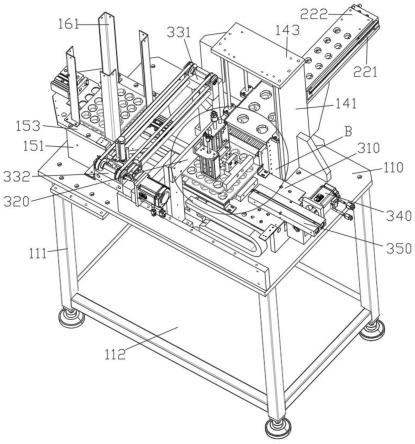
1.本发明涉及换向器加工技术领域,具体地说,涉及一种换向器加工生产装置。
背景技术:2.换向器,亦称整流子,其通常为直流电机和交流换向器电动机电枢上的重要部件之一。换向器在加工时通常有着向铜片内压制电木粉以用于制作换向器毛坯、换向器外观检测、换向器包装等加工工序,由于目前在电木粉压制、外观检测、包装等工序中通常出现全部步骤或部分步骤由人工操作的现象,故而使得换向器的质量稳定性、加工效率依然受人工影响。
技术实现要素:3.针对现有技术中存在的电木粉压制、外观检测、包装等工序中由人工操作的缺陷,本发明提供了一种换向器加工生产装置。其能够较佳地实现电木粉压制、外观检测、包装等工序的全自动化运行。
4.为了解决上述技术问题,本发明通过下述技术方案得以解决:
5.一种换向器加工生产装置,其包括用于制造换向器的换向器制造设备、用于对制造完成后的换向器进行检测的换向器监测设备、以及用于对检测合格后的换向器进行包装的换向器全自动包装机构;换向器制造设备包括用于将电木粉压入铜片处的换向器电木粉全自动压制机构,换向器监测设备包括用于检测换向器外观的换向器铜片在线视觉监测机构。
6.通过上述,能够较佳地实现对电木粉的全自动化压制、对换向器外观的全自动化监测、对检测合格后换向器的全自动化包装。从而较佳地在压制电木粉时降低了工人的危险性、在检测换向器外观时降低了由人工带来的检测结果不稳定性,同时还较佳地提升了电木粉压制、外观检测、包装等工序的工作效率,进而较佳地提高了换向器的加工效率与加工质量。
7.作为优选,换向器全自动包装机构包括机台a,机台a沿其宽度方向从左至右依次设有上料区域a、包装区域与码垛区域;机台a上端处设有转运台a与第一转运机构a,第一转运机构a用于驱使转运台a沿直线方向依次移动至上料区域a、包装区域与码垛区域;机台a上端处的前端与后端分别设有吸塑盒存储台与换向器存储区域,机台a上端处还设有第三转运机构a与第四转运机构a;第三转运机构a用于将吸塑盒从吸塑盒存储台处移动至位于上料区域a的转运台a处,第四转运机构a用于将换向器从换向器存储区域移动至位于包装区域的吸塑盒处;码垛区域设有码垛机构a,码垛机构a用于堆叠包装有换向器的吸塑盒;转运台a上端面处设有用于将包装有换向器的吸塑盒从转运台a处转运至码垛机构a处的第二转运机构a。能够较佳地实现对换向器的全自动化包装,相较于包装换向器时全流程或部分流程使用人工操作的包装方式,该换向器全自动包装机构较佳地提升了包装换向器的效率,同时降低了人工成本。
8.作为优选,吸塑盒存储台包括依次构成长方形框体的上框板a、第一框板a、下框板a与第二框板a,第一框板a与第二框板a内端板面处均对应设有多个第一放置槽a,所述多个第一放置槽a沿高度方向间隔设置,吸塑盒两端部分别伸入对应第一放置槽a内;上料区域a上方设有第一中转区域a,第三转运机构a包括抬升单元a、第一动力单元a、第二动力单元a;抬升单元a用于驱使吸塑盒存储台沿竖直方向移动,吸塑盒存储台内吸塑盒在抬升单元a作用下自上而下依次移动至第一动力单元a处,第一动力单元a用于驱使吸塑盒从吸塑盒存储台处水平移动至第一中转区域a处、第二动力单元a用于驱使吸塑盒从第一中转区域a处竖直移动至转运台a处;机台a上端面处设有第一安装架a,第二动力单元a包括设于第一安装架a处的第一气缸a、以及设于第一气缸a输出端处用于夹持吸塑盒的第一手指气缸a;第一手指气缸a的两夹持端均设有夹板a,两夹板a的内端板面处设有平行第一放置槽a设置的第二放置槽a;机台a处设有第二安装架a,第二安装架a设于吸塑盒存储台的前侧,第一动力单元a包括设于第二安装架a上端处的直线电机a、以及设于直线电机a滑台处的推板a;吸塑盒存储台与手指气缸a之间设有两支撑板a,两支撑板a分别与两夹板a对应设置,两支撑板a的内端均设有支撑滑板a;推板a在直线电机a作用下推动吸塑盒使其两端部从第一放置槽a内途径支撑滑板a处移动至第二放置槽a内;第一手指气缸a在第一气缸a作用下带动吸塑盒从第一中转区域a处向下移动至转运台a处;第一安装架a处还设有第七气缸a,第七气缸a的输出端用于驱使吸塑盒处包装槽下侧壁抵靠在转运台a上端面处。
9.通过第三转运机构a的设置,较佳地实现了将吸塑盒从吸塑盒存储台处转运至上料区域a的转运台a处,从而较佳地实现了吸塑盒的连续转运,进而提升了该换向器全自动包装的工作效率。
10.作为优选,夹板a包括呈左右设置的第一子夹板a与第二子夹板a,第二子夹板a处设有对吸塑盒进行定位的限位单元a;限位单元a包括分别设于第二放置槽a前端处与后端处用于与吸塑盒前侧壁与后侧壁配合的滑动块a与封堵块a;第二放置槽a上端面处设有竖直设置的滑动槽a,滑动槽a上端壁设有竖直设置的滑动柱a,滑动块a处设有用于与滑动柱a滑动配合的滑动孔a,滑动槽a上端壁与滑动块a上端面之间的滑动柱a处套设有用于驱使滑动块a下移的第一弹簧a,滑动块a前端面处设有第三导向斜面a,吸塑盒在推板a推动下挤压第三导向斜面a以实现滑动块a的上移;封堵块a前侧壁为呈左右设置的斜侧壁a与垂直侧壁a,垂直侧壁a用于对吸塑盒进行定位;第二放置槽a右侧壁处设有弹出单元a,弹出单元a用于在第一子夹板a与第二子夹板a背向移动时驱动吸塑盒从垂直侧壁a处移动至斜侧壁a处;弹出单元a包括间隔设于第二放置槽a右侧壁处的多个圆形槽a,圆形槽a内设有半球形件a,圆形槽a开口处向内扩张形成限制半球形件a脱离圆形槽a的限位部,半球形件a朝向圆形槽a槽底的平面处设有导向槽a,圆形槽a槽底与导向槽a槽底之间设有用于驱使半球形件a的半球形面弹出圆形槽a的第二弹簧a,吸塑盒在推板a推动下挤压半球形件a的半球形面以实现半球形件a缩回圆形槽a内。通过限位单元a的设置,较佳地限制了位于吸塑盒随第一手指气缸a下移时与夹板a之间的相对移动;通过弹出单元a的设置,较佳地实现了吸塑盒与第一子夹板a之间的脱离。
11.作为优选,机台a上方处设有第一安装座a与第二安装座a,第一安装座a与第二安装座a之间设有第二导向柱a、以及用于与第二导向柱a滑动配合的第一移动座a;第四转运机构a包括用于夹持转向器的第二手指气缸a、以及用于驱使第二手指气缸a沿竖直方向移
动的第二气缸a,第二手指气缸a设于第二气缸a输出端,第二气缸a设于第一移动座a处;
12.第四转运机构a还包括设于第一安装座a与第二安装座a处的第一同步轮a、设于对应两第一同步轮a之间的第一同步带a、以及用于通过驱动第一同步轮a转动以带动第一移动座a移动的第一电机a;机台a上端面处设有第三安装座a与第四安装座a,第三安装座a设于上料区域a左端,第四安装座a设于码垛机构a左端,第三安装座a与第四安装座a之间设有位于转运台a下端处的第三导向柱a,转运台a下端面处设有用于与第三导向柱a滑动配合的第二导向座a;
13.第一转运机构a包括设于第三安装座a与第四安装座a处的第二同步轮a、设于对应两第二同步轮a之间的第二同步带a、以及用于通过驱动第二同步轮a转动以带动转运台a移动的第二电机a。通过第四转运机构a的设置,较佳地实现了将换向器从换向器存储区域处转运至吸塑盒处包装槽内,从而较佳地方便了换向器的包装。其中,第二气缸a的设置,较佳地适应了转运台a上端处吸塑盒与换向器存储区域之间的高度差,进而较佳地提升了该换向器全自动包装机构的适用性。第一转运机构a的设置,实现了转运台a的移动,从而较佳地整合了吸塑盒的上料、换向器的包装、以及包装有转向器的吸塑盒的码垛等工序,进而较佳地实现了对换向器的全自动包装,故而提升了包装换向器的效率。
