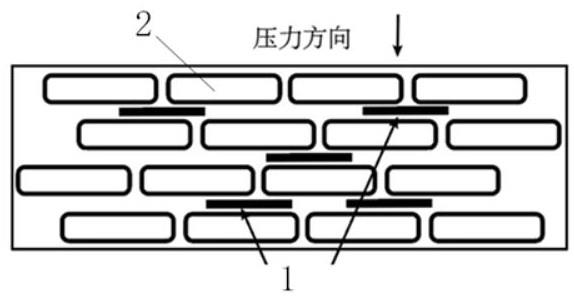
1.本技术涉及永磁材料领域,具体而言涉及一种热变形钕铁硼磁体及提升其均匀性的方法。
背景技术:2.热变形钕铁硼磁体凭借优异的磁性能,广泛应用于风力发电、节能家电以及新能源汽车等领域。但是,现有的热变形钕铁硼磁体常在热变形加工过程中受设备限制,使得磁体在加热加压过程中受热不均匀,导致磁体中心部位和边缘部位存在较大的温度差,使得磁体磁性能和力学性能均匀性较差。
3.现有工艺水平下,热变形钕铁硼磁体的磁性能均匀性较差。较差的均匀性会导致磁体在服役过程中磁场频度不稳定,影响使用效率。
4.此外,现有加工方式下,热变形钕铁硼磁体的力学性能同样不稳定,容易导致现有热变形钕铁硼磁体在高频环境服役过程中容易发生开裂、脱落等现象,造成安全隐患。
技术实现要素:5.本技术针对现有技术的热压/热变形设备受热不均、受压力不均,导致磁体一致性较差的问题,提供一种热变形钕铁硼磁体及提升其均匀性的方法,本技术通过利用晶界相形成高熔点、高导热性析出相,配合特殊的外加感应磁场和应力场,促进磁体内部传热和传力作用,能够显著提升磁体均匀性。本技术具体采用如下技术方案。
6.首先,为实现上述目的,提出一种热变形钕铁硼磁体,其内部混合有:亚微米尺度的棒状导热材料,所述棒状导热材料按照0.1%-1.0%的质量比均匀混合在钕铁硼磁粉中,与钕铁硼磁粉共同经热压和热变形处理形成钕铁硼磁体。
7.可选的,如上任一所述的热变形钕铁硼磁体,其中,所述亚微米尺度的棒状导热材料,其熔点不低于800℃,其导热率不低于30w/(m.k)。
8.可选的,如上任一所述的热变形钕铁硼磁体,其中,所述亚微米尺度的棒状导热材料为如下任意一种或其组合:聚乙炔、聚亚苯基硫醚、聚噻吩、mgo、beo、石墨、si、aln、碳纤维、导热玻璃、高温陶瓷。
9.可选的,如上任一所述的热变形钕铁硼磁体,其中,所述亚微米尺度的棒状导热材料的粒径范围为5nm-10nm。
10.可选的,如上任一所述的热变形钕铁硼磁体,均匀混合有亚微米尺度棒状导热材料的钕铁硼磁粉,先在600℃-700℃,200-400mpa,真空度8.0x10-3pa条件下进行致密化,热压后获得热变形前驱体。
11.可选的,如上任一所述的热变形钕铁硼磁体,所述热变形钕铁硼磁体为:继续对所述热变形前驱体在650℃-800℃,150-250mpa,真空度8.0x10-3pa条件下进行热变形处理所获得
,
热变形处理中变形量控制在70%-80%之间。
12.同时,为实现上述目的,本技术还提供一种提升热变形钕铁硼磁体均匀性的方法,
其中,包括如下步骤:将亚微米尺度的棒状导热材料按照0.1%-1.0%的质量比均匀混合在钕铁硼磁粉中,获得混合磁粉;将混合磁粉置于600℃-700℃,200-400mpa,真空度8.0x10-3pa条件下进行致密化,热压处理后获得热变形前驱体;对所述热变形前驱体进行热变形处理获得热变形钕铁硼磁体。
13.可选的,如上任一所述的方法,其中,对所述热变形前驱体进行热变形处理前还进行如下步骤:打磨掉热变形前驱体表面残留杂质及氧化层,然后置入模具中;热变形处理过程中,在模具的垂直压力方向施加局域场并在650℃-800℃,150-250mpa,真空度8.0x10-3pa条件下进行对前驱体进行70%-80%的大变形。
14.可选的,如上任一所述的方法,其中,亚微米尺度的棒状导热材料为能够由局域场原位生成顺磁性的:聚乙炔、聚亚苯基硫醚、聚噻吩、mgo、beo、石墨、si、aln、碳纤维、导热玻璃、高温陶瓷中的任意一种或其组合,其粒径范围为5nm-10nm。
15.可选的,如上任一所述的方法,其中,热变形处理过程中,热变形前驱体中的富钕相保持在熔融状态;原位生成顺磁性的棒状导热材料由局域场、应力场驱使,垂直于压力方向排布于主相晶粒之间。
16.有益效果
