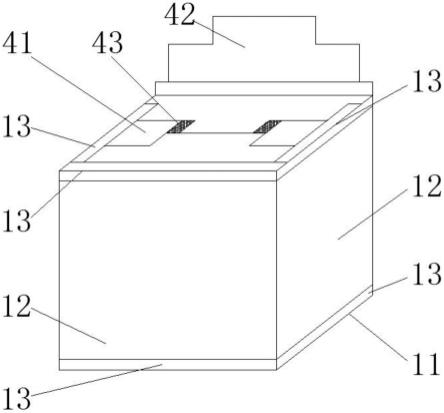
1.本实用新型涉及保护膜技术领域,具体地说,涉及一种锂电池模组封装用耐腐蚀绝缘包膜。
背景技术:2.锂电池模组的铝壳表面通常会包覆有绝缘包膜,随着新能源汽车的快速发展,要求绝缘包膜具备隔热、绝缘、防穿刺的功能,以提高锂电池组的使用安全性。现有的绝缘包膜缺少对锂电池模组的铝壳边棱部位保护的作用。
技术实现要素:3.为达到上述目的,本实用新型公开了一种锂电池模组封装用耐腐蚀绝缘包膜,包括:
4.底膜,所述底膜呈方形设置;
5.侧膜,四个所述侧膜通过棱角膜连接于所述底膜边沿端;
6.顶拼接膜,四个所述顶拼接膜通过棱角膜连接于所述侧膜远离底膜端;
7.其中所述底膜、侧膜、棱角膜以及顶拼接膜靠近锂电池模组的铝壳端均连接有玻璃纤维层。
8.优选的,所述底膜包括:
9.pet膜;
10.压敏胶层,所述压敏胶层连接于两个所述pet膜之间、以及其中一个所述 pet膜靠近锂电池模组的铝壳端所述玻璃纤维层与pet膜之间连接有压敏胶层;
11.第一镀铝薄层,所述第一镀铝薄层连接于所述pet膜远离锂电池模组的铝壳端;
12.离型膜,所述离型膜连接于所述玻璃纤维层远离压敏胶层端。
13.优选的,所述侧膜、顶拼接膜的结构均与所述底膜的结构相同。
14.优选的,所述pet膜的厚度为25μm。
15.优选的,所述压敏胶层厚度为30μm。
16.优选的,相邻的所述侧膜留有包覆倒角。
17.优选的,所述棱角膜包括:
18.基膜,所述基膜截面呈锯齿形折弯设置,所述基膜的锯齿凹槽开槽方向与所述锂电池模组的铝壳边棱平行设置,所述玻璃纤维层连接于所述基膜靠近锂电池模组的铝壳端;
19.第二镀铝薄层,所述第二镀铝薄层连接于所述基膜远离锂电池模组的铝壳端;
20.压敏胶层,所述玻璃纤维层和基膜之间、以及所述第二镀铝薄层和基膜之间均通过压敏胶层连接;
21.阻燃纤维,所述阻燃纤维埋设于所述基膜靠近第二镀铝薄层端的锯齿凹槽内;
22.固化胶滴,所述固化胶滴连接于所述基膜靠近玻璃纤维层端,若干个所述固化胶
滴所在直线与所述基膜的锯齿凹槽开槽方向呈垂直分布。
23.优选的,所述顶拼接膜包括:
24.条状拼接膜,两个所述条状拼接膜通过棱角膜对向连接于所述侧膜远离底膜端;
25.t型拼接膜,两个所述t型拼接膜通过棱角膜对向连接于所述侧膜远离底膜端,两个所述t型拼接膜拼成h型结构,两个所述条状拼接膜对称位于两个所述t型拼接膜横向段的两侧;
26.自粘胶涂液,所述自粘胶涂液涂布于所述条状拼接膜拼接口位置。
27.优选的,所述底膜、侧膜以及顶拼接膜上均预留有连接口。
附图说明
28.为了更清楚地说明本实用新型具体实施方式或现有技术中的技术方案,下面将对具体实施方式或现有技术描述中所需要使用的附图作简单地介绍,显而易见地,下面描述中的附图是本发明的一些实施方式,对于本领域普通技术人员来讲,在不付出创造性劳动的前提下,还可以根据这些附图获得其他的附图。
29.图1为本实用新型立体示意图;
30.图2为本实用新型展开示意图;
31.图3为本实用新型中底膜结构示意图;
32.图4为本实用新型中棱角膜结构示意图。
33.图中:11.底膜;12.侧膜;13.棱角膜;14.顶拼接膜;15.玻璃纤维层;21.pet 膜;22.压敏胶层;23.第一镀铝薄层;24.离型膜;31.基膜;32.第二镀铝薄层; 33.阻燃纤维;34.固化胶滴;41.条状拼接膜;42.t型拼接膜;43.自粘胶涂液。
具体实施方式
34.下面将结合附图对本实用新型的技术方案进行清楚、完整地描述,显然,所描述的实施例是本发明一部分实施例,而不是全部的实施例。基于本实用新型中的实施例,本领域普通技术人员在没有做出创造性劳动前提下所获得的所有其他实施例,都属于本实用新型保护的范围。
35.实施例
36.下面将结合附图对本实用新型做进一步描述。
37.如图1、图2所示,本实施例提供的一种锂电池模组封装用耐腐蚀绝缘包膜,包括:
38.底膜11,所述底膜11呈方形设置;
39.侧膜12,四个所述侧膜12通过棱角膜13连接于所述底膜11边沿端;