14.作为优选,换向器电木粉全自动压制机构包括具有上料机构的第一机台c、具有加热机构c的第二机台c、具有中转区域c与压制区域c的第三机台c、以及转运机构c;压制区域c处设有压制机构,中转区域c处设有第一中模;转运机构c包括第一转运机构c、第二转运机构c与第三转运机构c;
15.第一转运机构c用于将上料机构c处铁木粉饼块转运至加热机构c处进行加热,第二转运机构c用于将加热后的铁木粉饼块从加热机构c处转运至中转区域c处的第一中模内,第三转运机构c用于将携带铁木粉饼块的第一中模从中转区域c处转运至压制机构处进行压制、以及用于将携带铁木粉废料的第一中模从压制机构处转运至中转区域c处;中转区域c处还设有用于将第一中模内的铁木粉废料移出第一中模的转移机构c。能够较佳地实现对电木粉的全自动化上料,从而较佳地实现了对电木粉饼块的全自动化压制;进而较佳地降低了因人工上料带来的例如危险性高、工作效率低等缺陷,故而提升了电木粉压制效率。
16.作为优选,第一机台c上端处设有转盘c与第一驱动件c,转盘c上端面处沿其圆周间隔设有多个存储单元c;转盘c上方设有上料区域c,第一驱动件c用于通过驱动转盘c转动以带动所述多个存储单元c依次转动至上料区域c处;
17.存储单元c包括竖直设置的存储件c,存储件c处沿竖直方向贯穿设有用于存储铁木粉饼块的存储腔c;第一机台c处设有用于将位于上料区域c的存储腔内铁木粉饼块推出存储腔上端部开口处的抬升单元,第一机台c上端处设有用于监测位于上料区域c的存储腔c内铁木粉饼块的探头c;转盘c处设有多个连通对应存储腔c的通孔c,通孔c与存储件c依次对应设置,通孔c截面积小于存储腔c截面积;抬升单元包括设于第一机台c处的丝杆步进电机c,丝杆步进电机c的输出端从通孔c处伸入存储腔c内。通过上述,较佳地实现了电木粉饼块的存储与后续自动化转运。
18.作为优选,加热机构c包括设于第二机台c处用于加热电木粉饼块的加热板c,以及设于加热板c上端处的加热台c,加热台c包括两平行设置且上端处用于放置铁木粉饼块的转动棍c;中转区域c处设有第四安装架c,第四安装架c包括呈上下设置的第一安装条c与第
一安装板c,第一安装条c设有两个且两第一安装条c平行设置,第四安装架c还包括设于第一安装板c与两第一安装条c之间的多个第一安装柱c,第一中模设于两第一安装条c之间;压制机构包括设于第三机台c处的载台c,第三转运机构c包括设于第三机台c上端处的第三驱动件c,第三驱动件c用于驱使第一中模从两第一安装条c之间移动至载台c处;
19.第一转运机构c包括第一机械手、以及用于驱动第一机械手直线移动的第一直线电机c,第一机械手与第一直线电机c相互配合用于将铁木粉饼块从存储腔c上端部开口处转运至转动棍c上端处;第二转运机构c包括第二机械手、以及用于驱动第二机械手直线移动的第二直线电机c,第二机械手与第二直线电机c相互配合用于将铁木粉饼块从转动棍c上端处转运至位于两第一安装条c之间的第一中模内;转移机构c包括设于第一安装板c与第一安装条c之间的顶升件c,顶升件c上端处设有多个顶针c,顶针c用于顶出第一中模内铁木粉废料;转移机构c还包括用于吸取被顶出铁木粉废料的吸盘、用于驱使吸盘竖直移动的第五气缸c、以及用于驱使第五气缸c与吸盘同步移出放置槽c上方处的第三直线电机c,第一安装条c上端处设有用于安装第三直线电机c的第七安装架c。通过上述,能够较佳地实现对电木粉饼块的加热、转运、压制与废料清理。
20.作为优选,换向器铜片在线视觉监测机构包括机台b,机台b处沿其长度方向从后至前依次设有上料区域b、监测区域以及换向器存储区域;监测区域从后至前依次设有分别用于监测换向器侧面、云母、底面、顶面与内孔的第一监测单元、第二监测单元、第三监测单元、第四监测单元与第五监测单元;第一监测单元、第二监测单元、第三监测单元、第四监测单元与第五监测单元右侧处均设有废品出料口;
21.机台b处设有用于沿机台b长度方向做往复运动的转运机构b;转运机构b通过往复运动以实现将上料区域b、第一监测单元、第二监测单元、第三监测单元、第四监测单元与第五监测单元处换向器转运至第一监测单元、第二监测单元、第三监测单元、第四监测单元、第五监测单元与换向器存储区域处、以及将监测不合格的换向器转运至对应的废品出料口处。较佳地实现了换向器的自动化上下料、换向器外观的连续性自动监测与换向器的分类,进而提升了换向器的监测效率,且提升了换向器监测结果的稳定性,故而提高了分级精度和生产率,同时方便了后续对换向器加工数据的统计与分析。
22.作为优选,机台b上端面处设有第一导轨b,转运机构b包括用于与第一导轨b滑动配合的转运板b、以及用于夹取换向器的机械手b,机械手b设有6个且6个机械手b间隔设于转运板b上端面处,转运板b与监测区域呈左右设置;转运机构b还包括设于机台b上端面处用于驱动转运板b往复移动的多个第一气缸b。故而较佳地实现了转运板b的往复运动。
附图说明
23.图1为具体实施方式中吸塑盒的结构示意图。
24.图2为具体实施方式中换向器的结构示意图。
25.图3为具体实施方式中一种换向器全自动包装机构的结构示意图。
26.图4为图1中a结构的放大示意图。
27.图5为具体实施方式中一种换向器全自动包装机构的结构示意图。
28.图6为图3中b结构的放大示意图。
29.图7为具体实施方式中机台a、转运台a、第一转运机构a、第二转运机构a与第三转
运的结构示意图。
30.图8为图5中c结构的放大示意图。
31.图9为具体实施方式中机台a、转运台a、第一转运机构a、第二转运机构a与第三转运机构a的结构示意图。
32.图10为图7中d结构的放大示意图。
33.图11为具体实施方式中机台a、转运台a、第一转运机构a、第二转运机构a与第三转运机构a的结构示意图。
34.图12为具体实施方式中机台a、转运台a、码垛机构a、第一转运机构a与第二转运机构a的结构示意图。
35.图13为图10中e结构的放大示意图。
36.图14为具体实施方式中机台a、转运台a、码垛机构a、第一转运机构a与第二转运机构a的结构示意图。
37.图15为图12中f结构的放大示意图。
38.图16为具体实施方式中第一手指气缸a的结构示意图。
39.图17为具体实施方式中第二子夹板a的爆炸示意图。
40.图18为图17中g结构的放大示意图。
41.图19为图17中h结构的放大示意图。
42.图20为具体实施方式中安装台a的爆炸示意图
43.图21为实施例1中一种换向器铜片在线视觉监测机构的结构示意图。
44.图22为实施例1中一种换向器铜片在线视觉监测机构的结构示意图。
45.图23为图22中i结构的放大示意图。
46.图24为图23中j结构的放大示意图。
47.图25为实施例1中一种换向器铜片在线视觉监测机构的结构示意图。
48.图26为图25中k结构的放大示意图。
49.图27为实施例1中一种换向器电木粉全自动压制机构的结构示意图。
50.图28为图27中m结构的放大示意图。
51.图29为实施例1中一种换向器电木粉全自动压制机构的结构示意图。
52.图30为实施例1中第一机台c处结构的结构示意图。
53.图31为实施例1中转盘c、第一驱动件c与存储单元c的结构示意图。
具体实施方式
54.实施例1
55.本实施例中提供了一种换向器加工生产装置,包括一种换向器全自动包装机构、一种换向器铜片在线视觉监测机构以及一种换向器电木粉全自动压制机构。
56.其中整个加工生产装置具有如下加工工序:生产产品毛坯
→
送料
→
车外圆
→
铣槽
→
抛光
→
通电检测
→
内孔检测
→
外观检测
→
包装;目前工厂在生产换向器时,通常由振动盘送料、由外圆机车外圆、由铣槽机在换向器毛坯上铣接铣槽铣下刻槽、由四工位抛光机对换向器毛坯进行砂光抛面、由耐压测试机对换向器片间片轴进行(耐压检测)、由内孔检测机对换向器内孔进行检测。
