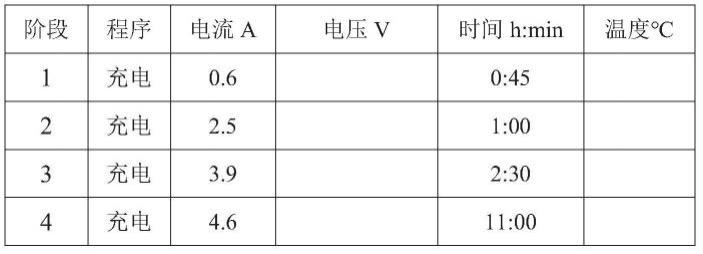
1.本发明涉及蓄电池技术领域,特别是涉及一种蓄电池内化成工艺方法。
背景技术:2.铅蓄电池是一种广泛使用的一种化学电源,该产品具有良好的可逆性、电压特性平稳、使用寿命长、适用范围广、原材料丰富、可再生使用,且造价低廉等优点。近年来,随着环保意识的增强及能源问题的日趋严重,铅蓄电池作为动力电源在电动车系统中起着极其重要的作用。
3.在工厂电池制作过程工序中所涉及的电池电化学转化技术,电池化成充放电工艺的方法直接影响成品电池的容量、充电接受能力、放电效率等性能特性。为了实现更换的电池化成充放电能力、提高生产效率、降低能耗,采用优化电池化成充电工艺以及对电池进行性能一致性的筛选,对后期电池使用寿命以及降低电池退货率有重要意义。
4.如何提高配组一致性,是提升蓄电池组一致性的其中一个关键。
5.比如,公开号为cn111416164a的发明公开了一种蓄电池内化成配组方法,在容检放电时,放电到10.3v/只以下;配组时,回看每只电池容检放电到10.3v时所需的放电时间,根据该放电时间进行分档,取同一档中的若干只电池配为一组,从而可以基本确保所有电池的容量能够完全放电到终止而被筛选到,提高筛选范围,提高一次性放电合格率和配组率。
6.再比如,公开号为cn106972212a的发明公开了一种铅蓄电池内化成及配组方法,内化成中的容检放电阶段先以电流1~3c安培进行定时间或定电压放电,记录终止电压值为电压1;再以电流0.5c安培放电至平均电压10.2~10.5v,记录终止电压值为电压2,容检放电阶段放出容量控制在1.0~1.1c安时;内化成结束后,蓄电池下线,静置后检测开路电压;以电压1为指标剔除不合格蓄电池,再以电压2分档后配组,且需保证同一组内蓄电池的开路电压差值不大于20mv。然而,上述现有技术中分档方法还是比较粗糙,同一组中的不同电池之间差异依然比较大。
7.现有技术中还有在电池内化成工艺过程中的容量检测阶段之前,先以恒电流值i2(a)对电池进行充电、放电几次周期,到达容量检测时以1~3c(a)进行定时间或定电压放电到终止到设定电压值1.75v/单格,再以放电时间值大小或电压值大小进行分段筛选,根据指标剔除不合格蓄电池,实现线上容量检测分类配组方法,结束后,再对电池回充电满电后进行小电流0.03~0.05c i2(a)浮充电,在浮充电进行的同时,对电池抽取多余电解液,控制电池内部极群电解液饱和度在96~98%,实现铅蓄电池阀控式贫液原理。
8.上述技术中,如电池容量检测放电后已筛选分档完毕,再进行小电流浮充电抽取多余电解液(游离酸),这样存在问题是电池抽完余酸后,电池内部电解液含量发生变化,电池容量也随之发生改变,从而影响前期电池容量检测分档的准确性。
技术实现要素:9.本发明针对现有技术中存在的不足,提供了一种蓄电池内化成充电工艺方法。
10.一种蓄电池内化成充电工艺方法,包括以下步骤:
11.在蓄电池内化成至容检阶段前,蓄电池内部真空负压后进行抽酸;
12.(2)抽酸前,先对蓄电池进行恒流浮充电,达到设定电压值,且电池内部酸液温度控制在40~45℃时,再进行抽酸;
13.(3)抽酸完成后,进行容检放电,同批次蓄电池设置终止电压,采集放电时间,根据放电时间进行分档,线上配组;
14.(4)配组完成后,将蓄电池进行回充满电,蓄电池下线。
15.优选的,步骤(1)中真空负压为-0.07~-0.08mpa。
16.本发明规定抽取多余电池内部游离酸工艺,必须在容量放电检测之前、负压真空-0.07~-0.08mpa之后进行,避免电池容量检测结束后电池容量配组发生改变。
