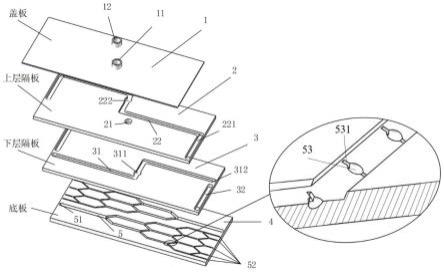
1.本发明涉及电子芯片冷却技术领域,具体地说,涉及一种通道壁面对流换热系数可调节的散热装置。
背景技术:2.随着微电子技术的高速发展,电子芯片朝着微型化、大功率、高集成度的方向飞速发展,其发热量日益提高。“热致失效”已经成为微电子设备最主要的失效形式之一。目前电子芯片热负荷水平的升高主要源自三个方面:(1)微电子器件的高度封装集成,使得芯片级的热流密度可达到60~1100w/cm2;(2)芯片内部功率分布不均匀导致内部热点频发,从而引起局部温度过高,影响使用寿命;(3)微电子设备使用范围日益广泛,所处环境温度高,温差大,而过大的热应力使得芯片结构变形致使其工作性能和稳定性大为降低。将高热流密度电子芯片上集聚的热量进行有效疏导以维持其处于正常的工作温度和较低的热应力水平(温度梯度),避免电子元器件发生热致失效,是芯片散热装置结构设计的关键目标。
3.微通道液冷散热技术是目前最常用的高热流密度芯片冷却方式之一。然而传统的直微通道主要通过增加换热面积来提高换热量,其对单位面积上的换热系数提升有限,又会因导流水管过于细小导致需要较大的驱动泵功。此外,微通道结构相对固定导致其当地换热系数无法及时响应芯片局部热点处热流密度和温度的变化,整体温度场的分布均匀性较差,因此只能牺牲芯片热点处的高功率来保证整体芯片的正常工作。
技术实现要素:4.本发明所要解决的技术问题是针对现有技术不足,提供一种可以根据芯片工况自适应调节通道表面当地换热系数的微通道液冷散热装置,该散热装置包括带凹坑绕流元件的类蜂窝状微通道冷却结构,具有低流动阻力、高换热效率和良好的温度分布均匀性,能够对高热流密度芯片进行有效冷却。
5.为了解决上述技术问题,本发明采用了如下技术方案:
6.一种具有低流动阻力、高换热效率和良好的温度分布均匀性,并且可以根据芯片工况自适应调节通道表面当地换热系数的微通道液冷散热装置,包括依次密封配合的散热器盖板,上层隔板,下层隔板和底板;所述散热器盖板上设置有进液口和出液口;所述上层隔板上设有进液口导流孔和出液口过渡流道;所述下层隔板上设有进液口过渡流道和出液口导流槽;所述底板上加工有由若干组多边形分叉回路构成的类蜂窝状微通道,每组类蜂窝状微通道包括一个通道进口和多个通道出口;该结构借鉴自然界的蜂窝结构,分叉3~5次,经历第一次分叉后的次级通道,不断再次分叉并与同级通道不断合并、分离,形成类蜂窝状的多边形回路;
7.所述底板上的通道进口依次与下层隔板上的进液口过渡流道、上层隔板上的进液口导流孔和盖板上的进液口连通,形成冷却液的进液通路;所述底板上的通道出口依次与下层隔板上的出液口导流槽、上层隔板上的出液口过渡流道和盖板上的出液口连通,形成
冷却液的出液通路。
8.优选方案为,所述微通道底部加工出排列有序的凹坑阵列,每个凹坑中填充有热缩型温敏高分子材料。
9.优选方案为,所述通道底部的凹坑按一定规律布置,即沿流向布置为单列或多列凹坑。
10.优选方案为,凹坑间距与其投影直径之比为2~5。
11.优选方案为,所述凹坑的投影直径大于凹坑内填充的热缩型温敏高分子材料的投影直径,而且沿着所述凹坑投影直径并垂直于流动方向加工有一字型定位槽道,使填充材料能在凹坑中得到可靠固定。
12.优选方案为,所述凹坑的投影面均为圆形、椭圆形、水滴形、三角形、菱形、梯形或矩形。
13.优选方案为,填充的热缩型温敏高分子材料的体积与凹坑体积之比为3/5~2/3。
14.优选方案为,所述底板一侧表面与所需冷却的热源紧密接触,中间可填充高导热材料,所述底板上的通道进口与下层隔板上的进液口过渡流道的出口相连通;
15.优选方案为,所述底板上的相邻类蜂窝状微通道呈反向对称布置。
16.本发明的有益效果:
17.1.本技术提供的适用于高热流密度芯片的微通道散热装置,采用带凹坑绕流元件的类蜂窝状微通道冷却结构,并在凹坑中填充有热缩型温敏高分子材料。借鉴生物系统特有的高效质能输运特性设计的类蜂窝状微通道在减小通道压降,优化流动的同时,提高了底板的冷却均匀性。微通道底部的凹坑能够在通道中产生强烈有序的涡旋,会在近壁面区域引起气流的分离和重附着,一方面能够更加快速的从热源面带走热量,另一方面能够加强近壁面流体和主流中心区域流体的混合,从而有效的强化传热;
18.2.本技术提供的带凹坑绕流元件的类蜂窝状微通道冷却结构,通道壁面的当地换热系数与凹坑的深度有关。凹坑深度大的换热增幅大,凹坑深度小的换热增幅小。在凹坑中填充的热缩型温敏高分子材料,其具有随温度变化而发生溶胀-收缩的非连续性体积变化的特性。当感应到热源温度的变化,一旦该材料温度超过自身的最低临界转变温度,其体积将快速收缩,使得凹坑的深度变大,从而使得凹坑处对应的通道表面当地换热系数增加,进而提高了整个散热器的换热性能。
