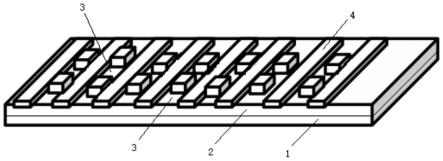
1.本发明涉及micro led相关技术领域,具体为用于micro led的氮化镓晶体,更具体为涉及一种可消除外壁损伤的氮化镓晶体制备工艺。
背景技术:2.micro-led显示技术是最新一代的显示技术,与oled显示技术相比具有亮度高,耐高温,像素密度高的特点。micro-led显示技术的优势来自于其1-10微米的小型化尺寸,形成微型尺寸需要进行大量的刻蚀工作。然而刻蚀带来的有源层外壁损伤就成为严重困扰micro-led技术进一步发展的障碍。
3.常用的micro-led器件结构自下而上为金属电极、n型氮化镓,ingan/gan多量子阱层(有源层),p型gan,ito。空穴及电子经电极注入后于多量子阱层发生复合,这一复合过程按照是否释放出光子分为辐射复合与非辐射复合。非辐射复合多发生于禁带中央的缺陷陷阱中,刻蚀带来的缺陷为非辐射复合提供了大量的复合中心,降低了器件的辐射效率。
技术实现要素:4.本发明的目的在于去除刻蚀工艺导致的外壁损伤问题,不用再修复强碱腐蚀产生的外壁缺陷。使用氧化硅对氮化镓生长实现限制,减少刻蚀这一工艺步骤,进而减少对外壁的损坏,本发明提供技术方案具体如下:
5.一种可消除外壁损伤的氮化镓晶体制备工艺,包括步骤
6.s1:形核层gan生长,
7.使用mocvd技术在蓝宝石衬底上生长无掺杂的氮化镓形核层,
8.s2:n型gan生长,
9.使用mocvd技术在氮化镓形核层上继续生长掺杂的si的n型氮化镓样品,
10.其特征在于,
11.所述n型氮化镓生长后,去除对n型氮化镓的刻蚀,使用氧化硅对氮化镓生长实现限制。
12.优选地,所述使用氧化硅对氮化镓生长实现限制,为形成相互间隔开的槽状结构,让氮化镓在所述槽状结构中沉积。
13.进一步,还包括s3:导光层生长,
14.在所述n型氮化镓上沉积一层sio2薄膜层,
15.s4:刻蚀导光层,使部分n型gan可以露出表面,
16.通过标准的光刻及显影工艺使得留在n型氮化镓样品表面的光刻胶为设计的槽状结构图案。
17.进一步,还包括步骤s5:多量子阱层沉积,
18.在所述槽状结构内沉积in-gan层和n-gan层;
19.s6:继续沉积p型氮化镓,
20.使用mocvd技术在氮化镓形核层上继续生长掺杂的mg的p型氮化镓。
21.优选地,所述步骤s3沉积sio2薄膜层厚度为150-200nm。
22.进一步,所述导光层生长步骤具体为:
23.首先采用丙酮、乙醇和去离子水对n型氮化镓样品进行超声清洗,以去除表面有机污染物;
24.在洗净后的样品表面采用等离子体增强化学气相沉积法生长一层厚度为150-200nm的sio2薄膜层;
25.采用匀胶机将az1500光刻胶旋涂于样品表面,通过标准的光刻及显影工艺使得留在样品表面的光刻胶为设计的图案:宽1-2微米、内径长为3-6微米的槽状结构;
26.利用反应离子刻蚀技术通入o2去除残胶,在通入cf4利用上一步制备的光刻胶图案作为掩膜刻蚀sio2,将光刻胶图案转移至sio2上,通过丙酮和氢氟酸对样片表面残余的光刻胶和sio2进行清除。
27.优选地,所述多量子阱层沉积过程为:
28.将样品衬底送至mbe送样室进行时长为0.5-2h、温度为40-50℃,进行初步的除气工作;
29.完成后将样品送入样品预处理室,进行时长为1-2h、温度为400-500℃,进行进一步除气;
30.除气完毕之后,将样品送至生长腔室,待其升温至生长温度后开启ga和si源炉的挡板进行ingan层和n-gan层沉积。
31.优选地,所述ingan层和n-gan层为间隔沉积,具体为时长为0.5
ꢀ‑
1分钟的ingan层、10
ꢀ‑
15分钟的n-gan层周期性生长,ingan层厚度为2-3nm,n-gan层的厚度为15-20nm,持续5-10个周期。
32.优选地,所述ingan层和n-gan层的厚度小于等于槽状结构的深度。
33.进一步,还包括步骤:
34.s7:在p型氮化镓上沉积电极。
35.s8:沉积介电层于p型氮化镓上。
36.s9:于未沉积多量子阱层部分使用刻蚀将器件分离。
37.利用氮化镓材料生长条件苛刻的原理,使用绝缘层将多量子阱层沉积于特定槽状结构位置,在后续的刻蚀工艺中只需刻蚀绝缘层即可保护多量子阱层,减少刻蚀损伤带来的非辐射复合中心,提高量子效率。