57.其中,在生产换向器毛坯时,需要先通过预压设备将铜片压制成型,再向压制成型的铜片内压制电木粉。目前用于压制电木粉的模具通常设有上压模、第一中模、第二中模与下压模,第一中模用于放置电木粉饼块,第二中模用于放置铜片;在压制电木粉时,装有铜片的第一中模与装有电木粉饼块的第二中模上下重叠设于上压模与下压模之间,并通过上压模将第一中模内的电木粉压入第二中模内预压后的铜片内,再将压制后残留在第一中模内的电木粉废料移出第一中模;目前在压制电木粉时通常由人工上料,也即由人工将电木粉饼块放入第一中模内。
58.其中,通常由人工对换向器外观进行检测,换向器包装工序通常包括吸塑盒上料、将换向器转移至吸塑盒内、堆叠包装有换向器的吸塑盒等流程;目前工厂在包装换向器时通常其全部流程或部分流程由人工操作;如图1-2所示,目前用于包装换向器的吸塑盒通常为长方形,该吸塑盒沿其宽度方向间隔设有多行包装槽,每行包装槽均包括间隔设置的多个包装槽,包装槽由该吸塑盒的一端面向下凹陷形成,该包装槽为用于与换向器相互配合的圆柱形。
59.如图3-31所示,本实施例提供了一种换向器加工生产装置,其包括用于制造换向器的换向器制造设备、用于对制造完成后的换向器进行检测的换向器监测设备、以及用于对检测合格后的换向器进行包装的换向器全自动包装机构;换向器制造设备包括用于将电木粉压入铜片处的换向器电木粉全自动压制机构,换向器监测设备包括用于检测换向器外观的换向器铜片在线视觉监测机构。
60.通过上述,能够较佳地实现对电木粉的全自动化压制、对换向器外观的全自动化监测、对检测合格后换向器的全自动化包装。从而较佳地在压制电木粉时降低了工人的危险性、在检测换向器外观时降低了由人工带来的检测结果不稳定性,同时还较佳地提升了电木粉压制、外观检测、包装等工序的工作效率,进而较佳地提高了换向器的加工效率与加工质量。
61.如图3-6所示,本实施例提供了一种换向器加工生产装置,其包括一种换向器全自动包装机构,换向器全自动包装机构包括机台a 110,机台a 110沿其宽度方向从左至右依次设有上料区域a、包装区域与码垛区域;机台a 110上端处设有转运台a 310与第一转运机构a第一转运机构a第一转运机构a,第一转运机构a用于驱使转运台a 310沿直线方向依次移动至上料区域a、包装区域与码垛区域;机台a 110上端处的前端与后端分别设有吸塑盒存储台120与换向器存储区域,机台a 110上端处还设有第三转运机构a与第四转运机构a;第三转运机构a用于将吸塑盒从吸塑盒存储台120处移动至位于上料区域a的转运台a 310处,第四转运机构a用于将换向器从换向器存储区域移动至位于包装区域的吸塑盒处;码垛区域设有码垛机构a,码垛机构a用于堆叠包装有换向器的吸塑盒;转运台a 310上端面处设有用于将包装有换向器的吸塑盒从转运台a310处转运至码垛机构a处的第二转运机构a;机台a 110下端面设有用于支撑机台a 110的支腿a 111,两相邻支腿a 111之间设有围板a 112。
62.通过上述,能够较佳地实现对换向器的全自动化包装,且较佳地提升了该换向器全自动化包装的效率。具体地,第三转运机构a将吸塑盒存储台120处吸塑盒移动至位于上料区域a的转运台a 310处,第一转运机构a第一转运机构a驱动携带吸塑盒的转运台a 310移动至包装区域,第四转运机构a将换向器存储区域处的换向器依次移动至吸塑盒处包装
槽内,待吸塑盒处包装槽内均装有换向器后,第一转运机构a第一转运机构a驱动吸塑盒移动,使得包装有换向器的转运台a 310移动至码垛区域,当第二转运机构a将包装有换向器的吸塑盒从转运台a 310处转移至码垛机构a处后,码垛机构a将包装有换向器的吸塑盒堆叠整齐。从而较佳地实现了换向器包装工序的全自动化设置,相较于包装换向器时全流程或部分流程使用人工操作的包装方式,该换向器全自动包装机构较佳地提升了包装换向器的效率,同时降低了人工成本。
63.其中,吸塑盒存储台120与换向器存储区域分别设于机台a 110的前端与后端,也即,上料区域a、包装区域与码垛区域均位于吸塑盒存储台120与换向器存储区域之间;通过该位置设置,使得吸塑盒与换向器分别从转运台a 310两侧处转运至转运台a 310处,从而较佳地缩短了上料区域a、包装区域与码垛区域之间的距离,进而缩短了转运台a 310在上料区域a、包装区域与码垛区域之间转运吸塑盒的时间,故而提升了该换向器全自动包装的工作效率;与此同时,还较佳地提升了机台a 110处的空间利用率。
64.其中,换向器存储区域单独位于机台a 110后端处,该位置设置较佳地增大了换向器存储区域的空间,从而较佳地方便了该换向器全自动包装机构与换向器生产机构出料端或换向器检测机构出料端的直接对接,进而进一步提升了换向器生产、检测与包装整体流程的工作效率。
65.结合图3-6所示,本实施例中,吸塑盒存储台120包括依次构成长方形框体的上框板a 121、第一框板a 122、下框板a 123与第二框板a 124,第一框板a122与第二框板a 124内端板面处均对应设有多个第一放置槽a 210,所述多个第一放置槽a 210沿高度方向间隔设置,吸塑盒两端部分别伸入对应第一放置槽a 210内;上料区域a上方设有第一中转区域a,第三转运机构a包括抬升单元a、第一动力单元a、第二动力单元a;抬升单元a用于驱使吸塑盒存储台120沿竖直方向移动,吸塑盒存储台120内吸塑盒在抬升单元a作用下自上而下依次移动至第一动力单元a处,第一动力单元a用于驱使吸塑盒从吸塑盒存储台120处水平移动至第一中转区域a处、第二动力单元a用于驱使吸塑盒从第一中转区域a处竖直移动至转运台a 310处。
66.通过第三转运机构a的设置,较佳地实现了将吸塑盒从吸塑盒存储台120处转运至上料区域a的转运台a310处。具体地,通过第一动力单元a将吸塑盒从吸塑盒存储台120处水平移动至第一中转区域a处,再通过第二动力单元a将吸塑盒从第一中转区域a处竖直移动至上料区域a的转运台a 310处;此时抬升单元a驱使吸塑盒存储台120上移,使得位于下一层的吸塑盒上移至与第一动力单元a位于同一水平处;从而较佳地实现了吸塑盒的连续转运,进而提升了该换向器全自动包装的工作效率。
67.其中,吸塑盒存储台120处的吸塑盒采取自上而下依次转运的转运方式,使得吸塑盒存储台120内需要补充吸塑盒的区域位于第一动力单元a上方处,从而较佳地增大了向吸塑盒存储台120内填补吸塑盒的操作空间,进而较佳地方便了吸塑盒存储台120内吸塑盒的上料。其中,第一放置槽a 210较佳地方便了吸塑盒的放置与转运。其中,设于不同水平面与不同竖直面的吸塑盒存储台120与上料区域a,较佳地提升了该换向器全自动包装机构的空间利用率,故而提升了该换向器全自动包装的工作效率。
68.结合图3-8所示,本实施例中,机台a 110上端面处设有第一安装架a310,第二动力单元a包括设于第一安装架a 310处的第一气缸a 420、以及设于第一气缸a 420输出端处用
于夹持吸塑盒的第一手指气缸a 410;第一手指气缸a 410的两夹持端均设有夹板a 411,两夹板a 411的内端板面处设有平行第一放置槽a 210设置的第二放置槽a 610;机台a110处设有第二安装架a 130,第二安装架a 130设于吸塑盒存储台120的前侧,第一动力单元a包括设于第二安装架a 130上端处的直线电机a 221、以及设于直线电机a 221滑台处的推板a 222;吸塑盒存储台120与手指气缸a 410之间设有两支撑板a 440,两支撑板a 440分别与两夹板a 411对应设置,两支撑板a 440的内端均设有支撑滑板a 441,位于第一中转区域a的夹板a 411处的第一放置槽a 210下端面、位于推板a 222处的第二放置槽a 610下端面、支撑滑板a 441上端面位于同一高度;推板a 222在直线电机a 221作用下推动吸塑盒使其两端部从第一放置槽a 210内途径支撑滑板a 441处移动至第二放置槽a 610内;第一手指气缸a 410在第一气缸a 420作用下带动吸塑盒从第一中转区域a处向下移动至转运台a 310处。
