10-20h,例如可以是10h、11h、12h、13h、14h、15h、16h、17h、18h、19h或20h等。
41.优选地,所述球磨的过程中研磨球与补锂添加剂和金属氧化物的混合物的质量比为(10-20):1,例如可以是10:1、11:1、12:1、13:1、14:1、15:1、16:1、17:1、18:1、19:1或20:1等。
42.本发明中,研磨球与补锂添加剂和金属氧化物的混合物的质量比即为球料比。
43.优选地,所述球磨的转速为200-650rpm,例如可以是200rpm、250rpm、300rpm、350rpm、400rpm、450rpm、500rpm、550rpm、600rpm或650rpm等,优选为400-650rpm。
44.本发明中,球磨的转速过大,则会粘结结块,破碎li2nio2的本体结构,而球磨的转速过小,则能量过低,起不到机械力球磨作用,实现不了体相掺杂。
45.优选地,所述球磨的时间为30-480min,例如30min、60min、120min、180min、240min、300min、360min、420min或480min等,优选为240-480min。
46.本发明中,球磨的时间过长,则会导致研磨的材料粘结结块,破坏li2nio2的本体结构,而过短的球磨时间则会无法实现高能研磨,起不到体相掺杂的效果。
47.优选地,所述球磨的气氛为惰性气氛。
48.本发明对惰性气氛不作限定,示例性的,惰性气氛可以是惰性气体,包括氩气和氮气中的至少一种,也可以是惰性气体和少量氧组合的气体,其中氧分压<200ppm。
49.优选地,所述烧结的温度为600-770℃,例如可以是600℃、630℃、660℃、690℃、720℃、750℃或770℃等。
50.本发明中,烧结的温度对于体相掺入的效果具有重要影响,当烧结的温度过低时,只有混合作用,不能发生相互扩散,实现体相掺杂,而当烧结的温度过高时,li2nio2基体结构被破坏,材料分解失效。
51.优选地,所述烧结的升温速率为2-10℃/min,例如可以是2℃/min、3℃/min、4℃/min、5℃/min、6℃/min、7℃/min、8℃/min、9℃/min或10℃/min等。
52.优选地,所述烧结的时间为10-20h,例如可以是10h、11h、12h、13h、14h、15h、16h、17h、18h、19h或20h等。
53.作为本发明优选的技术方案,所述补锂添加剂的制备方法包括以下步骤:
54.(i)将摩尔比为(1.9-2.2):1的锂盐和镍盐在溶剂中搅拌混合,得到固含量为15-60%的混合液;
55.(ⅱ)将步骤(i)所述混合液干燥,并在惰性气氛中煅烧10-20h,温度为600-770℃,得到li2nio2;
56.(ⅲ)将li2nio2与m的氧化物在惰性气氛中以200-650rpm的转速干法球磨30-480min,得混合产物,其中研磨球与补锂添加剂和金属氧化物的混合物的质量比为(10-20):1;
57.(ⅳ)将步骤(ⅲ)所述混合产物在600-770℃下烧结10-20h,得到所述补锂添加剂。
58.本发明中,步骤(ⅱ)和步骤(ⅲ)所述的惰性气氛相同。
59.第三方面,本发明提供一种锂离子电池,所述锂离子电池的正极中包括如第一方面所述的补锂添加剂。
60.相对于现有技术,本发明具有以下有益效果:
61.本发明提供了一种具有核壳结构的补锂添加剂,包括m掺杂的内核以及位于所述内核表面的包覆层。通过体相掺杂和表面包覆,制备得到的补锂添加剂不仅可以抑制副反应、稳定材料结构,而且还能减少材料表面的残碱量,从而降低电芯中的产气,提高电池的电化学性能。
附图说明
62.图1为对比例5提供的未进行体相掺杂和表面包覆的补锂添加剂的sem图。
63.图2为实施例1提供的体相掺杂和表面包覆后的补锂添加剂的sem图。
具体实施方式
64.下面通过具体实施方式来进一步说明本发明的技术方案。本领域技术人员应该明了,所述实施例仅仅是帮助理解本发明,不应视为对本发明的具体限制。
65.实施例1
