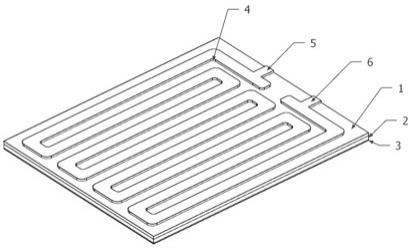
1.本发明属于液冷板技术领域,特别涉及一种基于石墨烯涂层液冷板及其制备方法。
背景技术:2.动力电池是新能源电动汽车的能量来源,其工作效率制约着电动汽车的行驶里程与行驶速度。动力电池工作电流大,产热量高,同时电池处于一个相对封闭的环境,散热难,容易导致动力电池温度上升;动力电池对温度的敏感性很高,温度过高时,容易造成电池包模组一致性差、寿命缩短,电机和电控寿命也会手段,更甚者容易引发电池热失控,从而使电池发生爆炸。电池的性能安全稳定,将成为影响新能源电动汽车未来发展的重要因素,液冷板能够有效解决动力电池散热难、温度过高问题。液冷板是通过在液冷板流道内通入冷却液,短时间内带走大量热量,实现电池组迅速降温。
3.现有的液冷板主要存在以下缺陷:管板式液冷板体积较大占用空间大,且圆管本身的形状在电池包的设计上存在较多的限制,管式散热器受结构的限制,管道与换热面积接触面积相对较小,从而热交换效率降低,且无法适应电池箱中复杂的结构特点;型材类液冷板壁厚过大,本身较重,运用到电池系统上无法达到轻量化的目的,且成本较高;采用先冲压上下板材再钎焊焊接的工艺,加工难度大,在液冷板形状复杂的情况下,很难保证上下液冷板的整体密封性,而且加工效率低、次品率较高、焊接加工污染较严重、液冷板散热性能较差等。亟需研发安全环保且性能优越的新型液冷板。
技术实现要素:4.本发明的目的在于提供一种基于石墨烯涂层液冷板及其制备方法,克服背景技术提高的不足与缺陷。
5.为实现上述目的,本发明提供了一种基于石墨烯涂层液冷板,包括:上基板、下基板、石墨烯涂层,所述上基板上设置有凹槽,所述上基板和下基板之间通过凹槽形成用于流通冷却液的流动通道,所述流动通道分别连接进液口和出液口;所述石墨烯涂层设于所述下基板远离所述上基板的一面,所述石墨烯涂层设有阵列排布的凹形单元微结构;所述上基板和下基板通过轧制连接在一起,所述流动通道通过吹胀成型制得。石墨烯涂层具有优异的导热性,有利于热量向冷却液传导,在石墨烯涂层表面设置阵列排布的凹形单元微结构,有利于加大换热面积进行充分散热和传热,提高热交换效率,提高液冷板的散热效果。采用轧制和吹胀成型,液冷板的密封可靠性更高,整体成形性好。
6.优先的,上述基于石墨烯涂层液冷板中,所述凹形单元微结构形状为圆柱形。
7.优先的,上述基于石墨烯涂层液冷板中,所述凹形单元微结构的直径为100~300μm,深度为20~40μm,凹形单元微结构之间间距为100~300μm。
8.优先的,上述基于石墨烯涂层液冷板中,所述下基板为石墨烯增强铝基板,所述上基板为铝板。下基板采用石墨烯增强铝基板强度好、导热性能好,上基板采用铝板有利于吹
胀成型。
9.一种上述的基于石墨烯涂层液冷板的制备方法,包括以下步骤:(1)石墨烯增强铝基板的制备;(2)将石墨烯增强铝基板一面进行粗化处理,对非流动通道区域进行遮挡,将石墨烯油基涂料涂覆在石墨烯增强铝基板粗糙面上,干燥形成石墨烯流动流道线路图;(3)在步骤(2)处理得到的石墨烯增强铝基板具有石墨烯流动流道线路图的一面覆盖一层铝板,进行热轧复合、退火处理;(4)采用吹胀工艺成型流动通道;(5)在石墨烯增强铝基板远离所述上基板的一面进行粗化,涂覆石墨烯涂层;(6)采用激光刻蚀在石墨烯涂层上制备阵列排布的凹形单元微结构。
