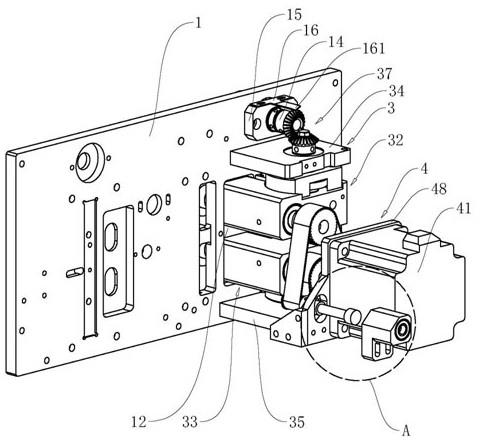
1.本技术涉及剥线机设备领域,尤其是涉及一种自动剥线机的压线组件。
背景技术:2.剥线机是一种将电缆外部所包裹的塑料包皮与电缆内部的金属线芯相互剥离的机器。现有的剥线机一般都可实现电缆的自动剥线,其一般具有送线装置和出线装置,在送线装置和出线装置中间设置有切线装置,通过送线装置、出线装置和切线装置之间的相互联动配合,即可实现对线缆的切断、单头剥线或是双头剥线等操作。
3.相关技术中的送线装置和出线装置,其中一般需要配备有压线组件,压线组件一般包括上下两个走线轮,在进行剥线操作时,电缆位于上下两个走线轮之间,且电缆表面与走线轮表面之间紧密贴合,在两个走线轮同步反向转动时,电缆即可跟随走线轮实现进线和退线的操作。
4.针对上述中的相关技术,发明人认为在实际使用的过程中,在对不同直径的电缆进行剥线操作时,为了达到最好的剥线效果,两个走线轮之间的距离需要跟随电缆直径的改变而改变,现有的剥线机,两个走线轮一般都可手动实现独立的位置调节,从而实现两个走线轮之间的间距调节,但是该种调节方式精度较低,且频繁调节后,容易导致走线轮的固定处产生松动,不仅调节的操作较为麻烦,剥线机的精度还有可能受到影响,从而导致最终剥线质量的下降。
技术实现要素:5.为了解决现有的剥线机的压线组件的压线轮间距调节较为麻烦的问题,本技术提供一种自动剥线机的压线组件。
6.本技术提供的一种自动剥线机的压线组件采用如下的技术方案:
7.一种自动剥线机的压线组件,该种压线组件安装在剥线机的组装面板上,所述压线组件包括有压线结构、间距调节结构和驱动结构,所述压线结构包括有第一传动轴和第二传动轴,所述第一传动轴的末端设置有第一走线轮,所述第二传动轴的末端设置有第二走线轮,所述间距调节结构包括有竖直设置的调节丝杆,所述调节丝杆表面形成有第一螺纹段和第二螺纹段,所述第一螺纹段和第二螺纹段分别设置在调节丝杆的两端且两者之间的螺纹旋向相反,所述第一螺纹段处螺纹连接有第一螺母组件,所述第一传动轴通过轴承与第一螺母组件之间实现转动连接,所述第二螺纹段处螺纹连接有第二螺母组件,所述第二传动轴通过轴承与第二螺母组件之间实现转动连接,所述驱动结构驱动第一传动轴和第二传动轴实现同步反向转动。
8.通过采用上述技术方案,在需要调节第一走线轮和第二走线轮之间的距离时,只需转动调节丝杆,由于第一螺纹段和第二螺纹段的螺纹旋向相反,故第一螺母组件和第二螺母组件会沿调节丝杆实现相反方向的移动,从而即可实现第一走线轮和第二走线轮之间的靠近或远离,即可方便的对第一走线轮和第二走线轮之间的间距进行调整,以便于适配
直径不同的电缆。在进行调节时,无需对第一螺母组件和第二螺母组件进行拆卸,故有效减少了频繁调节后第一螺母组件或第二螺母组件产生松动的可能性。且调节丝杆转动时,第一走线轮和第二走线轮以相同的速度实现移动,可以使得电缆始终保持在相同的工作位置,从而使得在调节后,无需再对剥线机的剩余部分进行位置调节,大大降低了操作难度,并通过减少操作步骤提高了剥线精度。
9.优选的,所述压线结构还包括有第一辅助轮、第二辅助轮和走线同步带,所述第一走线轮、第二走线轮、第一辅助轮和第二辅助轮表面均设置有同步齿,所述走线同步带环绕设置在第一走线轮和第一辅助轮之间,所述走线同步带环绕设置在第二走线轮和第二辅助轮之间;
