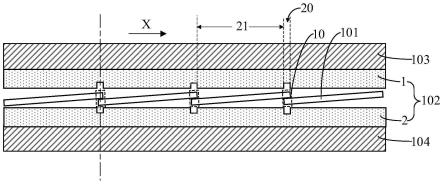
1.本技术实施例涉及太阳能电池领域,特别涉及一种光伏组件及制备方法。
背景技术:2.光伏组件,也叫太阳能电池板,通过“光伏打效应”而发电。叠焊技术作为一种新型的组装方式,通过将相邻的电池片进行微间距“重叠”焊联,极大缩短了传统焊接过程中电池片间距,实现了高能量密度,增加了组件功率。
3.然而,目前在采用叠焊技术对光伏组件进行组装的过程中,容易发生隐裂的问题。
技术实现要素:4.本技术实施例提供一种光伏组件及制备方法,至少有利于改善在采用叠焊技术对光伏组件进行组装的过程中容易发生隐裂的问题。
5.本技术实施例提供一种光伏组件,包括:多个电池片,多个所述电池片沿第一方向排布,且一所述电池片的一个端部与相邻的所述电池片的一个端部层叠放置,其中,两个所述电池片层叠的区域形成叠焊区域,所述叠焊区域具有叠焊中心,其中,一所述电池片对应的所述叠焊中心到该所述电池片远离所述叠焊中心的侧边之间的距离为第一距离,所述第一距离与所述电池片沿所述第一方向的宽度之比为99.693%~99.783%;胶膜,所述胶膜覆盖所述多个电池片表面,所述胶膜包括压痕区域和与所述压痕区域相接的非压痕区域,至少部分所述压痕区域与所述叠焊区域重叠,所述压痕区域的胶膜厚度小于所述非压痕区域的胶膜厚度,且所述压痕区域的中心与所述叠焊中心重合。
6.另外,电池片沿所述第一方向的宽度为182mm~193mm,所述第一距离与所述电池片沿所述第一方向的宽度之比为99.725%~99.741%。
7.另外,电池片沿所述第一方向的宽度为163mm~165mm,所述第一距离与所述电池片沿所述第一方向的宽度之比为99.693%~99.697%。
8.另外,所述电池片沿所述第一方向的宽度为210~230mm,所述第一距离与所述电池片沿所述第一方向的宽度之比为99.762%~99.783%。
9.另外,压痕区域的胶膜与所述叠焊区域的电池片重合。
10.另外,叠焊区域在所述胶膜上的正投影位于所述压痕区域内,所述压痕区域在所述第一方向上的宽度与所述叠焊区域在所述第一方向上的宽度之比为1:40。
11.另外,叠焊区域在沿所述第一方向上的宽度为0.5mm。
12.另外,压痕区域的胶膜厚度与所述非压痕区域的胶膜厚度之比不大于1。
13.另外,压痕区域的胶膜厚度为不大于0.8mm,所述非压痕区域的胶膜厚度为0.2mm~0.8mm。
14.另外,电池片在第一方向上的宽度与所述电池片在第二方向上的长度之比为0.3543~0.7055,所述第二方向垂直于所述第一方向。
15.相应地,本技术实施例还提供一种光伏组件的制备方法,应用于上述任一项所述
的光伏组件,包括:提供多个电池片,多个所述电池片沿第一方向排布,且一所述电池片的一个端部与相邻的所述电池片的一个端部层叠放置,其中,两个所述电池片层叠的区域形成叠焊区域,所述叠焊区域具有叠焊中心,其中,一所述电池片对应的所述叠焊中心到该所述电池片远离所述叠焊中心的侧边之间的距离为第一距离,所述第一距离与所述电池片沿所述第一方向的宽度之比为99.693%~99.783%;在所述多个电池片表面铺设胶膜,所述胶膜包括压痕区域和与所述压痕区域相接的非压痕区域,至少部分所述压痕区域与所述叠焊区域重叠,所述压痕区域的胶膜厚度小于所述非压痕区域的胶膜厚度,且所述压痕区域的中心与所述叠焊中心重合。
16.另外,基于所述第一距离与所述电池片沿所述第一方向的宽度之比和所述电池片沿所述第一方向上的宽度制备所述胶膜。
17.另外,制备所述胶膜的方法包括:制备初始胶膜,所述初始胶膜的表面为平整表面;采用多个间隔排布的压辊对所述初始胶膜进行热压,以在所述初始胶膜表面形成多个间隔排布的所述压痕区域,具体包括:基于所述第一距离与所述电池片沿所述第一方向的宽度之比和所述电池片沿所述第一方向上的宽度,调整所述压辊间距,以在所述初始胶膜表面形成多个所述压痕区域,得到所述胶膜。