10.优选的,上述的基于石墨烯涂层液冷板的制备方法中,所述步骤(1)中,石墨烯增强铝基板的制备过程为:采用真空蒸镀法在石墨烯气凝胶表面形成锡膜;将所述表面形成有锡膜的石墨烯气凝胶通过搅拌粉碎得到表面形成有锡膜的石墨烯粉体;将铝锭熔融成铝液,加入有锡膜的石墨烯粉体混合,按照石墨烯与铝锭的重量比为0.002~0.005:1进行添加;倒入模具中冷却,轧制、退火得到石墨烯增强铝基板。加入石墨烯能够提高铝板的强度和导热性,但是石墨烯与铝的密度和表面性能差别大,石墨烯难以在铝基中分散均匀,表面形成有锡膜的石墨烯粉体,能够改善了石墨烯粉体和铝基体之间的浸润性,提高石墨烯在铝基中的分散均匀,表面锡膜还可以有效避免碳与铝在高温下反应形成脆性相,提高铝板的强度。
11.优选的,上述的基于石墨烯涂层液冷板的制备方法中,所述石墨烯油基涂料为石墨烯粉末与聚二甲基硅氧烷的质量比为1:8~15进行混合,然后加入有机溶剂稀释3~8倍得到。
12.优选的,上述的基于石墨烯涂层液冷板的制备方法中,所述步骤(3)中,热轧温度为400~450℃,退火处理为:400℃~450℃温度下热压处理1h~3h。
13.优选的,上述的基于石墨烯涂层液冷板的制备方法中,所述步骤(5)具体过程包括:将氧化石墨烯分散在水中,氧化石墨烯与水比例为1~15mg:1ml,然后加入氧化石墨烯重量的30~50%的r-氨基丙基三乙氧基硅烷,超声分散1~3h,得到改性氧化石墨烯分散液;将改性氧化石墨烯分散液涂覆在石墨烯增强铝基板的粗化面,然后在氢气和氩气气氛中400~500℃进行热处理1~2h得到石墨烯涂层。采用r-氨基丙基三乙氧基硅烷对氧化石墨烯进行改性,然后涂覆在基板上,能够增强石墨烯涂层与基板的结合力。
14.优选的,上述的基于石墨烯涂层液冷板的制备方法中,所述石墨烯涂层的厚度为30~50μm。
15.与现有的技术相比,本发明具有如下有益效果:1. 本发明的基于石墨烯涂层液冷板,利用石墨烯涂层具有优异的导热性,能够将热量向液冷板的流动通道中冷却液传导,在石墨烯涂层表面设置阵列排布的凹形单元微结构,有利于加大换热面积进行充分散热和传热,提高热交换效率,提升液冷板的散热效果。采用上基板和下基板通过轧制连接,流动通道通过吹胀成型,使得液冷板的密封可靠性更高,整体成形性好。
16.2. 本发明的基于石墨烯涂层液冷板的制备方法中,采用表面形成有锡膜的石墨
烯粉体与铝液混合制备石墨烯增强铝基板,能够改善了石墨烯粉体和铝基体之间的浸润性,提高石墨烯在铝基中的分散均匀,表面锡膜还可以有效避免碳与铝在高温下反应形成脆性相,从而提高铝板的强度和导热性。采用石墨烯油基涂料涂覆在石墨烯增强铝基板粗糙面上形成石墨烯流动流道线路图,由于石墨烯的防键合作用,在上基板和下基板轧制连接时流动流通位置并未连接,通过吹胀成型即可得到用于流通冷却液的流动通道。
附图说明
17.图1为本发明实施例1的液冷板结构示意图。
18.图2为本发明实施例1的液冷板石墨烯涂层局部放大结构示意图。
19.主要图例说明:1-上基板,2-下基板,3-石墨烯涂层,4-流动通道,5-进液口,6-出液口,7-凹形单元微结构。
具体实施方式
20.下面对本发明的具体实施方式进行详细描述,但应当理解本发明的保护范围并不受具体实施方式的限制。
21.实施例1如图1和图2所示,一种基于石墨烯涂层液冷板,包括上基板1、与上基板1通过轧制连接的下基板2以及设于下基板2远离上基板1的一面石墨烯涂层3,上基板1上设置有凹槽,上基板1和下基板2之间通过凹槽形成用于流通冷却液的流动通道4,流动通道4分别连接进液口5和出液口6,流动通道通过吹胀成型制得;石墨烯涂层3设有阵列排布的凹形单元微结构7。凹形单元微结构为圆柱形,直径为200μm,深度为20μm,凹形单元微结构之间间距l为200μm。上基板1为铝板,下基板2为石墨烯增强铝基板。