10.所述第一辅助轮转动连接有第一固定柱,所述第二辅助轮转动连接有第二固定柱,所述第一传动轴和第二传动轴上均通过转动轴承连接有辅助连臂,位于所述第一传动轴上的辅助连臂远离第一传动轴的一端套设在第一固定柱外,位于所述第二传动轴上的辅助连臂远离第二传动轴的一端套设在第二固定柱外,所述辅助连臂绕第一传动轴或第二传动轴双向转动至极限位置时,所述第一固定柱和第二固定柱分别位于第一安装位和第二安装位;
11.所述第一固定柱和第二固定柱均安装于第一安装位时,线缆与走线同步带位于第一辅助轮和第一走线轮之间的部分相贴合,线缆与走线同步带位于第二辅助轮和第二走线轮之间的部分相贴合;
12.所述第一固定柱和第二固定柱均位于第二安装位时,线缆与走线同步带包覆在第一走线轮和第二走线轮外部的部分相贴合。
13.通过采用上述技术方案,在待剥线的线缆长度较长的情况下,为了提高剥线时的稳定性,工作人员可以转动辅助连臂,使得第一固定柱和第二固定柱均位于第一安装位,此时走线同步带和线缆之间有较长的接触长度,可以实现对线缆更为稳定的输送,以有效减少线缆在移动时与第一走线轮和第二走线轮之间发生脱离的可能性。
14.当待剥线的线缆长度比较小的情况下,工作人员可以转动辅助连臂,使得第一固定柱和第二固定柱均位于第二安装位,此时走线同步带和线缆之间的接触长度大大减少,可以为切线提供足够的切线空间。
15.通过转动辅助连臂改变第一固定柱和第二固定柱的位置,可以使得该种自动剥线机更加适合于长线缆和短线缆的剥线,大大提高了该种自动剥线机的适用性。
16.优选的,所述间距调节结构包括有第一固定板和第二固定板,所述第一固定板和第二固定板分别设置在调节丝杆长度方向的两端,所述第一固定板和第二固定板内部均固定设置有转动轴承,所述第一固定板和第二固定板内的转动轴承的内圈分别与调节丝杆的两端之间固定连接。
17.通过采用上述技术方案,第一固定板和第二固定板用于对调节丝杆的两端进行固定,并有效提高调节丝杆转动时的稳定性。
18.优选的,所述第一螺母组件包括有第一螺母、第一固定座和第一连接箱,所述第一螺母和第一固定座之间固定连接,所述第一连接箱与第一固定座之间固定连接,所述第一连接箱的侧部沿第一传动轴的长度方向开设有第一连接通孔,所述第一连接通孔的两端均设置有转动轴承,所述第一传动轴两端穿出第一连接通孔设置;
19.所述第二螺母组件包括有第二螺母、第二固定座和第二连接箱,所述第二螺母和第二固定座之间固定连接,所述第二连接箱与第二固定座之间固定连接,所述第二连接箱的侧部沿第二传动轴的长度方向开设有第二连接通孔,所述第二连接通孔的两端均设置有转动轴承,所述第二传动轴两端穿出第二连接通孔设置。
20.通过采用上述技术方案,第一连接箱和第二连接箱分别用于对第一传动轴和第二传动轴实现固定,从而使得第一螺母和第二螺母能够带动第一传动轴和第二传动轴移动,第一连接箱和第二连接箱中转动轴承的设置能够实现第一传动轴和第二传动轴的稳定转动。
21.优选的,所述第一连接箱和第二连接箱内部沿调节丝杆长度方向开设有供调节丝杆穿过的传动通孔,所述传动通孔为阶梯孔且由大径通孔和小径通孔组成,所述大径通孔的直径大于小径通孔;
22.所述大径通孔位于小径通孔和第一螺母之间,所述大径通孔内设置有第一压缩弹簧,所述第一压缩弹簧的两端分别与第一螺母表面和传动通孔的阶梯面抵接;
23.所述大径通孔位于小径通孔和第二螺母之间,所述大径通孔内设置有第二压缩弹簧,所述第二压缩弹簧的两端分别与第二螺母表面和传动通孔的阶梯面抵接。