18.本技术实施例提供的技术方案至少具有以下优点:
19.本技术实施例提供的光伏组件的技术方案中,设置电池片对应的叠焊中心到该电池片远离叠焊区域的侧边之间的距离为第一距离,第一距离与电池片沿第一方向的宽度之比为99.693%~99.783%,即对叠焊中心在电池片中沿第一方向上的位置进行了限定,在这个范围内,既保持了光伏组件中层叠放置的电池片的数量较多,保证光伏组件中的电池片具有较高的密度。另一方面,通过合理设置叠焊中心到电池片远离叠焊区域的侧边之间的距离,进而调整叠焊区域与非叠焊区域(电池片中除叠焊区域以外的区域)在电池片中所占的宽度比例,使得在对光伏组件进行层压时,该叠焊中心所在的叠焊区域的电池片所受到的层压应力传递至与叠焊区域相邻的非叠焊区域的电池片上时,对非叠焊区域的电池片产生的弯矩不会过大,进而可以改善非叠焊区域的电池片表面在受到过大的弯矩的作用下发生弯曲甚至隐裂的问题。此外,还设置胶膜,压痕区域的胶膜厚度较薄,可以防止发生由于层压时叠焊区域的胶膜厚度过大而对叠焊区域的电池片产生挤压进而导致隐裂的问题。并且,设置叠焊区域的中心与胶膜中压痕区域的中心重合,即叠焊中心两侧的压痕区域为对称结构,进而使得在实际层压时,使得叠焊中心两侧的叠焊区域的电池片受到的作用力保持平衡,进一步防止电池片隐裂问题的发生。
附图说明
20.一个或多个实施例通过与之对应的附图中的图片进行示例性说明,这些示例性说明并不构成对实施例的限定,除非有特别申明,附图中的图不构成比例限制。
21.图1为本技术一实施例提供的一种光伏组件的剖面结构示意图;
22.图2为本技术一实施例提供的一种光伏组件的俯视结构示意图;
23.图3为本技术一实施例提供的另一种光伏组件的剖面结构示意图。
具体实施方式
24.由背景技术可知,目前存在光伏组件的性能不佳的问题。
25.分析发现,导致光伏组件的性能不佳的原因之一在于,目前叠焊设计的电池片中,相邻的两个电池片的端部层叠放置,以形成叠焊区域。由于叠焊区域的电池片为层叠放置,使得叠焊区域的厚度较大,而非叠焊区域的电池片的厚度较小,这使得叠焊区域与非叠焊区域的电池片不是水平放置。如此,当对电池片进行层压时,叠焊区域的电池片由于厚度较大而受到较大的层压应力,由于力会沿电池片的表面传递至与叠焊区域邻接的非叠焊区域的电池片表面,并对非叠焊区域的电池片表面产生一个向下的拉力,使得被向下拉的这一部分很可能在拉力的作用下产生弯矩,进而发生弯曲,甚至隐裂。叠焊区域的弯矩与叠焊区域的宽度以及所受到的拉力相关,当叠焊区域的宽度与非叠焊区域的宽度不匹配时,容易造成非叠焊区域的电池片所产生的弯矩过大而导致电池片发生弯曲以及隐裂的问题。
26.本技术实施例提供一种光伏组件,对叠焊中心在电池片中沿第一方向上的位置进行了限定,通过合理设置叠焊中心到电池片远离叠焊区域的侧边之间的距离,进而调整叠焊区域与非叠焊区域在电池片中所占的宽度比例,使得在对光伏组件进行层压时,该叠焊中心所在的叠焊区域的电池片所受到的层压应力传递至与叠焊区域相邻的非叠焊区域的电池片上时,对非叠焊区域的电池片产生的弯矩不会过大,进而可以改善非叠焊区域的电池片表面在受到过大的弯矩的作用下发生弯曲甚至隐裂的问题。此外,还设置胶膜,压痕区域的厚度较薄,可以防止发生由于层压时叠焊区域的胶膜厚度过大而对叠焊区域的电池片产生挤压进而导致隐裂的问题。并且,设置叠焊区域的中心与胶膜中压痕区域的中心重合,即叠焊中心两侧的压痕区域为对称结构,进而使得在实际层压时,使得叠焊中心两侧的叠焊区域的电池片受到的作用力保持平衡,进一步防止电池片隐裂问题的发生。