38.本发明将二氧化硅或氮化硅等绝缘层,引入器件中,因为氮化镓不能在氧化硅上生长只能填充到氧化硅界定的格子中,生长完成后光刻掉氧化硅,即可得到外壁光滑无缺陷的氮化镓晶体,解决了刻蚀工艺带来的器件外壁损伤问题,从而解决外壁损伤所带来的发光效率降低的问题。
附图说明
39.图1是本发明氮化镓晶体形成槽状结构的示意图;
40.图2为图1中槽状结构的内部结构示意图;
41.图3位最终器件刻蚀时的示意图。
具体实施方式
42.下面将结合示意图对本发明的具体实施方式进行更详细的描述。根据下列描述和申请专利范围,本发明的优点和特征将更清楚。需说明的是,附图均采用非常简化的形式且均使用非精准的比例,仅用以方便、明晰地辅助说明本发明实施例的目的。
43.一种可消除外壁损伤的氮化镓晶体制备工艺,包括步骤
44.s1:形核层gan生长,
45.使用mocvd技术在蓝宝石衬底上生长无掺杂的氮化镓形核层1,无掺杂的氮化镓形核层1厚度为2-3微米,本实施为2微米。
46.s2:n型gan生长,
47.使用mocvd技术在氮化镓形核层1上继续生长掺杂的si的n型氮化镓样品2,n型氮化镓大于掺杂的氮化镓形核层1的厚度,约为3-5微米,本实施例为3微米。
48.s3:导光层生长,
49.在所述n型氮化镓上沉积一层sio2薄膜层4,
50.具体为:
51.首先采用丙酮、乙醇和去离子水对n型氮化镓样品进行超声清洗,以去除表面有机污染物;
52.在洗净后的样品表面采用等离子体增强化学气相沉积法生长一层厚度为150-200nm的sio2薄膜层4,本实施例为180nm;
53.s4:刻蚀导光层,使部分n型gan可以露出表面,
54.通过标准的光刻及显影工艺使得留在n型氮化镓样品表面的光刻胶为设计的槽状结构图案。
55.采用匀胶机将az1500光刻胶旋涂于样品表面,通过标准的光刻及显影工艺使得留在样品表面的光刻胶为设计的图案:宽1-2微米、内径长为3-6微米的槽状结构3,本实施例为宽2微米、内径长为5微米的槽状结构3;槽状结构3相互独立并彼此间隔开,不互相连通。
56.利用反应离子刻蚀技术通入o2去除残胶,在通入cf4利用上一步制备的光刻胶图案作为掩膜刻蚀sio2,将光刻胶图案转移至sio2上,通过丙酮和氢氟酸对样片表面残余的光刻胶和sio2进行清除。
57.s5:多量子阱层沉积,
58.在所述槽状结构内沉积in-gan层3-1和n-gan层3-1;
59.因为氮化镓不能在介电层上生长,所以只能沉积在n型gan上,具体过程为:
60.将样品衬底送至mbe送样室进行时长为1h、温度为45℃,进行初步的除气工作;
61.完成后将样品送入样品预处理室,进行时长为1h、温度为450℃,进行进一步除气;
62.除气完毕之后,将样品送至生长腔室,待其升温至生长温度后开启ga和si源炉的挡板进行ingan层和n-gan层沉积。
63.ingan层和n-gan层为间隔沉积,具体为时长为0.5分钟的ingan层、10分钟的n-gan层周期性生长,ingan层3-1厚度为3nm,n-gan层3-2的厚度为17nm,持续9个周期。
64.使用氧化硅对氮化镓生长实现限制,为形成相互间隔开的槽状结构,让氮化镓在所述槽状结构3中沉积。ingan层3-1和n-gan层3-2的总厚度小于等于槽状结构3的深度,优选地为150-200nm,本实施例刚好相等,都是180nm。
65.s6:继续沉积p型氮化镓,
66.使用mocvd技术在氮化镓形核层上继续生长掺杂的mg的p型氮化镓,p型氮化镓厚度为400-500nm,本实施例为450nm。
67.s7:在p型氮化镓上沉积电极。
68.s8:沉积介电层于p型氮化镓上。
69.s9:于未沉积多量子阱层部分使用刻蚀将器件分离,刻蚀过程如附图3所示,刻蚀线p沿着形成槽状结构、横竖交错的sio2薄膜层4将器件刻蚀成一块块,该过程只需对sio2薄膜层4进行刻蚀,而不用对槽状结构3内部氮化镓层刻蚀,避免了外壁损伤。
70.n型氮化镓生长后,去除对n型氮化镓的刻蚀,使用氧化硅对氮化镓生长实现限制。
71.通过以上较佳具体实施例的详述,希望能更加清楚描述本发明的特征与精神,而并非以上述所揭示的较佳具体实施例来对本发明的范畴加以限制。相反地,其目的是希望能涵盖各种改变及具相等性的安排于本发明所欲申请权利要求的范畴内。