24.通过采用上述技术方案,以第一螺母组件为例,由于结构本身的限制,第一螺母与调节丝杆连接时,两者之间的配合会不可避免的存在一定的间隙,反映到第一走线轮上,则在调节丝杆未转动的情况下,第一走线轮可能会在竖直方向上产生轻微的位置偏移,从而导致第一走线轮和电缆之间摩擦力不足,并最终导致电缆无法在第一走线轮的带动下实现前后移动。故在大径通孔内设置第一压缩弹簧,第一压缩弹簧在压缩状态下同时对第一螺母和第一连接箱产生作用力,从而使得第一螺母与调节丝杆之间紧密贴合,有效减少第一螺母产生位置偏移的情况。类似的,第二压缩弹簧也可使得第二螺母与调节丝杆之间紧密贴合,从而有效减少第二螺母产生位置偏移的情况。通过设置第一压缩弹簧和第二压缩弹簧,有效提高了第一走线轮和第二走线轮的位置精度,从而有效提高了电缆的移动精度,进一步提高了剥线精度。
25.优选的,所述组装面板上朝向第一连接箱的一面设置有滑轨,所述滑轨沿调节丝杆的长度方向延伸设置,所述第一连接箱上固定连接有第一滑块,所述第二连接箱上固定连接有第二滑块,所述第一滑块和第二滑块均与滑轨相配合且与滑轨之间滑动连接。
26.通过采用上述技术方案,滑轨的设置可以对第一滑块和第二滑块的移动轨迹进行限定,从而有效提高第一滑块和第二滑块的移动稳定性,减少移动过程中可能产生的位置偏移。
27.优选的,所述组装面板朝向第一连接箱的一面开设有容纳槽,所述容纳槽沿调节丝杆的长度方向延伸,所述第一连接通孔的外部形成有第一连接部,所述第一连接部的端面插入至容纳槽中,所述容纳槽的宽度与第一连接部的宽度相同;
28.所述第二连接孔的外部形成有第二连接部,所述第二连接部的端面插入至容纳槽中,所述容纳槽的宽度与第二连接部的宽度相同。
29.通过采用上述技术方案,容纳槽起到避让作用,可以有效降低第一传动轴和第二传动轴的所需长度,从而提高第一传动轴自身的结构稳定性。
30.优选的,所述调节丝杆的一端穿出第一固定板设置,所述组装面板上设置有调节
旋钮,所述调节旋钮连接有垂直于组装面板设置的调节柱,所述调节柱穿过组装面板的一端与调节丝杆穿出第一固定板的一端之间通过锥齿轮传动结构连接,所述锥齿轮传动结构包括有固定设置在调节柱末端的第一锥齿轮和固定设置在调节丝杆末端的第二锥齿轮。
31.通过采用上述技术方案,在需要对第一走线轮和第二走线轮之间的距离进行调节时,用户只需转动调节旋钮,调节旋钮带动调节柱产生转动,随后通过锥齿轮传动结构将动力传输至调节丝杆,即可实现调节丝杆转动,便于用户操作。
32.优选的,所述组装面板朝向调节丝杆的一端设置有调节安装板,所述调节柱穿过调节安装板设置,所述调节安装板上固定连接有卡片,所述卡片沿调节柱长度方向延伸,所述卡片远离调节安装板的一端形成有尖端朝向第一锥齿轮设置的v形口,所述v形口的尖端插入至第一锥齿轮的齿根处,所述卡片由弹性材料制成。
33.通过采用上述技术方案,用户在转动调节旋钮进行间距调节时,由于卡片的v形口的尖端插入至第一锥齿轮的齿根处,故用户会感受到调节旋钮的转动受到阻力,持续施力后,第一锥齿轮会克服来自卡片的阻力并使得具有弹性的卡片发生形变,且用户可感受到卡片撞击第一锥齿轮时所产生的振动。同时,卡片的设置可以对第一锥齿轮起到限位的作用,并使得第一锥齿轮在剥线机的工作过程中不易发生转动。