27.下面将结合附图对本技术的各实施例进行详细的阐述。然而,本领域的普通技术人员可以理解,在本技术各实施例中,为了使读者更好地理解本技术而提出了许多技术细节。但是,即使没有这些技术细节和基于以下各实施例的种种变化和修改,也可以实现本技术所要求保护的技术方案。
28.图1为本技术一实施例提供的一种光伏组件的剖面结构示意图,图2为本技术一实施例提供的一种光伏组件的俯视结构示意图,图3为本技术一实施例提供的另一种光伏组件的剖面结构示意图。
29.参考图1以及图2,光伏组件包括:多个电池片101,多个电池片101沿第一方向x排布,且一电池片101的一个端部与相邻的电池片101的一个端部层叠放置,其中,两个电池片101层叠的区域形成叠焊区域10,叠焊区域10具有叠焊中心11,其中,一电池片101对应的叠焊中心11到该电池片101远离叠焊中心11的侧边之间的距离为第一距离d1,第一距离d1与电池片101沿第一方向x的宽度d2之比为99.693%~99.783%;胶膜102,胶膜102覆盖多个电池片101表面,胶膜102包括压痕区域20和与压痕区域20相接的非压痕区域21,至少部分压痕区域20与叠焊区域10重叠,压痕区域20的胶膜102厚度小于非压痕区域21的胶膜102厚度,且压痕区域20的中心与叠焊中心11重合。叠焊中心11指的是,沿第一方向x上,到叠焊区域两侧的距离相等的点。
30.电池片101用于吸收入射光线中的光子,并产生电子空穴对,电子空穴对被电池片101中的内建电场分离,在pn结两端产生电势,从而将光能转换为电能。在一些实施例中,电
池片101的一个表面作为受光面,用于吸收入射光线。在另一些实施例中,电池片101的两个表面均作为受光面,用于吸收入射光线。在一些实施例中,电池片101可以是晶体硅太阳能电池,例如可以是单晶硅太阳能电池或者多晶硅太阳能电池。可以理解的是,在一些实施例中,电池片101可以以多分片(例如,1/2等分片、1/3等分片、1/4等分片等多分片)的形式电连接形成多个电池串,多个电池串以串联和/或并联的方式进行电连接。在一个具体的例子中,电池片101以1/2等分片的形式,即半片的形式电连接,半片电池片通过将一个电池片101切割成两半之后得到。
31.设置相邻的两个电池片101的端部层叠放置,相较于相邻的两个电池片101间隔排布而言,可以增加单位面积内光伏组件中电池片101的数量,进而可以增加光伏组件的组装密度,有利于提高组件功率。
32.设置第一距离d1与电池片101沿第一方向x的宽度之比为99.693%~99.783%。可以理解的是,在这个范围内,当比值越小时,意味着第一距离d1越小,即,叠焊中心11越靠近电池片101的中心设置,使得叠焊区域10在第一方向x上的宽度占整个电池片101在第一方向x上的宽度的比例越大。即,通过调节第一距离d1与电池片101沿第一方向x上的宽度之比,对叠焊中心11在电池片101中的位置进行调节,进而对叠焊区域10的宽度与非叠焊区域10的宽度之比进行调控。可以理解的是,第一距离d1指的是在沿第一方向x上,一电池片101对应的叠焊中心11到该电池片101远离叠焊中心11的侧边之间的距离。
33.在一些实施例中,一电池片101中与其中一叠焊中心11相对的侧边可以为非切割边,即可以具有倒角。在一些实施例中,一电池片101中于其中一叠焊中心11相对的侧边也可以为切割边,即没有倒角。
34.在上述范围内,一方面使得叠焊区域10在第一方向x上的宽度不至于过大,防止发生由于电池片101的重叠区域过大而对电池片101造成过多遮挡,使得电池片101对入射光线的吸收减弱的问题,进而可以实现在提高光伏组件中电池片101封装密度的同时,保证光伏组件对入射光线较高的吸收利用率,提高光伏组件的组件功率。