17.优选的,步骤(2)中,对蓄电池进行恒流浮充电,恒流为0.03~0.05c i2。步骤(2)中设定电压值为2.70~2.74v/单格。步骤(2)中抽酸过程中保持恒流浮充电。
18.对电池进行恒小电流0.03~0.05c i2(a)浮充电,必须达到电池电压值在2.70~2.74v/单格,电池内部酸液温度控制在40~45℃,温度大小根据水浴槽冷却书流量大小进行调节,才可以进行抽取余酸动作,提高电池性能一致性,抽取游离酸的同时,充电设备不能暂停工艺。
19.优选的,步骤(3)中设置的终止电压为每单格1.683v。
20.步骤(3)中,根据放电时间进行分档,选取单只蓄电池容检放电到1.75v/单格时所需的放电时间。
21.结束抽取游离酸后,电池接着进行容量放电工艺,过度不能暂停或静止工艺,终止电压1.683v/单格(回路总电压值根据电池只数决定),放电时间大小分档配组,选取单只1.75v/单格档位,从而基本确保了所有电池都能够放电到1.683v/单格以下,这样在配组时,回看每只电池容检放电到1.75v/单格时所需的放电时间,基本可以确保所有电池都能够在一次放电容检就能够配组完成。
22.内化成充放电工艺具体操作步骤:
23.每个回路有24只电池串联组成,内化成步骤包括六步放电、十七步充电;
24.一充:以恒电流0.06i2充电45min;
25.二充:以恒电流0.25i2充电60min;
26.三充:以恒电流0.39i2充电2.5h;
27.四充:以恒电流0.46i2充电11h;
28.五充:以恒电流0.40i2充电4h;
29.一放:以恒电流0.8i2放电18min;
30.六充:以恒电流0.46i2充电7h;
31.七充:以恒电流0.42i2充电1.5h;
32.二放:以恒电流0.8i2放电45min;
33.八充:以恒电流0.46i2充电5.5h;
34.九充:以恒电流0.42i2充电2.0h;
35.三放:以恒电流0.8i2放电50min;
36.十充:以恒电流0.46i2充电5.5h;
37.十一充:以恒电流0.42i2充电1.5h;
38.四放:以恒电流0.8i2放电1.0h;
39.十二充:以恒电流0.45i2充电3.5h;
40.十三充:以恒电流0.38i2充电3.0h,充电结束后进行负压真空-0.07~-0.08mpa;
41.十四充:以恒电流0.03~0.05浮充3.0h,酸液温度为40~45℃,电压值在2.70~2.74v/单格;
42.五放:以恒电流0.8i2放电2.0h;
43.六放:以恒电流0.8i2放电,限压终止电压1.683v/单格;
44.十五充:以恒电流0.49i2充电4.0h;
45.十六充:以恒电流0.43i2充电2.5h;
46.十七充:以恒电流0.3i2充电2.0h;
47.结束。
48.电池下线后,在过度平台静置需≥2.0h后,盖上安全帽。
49.本发明的有益效果:
50.本发明蓄电池内化成工艺方法通过容量检测前进行抽取多余游离酸方法,并且控制抽酸电池电压值、酸温度、安全帽静止≥2.0h后再盖上,从而可以确保所有电池在线放电一次性合格率、容量在线配组合格率,提高电池筛选准确性、稳定性、性能一致性。
附图说明
51.图1为现有工艺电池组循环寿命图。
52.图2为本发明工艺电池组循环寿命情况图。
具体实施方式
53.实施例1
54.型号为6-dzf-20的铅蓄电池,10000只电池,内化成充放电工艺参数如表1所示。
55.表1
56.[0057][0058]
如表1所示,电池化成过程中整个工艺分两个部份,充电工艺和放电工艺阶段,充电工艺1-19步,放电工艺20-24步。充电工艺第1-5步、第7-8步、第10-11步、第13-14步、第16-18步采用恒电流充电、共4步恒流放电,在最后第19步采用恒电流浮充方式,限压16.2v,酸温度控制40℃,调节冷却水循环流量,并同时监控电池内部酸温度,当浮充电1.5小时后开始进行抽取游离酸,每回路24只电池串联方式,总放电终止电压限制在242.4v。