34.优选的,所述驱动结构包括有驱动电机,所述驱动电机的输出轴的轴线与第一传动轴的轴线相平行,所述驱动电机的输出轴上套设有主动齿轮,所述第一传动轴靠近驱动电机的一端套设有第一传动齿轮,所述第二传动轴靠近驱动电机的一端套设有第二传动齿轮,所述驱动结构还包括有辅助轴和传动同步带,所述辅助轴上套设有辅助齿轮,所述第一传动齿轮设置在第二传动齿轮上方,所述主动齿轮和辅助齿轮分别设置在第二传动齿轮下方两侧的位置,所述传动同步带从第一传动齿轮处向下到达辅助齿轮,随后向上到达第二传动齿轮,随后向下到达主动齿轮,随后向上到达第一传动齿轮并形成闭环。
35.通过采用上述技术方案,通过辅助齿轮和主动齿轮的设置,传动同步带得以实现特定的缠绕方式,从而使得第一传动齿轮和第二传动齿轮能够以相反的方向同步转动,反映到第一走线轮和第二走线轮上,即第一走线轮和第二走线轮可以将电缆向同个方向移动。且上述缠绕方式还大大提高了主动齿轮、第一传动齿轮、第二传动齿轮及辅助齿轮与传动同步带之间的接触长度,从而有助于提高传动时的稳定性。
36.优选的,所述驱动结构包括有电机安装板,所述电机安装板与组装面板平行,所述电机安装板上分有供驱动电机安装的第一安装区和供辅助轴安装的第二安装区,所述第二安装区处设置有安装圆孔和第一腰形调节孔,所述第二安装区处安装有同步带调节块,所述同步带调节块上设置有第二腰形调节孔,所述第二腰形调节孔和安装圆孔之间穿设有螺钉以实现同步带调节块在电机安装板上的固定,所述同步带调节块内设置有供辅助轴安装的转动轴承,所述辅助轴穿过第一调节孔设置。
37.通过采用上述技术方案,通过第二腰形调节孔和安装圆孔,可以对同步带调节块的位置进行调节,即可以对辅助轴的位置进行有效调节。一方面,在初始的调试状态下或是长期使用后,传动同步带可能会产生张紧力不足的情况,通过调节同步带调节块的位置,即可对传动同步带的张紧度进行调节,以便于实现稳定的传动。另一方面,在对第一走线轮和第二走线轮的间距进行调节时,若调节量较小,传动同步带可以通过自适应而维持传动的稳定性,若调节量较大,则传动同步带会产生张紧力过大或过低的情况,此时可以通过调节
同步带调节块来对传动同步带的张紧力进行调节,以提高传动的稳定性。
38.综上所述,本技术包括以下至少一种有益技术效果:
39.1.通过调节丝杆、第一螺母组件和第二螺母组件的设置,能够起到快速方便实现第一走线轮和第二走线轮之间位置调节的效果;
40.2.通过辅助连臂、第一辅助轮和第二辅助轮的设置,能够起到使得该种自动剥线机更加适合于长线缆和短线缆剥线的效果;
41.3.通过调节旋钮、调节柱和锥齿轮传动结构的设置,能够起到方便用户通过调节旋钮调节间距的效果。
附图说明
42.图1是本技术实施例1的一种自动剥线机的压线组件的整体结构正面的示意图。
43.图2是本技术实施例1的一种自动剥线机的压线组件的整体结构背面的示意图。
44.图3是本技术实施例1的一种自动剥线机的压线组件的俯视图示意图。
45.图4是图3中b-b方向的剖面示意图(仅展示右半部分)。
46.图5是图4中e部的放大示意图。
47.图6是图3中c-c方向的剖面示意图(仅展示右半部分)。
48.图7是图3中d-d方向的剖面示意图。
49.图8是图2中a部的放大示意图,用于展示同步带调节块的爆炸结构。
50.图9是本技术实施例2的一种自动剥线机的压线组件的整体结构的示意图,第一固定柱和第二固定柱均位于第一安装位。
51.图10是图9中f部的放大示意图。
