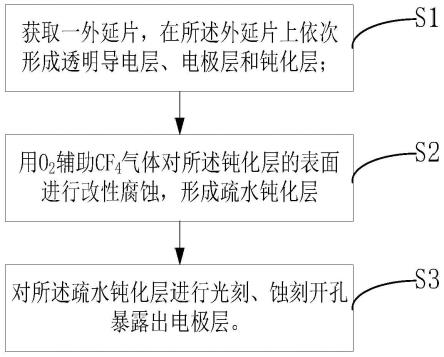
一种抗水解led芯片的制作方法
技术领域
1.本发明涉及发光二极管技术领域,尤其涉及一种抗水解led芯片的制作方法。
背景技术:2.户外的led显示屏容易受到水汽的侵蚀,水汽容易附着在led芯片的钝化层(二氧化硅膜)上并且渗透进去,导致led芯片失效。
3.为了解决上述存在的问题,申请号为202210328384.4的中国专利公开了供一种疏水性led芯片及其制备方法,其方法通过获取一衬底,在衬底上形成外延层;在外延层表面依次形成电流阻挡层、电流扩展层、金属导电层以及钝化层,对钝化层光刻、蚀刻以及去光刻胶后,得到led晶圆;对led晶圆的表面进行sih4或cf4等离子体轰击、以对led晶圆的表面进行改性处理,形成疏水性钝化层,来防止水汽吸附及渗入,从而改善led芯片漏电,提升可靠性。
4.但是该专利的技术方案是在钝化层刻蚀暴露出金属导电层后进行的表面改性,这样会导致sih4或cf4等离子体轰击或附着在金属导电层表层,影响后续焊线;而且该专利的技术方案是在对钝化层光刻、蚀刻以及去光刻胶后再进行的表面改性,若钝化层表面的光刻胶去除不干净,还容易影响钝化层表面的疏水改性效果;另外该专利的技术方案对cf4的消耗大,也没有将使用cf4改性处理的疏水效果最大化。
技术实现要素:5.本发明的目的在于克服现有技术的不足,本发明提供了一种抗水解led芯片的制作方法,通过先对钝化层改性腐蚀再开孔暴露电极层的方式避免因改性腐蚀影响电极层造成led芯片后续焊线不良,也避免了因引入光刻胶后去胶不干净而影响钝化层表面的疏水改性效果;通过用o2辅助cf4气体对钝化层进行改性腐蚀,减少了cf4气体的消耗并增强了疏水效果。本发明提供了一种抗水解led芯片的制作方法,包括以下步骤:
6.获取一外延片,在所述外延片上依次形成透明导电层、电极层和钝化层;用o2辅助cf4气体对所述钝化层的表面进行改性腐蚀,形成疏水钝化层;对所述疏水钝化层进行光刻、蚀刻开孔暴露出电极层。
7.具体的,所述用cf4气体对所述钝化层的表面进行改性腐蚀包括:
8.第一阶段:在真空环境内,通入5~10sccm的cf4气体进行稳压处理;
9.第二阶段:在真空环境内,开启射频,射频功率为80~100w,通入5~10sccm的cf4气体腐蚀所述钝化层。
10.具体的,所述第一阶段的温度条件为280~320℃,所述第二阶段的温度条件为280~320℃。
11.具体的,所述第一阶段的真空环境的压强为80~120pa;所述第二阶段的真空环境的压强为80~120pa。
12.具体的,所述第一阶段的稳压处理时间为30~60s;所述第二阶段的腐蚀处理时间
为100~120s。
13.具体的,在所述第一阶段和所述第二阶段中,通入一定量o2作为稀释气体,控制气体流量的比例cf4:o2为1:3~4。
14.具体的,在所述第二阶段中,将所述cf4气体电离成cf
3+
和f-等离子体。
15.具体的,在所述透明导电层上形成厚的电极层;在所述电极层上形成厚的钝化层;所述电极层被所述钝化层完全包覆。
16.具体的,所述疏水钝化层的整体厚度在所述疏水钝化层包括疏水子层、钝化子层。
17.具体的,所述钝化层为二氧化硅膜层、或者氮化硅膜层。
18.本发明提供的抗水解led芯片的制作方法具有以下优点:
19.先对钝化层进行改性腐蚀,再光刻、蚀刻开孔暴露出电极层,避免了cf4等离子体直接轰击电极层导致其损伤,也避免了cf4等离子体附着在电极层表层,从而避免了改性腐蚀会对led芯片后续焊线造成不良影响;
20.先对钝化层进行改性腐蚀,再光刻、蚀刻开孔暴露出电极层,还避免在对钝化层进行改性腐蚀前引入光刻胶,从而避免了因引入光刻胶后去胶不干净而影响钝化层表面的疏水改性效果;
21.通过用o2辅助cf4气体对钝化层进行改性腐蚀,减少了cf4气体的消耗并增强了疏水效果。
附图说明
22.图1是本发明实施例中抗水解led芯片的制作方法的流程示意图;
23.图2是本发明实施例中获取的外延片的结构示意图;
24.图3是本发明实施例中外延片经mesa刻蚀形成n型gan层台阶的结构示意图;