[0059]
根据以上方法进行,工艺到达第20-21步时,电池组回路放电时间,可明显电池的放电容量一致性较高,提高5%电池合格率、提高电池配组率。结果如下表2所示。
[0060]
表2
[0061][0062]
电池结束化成工艺后下架后,经静置2h以上后盖安全帽,封电池盖片后测量开路电压值,开路电压值极差小、电压稳定性较好,如下表3。
[0063]
表3
[0064][0065]
实施例2
[0066]
型号为6-dzf-20的铅蓄电池,10000只电池,内化成充放电工艺参数如表1所示。
[0067]
如表1所示,电池化成过程中整个工艺分两个部份,充电工艺和放电工艺阶段,充电工艺1-19步,放电工艺20-24步。充电工艺第1-5步、第7-8步、第10-11步、第13-14步、第16-18步采用恒电流充电、共4步恒流放电,在最后第19步采用恒电流浮充方式,限压16.4v,酸温度控制45℃,调节冷却水循环流量,并同时监控电池内部酸温度,当浮充电1.5小时后开始进行抽取游离酸,每回路24只电池串联方式,总放电终止电压限制在242.4v。
[0068]
根据以上方法进行,工艺到达第20-21步时,电池组回路放电时间进行档位筛选,可明显电池的放电容量一致性较高,提高6%电池合格率、提高电池配组率。结果如下表4所示。
[0069]
表4
[0070][0071]
电池结束化成工艺后下架后,经静置3h后盖安全帽,封电池盖片后测量开路电压值,开路电压值极差小、电压稳定性较好,如下表5。
[0072]
表5
[0073][0074]
对比例1
[0075]
型号为6-dzf-20的铅蓄电池,10000只电池,内化成充放电工艺参数如表6所示。
[0076]
表6
[0077]
阶段程序电流(a)电压时间1充电3 5h2充电5 7h30min3放电5 30min4充电5 3h5放电6 1h6充电5 3h30min7放电8 1h8充电5 3h30min9放电8 1h
10充电5 4h11放电8 1h15min12充电5 4h13放电8 1h15min14充电5 7h15充电3.5 5h16放电10至平均11v/只1h40min17放电10至平均10.3v/只 18充电5 6h19充电3.5 5h20充电2 2h21充电(抽酸)0.3 5h
[0078]
如表6所示,电池化成过程中整个工艺分两个部份,充电工艺和放电工艺阶段,充电工艺1-15步,放电工艺16-21步。根据充电工艺第16-17步放电容量检测后,经过到21步进行抽酸工艺,每回路18只电池串联方式,总放电终止电压限制在185.4v。
[0079]
表7
[0080][0081][0082]
根据以上工艺方法化成充电,在线容量放电检测,整体电池容量2h率偏低在120-124min。电池放电合格率79.8%,配组合格率90.9%。
[0083]
电池结束化成工艺后下架后,按照现有工艺流水想测量开路电压值,开路电压值极差大、电压稳定性较差,如下表8。
[0084]
表8
[0085][0086]
根据实施例和对比例各抽样电池10组48v/20ah进行常温容量性能检测对比,常温容量都合格符合出货标准,并且本发明新工艺抽样电池比现有工艺初始容量偏高约2分钟。结果如表9所示。
[0087]
表9
[0088][0089]
抽样现有工艺电池与本发明工艺电池各1组进行循环寿命测试对比,图1是现有加酸化成充电工艺电池组循环寿命情况,图2是发明新工艺电池组循环寿命情况,结果显示,本发明的工艺制备出的电池循环寿命比现有工艺寿命多50次左右。