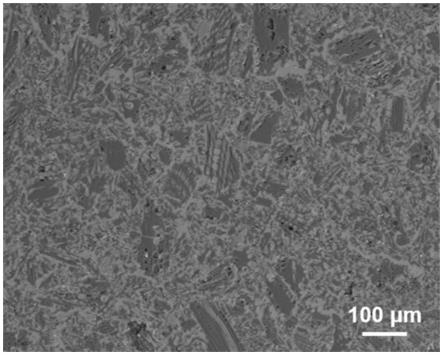
1.本发明涉及一种新型复合材料及其制备方法。
背景技术:2.为了解决短期暂态、频率调节和负载平衡问题,电网对能量存储的需求越来越大。作为电化学储能的代表,高比容量、高能量密度以及环境友好的可充电电池的发展成为了现代电化学所面临的最大挑战。
3.锂离子电池在储能设备和电子产品领域有着广泛而成熟的应用。然而,受限于锂资源稀少、成本高以及难以回收再利用等,随着未来应用在能量密度和高安全性方面的要求越来越高,目前的锂离子电池预计不足以满足这一快速增长市场的需求。因此,迫切需要发明新一代的储能系统来解决这些问题。与锂离子电池相比,镁电池具有三个无可比拟的优势:一、资源丰富,镁是地壳中除去氧和硅元素之外第六丰富的元素,含量约为2%,特别地,我国镁储量位居世界首位;二、镁负极体积能量密度高,体积比容量高达3833mah
·
cm-3
,将近是锂负极(2046mah
·
cm-3
)的两倍;三、安全性高,在某些电解液中具有100%库仑效率的无枝晶沉积有效缓解类似锂离子电池在生产和使用过程中使用不当导致电解液易燃易爆的问题,提高了储能系统的安全性。
4.然而,当前限制可充电镁电池发展的最大因素之一是镁的高化学活性决定,只有既不提供也不接受质子的溶液才适合作为电解质,但是这些溶液会在镁表面容易生成钝化膜。该钝化膜是电子的绝缘体,但同时也会阻碍镁离子的传输,从而阻断可逆的电化学反应。目前镁电池负极设计主要集中在嵌入型负极和合金化负极材料等非金属镁负极方面的研究。作为镁离子宿主材料,受正、负极材料限制,电池容量有限,此外负极材料的结构和化学不稳定性导致电池的循环性能以及倍率性能相对较差。采用纳米级的镁颗粒作为负极材料,通获得更薄的钝化膜使得镁离子的传输距离缩短,迁移动力学加快,然而却不能从根本上解决钝化的问题。因此急需一种成本低廉,工艺简单,环境友好,可大规模制备且能直接应用在商用电解液中的镁电池负极极片的制备方法。
技术实现要素:5.本发明为了解决金属镁负极在大多数常规电解液中生成钝化膜而导致电池循环性能降低的问题,提出了一种用于镁电池负极的生物质炭/镁复合材料的制备方法
6.本发明用于镁电池负极的生物质炭/镁复合材料的制备方法按照以下步骤进行:
7.一、称料:称取块状的生物质炭和金属基体作为原料;
8.二、生物质炭预制体的制备:
9.将步骤一称取的块状的生物质炭置于钢模具中,得到预制体,将预制体带模具移至加热炉中进行预热,得到预热的生物质炭预制体;
10.或将步骤一称取的块状的生物质炭依次进行球磨、过筛和干燥;得到粒径均匀的生物质炭粉;将生物质炭粉置于钢模具中,预压后得到预制体,将预制体带模具移至加热炉
中进行预热,得到预热的生物质炭预制体;
11.三、熔融态金属基体制备:
12.将步骤一称取的金属基体在保护气氛下加热,得到熔融态的金属基体;
13.四、液态金属浸渗:
14.在氦气、氮气或氩气保护气氛下,将步骤二中所得的预热的生物质炭预制体带模具置于压力机台面上,将熔融态的金属基体倒入模具内,进行压力浸渗,得到用于镁电池负极的生物质炭/镁复合材料。
15.本发明具备以下有益效果:
