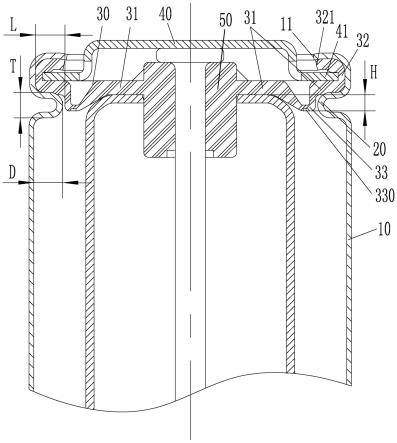
1.本实用新型涉及电池部件领域,尤其涉及一种深扎线碱性电池密封结构。
背景技术:2.目前,我国各碱性电池厂家的碱性电池生产线大多数引进日本fdk的生产设备、配方、配件结构及技术工艺,所制得碱性电池的一般结构为:包括正极钢壳,正极钢壳为仅上端敞开的筒形结构,正极钢壳内同轴套设隔离管,正极钢壳与隔离管之间的环形空腔内填入压制好的正极环,隔离管内填充有负极材料,隔离管的上端开口处盖设有一密封圈,正极钢壳的上端开口处嵌置有负极盖,负极盖底面中心位置垂直固设有一集流钉,所述密封圈位于负极盖的下方,所述密封圈包括密封圈本体,所述密封圈本体的中心位置设有中心柱,所述中心柱的中心位置开设有集流钉通孔;所述集流钉穿过集流钉通孔并与集流钉通孔过盈配合,集流钉的下端插设在负极材料内;所述负极盖的外周壁与正极钢壳的内周壁之间留有环形缝隙,所述密封圈本体径向向外延伸至正极钢壳的内周壁处并向上形成翻边,该翻边插设在所述环形缝隙内将环形缝隙封闭;所述密封圈本体向下凹陷从而在所述密封圈本体上形成底部凸起,所述底部凸起位于隔离管外侧;所述密封圈外侧的所述正极钢壳周壁沿径向向内凹陷形成弧形凹槽(也称“扎线槽”),所述弧形凹槽对应的正极钢壳内周壁上形成向内拱起的凸缘,所述密封圈位于所述凸缘的上方且其底面与所述凸缘相抵接。
3.由于现有的碱性电池的所述凸缘设计只是起到对密封圈进行限位的作用,因此,所述正极钢壳上的凸缘的径向高度通常只有0.3
±
0.05mm。在碱性电池装配时,所述正极钢壳的上边沿向内弯折并向下压紧密封圈和负极盖进行收边,以实现正极钢壳与负极盖之间的扣合。但是,由于所述弧形凸起的径向高度偏低,在向内折弯所述正极钢壳的上边沿实现其与所述负极盖之间的扣合时,所述密封圈在受到的向下挤压力过大时会过度下移导致密封圈挤压进入所述弧形凸缘,导致所述密封圈局部发生形变或歪斜,影响电池的密封性。
技术实现要素:4.本实用新型旨在提供一种深扎线碱性电池密封结构,其能够解决现有技术中所存在的密封不佳的问题。
5.一种深扎线碱性电池密封结构,包括正极钢壳,所述正极钢壳上端敞开设置,所述正极钢壳的周壁在靠近其上端开口位置处沿所述正极钢壳的径向向内凹陷从而在所述正极钢壳的内周壁上形成凸缘,所述凸缘沿所述正极钢壳的内圆周分布;所述凸缘上方的所述正极钢壳内设置有密封圈,所述密封圈包括密封圈本体,所述密封圈本体的外沿与所述正极钢壳的内周壁相抵接,所述密封圈本体的底面与所述凸缘相抵接;所述凸缘在所述正极钢壳的径向上的高度(简称“所述凸缘的径向高度”)控制在0.5~1.5mm。
6.本实用新型通过加大所述凸缘的径向高度,避免正极钢壳的上边沿在进行向内弯折进行收边时密封圈下陷进入所述凸缘的中心腔内而导致密封圈发生局部变形或歪斜从而影响电池密封性能;同时,也加长了密封圈本体的底面与所述凸缘的接触段,利于提高电
池密封性能。
7.优选的,所述凸缘的径向高度控制在1.0~1.5mm,进一步加长密封圈本体的底面与所述凸缘的接触段,电池密封性能更好。
8.优选的,所述凸缘在所述正极钢壳轴向上的厚度控制在0.9~2.4mm。
9.在具体实施过程中,所述密封圈的上方设有负极盖,所述负极盖具有外沿部,所述负极盖的外沿部与所述正极钢壳的内周壁之间留有环形缝隙,所述密封圈本体的外沿向上弯折延伸形成翻边,所述翻边插设在所述环形缝隙内并将环形缝隙封闭;所述正极钢壳的上边沿和所述翻边的上边沿均高于所述负极盖的外沿部,所述正极钢壳的上边沿带动所述翻边一起向内弯折并一起向下压紧所述负极盖的外沿部,实现收边。
10.在具体实施过程中,所述密封圈本体向下凹陷在所述密封圈本体的下表面上形成底部凸起。优选的,所述底部凸起与所述正极钢壳的内周壁在所述正极钢壳的径向上的距离(简称“所述底部凸起与所述正极钢壳的内周壁之间的径向距离”)控制在0.6~1.6mm。所述底部凸起的设计能够提高密封圈的径向上的柔韧性,进而提高所述密封圈与正极钢壳之间的压紧力,并且,与现有碱性电池的密封圈的底部凸起与正极钢壳之间的径向距离通常只有0.5
±
0.05mm相比,为所述凸缘提供足够的容置空间。进一步的,所述底部凸起在所述正极钢壳轴向上的高度控制在0.5~1.3mm。与现有碱性电池的密封圈的底部凸起在所述正极钢壳轴向上的高度控制在2.0
±