69.第一手指气缸a 410与第一气缸a 420的设置,实现了将吸塑盒从第一中转区域a处转运至上料区域a的转运台a 310处,故而较佳地提升了该换向器全自动包装机构的适用性。通过第一气缸a 420与线性电机a 221的设置,较佳地适应了吸塑盒在位于不同水平面与不同竖直面的吸塑盒存储台120与上料区域a之间的转运,故而较佳地提升了该换向器全自动包装机构的适用性。
70.其中,第二放置槽a 610的设置,较佳地方便了吸塑盒的转运;其中,支撑滑板a 441的设置,较佳地避免了吸塑盒端部脱离第一放置槽a 210较多时出现吸塑盒倾斜而导致的吸塑盒端部无法插入第二放置槽a 610内的概率,故而较佳地提升了吸塑盒转运的平稳性。
71.结合图3-4所示,本实施例中,机台a 110前端处设有安装槽a 160,第二安装架a 130下端部固定设于安装槽a 160底壁处;
72.机台a 110上端面处设有第三安装架a 140,第三安装架a 140包括两竖直设置的第一安装板a 141与第二安装板a 142、以及用于连接第一安装板a 141与第二安装板a 142上端部的上安装板a 143,吸塑盒存储台120设于第一安装板a 141与第二安装板a 142之间,吸塑盒存储台120设于安装槽a 160处;
73.安装槽a 160底壁与上安装板a 143之间设有多个第一导向柱a 144,吸塑盒存储台120处设有多个用于与对应第一导向柱a 144滑动配合的第一导向座a 230;抬升单元a包括设于安装槽a 160下端处且用于驱使吸塑盒存储台120沿竖直方向移动的丝杆步进电机a 510。
74.通过抬升单元a的设置,较佳地实现了吸塑盒存储台120沿竖直方向的移动。其中,当吸塑盒存储台120下端部位于安装槽a 160槽底时,吸塑盒存储台120最上层第一放置槽a 210位置与位于第一中转区域a的第二放置槽a 610位置齐平;也即,通过安装槽a 160的设置,较佳地降低了第一中转区域a与机台a 110上端面之间的竖直距离,从而较佳地缩短了第一气缸a 420的最大行程,进而较佳地在增加吸塑盒存储台120内吸塑盒存储数量的同时节省了成本;且吸塑盒存储台120较佳地利用了机台a 110下端处的空间,从而较佳地提升了空间利用率。
75.结合图3-6、图11所示,本实施例中,机台a 110上方处设有第一安装座a 331与第二安装座a 332,第一安装座a 331设于第二安装板a 142处,第二安装座a 332设于第一安
151与第五安装板a 152上端面处的安装台a 153;安装台a 153上端面处设有竖直设置且截面呈l型的定位条a 161,定位条a 161设有四个,四个定位条a 161合围区域形成截面呈长方形的堆叠区域a;
82.第四安装板a 151与第五安装板a 152之间设有转运板a 1310,第二转运机构a包括第三气缸a 350,第三气缸a 350设于转运台a 310左侧,第三气缸a 350输出端设有与吸塑盒侧壁配合的l型推板a 450,l型推板a 450在第三气缸a 350作用下用于将包装有转向器的吸塑盒从转运台a 310处推动至转运板a 1310处;安装台a 153处设有通孔a 1320,机台a 110下端处设有第四气缸a 1010,第四气缸a 1010用于驱使转运台a 310上移以使得包装有转向器的吸塑盒穿出通孔a 1320移动至堆叠区域a;
83.安装台a 153上端处设有两第五气缸a 1020,堆叠区域a位于两第五气缸a 1020之间,第五气缸a 1020输出端设有夹持片a 1020,夹持片a 1020朝向堆叠区域a的端部设有用于与吸塑盒处包装槽侧壁相配合的弧形槽a 1121,两第五气缸a 1020用于驱使两夹持片a 1120相向移动至夹紧堆叠区域a最下层包装有转向器的吸塑盒;通过码垛机构a的设置,随转运台a 310移动至码垛区域的包装有转向器的吸塑盒,先通过第四气缸a 1010转运至转运板a 1310处,再通过第三气缸a 350转运至堆叠区域a;从而较佳地实现了对包装有转向器的吸塑盒的堆叠,进而较佳地增加了换向器包装过程中的整齐度,且较佳地方便了后期转运包装有转向器的吸塑盒。
84.通过夹持片a 1020的设置,当第四气缸a 1010驱动转运台a 310上移时两夹持片a 1120背向移动,使得转运台a 310处包装有转向器的吸塑盒挤压堆叠区域a包装有转向器的吸塑盒使其整体上移;当转运台a 310处包装有转向器的吸塑盒移动至堆叠区域a后两夹持片a 1120相向移动至夹紧该包装有转向器的吸塑盒,使得转运台a 310下移后堆叠区域a包装有转向器的吸塑盒保持在原位;故而较佳地实现了对包装有转向器的吸塑盒的定位与堆叠。
85.其中,当第一手指气缸a 410夹取吸塑盒时,位于收缩状态下的第三气缸a350处的l型推板a 450位于夹板a 411正下方。进而较佳地缩短了第三气缸a350的最大行程,故而较佳地节省了成本,同时增加了空间利用率。其中,码垛机构a采用从下至上堆叠包装有转向器的吸塑盒的码垛方式,较佳地使得吸塑盒处包装槽的开口侧一直朝上设置,故而较佳地避免了在堆叠包装有转向器的吸塑盒时吸塑盒内换向器脱离吸塑盒的概率,故而较佳地实现了包装有转向器的吸塑盒的包装。其中,通过l型推板a 450的设置,当第四气缸a 1010推动包装有转向器的吸塑盒时,吸塑盒侧壁、吸塑盒处包装槽侧壁均与l型推板a 450内侧壁相互抵靠,从而较佳地提升了包装有转向器的吸塑盒移动时的稳定性。其中,通过截面呈l型的定位条a 161的设置,包装有转向器的吸塑盒侧壁与定位条a 161内侧壁相互配合,较佳地方便了对包装有转向器的吸塑盒的堆叠与整理,同时较佳地方便了堆叠区域a内包装有转向器的吸塑盒的后续转移。
86.结合图7-11所示,本实施例中,转运台a 310处设有用于固定安装盒第一的定位单元;第一定位单元a包括两固定设于转运台a 310上端面处且用于与吸塑盒左侧壁配合的定位片a 621,第三气缸a 350输出端位于两定位片a 621之间;定位单元包括两固定设于转运台a 310下端面处的第六气缸a 811,第六气缸a811输出端形成定位凸起a 622,定位凸起a 622在第六气缸a 811的作用下上移至穿出转运台a 310对吸塑盒右侧壁进行定位;第一定
153下侧壁处设有用于与装有换向器的吸塑盒上侧壁配合以限制其上移的限位板a 1810,限位板a 1810设于通孔a 1320左侧,限位板a 1810右侧设有用于引导装有换向器的吸塑盒移动至限位板a 1810与转运板a 1310之间的第四导向斜面a 1811。
92.通过上述设置,当装有换向器的吸塑盒在l型推板a 450的推动下从转运台a移动至转运板a 1310的过程中,限位板a 1810下侧壁较佳地对装有换向器的吸塑盒上侧壁形成限位,从而较佳地避免了装有换向器的吸塑盒右端部或整体上移的概率,进而较佳地提升了装有换向器的吸塑盒移动过程中的稳定性。
93.本实施例中,第一手指气缸a 410与第二手指气缸a 920均采用现有技术中常见的手指气缸a即可;第一气缸a 420、第二气缸a 921、第一电机a 914、第二电机a 340、第三气缸a 350、第四气缸a 1010、第五气缸a 1020与第六气缸a 811均采用现有技术中常见的气缸即可;丝杆步进电机a 510采用现有技术中常见的丝杆步进电机a即可。