17.本技术所提供的提升热变形钕铁硼磁体均匀性的方法,通过将亚微米尺度的棒状导热材料按照0.1%-1.0%的质量比均匀混合在钕铁硼磁粉中,可在晶界相中形成垂直于压力方向的棒状高熔点、高导热性物质,以使其在混合磁粉加热过程中迅速将热量由高温区域传导至中低温区域,平衡磁体内部的温度。加压过程中,本技术还可利用棒状相的形状特性使应力向垂直于压力方向传递,避免应力过于集中导致磁体开裂。本技术通过亚微米尺度的棒状导热材料的加入,能够在磁体内部中心和边缘形成晶粒尺寸均匀的组织,通过控制热压/热变形过程中的晶粒生长行为,能够极大增加材料的磁性能和力学性能,克服现有设备加工条件下磁性能均匀性、力学性能均匀性较差的缺陷,获得高综合性能性能热变形钕铁硼磁体。
18.本技术中,棒状相的加入可以加强去磁耦合作用,同时高的导热性和传力性能可以减小温度场和应力场,从而提高磁体整体的均匀性。
19.本技术的其它特征和优点将在随后的说明书中阐述,并且,部分地从说明书中变得显而易见,或者通过实施本技术而了解。
附图说明
20.附图用来提供对本技术的进一步理解,并且构成说明书的一部分,并与本技术的实施例一起,用于解释本技术,并不构成对本技术的限制。在附图中:
21.图1是本技术中混合磁粉的制备方式示意图;
22.图2是本技术中对热变形前驱体进行热变形处理过程中的棒状导热材料的分布方式示意图;
23.图中,1表示棒状导热材料;2表示钕铁硼磁粉。
具体实施方式
24.为使本技术实施例的目的和技术方案更加清楚,下面将结合本技术实施例的附
图,对本技术实施例的技术方案进行清楚、完整地描述。显然,所描述的实施例是本技术的一部分实施例,而不是全部的实施例。基于所描述的本技术的实施例,本领域普通技术人员在无需创造性劳动的前提下所获得的所有其他实施例,都属于本技术保护的范围。
25.本技术领域技术人员可以理解,除非另外定义,这里使用的所有术语(包括技术术语和科学术语)具有与本技术所属领域中的普通技术人员的一般理解相同的意义。还应该理解的是,诸如通用字典中定义的那些术语应该被理解为具有与现有技术的上下文中的意义一致的意义,并且除非像这里一样定义,不会用理想化或过于正式的含义来解释。
26.本技术中所述的“和/或”的含义指的是各自单独存在或两者同时存在的情况均包括在内。
27.本技术中所述的“内、外”的含义指的是相对于容器而言,由容器外壳指向内部混合磁粉或热变形前驱体的方向为内,反之为外;而非对本技术的装置机构的特定限定。
28.本技术中所述的“连接”的含义可以是部件之间的直接连接也可以是部件间通过其它部件的间接连接。
29.本技术中所述的“上、下”的含义指的是使用者正对模具时,模具所受垂直压力的来源方向即为上,反之即为下,而非对本技术的装置机构的特定限定。
30.本技术针对现有热变形钕铁硼磁体加工过程中热压/热变形设备受热不均、受压力不均,导致磁体一致性较差的问题,通过在热变形钕铁硼磁体中混合亚微米尺度的棒状导热材料1,将所述棒状导热材料按照0.1%-1.0%的质量比均匀混合在钕铁硼磁粉中,与钕铁硼磁粉共同经热压和热变形处理形成钕铁硼磁体,以利用聚乙炔、聚亚苯基硫醚、聚噻吩、mgo、beo、石墨、si、aln、碳纤维、导热玻璃、高温陶瓷等高熔点、高导热性的棒状材质以垂直于施压方向的方式填充在钕铁硼磁粉缝隙中,隔绝钕铁硼磁粉料主相晶粒之间的去磁耦合作用,并同在受压变形过程中阻隔热变形钕铁硼磁体中裂纹的扩展,抑制裂纹的传递,降低磁体内部的能量传递,显著提升力学性能。
31.热变形过程是通常采用略高于富钕相熔点(650℃)的温度进行热变形,良好的导热性可以减小温度场的范围。因此本技术的亚微米尺度的棒状导热材料,其熔点一般设置为不低于800℃,导热率一般设置为不低于30w/(m.k),以由此实现在热压热变形过程保持条状结构,实现在均匀的排列在条状主相之间。考虑到热变形钕铁硼磁体所选用的商业钕铁硼磁粉主相晶粒之间缝隙一般在10nm-15nm范围之间,因此,本技术优选将所述亚微米尺度的棒状导热材料的粒径范围为设置在5nm-10nm之间,以由此实现棒状材料合理分布在富钕相之间。
32.参考图1所述,本技术可在热变形钕铁硼磁体制备过程中,将亚微米尺度的棒状高熔点、高导热性材料按照0.1%-1.0%的质量比置入容器密封,以通过对容器上下方向施加一个震荡衰减波动使其均匀混合在钕铁硼磁粉2中,获得混合磁粉;