25.图4是本发明实施例中外延片经ito图案化形成透明导电层的结构示意图;
26.图5是本发明实施例中外延片经蒸镀形成电极层的结构示意图;
27.图6是本发明实施例中外延片经沉积形成钝化层的结构示意图;
28.图7是本发明实施例中钝化层经改性腐蚀形成疏水钝化层的结构示意图;
29.图8是本发明实施例中疏水钝化层经开孔暴露出电极层的结构示意图;
30.图9是本发明实施例中钝化层表面改性腐蚀的过程示意图。
31.附图中,10、蓝宝石衬底;20、n型gan层;30、量子阱发光结构;40、p型gan层;50、n型gan层台阶;60、透明导电层;70、电极层;80、钝化层;90、疏水钝化层;91、钝化子层;92、疏水子层;100、开孔。
具体实施方式
32.下面将结合本发明实施例中的附图,对本发明实施例中的技术方案进行清楚、完整地描述,显然,所描述的实施例仅仅是本发明一部分实施例,而不是全部的实施例。基于本发明中的实施例,本领域普通技术人员在没有作出创造性劳动前提下所获得的所有其它实施例,都属于本发明保护的范围。
33.图1示出了本发明实施例中抗水解led芯片的制作方法的流程示意图,该制作方法包括以下步骤:
34.s1、获取一外延片,在所述外延片上依次形成透明导电层、电极层和钝化层;
35.图2示出了本发明实施例中获取的外延片的结构示意图,外延片包括蓝宝石衬底10(厚度为500~600um)、n型gan层20、量子阱发光结构30和p型gan层40,具体的,通过mesa刻蚀在外延片上形成n型gan层台阶50,图3示出了本发明实施例中外延片经mesa刻蚀形成n型gan层台阶的结构示意图;通过ito图案化在p型gan层40上形成透明导电层60,图4示出了本发明实施例中外延片经ito图案化形成透明导电层的结构示意图;通过蒸镀的方式形成电极层70,图5示出了本发明实施例中外延片经蒸镀形成电极层的结构示意图,电极层70的厚度为厚度为由铬、钛、钌、铝、镍、铂、金等元素中的一种或多种组成,电极层70包括位于透明导电层60上的p型电极和位于n型gan层台阶50上的n型电极。
36.沿透明导电层60、电极层70和n型gan层台阶50的表面沉积形成钝化层80,将电极层70完全包覆,图6示出了本发明实施例中外延片经沉积形成钝化层的结构示意图;钝化层80的厚度要适合,的厚度就比较适中,过厚则会造成膜层之间的应力过大,容易碎裂,而且还会削弱芯片出光效果;过薄则会容易漏电,影响芯片的电学性能;在这里,钝化层80厚度适宜,并且将电极层70完全包覆,保护着电极层70避免在后续改性腐蚀过程中被cf4等离子体轰击或附着,从而避免影响后续焊线的质量。
37.控制钝化层80沉积时的温度为280~320℃,对于钝化层80沉积而言,若温度低于280℃,形成的钝化层80致密性较差,水汽容易穿过钝化层80到达芯片表面导致水解腐蚀;若温度高于320℃,电极层70中的al异常活泼,会引起电极层70鼓泡。
38.钝化层80可以是二氧化硅膜层、或者氮化硅膜层,可以与cf4气体反应,在膜层表面形成疏水薄膜。
39.s2、用o2辅助cf4气体对所述钝化层的表面进行改性腐蚀,形成疏水钝化层;
40.钝化层80沉积工序与钝化层80改性腐蚀工序是在同一设备腔体进行,可以保持获得的疏水钝化层90的洁净,确保其拥有较好的疏水效果。
41.图7示出了本发明实施例中钝化层经改性腐蚀形成疏水钝化层的结构示意图,控制疏水钝化层90的整体厚度在疏水钝化层90包括疏水子层92、钝化子层91。
42.改性腐蚀在增强等离子体气相沉积设备中进行,主要分为两个阶段:
43.第一阶段为稳压阶段,在压强为80~120pa的真空环境内,在280~320℃的温度条件下,往设备腔体内通入5~10sccm的cf4气体进行稳压处理,同时通入一定量o2作为稀释气体,控制气体流量的比例cf4:o2为1:3~4,第一阶段不开启射频,cf4气体不发生电离。