52.附图标记说明,1、组装面板;11、滑轨;12、容纳槽;13、调节旋钮;14、调节柱;15、调节安装板;16、卡片;161、v形口;2、压线结构;21、第一传动轴;211、辅助连臂;22、第二传动轴;23、第一走线轮;24、第二走线轮;25、第一辅助轮;26、第二辅助轮;27、走线同步带;28、第一固定柱;29、第二固定柱;3、间距调节结构;31、调节丝杆;311、第一螺纹段;312、第二螺纹段;32、第一螺母组件;321、第一螺母;322、第一固定座;323、第一连接箱;3231、第一连接通孔;324、第一压缩弹簧;325、第一滑块;326、第一连接部;33、第二螺母组件;331、第二螺母;332、第二固定座;333、第二连接箱;3331、第二连接通孔;334、第二压缩弹簧;335、第二滑块;336、第二连接部;34、第一固定板;35、第二固定板;36、传动通孔;361、大径通孔;362、小径通孔;37、锥齿轮传动结构;371、第一锥齿轮;372、第二锥齿轮;4、驱动结构;41、驱动电机;42、主动齿轮;43、第一传动齿轮;44、第二传动齿轮;45、辅助轴;46、传动同步带;47、辅助齿轮;48、电机安装板;481、安装圆孔;482、第一腰形调节孔;49、同步带调节块;491、第二腰形调节孔。
具体实施方式
53.以下结合附图1-8对本技术作进一步详细说明。
54.本技术实施例公开一种自动剥线机的压线组件。
55.实施例1
56.参照图1-8,该种压线组件安装在剥线机的组装面板1上,压线组件包括有压线结
构2、间距调节结构3和驱动结构4。
57.参照图1-8,压线结构2包括有第一传动轴21和第二传动轴22,第一传动轴21的末端设置有第一走线轮23,第二传动轴22的末端设置有第二走线轮24,在进行剥线时,电缆设置在第一走线轮23和第二走线轮24之间。
58.参照图1-8,间距调节结构3包括有竖直设置的调节丝杆31,调节丝杆31表面形成有第一螺纹段311和第二螺纹段312,第一螺纹段311和第二螺纹段312分别设置在调节丝杆31的两端且两者之间的螺纹旋向相反,第一螺纹段311处螺纹连接有第一螺母组件32,第一传动轴21通过轴承与第一螺母组件32之间实现转动连接,第二螺纹段312处螺纹连接有第二螺母组件33,第二传动轴22通过轴承与第二螺母组件33之间实现转动连接。间距调节结构3包括有第一固定板34和第二固定板35,第一固定板34和第二固定板35分别设置在调节丝杆31长度方向的两端,第一固定板34和第二固定板35内部均固定设置有转动轴承,第一固定板34和第二固定板35内的转动轴承的内圈分别与调节丝杆31的两端之间固定连接。第一固定板34和第二固定板35用于对调节丝杆31的两端进行固定,并有效提高调节丝杆31转动时的稳定性。
59.参照图1-8,第一螺母组件32包括有第一螺母321、第一固定座322和第一连接箱323,第一螺母321和第一固定座322之间固定连接,第一连接箱323与第一固定座322之间固定连接,第一连接箱323的侧部沿第一传动轴21的长度方向开设有第一连接通孔3231,第一连接通孔3231的两端均设置有转动轴承,第一传动轴21两端穿出第一连接通孔3231设置。第二螺母组件33包括有第二螺母331、第二固定座332和第二连接箱333,第二螺母331和第二固定座332之间固定连接,第二连接箱333与第二固定座332之间固定连接,第二连接箱333的侧部沿第二传动轴22的长度方向开设有第二连接通孔3331,第二连接通孔3331的两端均设置有转动轴承,第二传动轴22两端穿出第二连接通孔3331设置。第一连接箱323和第二连接箱333分别用于对第一传动轴21和第二传动轴22实现固定,从而使得第一螺母321和第二螺母331能够带动第一传动轴21和第二传动轴22移动,第一连接箱323和第二连接箱333中转动轴承的设置能够实现第一传动轴21和第二传动轴22的稳定转动。