33.而后,可将上述混合磁粉置于特定温度和压力下,对混合磁粉进行致密化挤压获得块体或棒状的热变形前驱体,以便进一步对所述热变形前驱体进行热变形处理获得热变形钕铁硼磁体。
34.棒状高熔点、高导热性材料的不同混合比例对磁体力学性能和磁性能带来的影响可参照下表:
35.表1力学性能
36.添加量x抗弯强度/mpa抗拉强度/mpa抗压强度/mpa硬度/hvx=04402401150590x<0.1%4422451200635x=0.1%47035013107500.1%<x<1%45531012706801%<x3982001020540
37.表2磁性能
38.添加量x矫顽力/koe剩磁/kgs磁能积/mgoe密度/g/cm3x=013.3212.6438.047.6604x<0.1%13.4512.8939.657.7438x=0.1%14.6713.4343.327.81210.1%<x<1%14.2112.9841.307.74611%<x14.8610.3426.727.6542
39.本技术优选可在对所述热变形前驱体进行热变形处理前,先打磨掉热变形前驱体表面残留杂质及氧化层,然后将其置入图2所示的模具中,以便在热变形处理过程中,在模具的垂直压力方向施加局域场并在特定的温度和应变率下对前驱体进行变形处理。完成热变形过程后,可获得热变形磁体毛坯;不同热变形量对磁体的影响可参照表3所示,一般选择将热变形处理的变形量控制在70%-80%之间可获得较优性能:
40.表3不同热变形量对磁体性能的影响
[0041][0042][0043]
进一步将毛胚切割至合适形状并对其进行表面防腐处理后,即可得到高综合性能性能热变形钕铁硼磁体。该高综合性能性能热变形钕铁硼磁体的微观组织示意图如图2所示,能够通过棒状的粒径范围在5nm-10nm之间的聚乙炔、聚亚苯基硫醚、聚噻吩、mgo、beo、石墨、si、aln、碳纤维、导热玻璃、高温陶瓷中的任意一种或其组合。这些材料相较于热变形磁体具有良好的导热性,由于热压和热变形过程中磁体的受热是由内至外,会使磁体内部的温度低于表层温度,从而导致受热不均匀。通过添加高导热性物质,能够促进热量在磁体
内部的传导,从而实现组织分布的均匀性,有效提升磁性能和力学性能。
[0044]
综上,本技术利用晶界相形成高熔点、高导热性析出相来改变磁体结构和性质,利用高熔点和高导热性的析出相在热变形过程提供传热和传力,来减小磁体内部的温度场和应力场,提高磁体内部的均匀性。由此,与现有技术比,本技术的有益效果在于:
[0045]
1)本技术在热变形钕铁硼磁体配置原料混粉的过程中,通过震荡作用使两种相同粒晶不同粉末充分混合,有利于顺磁性棒状难熔物质在热变形钕铁硼磁体中均匀水平排布;并且,此过程中聚乙炔、聚亚苯基硫醚、聚噻吩、
[0046]
mgo、beo、石墨、si、aln、碳纤维、导热玻璃、高温陶瓷等材料的选择与组合可满足对添加相的需求。
[0047]
2)本技术在制备热变形钕铁硼磁体的过程中,由其在对热变形前驱体热进行变形处理的过程中,能够利用熔融的富钕相作为流通通道将不同区域联通,同时通过施加局域场原位生成顺磁性纳米颗粒,由此,顺磁性的亚微米尺度的棒状导热材料能够在局域场、应力场驱使下择优分布于主相晶粒之间,配合特殊的外加感应磁场和应力场,例如,通过热压过程施加的应力场和热变形过程施加感应磁场实现棒状相的均质分布和取向调整。使其进一步沿着垂直于压力的方向排布,能够有效隔绝主相晶粒之间的去磁耦合作用;
[0048]
3)本技术中震荡波可以均匀分散纳米粒子,保证纳米粒子在热压前驱体中分散均匀,使得随机分布的纳米棒状难熔颗粒可在磁场提高热变形过程中调整其棒状相的取向,以有效阻隔热变形钕铁硼磁体中裂纹的扩展,抑制裂纹的传递,降低磁体内部的能量传递,显著提升力学性能;
[0049]
4)本发明工艺简单,设备要求相对较低,可在原有热变形铁硼生产设备基础上进行改造完成。
[0050]
以上仅为本技术的实施方式,其描述较为具体和详细,但并不能因此而理解为对本技术专利范围的限制。应当指出的是,对于本领域的普通技术人员来说,在不脱离本技术构思的前提下,还可以做出若干变形和改进,这些均属于本技术的保护范围。