16.1、本发明给出了一种用于镁电池负极的生物质炭/镁复合材料的制备方法,将生物质炭与金属镁采用自排气压力浸渗技术进行复合,利用具有高离子导通及低电子电导的生物质炭作为金属镁表面的保护膜,一方面阻止了常规电解液在金属镁上的还原分解而生成钝化膜,另一方面在镁金属表面可作为镁离子传输通道。在基于稳定的mg盐(0.5mol/l的mg(tfsi)2)溶解在乙腈(acetonitrile,an)和碳酸丙烯酯(propylene carbonate,pc)的两种电解质中对该复合材料极片组装的对称电池极化电位的测试,首次证实了该生物质炭/镁复合材料极片可直接应用在这两种商业化电解质中,实现了镁离子可逆的沉积/剥离。
17.2、本发明实现了将生物质特别是天然生物质废弃材料合理利用转化为一种环境友好和可持续的功能材料,展示出生物质炭材料在能源领域的巨大实际应用潜力,同时为废弃生物质的高价值利用提供了全新思路。
18.3、本发明工艺方法简单、成本低、环境友好,能够实现大体积的生物质炭粉预制体或复合材料的制备,满足产业化生产及应用。
附图说明
19.图1为实施例1得到的生物质炭/镁复合材料的sem图;
20.图2为图1的局部放大图;
21.图3为实施例1得到的生物质炭/镁复合材料的对称电池极化电位测试实验结果。
具体实施方式
22.本发明技术方案不局限于以下所列举具体实施方式,还包括各具体实施方式间的任意合理组合。
23.具体实施方式一:本实施方式可直接应用在常规电解液中的作为镁电池负极的生物质炭/镁复合材料制备方法按照以下步骤进行:
24.一、称料:称取块状的生物质炭和金属基体作为原料;
25.二、生物质炭预制体的制备:
26.将步骤一称取的块状的生物质炭置于钢模具中,得到预制体,将预制体带模具移至加热炉中进行预热,得到预热的生物质炭预制体;
27.或将步骤一称取的块状的生物质炭依次进行球磨、过筛和干燥;得到粒径均匀的生物质炭粉;将生物质炭粉置于钢模具中,预压后得到预制体,将预制体带模具移至加热炉中进行预热,得到预热的生物质炭预制体;
28.三、熔融态金属基体制备:
29.将步骤一称取的金属基体在保护气氛下加热,得到熔融态的金属基体;
30.四、液态金属浸渗:
31.在氦气、氮气或氩气保护气氛下,将步骤二中所得的预热的生物质炭预制体带模具置于压力机台面上,将熔融态的金属基体倒入模具内,进行压力浸渗,得到用于镁电池负极的生物质炭/镁复合材料。
32.1、本实施方式给出了一种用于镁电池负极的生物质炭/镁复合材料的制备方法,将生物质炭与金属镁采用自排气压力浸渗技术进行复合,利用具有高离子导通及低电子电导的生物质炭作为金属镁表面的保护膜,一方面阻止了常规电解液在金属镁上的还原分解而生成钝化膜,另一方面在镁金属表面可作为镁离子传输通道。在基于稳定的mg盐(0.5mol/l的mg(tfsi)2)溶解在乙腈(acetonitrile,an)和碳酸丙烯酯(propylene carbonate,pc)的两种电解质中对该复合材料极片组装的对称电池极化电位的测试,首次证实了该生物质炭/镁复合材料极片可直接应用在这两种商业化电解质中,实现了镁离子可逆的沉积/剥离。
33.2、本实施方式实现了将生物质特别是天然生物质废弃材料合理利用转化为一种环境友好和可持续的功能材料,展示出生物质炭材料在能源领域的巨大实际应用潜力,同时为废弃生物质的高价值利用提供了全新思路。
34.3、本实施方式工艺方法简单、成本低、环境友好,能够实现大体积的生物质炭粉预制体或复合材料的制备,满足产业化生产及应用。