60.参照图1-8,第一连接箱323和第二连接箱333内部沿调节丝杆31长度方向开设有供调节丝杆31穿过的传动通孔36,传动通孔36为阶梯孔且由大径通孔361和小径通孔362组成,大径通孔361的直径大于小径通孔362。大径通孔361位于小径通孔362和第一螺母321之间,大径通孔361内设置有第一压缩弹簧324,第一压缩弹簧324的两端分别与第一螺母321表面和传动通孔36的阶梯面抵接;大径通孔361位于小径通孔362和第二螺母331之间,大径通孔361内设置有第二压缩弹簧334,第二压缩弹簧334的两端分别与第二螺母331表面和传动通孔36的阶梯面抵接。
61.参照图1-8,以第一螺母组件32为例,由于结构本身的限制,第一螺母321与调节丝杆31连接时,两者之间的配合会不可避免的存在一定的间隙,反映到第一走线轮23上,则在调节丝杆31未转动的情况下,第一走线轮23可能会在竖直方向上产生轻微的位置偏移,从而导致第一走线轮23和电缆之间摩擦力不足,并最终导致电缆无法在第一走线轮23的带动下实现前后移动。故在大径通孔361内设置第一压缩弹簧324,第一压缩弹簧324在压缩状态下同时对第一螺母321和第一连接箱323产生作用力,从而使得第一螺母321与调节丝杆31之间紧密贴合,有效减少第一螺母321产生位置偏移的情况。类似的,第二压缩弹簧334也可
使得第二螺母331与调节丝杆31之间紧密贴合,从而有效减少第二螺母331产生位置 偏移的情况。通过设置第一压缩弹簧324和第二压缩弹簧334,有效提高了第一走线轮23和第二走线轮24的位置精度,从而有效提高了电缆的移动精度,进一步提高了剥线精度。
62.参照图1-8,组装面板1上朝向第一连接箱323的一面设置有滑轨11,滑轨11沿调节丝杆31的长度方向延伸设置,第一连接箱323上固定连接有第一滑块325,第二连接箱333上固定连接有第二滑块335,第一滑块325和第二滑块335均与滑轨11相配合且与滑轨11之间滑动连接。组装面板1朝向第一连接箱323的一面开设有容纳槽12,容纳槽12沿调节丝杆31的长度方向延伸,第一连接通孔3231的外部形成有第一连接部326,第一连接部326的端面插入至容纳槽12中,容纳槽12的宽度与第一连接部326的宽度相同;第二连接孔的外部形成有第二连接部336,第二连接部336的端面插入至容纳槽12中,容纳槽12的宽度与第二连接部336的宽度相同。滑轨11的设置可以对第一滑块325和第二滑块335的移动轨迹进行限定,从而有效提高第一滑块325和第二滑块335的移动稳定性,减少移动过程中可能产生的位置偏移。容纳槽12起到避让作用,可以有效减少第一传动轴21和第二传动轴22的所需长度。