94.本实施例中的一种换向器全自动包装机构在使用时,其具有如下步骤:
95.步骤一、位于上料区域a上方的第三转运机构a将吸塑盒转运至位于上料区域a的转运台a 310上端面处;步骤二、第一转运机构a驱动携带吸塑盒的转运台a 310移动至包装区域,第四转运机构a依次将换向器从换向器存储区域转运至吸塑盒处的包装槽内;与此同时,第三转运机构a将吸塑盒从吸塑盒存储台120处转运至上料区域a上方;步骤三、吸塑盒处的包装槽内装满换向器后,第一转运机构a驱动携带包装有换向器的吸塑盒的转运台a 310移动至码垛区域;步骤四、第二转运机构a将包装有换向器的吸塑盒从转运台a 310处转运至码垛机构a处;步骤五、第一转运机构a驱动转运台a 310移动至上料区域a;与此同时,码垛机构a将包装有换向器的吸塑盒堆叠整齐。
96.如图16-19所示,本实施例中夹板a 411包括左右设置的第一子夹板a 1411与第二子夹板a 1412,第二子夹板a 1412处设有对吸塑盒进行定位的限位单元a;限位单元a包括分别设于第二放置槽a 610前端处与后端处用于与吸塑盒侧壁配合的滑动块a 1611与封堵块a 1510;第二放置槽a 610上端面处设有竖直设置的滑动槽a 1610,滑动槽a 1610上端壁设有竖直设置的滑动柱a 1612,滑动块a 1611处设有用于与滑动柱a 1612滑动配合的滑动孔a 1614,滑动槽a 1610上端壁与滑动块a 1611上端面之间的滑动柱a 1612处套设有用于驱使滑动块a 1611下移的第一弹簧a 1613,滑动块a 1611前端面处设有第三导向斜面a 1615,吸塑盒在推板a 222推动下挤压第三导向斜面a 1615以实现滑动块a 1611的上移;
97.封堵块a 1510前侧壁为呈左右设置斜侧壁a 1711与垂直侧壁a 1712,斜侧壁a 1711从垂直侧壁a 1712处至远离垂直侧壁a 1712端背向滑动块a 1611倾斜,垂直侧壁a 1712用于对吸塑盒进行定位;
98.第二放置槽a 610右侧壁处设有弹出单元a,弹出单元a用于在第一子夹板a 1411与第二子夹板a 1412背向移动时驱动吸塑盒从垂直侧壁a1712处移动至斜侧壁a 1711处;弹出单元a包括间隔设于第二放置槽a 610右侧壁处的多个圆形槽a 1620,圆形槽a 1620内设有半球形件a 1621,圆形槽a 1620开口处向内扩张形成限制半球形件a 1621脱离圆形槽a 1620的限位部a 1622,半球形件a 1621朝向圆形槽a 1620槽底的平面处设有导向槽a 1721,圆形槽a 1620槽底与导向槽a 1721槽底之间设有用于驱使半球形件a 1621的半球形面弹出圆形槽a 1620的第二弹簧a 1722,吸塑盒在推板a 222推动下挤压半球形件a1621的半球形面以实现半球形件a1621缩回圆形槽a 1620内。
99.通过限位单元a的设置,限制了位于吸塑盒随第一手指气缸a 410下移时与夹板a 411之间的相对移动,故而较佳地使得吸塑盒处的包装槽移动至第一定位槽a 624内;通过弹出单元a的设置,较佳地避免了吸塑盒因其前侧壁与后侧壁被封堵块a 1510与滑动块a 1611抵紧导致较难脱离第二放置槽a 610的概率,从而较佳地实现了吸塑盒与第一子夹板a 1411之间的脱离。其中,限位单元a设置于第二子夹板a 1412处,较佳地给定位片a 621提供了避让空间;其中,通过斜侧壁a 1711与垂直侧壁a 1712的设置,较佳地缩短了半球形件a1621的移动行程,较佳地方便了吸塑盒右侧壁移动至第二放置槽a 610内。
100.具体地,第二子夹板a 1412随第一手指气缸a 410移动至第一中转区域a后,在推板a 222的推动下,吸塑盒后端部挤压第三导向斜面a1615驱使滑动块a 1611挤压第一弹簧a 1613并上移至滑动槽a 1610内,吸塑盒后端侧挤压滑动块a 161挤压半球形件a 1621的半球形面驱使半球形件a 1621缩回圆形槽a 1620内;当吸塑盒移动至其后端部抵紧在垂直侧壁a 1712处后,滑动块a1611在第一弹簧a 1613作用下下移至其后侧壁抵靠在吸塑盒前端部处,半球形件a 1621的半球形面抵紧在吸塑盒右侧壁处;当夹板a 411随第一手指气缸a 410移动至接近l型推板a 450后,第一子夹板a 1411与第二子夹板a 1412逐渐背向移动,半球形件a 1621在第二弹簧a 1722作用下弹出圆形槽a 1620,驱使吸塑盒后侧壁从垂直侧壁a 1712处移动至斜侧壁a 1711处,此时吸塑盒前侧壁与后侧壁不再被垂直侧壁a 1712与滑动块a 1611抵紧,吸塑盒后端部脱离第二放置槽a 610。
101.如图27-31所示,本实施例中一种换向器电木粉全自动压制机构包括具有上料机构的第一机台c 3110、具有加热机构c的第二机台c 3120、具有中转区域c与压制区域c的第三机台c 3130、以及转运机构c;压制区域c处设有压制机构,中转区域c处设有第一中模3240;转运机构c包括第一转运机构c、第二转运机构c与第三转运机构c;第一转运机构c用于将上料机构c处铁木粉饼块转运至加热机构c处进行加热,第二转运机构c用于将加热后的铁木粉饼块从加热机构c处转运至中转区域c处的第一中模3240内,第三转运机构c用于将携带铁木粉饼块的第一中模3240从中转区域c处转运至压制机构处进行压制、以及用于将携带铁木粉废料的第一中模3240从压制机构处转运至中转区域c处,中转区域c处还设有用于将第一中模3240内的铁木粉废料移出第一中模3240的转移机构c。
102.通过上述,能够较佳地实现对电木粉的全自动化上料,从而较佳地实现了对电木粉饼块的全自动化压制;进而较佳地降低了因人工上料带来的例如危险性高、工作效率低等缺陷,故而提升了电木粉压制效率。具体地,电木粉饼块存储在上料机构c处,第一转运机构c将上料机构c处的电木粉饼块转运至加热机构c处进行加热,加热后的铁木粉饼块通过第二转运机构c转运至中转区域c处的第一中模3240内,再通过第三转运机构c将携带电木粉饼块的第一中模3240转运至压制机构处,经压制机构压制后,残留在第一中模3240内的电木粉废料随第一中模3240被第三转运机构c转运至中转区域c处,再由转移机构c将电木粉废料转移出第一中模3240。进而较佳地实现了对电木粉饼块的全自动化连续压制。
103.本实施例中,第一机台c 3110上端处设有转盘c 3121与第一驱动件c,转盘c 3121上端面处沿其圆周间隔设有多个存储单元c;转盘c 3121上方设有上料区域c,第一驱动件c用于通过驱动转盘c 3121转动以带动所述多个存储单元c依次转动至上料区域c处,第一驱动件c为第一电机c 3124;存储单元c包括竖直设置的存储件c 3122,存储件c 3122处沿竖直方向贯穿设有用于存储铁木粉饼块的存储腔c 3123;第一机台c 3110处设有用于将位于
上料区域c的存储腔c 3123内铁木粉饼块推出存储腔c 3123上端部开口处的抬升单元,第一机台c 3110上端处设有用于监测位于上料区域c的存储腔c 3123内铁木粉饼块的探头c 3124。较佳地实现了电木粉饼块的存储与后续自动化转运。具体地,抬升单元逐渐将位于上料区域c处存储件c 3122内的电木粉饼块推出存储腔c 3123上端开口处,探头c 3124用于监测该处存储腔c 3123内电木粉的剩余数量,当存储腔c 3123内电木粉饼块全部推动至存储腔c 3123上端开口处并由第一转运机构c转移至加热机构c后,第一驱动件c带动转盘c 3121转动,使得相邻的存储件c 3122转移至上料区域c。