22.本实施例的基于石墨烯涂层液冷板的制备方法,包括以下步骤:(1)石墨烯增强铝基板的制备:采用真空蒸镀法在石墨烯气凝胶表面形成锡膜,石墨烯气凝胶放入真空镀膜设备中,对真空室进行抽真空处理,真空度至0.1pa,对样品进行离子轰击,电压为200v,轰击时间为30min;然后进行镀锡,真空蒸镀工作压强为10-4
pa,蒸发功率为300w,蒸镀时间为10min,得到表面形成有铝膜的石墨烯气凝胶;将表面形成有锡膜的石墨烯气凝胶通过密封磁力搅拌粉碎,搅拌机转速为500rpm/min,搅拌时间为15min,得到表面形成有锡膜的石墨烯粉体;将铝锭置于熔炉内650℃熔融成铝液,加入有锡膜的石墨烯粉体搅拌混合,按照石墨烯与铝锭的重量比为0.0035:1进行添加;倒入模具中常温空冷,压制,得到石墨烯增强铝基板;(2)将石墨烯增强铝基板一面进行粗化处理,对非流动通道区域进行遮挡,将石墨烯油基涂料涂覆在石墨烯增强铝基板粗糙面上,石墨烯油基涂料为石墨烯粉末与聚二甲基硅氧烷的质量比为1:12进行混合,然后加入甲苯稀释5倍得到;真空100℃干燥形成石墨烯流动流道线路图;(3)在步骤(2)处理得到的石墨烯增强铝基板具有石墨烯流动流道线路图的一面覆盖一层纯铝板,对齐铆合,在400℃加热炉中加热后,送入热轧机内轧制,然后450℃温度
下热压处理1h,得到复合铝板;(4)在复合铝板石墨烯线路位置钻工艺孔至石墨烯层,通过工艺孔进气,石墨烯流动流道线路上的铝板膨胀形成用于流通冷却液的流动通道;(5)在石墨烯增强铝基板远离上基板的一面进行粗化,涂覆石墨烯涂层,具体过程包括:将氧化石墨烯分散在水中,氧化石墨烯与水比例为10mg:1ml,然后加入氧化石墨烯重量30%的r-氨基丙基三乙氧基硅烷,超声分散2h,得到改性氧化石墨烯分散液;将改性氧化石墨烯分散液涂覆在石墨烯增强铝基板的粗化面,然后在氢气和氩气气氛(v(h2):v(ar)=30:70)中450℃进行热处理1h得到石墨烯涂层,石墨烯涂层厚度为30μm;(6)采用激光刻蚀在石墨烯涂层上制备阵列排布的凹形单元微结构,激光加工时,控制功率为5w,频率为20000hz,脉冲为300ns,扫描速度为300mm/s。
23.实施例2一种基于石墨烯涂层液冷板,包括上基板、与上基板通过轧制连接的下基板以及设于下基板远离上基板的一面石墨烯涂层,上基板上设置有凹槽,上基板和下基板之间通过凹槽形成用于流通冷却液的流动通道,流动通道分别连接进液口和出液口,流动通道通过吹胀成型制得;石墨烯涂层设有阵列排布的凹形单元微结构。凹形单元微结构为圆柱形,直径为200μm,深度为20μm,凹形单元微结构之间间距l为100μm。上基板为铝板,下基板为石墨烯增强铝基板。
24.本实施例的基于石墨烯涂层液冷板的制备方法,包括以下步骤:(1)石墨烯增强铝基板的制备:采用真空蒸镀法在石墨烯气凝胶表面形成锡膜,石墨烯气凝胶放入真空镀膜设备中,对真空室进行抽真空处理,真空度至0.1pa,对样品进行离子轰击,电压为200v,轰击时间为30min;然后进行镀锡,真空蒸镀工作压强为10-4