63.参照图1-8,驱动结构4包括有驱动电机41,驱动电机41的输出轴的轴线与第一传动轴21的轴线相平行,驱动电机41的输出轴上套设有主动齿轮42,第一传动轴21靠近驱动电机41的一端套设有第一传动齿轮43,第二传动轴22靠近驱动电机41的一端套设有第二传动齿轮44,驱动结构4还包括有辅助轴45和传动同步带46,辅助轴45上套设有辅助齿轮47,第一传动齿轮43设置在第二传动齿轮44上方,主动齿轮42和辅助齿轮47分别设置在第二传动齿轮44下方两侧的位置,传动同步带46从第一传动齿轮43处向下到达辅助齿轮47,随后向上到达第二传动齿轮44,随后向下到达主动齿轮42,随后向上到达第一传动齿轮43并形成闭环。通过辅助齿轮47和主动齿轮42的设置,传动同步带46得以实现特定的缠绕方式,从而使得第一传动齿轮43和第二传动齿轮44能够以相反的方向同步转动,反映到第一走线轮23和第二走线轮24上,即第一走线轮23和第二走线轮24可以将电缆向同个方向移动。且上述缠绕方式还大大提高了主动齿轮42、第一传动齿轮43、第二传动齿轮44及辅助齿轮47与传动同步带46之间的接触长度,从而有助于提高传动时的稳定性。
64.参照图1-8,驱动结构4包括有电机安装板48,电机安装板48与组装面板1平行,电机安装板48上分有供驱动电机41安装的第一安装区和供辅助轴45安装的第二安装区,第二安装区处设置有安装圆孔481和第一腰形调节孔482,第二安装区处安装有同步带调节块49,同步带调节块49上设置有第二腰形调节孔491,第二腰形调节孔491和安装圆孔481之间穿设有螺钉以实现同步带调节块49在电机安装板48上的固定,同步带调节块49内设置有供辅助轴45安装的转动轴承,辅助轴45穿过第一调节孔设置。通过第二腰形调节孔491和安装圆孔481,可以对同步带调节块49的位置进行调节,即可以对辅助轴45的位置进行有效调节。一方面,在初始的调试状态下或是长期使用后,传动同步带46可能会产生张紧力不足的情况,通过调节同步带调节块49的位置,即可对传动同步带46的张紧度进行调节,以便于实现稳定的传动。另一方面,在对第一走线轮23和第二走线轮24的间距进行调节时,若调节量较小,传动同步带46可以通过自适应而维持传动的稳定性,若调节量较大,则传动同步带46会产生张紧力过大或过低的情况,此时可以通过调节同步带调节块49来对传动同步带46的张紧力进行调节,以提高传动的稳定性。
65.参照图1-8,调节丝杆31的一端穿出第一固定板34设置,组装面板1上设置有调节
旋钮13,调节旋钮13连接有垂直于组装面板1设置的调节柱14,调节柱14穿过组装面板1的一端与调节丝杆31穿出第一固定板34的一端之间通过锥齿轮传动结构37连接,锥齿轮传动结构37包括有固定设置在调节柱14末端的第一锥齿轮371和固定设置在调节丝杆31末端的第二锥齿轮372。组装面板1朝向调节丝杆31的一端设置有调节安装板15,调节柱14穿过调节安装板15设置,调节安装板15上固定连接有卡片16,卡片16沿调节柱14长度方向延伸,卡片16远离调节安装板15的一端形成有尖端朝向第一锥齿轮371设置的v形口161,v形口161的尖端插入至第一锥齿轮371的齿根处,卡片16由弹性材料制成。
66.本技术实施例1的实施原理为:在需要调节第一走线轮23和第二走线轮24之间的距离时,用户只需转动调节旋钮13,调节旋钮13带动调节柱14产生转动,随后通过锥齿轮传动结构37将动力传输至调节丝杆31,调节丝杆31转动后,由于第一螺纹段311和第二螺纹段312的螺纹旋向相反,故第一螺母组件32和第二螺母组件33会沿调节丝杆31实现相反方向的移动,从而即可实现第一走线轮23和第二走线轮24之间的靠近或远离,即可方便的对第一走线轮23和第二走线轮24之间的间距进行调整,以便于适配直径不同的电缆。在进行调节时,无需对第一螺母组件32和第二螺母组件33进行拆卸,故有效减少了频繁调节后第一螺母组件32或第二螺母组件33产生松动的可能性。且调节丝杆31转动时,第一走线轮23和第二走线轮24以相同的速度实现移动,可以使得电缆始终保持在相同的工作位置,从而使得在调节后,无需再对剥线机的剩余部分进行位置调节,大大降低了操作难度,并通过减少操作步骤提高了剥线精度。