104.本实施例中,转盘c 3121处设有多个连通对应存储腔c 3123的通孔c 3511,通孔c 3511与存储件c 3122依次对应设置,通孔c 3511截面积小于存储腔c 3123截面积;抬升单元包括设于第一机台c 3110处的丝杆步进电机c 3231,丝杆步进电机c 3231的输出端从通孔c 3511处伸入存储腔c 3123内。丝杆步进电机c 3231的输出端伸入位于上料区域c处存储件c 3122的存储腔c 3123内,并逐渐驱使存储腔c 3123内整体电木粉饼块上移,进而能够较佳地将存储腔c 3123内电木粉饼块顶出存储腔c 3123开口处,进而较佳地方便了后续对电木粉饼块的转运;当存储腔c 3123电木粉饼块全部转移后,丝杆步进电机c 3231的输出端下移并退出存储腔c 3123,故而方便了转盘c 3121的转动。
105.本实施例中,加热机构c包括设于第二机台c 3120处用于加热电木粉饼块的加热板c 3131,以及设于加热板c 3131上端处的加热台c,加热机构c还包括倾斜设于加热板c 3131上端处的加热罩c 3132;加热台c包括两平行设置且上端处用于放置铁木粉饼块的转动棍c 3221、以及用于通过驱动两转动棍c 3221转动以带动铁木粉饼块转动的驱动单元c;加热板c 3131上端处设有用于安装两转动棍c 3221的多个第一安装架c 3222;驱动单元c包括设于转动棍c 3221一端处的第一蜗轮c 3223、以及用于与两第一蜗轮c 3223配合的蜗杆c 3224,加热台c处设有用于安装蜗杆c 3224的多个第二安装架c 3225、以及用于驱动蜗杆c 3224转动的第二驱动件c,第二驱动件c为第二电机c。
106.通过上述,能够较佳地实现对电木粉饼块的加热,由于电木粉饼块在常温状态时质地坚硬,在加热后会软化,故而方便了后续对电木粉饼块的压制。其中,驱动单元c较佳地驱动了位于转动棍c 3221上端处电木粉饼块的转动,进而较佳地提升了电木粉饼块的受热均匀性。
107.本实施例中,中转区域c处设有第四安装架c,第四安装架c包括呈上下设置的第一安装条c 3211与第一安装板c 3212,第一安装条c 3211设有两个且两第一安装条c 3211平行设置,第四安装架c还包括设于第一安装板c 3212与两第一安装条c 3211之间的多个第一安装柱c 3213;第一中模3240设于两第一安装条c 3211之间,两第一安装条c 3211内端均沿水平方向设有第一滑轨c 3214,第一中模3240处设有用于与对应第一滑轨c 3214滑动配合的第一滑条3241;压制机构包括设于第三机台c 3130处的载台c 3231,载台c 3231两相向侧壁处均设有平行第一滑轨c 3214设置的第二滑轨c 3232;第三转运机构c包括设于第三机台c 3130上端处的第三驱动件c,第三驱动件c用于驱使第一中模3240移动至其第一滑条3241从第一滑轨c 3214内转移至第二滑轨c3232内;能够较佳地将携带电木粉饼块的第一中模3240转运至压制机构处进行压制、以及将携带压制后电木粉废料的第一中模3240转运至中转区域c处,从而较佳地方便了电木粉饼块的后续压制以及压制后电木粉饼废料的转移。
108.本实施例中,第三驱动件c为设有磁性开关的第一气缸,压制机构设于第一气缸与中转区域c之间;由于第一气缸设有磁性开关,故而使得第一气缸活塞杆在伸长状态时其推出端能够吸紧第一中模3240,且当其将第一中模3240转移至压制机构处后,由于其活塞杆处于收缩状态故而其推出端能够与第一中模3240相互脱离。
109.本实施例中,第一转运机构c包括第一机械手3141、以及用于驱动第一机械手3141直线移动的第一直线电机c 3142,第一机械手3141与第一直线电机c 3142相互配合用于将铁木粉饼块从存储腔c 3123上端部开口处转运至转动棍c 3221上端处,第一机台c 3110上端处设有用于安装第一直线电机c 3142的第三安装架c 3143。故而较佳地实现了将电木粉饼块从存储腔c 3123上端处转移至转动棍c 3221上端处处,从而方便了后续对电木粉饼块的加热。
110.本实施例中,第二转运机构c包括第二机械手3151、以及用于驱动第二机械手3151直线移动的第二直线电机c 3152,第二机械手3151与第二直线电机c 3152相互配合用于将铁木粉饼块从转动棍c 3221上端处转运至位于两第一安装条c 3211之间的第一中模3240内,第一机台c 3110上端处设有用于安装第二直线电机c 3152的第五安装架c 3153。故而较佳地实现了将加热后的电木粉饼块从转动棍c 3221上端处转移至第一中模3240内,从而方便了后续对电木粉饼块的压制。
111.本实施例中,第一中模3240包括设于其上端面处用于放置电木粉饼块的放置槽c 3242、以及设于其下端面处连通放置槽c 3242的多个压制孔c 3243;压制机构包括设于载台c 3231下端处的下压模3233、以及设于下压模3233与载台c 3231之间且用于放置铜片的第二中模,压制机构还包括用于驱使载台c3231下移以带动第一中模3240移动至第二中模上端面处的第四驱动件c,第四驱动件c为第二气缸c,第三机台c 3130上端面处设有用于安装第二气缸c的第二安装板c 3234;载台c 3231上端处设有上压模3161、以及用于驱动上压模3161下端处伸入放置槽c 3242内的第三气缸c 3162,上压模3161用于将放置槽c 3242内的铁木粉饼块从压制孔c 3243处压入第二中模内,载台c 3231上端处设有用于安装第三气缸c 3162与上压模3161的第六安装架c 3163。
112.当第一中模3240通过第三驱动件c移动至载台c 3231后,第四驱动件c驱动载台c 3231下移,当第一中模3240移动至下端部接触第二中模上端部后,第三气缸c 3162驱动上压模3161下移至七下端部伸入放置槽c 3242内,上压模3161在下移过程种将放置槽c 3242内电木粉饼块从压制孔c 3243内挤压至第二中模内的铜片处,压制完成后,第三气缸c 3162驱动上压模3161上移,第四驱动件c驱动载台c 3231上移至第三驱动件c处,第三驱动件c驱动第一中模3240移动至中转区域c;此时,压制后残留在放置槽c 3242内的电木粉废料随第一中模3240移动至中转区域c。
113.本实施例中,转移机构c包括设于第一安装板c 3212与第一安装条c 3211之间的顶升件c 3251,顶升件c 3251上端处设有多个顶针c 3252,第一安装板c 3212处设有用于驱使顶升件c 3251带动所述多个顶针c 3252上移的第四气缸c 3253,顶针c 3252用于伸入对应压制孔c 3243内将铁木粉废料顶出压制孔c 3243;转移机构c还包括设于第一安装条c 3211上端处的第七安装架c3254,第七安装架c 3254处设有水平设置的第三直线电机c 3255,第三直线电机c 3255滑块处设有第五气缸c 3256,第五气缸c 3256输出端设有吸盘3257;第五气缸c 3256用于驱使吸盘3257沿竖直方向移动,吸盘3257用于吸取被顶出压制
