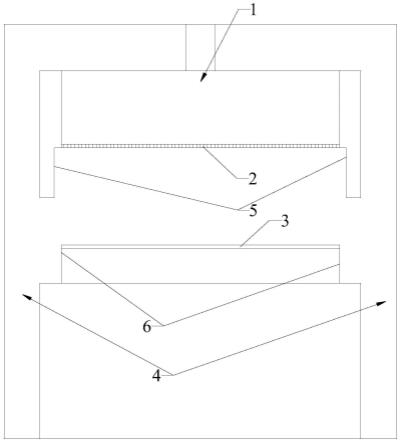
1.本发明涉及半导体制备方法技术领域,具体涉及一种半导体沉积腔残留物的清洁方法。
背景技术:2.led半导体芯片在生产加工过程中通常需要利用等离子体增强化学气相沉积技术在晶圆片(led芯片的半成品)上沉积sio2;具体的,晶圆片需要放置在沉积设备的沉积腔内,但是在sio2的沉积过程中,sio2会无差别的覆盖到沉积腔内的各处。为了防止避免sio2掉落到后续的加工晶圆片上,沉积腔需要被定期的清洗。
3.现有的对沉积腔清洁技术一般采用大功率电离的单一清洁方法。但沉积腔顶部间距1cm排布的4500-5000个孔径0.6mm进气孔无法彻底清洁,在led芯片量产时,sio2随着气体流动偶发性的脱落并覆盖于晶圆片表面,仍然会造成led芯片外观异常及电性异常,影响产品质量。
技术实现要素:4.本发明所要解决的技术问题是:提供一种半导体沉积腔残留物的清洁方法,提高沉积腔进气孔处sio2的清洁程度。
5.为了解决上述技术问题,本发明采用的一种技术方案为:一种半导体沉积腔残留物的清洁方法,包括如下步骤:
6.s1:对沉积腔进行多次有氧电离;所述有氧电离的同时设定沉积腔腔压80-200pa,同时向沉积腔内通入四氟化碳和氧气;
7.s2:排出沉积腔内的氧气;
8.s3:设定沉积腔腔压160-200pa,通入400-600sccm的四氟化碳并进行电离;
9.s4:设定沉积腔腔压40-60pa,通入400-600sccm的四氟化碳;
10.s5:设定沉积腔腔压160-200pa,通入400-600sccm的四氟化碳。
11.本发明的有益效果在于:设定四氟化碳和sio2的不同反应条件使sio2被反应的更充分。
12.具体的,首先对sio2进行有氧环境下的电离工序;有氧电离不仅使沉积腔上的sio2能被反应,还主要用于清除沉积腔腔壁上的sio2。
13.随后,设定沉积腔内低于大气压的腔压使沉积腔的出气端对沉积腔进行抽气,排出沉积腔内的反应物和氧气,使沉积腔处于无氧环境;接着对沉积腔内进行一次电离,再改变沉积腔的腔压设定,使四氟化碳的流速变快,对进气孔的冲击变强;最后再改变沉积腔的腔压设定,使四氟化碳的流速变慢,对进气孔的冲击变弱。
14.四氟化碳不同流速、以不同强度冲击进气孔上的sio2,都能使sio2以不同的形式被消耗;另外,在四氟化碳流速以及冲击力的两次变化,形成四氟化碳流速突变的突变气流,突变气流能使sio2被反应的更充分。
附图说明
15.图1为本发明具体实施方式的一种沉积腔的整体结构剖视图;
16.标号说明:
17.1、进气端;2、进气板;3、基板;4、出气端;5、导向板内壁;6、基台侧壁。
具体实施方式
18.为详细说明本发明的技术内容、所实现目的及效果,以下结合实施方式并配合附图予以说明。
19.本发明提供的一种半导体沉积腔残留物的清洁方法,包括如下步骤:
20.s1:对沉积腔进行多次有氧电离;所述有氧电离的同时设定沉积腔腔压80-200pa,同时向沉积腔内通入四氟化碳和氧气;
21.s2:排出沉积腔内的氧气;
22.s3:设定沉积腔腔压160-200pa,通入400-600sccm的四氟化碳并进行电离;
23.s4:设定沉积腔腔压40-60pa,通入400-600sccm的四氟化碳;
24.s5:设定沉积腔腔压160-200pa,通入400-600sccm的四氟化碳。
25.由上描述可知,本发明的有益效果在于:设定四氟化碳和sio2的不同反应条件使sio2被反应的更充分。
26.具体的,首先对sio2进行有氧环境下的电离工序;有氧电离不仅使沉积腔上的sio2能被反应,还主要用于清除沉积腔腔壁上的sio2。
27.随后,设定沉积腔内低于大气压的腔压使沉积腔的出气端对沉积腔进行抽气,排出沉积腔内的反应物和氧气,使沉积腔处于无氧环境;接着对沉积腔内进行一次电离,再改变沉积腔的腔压设定,使四氟化碳的流速变快,对进气孔的冲击变强;最后再改变沉积腔的腔压设定,使四氟化碳的流速变慢,对进气孔的冲击变弱。
28.四氟化碳不同流速、以不同强度冲击进气孔上的sio2,都能使sio2以不同的形式被消耗;另外,在四氟化碳流速以及冲击力的两次变化,形成四氟化碳流速突变的突变气流,突变气流能使sio2被反应的更充分。
