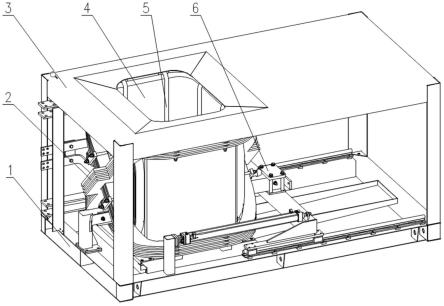
1.本实用新型涉及无损检测领域的一种非接触式三维旋转磁场井式多功能磁粉探伤检测装置,可以对铁路机车车辆、机械制造和铸造等行业形状复杂零部件的外表面及内孔表面进行湿法磁粉探伤。
背景技术:2.磁粉探伤是工业无损检测领域中对铁磁性材料工件表面和近表面缺陷进行无损检测的主要手段,磁粉探伤是利用磁现象来检测零件表面及近表面缺陷的方法,将铁磁性零件置于外加磁场中,零件被磁场磁化,磁力线在零件的表面和近表面形成一定的走向,如果零件表面和近表面有不连续或裂纹等缺陷,并与磁力线交叉一定角度时,则会引起磁通密度的改变,部分磁力线泄漏到空气绕过缺陷又折回到零件形成漏磁场,在缺陷处产生磁极。将一定粘度和导磁性的磁粉(如磁悬液),喷洒在零件的表面,零件被磁化后,则缺陷处的磁极吸附磁粉,磁粉的堆积形成磁痕,磁痕的外观显示出缺陷的长度、走向等一系列轮廓图像,从而达到探伤检查的目的。
3.在铁路机车车辆、机械制造及铸造行业的零部件多数零件为非规则的形状复杂的异形零部件,采用传统复合磁化时,通电磁化方式存在通电位置不好选取,接触面不平整接触不良、缺陷被通电电极遮挡等问题,特别是铁路机车车辆的车钩、钩尾框、钩舌等缓冲器零件需要磁粉探伤检测的零部件因常年暴露在外,检修时的已使用多年,零部件的表面形状复杂,表面不平整并存在锈蚀的情况,当零件通电磁化电流2000a以上时通电电极与零件的接点处会产生接触不良或打火的现象,打火现象严重时可能灼伤零件,造成零件的报废,这使得磁粉探伤的可靠性及安全性大大降低,甚至满足不了探伤零件各部位检测灵敏度的要求。再者带有内孔零件,传统的复合磁化磁粉检测,线圈法磁化时由于磁场的作用主要在零件的外表面,由于零件本身对内孔部位磁场的屏蔽,内孔的磁场较弱,无法达到内孔检测磁场强度要求。
技术实现要素:4.本实用新型针对现有技术中存在的缺陷和不足,提供一种适合于异型复杂零件外表面及内孔表面缺陷磁粉探伤检测的三维旋转磁场井式多功能磁化装置。
5.本实用新型的技术解决方案是:一种三维旋转磁场井式多功能磁化装置,包括不锈钢底座、旋转磁化装置、不锈钢机架、pvc板、喷淋管路和穿棒及感应一体化磁化装置,不锈钢底座上设有旋转磁化装置、不锈钢机架和穿棒及感应一体化磁化装置,pvc板包封在旋转磁化装置内、外表面,喷淋管路固定在不锈钢机架井口处。
6.所述的旋转磁化装置包括交叉线圈ⅰ组、交叉线圈ⅱ组、侧置线圈ⅲ组,不锈钢底座上设有支撑板,支撑板上设有立板,交叉线圈ⅰ组和交叉线圈ⅱ组以90
°
交叉的方式安装固定在不锈钢底座上,侧置线圈ⅲ组位于交叉点一侧并安装固定在立板上。
7.所述的穿棒及感应一体化磁化装置包括直线轴承,穿棒铜排、移动支架、压板、气
缸、喷淋管、pvc封板、感应铁芯、套管、电极头、支座及固定座,固定座与气缸的缸体铰接,气缸的活塞杆与移动支架螺纹连接,同时移动支架固定在直线轴承的滑块上,穿棒铜排、pvc封板、感应铁芯及套管用紧固件连接在一起,并用压板安装紧固定在移动支架上,pvc封板顶面设有喷淋管,电极头紧固在支座上,支座同直线轴承的导轨都安装在不锈钢底座上。
8.本实用新型采用井式结构设计,磁化装置一次磁化可全方位显示检测件表面或近表面缺陷,便于实现自动探伤和重点部位的手动探伤,操作方便快捷,效率高;磁化装置不与工件接触,检测可靠;寿命长、少维修;由于采用了井式结构,探伤零件垂直吊挂探伤可以很方便应用于检修或生产的流水线上,提高了生产效率。磁化装置线圈大小和形状可以根据检测零件尺寸和形状而改变,可以是圆形及椭圆形及不规则形状,满足多种复杂零件的探伤需要。
附图说明
9.图1为本实用新型的结构示意图。
10.图2本实用新型旋转磁化装置结构示意图。
11.图3本实用新型穿棒及感应一体化磁化装置结构示意图。
具体实施方式
12.一种三维旋转磁场井式多功能磁化装置,包括不锈钢底座1、旋转磁化装置2、不锈钢机架3、pvc板4、喷淋管路5和穿棒及感应一体化磁化装置6。不锈钢底座1上设有旋转磁化装置2、不锈钢机架3和穿棒及感应一体化磁化装置6,pvc板4包封在旋转磁化装置2内、外表面,喷淋管路5固定在不锈钢机架3井口处。
13.所述的旋转磁化装置2包括支撑板7、绝缘垫a8、m12螺母9、m12螺柱10、交叉线圈ⅰ组11、交叉线圈ⅱ组12、侧置线圈ⅲ组13、立板14、角铁15、绝缘垫b16、m8螺母17、m8螺栓18、支座19及m8螺钉20。交叉线圈ⅰ组11和交叉线圈ⅱ组12以90