35.另一方面,在这个范围内,叠焊中心11到电池片101远离叠焊区域10的侧边之间的距离不至于过小,进而使得叠焊区域10的电池片101的宽度较大,即相邻的两个电池片101层叠的面积较大,如此,在对光伏组件进行层压的过程中,使得叠焊区域10的电池片101所产生的层压压强不至于过大,防止叠焊区域10的电池片101由于受到过大的压强而发生隐裂的问题。
36.另外,由于在对光伏组件进行层压的过程中,叠焊区域10首先受到层压作用,且叠焊区域10的电池片101所受到的层压应力较大,该层压应力会传递至非叠焊区域的电池片101,对非叠焊区域的电池片101表面产生一个沿层压应力作用方向的拉力,电池片101在该拉力的作用下产生弯矩。
37.为了防止过大的弯矩导致非叠焊区域的电池片101发生弯曲进而发生隐裂的问题,设置第一距离d1与电池片101沿第一方向x的宽度d2之比在99.693%~99.783%。在这个范围内,对非叠焊区域的电池片101在第一方向x上的宽度与叠焊区域10的电池片101在第一方向x上的宽度之比进行了合理的设计,使得非叠焊区域的电池片101在第一方向x上的宽度与非叠焊区域的电池片101表面受到的向下的拉力相匹配,进而使得非叠焊区域的电池片101所产生的弯矩较小,防止非叠焊区域的电池片101在过大的弯矩的作用下发生弯
曲而进而产生隐裂的问题。在一些实施例中,第一距离d1与电池片101沿第一方向x的宽度之比可以为99.693%~99.7%、99.7%~99.725%、99.725%~99.728%、99.728%~99.73%、99.73%~99.733%、99.733%~99.735%、99.735%~99.737%、99.737%~99.746%、99.746%~99.755%、99.755%~99.768%、99.768%~99.776%、99.776%~99.78%或者99.78%~99.783%。在这些范围内,既可以保持光伏组件具有较高的组件功率,又可以有效防止隐裂的发生。
38.可以理解的是,对于不同规格的电池片101而言,发生弯曲所需要的弯矩是不同的,为了进一步减小非叠焊区域的电池片101发生隐裂的风险,需要对非叠焊区域的电池片101在第一方向x上的宽度与叠焊区域10的电池片101在第一方向x上的宽度之比和电池片101在第一方向x上的宽度进行匹配性的设计。基于此,在一些实施例中,若电池片沿第一方向x的宽度d2为182mm~193mm,则设置第一距离d1与电池片101沿第一方向x的宽度之比为99.725%~99.741%。在这个范围内,当作用于叠焊区域10的电池片101上的层压应力传递至非叠焊区域的电池片101表面时,基于非叠焊区域表面所受到的拉力与非叠焊区域的电池片101的实际宽度所产生的弯矩并不足以使非叠焊区域的电池片101产生弯曲,进而进一步防止了非叠焊区域的电池片101由于弯曲而发生隐裂的风险。在一些实施例中,电池片101沿第一方向x的宽度为182mm~193mm时,例如,电池片101沿第一方向x的宽度为182mm~185mm、185mm~188mm、188mm~190mm、190mm~192mm或192mm~193mm时,第一距离d1与电池片101沿第一方向x的宽度之比可以为99.725%~99.728%、99.728%~99.73%、99.73%~99.733%、99.733%~99.735%、99.735%~99.737%、99.737%~99.739%或者99.739%~99.741%。
39.当电池片101沿第一方向x的宽度d2较大时,非叠焊区域的表面需要受到较大的拉力才能产生足够的弯矩以使电池片101弯曲。也就是说,在拉力不变的情况下,当电池片101沿第一方向x的宽度较大时,可以设置非叠焊区域沿第一方向x的宽度占电池片101沿第一方向x上的宽度的比例较小,进而可以扩大叠焊中心11在电池片101中的位置调节范围。