附图说明
19.图1为本发明组装置的爆炸图;
20.图2为本发明的类蜂窝状微通道冷却结构局部放大示意图
21.图3为本发明的盖板结构示意图;
22.图4为本发明的上层隔板结构示意图;
23.图5为本发明的下层隔板结构示意图;
24.图6为本发明的底板结构示意图;
25.图7为感受到热源温度变化后凹坑通道内热缩型温敏高分子材料发生体积收缩行为以及通道内涡旋尺度变化示意图
26.图8为换热仿真结果。
具体实施方式
27.应该指出,以下详细说明都是例示性的,旨在对本技术提供进一步的说明。除非另有指明,本文使用的所有技术和科学术语具有与本技术所属技术领域的普通技术人员通常理解的相同含义。
28.实施例1:如图1-图6所示,一种具有低流动阻力、高换热效率和良好的温度分布均匀性,并且可以根据芯片工况自适应调节通道表面换热系数的微通道液冷散热装置,包括由上而下依次密封配合的散热盖板1,上层隔板2,下层隔板3和底板4,所述散热盖板上设置有进液口11和出液口12;所述上层隔板上设有进液口导流孔21和出液口过渡流道22;所述下层隔板3上设有进液口过渡流道31和出液口导流槽32;所述底板4上加工有由若干组多边形分叉回路构成的类蜂窝状微通道5,每组类蜂窝状微通道5包括一个通道进口51和多个通道出口52;
29.所述底板上的通道进口51依次与下层隔板上的进液口过渡流道31、上层隔板上的进液口导流孔21和盖板上的进液口连通11,形成冷却液的进液通路;所述底板上的通道出口52依次与下层隔板上的出液口导流槽32、上层隔板上的出液口过渡流道22和盖板上的出液口12连通,形成冷却液的出液通路;散热盖板1、上层隔板2和下层隔板3以及底板4采用的材料相同,均为铜或铝等高导热金属,并使用高分子扩散焊的方式将各层板无缝焊接起来,或使用金属3d打印工艺制造,以保证良好的密封性能。
30.所述类蜂窝状微通道5的底部加工出排列有序的凹坑53,凹坑的投影面为圆形,每个凹坑中填充有热缩型温敏高分子材料6。所述凹坑的投影直径大于凹坑内填充的热缩型温敏高分子材料6的投影直径,而且沿着所述凹坑投影直径并垂直于流动方向加工有一字型定位槽道531,使填充材料6能在凹坑中得到可靠固定。
31.工作过程:所述底板4的一个表面与所需冷却的热源紧密接触,中间可填充高导热材料,以减小接触热阻的影响;所述底板4的另一个表面则与下层隔板3连接并可靠密封。所述底板4上的通道进口51与下层隔板上的进液口过渡流道的出口312相连通;所述底板上的通道出口52与所述下层隔板上的出液口导流槽32相连通。
32.所述上层隔板上2的一个表面与下层隔板3连接并可靠密封,另一个表面则与散热器盖板1连接并可靠密封。所述上层隔板2上的进液口导流孔21分别与所述下层隔板3上的进液口过渡流道的入口311和散热器盖板1上的进液口11相连通。所述上层隔板2上的出液口过渡流道的入口222与散热器盖板上的出液口12相连通;所述上层隔板2上的出液口过渡流道的出口221与下层隔板3上的出液口导流槽32相连通。
33.在其他实施例中,所述凹坑的投影面还可以为椭圆形、水滴形、三角形、菱形、梯形或矩形。
34.为了进一步提高冷却的效果,微通道进口51当量直径不大于3mm,微通道出口52当量直径不小于0.3mm;所述底板上的相邻结构的类蜂窝状微通道5呈反向对称布置。
35.如图7所示,展示了冷却工质在通道近壁面区域的流场结构随凹坑尺度的变化示意图,可知当热源温度较低时,凹坑中的热缩型温敏高分子材料6的体积不会发生明显变化。因此凹坑深度较浅,从而诱发的流体涡旋尺度和强度都较小,使得该区域处的壁面对流换热系数相对较低。一旦热源的热量积聚使得热缩型温敏材料的温度超过自身的最低临界温度后,该材料的体积将会急剧收缩,使得凹坑空间扩大,从而诱发更大更强的流体涡旋,
使得该区域处的壁面对流换热系数得到明显提升。
36.图8显示了冷却工质进口流速为1m/s,热流密度为100kw/m2时,三种通道热沉加热面的温度云图和通道表面换热系数云图分布。表1给出了相同热流边界和进口速度条件下,单个光滑壁面分叉微通道和带凹坑分叉微通道的散热结果。可以看出,凹坑中填充热缩型温敏高分子材料的分叉微通道在强化传热方面的优势。
37.表1芯片散热结果
[0038][0039][0040]
对于本领域技术人员而言,显然本发明不限于上述示范性实施例的细节,而且在不背离本发明的精神或基本特征的情况下,能够以其他的具体形式实现本发明。因此,无论从哪一点来看,均应将实施例看作是示范性的,而且是非限制性的,本发明的范围由所附权利要求而不是上述说明限定,因此旨在将落在权利要求的等同要件的含义和范围内的所有变化囊括在本发明内。不应将权利要求中的任何附图标记视为限制所涉及的权利要求。