66.本实施例提供了一种补锂添加剂,包括co掺杂的li2nio2内核以及位于所述内核表面的包覆层co3o4,其中内核的化学组成为li2ni
0.994
co
0.006
o2。
67.在该补锂添加剂中,包覆层co3o4的含量占主元素li、ni和o总质量的2.4%。
68.(1)将摩尔比为2:1的氧化锂(d50为30μm)和氧化亚镍(d50为25μm)在水中搅拌混合,得到固含量为40%的混合液;
69.(2)将步骤(1)所述混合液干燥,并以6℃/min的速率升温至685℃后煅烧15h,得到li2nio2;
70.(3)将li2nio2与co3o4(co3o4的加入量占li2nio2的3%,co3o4的粒径d50为25nm)在氩气气氛中以450rpm的转速干法球磨240min,得混合产物,其中球料比为(10-20):1;
71.(4)将步骤(3)所述混合产物在685℃下烧结15h,升温速率为6℃/min,得到所述补锂添加剂。
72.图2示出了本实施例提供的补锂添加剂的sem图,有图可知,颗粒表面具有均匀分布的包覆物。
73.实施例2
74.本实施例提供了一种补锂添加剂,包括fe掺杂的li2nio2内核以及位于所述内核表面的包覆层fe2o3,其中内核的化学组成为li2ni
0.996
fe
0.004
o2。
75.在该补锂添加剂中,包覆层fe2o3的含量占主元素li、ni和o总质量的1.6%。
76.(1)将摩尔比为2.1:1的碳酸锂(d50为25μm)和三氧化二镍(d50为30μm)在乙醇中搅拌混合,得到固含量为35%的混合液;
77.(2)将步骤(1)所述混合液干燥,并以4℃/min的速率升温至730℃后煅烧13h,得到li2nio2;
78.(3)将li2nio2与fe2o3(fe2o3的加入量占li2nio2的2%,fe2o3的粒径d50为20nm)在氮气中以350rpm的转速干法球磨120min,得混合产物,其中球料比为(10-20):1;
79.(4)将步骤(3)所述混合产物在730℃下烧结13h,升温速率为4℃/min,得到所述补锂添加剂。
80.实施例3
81.本实施例提供了一种补锂添加剂,包括mn掺杂的li2nio2内核以及位于所述内核表面的包覆层mno2,其中内核的化学组成为li2ni
0.992
mn
0.008
o2。
82.在该补锂添加剂中,包覆层mno2的含量占主元素li、ni和o总质量的2.22%。
83.(1)将摩尔比为1.9:1的氢氧化锂(d50为35μm)和氢氧化镍(d50为35μm)在丙酮中搅拌混合,得到固含量为45%的混合液;
84.(2)将步骤(1)所述混合液干燥,并以6℃/min的速率升温至640℃后煅烧18h,得到li2nio2;
85.(3)将li2nio2与mno2(mno2的加入量占li2nio2的3%,mno2的粒径d50为30nm)在氮气和氧气(氧分压为180ppm)的混合气中以500rpm的转速干法球磨360min,得混合产物,其
中球料比为(10-20):1;
86.(4)将步骤(3)所述混合产物在640℃下烧结18h,升温速率为6℃/min,得到所述补锂添加剂。
87.实施例4
88.本实施例提供了一种补锂添加剂,包括ti掺杂的li2nio2内核以及位于所述内核表面的包覆层tio2,其中内核的化学组成为li2ni
0.99
ti
0.01
o2。
89.在该补锂添加剂中,包覆层tio2的含量占主元素li、ni和o总质量的4%。
90.(1)将摩尔比为2.2:1的氟化锂(d50为5μm)和碳酸镍(d50为5μm)在乙醇中搅拌混合,得到固含量为15%的混合液;
91.(2)将步骤(1)所述混合液干燥,并以2℃/min的速率升温至600℃后煅烧20h,得到li2nio2;
92.(3)将li2nio2与tio2(tio2的加入量占li2nio2的5%,tio2的粒径d50为10nm)在氩气和氧气(氧分压为180ppm)的混合气中以200rpm的转速干法球磨480min,得混合产物,其中球料比为(10-20):1;