40.基于上述考虑,在一些实施例中,若电池片沿第一方向x的宽度d2为210~230mm,则第一距离d1与电池片101沿第一方向x的宽度之比为99.762%~99.783%。在这个范围内,可以较为灵活地调节叠焊中新在电池片101上的位置。并且,当作用于叠焊区域10的电池片101上的层压应力传递至非叠焊区域的电池片101表面时,基于非叠焊区域表面所受到的拉力与非叠焊区域的电池片101的实际宽度所产生的弯矩也不足以使非叠焊区域的电池片101产生弯曲,防止了非叠焊区域的电池片101由于弯曲而发生隐裂的风险。在一些实施例中,电池片101沿第一方向x的宽度可以为210mm~213mm、213mm~215mm、215mm~218mm、218mm~221mm、221mm~224mm、224mm~226mm、226mm~228mm或者228mm~230mm,第一距离d1与电池片101沿第一方向x的宽度之比可以为99.762%~99.764%、99.764%~99.766%、99.769%~99.771%、99.771%~99.773%、99.773%~99.775%、99.775%~99.777%、99.777%~99.779%、99.779%~99.781%或者99.781%~99.783%。
41.在一些实施例中,若电池片101沿第一方向x的宽度d2为163mm~165mm,则第一距离d1与电池片101沿第一方向x的宽度之比为99.693%~99.697%。在这个范围内,电池片沿第一方向x的宽度d2较小,且第一距离d1与电池片101沿第一方向x的宽度之比与电池片101沿第一方向x的宽度d2相匹配,可以降低非叠焊区域的电池片101由于弯曲而发生隐裂
的风险。在一些实施例中,电池片101沿第一方向x的宽度d2可以为163mm~163.5mm、163.5mm~164mm、164mm~164.5mm或者164.5mm~165mm,第一距离d1与电池片101沿第一方向x的宽度之比可以为99.693%~99.694%、99.694%~99.695%、99.695%~99.696%或者99.696%~99.697%。
42.对于不同规格的电池片101而言,发生弯曲所需要的拉力是不同的,例如,电池片101在沿第二方向y上的长度大小对于非叠焊区域的电池片101的弯曲能力也具有一定的影响。当电池片101在沿第二方向y上的长度越大时,非叠焊区域弯曲所需要受到的拉力越大,使得非叠焊区域的电池片101发生隐裂的风险越小。但是,考虑到光伏组件的整体面积不宜过大,又不能设置电池片101在第二方向y上的长度过大。基于此,在一些实施例中,电池片在第一方向x上的宽度与电池片101在第二方向y上的长度之比为0.3543~0.7055,例如可以为0.3543~0.37、0.37~0.41、0.41~0.44、0.44~0.49、0.49~0.55、0.55~0.58、0.58~0.63、0.63~0.66、0.66~0.68或者0.68~0.7055,第二方向y垂直于第一方向x。在这个范围内,电池片101在第二方向y上的长度相较于电池片101在沿第一方向x上的宽度而言不至于过小,进而使得非叠焊区域的电池片101需要在受到较大的拉力条件下才会弯曲,进一步减小非叠焊区域的电池片101产生隐裂的风险。
43.设置压痕区域20的胶膜102厚度相较于非压痕区域21的胶膜102厚度更薄,可以防止发生由于层压时叠焊区域10的胶膜102厚度过大而对叠焊区域10的电池片101产生挤压进而导致叠焊区域10的电池片101发生隐裂的问题。并且,设置叠焊区域10的中心与胶膜102中压痕区域20的中心重合,即叠焊中心11两侧的压痕区域20为对称结构,进而使得在实际层压时,叠焊中心11两侧的叠焊区域10的电池片101受到的作用力保持平衡,进一步防止电池片101隐裂问题的发生。其中,胶膜102厚度由较厚跳变为较薄处可定义为压痕区域20的边界。