0.05mm相比,加大了电池内部空间。在具体实施过程中,所述密封圈本体的中心位置处设有中心柱,所述底部凸起位于所述中心柱的径向外侧。优选的,在所述底部凸起上开设环形的泄气防爆槽,所述泄气防爆槽的中心轴线与所述密封圈本体的中心轴线相重合。现有的碱性电池密封圈的泄气防爆槽一般是沿所述中心柱的外周开设,而本实用新型的所述泄气防爆槽设置在所述底部凸起上,在向所述中心柱的中心孔内插入集流钉时不容易导致泄气防爆槽撕裂和中心柱断裂,并且,泄气防爆槽的直径更大,泄气槽更长,泄气量也更大,降低爆炸风险。
附图说明
11.图1是本实用新型的深扎线碱性电池密封结构的立体结构图,其中的点划线均为正极钢壳的中心轴线。
具体实施方式
12.下面结合附图对本实用新型的深扎线碱性电池密封结构的具体实施方式作详细的说明:
13.如图1所示,一种深扎线碱性电池密封结构,包括正极钢壳10,所述正极钢壳10上端敞开设置,所述正极钢壳10的周壁在靠近其上端开口位置处沿所述正极钢壳10的径向向内凹陷从而在所述正极钢壳10的内周壁上形成凸缘20,所述凸缘20沿所述正极钢壳10的内圆周分布;所述凸缘20上方的所述正极钢壳10内设置有密封圈30,所述密封圈30包括密封圈本体31,所述密封圈本体31的外沿与所述正极钢壳10的内周壁相抵接,所述密封圈本体31的底面与所述凸缘20相抵接;所述凸缘20在所述正极钢壳10的径向上的高度d控制在0.5~1.5mm。
14.本实用新型通过加大所述凸缘20的径向高度d,避免正极钢壳10的上边沿在进行
向内弯折进行收边时密封圈30下陷进入所述凸缘20的中心腔内而导致密封圈30发生局部变形或歪斜从而影响电池密封性能;同时,也加长了密封圈本体31的底面与所述凸缘20的接触段,利于提高电池密封性能。
15.优选的,如图1所示,所述凸缘20的径向高度d控制在1.0~1.5mm,进一步加长密封圈本体31的底面与所述凸缘20的接触段,电池密封性能更好。当然,所述凸缘20的径向高度也可以为0.5~1.0mm,此时,所述凸缘20也能起到较好的支撑密封圈的作用。
16.优选的,如图1所示,所述凸缘20在所述正极钢壳轴向上的厚度t控制在0.9~2.4mm。
17.在具体实施过程中,如图1所示,所述密封圈30的上方设有负极盖40,所述负极盖40具有外沿部41,所述负极盖40的外沿部41与所述正极钢壳10的内周壁之间留有环形缝隙,所述密封圈本体31的外沿向上弯折延伸形成翻边32,所述翻边32插设在所述环形缝隙内并将环形缝隙封闭;所述正极钢壳10的上边沿11和所述翻边32的上边沿321均高于所述负极盖40的外沿部41,所述正极钢壳10的上边沿11带动所述翻边32一起向内弯折并一起向下压紧所述负极盖40的外沿部41,实现收边。
18.优选的,如图1所示,所述密封圈本体31向下凹陷在所述密封圈本体31的下表面上形成底部凸起33,所述底部凸起33与所述正极钢壳10的内周壁在所述电池钢壳的径向上的距离l控制在0.6~1.6mm。所述底部凸起33的设计能够提高密封圈30的径向上的柔韧性,进而提高所述密封圈30与正极钢壳10之间的压紧力,并且,与现有碱性电池的密封圈的底部凸起33与正极钢壳10之间的径向距离l通常只有0.5
±
0.05mm相比,为所述凸缘20提供足够的容置空间。当然,本实用新型的所述密封圈本体31上也可以不设置底部凸起33。进一步的,如图1所示,所述底部凸起33在所述正极钢壳轴向上的高度h控制在0.5~1.3mm。与现有碱性电池的密封圈的底部凸起33在所述正极钢壳轴向上的高度h控制在2.0
±
0.05mm相比,加大了电池内部空间。所述底部凸起33在所述正极钢壳轴向上的高度h也可以大于1.3mm,但此时占用电池内部空间较大,电池内部空间利用率随之降低。在具体实施过程中,如图1所示,所述密封圈本体31的中心位置处设有中心柱50,所述底部凸起33位于所述中心柱50的径向外侧。优选的,如图1所示,在所述底部凸起33上开设环形的泄气防爆槽330,所述泄气防爆槽330的中心轴线与所述密封圈本体41的中心轴线相重合。现有的碱性电池密封圈的泄气防爆槽一般是沿所述中心柱的外周开设,而本实用新型的所述泄气防爆槽330设置在所述底部凸起33上,在向所述中心柱的中心孔内插入集流钉时不容易导致泄气防爆槽撕裂和中心柱断裂,并且,泄气防爆槽330的直径更大,泄气槽更长,泄气量也更大,降低爆炸风险。当然,本实用新型的泄气防爆槽330也可以沿所述中心柱50的外周开设。
19.需要说明的是,本实用新型的负极盖40的形状并不限于附图中的具体形状,其可以是现有的任意形状的负极盖40,例如:所述负极盖40的外沿部41不限于附图中的仅沿所述正极钢壳的径向延伸的一字型结构,其也可以采用弯钩形结构。
20.本实用新型对于本实用新型所属技术领域的普通技术人员来说,在不脱离本实用新型构思的前提下,还可以做出若干简单推演或替换,都应当视为属于本实用新型的保护范围。