93.(4)将步骤(3)所述混合产物在600℃下烧结20h,升温速率为2℃/min,得到所述补锂添加剂。
94.实施例5
95.本实施例提供了一种补锂添加剂,包括mg掺杂的li2nio2内核以及位于所述内核表面的包覆层mgo,其中内核的化学组成为li2ni
0.998
mg
0.002
o2。
96.在该补锂添加剂中,包覆层mgo的含量占主元素li、ni和o总质量的0.3%。
97.(1)将摩尔比为2:1的磷酸锂(d50为50μm)和草酸镍(d50为50μm)在丙酮中搅拌混合,得到固含量为60%的混合液;
98.(2)将步骤(1)所述混合液干燥,并以10℃/min的速率升温至770℃后煅烧10h,得到li2nio2;
99.(3)将li2nio2与mgo(mgo的加入量占li2nio2的0.5%,mgo的粒径d50为40nm)在氮气和氧气(氧分压为100ppm)的混合气中以650rpm的转速干法球磨30min,得混合产物,其中球料比为(10-20):1;
100.(4)将步骤(3)所述混合产物在770℃下烧结10h,升温速率为10℃/min,得到所述补锂添加剂。
101.实施例6
102.本实施例与实施例1不同之处为,内核的化学组成为li2ni
0.999
co
0.001
o2。
103.其余制备方法和参数与实施例1保持一致。
104.实施例7
105.本实施例与实施例1不同之处为,内核的化学组成为li2ni
0.98
co
0.02
o2。
106.其余制备方法和参数与实施例1保持一致。
107.实施例8
108.本实施例与实施例1不同之处为,包覆层co3o4的含量为0.2%。
109.其余制备方法和参数与实施例1保持一致。
110.实施例9
111.本实施例与实施例1不同之处为,包覆层co3o4的含量为5%。
112.其余制备方法和参数与实施例1保持一致。
113.实施例10
114.本实施例与实施例1不同之处为,co3o4的粒径d50为60nm。
115.其余制备方法和参数与实施例1保持一致。
116.实施例11
117.本实施例与实施例1不同之处为,步骤(4)中烧结的温度为550℃。
118.其余制备方法和参数与实施例1保持一致。
119.实施例12
120.本实施例与实施例1不同之处为,步骤(4)中烧结的温度为800℃。
121.其余制备方法和参数与实施例1保持一致。
122.实施例13
123.本实施例与实施例1不同之处为,步骤(3)中球磨的转速为150rpm。
124.其余制备方法和参数与实施例1保持一致。
125.实施例14
126.本实施例与实施例1不同之处为,步骤(3)中球磨的转速为700rpm。
127.其余制备方法和参数与实施例1保持一致。
128.实施例15
129.本实施例与实施例1不同之处为,步骤(3)中球磨的时间为20min。
130.其余制备方法和参数与实施例1保持一致。
131.实施例16
132.本实施例与实施例1不同之处为,步骤(3)中球磨的时间为510min。
133.其余制备方法和参数与实施例1保持一致。
134.对比例1
135.本对比例与实施例1的不同之处为,烧结的温度为300℃。
136.其余制备方法和参数与实施例1保持一致。
137.对比例2
138.本对比例与实施例1的不同之处为,zr掺杂代替co掺杂,包覆层为zro2。
139.其余制备方法和参数与实施例1保持一致。
140.对比例3
141.本对比例与实施例1的不同之处为,步骤(3)不进行球磨,li2nio2与co3o4在氩气气氛中混合后直接烧结。
142.其余制备方法和参数与实施例1保持一致。
143.对比例4
144.本对比例与实施例1的不同之处为,co3o4的总添加量占li2nio2的0.2%。
145.其余制备方法和参数与实施例1保持一致。
146.对比例5
147.本对比例与实施例1的不同之处为,不进行步骤(3)和(4)。
148.其余制备方法和参数与实施例1保持一致。
149.图1示出了本对比例提供的补锂添加剂的sem图。
150.性能测试:
151.将实施例1-16和对比例1-5提供的补锂添加剂搭配到正极材料中使用,将待测的正极材料磷酸铁锂(以磷酸铁锂为例,其余正极材料如三元正极材料、钴酸锂等常见正极体系均有同样增益效果)、补锂材料、粘结剂(pvdf)、导电剂sp以质量比93:2:2.5:2.5混合,加入分散剂n-甲基吡咯烷酮(nmp),调成浆料,均匀涂敷在的铝箔上,烘干后压制成片,然后冲片,在干燥箱中80℃干燥12h后备用。以金属锂片作为对电极,使用1mol/l的lipf6电解液,溶剂为三组分混合溶剂,即ec:dmc:emc体积比为1:1:1的混合物,采用celgard2400微孔聚丙烯膜为隔膜,在米开罗那的氩气手套箱中组装成cr2032型扣式电池。扣式电池的充放电测试在蓝电电池测试系统上进行,充放电的电压为2.0-3.8v,充放电倍率为1c。
152.测试结果如表1所示。
153.表1
154.[0155][0156]
分析:
[0157]
实施例1与实施例6、7的数据结果对比可知,掺杂量过大或过小均会使得残碱值较大,电芯中的产气改善效果微弱,首周效率下降和容量保持率衰减,这说明掺杂量过少起不到掺杂的效果,掺杂量过大又会影响基体的结构,影响电池的首周效率和循环稳定性。
[0158]
实施例1与实施例8、9的数据结果对比可知,包覆层的含量过大或过小均会对降低残碱的效果减弱,电芯中的产气也难以有效降低,并且电池首周效率和容量保持率也有所减少,这是因为包覆层的含量过少时,不能有效的隔绝材料表面被电解液侵蚀的副反应,而当包覆层的含量过多时,会影响锂离子的迁移,从而降低电池的容量保持率和首周效率。
[0159]
实施例1与实施例10的数据结果对比可知,当添加的氧化物粒径过大时,由于难以有效掺杂进入到晶格中,并且也无法起到包覆效果,使得残碱值较高,难以降低电芯中的产气,容量保持率和首周效率也都有所降低。
[0160]
实施例1与实施例11、12的数据结果对比可知,当烧结的温度过低时,球磨仅能局限在表面掺杂,无法实现良好的体相掺杂效果,故得到的残碱值较高,难以降低电芯中的产气,容量保持率和电池的首周效率也呈现下降的趋势,而当烧结的温度过高时,li2nio2基体结构被破坏,材料分解失效,故电池失效。
[0161]
实施例1与实施例13-16的数据结果对比可知,球磨的时间和转速过大会使得材料粘结结块,破坏li2nio2的本体结构,导致残碱值升高,电芯中的产气无法减少,容量保持率衰减和首周效率下降。而球磨的时间和转速过小,则无法实现高能研磨,起不到体相掺杂的效果,因此得到的电池中残碱值高,产气量增大,容量保持率以及首周效率均呈现下降的趋势。
[0162]
实施例1和对比例1的数据结果对比可知,残碱值明显升高,表明电芯中的产气没有得到改善,与电解液的副反应没有得到抑制,其首周效率和容量保持率也均大幅度降低,这是因为烧结的温度过低时,m的氧化物无法发生相互扩散,因此难以实现体相掺杂,起不
到效果。
[0163]
实施例1与对比例2的数据结果对比可知,不与ni同一周期的元素掺杂会对电池的性能造成不利影响,不仅无法有效降低残碱值,减少产气,而且对于电池的首周效率和和容量保持率也呈现出消极影响。
[0164]
实施例1和对比例3的数据结果对比可知,不进行球磨,就难以实现体相掺杂的效果,从而无法降低材料表面的残碱,使得电池的首周效率和和容量保持率均大幅降低。
[0165]
实施例1和对比例4的数据结果对比可知,m的氧化物的原料过少,使得体相掺杂和表面包覆难以起到明显的效果,从而对材料表面的残碱、电池的首周效率和容量保持率的改善影响不大。
[0166]
实施例1和对比例5的数据结果对比可知,不进行体相掺杂和表面包覆,则材料的残碱无法得到降低,其电池的首周效率和容量保持率也得不到显著的改善。
[0167]
申请人声明,本发明通过上述实施例来说明本发明的工艺方法,但本发明并不局限于上述工艺步骤,即不意味着本发明必须依赖上述工艺步骤才能实施。所属技术领域的技术人员应该明了,对本发明的任何改进,对本发明所选用原料的等效替换及辅助成分的添加、具体方式的选择等,均落在本发明的保护范围和公开范围之内。