44.参考图1,在一些实施例中,压痕区域20的胶膜102与叠焊区域10的电池片101重合。也就是说,叠焊区域10的电池片101正好位于压痕区域20的胶膜102内,使得在实际层压过程中,对胶膜102进行融化时,叠焊区域10的胶膜102量较少,防止发生由于过多胶膜102流入叠焊区域10的电池片101之间而造成对叠焊区域10的电池片101的挤压力增大的问题,避免叠焊区域10的电池片101发生隐裂。
45.在光伏组件的层压过程中,胶膜102会融化,由于胶膜102的流动性,使得电池片101与胶膜102之间会发生偏移。基于此,参考图3,在一些实施例中,设置叠焊区域在胶膜102上的正投影位于压痕区域20内,压痕区域20在第一方向x上的宽度d1与叠焊区域10在第一方向x上的宽度d2之比为1:40,例如可以为1:5、1:8、1:12、1:18、1:22、1:27、1:32、1:34、1:36或者1:40。也就是说,压痕区域20在第一方向x上的宽度d1大于叠焊区域10在第一方向x上的宽度d2,如此,可以为光伏组件在实际层压过程中产生的偏移提供较大的容差,使得光伏组件即使在实际层压中发生偏移,压痕区域20也能够覆盖叠焊区域10的电池片101,减小电池片101发生隐裂的风险。
46.在一些实施例中,叠焊区域10在沿第一方向x上的宽度d2为0.2mm~0.8mm,例如可以为0.2mm~0.3mm、0.3mm~0.4mm、0.4mm~0.5mm、0.5mm~0.6mm、0.6mm~0.7mm或者0.7mm~0.8mm。在这个范围内,使得叠焊区域10在第一方向x上的宽度不至于过小,使得叠焊区域10的电池片101的面积不至于过小,进而使得在实际层压过程中,在层压应力不变的情况
下,对叠焊区域10所产生的压强不至于过大,防止过大的压强使叠焊区域10的电池片101发生隐裂。另一方面,在这个范围内,使得叠焊区域10在第一方向x上的宽度也不至于过大,防止发生由于相邻的电池片101之间的层叠面积过大而对电池片101产生过多遮挡,使得电池片101对入射光线的利用率较低的问题。
47.在一些实施例中,压痕区域20的胶膜102厚度与非压痕区域21的胶膜102厚度之比不大于1,例如可以为0.2、0.3、0.5、0.65、0.7、0.8、0.85、0.91或者0.97。在这个范围内,可以实现压痕区域20的胶膜102在对叠焊区域10的电池片101起到较好的密封作用的同时,防止在实际层压过程中,对叠焊区域10的电池片101产生过大的挤压力,进而改善叠焊区域10的电池片101发生隐裂的问题。此外,在这个范围内,压痕区域20的胶膜102厚度与非压痕区域21的胶膜102厚度相匹配,使得胶膜102覆盖于电池片101表面后,位于非叠焊区域的胶膜102以及电池片101的整体厚度与位于叠焊区域10的胶膜102以及电池片101的整体厚度相同或者接近于相同,使得层压过程中,压痕区域20的电池片101与非压痕区域21的电池片101受力接近,进一步防止隐裂问题的发生。
48.在一些实施例中,压痕区域20的胶膜102厚度不大于0.8mm,例如可以为0.05mm~0.1mm、0.1mm~0.2mm、0.2mm~0.3mm、0.3mm~0.45mm、0.45mm~0.55mm、0.55mm~0.6mm、0.6mm~0.7mm或者0.7mm~0.79mm,非压痕区域21的胶膜102厚度为0.2mm~0.8mm,例如可以为0.2mm~0.3mm、0.3mm~0.4mm、0.4mm~0.5mm、0.5mm~0.6mm、0.6mm~0.7mm或者0.7mm~0.8mm。在这个范围内,可以较好地防止叠焊区域10的电池片101发生隐裂的问题,同时可以保持胶膜102较好的密封效果。