67.用户在转动调节旋钮13进行间距调节时,由于卡片16的v形口161的尖端插入至第一锥齿轮371的齿根处,故用户会感受到调节旋钮13的转动受到阻力,持续施力后,第一锥齿轮371会克服来自卡片16的阻力并使得具有弹性的卡片16发生形变。同时,卡片16的设置可以对第一锥齿轮371起到限位的作用,并使得第一锥齿轮371在剥线机的工作过程中不易发生转动。
68.在对第一走线轮23和第二走线轮24的间距进行调节时,若调节量较小,传动同步带46可以通过自适应而维持传动的稳定性,若调节量较大,则传动同步带46会产生张紧力过大或过低的情况,此时可以通过调节同步带调节块49来对传动同步带46的张紧力进行调节,以提高传动的稳定性。
69.实施例2
70.参照图9-10,本实施例与实施例1的不同之处在于,所述压线结构2还包括有第一辅助轮25、第二辅助轮26和走线同步带27,所述第一走线轮23、第二走线轮24、第一辅助轮25和第二辅助轮26表面均设置有同步齿,所述走线同步带27环绕设置在第一走线轮23和第一辅助轮25之间,所述走线同步带27环绕设置在第二走线轮24和第二辅助轮26之间。
71.参照图9-10,所述第一辅助轮25转动连接有第一固定柱28,所述第二辅助轮26转动连接有第二固定柱29,所述第一传动轴21和第二传动轴22上均通过转动轴承连接有辅助连臂211,位于所述第一传动轴21上的辅助连臂211远离第一传动轴21的一端套设在第一固定柱28外,位于所述第二传动轴22上的辅助连臂211远离第二传动轴22的一端套设在第二固定柱29外,所述辅助连臂211绕第一传动轴21或第二传动轴22双向转动至极限位置时,所述第一固定柱28和第二固定柱29分别位于第一安装位和第二安装位。
72.参照图9-10,所述第一固定柱28和第二固定柱29均安装于第一安装位时,线缆与
走线同步带27位于第一辅助轮25和第一走线轮23之间的部分相贴合,线缆与走线同步带27位于第二辅助轮26和第二走线轮24之间的部分相贴合;所述第一固定柱28和第二固定柱29均位于第二安装位时,线缆与走线同步带27包覆在第一走线轮23和第二走线轮24外部的部分相贴合。
73.本技术实施例2的实施原理为:在待剥线的线缆长度较长的情况下,为了提高剥线时的稳定性,工作人员可以转动辅助连臂211,使得第一固定柱28和第二固定柱29均位于第一安装位,此时走线同步带27和线缆之间有较长的接触长度,可以实现对线缆更为稳定的输送,以有效减少线缆在移动时与第一走线轮23和第二走线轮24之间发生脱离的可能性。
74.当待剥线的线缆长度比较小的情况下,工作人员可以转动辅助连臂211,使得第一固定柱28和第二固定柱29均位于第二安装位,此时走线同步带27和线缆之间的接触长度大大减少,可以为切线提供足够的切线空间。
75.通过转动辅助连臂211改变第一固定柱28和第二固定柱29的位置,可以使得该种自动剥线机更加适合于长线缆和短线缆的剥线,大大提高了该种自动剥线机的适用性。
76.以上均为本技术的较佳实施例,并非依此限制本技术的保护范围,故:凡依本技术的结构、形状、原理所做的等效变化,均应涵盖于本技术的保护范围之内。