pa,蒸发功率为300w,蒸镀时间为10min,得到表面形成有铝膜的石墨烯气凝胶;将表面形成有锡膜的石墨烯气凝胶通过密封磁力搅拌粉碎,搅拌机转速为500rpm/min,搅拌时间为15min,得到表面形成有锡膜的石墨烯粉体;将铝锭置于熔炉内650℃熔融成铝液,加入有锡膜的石墨烯粉体搅拌混合,按照石墨烯与铝锭的重量比为0.002:1进行添加;倒入模具中常温空冷,压制,得到石墨烯增强铝基板;(2)将石墨烯增强铝基板一面进行粗化处理,对非流动通道区域进行遮挡,将石墨烯油基涂料涂覆在石墨烯增强铝基板粗糙面上,石墨烯油基涂料为石墨烯粉末与聚二甲基硅氧烷的质量比为1:12进行混合,然后加入甲苯稀释5倍得到;真空100℃干燥形成石墨烯流动流道线路图;(3)在步骤(2)处理得到的石墨烯增强铝基板具有石墨烯流动流道线路图的一面覆盖一层纯铝板,对齐铆合,在400℃加热炉中加热后,送入热轧机内轧制,然后450℃温度下热压处理1h,得到复合铝板;(4)在复合铝板石墨烯线路位置钻工艺孔至石墨烯层,通过工艺孔进气,石墨烯流动流道线路上的铝板膨胀形成用于流通冷却液的流动通道;(5)在石墨烯增强铝基板远离上基板的一面进行粗化,涂覆石墨烯涂层,具体过程包括:将氧化石墨烯分散在水中,氧化石墨烯与水比例为10mg:1ml,然后加入氧化石墨烯重量30%的r-氨基丙基三乙氧基硅烷,超声分散2h,得到改性氧化石墨烯分散液;将改性氧化
石墨烯分散液涂覆在石墨烯增强铝基板的粗化面,然后在氢气和氩气气氛(v(h2):v(ar)=30:70)中450℃进行热处理1h得到石墨烯涂层,石墨烯涂层厚度为30μm;(6)采用激光刻蚀在石墨烯涂层上制备阵列排布的凹形单元微结构,激光加工时,控制功率为5w,频率为20000hz,脉冲为300ns,扫描速度为300mm/s。
25.对比例1本对比例同实施例1,不同在于:本对比例中石墨烯涂层3没有设置阵列排布的凹形单元微结构。实施例1和对比例1的液冷板对电池进行散热,实施例1的液冷板散热效率高、散热效果好。
26.对比例2本对比例同实施例1,不同在于:制备方法中步骤(1)为:采用真空蒸镀法在石墨烯气凝胶表面形成铝膜,石墨烯气凝胶放入真空镀膜设备中,对真空室进行抽真空处理,真空度至0.1pa,对样品进行离子轰击,电压为200v,轰击时间为30min;然后进行镀铝,真空蒸镀工作压强为5
×
10-3
pa,蒸发功率为500w,蒸镀时间为5min,得到表面形成有铝膜的石墨烯气凝胶;将表面形成有铝膜的石墨烯气凝胶通过密封磁力搅拌粉碎,搅拌机转速为500rpm/min,搅拌时间为15min,得到表面形成有铝膜的石墨烯粉体;将铝锭置于熔炉内650℃熔融成铝液,加入有铝膜的石墨烯粉体搅拌混合,按照石墨烯与铝锭的重量比为0.0035:1进行添加;倒入模具中常温空冷,压制,得到石墨烯增强铝基板。
27.采用激光导热仪测定实施例1~2、对比例2制备的石墨烯增强铝基板和纯铝板的导热系数,采用万能试验机实施例1~2、对比例2制备的石墨烯增强铝基板和纯铝板进行了拉伸强度测试,采用板形试样测试,测试参照hb5143-96金属室温拉伸试验方法。结果如表1。
28.由表1可知,实施例组的导热系数和拉伸强度都高于对比例和纯铝板,说明本发明制备的石墨烯增强铝基板导热系数和力学性能得到提高,有利于提高液冷板的散热性能和热交换效率以及承载能力。
29.表1 石墨烯增强铝基板和纯铝板的导热系数和拉伸强度组别拉伸强度(mpa)导热系数/w/(m*k)实施例1190.4247.8实施例2181.2236.1对比例2183.5241.7纯铝板113.8211.5前述对本发明的具体示例性实施方案的描述是为了说明和例证的目的。这些描述并非想将本发明限定为所公开的精确形式,并且很显然,根据上述教导,可以进行很多改变和变化。对示例性实施例进行选择和描述的目的在于解释本发明的特定原理及其实际应用,从而使得本领域的技术人员能够实现并利用本发明的各种不同的示例性实施方案以及各种不同的选择和改变。本发明的范围意在由权利要求书及其等同形式所限定。