49.在一些实施例中,胶膜102可以包括:第一胶膜1与第二胶膜2,第一胶膜1与第二胶膜2均具有压痕区域20以及非压痕区域21。其中,第一胶膜1可以与位于电池片101的上表面,第二胶膜2可以位于电池片101的下表面,以对电池片101的两个表面均起到密封以及保护作用。
50.在一些实施例中,还包括:第一盖板103以及第二盖板104,第一盖板103位于第一胶膜1远离电池片101的一侧,用于对电池片101的上表面起到保护作用,第二盖板104位于第二胶膜2远离电池片101的一侧,用于对电池片101的下表面起到保护作用。在一些实施例中,第一盖板103的材料可以为玻璃或者背板中的任一者;第二盖板104的材料可以为玻璃或者背板中的任一者。
51.在一些实施例中,还包括:焊带,焊带用于串联相邻的两个电池片101,焊带可以位于电池片101的表面,用于电连接相邻的两个电池片101。
52.上述实施例提供的光伏组件中,对叠焊中心11在电池片101中沿第一方向x上的位置进行了限定,通过合理设置叠焊中心11到电池片101远离叠焊区域10的侧边之间的距离,进而调整叠焊区域10与非叠焊区域在电池片101中所占的宽度比例,使得在对光伏组件进行层压时,该叠焊中心11所在的叠焊区域10的电池片101所受到的层压应力传递至与叠焊区域10相邻的非叠焊区域的电池片101上时,对非叠焊区域的电池片101产生的弯矩不会过大,进而可以改善非叠焊区域的电池片101表面在受到过大的弯矩的作用下发生弯曲甚至隐裂的问题。此外,还设置胶膜102,压痕区域20的厚度较薄,可以防止发生由于层压时叠焊区域10的胶膜102厚度过大而对叠焊区域10的电池片101产生挤压进而导致隐裂的问题。并且,设置叠焊区域10的中心与胶膜102中压痕区域20的中心重合,即叠焊中心11两侧的压痕
区域20为对称结构,进而使得在实际层压时,使得叠焊中心11两侧的叠焊区域10的电池片101受到的作用力保持平衡,进一步防止电池片101隐裂问题的发生。
53.相应地,本技术实施例还提供一种光伏组件的制备方法,应用于上述任一项的光伏组件,包括:提供多个电池片101(参考图1),多个电池片101沿第一方向x排布,且一电池片101的一个端部与相邻的电池片101的一个端部层叠放置,其中,两个电池片101层叠的区域形成叠焊区域10(参考图1),叠焊区域10具有叠焊中心11,其中,一电池片101对应的叠焊中心11到该电池片101远离叠焊中心11的侧边之间的距离为第一距离d1(参考图2),第一距离d1与电池片101沿第一方向x的宽度之比为99.693%~99.783%;在多个电池片101表面铺设胶膜102(参考图1),胶膜102包括压痕区域20(参考图2)和与压痕区域20相接的非压痕区域21(参考图2),至少部分压痕区域20与叠焊区域10重叠,压痕区域20的胶膜102厚度小于非压痕区域21的胶膜102厚度,且压痕区域20的中心与叠焊中心11重合。
54.在一些实施例中,基于第一距离d1(参考图2)与电池片101沿第一方向x的宽度d2(参考图2)之比和电池片101沿第一方向x上的宽度d2制备胶膜102(参考图1)。由于压痕区域20(参考图1)的中心与叠焊中心11(参考图2)重合,因此,胶膜102中压痕区域20(参考图1)的位置与电池片101(参考图2)的尺寸以及叠焊中心11(参考图2)在电池片101上的位置相关。也就是说,只要确定了叠焊中心11在电池片101上的位置以及电池片101的尺寸即可以确定叠焊中心11在胶膜102中的位置,并基于此在胶膜102上制备压痕区域20。如此,对应于不同尺寸的电池片101,只需确定第一距离d1与电池片101沿第一方向x的宽度之比以及电池片101沿第一方向x上的宽度尺寸即可快速获取压痕区域20在胶膜102中的位置,有利于快速制备胶膜102。