29.进一步地,在所述s1前,需要设定沉积腔腔压100pa,通入200-300sccm的氧气和800-1200sccm的四氟化碳,持续10-20s。
30.由上描述可知,此步骤用于排尽沉积腔内的杂气,并使沉积腔内填充反应气体。
31.进一步地,所述s1的“对沉积腔进行多次有氧电离”具体为:对沉积腔进行2次有氧电离;
32.所述s1的“向沉积腔内通入四氟化碳和氧气”具体为:向沉积腔内通入800-1200sccm的四氟化碳和200-300sccm氧气。
33.由上描述可知,提供具体次数的有氧电离,并提供有氧电离的一种合理反应条件;使所述半导体沉积腔残留物的清洁方法的步骤仅可能简单的情况下,使sio2被反应的更彻底。
34.进一步地,所述s1的“对沉积腔进行2次有氧电离”具体为:第一次有氧电离设定沉积腔腔压100pa,第二次有氧电离设定积腔腔压180pa;每次有氧电离持续1000-1400s,每次的电离功率为400-600w。
35.由上描述可知,提供两次有氧电离不同的反应条件,使sio2被反应得更充分。
36.进一步地,所述s3、s4和s5循环2-4次。
37.由上描述可知,所述s3、s4和s5循环2-4次使四氟化碳的突变气流形成更多次,使sio2被反应得更充分。
38.进一步地,所述s3具体为:设定沉积腔腔压160-200pa,通入400-600sccm的四氟化碳并进行电离,持续400-600s,电离功率50-150w。
39.由上描述可知,提供s3合理的反应条件及时长。
40.进一步地,所述s4具体为:设定沉积腔腔压40-60pa,通入400-600sccm的四氟化碳,持续40-60s。
41.由上描述可知,提供s4合理的反应时长。
42.进一步地,所述s5具体为:设定沉积腔腔压160-200pa,通入400-600sccm的四氟化碳,持续10-20s。
43.由上描述可知,提供s5合理的反应时长
44.进一步地,所有清洁方法中,沉积腔内温度始终保持200-300度。
45.由上描述可知,250度的温度下,sio2的反应更剧烈。
46.本发明的应用背景为:需要沉积腔内的sio2、以及特别是沉积腔内的进气孔处的sio2需要被清洁彻底时。
47.请参考附图1,在此先说明沉积腔内部结构;所述沉积腔内自上到下设有进气端1、水平的进气板2和水平的基板3;所述进气板2上设有多个进气孔,所述沉积腔的出气端4在沉积腔下端的周缘,也就是在基板3的侧下方。
48.沉积腔内除了进气孔处以及基板3上需要除去sio2,还有以下几处的sio2需要除尽。进气板2的边沿设置在竖直的导向板上,进气板2下端的导向板内壁5上的sio2需要清除。基板3设置基台上,基台侧壁6也需要清洁,出气端4也在基台侧下方。
49.实施例一
50.一种半导体沉积腔残留物的清洁方法包括以下步骤:
51.在s1前,设定沉积腔温度200℃并保持以下整个清洁过程;
52.对沉积腔设定腔压100pa,氧气200sccm,四氟化碳800sccm,持续时间15s。
53.s1包括如下步骤:
54.s1.1(第一次有氧电离):对沉积腔设定腔压80pa,氧气200ssccm,四氟化碳800sccm,电离功率设定400w,持续时间1000s。
55.s1.2:对沉积腔设定腔压160pa,氧气200sccm,四氟化碳800sccm,持续时间10s。
56.s1.3:(第二次有氧电离):对沉积腔、设定腔压160pa,氧气200sccm,四氟化碳800sccm,电离功率设定400w,持续时间1000s。
57.s2:对沉积腔设定腔压160pa,四氟化碳800sccm,持续时间15s。
58.s3:对沉积腔设定腔压160pa,氧气0sccm,四氟化碳400sccm,电离功率设定50w,持续时间400s。
59.s4:对沉积腔设定腔压40pa,氧气0sccm,四氟化碳400sccm,电离功率设定0w,持续时间40s。
60.s5:对沉积腔设定腔压160pa,氧气0sccm,四氟化碳400sccm,电离功率设定0w,持
续时间10s。
61.s6:将上述s3、s4、s5循环2次。
62.s7:对沉积腔设定腔压180pa,氧气0sccm,四氟化碳800sccm,持续时间15s。将沉积腔内最后的反应物全部抽出腔外。
63.实施例二
64.所述半导体沉积腔残留物的清洁方法包括以下步骤:
65.设定沉积腔温度250℃并保持以下整个清洁过程;对沉积腔设定腔压100pa,氧气250sccm,四氟化碳1000sccm,持续时间15s。
66.s1包括如下步骤:
67.s1.1(第一次有氧电离):对沉积腔设定腔压100pa,氧气250ssccm,四氟化碳1000sccm,电离功率设定500w,持续时间1200s。
68.反应物会随着出气端的抽气排出沉积腔,四氟化碳比例1:4能加速四氟化碳的反应;500w的电离功率属于大功率,腔压100pa属于较低腔压;大功率电离以及较低腔压可使沉积腔边沿的sio2反应强度大于沉积腔中部的反应强度;也就是基台侧壁和导向板内壁上的sio2能被更充分的反应。
69.s1.2:对沉积腔设定腔压180pa,氧气250sccm,四氟化碳1000sccm,持续15s,能将腔体内的上个阶段的反应物排到腔外,并使腔体充满下阶段待反应气体。
70.s1.3:(第二次有氧电离):对沉积腔、设定腔压180pa,氧气250sccm,四氟化碳1000sccm,电离功率设定500w,持续时间1200s。
71.大电离功率及180pa高腔压状态可使沉积腔中部(进气板和基板)的反应大于边缘区域。
72.s2:对沉积腔设定腔压180pa,四氟化碳800-1200sccm,持续时间15s。
73.此步骤能将沉积腔内上个阶段的反应物和氧气排到腔外,并使腔体充满下阶段待反应气体。
74.s3:对沉积腔设定腔压180pa,氧气0sccm,四氟化碳500sccm,电离功率设定100w,持续时间500s。
75.100w的电离功率,无氧气下小流量四氟化碳的缓慢反应,轻缓处理气孔壁上阶段的残留。
76.s4:对沉积腔设定腔压50pa,氧气0sccm,四氟化碳500sccm,电离功率设定0w,持续时间50s。
77.大量增加四氟化碳通气量,并调低腔压,出气端快速抽气,使四氟化碳高速冲击进气孔。
78.s5:对沉积腔设定腔压180pa,氧气0sccm,四氟化碳500sccm,电离功率设定0w,持续时间15s。
79.通过小功率电离反应上个阶段残留在进气孔的sio2,大量增加四氟化碳通气量,并调低腔压快速抽气,再减气恢复腔压,利用低腔压提速与高腔压减速的突变流速带走进气孔sio2及其反应物。
80.s6:将上述s3、s4、s5依次循环3次。
81.多次实验验证三个循环将有效的去除进气孔的残留物。
82.s7:对沉积腔设定腔压180pa,氧气0sccm,四氟化碳1000sccm,持续时间15s。将沉积腔内最后的反应物全部抽出腔外。
83.实施例三
84.所述半导体沉积腔残留物的清洁方法包括以下步骤:
85.设定沉积腔温度250℃并保持以下整个清洁过程;对沉积腔设定腔压120pa,氧气300sccm,四氟化碳1200sccm,持续时间20s。
86.s1包括如下步骤:
87.s1.1(第一次有氧电离):对沉积腔设定腔压120pa,氧气300ssccm,四氟化碳1200sccm,电离功率设定600w,持续时间1400s。
88.s1.2:对沉积腔设定腔压200pa,氧气300sccm,四氟化碳1200sccm,持续时间20s。
89.s1.3:(第二次有氧电离):对沉积腔、设定腔压200pa,氧气300sccm,四氟化碳1200sccm,电离功率设定600w,持续时间1400s。
90.s2:对沉积腔设定腔压200pa,四氟化碳1200sccm,持续时间20s。
91.s3:对沉积腔设定腔压200pa,氧气0sccm,四氟化碳600sccm,电离功率设定150w,持续时间600s。
92.s4:对沉积腔设定腔压60pa,氧气0sccm,四氟化碳600sccm,电离功率设定0w,持续时间60s。
93.s5:对沉积腔设定腔压200pa,氧气0sccm,四氟化碳600sccm,电离功率设定0w,持续时间20s。
94.s6:将上述s3、s4、s5循环4次。
95.s7:对沉积腔设定腔压180pa,氧气0sccm,四氟化碳800-1200sccm,持续时间15s。将沉积腔内最后的反应物全部抽出腔外。
96.以上所述仅为本发明的实施例,并非因此限制本发明的专利范围,凡是利用本发明说明书及附图内容所作的等同变换,或直接或间接运用在相关的技术领域,均同理包括在本发明的专利保护范围内。