孔c 3243的铁木粉废料,第三直线电机c 3255用于驱使第五气缸c 3256带动吸盘3257与铁木粉废料同步移出放置槽c 3242上方处;第三直线电机c3255一端位于两第一安装条c 3211之间,第三直线电机c 3255另一端下方设有电木粉废料收集盒c。能够较佳地将第一中模3240内铁木粉饼块压制后残留的铁木粉废料转移出第一中模3240。具体地,第四气缸c 3253驱使顶升件c 3251上移,带动顶针c 3252伸入逐渐压制孔c 3243内将铁木粉废料向上顶出压制孔c 3243,铁木粉废料在移动过程中逐渐松动;于此同时,吸盘3257通过第五气缸c 3256移动至放置槽c 3242内并吸住松动状态的电木粉废料,当第五气缸c 3256驱动吸盘3257上移带动铁木粉废料移动至第一中模3240上方后,第三直线电机c 3255驱使第五气缸c 3256移动至铁木粉废料位于电木粉废料收集盒c上方,电木粉废料从吸盘3257处落入电木粉废料收集盒c内。进而较佳地方便了对电木粉废料的清理与收集。
114.如图21-26所示,本实施例一种换向器铜片在线视觉监测机构包括机台b2100,机台b 2100处沿其长度方向从后至前依次设有上料区域b、监测区域以及换向器存储区域;监测区域从后至前依次设有分别用于监测换向器侧面、云母、底面、顶面与内孔的第一监测单元、第二监测单元、第三监测单元、第四监测单元与第五监测单元;第一监测单元、第二监测单元、第三监测单元、第四监测单元与第五监测单元右侧处均设有废品出料口2110;
115.机台b 2100处设有用于沿机台b 2100长度方向做往复运动的转运机构b;转运机构b通过往复运动以实现将上料区域b、第一监测单元、第二监测单元、第三监测单元、第四监测单元与第五监测单元处换向器转运至第一监测单元、第二监测单元、第三监测单元、第四监测单元、第五监测单元与换向器存储区域处、以及将监测不合格的换向器转运至对应的废品出料口2110处。实现了换向器的自动化上下料、换向器外观的连续性自动监测与换向器的分类,进而提升了换向器的监测效率,且提升了换向器监测结果的稳定性,故而提高了分级精度和生产率。具体地,转运机构b前移将上料区域b、第一监测单元、第二监测单元、第三监测单元、第四监测单元与第五监测单元处换向器转运至第一监测单元、第二监测单元、第三监测单元、第四监测单元、第五监测单元与换向器存储区域处;在前移途中,经第一监测单元、第二监测单元、第三监测单元、第四监测单元与第五监测单元监测不合格的换向器落入对应废品出料口2110处;单次转运完成后,转运机构b后移返回至初始区域。故而较佳地实现了对换向器侧面、云母、底面、顶面与内孔处各技术参数的监测,故而较佳地实现了对换向器表面技术参数的全面监测,且在监测的同时实现了换向器的分级,进而方便了后续对换向器加工数据源的统计与分析。
116.本实施例中,机台b 2100上端面处设有第一导轨b 2120,转运机构b包括用于与第一导轨b 2120滑动配合的转运板b 2121、以及用于夹取换向器的机械手b 2122,机械手b 2122设有6个且6个机械手b 2122间隔设于转运板b 2121上端面处,转运板b 2121与监测区域呈左右设置。所述6个机械手b2122依次对应上料区域b、第一监测单元、第二监测单元、第三监测单元、第四监测单元与第五监测单元设置。
117.转运板b 2121后移至6个机械手依次位于上料区域b、第一监测单元、第二监测单元、第三监测单元、第四监测单元与第五监测单元处后,6个机械手夹取对应区域换向器;当转运板b 2121前移至换向器位于对应废品出料口2110上方时,机械手松开经上一监测单元监测的不合格换向器并使其落入废品出料口2110处;当转运板b 2121前移至6个机械手依次位于第一监测单元、第二监测单元、第三监测单元、第四监测单元、第五监测单元与换向
器存储区域处时,机械手松开换向器并后移;单次转运完成。
118.转运机构b还包括设于机台b 2100上端面处用于驱动转运板b 2121往复移动的多个第一气缸b 2123。故而较佳地实现了转运板b 2121的往复运动。机台b 2100处设有第一监测孔b 3310,第一监测单元包括设于第一监测孔b 3310处用于放置换向器的第一放置台b 2321,第一放置台b 2321上方处设有用于监测第一放置台b 2321处换向器的第一监测相机b 2331,机台b2100处设有第一光源组件b;机台b 2100下端部设有第一固定架b 2340,第一固定架b 2340处设有用于安装第一放置台b 2321的第一活动板b 2341、以及用于驱动第一活动板b 2341沿竖直方向移动的第二气缸b 2611,第一活动板b 2341处设有用于驱动第一放置台b 2321转动的第一电机b 2612;机台b 2100上端部设有第二固定架b 2342,第二固定架b 2342处转动设有轴向平行于机台b 2100长度方向的第一安装轴b 2410、以及用于与第一安装轴b 2410转动配合且用于安装第一监测相机b 2331的第二活动板b 2343;第一光源组件b包括设于机台b 2100上端面处的第一背光源b 2351与第一线形光源b 2352,第一背光源b 2351与第一线形光源b 2352分别设于第一监测孔b 3310左侧与右侧,第一线形光源b2352设有两个且第一放置台b 2321设于两第一线形光源b 2352之间。
119.本实施例中,机台b 2100处设有第二监测孔b 2360,第二监测单元包括设于第二监测孔b 2360处用于放置换向器的第二放置台b 2361,第二放置台b 2361上方处设有用于监测第二放置台b 2361处换向器的第二监测相机b,机台b 2100处设有第二光源组件b;机台b 2100下端部设有第三固定架b 2371,第三固定架b 2371处设有用于安装第二放置台b 2361的第三活动板b 2372、以及用于驱动第三活动板b 2372沿竖直方向移动的第三气缸b 2521,第三活动板b 2372处设有用于驱动第二放置台b 2361转动的第二电机b 2522;机台b 2100上端部设有第四固定架b 2373,第四固定架b 2373处转动设有轴向平行于机台b 2100长度方向的第二安装轴b 2374、以及用于与第二安装轴b 2374转动配合且用于安装第二监测相机b的第四活动板b 2375;第二光源组件b包括设于机台b 2100上端面处的第二背光源b 2381与第二背光源b 2381,第二背光源b 2381与第二背光源b 2381分别设于第二监测孔b 2360左侧与右侧,第二背光源b 2381设有两个且第二放置台b 2361设于两第二背光源b 2381之间。
120.通过第一监测单元的设置,能够较佳地实现在侧面正光条件下对例如侧面高度、槽内异物、铜皮表面伤、铜皮表面伤、铜皮底部缺角、槽宽、漏铣槽、铜皮缺失等换向器侧部技术参数的采集与监测,以及在侧面线光条件下对钩长、钩损、钩缺失等换向器侧部技术参数的采集与监测;通过第二监测单元的设置,能够较佳地实现在侧面角度对例如侧面高度、铜皮表面伤、槽区云母残留、槽宽、钩长、钩损、顶面电木缺陷、底部电木缺陷等换向器侧部处云母技术参数的采集与检测。其中,第一线形光源b 2352与第一背光源b 2351相互配合形成了侧面正光与侧面线光的监测条件;第二背光源b 2381与第二背光源b 2381相互配合提升了换向器的轮廓特征,进而提升了监测精准度。
121.其中,第二活动板b 2343与第四活动板b 2375分别可转动的安装于第一安装轴b 2410与第二安装轴b 2374处,从而较佳地方便了对第一监测相机b 2331与第二监测相机b监测角度的调节;其中,可转动的第一放置台b 2321与第二放置台b 2361较佳地驱动的换向器的转动,由于第一监测相机b 2331与第二监测相机b设于换向器侧部,故而实现了第一监测相机b 2331与第二监测相机b对转动中的换向器侧面进行全方位数据采集;其中,可上