°
交叉的方式用紧固件m12螺母9和m12螺柱10安装固定在不锈钢底座1上,侧置线圈ⅲ组13位于交叉点一侧并用m8螺母17、m8螺栓18及角铁15安装固定在立板14上,立板14用m8螺钉20及支座19安装固定在支撑板7上,支撑板7与不锈钢底座1固定连接。
14.所述的穿棒及感应一体化磁化装置6包括直线轴承21,穿棒铜排22、移动支架23、压板24、m10螺钉25、气缸26、喷淋管27、m8螺母17、m8螺栓18、pvc封板28、感应铁芯29、套管30、m6螺钉31、电极头32、支座33及固定座34。固定座34与气缸26的缸体铰链连接,气缸26的活塞杆与移动支架23螺纹连接,同时移动支架23用螺钉固定在直线轴承21的滑块上,穿棒铜排22、pvc封板28、感应铁芯29及套管30用紧固件m8螺母17、m8螺栓18连接在一起,并用压板24及m10螺钉25安装紧固定在移动支架23上,pvc封板28顶面设有喷淋管27,电极头32用m6螺钉31紧固在支座33上,支座33同直线轴承21的导轨都安装在不锈钢底座1上。
15.三维旋转磁场的建立:采用两组相互交叉的磁化线圈并在交叉磁化线圈交叉点处布置一组磁化线圈。三组磁化线圈分别接入相位不同的交流电,在线圈包容的空间内,各组线圈分别形成的幅值相同,相互呈一定角度,并具有一定的电流相位差的交流磁场发生矢量迭加,从而形成了强弱、方向随时间不断改变的周期性旋转磁场。当零件由输送装置送入在三维空间旋转磁场磁化时,工件表面任何方向的缺陷(裂纹)均能清晰显示出来,使形状
复杂的零件能够实现非接触式探伤。
16.本实用新型三维旋转磁场交叉线圈ⅰ组11、交叉线圈ⅱ组12、侧置线圈ⅲ组13采用井式布置,绝缘连接固定在不锈钢底座1上,由于探伤工作时使用的载液为水或煤油,为保证工作的安全,由交叉线圈ⅰ组11、交叉线圈ⅱ组12、侧置线圈ⅲ组13组成的旋转磁化装置2内、外表面采用pvc板4包封处理,磁悬液的喷淋管路5采用不锈钢钢管打孔的方式,喷淋管路5分别布置在井口的下方和磁化装置四周,保证被检测的零件表面磁悬液能得到充分的覆盖。将检测零件悬吊置于旋转磁化装置2腔体内,喷淋管路5喷散磁悬液直至充分覆盖检测零件表面,交叉线圈ⅰ组11、交叉线圈ⅱ组12及侧置线圈ⅲ组13接入不同相位的低压交流电,在线圈包容空间内产生三维旋转磁场可一次完成零件整体磁化,磁化结束后操作人员吊起工件,在紫外线灯照射下,观察检测零件是存在裂纹等缺陷,观察完毕后吊走检测零件探伤作业结束。
17.本实用新型内孔磁化为穿棒及感应一体化磁化装置6,包括:直线轴承21,穿棒铜排22、移动支架23、压板24、m10螺钉25、气缸26、喷淋管27、m8螺母17、m8螺栓18、pvc封板28、感应铁芯29、套管30、m6螺钉31、电极头32、支座33及固定座34。将带有内孔的检测零件悬吊置于旋转磁化装置2内,气缸26缩回带动移动支架23及安装在动移动支架23上穿棒铜排22、感应铁芯29及喷淋管27一起向左移动穿过检测零件内孔并顶紧电极头32,喷淋管27均匀喷散磁悬液至检测零件内孔表面;给穿棒铜排22和电极头32接入低压交流电,产生垂直于电流方向的周向磁场;同时给侧置线圈ⅲ组13接入低压交流电,在感应铁芯29内部会产生交变磁场,从而在检测零件内孔表面产生感应电流,形成垂直于感应电流方向的纵向磁场,这时在检测零件内孔里形成周向和纵向的复合磁场,在复合磁场的作用下可以一次完成检测零件内孔表面磁化,吊起检测零件,在紫外线灯的照射下,观察检测零件内孔表面是存在裂纹等缺陷,观察完毕后吊走检测零件探伤作业结束。
18.为了保证不同的零件探伤部位表面磁场达到有效检测磁场强度,采用可控硅模块调整磁化电流。试验表明,零件探伤时磁化电流峰值调整至2500a-3000a时a1型15/50标准灵敏度试片即可清晰显示。
19.为保证磁化后的零件有较小的剩磁,关闭磁化电源时采用了不等值的电流衰减措施,在三维旋转磁场磁化线圈中的电流逐级衰减过程中,作用在工件上的交变磁场幅度也逐渐降为零。探伤结束后,可使被检测件各部位剩磁小于0.3mt。
20.为使探伤机的开始喷淋、结束喷淋时间、磁化时间/间歇时间长短、磁化时机等的结合能满足零件探伤的实际需要,保证磁化结束时在探伤件表面缺陷处留下清晰的磁痕,我们通过多次试验,找出来出一个理想的磁化程序,将这个程序输入plc控制器,在程控探伤状态下,探伤机自动完成整个探伤过程,减小了影响探伤的人为因素。同时为便于探伤专业人员自由控制探伤过程,保留了手动控制探伤的功能。