44.第一阶段的稳压处理时间需维持30~60s,目的在于排尽上一工序沉积钝化层时所使用的气体,同时使设备腔体内部的压强、温度、气氛等条件过渡到下一阶段,避免因工艺参数改变而导致工艺曲线不稳定;若稳压处理时间维持过短,则上一工序沉积钝化层80时所用的气体未能及时排出,会影响钝化层80后续改性腐蚀的效果;若稳压处理时间维持过长,则耗时过长,影响生产效率,浪费资源。第一阶段的稳压处理提高了工艺过程的稳定性,使后续改性腐蚀得到的疏水钝化层90更稳定、致密,疏水效果更佳;
45.第二阶段为改性腐蚀阶段,在压强为80~120pa的真空环境内,在280~320℃的温度条件下,用5~10sccm的cf4气体腐蚀钝化层100~120s,同时通入一定量o2作为稀释气体,控制气体流量的比例cf4:o2为1:3~4,第二阶段需要开启射频,将所述cf4气体电离成cf
3+
和f-等离子体;射频功率为80~100w,功率过小,则腐蚀速率过慢;功率过大,则会导致腐蚀速率过快,从而不便控制腐蚀反应进程。第二阶段的腐蚀处理中,在o2及一定温度、压强条件下,精确控制反应速率,对cf4气体的消耗小,且获得的疏水钝化层90的疏水效果极好。
46.当钝化层80是二氧化硅膜层时,图9示出了本发明实施例中钝化层80表面改性腐蚀的过程示意图,钝化层80表面的羟基被f-等离子体取代,将si-o键转化为si-f键,从而实现钝化层80表面由亲水性变为疏水性。
47.控制真空环境的压强为80~120pa,压强太小会使cf4气体电离不充分,压强太大会使反应产物不能及时排出。
48.为了将真空环境的压强稳定在80~120pa,则需要通入一定流量的气体,如果仅通入cf4气体,对cf4气体的需求就会比较多,而且改性腐蚀速率会比较快,难以精准控制;通入一定量o2作为稀释气体,具体的,控制气体流量的比例cf4:o2为1:3~4,用o2来填充设备腔体稳定压强,可以减少cf4气体的占比,避免因cf4气体过多而导致改性腐蚀速率过快,有利于稳定控制改性腐蚀速率;而且o2通过射频会形成o-等离子体,在该环境中,o-等离子体能使cf4气体释放更多的f-等离子体,cf4+o-→
cof2+2f-,相对提高了f-等离子体的比例,对cf4气体的利用更充分,从而减少了cf4气体的消耗。
49.控制改性腐蚀的温度为280~320℃,该温度范围延续钝化层80沉积工序的温度,这样钝化层80沉积后,即可做钝化层80表面腐蚀改性,使工序间快速衔接,提高效率;温度范围不变,有利于保持钝化层80结构的稳定,也有利于保持工艺曲线的稳定,提高产品质量。
50.用cf4气体腐蚀钝化层80,控制cf4气体的流量为5~10sccm,较为合适,便于控制腐蚀速率,若cf4气体流量过低,则会导致钝化层80表面改性不均匀,形成的疏水子层92不能完全覆盖钝化子层91的表面,影响疏水效果;若cf4气体流量过高,则会导致腐蚀速率过快,不便控制,有可能严重腐蚀钝化层80,导致形成的疏水钝化层90凹凸不平,甚至其局部的厚度小于容易漏电,影响芯片的电学性能;
51.而且需要控制cf4气体腐蚀钝化层80的时长为100~120s,腐蚀时间过短形成的疏水子层92不完整,疏水效果差;腐蚀时间过长,会严重腐蚀钝化层80,影响芯片的电学性能。
52.s3、对所述疏水钝化层进行光刻、蚀刻开孔暴露出电极层,图8示出了本发明实施例中疏水钝化层经开孔暴露出电极层的结构示意图;
53.光刻是指经曝光系统将预制在掩模版上的图形按所要求的位置,精确传递到预涂在晶圆表面的光刻胶层上。光刻包括涂胶、曝光、显影三个子工序。
54.涂胶,在晶圆上涂正性光刻胶,制成厚度为2~4um的光刻胶层,若光刻胶层偏薄,则会导致在蚀刻过程中无法保护晶圆表面,从而导致部分不需蚀刻区域被蚀刻;若光刻胶层偏厚,则不易彻底显影,同时会降低分辨率,还会增加成本。
55.曝光,曝光后,通过掩模版,使得相应位置的光刻胶发生改性,从而在后续的显影过程中,图形得以保留。曝光量为40~80mj,曝光量过小,则有可能光刻胶没被曝透,从而在后续显影过程之后,图形无法被保留;若曝光量过大,则光刻胶因化学性质的变化会变得难
以去除,在后续去胶过程会有残胶。
56.显影,保留光刻胶层中想要的图形,显影时间与曝光量配合,可使得图形尺寸与设计值一致;