35.具体实施方式二:本实施方式与具体实施方式一不同的是:步骤一所述的块状生物质炭所述的块状生物质炭为通过天然生物质炭化制备获得的生物质炭、多糖炭化制备获得的生物质炭、合成树脂炭化制备获得的生物质炭等中的一种或几种的组合。
36.具体实施方式三:本实施方式与具体实施方式一或二不同的是:步骤一所述的原料中生物质炭体积分数为20%~80%,金属基体为余量。
37.具体实施方式四:本实施方式与具体实施方式一至三之一不同的是:步骤一所述金属基体为纯镁或镁合金;所述镁合金为mg-al合金、mg-al-zn-mn合金、mg-al-si合金及mg-si合金中的一种或其中几种的组合。
38.具体实施方式五:本实施方式与具体实施方式一至四之一不同的是:步骤二所述的球磨的转速为150~400rpm。
39.具体实施方式六:本实施方式与具体实施方式一至五之一不同的是:步骤二所述的球磨时间为2~8h。
40.具体实施方式七:本实施方式与具体实施方式一至六之一不同的是:步骤二所述的过筛用筛子目数为100~400目。
41.具体实施方式八:本实施方式与具体实施方式一至七之一不同的是:步骤二所述生物质炭粉置于钢模具中后进行预压,预压压力为5~120mpa,保压时间为5~15min。
42.具体实施方式九:本实施方式与具体实施方式一至八之一不同的是:步骤三所述的金属基体加热温度为金属基体熔点以上50~400℃,保护气氛为氦气、氮气或氩气。
43.具体实施方式十:本实施方式与具体实施方式一至九之一不同的是:步骤四所得的生物质炭/镁复合材料中的生物质炭呈三维联通或部分三维联通中的一种或两种的组合。
44.采用以下实施例验证本发明的有益效果:
45.实施例1:本实施例可作为镁电池负极的生物质炭/镁复合材料制备方法按照以下步骤进行:
46.一、称料:按体积分数称取30%的生物质炭和70%的金属基体;
47.所述的生物质炭为枣木炭;
48.所述金属基体为纯镁;
49.二、生物质炭预制体的制备:
50.将步骤一称取的生物质炭球磨,将球磨后的生物质炭粉进行过筛,得到粒径均匀的生物质炭粉,然后将生物质炭粉置于真空干燥箱中进行干燥;将干燥后的生物质炭置于钢模具中,预压后得到预制体,将预制体带模具移至加热炉中进行预热,得到预热的生物质炭预制体;
51.所述的球磨转速为150rpm,;
52.所述的球磨时间为6h;
53.所述的筛粉筛子目数为120目;
54.所述的预压压力为50mpa,保压时间为8min;
55.三、熔融态金属基体制备:
56.将步骤一称取的金属基体在保护气氛下加热,得到熔融态的金属基体;
57.所述的金属基体加热温度为金属基体熔点以上230℃,保护气氛为氦气;
58.四、液态金属浸渗:
59.在氦气保护气氛下,将步骤二中所得的预热的生物质炭预制体带模具置于压力机台面上,将熔融态的金属基体倒入模具内,进行压力浸渗,得到可作为镁电池负极的生物质炭/镁复合材料;
60.所述的生物质炭/镁复合材料中的生物质炭呈部分三维联通状。
61.图1为实施例1得到的生物质炭/镁复合材料的sem图;图2为图1的局部放大图。从图中1和2可知,复合材料中生物质炭分布均匀,与金属镁界面结合较好,表面的生物质炭可以较好的保护内部的金属镁。图3为实施例1得到的生物质炭/镁复合材料的对称电池极化电位测试实验结果;经检测,在0.5mol/l mg(tfsi)2/an电解液中对纯镁和c
pju