55.在一些实施例中,制备胶膜102的方法包括:
56.制备初始胶膜,初始胶膜的表面为平整表面。即初始胶膜为平整胶膜,在一些实施例中,初始胶膜可以通过热压工艺获取,例如可以通过胶膜挤出成型工艺制备初始胶膜。在一些实施例中,初始胶膜的材料可以包括eva胶膜或者poe胶膜。在一些实施例中,初始胶膜可以为单层胶膜或者复合胶膜。
57.采用多个间隔排布的压辊对初始胶膜进行热压,以在初始胶膜表面形成多个间隔排布的压痕区域,具体包括:基于第一距离d1(参考图2)与电池片101沿第一方向x的宽度d2(参考图2)之比和电池片101(参考图2)沿第一方向x上的宽度,调整压辊间距,以在初始胶膜表面形成多个压痕区域,得到胶膜。间隔排布的压辊中,每一压辊与一压痕区域20(参考图1)对应,压辊对初始胶膜进行热压后在初始胶膜的平整表面形成压痕区域20,以使压痕区域20的胶膜102(参考图1)厚度小于非压痕区域21(参考图1)的胶膜102厚度。
58.由于压痕区域20的中心可以基于第一距离d1与电池片101沿第一方向x上的宽度之比以及电池片101沿第一方向x上的宽度确定,而每一压痕区域20与一压辊对应,因此,也可以基于第一距离d1与电池片101沿第一方向x上的宽度之比和电池片101沿第一方向x上的宽度来确定相邻的压辊之间的间距。确定电池片101沿第一方向x上的宽度之后,可以确定与一电池片101对应的初始胶膜的宽度,确定第一距离d1与电池片101沿第一方向x上的宽度之比后,可以确定压痕区域20的中心在与一电池片101对应的初始胶膜中的具体位置,进而可以确定压痕区域20的位置。
59.在一些实施例中,当压辊位于压辊机上时,可以通过调整压辊机的参数来自动调
节压辊之间的间距。可以在压辊机中输入第一距离d1与电池片101沿第一方向x上的宽度之比以及电池片101沿第一方向x上的宽度,即可以自动调整压辊之间的间距,接着对初始胶膜进行热压后获得胶膜102。如此,对应不同尺寸的电池片101而言,若需要制备不同的胶膜102,仅需在压辊机中输入第一距离d1与电池片101沿第一方向x上的宽度之比以及电池片101沿第一方向x上的宽度,即可以快速在初始胶膜的平整表面制备压痕区域20以获取胶膜102。
60.在获取胶膜102之后,将胶膜102平铺至电池片101表面,并将胶膜102的压痕区域20的中心与叠焊中心11对准,以对光伏组件进行层压,使得压痕区域20的胶膜102与叠焊区域10的电池片101正对,由于压痕区域20的胶膜102厚度较小,可以防止叠焊区域10由于高度过高而受到过大的挤压力,造成叠焊区域10的电池片101隐裂的问题,并且,由于叠焊区域10的中心与胶膜102中压痕区域20的中心重合,即叠焊中心11两侧的压痕区域20为对称结构,进而使得在实际层压时,使得叠焊中心11两侧的叠焊区域10的电池片101受到的作用力保持平衡,进一步防止电池片101隐裂问题的发生。
61.本技术虽然以较佳实施例公开如上,但并不是用来限定权利要求,任何本领域技术人员在不脱离本技术构思的前提下,都可以做出若干可能的变动和修改,因此本技术的保护范围应当以本技术权利要求所界定的范围为准。
62.本领域的普通技术人员可以理解,上述各实施方式是实现本技术的具体实施例,而在实际应用中,可以在形式上和细节上对其作各种改变,而不偏离本技术的精神和范围。任何本领域技术人员,在不脱离本技术的精神和范围内,均可作各种改动与修改,因此本技术的保护范围应当以权利要求限定的范围为准。