57.蚀刻,利用等离子体耦合刻蚀机,主要使用o2、cf4气体,对未被光刻胶覆盖保护的二氧化硅进行蚀刻,从而露出电极层;
58.在本发明实施例中,光刻、蚀刻的主要过程为:
59.光刻过程,将正性光刻胶滴加至晶圆的疏水钝化层90表面,通过控制设备一定转速(1500~2000r/min)形成胶厚为2.8~3.4um的光刻胶层;然后,在紫外曝光机与晶圆表面的光刻胶层之间放置具有一定图形的掩膜版,开启紫外曝光机进行曝光,曝光剂量为50~70mj,受到紫外照射的光刻胶会发生变性;曝光后再经过烘烤(条件:温度100~120℃,时间60~100s)减少曝光时所形成的驻波效应,同时使得变性的光刻胶有效固化;再在晶圆表面的光刻胶层滴加显影液,显影时间为50~80s,晶圆表面的光刻胶层便可形成与掩膜版图形相同的图案。
60.蚀刻过程,将带有正性光刻胶图案的晶圆放进等电感耦合等离子刻蚀机,通入一定量的o2与cf4气体,cf4:o2气体比例为1:5~10,上射频功率为60~180w,下射频功率为200~800w,设备腔体压力维持5~10mtor。
61.若cf4气体的占比较小,则反应速率慢;若cf4气体的占比过高,则反应速率难以控制。
62.若上射频功率过低,则会导致产生的等离子体数量少,反应慢;若上射频功率过高,则产生的等离子体数量过多,则会抑制反应速率。
63.若下射频功率过低,则影响等离子体轰击时的能量,物理轰击能力较弱,反应较慢;若下射频功率过高,则等离子体蚀刻二氧化硅过程会将au电极表层轰伤,导致芯片电压偏高;
64.若设备腔体压力设定得过低,即真空度过低,则设备可能无法实现,或抽真空时间过长影响效率;若设备腔体压力设定得偏高,即真空度偏高,则腔体内存在气体杂质离子、原子、分子等,影响干法蚀刻效果。
65.通过一定量的o2,可加速蚀刻钝化层的二氧化硅,此外由于蚀刻在富氧条件下进行,相当于稀释了cf4气体,可以避免cf4与au电极层表面反应。
66.先对钝化层80进行改性腐蚀,再开孔暴露出电极层70,避免了cf4等离子体直接轰击电极层70导致其损伤,也避免了cf4等离子体附着在电极层70表层,从而避免了改性腐蚀会对led芯片后续焊线造成不良影响;
67.在对钝化层80进行改性腐蚀之后再光刻、蚀刻开孔暴露出电极层70,还避免了因引入光刻胶后去胶不干净而影响钝化层80表面的疏水改性效果;
68.最后,在85℃和85% rh的条件下对封装后的led芯片进行抗水解验证,本质是检测led芯片在高温高湿条件下,水汽能否透过钝化层80进入芯片内部进行电化学腐蚀,使led芯片失效,没有失效就判定为合格;改性腐蚀前的led芯片的合格率为60%,改性腐蚀后的抗水解led芯片的合格率为95%,合格率提高了35%,抗水解能力显著增强。
69.本发明实施例所提供的一种抗水解led芯片的制作方法,先对钝化层80进行改性腐蚀,再光刻、蚀刻开孔暴露出电极层70,避免了cf4等离子体直接轰击电极层70导致其损
伤,也避免了cf4等离子体附着在电极层70表层,从而避免了改性腐蚀会对led芯片后续焊线造成不良影响;
70.先对钝化层80进行改性腐蚀,再光刻、蚀刻开孔暴露出电极层70,还避免在对钝化层80进行改性腐蚀前引入光刻胶,从而避免了因引入光刻胶后去胶不干净而影响钝化层80表面的疏水改性效果;
71.通过用o2辅助cf4气体对钝化层80进行改性腐蚀,开启射频后cf4气体在o2的作用下相对提高了f-等离子体的比例,大幅度降低了cf4气体的消耗,更环保;
72.而且钝化层80沉积工序与钝化层80改性腐蚀工序是在同一设备腔体进行,工序间过渡稳定,不仅可以保持获得的疏水钝化层90的洁净,确保其拥有较好的疏水效果;还提高了工艺过程的稳定性,形成的疏水钝化层90致密性好,抗水解能力更佳。
73.以上对本发明实施例所提供的一种抗水解led芯片的制作方法进行了详细介绍,本文中应采用了具体个例对本发明的原理及实施方式进行了阐述,以上实施例的说明只是用于帮助理解本发明的方法及其核心思想;同时,对于本领域的一般技术人员,依据本发明的思想,在具体实施方式及应用范围上均会有改变之处,综上所述,本说明书内容不应理解为对本发明的限制。