(枣木炭粉)/mg复合材料极片组装的对称电池极化电位的测试实验发现,在0.01ma/cm2的电流密度下纯镁极片组装的对称电池在初始循环过程中就已经失效(过电位》1v),而生物质炭/镁复合材料在100次循环后过电位在0.3v左右,证实100次循环后仍然可以进行镁离子的可逆沉积/剥离。
62.经检测,在0.5mol/l的mg(tfsi)2/pc电解液中对该复合材料极片组装的对称电池极化电位的测试发现,在0.01ma/cm2的电流密度下实现了至少100次的镁离子可逆沉积/剥离循环。
63.实施例2:本实施例可作为镁电池负极的生物质炭/镁复合材料制备方法按照以下步骤进行:
64.一、称料:按体积分数称取50%的生物质炭和50%的金属基体;
65.所述的生物质炭为竹炭;
66.所述金属基体为纯镁。
67.二、生物质炭预制体的制备:
68.将步骤一称取的生物质炭球磨,将球磨后的生物质炭粉进行过筛,得到粒径均匀的生物质炭粉,然后将生物质炭粉置于真空干燥箱中进行干燥;将干燥后的生物质炭置于钢模具中,预压后得到预制体,将预制体带模具移至加热炉中进行预热,得到预热的生物质炭预制体;
69.所述的球磨转速为200rpm;
70.所述的球磨时间为8h;
71.所述的筛粉筛子目数为100目;
72.所述的预压压力为80mpa,保压时间为5min;
73.三、熔融态金属基体制备:
74.将步骤一称取的金属基体在保护气氛下加热,得到熔融态的金属基体;
75.所述的金属基体加热温度为金属基体熔点以上250℃,保护气氛为氮气;
76.四、液态金属浸渗:
77.在氮气保护气氛下,将步骤二中所得的预热的生物质炭预制体带模具置于压力机台面上,将熔融态的金属基体倒入模具内,进行压力浸渗,得到可作为镁电池负极的生物质炭/镁复合材料;
78.所述的生物质炭/镁复合材料中的生物质炭呈部分三维联通状。
79.经检测,在0.5mol/l的mg(tfsi)2/pc电解液中对该复合材料极片组装的对称电池极化电位的测试发现,在0.01ma/cm2的电流密度下实现了至少300次的镁离子可逆沉积/剥离循环。
80.实施例3:本实施例可作为镁电池负极的生物质炭/镁复合材料制备方法按照以下步骤进行:
81.一、称料:按体积分数称取40%的块状的生物质炭和60%的金属基体;
82.所述的生物质炭为竹炭;
83.所述金属基体为az91合金(mg-9al-0.7zn-0.2mn,wt.%)。
84.二、生物质炭预制体的制备:
85.将块状的生物质炭置于真空干燥箱中进行干燥;将干燥后的生物质炭置于钢模具中,制备预制体,将预制体带模具移至加热炉中进行预热,得到预热的生物质炭预制体;
86.三、熔融态金属基体制备:
87.将步骤一称取的金属基体在保护气氛下加热,得到熔融态的金属基体;
88.所述的金属基体加热温度为金属基体熔点以上200℃,保护气氛为氩气;
89.四、液态金属浸渗:
90.在氩气保护气氛下,将步骤二中所得的预热的生物质炭预制体带模具置于压力机台面上,将熔融态的金属基体倒入模具内,进行压力浸渗,得到可作为镁电池负极的生物质炭/镁复合材料;
91.所述的生物质炭/镁复合材料中的生物质炭呈三维联通状。
92.经检测,在0.5mol/l的mg(tfsi)2/an电解液中对该复合材料极片组装的对称电池极化电位的测试发现,在0.01ma/cm2的电流密度下实现了至少100次的镁离子可逆沉积/剥离循环。