40.顶拼接膜14,四个所述顶拼接膜14通过棱角膜13连接于所述侧膜12远离底膜11端;
41.其中所述底膜11、侧膜12、棱角膜13以及顶拼接膜14靠近锂电池模组的铝壳端均连接有玻璃纤维层15。
42.上述技术方案的工作原理和有益效果为:
43.本实用新型公开了一种锂电池模组封装用耐腐蚀绝缘包膜,由底膜11、四个侧膜12、以及顶拼接膜14组成,底膜11、侧膜12、棱角膜13以及顶拼接膜 14靠近锂电池模组的铝
壳端均连接有玻璃纤维层15,提高了绝缘包膜耐腐蚀的性能,棱角膜13包覆于锂电池模组的铝壳的顶端边沿端和底端边沿端,从而起到对锂电池模组的铝壳边棱保护作用,锂电池模组无论在那个方位摔落,棱角膜13都能很好的减少锂电池模组的铝壳表面受到的外力作用。
44.如图3所示,在一个实施例中,所述底膜11包括:
45.pet膜21;
46.压敏胶层22,所述压敏胶层22连接于两个所述pet膜21之间、以及其中一个所述pet膜21靠近锂电池模组的铝壳端所述玻璃纤维层15与pet膜21 之间连接有压敏胶层22;
47.第一镀铝薄层23,所述第一镀铝薄层23连接于所述pet膜21远离锂电池模组的铝壳端;
48.离型膜24,所述离型膜24连接于所述玻璃纤维层15远离压敏胶层22端。
49.上述技术方案的有益效果为:
50.pet膜21具有优良的耐候性和耐酸液性,提高了底膜11的韧性和抗拉强度,第一镀铝薄层23提高了底膜11的防穿刺性和热传导性,离型膜24的设置,使底膜11易剥离。
51.在一个实施例中,所述侧膜12、顶拼接膜14的结构均与所述底膜11的结构相同。
52.在一个实施例中,所述pet膜21的厚度为25μm。
53.在一个实施例中,所述压敏胶层22厚度为30μm。
54.在一个实施例中,相邻的所述侧膜12留有包覆倒角。
55.如图4所示,在一个实施例中,所述棱角膜13包括:
56.基膜31,所述基膜31截面呈锯齿形折弯设置,所述基膜31的锯齿凹槽开槽方向与所述锂电池模组的铝壳边棱平行设置,所述玻璃纤维层15连接于所述基膜31靠近锂电池模组的铝壳端;
57.第二镀铝薄层32,所述第二镀铝薄层32连接于所述基膜31远离锂电池模组的铝壳端;
58.压敏胶层22,所述玻璃纤维层15和基膜31之间、以及所述第二镀铝薄层 32和基膜31之间均通过压敏胶层22连接;
59.阻燃纤维33,所述阻燃纤维33埋设于所述基膜31靠近第二镀铝薄层32端的锯齿凹槽内;
60.固化胶滴34,所述固化胶滴34连接于所述基膜31靠近玻璃纤维层15端,若干个所述固化胶滴34所在直线与所述基膜31的锯齿凹槽开槽方向呈垂直分布。
61.上述技术方案的工作原理和有益效果为:
62.基膜31靠近玻璃纤维层15端的锯齿凹槽内滴设有固化胶滴34,从而使侧膜12、顶拼接膜14更方便的向靠近锂电池模组的铝壳方向翻折,基膜31截面呈锯齿形折弯设置,增加了棱角膜13的缓冲厚度,固化胶滴34的形变量提高了棱角膜13的防摔性,阻燃纤维33的设置,提高了棱角膜13的阻燃效率。
63.在一个实施例中,所述顶拼接膜14包括:
64.条状拼接膜41,两个所述条状拼接膜41通过棱角膜13对向连接于所述侧膜12远离底膜11端;
65.t型拼接膜42,两个所述t型拼接膜42通过棱角膜13对向连接于所述侧膜12远离底
膜11端,两个所述t型拼接膜42拼成h型结构,两个所述条状拼接膜41对称位于两个所述t型拼接膜42横向段的两侧;
66.自粘胶涂液43,所述自粘胶涂液43涂布于所述条状拼接膜41拼接口位置。
67.上述技术方案的有益效果为:
68.条状拼接膜41翻折于锂电池模组的铝壳顶端,烘烤固化的自粘胶涂液43,从而使自粘胶涂液43带沾附性,将t型拼接膜42沾附于自粘胶涂液43上,从而对锂电池模组的铝壳顶端进行包覆。
69.在一个实施例中,所述底膜11、侧膜12以及顶拼接膜14上均预留有连接口。
70.显然,上述实施例仅仅是为清楚地说明所作的举例,而并非对实施方式的限定。对于所属领域的普通技术人员来说,在上述说明的基础上还可以做出其它不同形式的变化或变动。这里无需也无法对所有的实施方式予以穷举。而由此所引伸出的显而易见的变化或变动仍处于本发明创造的保护范围之中。