下移动的第一活动板b 2341与第三活动板b 2372分别较佳地带动了第一放置台b 2321与第二放置台b 2361的同步移动,进而较佳地使得第一放置台b 2321与第二放置台b 2361带动换向器在机械手处与监测位置处之间的垂直移动。
122.本实施例中,第二固定架b 2342包括两竖直设于机台b 2100上端面处的第一固定柱b 2342a、以及横穿两第一固定柱b 2342a且呈u形的第一固定板b2342b,第一安装轴b 2410设于第一固定板b 2342b处;第二活动板b 2343处设有用于与第一安装轴b 2410配合的第一活动孔b 2421、以及用于连通对应第一活动孔b 2421的第一通道b 2422,第二活动板b 2343板面处设有垂直第一通道b 2422设置的第一螺纹孔b 2423、以及用于与第一螺纹孔b 2423配合对第二活动板b 2343周向与轴向位置进行锁定的第一螺栓b。
123.本实施例中,第四固定架b 2373包括两竖直设于机台b2100上端面处的第二固定柱b 2373a、以及横穿两第二固定柱b 2373a且呈u形的第二固定板b2373b,第二安装轴b 2374设于第二固定板b 2373b处;第四活动板b 2375处设有用于与第二安装轴b 2374配合的第二活动孔b、以及用于连通对应第二活动孔b的第二通道b,第二活动板b 2343板面处设有垂直第二通道b设置的第二螺纹孔b、以及用于与第二螺纹孔b配合对第二活动板b 2343周向与轴向位置进行锁定的第二螺栓b。穿过第一螺纹孔b 2423的第一螺栓能够驱使第一通道b 2422两侧的第二活动板b 2343同向移动,故而使得第一活动孔b 2421侧壁抵紧在第一安装轴b 2410外侧壁处,故而能够较佳地锁紧第二活动板b 2343的位置;穿过第二螺纹孔b的第二螺栓能够驱使第二通道b两侧的第四活动板b2375同向移动,故而使得第二活动孔b侧壁抵紧在第二安装轴b 2374外侧壁处,故而能够较佳地锁紧第四活动板b 2375的位置。
124.本实施例中,机台b 2100处设有第三监测孔b,第三监测单元包括设于第三监测孔b处用于放置换向器的第三放置台b 2211,第三放置台b 2211为无色透明材质制成,第三放置台b 2211可为玻璃;第三监测单元还包括第三光源组件b、以及设于第三放置台b 2211正下方的第三监测相机b 2510,第三光源组件b包括设于第三放置台b 2211正上方的第三背光源b 2131、以及设于第三放置台b 2211与第三监测相机b 2510之间的第一环形光源b 2511;机台b2100下端面处设有用于安装第三监测相机b 2510与第一环形光源b 2511的第五固定架b 2512,机台b 2100上端面处设有用于安装第三背光源b 2131的第六固定架b 2132。
125.通过第三监测单元的设置,能够较佳地实现在底面正光条件下对例如表面缺陷、表面异物、粉皮厚、完整度等换向器底部技术参数的采集与监测,以及在底面背光条件下对例如外径、内径等换向器底部技术参数的采集与监测;其中,第一环形光源b 2511与第三背光源b 2131相互配合形成了换向器底面正光与底面背光的监测条件。
126.本实施例中,机台b2100处设有第四监测孔b,第四监测单元包括设于第四监测孔b处用于放置换向器的第四放置台b 2212,第四放置台b 2212为无色透明材质制成;第四监测单元还包括第四光源组件b、以及设于第四放置台b 2212正上方的第四监测相机b 2133,第四光源组件b包括设于第四放置台b 2212正下方的第四背光源b 2520、以及设于第四放置台b 2212与第四监测相机b 2133之间的第二环形光源b 2134;机台b 2100下端面处设有用于安装第四背光源b2520的第七固定架b 2521,机台b 2100上端面处设有分别用于安装第二环形光源b 2134、第四监测相机b 2133的第八固定架b 2135与第九固定架b 2136。
127.第四监测单元的设置,能够较佳地实现在顶面正光条件下对例如侧面高度、槽内异物、铜皮表面伤、铜皮底部缺角、槽宽、漏铣槽、铜皮缺失等换向器顶部技术参数的采集与监测,以及在顶面背光条件下对例如钩宽、钩钩等分度、沟外径、外径、内径等换向器顶部技术参数的采集与监测;其中,第二环形光源b 2134与第四背光源b 2520相互配合形成了换向器顶面正光与顶面被光的监测条件。机台b 2100处设有第五监测孔b,第五监测单元包括设于第五监测孔b处用于放置换向器的第五放置台b 2213,第五放置台b 2213为无色透明材质制成,第五放置台b 2213可为玻璃;第五监测单元还包括分别设于第五放置台b 2213正上方与正下方的第五监测相机b 2137与第五光源组件b,第五光源组件b为第五背光源b 2530;机台b2100下端处设有用于安装第五背光源b 2530的第十固定架b 2531,第五监测相机b 2137设于第九固定架b 2136处。
128.通过第五监测单元的设置,能够较佳地实现了对例如内孔裂纹、内孔完整度等换向器内孔技术参数的采集与监测;其中,由于第五背光源b 2530能够突出换向器的轮廓特征,故而能够提升换向器监测结果的准确度;由于第五放置台b 2213的材质特性,能够较佳地降低对第五背光源b 2530的干扰。
129.本实施例中,机台b 2100下端部设有安装板b 2141、以及用于固定安装板b 2141的支撑柱b 2101;安装板b 2141处设有对应废品出料口2110设置的传送单元,传送单元用于将不合格换向器从废品出料口2110处运送至机台b2100左端部处;传送单元包括设于安装板b 2141处的安装座b 2142,安装座b 2142处设有皮带轮b 2143、以及用于与皮带轮b 2143配合的皮带b 2144,安装座b2142处还设有用于驱动皮带轮b 2143转动的第三电机b 2545。
130.通过传送单元的设置,通过机械手b 2122转运至废品出料口2110处的不合格换向器落入皮带b 2144处,并被皮带b 2144传送至机台b 2100左端部。由于机台b 2100左端部空间较大,故而方便对不合格换向器的分级与收集。
131.本实施例中,第一监测相机b2331、第二监测相机b、第三监测相机b 2510、第四监测相机b 2133与第五监测相机b 2137、转运机构b均与控制系统电线连接,第一监测相机b2331、第二监测相机b、第三监测相机b 2510、第四监测相机b 2133与第五监测相机b 2137用于采集换向器成像并将其采集数据传送至控制系统;plc控制系统通过分析换向器成像的各技术参数并将其与预设范围进行对比、并对转运机构b发送指令;当换向器技术参数位于预设范围内,换向器为合格品,转运机构b将换向器移动至下一监测单元或换向器存储区域处,当换向器技术参数不在预设范围内,换向器为不合格品,转运机构b将换向器移动至废品出料口2110处。
132.本实施例中,第一监测相机b2331、第二监测相机b、第三监测相机b 2510、第四监测相机b 2133与第五监测相机b 2137的摄像头处均前置显微镜,显微镜采用阵列式组合,显微器采用从2倍-nx的显微镜物镜,使得第一监测相机b2331、第二监测相机b、第三监测相机b 2510、第四监测相机b 2133与第五监测相机b 2137能够将换向器放大后的成像输入至控制系统,进而较佳地提高了检测精度。机台a 110长度方向平行于机台b 2100长度方向。
133.容易理解的是,本领域技术人员在本技术提供的实施例的基础上,可以对本技术的实施例进行结合、拆分、重组等得到其他实施例,这些实施例均没有超出本技术的保护范围。
134.总之,以上所述仅为本发明的较佳实施例,凡依本发明申请专利范围所作的均等变化与修饰,皆应属本发明专利的涵盖范围。